2020年《冲压工艺及模具设计》课程设计说明书参照模板
#0803班《冲压工艺及模具设计》课程设计任务书#

《冲压工艺及模具设计》课程设计指导书一、课程设计的目的《冲压工艺与模具设计》课程设计是冲模课程的最后一个教学环节,同时是第一次对学生进行全面的模具设计训练。
其基本目的是:(1)综合运用冷冲模课程和其它有关先修课程的理论及生产实践的知识去分析和解决模具设计问题,并使所学专业知识得到进一步巩固和深化。
(2)学习模具设计的一般方法,了解和掌握常用模具整体设计、零部件的设计过程和计算方法,培养正确的设计思想和分析问题、解决问题的能力,特别是总体设计和计算的能力。
(3)通过计算和绘图,学会运用标准、规范、手册、图册和查阅有关技术资料等,培养模具设计的基本技能。
二、冲压模具设计步骤1、分析冲压件的工艺性根据设计题目的要求,分析冲压件成形的结构工艺性,分析冲压件的形状特点、尽寸大小、精度要求及所用材料是否符合冲压工艺要求。
如果发现冲压件工艺性差,则需要对冲压件产品提出修改意见,经产品设计者同意后方可修改。
2、制定冲压件工艺方案在分析了冲压件的工艺性之后,通常可以列出几种不同的冲压工艺方案(包括工序性质、工序数目、工序顺序及组合方式),从产品质量、生产效率、设备占用情况、模具制造的难易程度和模具寿命高低、工艺成本、操作方便和安全程度等方面,进行综合分析、比较,然后确定适合于工厂具体生产条件的最经济合理的工艺方案。
3、确定毛坯形状、尺寸和下料方式在最经济的原则下,决定毛坯的形状、尺寸和下料方式,并确定材料的消耗量。
4、确定冲模类型及结构型式根据所确定的工艺方案和冲压件的形状特点、精度要求、生产批量、模具制造条件、操作方便及安全的要求,以及利用现有通用机械化、自动化装置的可能,选定冲模类型及结构型式,绘制模具结构草图。
5、进行必要的工艺计算1)计算毛坯尺寸,以便在最经济的原则下进行排样和合理使用材料。
2)计算冲压力(包括冲裁力、弯曲力、拉深力、卸料力、推件力、压边力等),以便选择压力机。
3)计算模具压力中心,防止模具因受偏心负荷作用影响模具精度和寿命。
冲压模具课程设计说明书 2
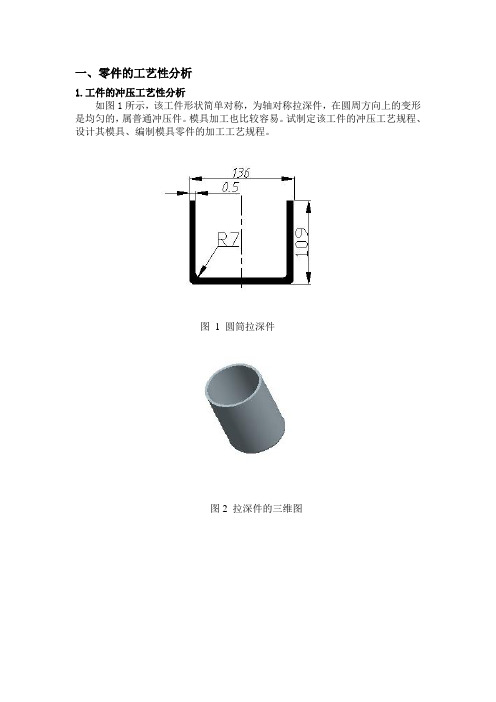
一、零件的工艺性分析1.工件的冲压工艺性分析如图1所示,该工件形状简单对称,为轴对称拉深件,在圆周方向上的变形是均匀的,属普通冲压件。
模具加工也比较容易。
试制定该工件的冲压工艺规程、设计其模具、编制模具零件的加工工艺规程。
图1 圆筒拉深件图2 拉深件的三维图2.工件材料化学成分和机械性能分析(1)材料分析工件的材料为08钢,属于优质碳素结构钢,优质沸腾钢,强度、硬度低,冷变形塑性很好,可深冲压加工,焊接性好。
成分偏析倾向大,时效敏感性大,故冷加工时应采用消除应力热处理或水韧处理,防止冷加工断裂。
08钢的主要机械性能如下:σ(兆帕) 280-390抗拉强度bσ(兆帕) 180屈服强度s抗剪强度(兆帕) 220-310延伸率δ 32%(2)结构分析工件为一窄凸缘筒形件,结构简单,圆角半径为r=7,厚度为t=0.5mm,满足筒形拉深件底部圆角半径大于一倍料厚的要求,因此,零件具有良好的结构工艺性。
(3)精度分析工件上尺寸均为未注公差尺寸,普通拉深即可达到零件的精度要求。
经上述分析,产品的材料性能符合冷冲压加工要求。
在零件工艺性分析的基础上制定其工艺路线如下:零件的生产包括落料、拉深(需计算确定拉深次数)、修边(采用机械加工)等工序,为了提高生产效率,可以考虑工序的复合,经比较决定采用落料与第一次拉深复合。
二、工件的拉深工艺分析及计算1.毛坯尺寸计算(1)计算原则相似原则:拉深前坯料的形状与拉深件断面形状相似;等面积原则:拉深前坯料面积与拉深件面积相等。
(2)计算方法由以上原则可知,旋转体拉深件采用圆形毛坯,其直径按面积相等的原则计算。
计算坯料尺寸时,先将拉深件划分为若干便于计算的简单几何体,分别求出其面积后相加,得拉深件总面积A。
图3 拉深件的坯料计算如图3所示,筒形件坯料尺寸,将圆筒件分成三个部分,每个部分面积分别为:(3)确定零件修边余量由于板料的各向异性和模具间隙不均等因素的影响,拉深后零件的边缘不整齐,甚至出现耳子,需在拉伸后进行修边。
冲压工艺及模具设计课程设计说明书
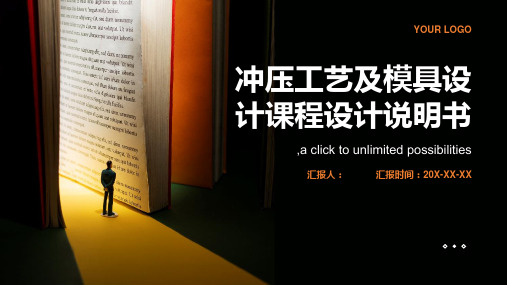
设计标准:满足生产效率、 质量、成本等方面的要求
设计内容:包括工艺流程、 模具设计、材料选择等方 面的内容
设计成果:提交设计报告、 图纸、模型等成果
设计时间:在规定时间内 完成设计任务
设计的步骤和方法
确定设计任务:明确设计目标、要求和 限制条件
绘制图纸:根据设计方案,绘制冲压 工艺及模具设计图纸
收集资料:查阅相关文献、标准、手 册等资料
编写说明书:详细描述设计过程、结 果、分析和改进建议等
制定设计方案:根据设计任务和资料, 制定设计方案
评审和修改:根据评审意见,对设计 方案和说明书进行修改和完善
课程设计过程
设计前期准备
确定设计目标:明确设计任务和要求, 制定设计计划
收集资料:查阅相关文献、标准、规 范,了解冲压工艺及模具设计的基本 原理和方法
模具设计的基本原则
安全性原则:保证模具在使用过程中的安 全性
可靠性原则:保证模具在生产过程中的稳 定性和可靠性
经济性原则:降低模具制造成本,提高生 产效率
环保性原则:减少模具制造和使用过程中 的环境污染
功能性原则:满足产品功能要求,保证产 品质量
创新性原则:采用新技术、新材料、新工 艺,提高模具设计水平
课程设计成果及总结
设计成果展示
冲压工艺及模具设计课程设计说 明书
设计总结:对设计过程中的难点、 重点进行总结,提出改进建议
添加标题
添加标题
添加标题
添加标题
设计成果:包括冲压工艺设计、 模具设计、生产工艺流程等
设计成果展示:展示设计成果, 包括设计图纸、实物模型等
遇到的问题及解决方法
问题:冲压工艺参数设置不合理,导致模具设计出现误差 解决方法:通过 查阅相关资料和请教老师,调整冲压工艺参数,确保模具设计准确无误
冲压工艺及模具设计说明书

目录:第1章冲压工艺性分析 (3)第2章确定模具的工艺方案 (4)第3章确定各工序模具结构形式 (4)第4章工艺计算 (5)第5章冲裁模工作部分结构参数的确定 (13)第6章拉深模工作部分结构参数的确定 (14)第7章模具主要零部件设计 (16)第8章绘制总装模具图、模具图 (21)第9章冲模的安装和安全技术 (21)第10章设计心得 (22)参考文献 (23)第1章冲压工艺性分析1.零件图(三角定位片)必须包含的冲压工序:拉深2. 工艺分析冲压件的工艺性要求是指冲压件对冲压工艺的适应性。
对冲压件工艺性影响最大的是制件的结构形状、精度要求、行位公差及技术要求等。
冲压件合理的工艺性能满足材料较省、工序较少、模具加工较易、寿命较长、操作方便及产品质量稳定等要求。
此工件只有落料、冲孔、拉深三个工序。
材料为08钢,为极软的碳素钢,强度、硬度很低,而韧性和塑性极高,具有良好的深冲、拉延、弯曲和镦粗等冷加工性能。
结构对称、简单。
有一个三角异形孔,工件的尺寸全部为自由公差,可为IT14级,尺寸精度底,普通冲裁就能满足要求。
(尺寸有表可查得,尺寸精度为IT14)。
第2章确定模具的工艺方案该工件包括落料、冲孔、拉深三个个基本工序,可有以下三种工艺方案:方案一:先冲孔,后落料再拉深,采用单工序模;方案二:冲孔、落料、拉深级进冲压,采用级进模;方案三:采用拉深-冲孔-落料复合模。
各方案优缺点的比较如下方案一:模具结构简单,制造比较方便,不过由于工序较多,需要多副模具,成本相对来说较高,生产效率比较低。
而且由于几道工序顺次进行,误差必定会增大,工件质量必定打折。
方案二:级进模是一种多工位的,高效率的加工方法。
一般适用于大批量的小型冲压件。
由于工序较多,构造会较为复杂,但是加工过程简单易操作,由于同一条生产线连续加工,所以会产生一定的累积误差,但是能满足设计要求。
方案三:拉深、冲孔,落料采用复合模一次性加工,只要一套模具,这样工序不会太复杂,但是拉深过程中会出现材料的位移,会使冲孔和落料的尺寸产生较大误差。
(整理)《冲压工艺及模具设计》课程设计指导与任务书

《冲压工艺及模具设计》课程设计指导书2.1 课程设计目的本课程设计是在学生学完“冲压工艺与冷冲模具设计”理论课并进行了上机练习之后进行的一个重要教学环节。
是学生运用所学理论,联系实际,提高工程技术能力和培养严谨细致作风的一次重要机会。
通过本次设计要达到以下目的:1、巩固与扩充“冲压工艺与冷冲模具设计”以及有关技术基础课程所学的内容,掌握制订冲压工艺规程和设计冲压模具的方法。
2、培养综合运用本专业所学课程的知识,解决生产中实际问题的工程技术能力(包括:设计、计算、绘图、技术分析与决策、文献检索以及撰写技术论文的能力)。
3、养成严肃、认真、细致地从事技术工作的优良作风。
2.2 课程设计步骤1. 设计准备1) 阅读产品零件图(1) 设计前应预先准备好设计资料、手册、图册、绘图用具、图纸、说明书用纸。
(2) 认真研究任务书及指导书,分析设计题目的原始图样、零件的工作条件,明确设计要求及内容。
(3) 熟悉各种可采用的模具结构形式及其优缺点。
2) 冲件图样分析产品零件图是分析编制冲压方案、设计模具的重要依据,对零件图的分析主要是从冲压工艺的角度出发,对冲压件的形状、尺寸(最小孔边距、孔径、材料厚度、最大外形)、精度、表面粗糙度、材料性能等逐项分析,确定冲压工序图。
若有与冲压工艺要求相悖者,应采取相应的解决措施或与指导教师协商更改。
(1) 工艺分析。
合理的冲压工艺,既能保证冲件的质量,使冲压工艺顺利进行,提高模具寿命,降低成本,提高经济效益,同时给模具的设计、制造与修理带来方便。
所以必须对指定的冲压件图样进行充分的工艺分析,在此基础上,拟订各种可能的不同工艺方案。
工艺分析主要是分析冲件的形状、尺寸及使用要求,分析冲件的工艺性;根据成形规律,确定所用冲压工艺方法;根据生产批量、冲压设备、模具加工的工艺条件等多方面因素,进行全面的分析、研究,确定冲件的工艺性质、工序数量、工序的组合和先后顺序。
在几种可能的冲压工艺方案中,选择一种经济、合理的工艺方案,并填写冲压工艺卡。
冲压模具课程设计说明书

冲压模具的动 作过程:包括 送料、冲压、 卸料、回程等
步骤
冲压模具的设 计要点:考虑 模具的强度、 刚度、耐磨性、
热处理等
冲压模具的应 用领域:汽车、 家电、电子等
行业
模具强度和刚度校核
刚度校核:确保模具在冲压过 程中不会发生过大的弹性变形
校核方法:有限元分析、实 验测试等
强度校核:确保模具在冲压 过程中不会发生断裂或变形
模具结构设计
模具类型: 根据冲压 工艺选择 合适的模 具类型
模具材料: 选择合适 的模具材 料,如钢、 铝等
模具尺寸: 根据冲压 件的尺寸 和精度要 求确定模 具尺寸
模具结构: 包括型腔、 型芯、模 架、导柱、 导套等部 件的设计 和布局
模具精度: 根据冲压 件的精度 要求确定 模具的精 度
模具寿命: 根据冲压 件的生产 数量和冲 压速度确 定模具的 寿命
感谢您的观看
伸等步骤
操作规程制定: 根据工艺流程
制定操作规程, 包括设备操作、
模具安装、材 料准备等
安全操作规程: 确保操作安全, 包括设备安全、 模具安全、材
料安全等
质量控制规程: 确保产品质量, 包括尺寸精度、 表面质量、材
料性能等
设计图纸和说明书编制
设计图纸:包括模具结构图、零件图、装配图等 说明书编制:包括设计目的、设计原理、设计过程、设计结果等 设计图纸和说明书的格式要求:符合国家标准或行业标准 设计图纸和说明书的审核:由专业人员进行审核,确保设计质量和准确性
工装选择: 根据冲压 工艺要求, 选择合适 的模具和 工装
模具设计: 考虑模具 的尺寸、 形状、材 料等因素
工装设计: 考虑工装 的尺寸、 形状、材 料等因素
冲压课程设计说明书模板

冲压成型工艺及模具设计课程设计说明书设计题目:姓名:班级:学号:设计时间:指导教师:机械工程系目录一.冲压件工艺性分析 (4)二.冲裁件工艺方案的确定 (4)1.方案种类 (4)2.方案的比较 (4)3.方案的确定 (4)三.主要设计计算 (5)1.排样方式的确定计算 (5)2.冲裁力的计算 (5)3.压力机公称压力的确定 (6)4.冲裁压力中心的确定 (6)5.刃口尺寸的计算 (7)四.模具总体设计 (8)1.模具类型的选择 (8)2.定位方式选择 (8)3.卸料、出件方式的选择 (8)4.导柱、导套位置的确定 (9)五.主要零部件设计 (9)1.工作零件的设计结构 (9)2.定位零件的设计 (9)五.模具总装图 (10)六.冲压设备的选取 (11)七.模具零件加工工艺 (11)八.模具的装配 (13)1.上模装配 (13)2.下模装配 (13)一.冲压件工艺性分析此工件既有冲孔,又有落料两个工序。
材料为20钢、t=1.8mm,具有良好的冲裁性能,适合冲裁。
工件结构相对简单,有一个直径 7mm的圆孔。
此工件满足冲裁的加工要求,孔与边缘之间的最小壁厚大于3mm。
工件的尺寸落料按IT12级,冲孔按IT11级计算。
尺寸精度一般,普通冲裁完全能满足。
二.冲裁件工艺方案的确定1.方案种类该工件包括落料、冲孔两个基本工序,可以有以下三种方案。
方案一:先冲孔,后落料。
采用单工序模生产。
方案二:冲孔—落料级进冲压。
采用级进模生产。
方案三:采用落料—冲孔同时进行的复合模生产。
2.方案的比较各方案的特点及比较如下。
方案一:模具结构简单,制造方便,但需要两道工序,两副模具,成本相对较高,生产效率低,且重要的是在第一道工序完成后,进入第二道工序必然会增大误差,使工件精度、质量大打折扣,达不到所需的要求,难以满足生产需要。
故而不选此案。
方案二:级进模是一种多工位、效率高的加工方法。
但级进模轮廓尺寸较大,制造复杂,成本较高。
冲压工艺及模具课程设计说明书(冲孔模)(终稿前稿)

储油油柜端盖冲压工艺及模具课程设计说明书(冲孔模)(终稿前稿)目录设计任务书及零件图 (2)绪论 (4)第一章设计要求 (7)第二章零件工艺性分析 (8)第三章冲压零件工艺方案的确定 (9)第四章工艺参数计算 (10)第五章模具的总体设计及装配 (15)第六章模具的动作过程和操作要求 (18)总结 (19)设计参考文献 (20)设计任务书及零件图任务书专业班级:材料成型及控制工程xxxx设计人:xxx设计题目:储油油柜端盖冲压工艺及模具设计设计参数:1。
零件尺寸如产品图所示。
2。
大批量生产.设计要求:1。
确立合理的工艺流程。
2。
保证材料的利用率及工件的精度3.如原产品设计不合理或工艺性差可提出修改方案.4。
保证模具的实用性和经济性.设计时间:X年X月X日——X年X月X日设计人:xxxx指导老师:xxx零件图如下图所示绪论改革开放以来,随着国民经济的高速发展,市场对模具的需求量不断增长。
近年来,模具工业一直以15%左右的增长速度快速发展,模具工业企业的所有制成分也发生了巨大变化,除了国有专业模具厂外,集体、合资、独资和私营也得到了快速发展。
浙江宁波和黄岩地区的“模具之乡”;广东一些大集团公司和迅速崛起的乡镇企业,科龙、美的、康佳等集团纷纷建立了自己的模具制造中心;中外合资和外商独资的模具企业现已有几千家。
近年许多模具企业加大了用于技术进步的投资力度,将技术进步视为企业发展的重要动力。
一些国内模具企业已普及了二维CAD,并陆续开始使用UG、Pro/Engineer、I-DEAS、Euclid-IS等国际通用软件,个别厂家还引进了Moldflow、C—Flow、DYNAFORM、Optris和MAGMASOFT等CAE软件,并成功应用于冲压模的设计中。
以汽车覆盖件模具为代表的大型冲压模具的制造技术已取得很大进步,东风汽车公司模具厂、一汽模具中心等模具厂家已能生产部分轿车覆盖件模具。
此外,许多研究机构和大专院校开展模具技术的研究和开发.经过多年的努力,在模具CAD/CAE/CAM技术方面取得了显著进步;在提高模具质量和缩短模具设计制造周期等方面做出了贡献。
- 1、下载文档前请自行甄别文档内容的完整性,平台不提供额外的编辑、内容补充、找答案等附加服务。
- 2、"仅部分预览"的文档,不可在线预览部分如存在完整性等问题,可反馈申请退款(可完整预览的文档不适用该条件!)。
- 3、如文档侵犯您的权益,请联系客服反馈,我们会尽快为您处理(人工客服工作时间:9:00-18:30)。
《冲压工艺与模具设计》课程设计说明书设计题目柴油机滤清器外壳底孔冲压单工序模设计系别______________专业班级______________学生姓名______________学号______________指导教师______________日期______________目录一、零件说明。
3二、零件工艺性分析。
41、材料分析。
42、结构分析。
43、精度分析。
4三、工艺方案确定。
4四、压力中心计算。
5五、冲裁力、卸料力、推件力、顶件力及总压力的计算。
5六、冲裁凸凹模刃口尺寸计算。
6七、其他主要零件的设计。
71、凹模设计。
72、凸模设计。
83、模架的选择。
94、卸料板的设计。
105、垫板的设计。
116、定位板的设计。
127、凸模固定板的设计。
128、弹簧的选用。
13八、压力机的选择。
13九、模柄的选用。
14十、紧固零件的选择。
14十一、各零部件的材料及要求。
15十二、该模具设计的优缺点。
15十三、心得体会。
15十四、参考文献。
17一、零件说明制件如下图所示:该制件名称为柴油滤清器外壳,其技术要求为:1,未注尺寸公差按GB/T15505的m级;2,毛刺小于0.15;3,质件要求平整,不允许有拉裂、起皱的现象;4,中批量生产;材料:08F,t=1.5mm设计任务:冲出滤清器外壳底部的孔。
二、零件工艺性分析1、材料分析(摘自GB/T 699-1999)该制件材料为08F,属于优质碳素结构钢,强度、硬度低,塑性极好,深冲压、深拉延性好,冷加工性、焊接性好。
成分偏析倾向大,时效敏感性大,故冷加工时,可采用消除应力热处理或水韧处理,防止冷加工断裂。
化学成分(%):C:0.05~0.11,Si≦0.03,Mn:0.25~0.50,Cr≦0.10,Ni≦0.30,Ca≦0.25力学性能:抗剪强度b 为270~340MPa,抗拉强度σb不小于300MPa,屈服强度σs 为180MPa,断面收缩率60%,伸长率不小于35%。
2、结构分析该零件为圆筒形件,其底部有一孔,为本次设计内容。
该孔的尺寸为φ14.5mm,满足冲裁最小孔径dmin≥1.0t=1.5mm的要求。
孔距已拉伸边之间的最小孔边距为9.3,满足冲裁最小孔边距lmin≥1.5t2.25mm的要求。
所以,该零件的结构满足冲裁要求。
3、精度分析图示零件未标注尺寸公差要求,按GB/T15055的m级可查得孔的尺寸公差为±0.40mm,普通冲裁可以达到零件的精度要求。
由以上分析可知,该零件的冲裁性能好,冲裁加工能够达到设计要求。
三、工艺方案确定该零件的工序有五道,有:落料、一次拉深、二次拉深、三次拉深、冲孔。
其工艺路线有两条:方案一:落料、一次拉深、二次拉深、三次拉深、冲孔方案二:落料、冲孔、一次拉深、二次拉深、三次拉深由于拉深件上所有的孔,均应安排落料而后进行冲孔,以防落料时大的变形力使孔边缘变形,所以采取方案一。
四、压力中心计算模具压力中心是指冲压时各个冲压部分冲压力合力的作用点。
为了确保压力机和模具正常工作,应使冲模的压力中心与压力机滑块的中心相重合。
对于带有模柄的冲压模,压力中心应通过模柄的轴心线。
否则会使冲模和压力机滑块产生偏心载荷,使滑块和导轨之间产生过大的磨损,模具导向零件加速磨损,降低模具和压力机的使用寿命。
冲模的压力中心,可按下述原则来确定:(1)对称形状的单个冲裁件,冲模的压力中心就是冲裁件的几何中心。
冲裁直线段时,其压力中心位于直线段的中点。
(2)工件形状相同且分布位置对称时,冲模的压力中心与零件的对称中心相重合。
(3)冲裁形状复杂的零件或多凸模的零件时,其压力中心可以通过解析计算法求出。
现在需要冲孔的零件是一个筒状件,在其底部正中心需要冲孔,所以其压力中心就是其几何中心。
五、冲裁力、卸料力、推件力、顶件力及总压力的计算计算冲裁力的目的在于合理的选用压力机和设计模具。
冲裁力是指冲裁过程中的最大剪切抵抗力。
它是随着凸模切入材料的深度而变化的,当材料达到了剪切强度时,便产生裂纹且材料相互分离,此时的冲裁力是最大值。
选择压力机就是按冲裁力最大力计算。
冲裁后,由于板料的弹性恢复,使零件(或废料)仍梗塞在凹模洞口内,需要把零件(或废料)从凹模洞口推出或顶出。
把从凹模洞口顺冲裁方向推出的力称推件力Ft;把逆冲裁方向从凹模洞口顶出的力称顶件力F d。
同样,由于冲裁后板料的弹性恢复,使废料(或零件)紧卡住凸模,需要把这废料(或零件)从凸模上卸下来的力称卸料力Fx。
此处所设计的模具为冲孔模,通过卸料板将卡在凸模上的零件卸下来,有卸料力存在。
采用的凹模刃口为阶梯式,在冲裁是会有废料卡在凹模中,又需要推件力。
由于所冲完的废料是直接从凹模落下,所以不需要在凹模下设置顶料装置,故不存在顶料力。
查参考文献2表2-86得08F的抗剪强度τb =220~310MPa,取τb=300MPa,查参考文献6表3-11得Kx=0.04-0.05mm,取0.045mm,Kt=0.055mm。
查参考文献2表4-2,得冲裁刃口高度h﹥8~10mm,取h=10mm。
F= KLtτb=1.3×3.14×14.5×1.5×300=26.635kNFx=KxF=0.045×26.635=1.199KNn=h/t=10/1.5=6件Ft=nKtF=6×0.055×26.635=8.790KNF=F+Fx+Ft=36.624KNZ六、冲裁凸凹模刃口尺寸计算凸模和凹模的刃口尺寸和公差,直接影响冲裁件的尺寸精度。
模具的合理间隙也靠凸、凹模的刃口尺寸及其公差来保证。
在计算模具刃口尺寸及其制造公差时,应按落料和冲孔两种情况分别进行,其原则如下:(1)落料落料件的光面是因凹模刃口挤切材料产生的,因此其光面尺寸与凹模尺寸相等,故应以凹模尺寸为基准。
又因落料件尺寸会随凹模刃口的磨损而增大,为保证凹模磨损到一定程度仍能冲出合格零件,故落料件凹模基本尺寸应取工件尺寸公差范围内的较小尺寸。
而落料凸模基本尺寸,则按凹模基本尺寸减最小初始间隙。
(2)冲孔孔的光面是凸模刃口挤切材料产生的,因此其光面的孔径与凸模尺寸相等,故应以凸模尺寸为基准。
又因冲孔的尺寸会随着凸模的磨损而减小,故冲孔凸模基本尺寸应取工件孔尺寸公差范围内的较大尺寸。
而冲孔凹模基本尺寸则按凸模基本尺寸加最小初始间隙。
(3)确定冲模刃口制造公差时,应考虑制件的公差要求。
如果对刃口精度要求过高( 即制造公差过小),会使模具制造困难,增加成本,延长生产周期;如果对刃口精度要求过低(即制造公差过大),则生产出来的制件可能不合格,会使模具的寿命降低。
刃口尺寸的计算方法由于模具加工方法不同,凸模与凹模刃口部分尺寸的计算公式与制造公差的标注也不同,刃口尺寸的计算方法可分为两类,一个是凹模与凸模分别加工法,另一个是凹模与凸模配合加工法。
分别加工法是指凸模和凹模分别按图纸标注的尺寸和公差进行加工,冲裁间隙由凸模、凹模刃口尺寸和公差来保证,需要分别标注凸模和凹模刃口尺寸与制造公差(凸模δp、凹模δd)。
其优点是具有互换性,但受到冲裁间隙的限制,它适用于圆形或简单规则形状(方形或矩形)的冲压件。
配作法就是先按设计尺寸制出一个基准件(凸模或凹模),然后根据基准件的实际尺寸按间隙配置另一件。
这种加工方法的特点是模具的间隙由配置保证,工艺比较简单,并且还可适当放大基准件的制造公差,是制造容易。
一般工厂常常采用这种加工方法。
冲孔凸凹模刃口计算查参考文献1表19.1-7得Z m ax=0.240mm Z min=0.132mm,表19.1-9得δp =-0.020mm δd=+0.020mm,表19.1-10得x=0.5冲孔凸模 d p=(d m in﹢x△)0pδ- =14.5020.0-mm冲孔凹模d d=(d p+ Z min)dδ+0=14.632020.0+mm校核间隙|δp |+ |δd |=(0.02+0.02)mm=0.04mm﹤Znax -ZMIN﹦(0.240-0.132)﹦0.108mm,故符合条件。
七、其他主要零件的设计1、凹模设计常见凹模的结构形式有筒带式、锥孔式、阶梯式、过渡圆锥台式以及低硬度凹模等。
筒带式凹模的优点是刃口强度高,刃磨后凹模工作尺寸不增大,适合于冲裁形状复杂、尺寸精度要求比较高的冲裁件凹模选用。
锥孔式凹模的优点是凹模洞口内集料少,洞壁承受来自冲裁件或废料的胀力和摩擦力大为减小,因而卸料力大幅度减少。
然而,此种刃口强度比较低,刃磨后凹模工作尺寸略有增大,故适合于冲裁件形状简单、尺寸精度为IT10~IT12级,板料厚度较薄、生产批量不大的冲裁件的凹模选用。
阶梯式凹模刃口厚度h较大,对顶件器导向性好,适合于向上推件的凹模选用。
其缺点是工作时顶件器和冲裁件均频繁的与刃口壁摩擦,从而导致刃口尺寸增大。
过渡圆锥台阶式凹模优点是可增强刃口强度,漏料部位呈圆形又使得凹模制造方便,这种凹模结构形式主要适合于当冲裁尺寸小于5mm时的圆形冲裁件凹模使用。
低硬度凹模的硬度一般为40HRC左右,适合于冲裁软而薄的金属和非金属材料的凹模选用。
在这里选用阶梯式凹模。
当材料厚度t=1.5mm时,查宛强表2-3得K=0.18凹模厚度H=Kb=0.18×75=13.5mm 取H=15mm凹模壁厚C≥﹙1.5-2﹚ H=2H=30mm 取C=35mm凹模刃口高度h取10mm则凹模外形尺寸=75+3+35+35=148mm2、凸模设计凸模是以外形为工作表面的零件,是冲模中直接成形冲压件的凸形工作零件。
冷冲模的凸模结构主要包含两部分,即工作部分和安装部分。
工作部分是直接完成冲压加工的部位,安装部分是通过固定板安装在模座上。
通常凸模都设计为整体式。
常用的标准圆凸模主要有三种:A型圆凸模、B型圆凸模、快换圆凸模。
A型圆凸模刚性较好,直径尺寸范围为1.1~30.2mm,材料一般选用9Mn2V、Cr12MoV、Cr12、T10A、Cr6WV等。
B型圆凸模适用于外形尺寸较大的时候,直径尺寸范围为3.0~30.2mm,材料与A型圆凸模相同。
快换圆凸模是指只用简单工具即可实现快速装卸和更换的圆凸模。
它与A型和B型圆凸模相比,,一是没有头部,二是固定按h6级制造。
在此选用A型圆凸模,其具体尺寸如下:凸模长度=固定板+已压缩弹簧+卸料板+料厚+进入深度=20+34+133.5+1.5+0.5=189.5mm凸模头部:直径22mm 长度6mm凸模杆部:直径18mm 长度20-6+34=48mm 与固定板按H7/m6配合凸模工作部分:21+4+110+0.5=135.5mm3、模架的选择中间配置的两导柱的导向直径一般不相等,这样可以避免合模时上模误装方向而损坏凹模刃口。