超声振动钻削机构设计
机械机床毕业设计85超声深孔钻床设计
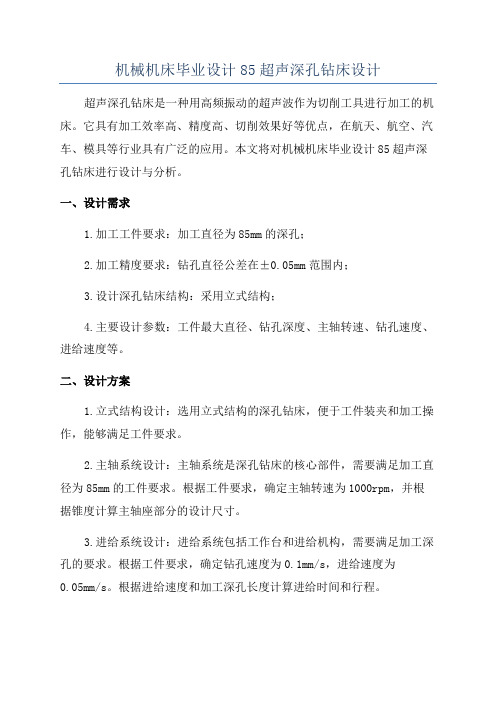
机械机床毕业设计85超声深孔钻床设计超声深孔钻床是一种用高频振动的超声波作为切削工具进行加工的机床。
它具有加工效率高、精度高、切削效果好等优点,在航天、航空、汽车、模具等行业具有广泛的应用。
本文将对机械机床毕业设计85超声深孔钻床进行设计与分析。
一、设计需求1.加工工件要求:加工直径为85mm的深孔;2.加工精度要求:钻孔直径公差在±0.05mm范围内;3.设计深孔钻床结构:采用立式结构;4.主要设计参数:工件最大直径、钻孔深度、主轴转速、钻孔速度、进给速度等。
二、设计方案1.立式结构设计:选用立式结构的深孔钻床,便于工件装夹和加工操作,能够满足工件要求。
2.主轴系统设计:主轴系统是深孔钻床的核心部件,需要满足加工直径为85mm的工件要求。
根据工件要求,确定主轴转速为1000rpm,并根据锥度计算主轴座部分的设计尺寸。
3.进给系统设计:进给系统包括工作台和进给机构,需要满足加工深孔的要求。
根据工件要求,确定钻孔速度为0.1mm/s,进给速度为0.05mm/s。
根据进给速度和加工深孔长度计算进给时间和行程。
4.冷却系统设计:深孔钻床在加工过程中会产生大量的热量,需要冷却系统进行冷却。
设计采用冷却液循环系统,保证工件和刀具的冷却。
5.安全系统设计:在深孔钻床设计过程中,需要考虑安全问题。
设计安装限位开关和急停开关,确保在紧急情况下能够及时停机。
三、设计分析通过以上设计方案的分析,深孔钻床能够满足加工85mm直径深孔的要求。
主轴系统保证了主轴的稳定性和刚性,进给系统保证了钻孔的速度和进给的准确性,冷却系统保证了加工过程中的散热,安全系统保证了操作的安全性。
此外,还需要进行结构强度和刚度的分析,以确保深孔钻床在加工过程中不会发生变形和振动。
通过有限元分析和实验验证,可以对深孔钻床的结构进行优化,提高其加工精度和刚性。
四、总结本文对机械机床毕业设计85超声深孔钻床进行了设计与分析。
通过立式结构、主轴系统、进给系统、冷却系统和安全系统的设计,确保深孔钻床能够满足加工85mm直径深孔的要求。
超声磨削装置结构设计
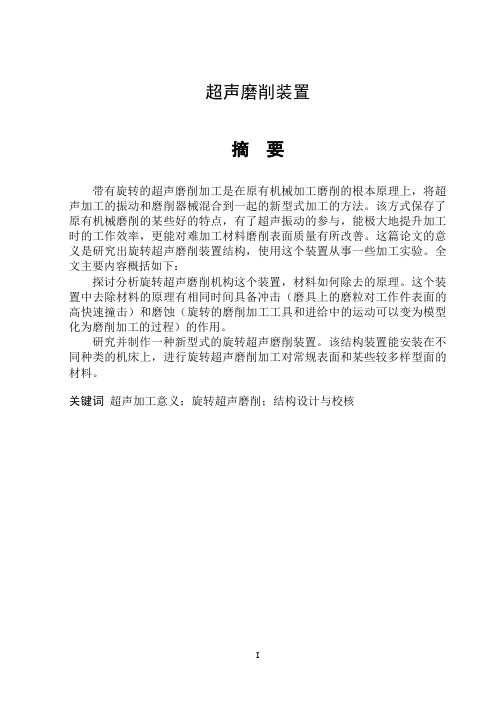
超声磨削装置摘要带有旋转的超声磨削加工是在原有机械加工磨削的根本原理上,将超声加工的振动和磨削器械混合到一起的新型式加工的方法。
该方式保存了原有机械磨削的某些好的特点,有了超声振动的参与,能极大地提升加工时的工作效率,更能对难加工材料磨削表面质量有所改善。
这篇论文的意义是研究出旋转超声磨削装置结构,使用这个装置从事一些加工实验。
全文主要内容概括如下:探讨分析旋转超声磨削机构这个装置,材料如何除去的原理。
这个装置中去除材料的原理有相同时间具备冲击(磨具上的磨粒对工作件表面的高快速撞击)和磨蚀(旋转的磨削加工工具和进给中的运动可以变为模型化为磨削加工的过程)的作用。
研究并制作一种新型式的旋转超声磨削装置。
该结构装置能安装在不同种类的机床上,进行旋转超声磨削加工对常规表面和某些较多样型面的材料。
关键词超声加工意义;旋转超声磨削;结构设计与校核Ultrasonic grinding deviceAbstractRotary ultrasonic grinding is a new machining method that combines ultrasonic vibration with grinding tools in the basic principle of the original mechanical grinding. This method saves some of the good features of the original mechanical grinding. With the participation of ultrasonic vibration, it can greatly improve the working efficiency and improve the quality of the grinding surface of difficult to machine materials. The significance of this paper is to study the structure of a rotating ultrasonic grinding device and to do some machining experiments with this device. The main contents are summarized as follows:The principle of how to remove material of rotary ultrasonic grinding mechanism is discussed. The material removal principle of this device in the same time (with the impact of abrasive abrasive on the work piece surface high impact and abrasion (fast) rotating grinding tool and feed movement in can be modeled as process of grinding) role.A new type of rotary ultrasonic grinding device is studied and fabricated. The structure can be installed on different kinds of machine tools, and rotary ultrasonic grinding is applied to conventional surfaces and some kinds of materials with various shapes.Keywords Ultrasound processing significance,Rotate ultrasound grind,Structure design and checking目录摘要 (I)Abstract (II)第1章绪论 (1)1.1 超声的发展史 (1)1.1.1 超声发展简介 (1)1.1.2 国外发展 (1)1.1.3 国内发展 (2)1.2 超声加工的原理及特点 (3)1.2.1 传统超声加工 (3)1.2.2 旋转超声加工 (4)1.3 超声加工陶瓷的意义及前景 (5)1.4 本章小节 (5)第2章工程陶瓷材料的使用价值及加工技术 (6)2.1 结构陶瓷 (6)2.2 陶瓷基本复合材料 (7)2.3 功能陶瓷 (8)2.4 本章小结 (10)第3章装超声磨削装置的结构设计 (11)3.1 超声加工设备及其组成部分 (11)3.2 初步结构设计 (11)3.3 结构的比较 (13)3.4 最后结构的确定 (16)3.5 本章小结 (17)第4章装置中的各部件的设计及校核 (18)4.1装电机的计算与选择 (18)4.2 变幅杆的设计 (20)4.3 压电陶瓷的选择 (22)4.4轴强度的较核 (23)4.5 键的校核 (25)4.6 本章小结 (26)第5章超声磨削与环境保护 (27)5.1 目前我国环境现状 (27)5.2 超声加工对环境影响 (27)5.3 本章小结 (28)结论 (29)致谢 (30)参考文献 (31)附录A (32)附录B (38)第1章绪论1.1超声的发展史1.1.1超声发展简介近年来科学水平的快速提升和飞机火箭等加工的需要,难加工材料使用越来越多如1Cr18Ni9、复合材料、工程陶瓷等,它们的特殊性质使其制造加工有些费力。
超声轴向振动钻削机构的设计与研究

类 型 。选择 变 幅杆 时一 般 可
从 三 方 面 来 考 虑 , 是 根 据 一
振 动 切 削 的具 体 要 求 , 别 特 是放 大倍 数 , 作 稳 定 性 、 工 切
削 用量等 来 选 择 合适 的变 幅
杆; 二是设 计 简单 , 获得 较 可
准 确 的设 计 数 据 ; 是 加 工 三 制 造容 易 。此 设 计 选择 了 比 图2超声圆 变幅杆 锥形 较 容易加 工 的 圆 锥 型 变 幅 杆 ( 2) 材 料 为 调 质 4 图 , 5
E et cl n ier g C a gh 4 00, H l r a E gne n , h nzi 6 0 C N) c i i 0
Ab t a t s r c :Ba e n vb ain c t n h oy,h spa e e eo d a x a i r t n d lig me h n s , n d s d o ir to ut g t e r t i p rd v lpe n a i vb ai r l c a im a d ma e i l o i n d li x e i n so h tras wh c s d f c l t r c s n t e v  ̄ia c i i g c ne .Th i ng e p rme t n t e mae l ih i if u t o p o e s i h e c lma h n n e tr rl i i e r s l h we ha c mp r d wih t e ta iin ld l n e h oo y,uta o i i r t n d li g h d a e ut s o d t t, o a e t h r dto a r l g t c n lg s i i l s n cv b a i r ln a r o i b te r c s e u t , ih c n i r v h r c s i g q a i n fii n y o malda trd e etr p o e sr s ls wh c a mp o e t e p o e sn u l y a d efce c fa s l imee e p t h l n k ta h e e t rl de p h ls o h tra swh c sd f c l t o e s oe a d ma e i c iv o d l e o e n t e mae l ih i i u t o pr c s . i i i Ke ywo d r s:Ul a o i b ai n; b a in Drli g; malDime e e l t s n c Vir to Vi rto i ln S l r a trDe p Hoe
超声磨削装置设计

超声磨削装置设计设计超声磨削装置超声磨削是目前工业加工领域中一种先进的磨削技术。
它利用超声波振动来实现高效、精确的磨削和研磨效果。
超声磨削具有磨削效率高、加工精度高、加工品质好等优点,因此被广泛应用于航空、航天、汽车、电子、机械制造等领域。
在设计超声磨削装置时,需要考虑以下几个关键因素:超声振动源、工作台、夹具、砂轮和磨削液。
首先,超声振动源是超声磨削装置的核心部件。
它产生高频振动,并将其传递给工作台和夹具,从而驱动砂轮进行磨削。
超声振动源的设计应着重考虑振幅、频率和功率等参数。
合理的超声振动源设计可以提高磨削效率和精度。
其次,工作台是超声磨削装置的支撑组件。
它用于承载工件,并提供与砂轮的运动配合。
工作台的设计应考虑到承载能力、运动精度和稳定性等因素。
合理的工作台设计可以提高磨削精度和稳定性。
夹具是用于夹紧工件的部件。
在夹具设计时,需要考虑夹紧力的大小、均匀程度以及对工件的保护。
合理的夹具设计可以提高工件的固定性和稳定性。
砂轮是进行磨削的工具。
其设计应考虑磨削效果、加工压力、磨削速度等因素。
合理的砂轮设计可以提高磨削效率和加工精度。
最后,磨削液在超声磨削中起到冷却、润滑和清洗的作用。
磨削液的设计应考虑到冷却效果、清洗效果、环保性等因素。
合理的磨削液设计可以提高磨削质量和工作环境。
综上所述,超声磨削装置的设计需要充分考虑超声振动源、工作台、夹具、砂轮和磨削液等关键因素。
通过合理的设计,可以提高超声磨削的效率、精度和质量,满足不同行业的加工需求。
超声波振动钻床主轴设计

超声波振动钻床主轴设计运用轴向超声波振动钻削技术加工微小孔(0.5mm以下),可以延长钻头寿命,提高孔的精度和孔壁表面质量,减小钻削出口毛刺,具有优良的工艺效果。
本文介绍了一种超声波振动钻床主轴设计方法,采用该设计方案,无须改动机床其它结构,只以超声波振动主轴替换钻床原有主轴,即可完成对机床的改装,结构紧凑,使用方便。
1.键槽2.传动轴3.后匹配块4、6.压电陶瓷5.电极7.前匹配块8.变幅杆9.集流环10.弹性卡爪11.圆套主轴结构简图1主轴结构设计普通钻床主轴下端安装钻夹,应能完成回转运动和轴向进给运动,超声波振动钻床主轴除应完成以上运动外,还需具备轴向超声波振动功能。
超声波振动主轴中的振动子可采用夹芯式压电陶瓷换能器(图中CDE段),其电声转换效率可达90%左右,结构十分紧凑。
它由一对压电陶瓷片、电极和前、后匹配块组成,由于用于微小孔加工的超声波换能器功率较小,发热量相对较少,可不设专门的冷却系统。
前匹配块与变幅杆可做成一体。
普通钻夹头结构复杂,质量较大,容易破坏主轴系统谐振状态,导致钻头振幅大幅度减小。
所以在变幅杆末端设计结构简单的弹性夹头,弹性夹头带有四个弹性卡爪,用于装夹钻头。
在变幅杆小端上装有集流环,用于传送换能器工作所需的电流。
后匹配块与阶梯传动轴作成一体,传动轴小端开有键槽,与钻床皮带轮作滑动配合,以便带动主轴系统回转。
在变幅杆小端和传动轴小端分别装有一个向心球轴承,用于支承安装主轴,轴承外圈与钻床主轴套筒过渡配合,带有齿槽的套筒可带动主轴进行轴向进给。
2换能器及变幅杆设计原理把超声频变化的电压加在压电陶瓷的两极上,其厚度将随电压的变化而变化,于是产生了纵向超声波振动,该纵向振动波将向前后两个方向传播。
当传播波的介质改变时,在界面上将发生波的折射和反射,反射量的比率取决于两种介质的密度比。
密度比越大,反射量越多。
由于钢与空气的密度比非常大,可以认为传播到主轴两端的波全部被反射回来。
超声波加工机床的结构设计与动力系统优化

超声波加工机床的结构设计与动力系统优化一、引言超声波加工机床是一种利用超声波振动进行加工的先进设备。
它具有精度高、效率高、能耗低等优点,因此在现代工业中得到了广泛应用。
本文将对超声波加工机床的结构设计与动力系统进行分析与优化,旨在进一步提高其加工质量和性能。
二、超声波加工机床的结构设计1. 传动系统设计超声波加工机床的传动系统是保证加工过程中能量传递和工具运动的关键部分。
采用传动系统可以将电机的转速转换为工作台或工具的运动速度。
传动系统的设计应保证其结构紧凑、刚性良好、传动效率高和稳定性强。
2. 悬挂系统设计超声波加工机床的悬挂系统用于支撑工具和工作台,使其在超声波振动下能够稳定运动。
悬挂系统应具备足够的刚性和稳定性,能够有效抵抗振动的影响。
同时,悬挂系统还应具备一定的调节能力,以适应不同加工任务的要求。
3. 结构刚度设计超声波加工机床在加工过程中需要承受较大的力和振动。
因此,其结构刚度设计至关重要。
合理的结构刚度设计可以提高加工精度,减小振动的影响,并降低设备的故障率和维修成本。
结构刚度设计需要考虑材料的选择、结构的合理性和加工工艺等因素。
三、超声波加工机床的动力系统优化1. 电机选择与匹配超声波加工机床的电机是动力系统的核心部分,对其性能和稳定性有重要影响。
电机的选择应根据加工机床的负载要求、工作条件和精度要求等因素进行选择。
同时,电机的匹配应保证其输出扭矩和速度与机床需求相匹配,以提高加工效率和精度。
2. 控制系统设计与优化超声波加工机床的控制系统对于保证加工过程的稳定性和精度至关重要。
控制系统应具备快速响应、精准调整和稳定运行的能力。
通过优化控制算法和调整控制参数,可以进一步提高加工机床的稳定性和控制精度。
3. 能源系统优化超声波加工机床的能源系统包括供电系统和能量转换系统两部分。
供电系统应能够稳定地为机床提供所需电能,以保证其正常运行。
能量转换系统应具备高效转换能量的能力,以提高能源利用率和机床的工作效率。
超声磨削装置结构设计

超声磨削装置结构设计1.振动源:超声磨削装置的核心是振动源,它产生高频的超声波振动。
振动源通常由发生器、转换器和振动工具组成。
发生器产生高频电能,通过转换器将电能转换成机械振动,然后通过振动工具传递到被加工的材料上。
2.振动工具:振动工具是超声磨削装置中的重要部件,它负责将振动源产生的超声波振动传递到被加工材料上。
振动工具通常采用金属材料制成,具有特定的形状和表面特征,例如凸轮形、圆柱形等。
振动工具的结构设计需要考虑振动传递的效率和加工性能。
3.加工台:加工台是超声磨削装置上用于支撑和夹持被加工材料的平台。
加工台通常由金属材料制成,具有坚固的结构和稳定的工作平面。
加工台的结构设计应考虑材料夹持的可靠性和加工精度的要求。
4.控制系统:超声磨削装置需要一个控制系统来控制振动源的工作参数,例如振动频率、振幅和工作时间等。
控制系统通常包括电子控制器和人机界面。
电子控制器负责控制振动源的工作状态,人机界面提供操作界面和参数设置功能。
5.辅助装置:为了提高超声磨削装置的效率和加工质量,常常需要一些辅助装置。
例如冷却系统可以冷却加工过程中产生的热量,减少工件的变形和表面质量的损坏;收集系统可以收集加工过程中产生的切削屑和废料,便于清理和回收利用。
1.功能需求:根据实际应用需求确定超声磨削装置的功能。
例如,不同的材料(金属、陶瓷、玻璃等)具有不同的物理性质和加工要求,需要针对性地设计不同的结构和参数。
2.材料选择:超声磨削装置的结构材料应具有高强度、高刚度和良好的耐磨性能,以满足高频振动的工作要求。
3.结构设计:超声磨削装置的结构设计应紧凑合理,以提高工作效率和加工精度。
同时,还需要考虑装置的稳定性和可靠性,以确保长时间连续工作的可行性。
4.参数调节:超声磨削装置应具有调节振动频率、振幅和工作时间等参数的功能,以适应不同材料和加工要求。
5.安全性设计:超声磨削装置的设计还需要考虑安全性,例如添加安全保护装置,防止误操作和意外伤害。
超声振动钻削装置结构设计研究.docx

超声振动钻削装置结构设计研究1引言本文所涉及的超声振动钻削机构的设计,采用现代设计方法和理念,即系统化设计方法来建立机构的总体布局和设计各主要部件并在现代制造工程设计方法下获得最佳原理方案。
钻削机床一般是指以实现钻孔加工为主的机床,所具有的运动相对其它机床来说比较简单,最主要的特点是在工件固定不动的情况下刀具做旋转和进给运动来实现加工,随着传动部件的发展和改进,钻削的加工质量和效率都有所提高,得到最广泛应用的是立式钻床和摇臂钻床。
立式钻床的主轴转速和进给量具有较大的变化范围,这使得其可以加工的材料范围也比较广泛,摇臂钻床是针对于立式钻床改进得到的,其主轴箱可在摇臂上左右移动,更加扩大了机床的可加工范围。
结合立式钻床和摇臂钻床的结构有点,进行下一步关于本文装置的设计。
2超声振动钻削机床结构原理分析通过对典型钻削机床结构的了解和深入分析,同时考虑超声振动的独特加工原理所带来的对机床结构的变革,在机构设计理论的基础上,开展超声振动钻削机床的设计的讨论,在机床的运动精度和结构合理性基础上,进行主体结构的原理性分析。
钻削加工虽然从机床运动角度来说相对于其它加工方法较简单,但是钻削加工因其所使用刀具即钻头的结构复杂性,注定了钻削加工原理的复杂性,而这种钻削原理决定了在设计钻削加工机床时要求钻头轴向与工件平面的垂直度保持性以及振动的快速消除等。
超声振动的原理主要是依赖超声波的高频振动转化为机械振动从而实现加工的,而在传统加工原理中振动被认为是对机构不利的,如何有效地利用超声波振动而又保持机构的稳定性是设计机床时需要主要考虑的问题,所以引入了振动加工使得机床的振动抑制和利用面临着考验。
在钻削原理和超声振动原理的综合分析下,结合钻削机床固有的特点,同时考虑机构的工艺可能性,结构简单性,易于制造和装配,操作方便等因素用来指导机构的总体设计。
3超声振动钻削系统的总体设计由上面钻削原理,超声振动原理和钻削机构运动原理,确定本文所要设计的超声振动钻削机构所应该满足的要求和设计要点如下:结构简单且灵活性强以适应实验的多样性和便于改进,装配和布局合理,影响工件加工的参数有较大变化范围,便于检测系统的安装和测试,部件装配的稳定性和能量传递的完整性,主轴垂直度保持几个方面。
- 1、下载文档前请自行甄别文档内容的完整性,平台不提供额外的编辑、内容补充、找答案等附加服务。
- 2、"仅部分预览"的文档,不可在线预览部分如存在完整性等问题,可反馈申请退款(可完整预览的文档不适用该条件!)。
- 3、如文档侵犯您的权益,请联系客服反馈,我们会尽快为您处理(人工客服工作时间:9:00-18:30)。
目次1.绪论 (3)1.1.引言 (3)1.2.课题的来源及其研究的内容 (3)1.3.超声振动钻削机构概述 (4)1.4.超声波的产生及其特性 (5)1.5.超声波的加工原理及特点 (6)1.6.超声波加工发展概况 (7)2.超声振动钻削系统的结构设计 (9)2.1.引言 (9)2.2.超声振动钻削系统的结构设计 (9)3.超声振动钻削机构声学系统的设计 (13)3.1.超声波发生器与换能器 (13)3.2.超声变幅杆的设计 (14)4.钻头夹具的设计与连接 (30)4.1.钻头夹具的选取与设计 (30)4.2.钻头夹具与变幅杆的连接 (31)5.其他零部件的设计 (32)5.1.其他零部件的设计 (32)6.校核与计算 (34)6.1.轴承的计算 (34)6.2.内轴套的校核 (34)设计总结 (36)致谢 (39)参考文献 (40)第一章绪论1.1引言自上世纪50年代以来,特别是近一二十年,由于材料科学、高新技术的发展和激烈的市场竞争、发展尖端国防及科学研究的需要,不仅新产品更新换代日益加快,而且要求产品具有很高的强度重量和性能价格比。
为此各种新材料、新结构、形状复杂的精密机械零件大量涌现,这些都对机械制造业提出了一系列迫切需要解决的新问题。
因此,一些材料采用传统加工方法十分困难,甚至无法加工,特种加工便应运而生。
超声波加工是特种加工的一种,它始于1927年,至今已有70多年的发展历史。
它是利用超声振动的工具在有磨料的液体介质中,产生磨料的冲击、抛磨、液压冲击以及由此产生的气蚀作用来去除材料已达到加工目的的加工方法。
提到超声波加工,不能不提到超声波加工设备——机床。
多年来,人们不断改进超声波加工机床,通过不断努力,使其取得了很大的进展,超声波加工效率提高了数倍,但它还是有很多的缺陷需要改进,本文将对超声波加工机提出一种新概念。
1.2课题来源及其研究的内容随着科学技术的迅速发展和激烈的市场竞争,加快了产品更新换代的步伐,为此,各种新材料、新结构、高要求的零部件大量涌现,这对机械制造业提出了新的要求。
解决各种难切削材料尤其是硬脆材料及复合材料的加工问题成了一个急待解决的问题。
传统加工方法难度大、质量差、特种加工也就应运而生。
特种加工包括电火花加工、超声波加工以及激光加工等。
其中,超声波加工适合于加工各种硬脆材料,尤其是加工难以加工的材料,如玻璃、陶瓷、石英、金刚石、半导体等材料。
因此在现在的加工中得到了广泛的应用。
但是,超声波机床具有体积大、成本高的缺陷。
还有加工的尺寸受到限制。
为此,本文提出了一种新型的旋转超声复合钻削机构,它的具体结构将会在第二章中得到具体阐述。
该新型结构可以作为一种机床附件,具有体积小、结构简单、成本低、可技工大型工件的优点,这对超声波加工以及机床的发展具有十分重要的意义。
课题研究的内容有以下六点:1、超声加工机床进行分析,通过和普通机床的比较,研究一种新的结构,使其可以安装在普通机床上便可进行旋转超声加工。
2、变幅杆是超声波机床振动系统的重要组成部分,本文将从声学角度和波动方程角度来探讨变幅杆的设计和刀具的设计问题。
3、对变.隔杆进行结构分析和动力学分析,分析其最大应力和振幅的变化曲线。
4、为满足不同用户的要求,以超声电源功率250W的磨削头结构为基型产品,对其进行系列化设计。
5、通过实验验证该结构的可行性,并且对其进行超声加工的效率和质量进行研究,以验证其是否达到专用机床的要求。
6、对本课题的内容做出总结和展望。
1.3 超声振动钻削机构概述超声振动钻削是近代出现的一种特殊的切削加工的方法,是对难加工材料或难加工工序进行加工的有效方法之一。
它是在传统的钻削过程中给钻头(或工件)加上某种有规律的、可控的高频振动,在切削参数优化的条件下,以达到改善钻削性能的一种本质的新颖的加工方法。
即超声振动钻削是将振动驱动装置的高频信号,通过一定的转换放大装置后变为机械位移附加到钻头或工件上,使之工具或工件以振动频率f,振幅a,在钻削方向上按正旋波形作强迫振动,为了得到良好的效果,要求切削速度V与振动参数f,a之间 2的条件,以形成的一种脉冲式的变速断续的切削过程。
因此,欲保持V<af完成超声振动钻削工艺,就需要设计一套声振系统:振源――放大系统――连接装置――工具或工件等装置。
具体讲需要设计产生高频信号的超声振动源(即超声波发生器)、将电信号变为机械信号的换能器、为实现工具振动必须放大的变幅杆、连接工具并与之适配的标准夹头及钻削工具等零部件。
工作时,超声波发生器产生的高频电振荡通过换能器变成机械振动,再由变幅杆把这种微小的机械振动加以放大并传递给由标准夹头连接的工具上使工具或工件产生规则的强迫振动并利用这种振动进行钻削加工。
超声振动钻削与普通钻削的区别是在钻孔过程中通过振动装置使钻头与工件之间产生可控的相对运动。
超声振动钻削装置主要有三种形式①轴向振动装置,即振动方向与钻头轴向方向相同的装置。
②扭转振动钻削装置,即振动方向与钻头旋转方向相同的装置。
③复合振动钻削装置,即轴向振动与扭转振动的叠加的装置。
1.4 超声波的产生及其特性声波与光波、电磁波一样,都是因物体在介质中发生振动,介质各点之间存在弹性联系,引起相邻各点的振动从而形成的纵波。
声波是人耳能感受到的一种纵波。
其频率范围是16—16000Hz。
当声波的频率低于16Hz时就叫次声波,高于16000Hz则称为超声波、加工用超声波的频率为16000-25000Hz。
它是由压电晶片(如石英、钦酸钡、错钦酸钡等)的逆压电效应产生的。
如图1一1所示,当压电晶片受到某一规律的压缩和拉伸时(晶片厚薄亦产生规律性变化),在晶片两面产生相同电压变化,称为正压电效应。
反之,把某一规律变化的电压加在压电晶体片两面上,它就作相应机械振动,称为逆压电效应。
当压电晶片受到来自高频(>20kHz)发生器的高频电压作用而发生逆压电效应时,晶片在其厚度方向发生变薄及变厚的振动,晶片周围介质点亦相应振动,这个振动在介质中传播,即形成超声波。
在现在的生产加工中,超声波的应用非常广泛.它具有如下特性:1)超声波可在气体、液体和固体介质中传播,其传播速度与频率、波长、介质密度等有关,2)声波能传递很强的能量。
超声波的作用主要是对其传播方向上的障碍物施加压力。
因此可用压力大小来表示超声波的强度,传播的波动能力越强压力也就越大。
3)超声波会产生反射、干涉和共振现象。
出现波的叠加作用,使弹性杆中某处质点始终不动4)超声波在液体介质中传播时,可在界面上产生强烈的冲击和空化现象,强化了加工过程的进行。
1.5 超声波加工原理及特点超声波加工是利用工具作超声振动,并沿工具头振动方向施加一定压力,通过液体磨料来加工材料。
超声波加工的基本原理是:加工时,超声波发生器通过换能器产生超声波(频率通常为16—25kHz),此波因振幅太小,仅0.005—0.01mm,不能用于加工,需通过变幅杆放大至0.01—0.1 mm,再传给工具。
此时,工具与工件之间充满了液体(水或煤油)与磨料(氧化铝或碳化硅等)混合的悬浮液。
工具以很小的压力压在工件上。
工作液中悬浮的磨粒在工具的超声振动下,以高速不断冲击工件加工表面,使该表面受到很大的压强而产生材料的变形,当应力超过其强度极限时,材料将发生破坏而成粉末状去除。
同时由于悬浮工作液的扰动,促使磨粒以高速抛磨工件的加工表面。
此外,悬浮工作液受工具端部的超声振动而产生的“空化”现象在工件表面形成液体空腔,促使液体渗入被加工材料的缝隙处,而空腔的瞬时闭合又引起强烈的液压冲击,加快了工件材料的机械碎除作用,并有利于加工区域磨料悬浮液的均匀搅拌和磨蚀产物的排除。
磨料悬浮液的循环流动使磨料不断更新,并带走被粉碎下来的材料微粒,工具逐渐渗入到材料中,工具形状便复现在工件上。
因此,超声加工是磨粒在超声振动下的机械冲击和抛磨作用与超声空化作用的综合结果,其中磨粒的连续冲击和抛磨作用是主要的。
1)悬浮液中磨料的不断机械冲击,是超声加工的主要因素,但不仅是这一因索;2)由于工具端部的超声振荡而产生的“空化”现象,令工件表面形成液体空腔,促使液体进入工件缝隙处,空腔的瞬间空化,更会加速磨料对工件表面的破碎作用;3)可以认为,超声加工正是磨料的机械冲击与空化作用的综合结果。
后来,在传统超声波加工的基础上发展了旋转超声波(RUM),它与传统超声波加工不同之处在于:工具在作超声振动的同时附加了旋转运动;工具由金属粉末和人造金刚石或立方氮化硼磨料按一定比例烧结而成;将冷却水而不是磨料一悬浮液输入到工具和工件表面之间。
超声波加工的特点:1)加工对象为各种硬脆材料,如玻璃、陶瓷、人造宝石、半导体等材料,尤其是电加工难以加工的材料。
其原因是超声加工是靠磨料及液体分子的不断冲击、空化作用。
2)加工精度高。
尺寸精度可达0.01—0.02mm,表面粗糙度R可达0.63—a ,被加工面也无组织改变,无残余应力,其原因是其加工靠微小磨粒作0.08m用。
3)工件在加工过程中受力小。
这是因为在加工过程中,磨料运动方向与加工表面垂直与切入方向一致,工件仅受磨料瞬时局部冲击力,不存在横向摩擦之故。
因此,对一于加工薄壁、窄缝及低刚度工件是有利的。
4)可加工出复杂型腔及型面。
其原因是工具可用较软材料制作,故易于制出复杂形状之工具。
基于此,决定了超声加工机床结构简单,易于维护。
5)与电解加工、电火花加工比较,超声波加工效率较低。
1.6 超声波加工发展概况我国超声波加工始于50年代末期,曾掀起一阵群众性的“超声热”,由于超声电源、换能器、声振系统很不成熟,缺乏合理的组织和持续的研究工作,很快就冷了下来。
60年代末,哈尔滨工业大学应用超声车削,加工了一批飞机上的铝制细长轴,取得了良好的切削效果。
1976年,我国再次开展超声加工的试验研究和理论探讨工作。
1983年,机械电子工业部科技司委托《机械工艺师》杂志编辑部在西安召开了我国第一次“振动与切削专题讨论会”,1985年,机械电子工业部第11研究所研制成功旋转超声加工机,在玻璃、陶瓷等硬脆材料的钻孔、套料、端铣、内外圆磨削及螺纹加工中,取得了优异的工艺效果。
80年代后期,天津大学的李天基等人在高速磨削时对磨头施以超声振动,提出了高效的超声磨削复合加工方法,效率比传统的超声加工提高6倍以上,表面质量也有了大幅度提高。
北京装甲兵技术学院提出了一种“超声微振车削”的新工艺、其特点是功率小、振幅小,同样可获得一般振动车削效果。
清华大学王先速等进行了45号钢制成的超声砂带研抛的实验研究。
第二章超声振动系统的结构设计2.1引言超声波加工在硬脆材料及复合材料的加工方面具有其它加工方法无可比拟的优越性,正日益成为加工硬脆材料的重要方法之一。