弹簧表面处理工艺
几种弹簧的表面处理方法

八种弹簧表面处理方法1.弹簧电泳在溶液中在直流电场的作用下,带电荷的树脂向相反的电极移动现象叫电泳,电泳后防腐能力强,可上不同的颜色。
电泳原理:电泳是电泳涂料在阴阳两极,施加于电压作用下,带电荷之涂料离子移动到阴极,并与阴极表面所产生之碱性作用形成不溶解物,沉积于弹簧表面。
电泳表面处理工艺的特点:电泳漆膜具有涂层丰满、均匀、平整、光滑的优点,电泳漆膜的硬度、附着力、耐腐、冲击性能、渗透性能明显优于其它涂装工艺。
2.弹簧电镀化学镍弹簧电镀化学镀镍溶液分为酸性镀液和碱性镀液两大类。
酸性镀比较稳定易于控制,沉积速度较快,镀层中磷的质量分数比较高(2%~11%)。
典型的酸性化学镀镍溶液的组成、工艺及性能见下表。
镀液成分(g/L)及工艺条件硫酸镍次磷酸钠醋酸钠柠檬酸钠乳酸PH温度(℃)沉积速度(μm·-1)h120~3020~25554~580~901022024254.4~4.890~94l0~13镀液温度是影响化学镀镍沉积速度的重要因素之一。
镀液温度低于65℃时,沉积速度很慢。
随着镀液温度的升高,沉积速度加快,但镀层中的含磷量降低。
温度过高或加热不均匀还会引起镀液的自发分解。
3.弹簧化学镀弹簧化学镀是在没有外电流通过的状态下,借助还原剂,通过可控制的氧化还原反应,使镀液中的金属离子还原成金属沉积在弹簧表面的一种涂覆方法,化学镀又称自催化镀。
目前,用化学镀的方法可以获得镍、铜、银等单金属镀层和合金镀层,其中以化学镀镍应用最为普遍。
由于化学镀镍层内含有质量分数为4%~12%的磷,所以化学镀镍也被称之为化学镀镍-磷合金。
化学镀镍层是一种无磁性的非晶态镀层,镀后的硬度比较低(~500HV)。
将化学镀镍层在一定的温度范围加热,非晶态镀镍层会转变为晶态组织,镀层的硬度也随着加热温度的升高而增加。
在加热温度为400℃时,镀层的硬度达到最大值(~1000HV)。
4.弹簧钝化处理钝化处理是化学清洗中最后一个工艺步骤,是关键一步。
弹簧热处理工艺流程
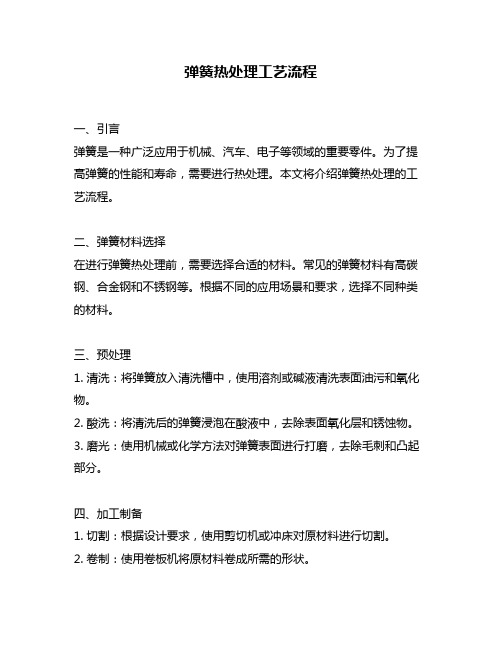
弹簧热处理工艺流程一、引言弹簧是一种广泛应用于机械、汽车、电子等领域的重要零件。
为了提高弹簧的性能和寿命,需要进行热处理。
本文将介绍弹簧热处理的工艺流程。
二、弹簧材料选择在进行弹簧热处理前,需要选择合适的材料。
常见的弹簧材料有高碳钢、合金钢和不锈钢等。
根据不同的应用场景和要求,选择不同种类的材料。
三、预处理1. 清洗:将弹簧放入清洗槽中,使用溶剂或碱液清洗表面油污和氧化物。
2. 酸洗:将清洗后的弹簧浸泡在酸液中,去除表面氧化层和锈蚀物。
3. 磨光:使用机械或化学方法对弹簧表面进行打磨,去除毛刺和凸起部分。
四、加工制备1. 切割:根据设计要求,使用剪切机或冲床对原材料进行切割。
2. 卷制:使用卷板机将原材料卷成所需的形状。
3. 预成形:将卷好的原材料放入预成形机中,进行初步成型。
4. 终成形:将预成形后的弹簧放入终成形机中,进行最终成型。
五、热处理1. 固溶处理:将弹簧放入固溶炉中,加热至固溶温度。
保持一定时间后,快速冷却至室温。
此过程可以消除材料内部的应力和组织不均匀性。
2. 淬火处理:将固溶后的弹簧放入淬火槽中,快速冷却至室温。
此过程可以提高弹簧的硬度和韧性。
3. 回火处理:将淬火后的弹簧放入回火炉中,加热至回火温度。
保持一定时间后,快速冷却至室温。
此过程可以改善弹簧的韧性和塑性。
六、表面处理1. 酸洗:将经过热处理的弹簧浸泡在酸液中,去除表面氧化层和锈蚀物。
2. 磨光:使用机械或化学方法对弹簧表面进行打磨,去除毛刺和凸起部分。
3. 镀层:根据需要,可以对弹簧表面进行镀铬、镀锌等处理,提高其耐腐蚀性。
七、质量检验1. 外观检查:对弹簧的外观进行检查,包括尺寸、形状、表面质量等。
2. 力学性能测试:对弹簧的硬度、韧性等力学性能进行测试。
3. 化学成分分析:对弹簧材料的化学成分进行分析。
八、包装运输将经过质量检验的弹簧进行包装,标注相关信息,并进行运输。
九、总结弹簧热处理是提高弹簧性能和寿命的重要工艺。
不锈钢弹簧的种类及不锈钢弹簧表面处理技术

不锈钢弹簧是化工机械和电子等诸多行业中工作环境要求耐腐蚀,耐温,无磁使用的一款的弹性元件,不锈钢弹簧在受载时能产生较大的弹性变形,把机械功或动能转化为变形能,而卸载后不锈钢弹簧的变形消失并回复原状,将变形能转化为机械功或动能。
不锈钢弹簧按受力性质,不锈钢弹簧可分为拉伸弹簧、压缩弹簧、扭转弹簧和弯曲弹簧,按形状可分为碟形弹簧、环形弹簧、弹簧片、螺旋弹簧、截锥涡卷弹簧以及扭杆弹簧等。
普通圆柱弹簧由于制造简单,且可根据受载情况制成各种型式,结构简单,故应用最广。
弹簧的一般来说应具有高的弹性极限、疲劳极限、冲击韧性及良好的耐热耐腐蚀性能等,常用的材料有参考如上。
常用弹簧丝直径20毫米以下的用冷卷法,不锈钢弹簧在制成后还要进行强压或抛光处理,可提高弹簧的承载能力和表面光洁度。
不锈钢弹簧表面处理技术:第一步给不锈钢弹簧去油污、去氧化皮有三种使用方法:1、把不锈钢弹簧浸入放有用清水稀释的金属清洗剂A(清洗剂A与清水稀释配比为1:1或1:2左右)的塑料容器中,时间以弹簧表面无油污、无氧化皮恢复金属本色为宜,浸泡时间不宜过长,取出用清水洗净。
这样不锈钢弹簧表面就有亚光效果。
2、在超声波设备中清洗剂与清水的配比为1:30左右,时间以弹簧表面无油污、无氧化皮恢复金属本色为宜,取出用清水洗净,这样不锈钢弹簧表面就能达到亚光效果。
以上两种方法,可适用于精密度高的弹簧。
3、清洗剂A放入有粗磨料、弹簧的振动光饰机中或六角滚筒中(弹簧与粗磨料的体积比最佳为1:3,清洗剂用量为弹簧重量的1%--2%)研磨抛光以后用清水洗净,弹簧表面的划痕就没有了,提高了弹簧表面的光洁度。
但精密度高易缠绕的弹簧不宜用此法。
第二步给不锈钢弹簧上光:把光亮剂B放入有粗磨料的振动光饰机或六角滚筒内(弹簧与精磨料的体积比为1:3,光亮剂B的用量为弹簧重量的1%--2%左右,时间越长越亮)抛光后,取出用清水洗净晾干即可,这样不锈钢弹簧表面如镀镍一般光亮照人,永不褪色。
60si2mn弹簧钢热处理工艺

弹簧钢热处理工艺
一、预备热处理
预备热处理是弹簧钢热处理工艺的重要环节,主要包括退火和正火处理。
退火处理的目的是消除钢锭中的内应力,提高钢的塑性和韧性,为后续的成型处理提供良好的材料基础。
正火处理则可以提高钢的硬度和强度,细化钢的组织结构,进一步优化弹簧的性能。
二、弹簧成型处理
弹簧成型处理是将预处理后的钢坯通过各种成型工艺加工成弹簧的形状。
在此过程中,需要控制弹簧的尺寸、形状和精度,确保弹簧的稳定性和可靠性。
常用的成型工艺包括卷制、弯曲、扭转等,成型后需要进行去应力退火处理,以消除成型过程中产生的内应力。
三、表面处理
表面处理是对成型的弹簧进行表面处理,以提高弹簧的耐磨性、耐腐蚀性和抗疲劳性能。
常用的表面处理方法包括喷丸强化、渗碳淬火、渗氮等。
喷丸强化是通过高速弹丸打击弹簧表面,使表面产生硬化的表面层,提高弹簧的抗疲劳性能。
渗碳淬火是将弹簧表面渗入碳元素,并进行淬火处理,以提高表面的硬度和耐磨性。
渗氮是将氮元素渗入弹簧表面,形成一层硬化的表面层,提高弹簧的耐腐蚀性和耐磨性。
四、稳定化处理
稳定化处理是指在弹簧的热处理过程中,采取一定的措施消除弹簧在使用过程中由于应力松弛而引起的形状变化。
常用的稳定化处理方法包括加热处理和老化处理。
加热处理是通过将弹簧加热到一定的温度并保持一定时间,使弹簧内部的结构更加稳定,减少应力松弛的可能性。
老化处理是在弹簧使用一段时间后,对其进行重新加热并进行短时间的保温,使弹簧内部的应力得到进一步松弛和稳定。
模具弹簧的表面处理技术与注意事项

模具弹簧的表面处理技术与注意事项第一、彩色漆面涂层使功能与美观集于一身弹簧表面用各种颜色漆层来作识别,如轻小荷重用黄色漆表示;轻荷重用蓝色漆表示;中荷重用红色漆表示;极重荷重用咖啡色漆表示;用好的漆层来做弹簧表面处理,可谓一举两得,用颜色来标识各种技术参数,方便生产操作,而且使弹簧表面的防腐性能得以更好的保证。
国内一般用人工喷漆,外观会出现漏喷、流挂、结合不好,防锈能力差。
本身的工艺局限性还会造成大量的产品要脱漆返工。
国外采用的是电泳漆,在水溶性的漆槽内,把工件做阴极,施加一定的电压和时间,便可在弹簧的所有表面形成厚度均匀的漆层,然后清洗烘干便可。
其外观清洁光亮,,无露底现象,结合力好不易脱落,硬度好有3-4H。
第二、用于弹簧油漆层的油漆1.沥青漆沥青漆具有良好的耐水、防潮、耐蚀性,有优异的耐酸性和良好的耐碱性。
但附着力、机械强度、装饰性差。
2.酚醛漆分为底漆与面漆两种,酚醛底漆附着力强,防锈性能好,但漆膜机械强度及光泽性差。
酚醛面漆漆膜坚硬,光泽性好,但耐气候性较差,漆膜易变黄。
3.醇酸漆漆膜坚韧,附着力强,机械性能好,有极好的光泽,良好的耐久性并具有一定的耐油、绝缘性能。
其缺点是表面干结快而粘手时间长,易起皱、不耐水、不耐碱4.环氧漆环氧漆附着力极强,硬度高,且韧性好,耐屈挠、耐冲击、硬而不脆,对水、酸、碱及许多有机溶剂都有极好的抵抗力,特别以耐碱更为突出。
其缺点是表面粉化快,溶剂选择性大。
5.水溶性环氧漆用于电泳涂漆。
在一般情况下,油漆层既可以单独使用,又可以作为磷化后的着色剂。
有时,有些弹簧为了按载荷分成等级,也涂喷不同颜色油漆来加以区别。
具体选用何种类型及牌号的油漆,应根据工作环境而定。
必要时,应在弹簧图样中注明。
第三、弹簧表面光饰处理近几年来,弹簧表面进行光饰处理也被弹簧设计者有所认识。
光饰工艺是将弹簧直接放入倾斜离心式或者螺旋振动式、涡流式等系列的光饰机中,并加入适量的研磨料、研磨剂和水,进行光整加工。
弹簧钢表面处理

弹簧钢表面处理的技术深析与应用弹簧钢作为一种常用的工业材料,因其优异的弹性和硬度特性而广泛应用于各种机械结构中。
表面处理技术作为提升弹簧钢性能的重要环节,不仅能够增强材料表面的耐磨损、耐腐蚀等特性,还能在一定程度上提升弹簧的工作寿命。
本文将对弹簧钢的表面处理技术进行多角度分析,探讨其在实际应用中的重要意义及操作要点。
一弹簧钢的基本特点与表面处理的必要性弹簧钢的力学性能要求极为严格,它需具备足够的弹性模量、抗拉强度和屈服强度,以应对反复的机械负载。
表面处理技术通过改变材料的表面结构和化学成分,有助于提升这些基本的力学特性。
例如,表面硬化可以增加弹簧表面的抵抗力,减少划痕和凹坑的产生。
(1)表面硬化处理通过渗碳、氮化等化学热处理过程,弹簧钢表面可以形成一层硬而耐磨的化合物层,显著提升其耐磨性能和抗疲劳寿命。
渗碳处理是在高温下将碳素扩散至弹簧钢表面,增加表面的碳含量,从而提升硬度。
氮化则是在一定条件下使氮元素扩散入钢材表面,形成硬质的氮化层。
(2)表面镀层技术镀层处理如镀锌、镀镍、镀铬等,能在弹簧表面形成保护层,有效隔离空气和水分,防止腐蚀。
这些镀层除了防护外,还可赋予弹簧美观的外观。
镀层过程中控制镀层的均匀性和附着力是技术关键。
二弹簧钢表面处理过程中的关键技术精确控制表面处理的过程对保证弹簧钢的质量至关重要。
这一过程涉及多种物理化学反应,对工艺参数的精细调控显得尤为重要。
(1)工艺参数优化在化学热处理中,温度、保持时间、气氛控制等参数的优化是确保处理效果的关键。
渗碳温度过高会导致晶界脆化,温度过低又达不到理想的硬化效果。
时间和气氛的控制需要精准以保证化合物层的均匀性。
(2)表面缺陷控制在镀层过程中,须严格清洁弹簧表面,防止镀层出现气泡、夹杂等缺陷。
采用适当的前处理和后处理技术可以有效减少缺陷发生。
三弹簧钢表面处理的实际应用和案例分析实际生产中,不同的应用场景对弹簧钢的表面处理技术提出了不同的要求。
通过具体案例的分析,可以更深入理解表面处理技术对弹簧性能的影响。
弹簧的表面处理工艺

弹簧的表面保护工艺,主要有:工序中的表面防锈、成品的发黑(发蓝)、磷化、油漆上防锈油、电泳漆、电镀、静电粉末喷涂等,特别后四种表面处理工艺得到广泛的应用和发展。
部分不锈钢丝和重要用途碳素弹簧钢丝的耐蚀性能相当于镀锌的耐蚀性能,若再镀一层ZnAl(5%)的合金,则耐蚀性可提高约3倍。
对电阻性能有要求的不锈钢丝或重要用途碳素弹簧钢丝,钢丝直径小于0.4mm可镀铜,大于0.4mm的可采用内部是铜,外部是不锈钢材料。
一般钢丝镀5um厚的Ni,可提高其导电性。
一般来说,能使材料表面硬化形成剩余应力的工艺(如喷丸强化和表面氮化等)均可提高疲劳强度。
目前正在研究非电解镀Ni,通过加热300~500℃,可将7%的P以PNi析出,可提高维氏硬度500HV,喷丸后,若在300℃以下加热镀Ni,亦可提高硬度10%达克罗(Dqcromet)涂覆新技术,具有很多的优点,无氢脆,高的抗腐性、高的耐温性、高渗透性、附着力强而且环保性能好。
目前已有应用,但需注意质量。
1)复合喷丸技术。
复合喷丸也通常称为复合喷丸。
最经济的方法是二次抛丸。
这是通过喷丸与不同直径的球。
首次使用较大的球团来获得残余压应力和表面光洁度。
2)应力喷丸喷丸过程。
应力喷丸加工过程也相对传统喷丸加工过程,仅仅因为它是很难适用于大规模生产,但近年来,由于应力喷丸加工设备的快速发展,它已经相对较大的高应力的大规模生产汽车悬架弹簧的发展。
特别是应力-强度喷丸强化与其它喷丸强化工艺的联合应用,具有良好的强化效果。
应力喷丸的预应力一般设置在700 ~ 800MPa。
应力喷丸后,残余应力峰值可达1200 ~ 1500MPa,从而获得较高的疲劳强度。
3)热压强压工艺热压强压工艺主要适用于对永久变形要求高的螺旋弹簧。
这是一个先进的稳定处理过程,防止永久变形。
除了能显著提高抗永久变形能力外,高温强压缩过程还能提高疲劳寿命。
弹簧加工工艺范文
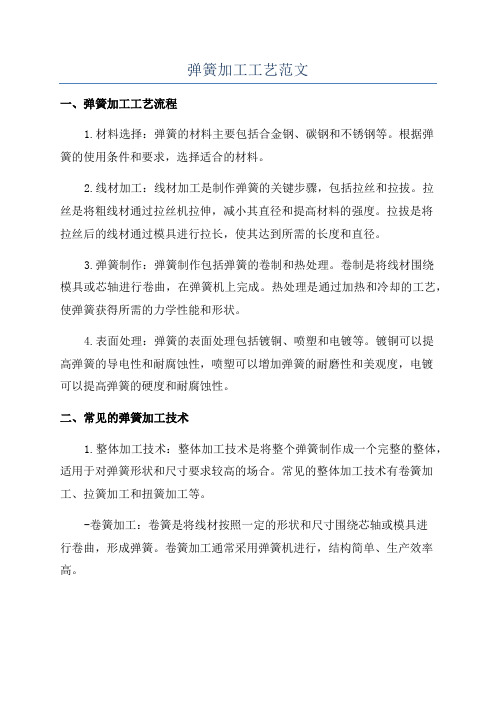
弹簧加工工艺范文一、弹簧加工工艺流程1.材料选择:弹簧的材料主要包括合金钢、碳钢和不锈钢等。
根据弹簧的使用条件和要求,选择适合的材料。
2.线材加工:线材加工是制作弹簧的关键步骤,包括拉丝和拉拔。
拉丝是将粗线材通过拉丝机拉伸,减小其直径和提高材料的强度。
拉拔是将拉丝后的线材通过模具进行拉长,使其达到所需的长度和直径。
3.弹簧制作:弹簧制作包括弹簧的卷制和热处理。
卷制是将线材围绕模具或芯轴进行卷曲,在弹簧机上完成。
热处理是通过加热和冷却的工艺,使弹簧获得所需的力学性能和形状。
4.表面处理:弹簧的表面处理包括镀铜、喷塑和电镀等。
镀铜可以提高弹簧的导电性和耐腐蚀性,喷塑可以增加弹簧的耐磨性和美观度,电镀可以提高弹簧的硬度和耐腐蚀性。
二、常见的弹簧加工技术1.整体加工技术:整体加工技术是将整个弹簧制作成一个完整的整体,适用于对弹簧形状和尺寸要求较高的场合。
常见的整体加工技术有卷簧加工、拉簧加工和扭簧加工等。
-卷簧加工:卷簧是将线材按照一定的形状和尺寸围绕芯轴或模具进行卷曲,形成弹簧。
卷簧加工通常采用弹簧机进行,结构简单、生产效率高。
-拉簧加工:拉簧是将线材拉伸成直线状态,然后使其两端呈现半圆形状,最后通过模具成型。
拉簧加工适用于对弹簧材料要求较高的场合,能够保证弹簧的材质均匀性和强度。
-扭簧加工:扭簧是将线材按照一定的形状围绕芯轴进行扭转,使其形成弹簧。
扭簧加工适用于对弹簧的形状和尺寸要求较高的场合,可以制作出各种不同形状的弹簧。
2.分体加工技术:分体加工技术是将弹簧制作成分体的形式,然后通过连接件将其组装成一个完整的弹簧装置。
常见的分体加工技术有拉伸簧加工和压缩簧加工等。
-拉伸簧加工:拉伸簧是将线材直接拉伸成直线状态,然后通过连接件将其两端固定起来。
拉伸簧加工适用于对弹簧的应力和形状要求较高的场合。
-压缩簧加工:压缩簧是将线材围绕芯轴或模具卷曲,然后通过连接件将其两端固定起来。
压缩簧加工适用于对弹簧的变形和压缩率要求较高的场合。
- 1、下载文档前请自行甄别文档内容的完整性,平台不提供额外的编辑、内容补充、找答案等附加服务。
- 2、"仅部分预览"的文档,不可在线预览部分如存在完整性等问题,可反馈申请退款(可完整预览的文档不适用该条件!)。
- 3、如文档侵犯您的权益,请联系客服反馈,我们会尽快为您处理(人工客服工作时间:9:00-18:30)。
弹簧表面处理工艺
1.弹簧发黑处理
(1)弹簧发黑工艺
碱性化学氧化处理发黑,是将加工完毕的合格弹簧放入含有浓碱溶液中加热处理,使弹簧表面获得一层微薄的致密氧化膜,这种氧化膜有抗腐蚀作用。
弹簧在加热的溶液中,由于碱对弹簧表面腐蚀,产生铁离子(亚铁化合物)在碱中加入氧化剂——亚硝酸钠能使氧化过程得到改变而在弹簧表面上生成致密的氧化膜(四氧化三铁)。
这种氧化膜主要是有磁性氧化铁组成,氧化膜的生成时间为30~60分钟。
若时间再延长,也不能提高氧化膜的厚度。
工艺过程:
去油———(去铜)——→酸洗——→清洗——→氧化(或二次氧化)——→清洗——→热水清洗——→皂化——→浸水膜装置换油——→入库。
各道工序要求
序号名称配方及技术要求备注
一去油 1.化学去油NaoH100~150克/升+Na2CO320-27克/升加热至沸点滚桶内加入少量废酸和铁悄
2.用汽油或柴油洗洗油。
3.用喷砂或喷丸去除油及锈
4.淬火回火的弹簧可用滚桶去油及锈
二去铜用铬酸250~300克/升+硫酸铵80~100克/升无铜时可省去此道工序
加水浸1~2分钟,然后再在清水中清洗
三酸洗用30%工业盐酸浸1~2分钟去除油污及锈酸洗时间不能太长
四清洗清洗后在弱碱槽内中和,防止酸带入氧化槽中
五氧化氢氧化钠650~700克/升+亚硝酸钠100~150克/升加热到140~144℃,保温30~60分钟 NaoH: NaNO2=5~8:1
六清洗氧化后在流动的清水中冲洗
七热水清洗热水90~100℃,清洗1~2分钟
八皂化 10~20%工业皂片或三乙油酸皂加热50~60℃1~2分钟温度不能太高
十上油浸MS-1水膜置换防锈油
十一入库
(2)发黑工艺操作规程
(Ⅰ)每天上班后开动电源将槽液加热至沸点,扒去槽中的氧化铁(沉淀物);
(Ⅱ)扒去沉淀物后加入0.5kg左右的黄血盐(亚铁氰化钾);
(Ⅲ)按发黑工艺技术要求加入一定量亚硝酸钠(符合5~8:1);
(Ⅳ)用温度计测量发黑槽液湿度,确保槽液温度140~144℃,若温度过高要加水,并控制好加热电源;(Ⅴ)发黑前,弹簧必须经充分的酸洗和清洗,拉力弹簧必须垂直装框,便于清洗;
(Ⅵ)发黑时必须严格执行工艺技术要求,液面的油渣要及时捞掉,槽液要及时补充;
(Ⅶ)发黑后弹簧须经高压水度分喷洗,经沸水清洗,皂化温度控制在50~60℃;
(Ⅷ)弹簧经沥掉过量油后装框、入库。
倒去弹簧的铁框须经高压水喷洗后再重复使用。
(Ⅸ)下班时,在氧化槽中加入一定量氢氧化钠(符合5~8:1),关掉电源。
清理、打扫工作场地,保持场地的整洁;
发黑工艺操作时的注意事项
(Ⅰ)氧化工件如发现有黄色挂霜现象,说明槽液温度过高,水份太少。
(Ⅱ)氧化工件不黑,呈灰色,是槽液温度过低或缺亚硝酸钠。
(Ⅲ)氧化槽的沸点在140℃以下则要加氢氧化钠。
(Ⅳ)皂化槽要经常补充皂片或三乙油酸皂以保持一定的浓度。
(Ⅴ)含硅钢材的氧化膜允许呈棕色或棕黑色;
(Ⅵ)工件发黑质量自检时,应在弹簧上油工序前进行,2%硫酸铜溶液浸泡法30秒后不析出铜为合格。
3%硫酸铜点滴试验。
在工件上点滴上硫酸铜或2%硫酸铜浸蚀试验,将工件完全浸设入此硫酸铜溶液,在30秒钟后肉眼观察氧化膜不变色为合格。
点滴试验和浸蚀试验都在工件未上油前进行,成品抽验时应先用酒清清除油污。
发黑氧化后的工件在正常保管下一年内不生锈。
2.弹簧的磷化处理
磷化是防止弹簧在运输和使用中腐蚀的一种工艺经磷化的弹簧在空气中,动植物矿物油中及甲苯等有机溶剂中均有抗腐蚀能力。
弹簧适用于锌磷酸盐处理可避免出现氢脆。
磷化膜比氧化膜厚,一般为5~10个微米。
通常磷化抗腐蚀性比氧化好。
尤其磷化处理适宜为弹簧上保护架的前道工序。
(1)弹簧磷化工艺冷水热水
(1)去油去锈——去铜——清洗——磷化——清洗——钝化——清洗————皂化——浸水膜置换油——入库
磷化工艺过程
序号名称技术要求备注
一去油 1.喷丸或喷沙去除油和锈及氧化皮用于淬火回火弹簧
2.汽油洗涤,吹干后可磷化(可洗涤二或三次)主要用于细弹簧
3.化学去油NaoH100~150克/升20~70%Na2CO2加热至100℃
4.滚桶去油污及锈用于拉伸弹簧
二去铜铬酸250~300克/升,硫酸铵80~100克/升加水无铜时可省去此工序
三清洗自来水冲洗去除酸性
四磷化磷酸锰铁盐30~35克/升,硝酸锌55~75克/升温度70~80℃保温10~15分钟,总酸度48~60
游离酸2.5~6.7硫酸根≦0.5
五清洗自来水冲洗
六钝化重铬酸钾(K2Cr2O2)80~100克/升90~100℃
七清洗自来水冲洗
八清洗热水90~100℃清洗1~2分钟
九皂化 10~20克/升工业皂片或三乙油酸皂50~70℃1~2分钟
十上油浸水膜量换油
十一入库
(2)弹簧磷工艺操作规程及注意事项
(Ⅰ)每天上班前要严格检查待磷化弹簧的表面状况,要求清洁、光亮。
不允许有任何油污、脏物、锈班、镀铜层等。
(Ⅱ)开启磷化槽、钝化槽、热水槽。
皂化槽加热电源,将磷化槽液确保在70~80℃,钝化槽90~100℃,热水槽90~100℃、皂片槽50~70℃。
(Ⅲ)磷化前所用的料框经充分喷洗后再装入弹簧,装框时必须或上清洗的涤棉手套,弹簧间不得有大面积或线接触。
(Ⅳ)磷化时严格执行磷化工艺要求,保温10~15分钟。
(Ⅴ)磷化后弹簧需经自来水充分冲洗。
(Ⅵ)弹簧在钝化槽中保温约1~2分,钝化后需自来水充分喷洗。
(Ⅶ)将弹簧再放入热水槽清洗1~2分钟再放入皂化槽1~2分钟,然后送涂柒处或上油后再送涂柒处。
(Ⅷ)下班后,关闭电源,认真打扫,确保工场整洁。
(Ⅸ)磷化槽添加磷酸锰铁盐与硝酸锌按1:2,钝化槽中的废重铬酸钾要集中统一处理,皂化槽中要经常补充皂片或三乙油酸皂。
(Ⅹ)若不要钝化时,可省去操作规程Ⅵ。
(Ⅺ)磷化前弹簧的喷沙、喷丸清理与磷化的间隔不得超过4小时,清理好后弹簧必须放入清洁的料框内。
(3)磷化质量检验方法
(Ⅰ)浸泡法
3%氯化钠NaCl,温度15~25℃,浸2小时无锈为合格。
(Ⅱ)点滴法之一
硫酸铜CuSO20.5N 40毫克氯化钠Nacl10% 20毫克,硫酸。
0.1N0.8毫克。
点滴后不起黄时间越长质量越好,3分钟内不变色者为合格。
(Ⅲ)点滴法之二
硫酸铜CuSO4、SH20 66克/升,氯化钠NaCL32.5克/升,盐酸HCL 1:10 1.2克/升,点滴3分钟以上不发黄者为合格。
(Ⅳ)浸泡法
硫酸铜5%溶液,浸1分钟后工件表面不出现黄色为合格。
在检验工件磷化质量的同时,必须对磷化槽液进行定期化验总酸度、游离酸、酸根参数以确保日常的工件磷化质量。