管式加热炉温度控制与分析
管式加热炉温度前馈-反馈控制系统设计解析

过程控制课程设计报告管式加热炉温度前馈-反馈控制系统设计学生:专业:自动化班级:重庆大学自动化学院2012年10目录前言 (1)1 管式加热炉系统描述 (1)1.1 管式加热炉的一般结构 (1)1.2 管式加热炉传热方式 (2)1.3 管式加热炉工艺流程 (2)1.4 主要控制参数、操作参数及影响因素 (2)2 方案设计 (3)2.1 方案一 (3)2.2 方案二 (4)3 管式加热炉温度控制系统模型的建立 (4)3.1 前馈-反馈控制系统传递函数 (4)3.2 过程响应分析 (6)3.3 PID控制算法 (7)3.4 PID 控制各参数的作用 (8)4 MATLAB/Simulink仿真 (8)4.1 用ITAE 方法设计控制器 (8)4.2 用Ziegler-Nichols方法设计控制器 (10)5 基于MATLAB/Simulink的仿真 (12)5.1 前馈-反馈控制与单回路控制模型的比较 (12)5.2 基于ITAE方法的仿真模型 (13)5.2.1 ITAE的PI控制模型仿真 (13)5.2.2 ITAE的PID控制模型仿真 (14)5.3基于Ziegler-Nichols方法的仿真模型 (14)5.3.1 Ziegler-Nichols的PI控制仿真模型 (14)5.3.2 Ziegler-Nichols的PID控制仿真模型 (15)6 报告总结 (15)参考文献 (16)前言管式加热炉是石油炼制、化纤工业、石油化工和化学行业主要的工艺设备之一,作用是将物料加热至工艺所要求的温度,具有操作方便, 自动化水平高, 加工成本低, 传热效率高等优点。
1967年4月,世界上第一台步进梁式加热炉由美国米兰德公司设计而成,之后,日本中外炉公司设计的世界上第二座步进梁式加热炉于1967年5月投产。
70年代末,发达工业国家己经进入大型连续加热炉计算机控制的实用阶段,但控制策略还主要局限于燃烧控制。
原油厂管式加热炉温度串级控制系统设计

4
四、管式加热炉出口温控仪表的选型
(四) 主、副调节器正反作用方式确定
由生产工艺安全考虑,燃料调节阀应选气开方式,这样保证系统出现故障时 调节阀处于全关状态,防止燃料进入加热炉,确保设备安全。主调节器作用方式 确定:炉膛温度升高,物料出口温度也升高,主被控过程 Ko1﹥0。为保证主回 路为负反馈,各环节放大系数乘积必须为正,所以负调节器的放大系数 K1﹥0, 主调节器作用方式为反作用。又为保证副回路是负反馈,各环节放大系数乘积必 须为正,所以负调节器大于 0,负调节器作用方式为反作用方式。
图 4 给出了温度变送器的原理框图,虽然温度变送器有多个品种、规格, 以配合不同的传感元件和不同的量程需要,但他们的结构基本相同。
本设计பைடு நூலகம்用 DDZ-III 型热电偶温度变送器。
图 4 DDZ-III 型调节器结果框图
(四) 调节器的汽开汽关特性及安全防爆设计 气动调节阀气开、气关方式的选择主要是从生产安全角度出发来考虑的。当
综上选择 ZMAS 型气动薄膜角形单座调节阀,阀体为直角形,阀芯不单导 向结构,阀的流路简单,便于自净和清洗。阻力小,适用于高粘度,含有悬浮物
5
四、管式加热炉出口温控仪表的选型
和颗粒状物质的流体的调节,可避免结焦、粘结、堵塞。 由 ZMAS 型气动薄膜角型调节阀型号编制说明知,选择 ZMAS-320K 型的调
高温管式炉使用方法
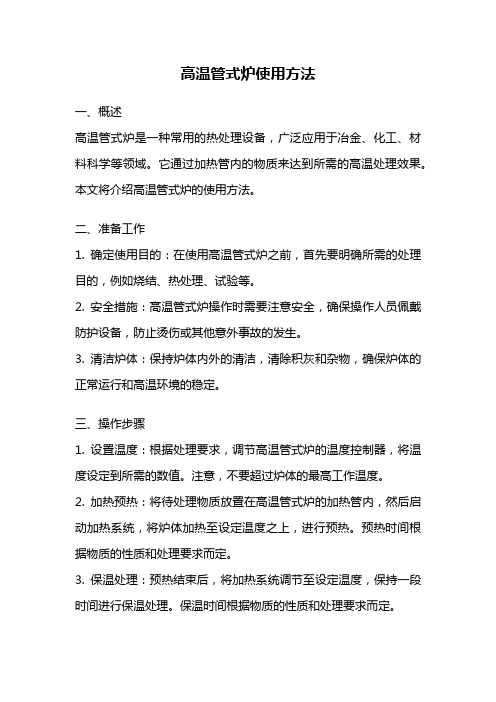
高温管式炉使用方法一、概述高温管式炉是一种常用的热处理设备,广泛应用于冶金、化工、材料科学等领域。
它通过加热管内的物质来达到所需的高温处理效果。
本文将介绍高温管式炉的使用方法。
二、准备工作1. 确定使用目的:在使用高温管式炉之前,首先要明确所需的处理目的,例如烧结、热处理、试验等。
2. 安全措施:高温管式炉操作时需要注意安全,确保操作人员佩戴防护设备,防止烫伤或其他意外事故的发生。
3. 清洁炉体:保持炉体内外的清洁,清除积灰和杂物,确保炉体的正常运行和高温环境的稳定。
三、操作步骤1. 设置温度:根据处理要求,调节高温管式炉的温度控制器,将温度设定到所需的数值。
注意,不要超过炉体的最高工作温度。
2. 加热预热:将待处理物质放置在高温管式炉的加热管内,然后启动加热系统,将炉体加热至设定温度之上,进行预热。
预热时间根据物质的性质和处理要求而定。
3. 保温处理:预热结束后,将加热系统调节至设定温度,保持一段时间进行保温处理。
保温时间根据物质的性质和处理要求而定。
4. 冷却降温:保温处理结束后,关闭加热系统,让炉体自然冷却至室温。
根据物质的性质,可以选择快速冷却或缓慢降温。
5. 取出样品:待炉体完全冷却后,小心取出处理完毕的样品。
注意,取出时应避免碰撞或其他损坏。
四、注意事项1. 温度控制:在使用高温管式炉时,要严格控制温度,避免超过设定的工作温度范围。
2. 防护措施:操作人员要佩戴防护手套、护目镜等,以防止烫伤或其他安全事故的发生。
3. 环境通风:高温管式炉在工作过程中会产生烟雾和有害气体,应确保操作环境的通风良好,避免对人员和设备造成伤害。
4. 清洁维护:定期清洁炉体内外的灰尘和杂物,保持设备的正常运行和高温环境的稳定。
5. 定期维护:定期检查高温管式炉的各项部件,确保设备的正常工作。
如发现故障或异常情况,应及时进行维修或更换。
五、总结高温管式炉是一种重要的热处理设备,正确使用和操作对于保证处理效果和设备寿命至关重要。
管式加热炉热效率下降的原因分析及解决措施
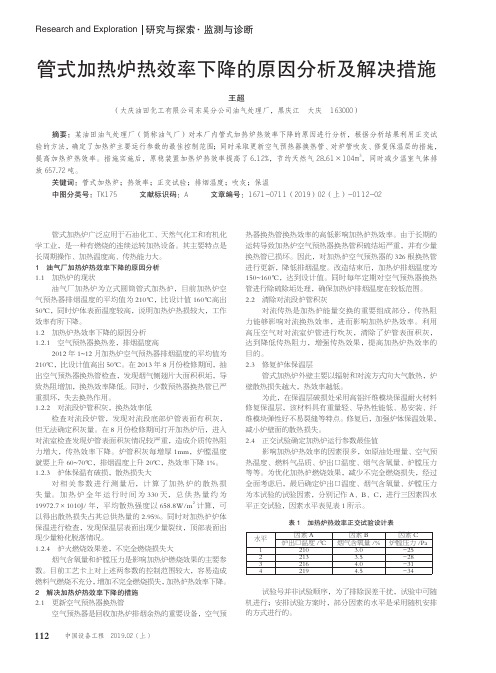
112研究与探索Research and Exploration ·监测与诊断中国设备工程 2019.02 (上)管式加热炉广泛应用于石油化工、天然气化工和有机化学工业,是一种有燃烧的连续运转加热设备。
其主要特点是长周期操作、加热温度高、传热能力大。
1 油气厂加热炉热效率下降的原因分析1.1 加热炉的现状油气厂加热炉为立式圆筒管式加热炉,目前加热炉空气预热器排烟温度的平均值为210℃,比设计值160℃高出50℃,同时炉体表面温度较高,说明加热炉热损较大,工作效率有所下降。
1.2 加热炉热效率下降的原因分析1.2.1 空气预热器换热差,排烟温度高2012年1~12月加热炉空气预热器排烟温度的平均值为210℃,比设计值高出50℃。
在2013年8月份检修期间,抽出空气预热器换热管检查,发现烟气侧翅片大面积积垢,导致热阻增加,换热效率降低。
同时,少数预热器换热管已严重损坏,失去换热作用。
1.2.2 对流段炉管积灰,换热效率低检查对流段炉管,发现对流段底部炉管表面有积灰,但无法确定积灰量。
在8月份检修期间打开加热炉后,进入对流室检查发现炉管表面积灰情况较严重,造成介质传热阻力增大,传热效率下降。
炉管积灰每增厚1mm,炉膛温度就要上升60~70℃,排烟温度上升20℃,热效率下降1%。
1.2.3 炉体保温有破损,散热损失大对相关参数进行测量后,计算了加热炉的散热损失量。
加热炉全年运行时间为330天,总供热量约为19972.7×1010J/年,平均散热强度以658.8W/m 2计算,可以得出散热损失占其总供热量的2.95%。
同时对加热炉炉体保温进行检查,发现保温层表面出现少量裂纹,顶部表面出现少量粉化脱落情况。
1.2.4 炉火燃烧效果差,不完全燃烧损失大烟气含氧量和炉膛压力是影响加热炉燃烧效果的主要参数。
目前工艺卡上对上述两参数的控制范围较大,容易造成燃料气燃烧不充分,增加不完全燃烧损失,加热炉热效率下降。
管式加热炉温度温度串级控制系统的设计说明
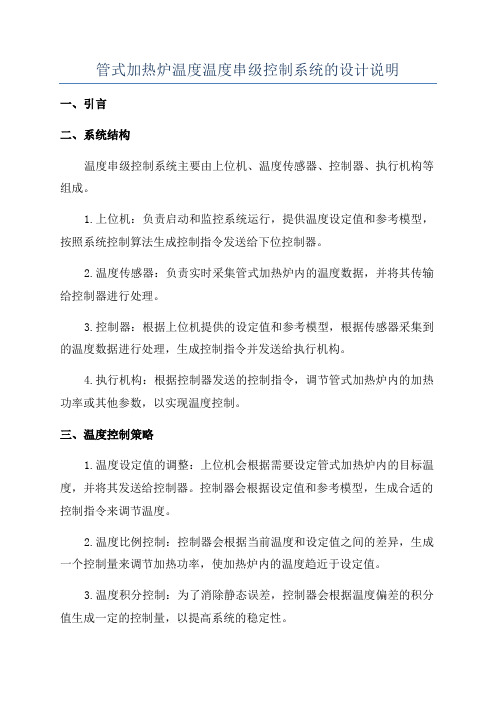
管式加热炉温度温度串级控制系统的设计说明一、引言二、系统结构温度串级控制系统主要由上位机、温度传感器、控制器、执行机构等组成。
1.上位机:负责启动和监控系统运行,提供温度设定值和参考模型,按照系统控制算法生成控制指令发送给下位控制器。
2.温度传感器:负责实时采集管式加热炉内的温度数据,并将其传输给控制器进行处理。
3.控制器:根据上位机提供的设定值和参考模型,根据传感器采集到的温度数据进行处理,生成控制指令并发送给执行机构。
4.执行机构:根据控制器发送的控制指令,调节管式加热炉内的加热功率或其他参数,以实现温度控制。
三、温度控制策略1.温度设定值的调整:上位机会根据需要设定管式加热炉内的目标温度,并将其发送给控制器。
控制器会根据设定值和参考模型,生成合适的控制指令来调节温度。
2.温度比例控制:控制器会根据当前温度和设定值之间的差异,生成一个控制量来调节加热功率,使加热炉内的温度趋近于设定值。
3.温度积分控制:为了消除静态误差,控制器会根据温度偏差的积分值生成一定的控制量,以提高系统的稳定性。
4.温度微分控制:为了快速响应温度变化,控制器还会根据温度变化的速率生成相应的控制量。
四、系统性能指标1.温度响应时间:系统需要具备较快的响应时间,即加热炉内的温度能够尽快达到设定值。
2.温度稳定度:系统应当保持较好的温度稳定度,即经过一定时间后,温度偏差应尽可能小。
3.抗干扰能力:系统需要具备较好的抗干扰能力,对于外界干扰因素的影响应尽可能小。
五、系统设计优化1.选择合适的温度传感器:合适的温度传感器能够提供准确的温度数据,为控制系统提供可靠的输入信号。
2.高性能控制器的选择:通过选用性能较好的控制器,能够提高控制系统的稳定性和响应速度。
3.优化控制策略:通过合理选择温度比例、积分和微分参数,能够提高控制系统的性能。
4.加入滤波器和抗干扰装置:通过加入合适的滤波器和抗干扰装置,能够降低系统对外界干扰的敏感度,提高系统的抗干扰能力。
过程控制课程设计报告—管式加热炉温度控制

课程设计报告课题名称:管式加热炉温度控制学院:电气信息工程学院专业:测控技术与仪器姓名:刘英皓学号:13指导教师:曹艳2010年12月16日课题要求:管式加热炉要求出口温度为4003℃。
1.由于燃料热值频繁变化,为此设计串级控制系统画出工艺流程图。
2.选择自动化设备,列出自动化设备表。
3.通过仿真验证方案可行性。
一、管式加热炉简介管式加热炉一般由四个主要部分组成:烟囱、对流室、辐射室及燃烧器,示意图如图1.1所示:图1.1 管式加热炉通风系统:将燃烧用空气引入燃烧器,并将烟气引出炉子,可分为自然通风方式和强制通风方式。
对流室:靠辐射室出来的烟气进行以对流传热为主的换热部分。
辐射室:通过火焰或高温烟气进行辐射传热的部分。
这部分直接受火焰冲刷,温度很高(600-1600℃),是热交换的主要场所(约占热负荷的70-80%)。
燃烧器:是使燃料雾化并混合空气,使之燃烧的产热设备,燃烧器可分为燃料油燃烧器,燃料气燃烧器和油一气联合燃烧器。
管式加热炉的特征:(1)被加热物质在管内流动,故仅限于加热气体和液体。
而且,这些气体或液体通常都是易燃易爆的烃类物质,同锅炉加热水和蒸汽相比,危险性大,操作条件要苛刻得多。
(2)加热方式为直接受火式,加热温度高,传热能力大。
(3)只烧气体或液体燃料。
(4)长周期连续运转,不间断操作,便于管理。
二、管式加热炉温度控系统工艺流程及控制要求管式加热炉的主要任务是把原油或重油加热到一定温度,以保证下一道工序(分馏或裂解)的顺利进行。
加热炉的工艺流程图如图 2.1所示。
燃料油经过蒸汽雾化后在炉膛中燃烧,被加热油料流过炉膛四周的排管中,就被加热到出口温度T1。
在燃料油管道上装设一个调节阀,用它来控制燃油量以达到调节温度T1的目的。
图2.1 管式加热炉工艺流程图引起温度T1改变的扰动因素很多,主要有:(1)燃料油方面(它的组分和调节阀前的油压)的扰动D2;(2)喷油用的过热蒸汽压力波动D4;(3)被加热油料方面(它的流量和入口温度)的扰动D1;(4)配风、炉膛漏风和大气温度方面的扰动D3;其中燃料油压力和过热蒸汽压力都可以用专门的调节器保持其稳定,以便把扰动因素减小到最低限度。
管式加热炉出口温度与炉膛的温度串级控制
设计题目:管式加热炉出口温度与炉膛温度串级控制系统设计系别:电子通讯与应用技术系班级:学生姓名:指导教师:成绩:________________________2012年 6 月29 日课程设计任务书课程设计题目管式加热炉出口温度与炉膛温度串级控制系统设计功能技术指标1. 选择控制器与调节阀的作用方式;2.画出控制系统框图;3.采用两步整定法整定主、副控制器PID的参数。
求出比例度与衰减振荡周期;4.按照经验公式且适当修正分别求得主、副控制器的最佳参数值;5.求出系统的阶跃响应曲线;6.求出设定值位0时,施加幅值为30%的一次阶扰动信号,系统的输出曲线;7.分析系统特点。
工作量两周工作计划1 设计前准备1天2 总体设计1天3 检测变送器的选用0.5天4 控制器的选择0.5天5 执行器件的选择0.5天6 控制器算法确定及参数整定 1.5天7 过程控制系统整体构成2天8 编写课程设计报告1天指导教师评语2012年6月29日目录第1章绪论.................................................................................................. - 2 -1.1 设计要求...................................................................................... - 2 -1.1.1 设计题目和设计指标...................................................... - 2 -1.1.2 设计功能.......................................................................... - 2 -第2章系统总体设计方案........................................................................ - 3 -2.1. 工艺流程图.................................................................................. - 3 -2.2. 方框图工艺流程介绍.................................................................. - 3 -第3章硬件设计和器件的选择................................................................ - 4 -3.1. 系统电气接线图.......................................................................... - 4 -3.2. 器件选择...................................................................................... - 4 -3.3. 译码电路设计.............................................................................. - 4 -第4章控制算法选择及参数整定............................................................ - 5 -第5章系统软件设计................................................................................ - 6 -结论................................................................................................................ - 8 -心得和体会.................................................................................................... - 9 -致谢.............................................................................................................. - 10 -参考文献...................................................................................................... - 10 -第1章绪论1.1 设计要求设计要求:选择加热炉出口温度为主变量,炉膛温度为副变量,设计串级控制系统1.1.1 设计题目和设计指标设计题目:管式加热炉出口温度与炉膛温度串级控制系统设计设计指标:1. 选择控制器与调节阀的作用方式;2.画出控制系统框图;3.采用两步整定法整定主、副控制器PID的参数。
管式加热炉温度-温度串级控制系统的设计
课程设计任务书学生姓名:方诗豪专业班级:自动化0804指导教师:傅剑工作单位:自动化学院题目:管式加热炉温度-温度串级控制系统的设计初始条件:管式加热炉是石油工业中重要的设备之一,它的任务是把原油加热到一定的温度,以保证下一道工序的顺利进行。
加热炉的工艺过程为:燃料油经雾化后在炉膛中燃烧,被加热油料流过炉膛四周的排管后,就被加热到出口温度。
试以温度-温度串级控制控制策略设计过程控制系统,使得管式加热炉出口温度为为70℃,稳态误差±2℃。
要求完成的主要任务:1、了解管式加热炉工艺设备及其工作流程2、基于对象特点分析,绘制控制系统方案图3、确定系统所需检测元件、执行元件、控制器技术参数4、撰写系统调节原理及调节过程说明书5、总结课程设计的经验和收获时间安排12月19日选题、理解课题任务、要求12月20日方案设计12月21~28日参数计算、撰写说明书12月29日答辩指导教师签名:年月日系主任(或责任教师)签名: 年月日目录前言 (2)1设计的目的及意义 (4)1。
1管式加热炉简介 (4)1.2 设计目的及意义 (4)2 管式加热炉温度控系统工作原理及控制要求 (6)3 总体设计方案 (7)3.1 温度-温度串级控制系统 (7)3。
2 方案特点 (8)4 串级控制系统分析 (9)4。
1 主回路设计 (9)4.2 副回路选择 (9)4.3 主、副调节器规律选择 (9)4.4 主、副调节器正反作用方式确定 (10)4。
5 控制器软件设计 (10)4.6数字PID控制器参数整定 (11)5 各仪表的选取及元器件清单 (13)5。
1 温度检测元件 (13)5。
2 温度变送器 (14)5。
3 调节阀 (15)5。
4 联锁保护 (16)6 感受与体会 (16)管式加热炉温度—温度串级控制系统的设计前言自70年代以来,由于工业过程控制的需要,特别是在微电子技术和计算机技术的迅猛发展以及自动控制理论和设计方法发展的推动下,国外温度控制系统发展迅速,并在智能化、自适应、参数自整定等方面取得成果,在这方面,以日本、美国、德国、瑞典等国技术领先,都生产出了一批商品化的、性能优异的控制器及仪器仪表,并在各行业广泛应用。
管式电阻炉温度定值控制实验
管式电阻炉温度定值控制实验简介管式电阻炉是一种常见的工业加热设备,用于加热物体或进行实验。
在许多应用中,需要对管式电阻炉的温度进行精确的控制,以满足实验或生产的要求。
本实验旨在研究管式电阻炉温度的定值控制方法,并进行实际操作验证。
实验目的1.理解管式电阻炉的基本原理和结构;2.掌握温度传感器的选取和安装方法;3.学习PID控制算法的原理和调参方法;4.进行管式电阻炉温度定值控制实验,并分析实验结果。
实验器材和材料1.管式电阻炉:用于加热物体或进行实验的设备;2.温度传感器:用于测量管式电阻炉的温度;3.控制器:用于控制管式电阻炉的加热功率;4.计算机:用于实时监测和记录管式电阻炉的温度;5.实验样品:用于进行管式电阻炉温度定值控制实验。
实验步骤1. 实验准备1.将管式电阻炉放置在实验台上,并确保其稳定;2.安装温度传感器,将其插入管式电阻炉内,确保与被加热物体接触良好;3.连接控制器和计算机,并确保其正常工作;4.准备实验样品,根据实验要求确定加热时间和温度范围。
2. 温度传感器选取和安装1.根据实验要求选择合适的温度传感器,常用的有热电偶和热电阻;2.将温度传感器插入管式电阻炉内,并确保与被加热物体接触良好;3.使用导线将温度传感器连接到控制器,确保信号传输正常。
3. PID控制算法调参1.在计算机上打开控制器软件,进入PID控制算法调参界面;2.根据管式电阻炉的特性和实验要求,设置合适的PID参数初值;3.依次调整PID参数,观察管式电阻炉温度的响应,直到达到理想的控制效果;4.记录最终的PID参数值,以备后续实验使用。
4. 管式电阻炉温度定值控制实验1.将实验样品放置在管式电阻炉内,并固定好;2.设置目标温度和加热时间,启动控制器;3.实时监测和记录管式电阻炉的温度,观察温度的变化过程;4.分析实验结果,比较目标温度和实际温度的偏差,并评估控制效果。
实验结果分析根据实验数据和分析结果,评估管式电阻炉温度定值控制的效果。
管式加热炉温度控制系统设计
管式加热炉温度控制系统设计管式加热炉温度控制系统是一种用来控制管式加热炉温度的系统。
管式加热炉是一种常用的工业加热设备,常用于热处理、烧结、退火等工艺过程中对物料的加热。
温度是管式加热炉工作过程中的一个重要参数,对于保证工艺过程的稳定性和产品质量具有重要意义。
因此,温度控制系统的设计对于管式加热炉的正常运行和工艺过程的稳定性至关重要。
管式加热炉温度控制系统一般包括传感器、执行器、控制器和显示器等组成部分。
传感器负责采集管式加热炉的温度信号,传输给控制器;控制器根据传感器采集到的温度信号来比较设定温度和实际温度的偏差,然后控制执行器来调节加热炉的加热功率,以使实际温度稳定在设定温度值附近;显示器用来显示管式加热炉的实时温度和设定温度值。
在管式加热炉温度控制系统的设计中,需要考虑以下几个方面:1.传感器的选择与安装:传感器的选择应考虑到其测量的温度范围和精度要求。
一般常用的温度传感器有热电偶和热敏电阻。
传感器的安装应尽量靠近加热炉内部,以获取更精确的温度信号。
2.控制器的选择:控制器的选择应根据加热炉的控制要求和控制精度来确定。
一般常用的控制器有PID控制器和模糊控制器。
PID控制器可以根据实际温度和设定温度之间的偏差来调整执行器的输出,以实现温度控制的精度。
3.执行器的选择与控制:执行器的选择应根据加热炉的加热功率和控制要求来确定。
常用的执行器有电阻加热器和电磁加热器。
控制器应根据传感器采集到的温度信号来计算并调整执行器的输出功率,以控制加热炉的温度。
4.系统的安全保护:温度控制系统设计中应考虑到系统的安全保护措施。
例如,在温度超过预定范围时,应设定报警装置,及时发出警报并停止加热,以防止温度过高造成炉体燃烧或其他事故。
5.系统的自动化与监控:温度控制系统设计中可以考虑加入自动化和监控功能,通过与计算机连接,实现对加热炉运行状态和温度变化的远程监控和控制。
总之,管式加热炉温度控制系统设计需要综合考虑传感器、执行器、控制器和显示器等组成部分,以及系统的安全保护和自动化与监控功能,以实现对管式加热炉温度的精确控制。
- 1、下载文档前请自行甄别文档内容的完整性,平台不提供额外的编辑、内容补充、找答案等附加服务。
- 2、"仅部分预览"的文档,不可在线预览部分如存在完整性等问题,可反馈申请退款(可完整预览的文档不适用该条件!)。
- 3、如文档侵犯您的权益,请联系客服反馈,我们会尽快为您处理(人工客服工作时间:9:00-18:30)。
管式加热炉温度-温度串级控制系统1设计意义及要求1.1设计意义管式加热炉是石油工业中重要装置之一,加热炉控制的主要任务就是保证工艺介质最终温度达到并维持在工艺要求范围内,由于其具有强耦合、大滞后等特性,控制起来非常复杂。
同时,近年来能源的节约、回收和合理利用日益受到关注。
加热炉是冶金、炼油等生产部门的典型热工设备,能耗很大。
因此,在设计加热炉控制系统时,在满足工艺要求的前提下,节能也是一个重要质量指标,要保证加热炉的热效率最高,经济效益最大。
另外,为了更好地保护环境,在设计加热炉控制系统时,还要保证燃料充分燃烧,使燃烧产生的有害气体最少,达到减排的目的。
1.2设计要求1)本课程设计题目为加热炉温度-温度串级控制系统设计,课程设计时间为2周;学生对选定的设计题目所涉及的生产工艺和控制原理进行介绍,针对具体设计选择相应的控制参数、被控参数以及过程检测控制仪表,并画出控制流程图及控制系统方框图。
2)课程设计说明书按学校“课程设计工作规范”中的“统一书写格式”撰写,具体包括:① 目录;② 摘要;③ 生产工艺和控制原理介绍;④ 控制参数和被控参数选择;⑤ 控制仪表及技术参数;⑥ 控制流程图及控制系统方框图;⑦ 总结与展望;(设计过程的总结,还有没有改进和完善的地方);⑧ 课程设计的心得体会(至少500字);⑨ 参考文献(不少于5篇);⑩ 其它必要内容等。
2方案论证2.1方案选择管式加热炉加热炉的工作原理如图1所示。
要加热的冷物料从左端的管口流入管式加热炉,而燃料从右端的管口流入管式加热炉的燃烧部分,以供热。
经加热的物料从右上端的管口流出,物料出口温度1()t θ为被控参数。
图1 管式加热炉工作原理图分析管式加热炉的工作过程可知,物料出口温度1()t θ受进入管式加热炉的物料初始温度,物料进入的流量(即物料入口的压强),进入管式加热炉的燃料的流量(也即燃料入口压强),燃料的燃烧值等因素的影响。
其中物料进入的流量(即物料入口的压强)和进入管式加热炉的燃料的流量(也即燃料入口压强)是影响物料出口温度1()t θ的主要因素。
如果采用单回路控制系统,根据操作量的选取原则,我们可以在物料入口处装上一个调节阀,以控制物料进入的流量;对于进入管式加热炉的燃料的流量,可以使它保持某一恒定值。
或在燃料的入口处安装一个调节阀,以控制进入管式加热炉的燃料的流量;对于进入管式加热炉的物料的流量,则可以使它保持某一恒定值。
而调节阀的开度大小由安装在物料出口处的温度传感器输出的大小间接控制。
它虽然结构简单,实现方便;但不符合生产工艺的要求。
因为如果将物料的进入流量进行限定后,则日生产总量也被限定。
这显然不符合实际的工业生产情况。
在此基础上进行一点改进——不对另一个量进行限制。
基于对燃料进入量进行控制的管式加热炉单回路温度控制系统原理图如图2所示。
图2 管式加热炉单回路温度控制系统原理图如图2所示的单回路温度控制系统初看起来是可行的。
而且它的结构简单,所需的器材少,投入小。
也符合工业设物料出口温度1()t θ1T C物料入口燃料 物料出口温度1()t θ计的经济原则。
但考虑到实际的被控对象——管式加热炉是一个大惯性系统,该方案实际上是行不通的。
在如图2所示的方案中,物料进入管式加热炉的流量变化和燃料入口压强的变化是一个对对被控量——物料出口温度1()t θ影响比较大的干扰。
假如流入管式加热炉的物料突然减少而燃料入口处的压强突然增大,由于物料在炉膛内的加热是一个过程(存在一个较大的时间滞后1T ),同时加热的物料经过炉膛内蜿蜒曲折的管道(用以实现物料的加热)流出加热炉也存在一个较大的滞后时间2T 。
经过较长时间滞后,才开始相应的调节显然是无法达到工艺要求的使物料出口温度只在2%±内波动。
而串级控制系统通常适用用于工业上一些有较大容量滞后或较大纯滞后的过程,有必要选择串级控制系统对管式加热炉的温度控制。
串级控制的原理图如图3所示。
图3 温度串级控制系统原理图在如图3所示的温度串级控制系统中,物料入口流量的变化和燃料入口压强的变化是影响物料出口温度的主要因素,而且它们对物料出口温度的影响存在较大的时间滞后——通过对管式加热炉的工作原理的分析可知,前者的时间滞后来源与物料在管道中流动的时间;而后者的时间滞后来源于前者的滞后时间加上管壁的热传递滞后时间。
即后者作用滞后时间2T 要大于前者的滞后时间1T 。
这种较大的滞后时间是给控制带来麻烦的关键因素。
那么减小或尽量消除这种较大的时间滞后成为控制系统设计的核心问题。
由工业生产工艺决定了由管道产生的时间滞后无法消除,而由炉膛和管壁产生的时间滞后可以尽量减小。
故可以选择物料出口温度作为主变量,炉膛温度作为副变量,构建串级控制系统。
其原理图如图3所示,方框图如图4所示。
主控制器温度变送器1温度变送器2物料管壁炉膛调节阀副控制器+-+-X1X2X3X4F3,F4F1,F2图4 温度串级控制系统原理方框图2.2温度串级控制系统分析在图4所示的温度串级控制系统中,由副控制器,调节阀,炉膛,温度变送器2构成温度控制系统的副环(内环)。
它将主控制器的输出作为给定信号,跟随信号X2;它的输出信号直接控制燃料进入调节阀的开度,从而控制炉膛内的温度。
由工程实践经验有——炉膛内的温度同物料出口温度存在某种关系,这样就可以达到间接控制物料出口温度的目的。
由于副环构成一个时间常数较小的负反馈环,它能在本环内引入的干扰信号(燃料入口压强变化和燃料热值变化分别用F3,F4表示)对物料出口温度产生较大影响前,及时进行调节。
对整个控制系统而言,可起到先调,粗调,快调的作用。
主控制器,副环,管壁,物料,温度变送器1构成主环(外环)。
由于主环回路前向通道较副环要长,控制作用的滞后时间较大,它的调节作用较慢;而且对副环所产生的控制偏差和物料入口温度及压强(分别用F1,F2表示)变化引起的干扰起到抑制作用。
它在整个控制系统中起到后调,慢调,细调的作用。
除此以外,主环和副环的协同作用还能大大提高系统的抗干扰能力。
假设在稳态工况下,物料进口温度和流量稳定,燃料的热值和流量不变,控制燃料的调节阀阀门开度保持一定,此时炉膛内的温度和物料出口温度都保持恒定。
如果干扰同时作用于主回路和副回路。
当燃料入口压强变化和燃料热值(分别用F3,F4表示)变化同物料入口温度及压强(分别用F1,F2表示)变化的作用方向相同(即同时曾大或变小)时,假如同时增加,在F1和F2的作用下,物料出口温度上升;通过温度变送器1 的反馈作用,使主调节器的输入减小,而相应的主调节器的输出也减小(即副控制环的给定值减小,也即减小燃料进入阀的开度)。
在副控制环中引入的干扰信号F3和F4使得炉膛内的温度升高,通过温度变送器2的反馈作用,也要使得副控制器的输入减小,也是要达到减小燃料进入阀的开度。
同样可以推出,当干扰信号同时减小时,主控制器和副控制器的控制作用都是使得燃料进入阀的开度增大。
二者作用的叠加使得整个系统抗干扰性能有很大的提高。
当燃料入口压强变化和燃料热值(分别用F3,F4表示)变化同物料入口温度及压强(分别用F1,F2表示)变化的作用方向相反时,例如当F1和F2的作用为减,而F3和F4的作用为曾时,F1和F2的作用使得物料的出口温度减小,通过温度变送器1的反馈作用,使得主调节器的输入增加,而相应的主调节器的输出也相应增加(即副控制环的给定值曾大,也即增大燃料进入阀的开度)。
在副控制环中引入的干扰信号F3和F4的作用下,炉膛内的温度增加,通过温度变送器2的反馈作用,使得副控制器的输入减小(即有减小燃料进入阀开度的趋势)。
同样可推出,当F1和F2的作用为曾,而F3和F4的作用为减时,主调节器有减小燃料进入阀开度的趋势,而副调节器有增大燃料进入阀开度的趋势。
主调节器和副调节器的这种相反的控制作用在某种程度上相互抵消,可以有效的抑制外界的干扰。
燃料1TTTT2T T 1T C 2T C物料出口温度1()t θ综上分析可知,串级控制系统不仅有较好的时间特性,而且还有较好的抗干如性能和动态性能。
2.3系统硬件及调节器选择在串级控制系统中,主副调节器所起的作用是不同的。
主调节器起定值控制作用,而副调节器起随动控制作用。
主参数是生产工艺的主要控制指标,它关系到所生产的产品的质量,一般都有较严格的工艺要求——不允许有残差,同时又由于要控制的工业过程有较大的容量滞后,所以主调节器通常选择PID 型调节器以实现主参数的无差控制。
而在串级控制系统中,稳定副参数并不是目的。
控制副参数是为了保证和提高主参数的控制质量,对副参数的要求一般没有像主参数那样的严格,可以在一定的范围内变化,允许有残差。
因此,副调节器一般选P 调节器。
为了能够快速的跟踪主调节器的输出,一般不引入积分环节,因为积分环节会延长调节过程,减弱副回路的快速特性。
副调节器一般也不引入微分环节,因为当调节器有微分环节时,主调节器输出稍有变化,就容易引起调节阀有较大的开度变化,对系统的稳定性能不利。
综上所述,主调节器应选用PID 型调节器,副调节器选用P 型调节器。
要使一个过程控制系统能正常的运行,系统必须构成一个负反馈。
因此,在串级控制系统中,主调节器和副调节器的正反作用方式的选择原则是使整个系统构成负反馈。
从生产工艺安全角度出发,燃料进入调节阀应选用气开式(正作用),即一旦出现故障或冷物料流入中断,调节阀完全关闭,切断燃料的输入,确保管式加热炉的安全。
由管式加热炉的工作原理可知,对于副调节器,当炉膛温度升高时,温度变送器2的测量信号增大,为了保证副控制回路为负反馈,则要使得副调节器的输出信号减小。
按照测量信号增大,输出信号减小的原则,副调节器应为反作用方式。
对于主调节器,当副参数炉膛温度升高时,主控参数物料出口温度也升高,而温度变送器一般都是正作用方式,故温度变送器1的测量信号也增大,为了保证主控制回路也为负反馈,要求主调节器的输出信号减少,按照测量信号增大,输出信号减小的原则,主调节器也应为反作用方式。
各个环节的正反作用如下图5所示。
图中“+”表示为正作用,“-”表示为反作用。
图5 管式加热炉温度串级控制系统各环节正反作用图根据以上的分析选择好相应的硬件后,构建管式加热炉温度串级控制系统。
3控制仪表及技术参数3.1主控制器软件设计管式加热炉温度串级控制系统主回路简化方框图如图6所示。
主控制器温度变送器1广义被控对象+-R(t)E(t)U(t)Y(t)图6 串级控制系统主回路简化方框图 对于主控制器采用数字PID 控制算法的选择由两种:位置型和增量型。
位置型PID 控制数学表达式如下:0()(1)()[()()]k p D i I T E k E k U k K E k E i T T T=--=+∑+ 增量型PID 控制数学表达式如下:()[()(1)]()[()2(1)(2)]D p pp I T T U k K E k E k K E k K E k E k E k T T ∆=--++--+- 物料出口温度1()t θ1TT TT 2T T1T C 2T C 燃料 物料入口管式加热炉 ++ + —— ——令0(1)D p I T T q K T T=++,1(12)D p T q K T =-+,2D p T q K T =则 012()()(1)(2)U k q E k q E k q E k ∆=+-+-012()(1)()(1)()(1)(2)U k U k U k U k q E k q E k q E k =-+∆=-++-+-比较两种数字PID 控制的数学表达式可知,增量型控制算法不需要做累加,控制量的增量的确定仅与最近几次误差采样值有关,计算误差和计算精度问题对控制量的计算影响较小。