加热炉出口温度控制系统设计
管式加热炉温度-流量串级控制系统的设计

管式加热炉温度-流量串级控制系统的设计1方案选定管式加热炉是炼油、化工生产中的重要装置之一,它的任务是把原料油加热到一定温度,以保证下道工序的顺利进行。
因此,常选原料油出口温度1tθ()为被控参数、燃料流量为控制变量,构成如图1-1所示的温度控制系统,控制系统框图如图1-2所示。
影响原料油出口温度1tθ()的干扰有原料油流量1()f t、原料油入口温度2()f t、燃料压力3()f t、燃料压力4()f t等。
该系统根据原料油出口温度1tθ()变化来控制燃料阀门开度,通过改变燃料流量将原油出口温度控制在规定的数值上,是一个简单控制系统。
图1-1 管式加热炉出口单回路温度控制系统图1-2 管式加热炉出口温度单回路控制系统框图由图1-1可知,当燃料压力或燃料热值变化时,先影响炉膛温度,然后通过传热过程逐渐影响原料油的出口温度。
从燃料流量变化经过三个容量后,才引起原料油出口温度变化,这个通道时间常数很大,约有15min ,反应缓慢。
而温度调节器1T C 是根据原料油的出口温度1()t θ与设定值的偏差进行控制。
当燃料部分出现干扰后,图1-1所示的控制系统并不能及时产生控制作用,克服干扰对被控参数1()t θ的影响,控制质量差。
当生产工艺对原料油出口温度1()t θ要求严格时,上述简单控制系统很难满足要求。
燃料在炉膛燃烧后,首先引起炉膛温度2()t θ变化,再通过炉膛与原料油的温差将热量传给原料油,中间还要经过原料油管道管壁。
显然,燃料量变化或燃料热值变化,首先使炉膛温度发生改变。
如果以炉膛温度作为被控参数组成单回路控制系统,会使控制通道容量滞后减少,时间常数约为3min ,对来自燃料的干扰3()f t 、4()f t 的控制作用比较及时,对应的控制系统如图1-3所示。
系统框图如图1-4。
但问题是炉膛温度2()t θ毕竟不能真正代表原料油出口温度1()t θ,即使炉膛温度恒定,原料油本身的流量或入口温度变化仍会影响原料油出口温度,图1-3 管式加热炉炉膛温度控制系统这是因为来自原料油的干扰1()f t 、2()f t 并没有包含在图1-4所示的控制系统(反馈回路)之内,控制系统不能克服1()f t 、2()f t 对原料油出口温度的影响,控制效果仍达不到生产工艺要求。
加热炉出口温度与燃料油压力串级控制系统
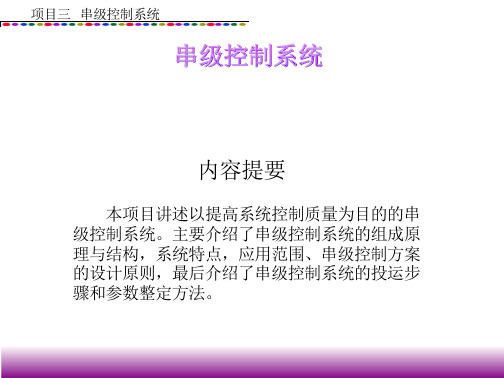
项目三 串级控制系统
串级控制系统
内容提要
本项目讲述以提高系统控制质量为目的的串 级控制系统。主要介绍了串级控制系统的组成原 理与结构,系统特点,应用范围、串级控制方案 的设计原则,最后介绍了串级控制系统的投运步 骤和参数整定方法。
项目三 串级控制系统
在简单反馈回路中增加了计算环节、控制环 节或其他环节的控制系统统称为复杂控制系统。 复杂控制系统的种类较多,按其所满足的控制要 求可分为两大类:
从上述分析中可以看出,在串级控制系统中,由于引入了一 个副回路,因而能及早克服从副回路进入的二次扰动对主变量的 影响,又能保证主变量在其他扰动(一次扰动)作用下能及时加 以控制,因此能大大提高系统的控制质量,以满足生产的要求。
项目三 串级控制系统
3.2 串级控制系统的特点
从总体来看,串级控制系统仍然是一个定值控制系统。 但是和简单控制系统相比,串级控制系统在结构上增加了一 个与之相连的副回路,因此具有很多特点,如下所述。
图3.3 加热炉温度串级控制系统方框图
项目三 串级控制系统
3.1.2 串级控制系统的结构
1.方框图 串级控制系统是一种常用的复杂控制系统,它是根据系统
结构命名的。串级控制系统由两个控制器串联连接组成,其中一 个控制器的输出作为另一个控制器的设定值。 如图3.4所示,为串级控制系统的通用原理方框图。由该图 可以看出,串级控制系统在结构上具有以下特征: (1)将原被控对象分解为两个串联的被控对象; (2)中间变量为副被控变量,称为副控制系统; (3)以原对象的输出信号为主被控变量,构成一个主控制系 统,称为主控制系统、主回路或主环; (4)主控制系统中控制器的输出信号作为副控制系统控制器 的设定值; (5)主回路是定值控制系统,副回路是随动控制系统。
加热炉温度串级控制系统设计

加热炉温度串级控制系统设计摘要:温度控制系统广泛应用于工业控制领域,如钢铁厂、化工厂、火电厂等锅炉的温度控制系统,电焊机的温度控制系统等。
加热炉温度控制在许多领域中得到广泛的应用。
生产自动控制过程中 ,随着工艺要求 ,安全、经济生产不断提高的情况下 ,简单、常规的控制已不能适应现代化生产。
传统的单回路控制系统很难使系统完全抗干扰。
串级控制系统具备较好的抗干扰能力、快速性、适应性和控制质量,因此在复杂的过程控制工业中得到了广泛的应用.对串级控制系统的特点和主副回路设计进行了详述,设计了加热炉串级控制系统,并将基于MATLAB的增量式PID算法应用在控制系统中。
结合基于计算机控制的PID参数整定方法实现串级控制,控制结果表明系统具有优良的控制精度和稳定性。
关键词:干扰串级控制主回路副回路Abstract:Automatic control of production process, with the technical requirements, security, economic production rising cases, simple, conventional control can not meet the modern production. The traditional single-loop control system is difficult to make the system completely anti-interference. Cascade control system with good anti-jamming capability, rapidity, flexibility and quality control, and therefore a complex process control industry has been widely used. Cascade control system of the characteristics and the main and sub-loop design was elaborate, designed cascade control system, furnace, and MATLAB-based incremental PID algorithm is applied in the control system. Combination of computer-based control method to achieve PID parameter tuning cascade control, control results show that the system has excellent control accuracy and stabilityKeywords:Cascade control, interference, the main circuit, the Deputy loop目录1.前言 (2)2、整体方案设计 (3)2.1方案比较 (3)2.2方案论证 (6)2.3方案选择 (7)3、串级控制系统的特点 (8)4. 温度控制系统的分析与设计 (9)4.1控制对象的特性 (9)4.2主回路的设计 (10)4.3副回路的选择 (10)4.4主、副调节器规律的选择 (10)4.5主、副调节器正反作用方式的确定 (10)5、控制器参数的工程整定 (12)6 、MATLAB系统仿真 (13)6.1系统仿真图 (13)6.2副回路的整定 (15)6.3主回路的整定 (16)7.设计总结 (18)【参考文献】 (19)11.前言随着我国国民经济的快速发展,加热炉的使用范围越来越广泛。
基于PLC控制的加热炉温度控制系统设计

基于PLC控制的加热炉温度控制系统设计概述加热炉是工业生产中常见的设备之一,其主要作用是提供高温环境用于加热物体。
为了确保加热炉的稳定性和安全性,需要设计一个可靠的温度控制系统。
本文将介绍一个基于PLC(可编程逻辑控制器)控制的加热炉温度控制系统设计方案。
系统设计原理在加热炉温度控制系统中,PLC作为核心控制器,通过监测温度传感器的输出信号,根据预设的温度设定值和控制策略,控制加热炉的加热功率,从而实现对加热炉温度的稳定控制。
以下是系统设计的主要步骤:1.硬件设备选择:选择适合的温度传感器和控制元件,如热电偶、温度控制继电器等。
2.PLC选型:根据实际需求,选择合适的PLC型号。
PLC需要具备足够的输入输出点数和计算能力。
3.传感器连接:将温度传感器接入PLC的输入端口,读取实时温度数据。
4.温度控制策略设计:根据加热炉的特性和工艺需求,设计合适的温度控制策略。
常见的控制策略包括比例控制、积分控制和微分控制。
5.控制算法实现:根据温度控制策略,编写PLC程序,在每个采样周期内计算控制算法的输出值。
6.加热功率控制:使用控制继电器或可调功率装置,控制加热炉的加热功率。
7.温度反馈控制:通过监测实际加热炉温度和设定值之间的差异,不断修正加热功率控制,使加热炉温度稳定在设定值附近。
系统硬件设计基于PLC控制的加热炉温度控制系统的硬件设计主要包括以下几个方面:1.温度传感器:常用的温度传感器有热电偶和热敏电阻。
根据加热炉的工艺需求和温度范围,选择适合的温度传感器。
2.PLC:选择适合的PLC型号,根据实际需求确定PLC的输入输出点数和计算能力。
3.控制继电器或可调功率装置:用于控制加热炉的加热功率。
根据加热炉的功率需求和控制方式,选择合适的继电器或可调功率装置。
4.运行指示灯和报警器:用于显示系统的运行状态和报警信息。
PLC程序设计PLC程序是基于PLC的加热炉温度控制系统的关键部分,其主要功能是实现温度控制算法。
加热炉出口温度控制系统的设计
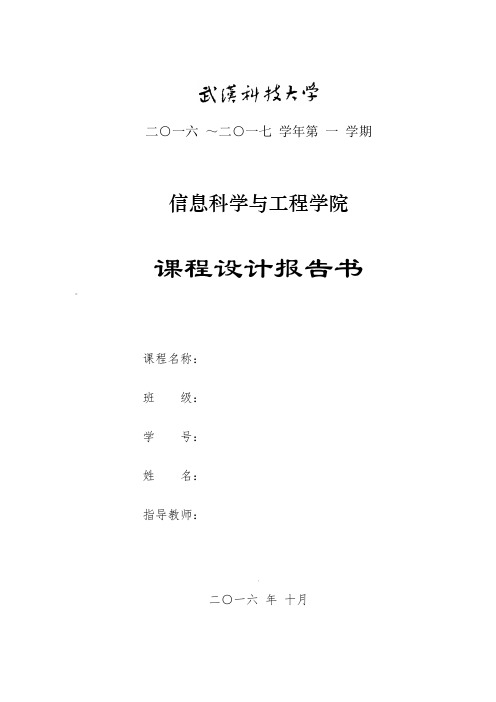
二○一六~二○一七学年第一学期信息科学与工程学院课程设计报告书<课程名称:班级:学号:姓名:指导教师:,二○一六年十月1. 设计题目加热炉出口温度控制系统的设计2. 设计任务图1所示为某工业生产中的加热炉,其任务是将被加热物料加热到一定温度,然后送到下道工序进行加工。
加热炉工艺过程为:被加热物料流过排列炉膛四周的管道后,加热到炉出口工艺所要求的温度。
在加热用的燃料油管道上装有一个调节阀,用以控制燃料油流量,以达到控制出口温度的目的。
被加热物料图1 加热炉出口温度系统,但是,由于炉子时间常数大,而且扰动的因素多,单回路反馈控制系统不能满足工艺对炉出口温度的要求。
为了提高控制质量,采用串级控制系统,运用副回路的快速作用,有效地提高控制质量,满足生产要求。
3. 设计要求1)绘制加热炉出口温度单回路反馈控制系统结构框图。
2)以加热炉出口温度为主变量,选择滞后较小的炉膛温度的副变量,构成炉出口温度对炉膛温度的串级控制系统,要求绘制该串级控制系统结构图。
3)假设主对象的传递函数为)2)(1(1)(01++=s s s G ,副对象的传递函数为)1(1)(02+=s s G ,主、副控制器的传递函数分别为sK s G c c 21)(11+=,22)(c c K s G =,1)()(21==s G s G m m ,请确定主、副控制器的参数(要求写出详细的参数估算过程)。
4)利用simulink实现单回路系统仿真和串级系统仿真,分别给出系统输出响应曲线。
一.单回路反馈控制系统的设计单回路反馈控制系统结构框图原料出口温度T受进入管式加热炉原料的初始温度和进入流量和燃烧值的影响。
在原料流量一定的情况下,在燃料入口处安装一个调节阀,控制进入管式加热炉的燃料流量,调节阀的开度大小由原料出口温度值控制,构成管式加热炉的燃料流量,调节阀的开度大小由原料出口温度值控制,构成管式加热炉出口温度单回路反馈控制系统。
二.串级控制系统的设计单回路控制系统的控制效果较差,很难达到满意的效果。
化工用加热炉出口温度控制和热平衡监测系统
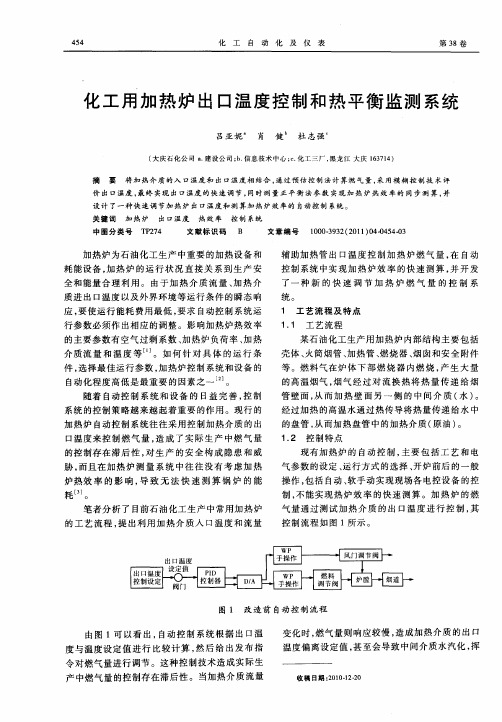
介 质流 量 和 温 度 等 … 。如 何 针 对 具 体 的 运 行 条
件, 选择 最佳 运行 参数 , 加热 炉控 制系统 和设 备 的 自动化程 度 高低是 最重 要 的 因素 之一 。 随着 自动控制 系统 和 设 备 的 日益完 善 , 制 控 系统 的控 制 策略越 来越 起着 重要 的作 用 。现 行 的 加 热炉 自动 控制 系统往 往采 用控 制加 热介质 的出 口温度 来控 制 燃气 量 , 成 了实 际 生产 中燃 气 量 造
温 度偏离 设定 值 , 至会 导致 中间介 质水 汽化 , 甚 挥
产 中燃气 量 的控制 存在 滞后性 。当加热 介质 流量
收稿 日期 :0 0 1 -0 2 1 - 2 2
第 4期
吕亚 妮 等 . 工 用 加 热 炉 出 口温 度 控 制 和 热 平 衡 监 测 系 统 化
45 5
发 出来 大 量水 蒸 汽 造 成 炉 腔 内 压力 升 高 , 压 力 当 升 高 到报 警设定 值 时 , 安全 阀打 开 , 燃气 加热 炉 向
辅助加 热管 出 口温 度 控 制 加热 炉 燃 气 量 , 自动 在 控制 系统 中实 现加 热 炉 效 率 的快 速 测算 , 开发 并
了一 种 新 的 快 速 调 节 加 热 炉 燃 气 量 的 控 制 系
统。 1 工 艺 流 程 及 特 点 1 1 工 艺 流 程 .
行参 数必 须作 出相 应 的调整 。影 响加 热炉热 效 率
外 排 出蒸 汽 。
要 因素情 况 下 , 过 直 接 测 量 介 质 的 流 量 得 到 实 通 测 热效 率 。用 正平 衡法 测定 加 热炉效 率 是一 种 直
马化腾管式加热炉出口温度单回路控制系统设计
目录一、管式加热炉的概论 (2)二、管式加热炉的意义 (3)2.1管式加热炉简介..................................... 错误!未定义书签。
2.2设计目的及意义 (4)三、管式加热炉温度控制系统工艺流程及控制要求 (4)3.1控制系统的简介 (4)3.2管式加热炉任务 (5)3.3控制系统的构成 (6)四、各仪表的选取及元器件清单 (6)4.1温度变送器 (6)4.2温度检测元件 (7)4.3调节阀 (8)4.4保护系统 (9)五、控制算法及系统仿真 (9)六、心得体会 (12)参考文献 (13)一、管式加热炉的概论管式加热炉是一种直接受热式加热设备,主要用于加热液体或气体化工原料,所用燃料通常有燃料油和燃料气。
管式加热炉的传热方式以辐射传热为主,管式加热炉通常由以下几部分构成:辐射室:通过火焰或高温烟气进行辐射传热的部分。
这部分直接受火焰冲刷,温度很高(600-1600℃),是热交换的主要场所(约占热负荷的70-80%)。
对流室:靠辐射室出来的烟气进行以对流传热为主的换热部分。
燃烧器:是使燃料雾化并混合空气,使之燃烧的产热设备,燃烧器可分为燃料油燃烧器,燃料气燃烧器和油一气联合燃烧器。
通风系统:将燃烧用空气引入燃烧器,并将烟气引出炉子,可分为自然通风方式和强制通风方式。
管式加热炉,包括加热炉本体和余热回收系统,余热回收系统包括空气预热器,其中空气预热器由非冷凝式空气预热器和冷凝式空气预热器两段组成,余热回收系统中另设有冷凝液收集池、引风机和鼓风机,冷凝液收集池直接设在冷凝式空气预热器下方,冷凝液收集池与引风机相连接,鼓风机与冷凝式空气预热器相连。
使用本发明所提供的加热炉,其加热炉的排烟温度可降低到100℃左右,实现烟气中含酸水蒸气的部分冷凝,且在回收烟气低温显热的同时,能回收部分含酸水蒸气的汽化潜热,进一步提高加热炉热效率,节约能源。
一种管式加热炉,包括加热炉本体和余热回收系统,加热炉本体内设置有烟囱档板,加热炉本体于烟囱档板下方设置有高温烟气出口,余热回收系统包括空气预热器,其特征在于:空气预热器由非冷凝式空气预热器和冷凝式空气预热器两段组成,非冷凝式空气预热器上设置有非冷凝式空气预热器烟气入口、非冷凝式空气预热器空气出口、非冷凝式空气预热器烟气出口和非冷凝式空气预热器空气入口,内部设有非冷凝式空气预热器调节档板,非冷凝式空气预热器烟气入口通过高温烟气管道与加热炉本体上的高温烟气出口相连,冷凝式空气预热器上设有冷凝式空气预热器烟气入口、冷凝式空气预热器空气出口和冷凝式空气预热器空气入口,内部设有冷凝式空气预热器调节档板,非冷凝式空气预热器烟气出口与冷凝式空气预热器烟气入口之间通过两预热器间烟气管道相连,非冷凝式空气预热器空气入口与冷凝式空气预热器空气进口之间通过两预热器间空气管道相连,余热回收系统中另设有冷凝液收集池、引风机和鼓风机,冷凝液收集池直接设在冷凝式空气预热器下方,引风机与冷凝液收集池相连接,鼓风机与冷凝式空气预热器相连。
管式加热炉出口温度串级控制系统设计说明
课程设计任务书目录1 管式加热炉概述 (1)1.1管式加热炉在石油工业中的重要性 (1)1.2管式加热炉的基本构成与组成 (1)1.3管式加热炉出口温度控制系统设计目的及意义 (1)2 管式加热炉温度控制系统工作原理及控制要求 (2)2.1 管式加热炉出口温度控制系统工作原理..................... ........ . (2)2.2 管式加热炉出口温度控制系统控制要求 (2)3 管式加热炉出口温度控系统工艺流程设计 (2)3.1 管式加热炉出口温度影响因素的扰动分析 (2)3.2 管式加热炉出口温度控制系统的工艺流程设计 (2)4 管式加热炉出口温度控系统现场仪表的选型与连线图 (3)4.1 控制系统中温度检测元件的选型 (3)4.2 控制系统中变送器的选型 (4)4.3 控制系统中执行器(调节阀)的选型 (4)4.4 控制系统中调节器的选型 (5)4.5 控制系统中的连锁保护与接线图 (6)5管式加热炉出口温度串级控制系统分析 (7)5.1 控制系统方框图与工作过程 (7)5.2 主、副调节器规律选择 (7)5.3 主、副调节器正反作用方式确定 (7)5.4 控制器参数工程整定 (8)6 管式加热炉出口温度串级控制系统的MATLAB SIMULINK仿真与分析 (9)6.1传递函数的选择 (9)6.2系统的参数的选择 (9)6.3系统的仿真分析 (10)7 感受与体会 (11)8参考文献 (11)1 管式加热炉概述1.1管式加热炉在石油工业中的重要性⑴加热温度高(火焰温度1000℃以上),传热速率快。
⑵是整个石油加工和石油化工过程中能耗最大的设备之一。
⑶是控制运转周期及自动化及自动化程度的关键设备。
1.2管式加热炉的基本构成与组成管式加热炉是一种直接受热加热设备主要用于加热气体或液体化工原料,所用燃料通常有燃料油和燃料气。
管式加热炉的传热方式以辐射传热为主。
管式加热炉一般由辐射室、余热回收系统、对流室、燃烧器和通风系统等五部分组成,如图1所示。
电阻加热炉温度控制系统设计
电阻加热炉温度控制系统设计一、温度控制系统的要求:1.稳定性:系统应能快速响应温度变化,并能在设定温度范围内保持稳定的温度。
2.精度:控制系统应具备高精度,确保炉内温度与设定温度的偏差控制在允许范围内。
3.可靠性:系统应具备高可靠性,能长时间稳定运行,并能在发生异常情况时及时报警或自动停止加热。
4.人机界面:温度控制系统应提供方便直观的人机界面,操作简单易懂。
二、温度控制系统的设计:1.传感器选择:选择合适的温度传感器进行温度检测。
常用的温度传感器有热电偶和热电阻。
根据实际需求选择合适的传感器类型和量程。
2.温度控制器选择:根据控制需求,选择适用于电阻加热炉的温度控制器。
具备温度显示功能的控制器可以直观地显示炉内温度。
还可以选择具备PID控制功能的控制器,以提高温度控制精度。
3.控制循环设计:将温度控制系统设计成闭环控制系统,以实现炉内温度的精确控制。
控制循环包括采样、比较、控制和执行四个环节。
采样环节将实际温度值与设定温度值进行比较,然后控制环节根据比较结果输出控制信号,最后执行环节根据控制信号调节电阻加热炉的加热功率。
4.温度传感器布置:将温度传感器布置在炉内合适位置,确保能够准确测量到炉内温度。
传感器的安装位置应避免热点和冷点,以避免温度不均匀。
5.控制参数调整:根据实际情况进行PID参数的调整。
通过实验或仿真等方法,逐步调整PID参数,使得系统能够快速响应温度变化、准确跟踪设定温度,并保持稳定的温度输出。
6.报警和保护设计:设计温度控制系统时,应考虑到电阻加热炉的过热或温度异常等情况,并设置相应的报警和保护功能。
当温度超过安全范围时,系统应及时报警,并自动停止加热。
7.人机界面设计:为了方便操作和监控,可以在温度控制系统上设置触摸屏或显示屏。
通过人机界面,操作人员可以方便地设定温度、监测炉内温度,并能够实时查看温度曲线和报警信息。
总之,电阻加热炉温度控制系统的设计需要考虑到温度控制精度、稳定性、可靠性和人机界面等方面的要求。
加热炉出口温度与炉膛温度串级控制系统设计
加热炉出口温度与炉膛温度串级控制系统设计一、引言加热炉是一种常用于工业生产中的设备,其作用是通过燃烧燃料加热空气或其他介质,使其达到所需温度。
加热炉的出口温度和炉膛温度是评估加热炉性能的关键指标。
为了提高加热炉的控制精度和稳定性,需要设计出一个合理的加热炉出口温度与炉膛温度串级控制系统。
二、串级控制系统的基本原理串级控制系统是一种将两个或以上的控制回路串接在一起,将一个控制器的输出作为另一个控制器的输入,通过不同层次的控制,实现对被控对象的精确控制。
在加热炉出口温度与炉膛温度串级控制系统中,可以将炉膛温度作为外环控制,将加热炉出口温度作为内环控制。
三、串级控制系统的设计步骤1.确定控制目标:在此串级控制系统中,控制目标是将加热炉出口温度控制在一定范围内,并同时保持炉膛温度稳定。
2.确定输入变量和输出变量:输入变量为控制器输出信号,输出变量为加热炉出口温度。
3.系统的数学模型:确定加热炉出口温度与炉膛温度之间的动态关系,建立数学模型。
可以采用传统的PID控制器或者现代控制理论中的模型预测控制等方法。
4.设计外环控制器:外环控制器根据炉膛温度的反馈信号调整燃料供给,以控制炉膛温度的稳定性。
5.设计内环控制器:内环控制器根据外环控制器的输出信号和加热炉出口温度的反馈信号调整燃料供给,以控制加热炉出口温度。
6.仿真与优化:使用仿真软件对设计的串级控制系统进行仿真,观察系统的响应特性,并根据实际需求进行调整和优化。
7.实际系统应用:将优化后的串级控制系统应用到实际加热炉中,并进行调试和验证。
四、串级控制系统的优势1.提高控制精度:串级控制系统将控制精度分为两个层次进行控制,可以快速响应外环控制器的调整,从而提高系统的控制精度。
2.提高稳定性:串级控制系统通过多层次的控制,减少了外界扰动对系统稳定性的影响。
3.提高动态响应速度:串级控制系统可以根据内环的控制效果对外环的控制进行调整,从而实现更快的动态响应。
- 1、下载文档前请自行甄别文档内容的完整性,平台不提供额外的编辑、内容补充、找答案等附加服务。
- 2、"仅部分预览"的文档,不可在线预览部分如存在完整性等问题,可反馈申请退款(可完整预览的文档不适用该条件!)。
- 3、如文档侵犯您的权益,请联系客服反馈,我们会尽快为您处理(人工客服工作时间:9:00-18:30)。
吉林建筑大学城建学院课程设计报告题目名称加热炉出口温度控制系统设计院(系)电气工程及其自动化课程名称过程控制工程课程设计班级电气13-1学号学生姓名指导教师起止日期2016.6.20-2016.7.1成绩目录摘要 (Ⅰ)ABSTRACT (Ⅱ)第1章绪论 (1)1.1 设计目的 (1)1.2 设计任务 (1)1.3加热炉温度控制系统简介 (1)1.4加热炉温度控制系统的发展 (2)第2章对象模型建立 (4)2.1 建立数学模型 (4)2.2控制系统分析 (5)第3章系统设备选型 (6)3.1 测量变送器和传感器的选择 (6)3.2执行器的选择 (6)3.3控制器的选择 (6)第4章控制器参数整定及Simulink仿真 (9)4.1控制器参数整定 (9)4.2Simulink仿真 (11)结论 (12)致谢 (13)参考文献 (14)摘要随着我国国民经济的快速发展,加热炉的使用范围越来越广泛。
随着网络技术的发展和整个工厂完全实现两级自动化管理,在过程级上通过相应的终端了解任何一个设备或任何一个装置的控制情况以及生产情况。
过程控制系统在加热炉系统中得到广泛的应用,它是加热炉控制系统的重要部分,是对以及控制系统的一个总领和扩充。
现代加热炉的生产过程可以实现高度的过程控制,以保证在加热过程中温度的准确控制,这就为工业生产提供了有利条件。
加热炉是工业生产中的一个重要装置,它的任务是把原料加热到一定温度,以保证下道工序的顺利进行。
因此加热炉的温度控制起着举足轻重的作用。
关键词:加热炉;过程控制系统;温度控制ABSTRACTWith the rapid development of China's national economy, the use of heating furnace is more and more extensive. With the development of network technology and the whole factory to achieve two level of automation management, in the process level through the corresponding terminal to understand any equipment or any one of the control of the device and the production situation. Process control system has been widely used in the heating furnace system, it is heating furnace control system is an important part of, and the control system of a consul general and expand. The production process of modern heating furnace can realize high process control, so as to ensure the accurate temperature control during the heating process, which provides favorable conditions for industrial production. Heating furnace is an important device in industrial production, it is the task of heating raw materials to a certain temperature, in order to ensure the smooth progress of the next process. So the temperature control of the heating furnace plays an important role.Keywords:Reheating furnace; process control system; temperature control第1章绪论1.1设计目的通过过程控制工程课程设计能从中学会从工程角度思考问题,熟悉本专业领域的过程控制仪表系统设计,学会过程控制系统各环节额的组合作用,学会对温度控制仪表的正确接口、温度信号调理、线性化、校准及常用的控制方法。
1.2设计任务在工业生产中经常要对加热炉出口温度进行控制,为了能够精确控制温度,保证正常生产,要求设计温度闭环反馈控制系统,能抑制波动,且系统无余差。
要求设计一个加热炉出口温度闭环反馈控制系统,采用适合的控制算法,输入设定温度值,并实时显示当前温度值。
1.3加热炉温度控制系统简介随着节能技术不断发展,加热炉节能控制系统正日趋完善。
以燃烧过程数学模型为依据建立的最佳燃烧过程计算机控制方案已进入实用阶段。
例如,按燃烧过程稳态数学模型组成的微机控制系统已开始在炼油厂成功使用。
有时利用计算机实现约束控制,使加热炉经常维持在约束条件边界附近工作,以保证最佳燃烧。
随着建立燃烧模型工作的进展和计算机技术的应用,加热炉燃烧过程控制系统将得到进一步的完善。
影响加热炉出口温度的干扰因素很多,炉子的动态响应一般都比较迟缓,因此加热炉温度控制系统多选择串级和前馈控制方案。
根据干扰施加点位置的不同,可组成多参数的串级控制。
使用气体燃料时,可以采用浮动阀代替串级控制中的副调节器,还可以预先克服燃料气的压力波动对出口温度的影响。
这种方案比较简单,在炼油厂中应用广泛。
随着科学技术的进步,自动控制技术在各个应用领域中的应用已日渐广泛,不但使得生产设备或生产过程实现自动化,大大提高了劳动生产率和产品质量,改善了劳动条件,还在人类征服大自然,改善居住条件等方面发挥了非常重要的作用。
自动控制(automatic control)是指在没有人直接参与的情况下,利用外加的设备或装置,使机器、设备或生产过程的某个工作状态或参数自动地按照预定的规律运行。
自动控制是相对人工控制概念而言的。
指的是在没人参与的情况下,利用控制装置使被控对象或过程自动地按预定规律运行。
1.4加热炉温度控制系统的发展自动控制理论是研究自动控制共同规律的技术科学,是分析和设计自动控制系统的理论的基础。
它的发展初期,是以反馈理论为基础的自动调节原理,主要用于工业控制,二战期间为了设计和制造飞机及船用自动驾驶仪,火炮定位系统,雷达跟踪系统以及其他基于反馈原理的军用设备,进一步促进并完善了自动控制理论的发展。
自动控制理论是研究自动控制共同规律的技术科学,是分析和设计自动控制系统的理论的基础。
到战后,已形成完整的自动控制理论体系,这就是以传递函数为基础的经典控制理论,它主要研究单输入-单输出,线形定常系统的分析和设计问题。
自动控制理论的发展历程如下:1.40年代--60年代初需求动力:市场竞争,资源利用,减轻劳动强度,提高产品质量,适应批量生产需要。
主要特点:此阶段主要为单机自动化阶段,主要特点是:各种单机自动化加工设备出现,并不断扩大应用和向纵深方向发展。
典型成果和产品:硬件数控系统的数控机床。
2.60年代中--70年代初期需求动力:市场竞争加剧,要求产品更新快,产品质量高,并适应大中批量生产需要和减轻劳动强度。
主要特点:此阶段主要以自动生产线为标志,其主要特点是:在单机自动化的基础上,各种组合机床、组合生产线出现,同时软件数控系统出现并用于机床,CAD、CAM等软件开始用于实际工程的设计和制造中,此阶段硬件加工设备适合于大中批量的生产和加工。
典型成果和产品:用于钻、镗、铣等加工的自动生产线。
3.70年代中期--至今需求动力:市场环境的变化,使多品种、中小批量生产中普遍性问题愈发严重,要求自动化技术向其广度和深度发展,使其各相关技术高度综合,发挥整体最佳效能。
自动控制理论是研究自动控制共同规律的技术科学,是分析和设计自动控制系统的理论的基础。
主要特点:自70年代初期美国学者首次提出CIM概念至今,自动化领域已发生了巨大变化,其主要特点是:CIM已作为一种哲理、一种方法逐步为人们所接受;CIM 也是一种实现集成的相应技术,把分散独立的单元自动化技术集成为一个优化的整体。
所谓哲理,就是企业应根据需求来分析并克服现存的“瓶颈”,从而实现不断提高实力、竞争力的思想策略;而作为实现集成的相应技术,一般认为是:数据获取、分配、共享;网络和通信;车间层设备控制器;计算机硬、软件的规范、标准等。
同时,并行工程作为一种经营哲理和工作模式自80年代末期开始应用和活跃于自动化技术领域,并将进一步促进单元自动化技术的集成。
典型成果和产品:CIMS工厂,柔性制造系统(FMS)。
随着现代应用数学新成果的推出和电子计算机的应用,为适应自动控制、宇航技术的发展,自动控制理论跨入了一个新阶段——现代控制理论。
主要研究具有高性能,高精度的多变量多参数的最优控制问题,主要采用的方法是以状态为基础的状态空间法。
目前,自动控制理论还在继续发展,正向以控制论,信息论,仿生学为基础的智能控制理论深入。
为了实现各种复杂的控制任务,首先要将被控制对象和控制装置按照一定的方式连接起来,组成一个有机的总体,这就是自动控制系统。
在自动控制系统中,被控对象的输出量即被控量是要求严格加以控制的物理量,它可以要求保持为某一恒定值,例如温度,压力或飞行航迹等;自动控制理论是研究自动控制共同规律的技术科学,是分析和设计自动控制系统的理论的基础。
而控制装置则是对被控对象施加控制作用的机构的总体,它可以采用不同的原理和方式对被控对象进行控制,但最基本的一种是基于反馈控制原理的反馈控制系统。
在反馈控制系统中,控制装置对被控装置施加的控制作用,是取自被控量的反馈信息,用来不断修正被控量和控制量之间的偏差从而实现对被控量进行控制的任务,这就是反馈控制的原理。
第2章对象模型建立2.1建立数学模型我们用系统辨识法—响应曲线法对加热炉出口温度控制系统建立数学模型。
根据表2-1确定响应曲线,并计算出被控对象的传递函数。
表2-1 由输出温度变化图2-1 响应曲线由阶跃响应曲线确定控制系统为一阶,则加热炉出口温度控制系统为单回路控制系统,并由此确定一阶纯滞后惯性环节的参数: 滞后常数:2=τ; 时间常数:120=T ; 放大系数:1)0()(00=-∞=x y y K ;被控过程数学模型:s s e s e s T K s W 200011211)(--+=+=τ。