冷轧带钢生产线技术解析
冷轧带钢生产技术

冷轧带钢生产技术冷轧带钢生产线技术解析1、了解带钢:带钢是相对于钢卷,由中小型生产线冷轧工艺轧制而成的带钢产品。
冷轧带钢的用途可谓广泛,根据后期的加工方式,可以分为如下类型:(1) 带式:如打包带、铠装电缆用带等;(2) 管式:如薄壁管(含家具用管)、复合管、缠绕管等;(3) 冷弯型材:如滑轨、龙骨、塑钢内衬、电缆桥架;(4) 压型钢板:如卷帘门板、钢结构建筑围护用墙板、屋面板等;(5) 冲压用板:如电池壳体、汽车用板、家电用板等。
冷轧的关键工序:一为酸洗、二为冷轧、三为热处理、四为平整。
酸洗是为了去除对冷轧有害的原料钢卷表面上的氧化铁皮;冷轧是生产冷轧板带钢的关键工序;热处理在冷轧工序中有二个作用,一是消除冷轧带钢的加工硬化和残余应力,软化金属,改善塑性,以便于进一步进行冷轧或其它加工;二是改善组织结构,产生所需要的晶粒大小和取向;平整是精整工序中十分重要的工序,它可以改善带钢的性能,提高钢板的成形性能,提高钢带的平直度及改善钢板的表面状态。
冷轧工艺的定义:轧制是将金属坯料通过一对旋转轧辊的间隙(各种形状),因受轧辊的压缩使材料截面减小,长度增加的压力加工方法,这是生产钢材最常用的生产方式,冷轧即是在常温下完成的轧制过程,其所使用的原料为热轧加工成的板带(卷)。
2、酸洗工艺带钢冷轧前必须酸洗,清洗其表面氧化铁皮,因为氧化铁皮在冷轧时会损坏轧辊表面,而导致带钢表面产生缺陷。
通常热轧带钢表面氧化铁皮通常是3层结构:外层为Fe2O3(三氧化二铁),中层为Fe304(四氧化三铁),内层为Fe0(氧化铁)。
先进的冷轧厂多采用高速运行的连续酸洗机组或推拉式酸洗。
以连续酸洗为例,是将带钢连续地通过几个酸洗槽进行酸洗。
为使作业线上过程连续,将前一个热轧带钢卷的尾部和后一个钢卷头部焊接起来,酸洗后带钢按需要的卷重、卷径切断带钢并收卷。
连续酸洗机组除完成清除带钢表面氧化铁皮的任务外,还有几个作用:(1) 用圆盘剪将带钢侧边剪齐。
冷轧带肋钢筋成型机构造及使用要点

冷轧带肋钢筋成型机构造及使用要点1、概述冷轧带肋钢筋(俗称冷轧螺纹钢筋)是近几年进展起来的一种新型、高效、节能建筑用钢材,它以一般低碳盘条或低合金盘条,经多道冷轧或冷拔减径和一道压痕,最终形成带有二面或三面月牙形横肋的钢筋。
由于其强度高(其抗拉强度比热轧线材提高50%~100%),塑性好(一般冷拔的δ10≥2.5%,冷轧的δ10≥4%),握裹力强(与混凝土粘结锚固力量提高2~6倍),因而得到快速进展。
它广泛应用于工业与建筑,水泥电杆与输运管,高速大路与桥梁的路面钢网和防护网,水电站坝基与各建筑工程。
冷轧带肋钢筋可以用钢筋网片成型机焊成网运至施工现场进行混凝土浇灌作业,转变了手工扎绑的落后作业方法。
另外,冷轧带肋钢筋适合生产φ10mm以下的小规格螺纹钢筋,弥补了热轧螺纹钢筋品种少的不足。
2、冷轧带肋钢筋成型机的构造冷轧带肋钢筋生产线是对焊机、放线架、除锈机、润滑机、冷轧带肋钢筋成型机、拉拔机、应力消退机构、收线机及电器操作掌握系统等组成,不同生产线工艺选用的设备形式及台数不同。
目前冷轧带肋钢筋生产工艺主要有滑轮式和直进式两种。
放线架:依据不同需要,可采纳架空式、卧式、回转式开卷机,卷重可达500~2000Kg。
为保证平安,其后可设乱线开关。
除锈机:为了去除对冷轧不利的氧化铁皮,一般使用机械清理的反复弯曲法,有直线型和空间型,最大处理线径可达φ20mm。
弯曲式机械除锈设备结构简洁,成本低廉,不污染环境。
润滑机:用蜗杆送料器将润滑剂连续送至材料入口,进入拉轧工序。
润滑剂大多为硬质硅钙--钠型,也可使用肥皂粉加二硫化钼或使用乳化液。
轧制设备:冷轧带肋钢筋成型机为作业线主体设备,它有主动与被动两种。
主动连轧投入高,且要求孔型研磨、调整精确,一般不常用。
目前趋向使用以拉丝机带动的辊模进行被动轧制。
拉拔机:拉拔机是作业线的动力源。
可采纳单筒与双筒,卧式与立式拉拔机。
一般为延长其使用寿命,拉拔机卷筒工作表面部分涂以特别的硬化层。
冷轧工艺介绍

冷轧⼯艺介绍冷轧⼯艺介绍⼀、概述⾸先介绍什么是冷轧和热轧冷轧是以热轧板卷为原料,在常温下进⾏各种型材轧制;热轧是钢坯在加热炉内加热到⼀定温度(1250℃出炉)后进⾏各种型材轧制。
冷轧和热轧都属于轧钢⽣产,轧钢⽣产是将钢锭轧制成钢材的⽣产环节。
与⽣铁和钢⼀样,钢材的⽣产在国民经济中占有重要地位。
⽣产钢材的⽅法有轧制、锻造、挤压、拉拔等。
⽤轧制⽅法⽣产钢材,具有⽣产率⾼、品种多、⽣产过程连续性强、易于机械化⾃动化等优点。
因此,85~90%以上的钢材是在轧钢车间⽣产的。
从轧制的⼯艺和车间作⽤来看,轧钢车间可分成两⼤类。
⼀类是将钢锭轧成钢坯的钢坯车间,其作⽤是为后继的轧钢车间提供坯料。
另⼀类是将钢坯进⼀步轧成各种钢材的成品车间。
成品轧钢车间⽣产的钢材种类很多,根据钢材断⾯形状,⼤致可分为三⼤类:型钢、钢板和钢管。
随着轧制⼯艺和设备的不断发展,近年来,轻型超薄型钢、周期断⾯型钢、冷弯型钢、宽翼⼯字钢等产品得到了发展。
此外,机器制造、国防、铁路车辆、矿⼭等部门需要的某些零件⽑坯或零件,亦开始⽤轧制⽅法⽣产。
例如,滚动轴承⽤的滚珠、滚⼦、内座圈;球磨机⽤的钢球;机械传动中的齿轮、丝杠;铁路车辆⽤的车轮和轮箍等,这不仅可以提⾼这些产品的产量和质量,⽽且实现了⽆切削或少切削加⼯,节约了⾦属消耗,对某些产品来说,也⼤⼤改善了劳动条件。
⼆、带钢冷连轧机厚道0.1~1.2毫⽶⼀般采⽤冷轧⽅法。
⽬前冷连轧机组为5机架,出⼝速度35⽶/秒,钢卷最重达60吨。
连轧的轧制过程:轧制开始,先采⽤低速(约2~3⽶/秒)穿带,待钢带端部通过各架轧机并卷上卷取机卷筒后,整个机组同步升速到稳定轧制阶段。
当焊缝进⼊轧机时,为防⽌断带和损伤轧辊,通常需降速⾄稳定轧速的60~70%,过焊缝后,⼜⾃动升速⾄稳定轧速。
当⼀个卷快轧完后,轧机减⾄爬⾏速度以通过带钢尾部,最后停车。
⼤型冷连轧机组各机座之间的距离⼀般在4~4.3⽶左右。
三、轧机的主要设备轧机主要技术特性、轧机类型、轧辊尺⼨、最⼤轧制速度、⽤途(需要⾃⼰做⼀个全⾯了解,就不⼀⼀详细介绍)。
冷轧钢带生产中的工艺改进与创新

冷轧钢带生产中的工艺改进与创新冷轧钢带是一种常见的钢材产品,广泛应用于建筑、汽车、电子等行业。
随着市场对质量和效益要求的不断提高,冷轧钢带生产工艺也在不断改进与创新。
本文将从工艺流程、设备改进和材料创新等方面,探讨冷轧钢带生产中的工艺改进与创新。
一、工艺流程改进冷轧钢带的生产工艺流程一般包括原料配料、熔炼、连铸、轧制、退火和表面处理等步骤。
工艺流程改进的目的是提高产品质量、降低生产成本、提高生产效率。
1. 原料配料:通过优化原料配比和加工工艺,改善原料粒度和均匀度,提高熔炼效率和质量。
2. 熔炼:采用高效的熔炼工艺,如精炼和真空熔炼等,提高钢液纯净度和均匀性,避免夹杂物的产生。
3. 连铸:采用连铸机进行连续铸造,提高铸坯质量,减少缺陷和夹杂物。
4. 轧制:采用先进的轧制工艺和设备,如四辊轧机、单机在线调质轧制等,提高轧制质量和效率。
5. 退火:通过优化退火工艺参数,如温度、时间和气氛等,提高产品的力学性能和表面质量。
6. 表面处理:采用先进的镀锌和镀涂工艺,如热镀锌、电镀和喷涂等,提高产品的耐腐蚀性和装饰效果。
二、设备改进冷轧钢带生产中的设备改进主要包括轧机、退火炉和表面处理设备等方面。
1. 轧机改进:采用高速、多辊次轧机,实现更精细的轧制和更高的生产效率。
2. 退火炉改进:采用自动化控制系统,实现温度和气氛的精细控制,提高退火效果和均匀性。
3. 表面处理设备改进:引进先进的镀锌设备和喷涂设备,实现更高的镀层质量和效率。
三、材料创新材料创新是冷轧钢带生产中的重要方面,其目的是提高产品的力学性能、耐腐蚀性和加工性能。
1. 材料配方改进:通过改变不同元素的含量和添加合金元素,实现材料的强化、硬化和耐腐蚀能力的提高。
2. 材料表面处理:采用先进的表面处理工艺,如钝化、镀锌和涂层等,提高材料的抗氧化和耐腐蚀性。
3. 材料微观结构调控:通过热处理和冷变形等工艺,调控材料的晶粒大小和组织结构,提高材料的力学性能和加工性能。
#0冷轧带钢生产线技术解析

冷轧带钢生产线技术分析1、了解带钢:酸洗段:酸洗、冷热水洗以及烘干;出口段:剪切、涂油以及最后卷取(收卷)。
2.2 酸洗工艺酸洗段可以采用硫酸酸洗、盐酸酸洗两种方式,但由于盐酸酸洗具有更多的优点,所以我们以盐酸的酸洗机理来说明。
盐酸溶液和氧化铁皮的化学反应为:FeO + 2HCl = FeCl2 + H2O(2) 盐酸基本上不腐蚀基体金属,这样,经盐酸酸洗后板面平滑、银亮,无酸洗痕迹,不会发生过酸洗;盐酸酸洗的铁损比硫酸酸洗低20%;硫酸酸洗时,金属铁在酸液中溶解时会生成氢,氢扩散进入板面,会引起氢脆,而盐酸酸洗就很少产生这种缺陷。
(3) 氧化铁很易溶解,易于除去,故不易引起表面酸斑,这也是盐酸酸洗板面特别光洁的原因之一。
而硫酸铁因会形成不溶解的水化物,往往使板面出现酸斑。
(4) 盐酸酸洗速率较高,特别在温度较高时,盐酸酸洗时间和硫酸相比有很大差别。
(5) 废盐酸和清洗废液可以完全再生为新酸,循环使用,从而解决了废酸污染问题。
因此,硫酸酸洗工艺已基本淘汰。
酸洗气泡产生的机理是:金属和酸产生化学反应时,生成了部分氢原子,它渗透到金属的结晶格子中,并使其变形,变形后使氢更向金属内扩散,其中一部分氢原子穿过金属并分子化,从酸液中逸出,部分氢原子的分子化在晶格变形产生的“显微空孔”边界上,或金属的夹杂及孔隙中进行,氢在空孔中的压力可达到很大值(几十兆帕),使金属中产生了引起氢脆的内应力。
防止产生气泡的措施是:调整酸液的浓度;控制酸洗时溶液的温度和带钢表面平直状态等。
(2) 过酸洗。
金属在酸溶液中停留时间过长,使其在酸溶液作用下,表面逐渐变成粗糙麻面的现象称为过酸洗。
过酸洗的带钢延伸性大大降低,在轧制过程中,很容易断裂和破碎,并且造成粘辊。
过酸洗的带钢即使轧制成材也不能作为成品,因为它的力学性能大大降低了。
产生过酸洗的原因是:机组连续作业中断,使酸洗失去连续性,或因带钢断带处理时间过长等。
防止措施是尽量密切全机组的操作配合,保证生产正常进行。
冷轧带钢生产工艺和精整工艺

第!章冷轧带钢生产工艺和精整工艺第一节冷轧带钢生产的工艺流程不锈钢冷轧带钢的生产是由!个以上的专业化机组完成的,见图"#$ #%。
热轧带钢首先在&’准备机组焊接引带,以减少冷轧不轧部分(头尾约())的消耗,并对带钢测长测厚,为冷轧做准备。
然后带钢在热轧带钢连续退火酸洗机组*+,上进行软化和去除氧化铁皮处理。
带钢在-./0辊或!"#$辊轧机上进行冷轧,在冷轧带钢连续退火酸洗机组!%&进行再结晶软化退火和酸洗。
成品冷轧带钢经平整机组’(&改善板形,提高表面光泽度,经纵切’)(钢卷交货)或横切!)机机组(单张板交货),完成冷轧带钢的生产。
图*+,+#不锈钢冷轧带钢生产工艺流程不锈钢除了铁素体不锈钢外,冷加工硬化率都非常高,一般为室温强度的$倍以上,为了对不锈钢进行冷轧,广泛使用$-辊整体机架的森吉米尔轧机或四柱分离式$-辊轧机或!"#$辊轧机。
多辊轧机工作辊径只有,./ #$-00,由于变形区面积小,相对总的变形抗力小,所以总变形率可达到1.2以上,可以生产-3#00薄规格产品,轧制速度可达1--04056。
在$-辊轧机中分离式轧机在通板中比较容易,不易伤害轧辊,同时检修方便。
!"#$辊轧机由于工作辊径较大,对提高轧速和轧机刚度(#7400)及降低热凸度有利,同时由于工作辊辊径范围大,因而可以采用小辊径生产薄规格产品。
这些轧机对厚度尺寸精度的控制能力都很强。
有预置88+%9!,对设定规格进行控制,有反馈8:+%9!,对厚度公差进行控制,对薄规格产品还设有张力%9!,秒流量%9!(:;’"%)。
另外有的工厂还采取了对轧制温度进行精确控制的措施。
因此带钢的厚度精度已达到<$3-!0的水平。
各种冷轧机的厚度控制精度和基本参数的比较见表*+,+#和表*+,+$。
表!"#"$新建的$%辊不锈钢冷轧机概要轧机参数日新制钢周南厂住友金属鹿岛厂川崎制铁千叶厂轧机速度(&·&’())**$***)**机组张力(+)%,$*-**工作辊!-*.$%*!/,.$!,(常用!)*.0,)辊直径(&&)中间辊!,*.$-*!%$*!/0.$%*支撑辊!%%*,!-*!,%*压下力(+),**$***$***轧机主电机(12)#***-!**钢卷宽度(&&)-**.$*,*0**.$!**-,*.$-**钢卷厚度(&&)来料*3$.%3*$3,.#3,$3*.)3*成品*3*,.*3-*3$.$3,*3%.,3,钢卷重量(+)$)%)!*生产日期(4)$0)0$00%$00$表!"#"%各种冷轧不锈钢宽板带(56$***&&)轧机的基本参数对比轧机典型型号森吉米尔%*辊轧机78%%5",#罗恩%*辊轧机29%*:"#*-"$!,*三菱$%辊轧机;8"$%<"$!,*日立<;-辊轧机=;>?=;#"$#**7型-辊轧机7"-"$/**机架形式零凸度整形机架四立柱分体式机架双牌坊闭口机架双牌坊闭口机架双牌坊闭口机架工作辊径直径(&&),)?/!3,-)?$**/,?$%*),?$%,$#*?%$*第一中间辊直径(&&)0-?$*,$$%?$!*$0,?%$*$,*?%$*!!,?#*,第二中间辊直径(&&)$/*?$/-%!%?%##支撑辊直径(&&)!**#*-3#,%*?,$),%)!?%),$#%*?$!%*$$,*?$%,*最大轧制带钢宽(&&)$!,*$!,*$!,*$$**$,,*辊缝开口度(&&)$%3/$,*.!**!**!**以上!**以上主传动轧辊数第二中间辊@#第二中间辊@#第二中间辊@%中间辊(或支撑辊)@%第二中间辊@%轧机刚度(1A·&&)-****约,,**约,****约#,***约#,***最大轧制力(1A))***$*,**$****$#***%****最大张力(1A),**,**,**#%*#**最大轧制度(&·&’())**)**)**)**—轧机典型型号森吉米尔!"辊轧机#$!!%&’(罗恩!"辊轧机)*!"+&(",&-.’"三菱-!辊轧机/$&-!0&-.’"日立0/,辊轧机1/231/(&-(""#型,辊轧机#&,&-4""道次最大压缩率(5)约!6约!4约!(约!(—轧程最大总压缩率(5)约6,约6(约6.约6.—!"世纪7"年代建设台数.!!’!’!-制造厂商西马克·德马克·82+,日立,9!+,):松德维·达涅利和:$;0<9=>联合三菱重工日立松德维注:"森吉米尔的最新机型为双牌坊闭口机架。
冷轧轧钢工艺的相关要点分析
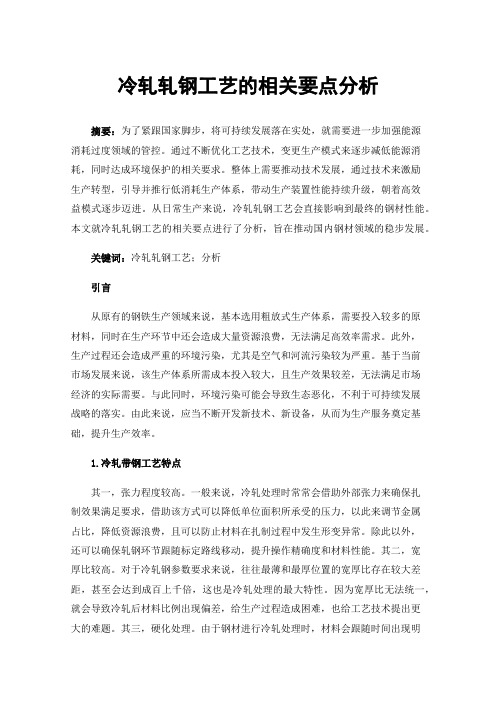
冷轧轧钢工艺的相关要点分析摘要:为了紧跟国家脚步,将可持续发展落在实处,就需要进一步加强能源消耗过度领域的管控。
通过不断优化工艺技术,变更生产模式来逐步减低能源消耗,同时达成环境保护的相关要求。
整体上需要推动技术发展,通过技术来激励生产转型,引导并推行低消耗生产体系,带动生产装置性能持续升级,朝着高效益模式逐步迈进。
从日常生产来说,冷轧轧钢工艺会直接影响到最终的钢材性能。
本文就冷轧轧钢工艺的相关要点进行了分析,旨在推动国内钢材领域的稳步发展。
关键词:冷轧轧钢工艺;分析引言从原有的钢铁生产领域来说,基本选用粗放式生产体系,需要投入较多的原材料,同时在生产环节中还会造成大量资源浪费,无法满足高效率需求。
此外,生产过程还会造成严重的环境污染,尤其是空气和河流污染较为严重。
基于当前市场发展来说,该生产体系所需成本投入较大,且生产效果较差,无法满足市场经济的实际需要。
与此同时,环境污染可能会导致生态恶化,不利于可持续发展战略的落实。
由此来说,应当不断开发新技术、新设备,从而为生产服务奠定基础,提升生产效率。
1.冷轧带钢工艺特点其一,张力程度较高。
一般来说,冷轧处理时常常会借助外部张力来确保扎制效果满足要求,借助该方式可以降低单位面积所承受的压力,以此来调节金属占比,降低资源浪费,且可以防止材料在扎制过程中发生形变异常。
除此以外,还可以确保轧钢环节跟随标定路线移动,提升操作精确度和材料性能。
其二,宽厚比较高。
对于冷轧钢参数要求来说,往往最薄和最厚位置的宽厚比存在较大差距,甚至会达到成百上千倍,这也是冷轧处理的最大特性。
因为宽厚比无法统一,就会导致冷轧后材料比例出现偏差,给生产过程造成困难,也给工艺技术提出更大的难题。
其三,硬化处理。
由于钢材进行冷轧处理时,材料会跟随时间出现明显形变,进而发生硬化问题,严重影响成品钢材的韧性、收缩程度以及延伸性能,致使材料所需承受压力提高。
其四,冷却和润滑操作。
基于实际生产经验来说,钢材进行冷轧处理时大多会由于热能变化出现一定的形变问题,而这也会导致钢材温度超出标准范围,轧辊外部温度甚至能够达到120℃以上,内部温度也高达40℃左右。
第一章冷轧带钢生产概述解析

一号生产作业区培训课件第一章冷轧带钢生产概述1、什么叫冷轧?冷轧带钢有哪些优点? (2)2、冷轧生产方法有哪几种? (2)3、冷轧板带的生产工艺过程? (5)4、冷轧薄带钢生产的发展概况怎样? (6)5、什么叫镀锡薄钢板? (9)6、什么叫镀锌板?其生产方法怎样? (10)7.热镀锌板的生产过程是怎样的? (11)8、什么是彩涂钢板,其生产工艺流程怎样? (12)9.对冷轧板带钢通常要求哪些机械性能和工艺性能? (13)10、公司机组和产品概况 (16)10.1 公司总体产能 (16)10.2、我公司生产产品种类 (19)1、什么叫冷轧?冷轧带钢有哪些优点?金属在再结晶温度以下进行轧制变形叫做冷轧。
一般指带钢不经加热而在室温直接进行轧制加工。
冷轧后的带钢可能烫手,但还是叫冷轧。
冷轧生产可提供大量高精确度和性能优良的钢板和带材,其最主要的特点是加工温度低,同热轧生产相比,它有以下优点:1)冷轧带钢产品尺寸精确,厚度均匀,带钢厚度差一般不超过0.01一0.03毫米或更小,完全可以符合高精度公差的要求;2)可获得热轧无法生产的极落带材(最薄可达0.001毫米以下)。
3)冷轧产品表面质量优越,不存在热轧带钢常常出现的麻点、压入氧化铁皮等缺陷,并且可根据用户的要求,生产出不同表面光洁度的带钢(光泽面或麻糙面等),以利于下道工序的加工。
4)冷轧带钢具有很好的机械性能和工艺性能(如较高的强度,较低的屈服极限、良好的深冲性能等);5)可实现高速轧制和全连续轧制,具有很高的生产率。
2、冷轧生产方法有哪几种?冷轧板带钢生产方法分为单片轧制和成卷轧制两种方法。
1)单片轧制。
单片轧制最早采用二辊式轧机,目前多用四辊式冷轧机。
四辊冷轧机按其轧辊运转方向可分为可逆式和不可逆式。
采用不可逆式四辊轧机进行单机生产时,轧制操作是由人工逐张将钢板喂入轧机,全垛钢板轧完一道次后,用吊车将板垛吊送到轧机前,进行下一道次的轧制,如此循环进行,直到轧成规定的成品尺寸时为止。
- 1、下载文档前请自行甄别文档内容的完整性,平台不提供额外的编辑、内容补充、找答案等附加服务。
- 2、"仅部分预览"的文档,不可在线预览部分如存在完整性等问题,可反馈申请退款(可完整预览的文档不适用该条件!)。
- 3、如文档侵犯您的权益,请联系客服反馈,我们会尽快为您处理(人工客服工作时间:9:00-18:30)。
冷轧带钢生产工艺中的常见问题1、冷轧的关键工序:一为酸洗、二为冷轧、三为热处理、四为平整。
酸洗是为了去除对冷轧有害的原料钢卷表面上的氧化铁皮;冷轧是生产冷轧板带钢的关键工序;热处理在冷轧工序中有二个作用,一是消除冷轧带钢的加工硬化和残余应力,软化金属,改善塑性,以便于进一步进行冷轧或其它加工;二是改善组织结构,产生所需要的晶粒大小和取向;平整是精整工序中十分重要的工序,它可以改善带钢的性能,提高钢板的成形性能,提高钢带的平直度及改善钢板的表面状态。
冷轧工艺的定义:轧制是将金属坯料通过一对旋转轧辊的间隙(各种形状),因受轧辊的压缩使材料截面减小,长度增加的压力加工方法,这是生产钢材最常用的生产方式,冷轧即是在常温下完成的轧制过程,其所使用的原料为热轧加工成的板带(卷)。
2、酸洗工艺带钢冷轧前必须酸洗,清洗其表面氧化铁皮,因为氧化铁皮在冷轧时会损坏轧辊表面,而导致带钢表面产生缺陷。
通常热轧带钢表面氧化铁皮通常是3层结构:外层为Fe2O3(三氧化二铁),中层为Fe304(四氧化三铁),内层为Fe0(氧化铁)。
先进的冷轧厂多采用高速运行的连续酸洗机组或推拉式酸洗。
以连续酸洗为例,是将带钢连续地通过几个酸洗槽进行酸洗。
为使作业线上过程连续,将前一个热轧带钢卷的尾部和后一个钢卷头部焊接起来,酸洗后带钢按需要的卷重、卷径切断带钢并收卷。
连续酸洗机组除完成清除带钢表面氧化铁皮的任务外,还有几个作用:(1) 用圆盘剪将带钢侧边剪齐。
(2) 调节钢卷的质量,根据生产要求将大的热轧钢卷分成小卷,或把几个小钢卷合并成一个大卷,以提高冷轧机的产量。
(3) 检查并剔除对以后各工序有害的带钢表面缺陷。
(4) 在酸洗好的带钢表面上涂上一层油,起防锈和润滑作用。
2.1 连续酸洗机组根据工作性质分成3段:入口段:上料、拆卷、带钢表面氧化铁皮破碎、矫正、剪头、剪尾、工整焊接;酸洗段:酸洗、冷热水洗以及烘干;出口段:剪切、涂油以及最后卷取(收卷)。
2.2 酸洗工艺酸洗段可以采用硫酸酸洗、盐酸酸洗两种方式,但由于盐酸酸洗具有更多的优点,所以我们以盐酸的酸洗机理来说明。
盐酸溶液与氧化铁皮的化学反应为:FeO + 2HCl = FeCl2 + H2OFe2O3 + 6HCl = 2FeCl3 + 3H2O盐酸溶液能较快地溶蚀各种氧化铁皮,酸洗反应可以从外层往里进行。
盐酸酸洗是以化学腐蚀为主,盐酸酸洗对金属基体的侵蚀甚弱。
因此,盐酸酸洗的效率对带钢氧化铁皮的结构并不敏感,而且酸洗后的板带钢表面银亮洁净。
酸洗反应速度与酸洗前带钢氧化铁皮的松裂程度密切相关。
带钢连续盐酸酸洗与硫酸酸洗相比较,有下列优点:(1) 盐酸能完全溶解3层氧化铁皮,因而不产生酸洗残渣。
而用硫酸酸洗时,就必须经常清刷酸槽,并中和这些黏液;硫酸不易除去压入板面的Fe2O3,从而会产生相应的表面缺陷。
(2) 盐酸基本上不腐蚀基体金属,这样,经盐酸酸洗后板面平滑、银亮,无酸洗痕迹,不会发生过酸洗;盐酸酸洗的铁损比硫酸酸洗低20%;硫酸酸洗时,金属铁在酸液中溶解时会生成氢,氢扩散进入板面,会引起氢脆,而盐酸酸洗就很少产生这种缺陷。
(3) 氧化铁很易溶解,易于除去,故不易引起表面酸斑,这也是盐酸酸洗板面特别光洁的原因之一。
而硫酸铁因会形成不溶解的水化物,往往使板面出现酸斑。
(4) 盐酸酸洗速率较高,特别在温度较高时,盐酸酸洗时间与硫酸相比有很大差别。
(5) 废盐酸和清洗废液可以完全再生为新酸,循环使用,从而解决了废酸污染问题。
因此,硫酸酸洗工艺已基本淘汰。
2.3 带钢酸洗会产生的缺陷和防止手段:普碳钢带经酸洗、水洗和干燥后,其表面应呈灰白色或银白色。
但因操作不当、酸洗工艺制度和某些机械设备不良的影响,往往会造成带钢的不同缺陷。
这些缺陷主要有:酸洗气泡、过酸洗、欠酸洗、锈蚀、夹杂、划伤和压痕等。
这些缺陷占冷轧产品缺陷的2%左右,其中主要是欠酸洗、过酸洗和酸洗气泡等。
(1) 酸洗气泡。
酸洗气泡是由于酸与裸露的金属作用生成氢气所造成的。
它在冷轧时会发生噼啪的爆炸声,它的外观特征是呈条状的小鼓泡,破裂后呈黑色细裂缝。
经过轧制后,气泡裂缝会延伸扩大,致使产品的力学性能(冲击韧性)降低。
酸洗气泡产生的机理是:金属和酸产生化学反应时,生成了部分氢原子,它渗透到金属的结晶格子中,并使其变形,变形后使氢更向金属内扩散,其中一部分氢原子穿过金属并分子化,从酸液中逸出,部分氢原子的分子化在晶格变形产生的“显微空孔”边界上,或金属的夹杂及孔隙中进行,氢在空孔中的压力可达到很大值(几十兆帕),使金属中产生了引起氢脆的内应力。
防止产生气泡的措施是:调整酸液的浓度;控制酸洗时溶液的温度和带钢表面平直状态等。
(2) 过酸洗。
金属在酸溶液中停留时间过长,使其在酸溶液作用下,表面逐渐变成粗糙麻面的现象称为过酸洗。
过酸洗的带钢延伸性大大降低,在轧制过程中,很容易断裂和破碎,并且造成粘辊。
过酸洗的带钢即使轧制成材也不能作为成品,因为它的力学性能大大降低了。
产生过酸洗的原因是:机组连续作业中断,使酸洗失去连续性,或因带钢断带处理时间过长等。
防止措施是尽量密切全机组的操作配合,保证生产正常进行。
(3)欠酸洗。
钢带酸洗之后,表面残留局部未洗掉的氧化铁皮时称为欠酸洗。
欠酸洗的带钢(或钢板),轻者在轧制之后产品表面呈暗色或花脸状;严重时氧化铁皮被压入呈黑斑。
此外,氧化铁皮的延伸性较差,故在轧制后因延伸不均使产品出现浪形或瓢曲等缺陷。
有时铁皮可能牢固地贴附在轧辊表面,直接造成轧制废品增多等。
造成欠酸洗的原因是:氧化铁皮厚度不匀,较厚部分的氧化铁皮需要较长酸洗时间,同时其中的Fe0分解成了较难溶解的Fe2O3(Fe3O4);带钢波浪度和镰刀弯较大,在酸洗过程中,起浪部分或弯起部分没有浸泡在酸液中通过,造成漏酸洗;酸洗前机械破鳞不完善,特别是带钢两边端铁皮未被破碎等。
实际生产中欠酸洗多出现在带钢的头尾段和两侧边缘。
根据实测数据,欲酸洗掉大块红色铁皮需要3~4倍的酸洗黑色氧化铁皮的时间,此时已洗掉铁皮的带钢将会形成过酸洗。
因此处理欠酸洗的方法是:预先平整好板形,对于铁皮较厚,而面积又不大的带钢,可采用先局部酸洗一次,而后再过酸洗线的方法去锈。
(4) 锈蚀。
原料酸洗后表面重新出现锈层的现象称为锈蚀。
锈蚀形成的原因是:带钢(钢板)酸洗后表面残留少许的酸溶液,或带钢清洗后没有达到完全干燥而使表面重新生锈。
此外,带钢在酸洗后于高温的清洗水中停留时间过长,也会产生锈蚀现象。
带钢锈蚀处的钢板表面在轧制之后呈暗色,它促使成品在库存时再次锈蚀,从而降低成品材的表面质量,严重时使产品报废。
防止锈蚀的措施是严格执行酸洗、清洗操作规程,及时给表面涂油,并应堆放在干燥的地方。
(5) 夹杂。
带钢在酸洗后表面出现深陷的星罗棋布的黑点疵病称为夹杂。
它是由于热轧时氧化铁皮被压入所形成的。
这样的缺陷不可能采取酸洗法除去。
当它经过冷轧后,黑点便扩展延伸呈黑色条状,大大降低了成品钢板的冲击性能。
(6) 划伤。
带钢在机组运行过程中新出现的划伤,是由于卷取辊、弯曲辊的表面出现质硬的异物,或带钢的浪形及折棱与导板成线接触,或带钢在拆卷过程中拍打折头刮板等,使表面划出新的伤痕。
另外也有部分伤痕出现在热轧后冷却和卷取的过程中。
带钢的划伤可分为上表面划伤和下表面划伤。
划伤的原料经冷轧后,在成品带钢表面将形成宽而长的黑条。
带钢划伤深度超过带钢厚度允许公差一半时,轧制后不能消除。
防止划伤的措施是经常检查机组的滚动部件和导板,维护好设备。
(7) 压痕。
压痕是指带钢(钢板)表面呈凹下去的压迹。
压痕形成的原因是:并卷焊时的焊渣没有吹净,被带钢带到拉辊上,而后在带钢表面压出了痕;拉辊在带钢表面滑动造成粘辊,使带钢表面造成压痕;热轧过程中压下失灵,突然压下停车,而后抬起压下轧制等。
压痕深度超过带钢厚度允许偏差一半时,冷轧之后,压痕不能消除。
总之,上述带钢表面缺陷,只要精心操作,严格执行酸洗工艺制度和操作规程,及时检查和维修设备,是可以避免或减少的。
3、轧制工序钢板的冷轧作为一种生产工艺,几十年来经过了多种演变,它由单机架非可逆单张轧制,到成卷可逆轧制,发展到多机架的全连续轧制。
冷轧不同于其他的轧制方法,它是将冷坯在常温下进行轧制,与热轧相比,冷轧轧制时金属变形抗力很大。
冷轧的道次压下率小,轧制设备要求也就特别高。
冷轧能够轧制出高精度及性能优异的板带钢产品,其主要特点为:(1) 可以生产厚度较簿的产品(分为板带钢与箔材),板带钢厚度在0.10-4.0之间;宽度在600—2500之间;箔材厚度为0.002-0.2毫米,宽度为200-600毫米。
(2) 冷轧板带钢表面质量高,不存在热轧常出现的麻点或压入的氧化铁皮等缺陷,同时还能根据用户的不同使用要求轧制出不同表面粗糙度的板带钢。
(3) 能够保证产品的尺寸精确,厚度均匀,板型平直,同板差不超过0.01-0.03毫米,完全能够达到高精度公差的要求。
(4) 冷轧产品的性能及金属组织能够满足一些特殊的要求,如对电磁、深冲性能的要求等。
具有代表性的冷轧产品是:金属镀层簿板(包括热镀锌板带、电镀锌板带、电镀锡板带等)、深冲钢板(以汽车板为典型)、电工用硅钢板、彩涂钢板、不锈钢板及特殊的冷轧板带钢等。
3.1 轧机分类冷轧带钢轧机可分为:二辊式、四辊式、六辊式、及其他多种多辊式。
随着市场对冷轧产品需求的迅速增长,冷轧生产从简单的单机架可逆轧制,向可逆式、多机架连轧发展。
冷连轧生产工艺技术随之得到迅猛的发展。
按照冷轧产品品种、规格,有三机架、四机架、五机架连轧机及以生产镀锡原板为主要品种的六机架连轧机等。
最高轧制速度可达41米/秒。
目前五机架连轧机组使用最为广泛。
而且连轧机的生产形式也在发生变化,从常规的连轧机组发展到全连续式冷连轧机组,即将带钢的头尾焊接在一起,进行“无头轧制”,使连轧机组的生产能力大幅度提高。
3.2 冷轧工序中可能出现的问题及防止办法3.2.1 带钢跑偏在连续作业机组中,由于机组设备的安装精度、传动辊子的磨损,特别是带钢板形等因素的影响.带钢运行时往往会产生跑偏现象。
带钢跑偏会影响带卷的质量,甚至损伤机组设备。
因此,带钢跑偏控制是很重要的。
减少带钢跑偏主要有以下4个措施:(1) 保证机组设备的安装精度和传动辊子的良好表面形状。
(2) 改善带钢板形,提高带卷质量。
(3) 选择合适的机组工艺参数。
机组速度和张力对带钢跑偏有较大的影响,增加机组张力能改善带钢跑偏现象,提高机组速度则易产生带钢跑偏现象。
(4) 机组中安装跑偏控制装置,控制带钢跑偏在一定范围之内。
(5) 合适的前后张力调整和轧制速度调整。
带钢跑偏控制装置一般有3种形式:刚性机械导向装置、定心辊装置和自动校正装置。
其中自动校正装置一般由带钢位置检测系统和自动校正装置本体组成。