固相法制备纳米微粒
固相法制备纳米微粒
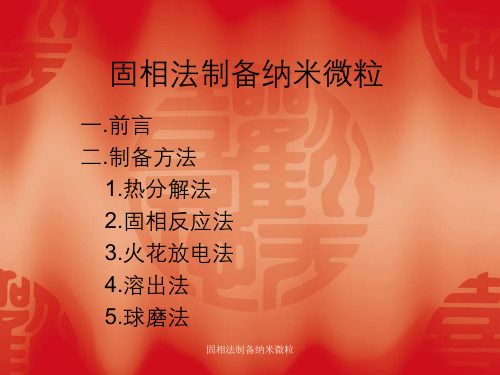
从电晕放电到电弧放电过程中的持续时间很短,只 有10-7~10-5s,而电压梯度则很高,达105~ 106V/cm,电流密度也大,为106~109A/cm2,也就 是说火花放电在短时间内能释放出很大的电能。因 此,在放电发生的瞬间产生高温,同时产生很强的 机械能。在煤油之类的液体中,利用电极和被加工 物之间的火花放电来进行放电加工是电加工中广泛 应用的一种方法。在放电加工中,电极、被加工物 会生成加工屑,如果我们积极地控制加工屑的生成 过程,就有可能制造微粉,也就是由火花放电法制 造微粉。有人对氧化铝制备进行了试验,图3-3是这 种装置的示意图。在水槽内放入金属铝粒的堆积层, 把电极插入层,利用在铝粒间发生的火花放电来制 备微粉。反应槽的直径是20cm,高度是120cm,铝 粒呈扁平状,直径为10~15mm。在放电电压为 24kV、放电频率为1200次/s的条件下来制备微粉。
固相法制备纳米微粒
一.前言 二.制备方法
1.热分解法 2.固相反应法 3.火花放电法 4.溶出法 5.球磨法
固相法制备纳米微粒
前言
气相法和液相法制备的微粒的微粉大多数情况都必 须再进一步处理,大部分的处理是把盐转变成氧化 物等等,使其更容易烧结,这属于固相法范围。再 者,像复合氧化物那样含有两种以上金属元素的材 料,当用液相或气相法的步骤难于制备时,必须采 用通过高温固相反应合成化合物的步骤,这也属于 固相法一类。
微粉除了粉末的粒度和形态外,纯度和组成也是主要因素。 从这点考虑很早就注意到了有机酸盐,其原因是:有机酸盐 易于提纯,化合物的金属组成明确,盐的种类少,容易制成 含两种以上金属的复合盐,分解温度比较低,产生的气体组 成为C、H、O。另一方面也有下列缺点:价格较高,碳容易 进入分解的生成物中等。下面就合成比较简单、利用率高的 草酸盐进行详细介绍。
纳米材料的固相反应研究
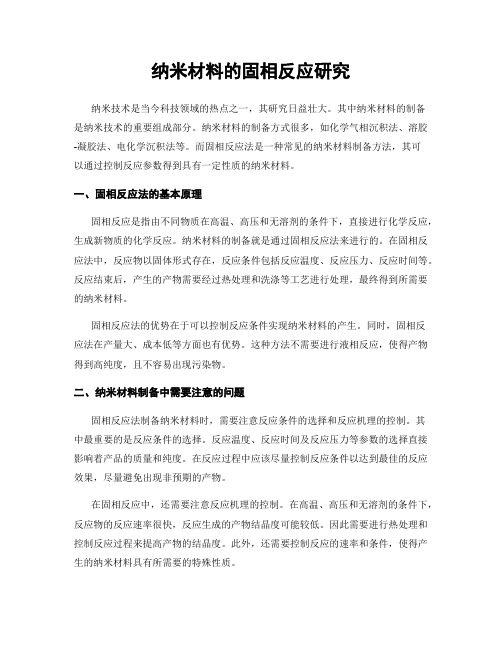
纳米材料的固相反应研究纳米技术是当今科技领域的热点之一,其研究日益壮大。
其中纳米材料的制备是纳米技术的重要组成部分。
纳米材料的制备方式很多,如化学气相沉积法、溶胶-凝胶法、电化学沉积法等。
而固相反应法是一种常见的纳米材料制备方法,其可以通过控制反应参数得到具有一定性质的纳米材料。
一、固相反应法的基本原理固相反应是指由不同物质在高温、高压和无溶剂的条件下,直接进行化学反应,生成新物质的化学反应。
纳米材料的制备就是通过固相反应法来进行的。
在固相反应法中,反应物以固体形式存在,反应条件包括反应温度、反应压力、反应时间等。
反应结束后,产生的产物需要经过热处理和洗涤等工艺进行处理,最终得到所需要的纳米材料。
固相反应法的优势在于可以控制反应条件实现纳米材料的产生。
同时,固相反应法在产量大、成本低等方面也有优势。
这种方法不需要进行液相反应,使得产物得到高纯度,且不容易出现污染物。
二、纳米材料制备中需要注意的问题固相反应法制备纳米材料时,需要注意反应条件的选择和反应机理的控制。
其中最重要的是反应条件的选择。
反应温度、反应时间及反应压力等参数的选择直接影响着产品的质量和纯度。
在反应过程中应该尽量控制反应条件以达到最佳的反应效果,尽量避免出现非预期的产物。
在固相反应中,还需要注意反应机理的控制。
在高温、高压和无溶剂的条件下,反应物的反应速率很快,反应生成的产物结晶度可能较低。
因此需要进行热处理和控制反应过程来提高产物的结晶度。
此外,还需要控制反应的速率和条件,使得产生的纳米材料具有所需要的特殊性质。
三、当前固相反应发展的趋势随着纳米科技的不断发展,纳米材料的制备方法也越来越多。
固相反应法在纳米材料制备中的地位也得到了不断的加强。
当前,固相反应不仅仅局限于制备金属和合金纳米材料,还有了向半导体、二维材料等方向拓展的趋势。
此外,通过固相反应法制备复合纳米材料和纳米多晶材料等也是当前的研究热点。
这些研究也为固相反应法未来的发展提供了新的思路。
低热固相反应制备无机纳米材料的方法
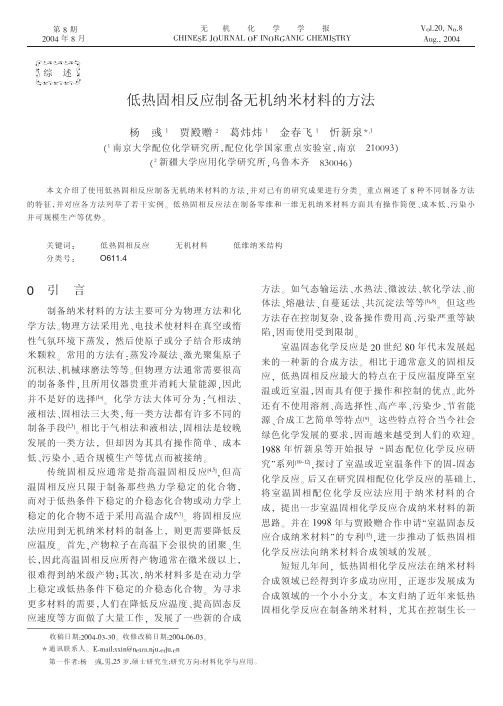
’(#!%." 去离子水洗涤得到纯净产物 " 在空气中干 燥 " 得到纳米 粒 子 " 如 果 于 真 空 条 件 下 干 燥 ! ) " 则 可得到图 ; 所示空心纳米椭球 ! 从图中可以看出 " 此 空心纳米椭球外形较为规则 " 球的直径约为 ."<=" (A! 图中的 %腰果型 &球可以看出为两个空心球体的
I5JK;
图; 直接反应法制备所得 ’(#!%. 空心纳米球的
CFGH4 相片
物 " 再通过煅烧等手段氧化得到目标产物的方法 ! 通 过氧化法可以制备那些在低热固相反应中动力学稳 定的还原性产物 " 再通过煅烧即可氧化得到需要制 备的热力学稳定的产物 ! 如 $ 将 &(#B! ) !C!% 和适量
!
学方法 !物理方法采用光 "电技术使材料在真空或惰 性气氛环境下蒸发 # 然后使原子或分子结合形成纳 米颗粒 ! 常用的方法有 $ 蒸发冷凝法 "激光聚集原子 沉积法 "机械球磨法等等 !但物理方法通常需要很高 的制备条件 # 且所用仪器贵重并消耗大量能源 #因此 并不是好的选择 89.:! 化学方法大体可分为 $ 气相法 " 液相法 "固相法三大类 #每一类方法都有许多不同的 制备手段854;:! 相比于气相法和液相法 #固相法是较晚 发展的一类方法 # 但却因为其具有操作简单 " 成本 低 "污染小 "适合规模生产等优点而被接纳 ! 传统固相反应通常是指高温固相反应 8"46:# 但高 温固相反应只限于制备那些热力学稳定的化合物 # 而对于低热条件下稳定的介稳态化合物或动力学上 稳定的化合物不适于采用高温合成 8&4<:! 将固相反应 法应用到无机纳米材料的制备上 # 则更需要降低反 应温度 ! 首先 #产物粒子在高温下会很快的团聚 "生 长 #因此高温固相反应所得产物通常在微米级以上 # 很难得到纳米级产物 % 其次 # 纳米材料多是在动力学 上稳定或低热条件下稳定的介稳态化合物 ! 为寻求 更多材料的需要 #人们在降低反应温度 " 提高固态反 应速度等方面做了大量工作 # 发展了一些新的合成
高压固相法合成OdS纳米粒子及其表征
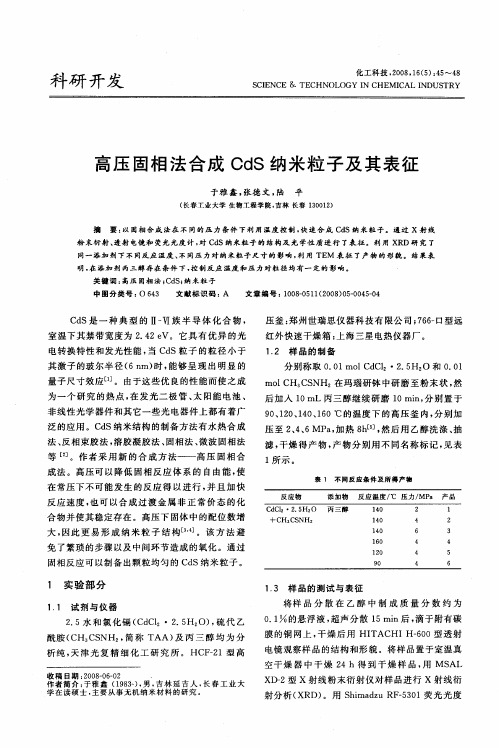
压 釜 : 州世 瑞思 仪器 科 技有 限公 司 ;6 一 郑 7 6 口型远 红 外快 速干燥 箱 : 上海 三 星电热 仪器厂 。
12 样 品 的制备 .
关 键 词 : 压 固相 法 ; d ; 米 粒 子 高 CS纳
中 图分 类 号 : 4 O6 3
ቤተ መጻሕፍቲ ባይዱ
文献标识码 : A
文 章 编 号 : 0 80 1 (0 8 0—0 50 10 —5 12 0 )50 4—4
C S是 一 种 典 型 的 Ⅱ Ⅵ 族 半 导 体 化 合 物 , d 一 室温 下其禁 带宽 度为 2 4 V。它 具 有 优异 的光 . 2e
分别 称取 0 0 l d 1 2 5 O和 0 0 . 1 C 2・ . H2 mo C .1 mo H。 S l C C NH。在玛瑙 研钵 中研 磨 至 粉末 状 , 然 后加 入 1 OmL丙三 醇继 续研 磨 1 n 分别 置 于 0mi, 9 、2 、4 、6 0 1 0 1 0 1 0℃的温度 下 的 高压 釜 内 , 别 加 分 压至 2 4 6MP , 热 8 [ 然后 用 乙 醇洗 涤 、 、 、 a 加 引, h 抽 滤, 干燥 得 产 物 , 产物 分 别 用不 同名 称标 记 , 表 见
等 ] 。作 者 采 用 新 的合 成 方 法 —— 高 压 固相 合 成法 。高 压可 以 降低 固相 反应 体 系 的 自由能 , 使
在常压 下 不可 能发 生 的反 应得 以进 行 , 且 加 快 并 反应 速度 , 也可 以合 成过 渡 金 属 非 正 常价 态 的化
纳米材料-5.2 液相法和固相法

第五章纳米材料的制备5.2 固相法和液相法徐强2009-03-11上次课内容重点1.气相法制备纳米颗粒气体冷凝法、流动液面上真空蒸镀法、通电加热蒸发法、激光诱导化学气相沉积2.气相法制备纳米薄膜物理气相沉积(蒸镀、溅射、离子镀的原理与比较)化学气相沉积(定义、化学反应)主要内容一、气相法二、固相法三、液相法固相法1、高能球磨法(机械合金化法)(重点)2、剧烈塑性变形法(等通道挤压和高压扭转)(了解)高能球磨高能球磨历史高能球磨技术简介高能球磨理论研究高能球磨结构材料开发 高能球磨功能材料开发高能球磨历史高能球磨(High-energy Ball Milling)技术,也称为机械合金化(Mechanical Alloying),是上世纪70年代初由美国国际镍公司(INCO)开发的,最初是用于研制氧化物弥散强化的镍基超合金。
自上世纪80年代初发现它可用来制备非晶态材料后,对它的研究引起人们极大的兴趣。
近年的研究表明,由于高能球磨过程中引入大量的应变、缺陷及纳米量级的微结构,使得合金化过程的热力学和动力学过程不同于普通的固态反应过程,提供了其它技术(如快速凝固等)不可能得到的组织结构,因而有可能制备出常规条件下难以合成的许多新型合金。
高能球磨技术简介高能球磨是一个高能量干式球磨过程。
简单地说,它是在高能量磨球的撞击研磨作用下,使研磨的粉末之间发生反复的冷焊和断裂,形成细化的复合颗粒,发生固态反应形成新材料的过程。
原材料可以是元素粉末、元素与合金粉末和金属间化合物、氧化物粉末等的混合物。
磨球一般采用钢球。
唯一一种由上到下制备纳米粒子的方法。
高能球磨工艺特点工艺简单,易于工业化生产,产量大。
整个过程在室温固态下进行,无需高温熔化,工艺简单灵活。
合成制备材料体系广,不受平衡相图的限制。
可得到其它技术较难得到的组织结构,如宽成分范围的非晶合金、超饱和固溶体、纳米晶合金及原位生成的超细弥散强化结构。
可合成制备常规方法无法得到的合金,特别是不互溶体系合金、熔点差别大的合金、比重相差大的合金及蒸汽压相差较大的合金等难熔合金的制备。
纳米材料的制备方法及原理 (整理)
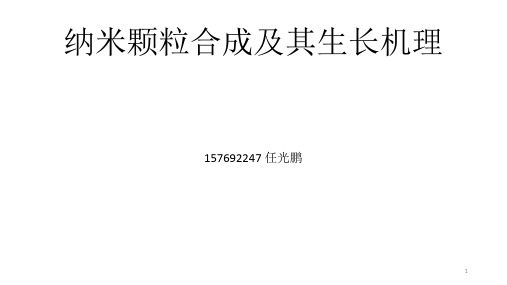
7、等离子体加热蒸发法
等离子体的概念及其形成
物质各态变化: 固体→液体→气体→等离子体→反物质(负)+物质(正) (正负电相反,质量相同) 只要使气体中每个粒子的能量超过原子的电离能,电子将 会脱离原子的束缚而成为自由电子,而原子因失去电子成 为带正电的离子(热电子轰击)。这个过程称为电离。当 足够的原子电离后转变另一物态---等离子态。
4
1、气相法制备纳米微粒的生长机理
• 2) 高频感应加热: 电磁感应现象产生的热来加热。 类似于变压器的热损耗。 高频感应加热是利用金属和磁 性材料在高频交变电磁场中存 在涡流损耗和磁滞损耗,因而 实现对金属和铁磁性性材料工 件内部直接加热。
5
1、气相法制备纳米微粒的生长机理
• 3) 激光加热: 将具有很高亮度的激光束经透镜聚焦后,能在焦点附近产生数千
17/372
3、非晶晶化法
原理:先将原料用急冷技术制成非晶薄带或薄膜, 就是把某些金属元素按一定比例高温熔化,然后 将熔化了的合金液体适量连续滴漏到高速转动的 飞轮表面,这些合金液体沿着飞轮表面的切线方 向被甩了出去同时急遽地冷却,成为非晶薄带或 薄膜。然后控制退火条件,如退火时间和退火温 度,使非晶全部或部分晶化,生成的晶粒尺寸可 维持在纳米级。
18/372
4、机械破碎法
是采用高能球磨、超声波或气流粉碎等机械方法,以粉 碎与研磨为主体来实现粉末的纳米化。 其机理主要是产生大量缺陷,位错,发展成交错的位错 墙,将大晶粒切割成纳米晶。 球磨工艺的目的是减小微粒尺寸、固态合金化、混合以 及改变微粒的形状。球磨的动能是它的动能和速度的函 数,致密的材料使用陶瓷球,在连续严重塑性形变中, 位错密度增加,在一定的临界密度下松弛为小角度亚晶 晶格畸变减小,粉末颗粒的内部结构连续地细化到纳米 尺寸
室温固相法制备纳米_Fe_2O_3过程中形貌影响研究

1 引言
纳米材料 ( nanom aterials) 一般是指其一维、二 维或者三维尺寸在 1~ 100nm 范围的材料, 包括纳米 尺寸的分子、纳米粒子、纳米管和纳米线、纳米薄 膜和纳米块料等
[ 1]
的制备方法及其制备过程中不同方法对纳米粒子形 貌的影响无疑具有 2 O ( 分析纯 ) 和 H 2 C2O4 2H 2 O ( 分析纯 ) 作为原料 , 按摩尔比 1 : 1 . 2 进行 室温固相反应。为了获得较高产率, 在反应物配比 中让 H 2 C2 O4 2 H 2O 稍稍过量 。 前驱体 A 的制备方法: 首先将 F eSO4
4 结论
( 1)以 FeSO4 7H 2 O 和 H 2 C 2O4 2 H 2O 为原料, 2 H 2 O。前
它具有节约能源、无环境污染、操作简单和生产成 本低等优点。目前已在多种纳米氧化物粉体的制备 中得到应用
[ 4]
。
纳米 -Fe2O 3 具有良好的耐候性、耐光性、磁 性和对紫外线有良好的吸收和屏蔽效应 , 可广泛应 用于闪光涂料、油墨、塑料、皮革、汽车面漆、电 子、高磁记录材料、气敏传感、催化剂、非线性光 学以及生物医药工程等方面
图 1 所获得前驱体的 XRD 谱图 F ig 1 the XRD pattern of the precursor
5h 的照片如图 3c 。
因而前驱体 FeC 2O4 应方程式为: F eSO4 7H 2 O + H 2 C2O4
2H 2 O 的室温固相化学反 2H 2 O→ F eC2 O4 2 H 2O +
随着煅烧温度的提高, 前驱体 A 分解产物分散性 提高 , 且颗粒尺寸降低, 平均粒径为 30n m, 由形貌仍 以球形为主, 而前驱体 B 在 400 煅烧的产物的 TE M 照片如图 4b , 与前驱体 A 在 300 煅烧的产物相比, 颗粒尺寸更小, 只有 23nm 分散性更好, 颗粒的形貌也 有别于前驱体 A, 主要为不规则多边形为主。 将前驱体 B 在 500 、 600 煅烧不同时间的产物 的 TEM 照片见图 5a 和 5b 。
纳米材料导论 第二章 纳米粒子的制备方法

2.2.1机械粉碎法
6.纳米气流粉碎气流磨
原 理 : 利 用 高 速 气 流 (300—500m/s) 或 热蒸气(300—450℃)的能量使粒子相互 产生冲击、碰撞、摩擦而被较快粉碎。 在粉碎室中,粒子之间碰撞频率远高 于粒子与器壁之间的碰撞。 特点:产品的粒径下限可达到0.1μm以 下。除了产品粒度微细以外,气流粉 碎的产品还具有粒度分布窄、粒子表 面光滑、形状规则、纯度高、活性大、 分散性好等优点。
基本粉碎方式:压碎、剪碎、冲击粉碎 和磨碎。
种类:湿法粉碎
干法粉碎
一般的粉碎作用力都是几种力的组合,如球磨机和振动
磨是磨碎与冲击粉碎的组合;雷蒙磨是压碎、剪碎、磨
碎的组合;气流磨是冲击、磨碎与剪碎的组合,等等。
7
球磨过程中引起粉末粒度发生变化的机理有两种: 一种:颗粒之间或颗粒与磨球之间互相摩擦,使得一定粒度范 围内的颗粒造成表面粉碎,结果形成大和小两种粒度的新颗粒, 称为摩擦粉碎或表面粉碎。 另一种:由于球对颗粒或颗粒对颗粒的冲击、碰撞和剪切等 作用,从颗粒中近似等体积地分割出两个小颗粒,称为冲击压缩 粉碎或体积粉碎。
4)材质可选择玛瑙, 氮化硅,氧化铝,氧化 锆,不锈钢,普通钢, 碳化钨,包裹塑料的不 锈钢。
12
滚筒式球磨
13
行星球磨
14
参考文献:
2.2.1机械粉碎法
1)高能球磨制备ZnSe纳米晶粉体
车俊 姚熹 姜海青 汪敏强,西安交通大学,
《稀有金属材料与工程》-2006
将相同摩尔比的Zn粉和Se粉放在球磨罐(WC)中,选用球石 直径为10mm,原料:球石=1:20,干磨,在氮气保护下, 球磨60min即可获得纯立方闪锌矿结构,避免了ZnO相的出 现。晶粒的尺寸用Scherrer公式计算为5nm,用TEM直接观察 的尺寸为10nm左右。
- 1、下载文档前请自行甄别文档内容的完整性,平台不提供额外的编辑、内容补充、找答案等附加服务。
- 2、"仅部分预览"的文档,不可在线预览部分如存在完整性等问题,可反馈申请退款(可完整预览的文档不适用该条件!)。
- 3、如文档侵犯您的权益,请联系客服反馈,我们会尽快为您处理(人工客服工作时间:9:00-18:30)。
通常采用的化合物中,大多数为Ⅳ族的四价元素和
ⅡA、ⅡB和ⅣB族的二价元素MⅡMⅣO3型。复合草 酸盐的制法与单盐基本相同,其方法是使草酸盐水 溶液在MⅣ元素和MⅡ元素的氯化物水溶液中反应, 在30℃左右加热进行,反应速度不如离子反应那样 快,生成物可用MⅡMⅣO(C2O4)2· nH2O通式表示。 热分解机理目前尚无定论,例如对BaTiO3就有六种 说法之多,在500~700℃反应形成的最终生成物不 仅限于BaTiO3 。另外,也可生成像(Sr、Ba)TiO3那 样的三元系化合物。
草酸盐的热分解基本上按下面的两种机理进行,究 竟以哪一种进行要根据草酸盐的金属元素在高温下 是否存在稳定的碳酸盐而定。对于两价金属的情况 如下。 机理Ⅰ: MC2O4· 2O -H2O MC2O4 -CO2,-CO MO或M nH 机理Ⅱ: MC2O4· 2O -H2O MC2O4 -CO MCO3 - CO2 MO nH 因ⅠA族、ⅡA族(除Be和Mg外)和ⅢA族中的元素 存在稳定的碳酸盐、可以按机理Ⅱ(ⅠA元素不能 进行到MO,因未到MO时MCO3就融熔了)进行, 除此以外的金属草酸盐都以机理Ⅰ进行。再者,从 热力学上可以预期到,对于机理Ⅰ的情况,或者生 成金属,或者生成氧化物。
3 火花放电法
把金属电极插入到气体或液体等绝缘体中,
不断提高电压,按图3-2所示的电压-电流曲 线进行,直至绝缘被破坏。如果首先提高电 压,可观察到电流增加,在b点产生电晕放电。 一过电晕放电点,即使不增加电压,电流也 自然增加,向瞬时稳定的放电状态即电弧过 电移动。
从电晕放电到电弧放电过程中的持续时间很短,只
2 固相反应法
由固相热分解可获得单一的金属氧化物,
但氧化物以外的物质,如碳化物、硅化 物、氮化物等以及含两种金属元素以上 的氧化物制成的化合物,仅仅用热分解 就很难制备,通常是按最终合成所需组 成的原料混合,再用高温使其反应的方 法,其一般工序于下图:
固相反应法制备粉体工艺流程
原 称 料 原 料 量
故若把对应于式(3-4)的K3和K4反应的自由能 变化设为△G3和△G4,则△G3>△G4关系必然对 应于K3<K4。并且根据式(3-4)K1>K2,则生成金
属氧化物。作为结果,在式(3-4)中可以比较 △G3和种种金属氧化物生成的自由能变化△G4的 大小关系。由此,Cu、Co、Pb和Ni的草酸盐热分 解后生成 再有,通过分解得到氧化物时,对于机理Ⅱ的草酸 盐生成碳酸盐后,碳酸盐的分解反应比草酸盐反应 更难引起。热分析表明,像机理Ⅱ中从草酸盐生成 碳酸盐后,此时的碳酸盐分解反应与以碳酸盐为试 样所测的热分解数据往往有所不同,但这可以认为 是由于设备和试样填充不同之故,而无本质上的差 别。草酸盐的分解温度设在生成氧化物的熔点的1 /4~1/3范围为合适。
一.热分解法
序言
草酸盐的分类
草酸盐的热分解
1.1 序言
热分解反应不仅仅限于固相,气体和液体也可引起热分解反
应。在此只介绍固相热分解生产新固相的系统,热分解通常 如下(S代表固相、G代表气相): S1 S2 + G1 (3-1) S1 S2 + G1 + G2 (3-2) S1 S2 + S3 (3-3) 式(3-1)是最普通的,式(3-3)是相分离,不能用于制 备粉体,式(3-2)是(3-1)的特殊情形。热分解分解反 应往往生成两种固体,所以要考虑同时生成两种固体时导致 反应不均匀的问题。热分解反应基本上是式(3-1)的形式。 微粉除了粉末的粒度和形态外,纯度和组成也是主要因素。 从这点考虑很早就注意到了有机酸盐,其原因是:有机酸盐 易于提纯,化合物的金属组成明确,盐的种类少,容易制成 含两种以上金属的复合盐,分解温度比较低,产生的气体组 成为C、H、O。另一方面也有下列缺点:价格较高,碳容易 进入分解的生成物中等。下面就合成比较简单、利用率高的 草酸盐进行详细介绍。
1.2 草酸盐的分类
通常按周期表对草酸盐进行分类。几乎所有金属元
素都有它的草酸盐,有单盐也有复盐。碱金属草酸 盐(M2C2O4)可溶于水,仅有Li盐和Na盐难溶于水。 对于碱土金属的草酸盐(MC2O4),除了 BeC2O4· 2O(24.8g/100g水)以外在水中不溶解。 3H 草酸盐的溶度积为10-4~10-30左右,二价金属盐的 情况为10-5~10-25,但是,这些金属盐的大部分在 酸中形成络和物而溶解。草酸盐的金属原子价有一 价(K2C2O4)、二价(CaC2O4)、三价 [SC2(C2O4)3]和四价U(C2O4)2,没有五价以上的。 也有取作像TiO(C2O4)· 2O那样的草酸盐。 2H
固相法制备纳米微粒
一.前言 二.制备方法 1.热分解法 2.固相反应法 3.火花放电法 4.溶出法 5.球磨法
前言
气相法和液相法制备的微粒的微粉大多数情况都必 须再进一步处理,大部分的处理是把盐转变成氧化 物等等,使其更容易烧结,这属于固相法范围。再 者,像复合氧化物那样含有两种以上金属元素的材 料,当用液相或气相法的步骤难于制备时,必须采 用通过高温固相反应合成化合物的步骤,这也属于 固相法一类。 固相法是通过从固相的变化来制造粉体,其特征是 不像气相法和液相法伴随有气相→固相、液相→固 相那样的状态(相)变化。对于气相或液相,分子 (原子)具有大的易动度,所以集合状态是均匀的, 对外界条件的反应很敏感。另一方面,对于固相, 分子(原子)的扩散很迟缓,集合状态是多样的。 固相法其原料本身是固体,这较之于液体和气体有 很大的差异。固相法所得的固相粉体和最初固相原 料可以是同一物质,也可以不是同一物质。
4 溶出法
化学处理或溶出法就是制造Raney Ni催化剂的方法。 例如W-2 Raney Ni的制备:在通风橱内,将380g的 氢氧化钠溶于1.6L的蒸馏水,置于一个4L的烧杯中, 装上搅拌器,在冰浴中冷至10℃。在搅拌下分小批 加入镍铝合金共300g,加入的速度应不使溶液温度 超过25℃(烧杯仍留在水浴中)。当全部加毕后 (约需2h)停止搅拌,从水浴中取出烧杯,使溶液 温度升至室温。当氢气发生缓慢时,在沸腾水浴上 逐渐加热(防止温度上升太快,避免气泡过多而溢 出)直至气泡发生再度缓慢时为止(约需8~12h, 在这一过程中时时用蒸馏水添补被蒸发的水分)。 然后静置让镍粉沉下,倾去上层液体,加入蒸馏水 至原来体积,并予以搅拌使镍粉悬浮,再次静置并 倾去上层液体。于是将镍在蒸馏水的冲洗下转移至 一个2L的烧杯中,倾去上层的水,
物质的微粉化机理大致可分为如下两类,一
类是将大块物质极细地分割[尺寸降低过程 (Size Reduction Process)]的方法。另一 类是将最小单位(分子或原子)组合[构筑 过程(Build up Process)]的方法。 尺寸降低过程——物质无变化:机械粉碎 (用球磨机、喷射磨等进行粉碎),化学处 理(溶出法)等。 构筑过程——物质发生变化:热分解法(大 多是盐的分解),固相反应法(大多数是化 合物),火花放电法(用金属铝生产氢氧化 铝)等。
对于由固相反应合成的化合物,原料的烧结和颗粒 生长均使原料的反应性降低,并且导致扩散距离增 加和接触点密度的减少,所以应尽量抑制烧结和颗 粒生长。使组分原料间紧密接触对进行反应有利, 因此应降低原料粒径并充分混合。此时出现的问题
是颗粒团聚,由于团聚,即使一次颗粒的粒径小也 变得不均匀。特别是颗粒小的情况下,由于表面状 态往往粉碎也难于分离,此时若采用恰当的溶剂使 之分散开来的方法是至关重要的。
固相反应是陶瓷材料科学的基本手段,粉体间的反 应相当复杂,反应虽从固体间的接触部分通过离子
扩散来进行,但接触状态和各种原料颗粒的分布情 况显著地受各颗粒的性质(粒径、颗粒形状和表面 状态等)和粉体处理方法(团聚状态和填充状态等 等)的影响。
另外,当加热上述粉体时,固相反应以外的现象也 同时进行。一个烧结,另一个是颗粒生产,这两种 现象均在同种原料间和反应生成物间出现。烧结和 颗粒生长是完全不同于固相反应的现象,烧结是粉 体在低于其熔点的温度以下颗粒间产生结合,烧结 成牢固结合的现象,颗粒间是由粒界区分开来,没 有各个被区分的颗粒之大小问题。 颗粒生长着眼于各个颗粒,各个颗粒通过粒界与其 他颗粒结合,要单独存在也无问题,因为在这里仅 仅考虑颗粒大小如何变化,而烧结是颗粒的接触, 所用颗粒边缘的粒界当然就决定了颗粒的大小,粒 界移动即为颗粒生长(颗粒数量减少)。通常烧结 时进行,颗粒也同时生长,但是,颗粒生长除了与 气相有关外,假设是由于粒界移动而引起的,则烧 结早在低温就进行了,而颗粒生长则在高温下才开 始明显。实际上,烧结体的相对密度超过90%以后, 则颗粒生长比烧结更显著。
草酸盐热分解时粉料往往呈灰色:
2CO→C+CO2 由于析出碳使粉料紧密填充,易于导致非氧化气氛, 若烧结这类粉体,因碳燃烧易造成气孔和空隙。 热分解草酸盐最有效的是利用由两种以上金属元素 组成的复合草酸盐。陶瓷材料大多数为复合氧化物 的形态,合成时特别重要的是:①组成准确可靠; ②在低温下就可以出现反应。因此,热分解以前的 原料要符合生成物所需组成并形成化合物,草酸盐 比较容易地制成适合上述要求的复合盐,所以复合 草酸盐是一种很好的原料。
1.3 草酸盐的热分解
机理Ⅰ的反应为:
MC2O4 MO + CO + CO2 K1 MC2O4 M + 2 CO2 K2 其中平衡常数K1和K2为: K1=[MO][CO][ CO2 ]/[MC2O4], K2=[M][ CO2 ]2/[MC2O4] 另一方面,CO 和之间CO2之间,金属和氧化物之间因有下 列平衡关系式: 2CO+O2 2 CO2 K3, 2M+O2 2MO K4 (3-4) 故其平衡常数为: K3=[ CO2 ]2/[CO]2[O2] K4=[MO]2/[M]2[O2] 所以K1、K2、K3和K4之间有下列关系: (K1/ K2)=(K4/ K3) (3-5) 生成反应的自由能变化为: △G=-RTlnK=-RTlnPG1