激光钻孔原理讲解
激光钻孔机工作原理
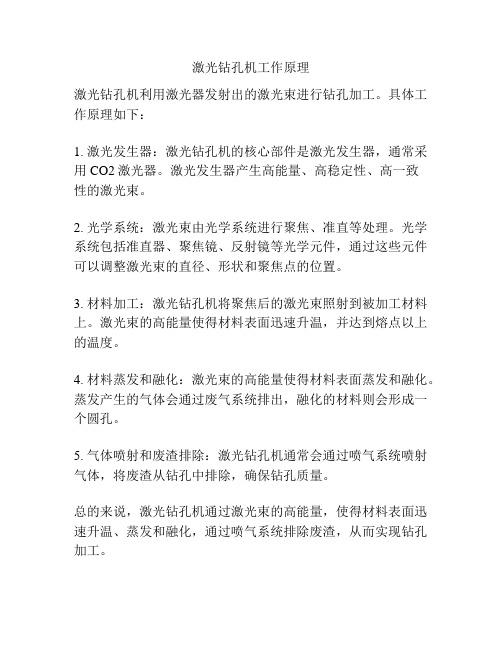
激光钻孔机工作原理
激光钻孔机利用激光器发射出的激光束进行钻孔加工。
具体工作原理如下:
1. 激光发生器:激光钻孔机的核心部件是激光发生器,通常采用CO2激光器。
激光发生器产生高能量、高稳定性、高一致
性的激光束。
2. 光学系统:激光束由光学系统进行聚焦、准直等处理。
光学系统包括准直器、聚焦镜、反射镜等光学元件,通过这些元件可以调整激光束的直径、形状和聚焦点的位置。
3. 材料加工:激光钻孔机将聚焦后的激光束照射到被加工材料上。
激光束的高能量使得材料表面迅速升温,并达到熔点以上的温度。
4. 材料蒸发和融化:激光束的高能量使得材料表面蒸发和融化。
蒸发产生的气体会通过废气系统排出,融化的材料则会形成一个圆孔。
5. 气体喷射和废渣排除:激光钻孔机通常会通过喷气系统喷射气体,将废渣从钻孔中排除,确保钻孔质量。
总的来说,激光钻孔机通过激光束的高能量,使得材料表面迅速升温、蒸发和融化,通过喷气系统排除废渣,从而实现钻孔加工。
激光钻孔原理

激光钻孔原理激光钻孔是一种利用激光束对材料进行加工的方法,它具有加工精度高、速度快、适用范围广等优点,因此在工业生产中得到了广泛的应用。
激光钻孔原理是指利用激光束对材料进行加热,使其局部熔化或气化,从而形成孔洞的过程。
下面我们将详细介绍激光钻孔的原理及其相关知识。
激光钻孔的原理主要包括以下几个方面,首先是激光的特性。
激光是一种具有高能量密度、高单色性、高相干性和定向性的光束,它可以聚焦成极小的光斑,因此可以在极短的时间内将能量聚焦到材料表面的微小区域上。
其次是材料的特性。
不同材料对激光的吸收、传导、反射等特性不同,这直接影响了激光在材料上的加工效果。
最后是激光与材料的相互作用。
当激光束照射到材料表面时,会引起材料的吸收和加热,从而产生熔化或气化,形成孔洞。
在激光钻孔过程中,激光束首先通过透镜聚焦成极小的光斑,然后照射到材料表面。
在照射过程中,激光能量被材料吸收,使材料局部加热,当温度达到材料的熔点或汽化点时,材料就会熔化或气化,形成孔洞。
同时,激光束的移动和材料的移动也会影响孔洞的形成。
通过控制激光束的能量、聚焦光斑的大小、照射时间和材料的移动速度等参数,可以实现对孔洞形状和尺寸的精确控制。
激光钻孔的原理使其具有许多优点。
首先,激光钻孔可以实现对材料的高精度加工,可以加工出直径微小、形状复杂的孔洞。
其次,激光钻孔速度快,加工效率高,可以大大提高生产效率。
此外,激光钻孔适用范围广,可以对金属、非金属等各种材料进行加工。
因此,激光钻孔在汽车制造、航空航天、电子器件等领域得到了广泛的应用。
总之,激光钻孔原理是利用激光束对材料进行加热,使其局部熔化或气化,形成孔洞的过程。
激光钻孔具有加工精度高、速度快、适用范围广等优点,因此在工业生产中得到了广泛的应用。
希望本文能够对激光钻孔的原理有所了解,并对相关领域的从业人员有所帮助。
玻璃激光打孔原理

玻璃激光打孔原理
玻璃激光打孔原理是利用激光束的高能量密度和可调控性,在玻璃表面形成一个微小的焦点点,使玻璃在焦点处发生局部的熔化或汽化,从而实现打孔的过程。
具体原理如下:
1. 激光束聚焦:通过使用透镜等光学元件,将激光束聚焦成一束相对较小的光斑。
聚焦的方式通常是使用球面或非球面透镜将平行光束集中到一个小区域内。
2. 光热效应:激光束聚焦后,它对玻璃表面的能量密度会非常高,玻璃吸收光能并转化为热能。
热量在聚焦点周围堆积,引起局部的温度升高。
3. 玻璃熔化或汽化:当局部温度升高到玻璃的熔点时,玻璃开始熔化,并在激光束的作用下形成一个小孔。
如果局部温度升高得更高,玻璃可能会发生汽化,形成气泡。
4. 打孔过程控制:通过调整激光束聚焦的位置、大小和功率等参数,可以控制打孔的深度和形状。
同时,激光束的扫描和移动也可以实现复杂的孔洞结构。
需要注意的是,激光打孔过程中,玻璃会在焦点周围产生热应力,可能导致破裂或产生裂纹。
因此,需要合理控制激光的功率和脉冲时间,以及适当冷却玻璃表面,以防止潜在的破坏。
激光钻孔的原理
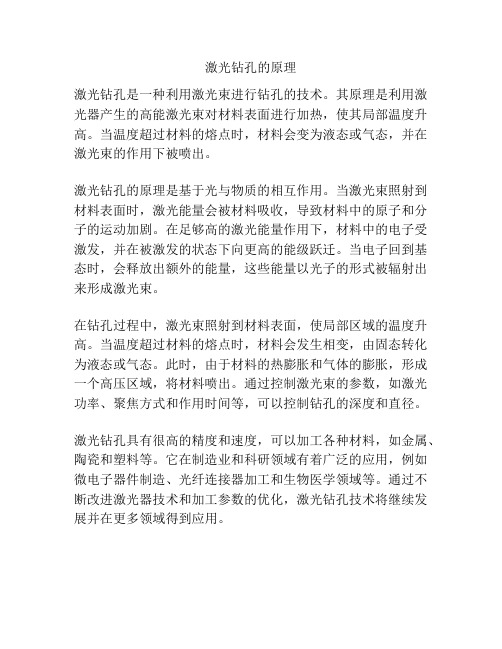
激光钻孔的原理
激光钻孔是一种利用激光束进行钻孔的技术。
其原理是利用激光器产生的高能激光束对材料表面进行加热,使其局部温度升高。
当温度超过材料的熔点时,材料会变为液态或气态,并在激光束的作用下被喷出。
激光钻孔的原理是基于光与物质的相互作用。
当激光束照射到材料表面时,激光能量会被材料吸收,导致材料中的原子和分子的运动加剧。
在足够高的激光能量作用下,材料中的电子受激发,并在被激发的状态下向更高的能级跃迁。
当电子回到基态时,会释放出额外的能量,这些能量以光子的形式被辐射出来形成激光束。
在钻孔过程中,激光束照射到材料表面,使局部区域的温度升高。
当温度超过材料的熔点时,材料会发生相变,由固态转化为液态或气态。
此时,由于材料的热膨胀和气体的膨胀,形成一个高压区域,将材料喷出。
通过控制激光束的参数,如激光功率、聚焦方式和作用时间等,可以控制钻孔的深度和直径。
激光钻孔具有很高的精度和速度,可以加工各种材料,如金属、陶瓷和塑料等。
它在制造业和科研领域有着广泛的应用,例如微电子器件制造、光纤连接器加工和生物医学领域等。
通过不断改进激光器技术和加工参数的优化,激光钻孔技术将继续发展并在更多领域得到应用。
激光打孔
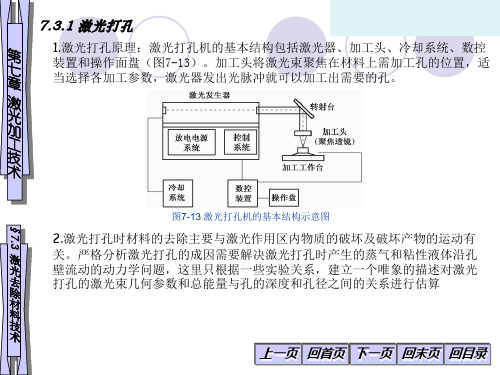
去
除 材 料
※ 氧助熔化切割: 金属被激光迅速加热至燃点以上,与氧发生剧烈的氧化反应(即燃 烧),放出大量的热,又加热下一层金属,金属被继续氧化,并借助气体压力将氧
技 化物从切缝中吹掉。
术
上一页 回首页 下一页 回末页 回目录
7.3.2 激光切割
第
4. 激光切割的工艺参数及其规律
七 章
※ 激光功率: 激光切割时所需功率的大小,是由材料性质和切割机理决定的。
激 结构钢和合金工具钢都能够用激光切割方法得到良好的切边质量 ;铝及铝合金
光 不能用氧助熔化切割而要熔化切割机制 ;飞机制造业常用的钛及钛合金采用空
加 工 技
气作为辅助气体比较稳妥,可以确保切割质量;大多数镍基合金也可实施氧助熔 化切割;铜及铜合金反射率太高,基本上不能用10.6μ的二氧化碳激光进行切割。
7.3.1 激光打孔
第
1.激光打孔原理:激光打孔机的基本结构包括激光器、加工头、冷却系统、数控
七
装置和操作面盘(图7-13)。加工头将激光束聚焦在材料上需加工孔的位置,适
章
当选择各加工参数,激光器发出光脉冲就可以加工出需要的孔。
激 光 加 工 技 术
§7.3
图7-13 激光打孔机的基本结构示意图
2.激光打孔时材料的去除主要与激光作用区内物质的破坏及破坏产物的运动有
第 七 章 激 光 加 工 技 术
去 嘴到工件表面的距离对切割质量也有较大影响,为了保证切割过程稳定,这个距
除 材
离必须保持不变。
料
技
术
上一页 回首页 下一页 回末页 回目录
7.3.2 激光切割
第
5.工业材料的激光切割
七 章
※ 金属材料的激光切割:二氧化碳激光器成功的用于许多金属的切割实践;利用 氧助熔化切割方法切割碳钢板的切缝可控制在满意的宽度范围内 ;大多数合金
激光钻孔的原理是应用

激光钻孔的原理是应用1. 激光钻孔的概述激光钻孔是一种通过激光束对材料进行钻孔加工的技术。
它利用激光的高能量密度、高聚焦度和可控性,可以在很多材料上实现高精度、高效率、非接触式的钻孔加工。
激光钻孔常应用于微电子、光电子、半导体、通信、医疗等领域。
2. 激光钻孔的原理激光钻孔的原理基于激光与材料的相互作用。
当激光束照射到材料表面时,激光能量会被吸收并转化为热能。
随着激光功率密度的增加,材料表面温度升高,超过其熔点或汽化点,导致材料在热作用下的相变。
3. 激光钻孔过程激光钻孔的过程包括以下几个步骤:•激光聚焦首先,激光束经过透镜或反射镜的聚焦,使激光束的直径变小,能量密度增加。
聚焦激光束能够使激光能量更集中地作用于材料表面。
•材料表面吸收能量聚焦后的激光束照射到材料表面,被材料吸收后转化为热能。
材料吸收光的能力取决于激光的波长和材料的性质。
•材料加热和相变随着能量的吸收,材料表面温度升高。
当温度超过材料的熔点或汽化点时,材料会经历相变,从固态转变为液态或气态。
•材料飞溅/蒸发在激光钻孔的过程中,材料表面受到激光热能作用后,可能会发生飞溅或蒸发的现象。
飞溅或蒸发可以形成孔洞,并将材料从孔洞中排出。
•孔洞形成随着激光钻孔过程的继续,激光束的穿透深度逐渐增加,形成一个或多个孔洞。
孔洞的直径和深度取决于激光束的参数以及加工条件。
4. 激光钻孔的特点激光钻孔相比传统钻孔方法具有以下特点:•高精度和高效率激光钻孔可以实现高精度的孔洞加工,因为激光束可以聚焦到很小的直径,并且激光剪切材料的能力较强。
同时,激光加工速度快,可以提高加工效率。
•非接触式加工激光钻孔是一种非接触式加工技术,激光束与材料无需直接接触,避免了传统钻孔中钻头与材料的磨损和热损伤。
•适用于多种材料激光钻孔可以应用于多种材料,包括金属、塑料、陶瓷、硅片等。
不同材料对激光的吸收和热反应有所不同,需要根据材料性质和加工要求进行调整。
•灵活性和可控性激光钻孔过程可以通过调整激光参数、材料性质、加工条件等进行控制,从而得到所需的加工结果。
激光凿洞的原理
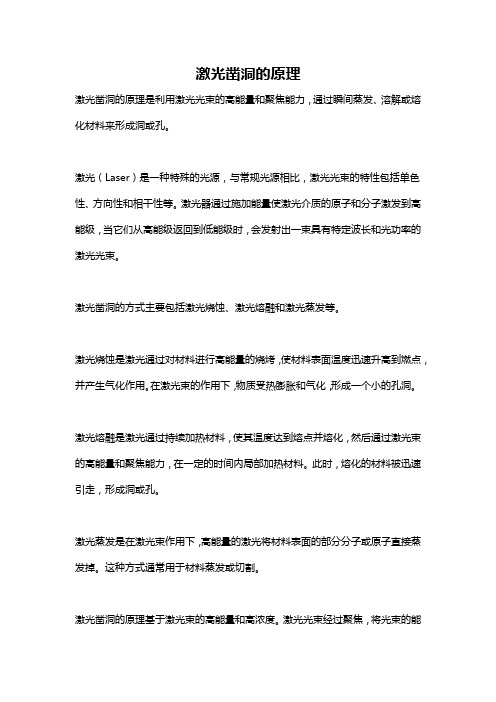
激光凿洞的原理激光凿洞的原理是利用激光光束的高能量和聚焦能力,通过瞬间蒸发、溶解或熔化材料来形成洞或孔。
激光(Laser)是一种特殊的光源,与常规光源相比,激光光束的特性包括单色性、方向性和相干性等。
激光器通过施加能量使激光介质的原子和分子激发到高能级,当它们从高能级返回到低能级时,会发射出一束具有特定波长和光功率的激光光束。
激光凿洞的方式主要包括激光烧蚀、激光熔融和激光蒸发等。
激光烧蚀是激光通过对材料进行高能量的烧烤,使材料表面温度迅速升高到燃点,并产生气化作用。
在激光束的作用下,物质受热膨胀和气化,形成一个小的孔洞。
激光熔融是激光通过持续加热材料,使其温度达到熔点并熔化,然后通过激光束的高能量和聚焦能力,在一定的时间内局部加热材料。
此时,熔化的材料被迅速引走,形成洞或孔。
激光蒸发是在激光束作用下,高能量的激光将材料表面的部分分子或原子直接蒸发掉。
这种方式通常用于材料蒸发或切割。
激光凿洞的原理基于激光束的高能量和高浓度。
激光光束经过聚焦,将光束的能量高度集中在一个小范围内。
由于光束能量的高度聚焦,激光在材料表面的作用时间极短,通过能量的局部聚焦作用,使被照射的物质的温度剧烈升高,从而引起材料的熔化、气化或蒸发,形成洞或孔。
激光凿洞的优点包括高精度、高速度和对材料的非接触性。
激光束可以进行精确定位和调整,可以在微米或亚微米尺度上进行操作,提供高精度的洞或孔。
激光加工速度快,通过调节激光的功率和扫描速度,可以实现快速而高效的加工。
另外,激光凿洞是非接触加工方式,不会引起物理损伤和磨损,对材料的热影响区域小。
激光凿洞在许多领域有广泛应用。
它可以用于金属、塑料、陶瓷、纸张、织物等材料的加工,可以用于制造业、电子产业、医疗设备、航空航天等领域。
例如,激光凿洞可以用于电子元器件的板孔加工、微细孔的制造和医疗器械的切割等。
其中,高精度和高速度的激光凿洞技术对于微电子学、光纤通信等高科技产业尤为重要。
总之,激光凿洞的原理是通过激光光束的高能量和聚焦能力,利用激光束对材料进行烧蚀、熔融或蒸发,形成洞或孔。
激光钻孔机原理

激光钻孔机原理
激光钻孔机是一种利用激光束进行钻孔的设备。
其原理是利用激光的高能量和高聚焦性,将激光束聚焦到一个极小的点上,通过高温和高能量的作用,使被钻孔的物质迅速熔化和气化,从而形成一个小孔。
激光钻孔机的核心部件是激光器和镜头系统。
激光器产生一束高能量的激光束,而镜头系统负责将激光束聚焦到一个极小的点上。
聚焦后的激光束能量密度极高,能够迅速将物质加热至高温。
在钻孔过程中,激光束穿过被钻孔的物质表面,作用在物质的内部。
由于激光的高能量和高聚焦性,激光束在物质内部迅速吸收,使物质迅速升温。
当物质温度达到其熔点时,物质开始熔化。
随着激光束的继续作用,被钻孔的物质继续加热,达到沸点后开始气化。
气化过程中产生的气体会迅速冷却,从而形成一个小孔。
激光钻孔机具有很高的钻孔速度和精度。
由于激光束的直径很小,可以实现微小孔径的钻孔。
而且,激光束的能量密度可以通过控制激光器的功率和镜头系统的聚焦来调节,从而实现不同材料的钻孔。
激光钻孔机广泛应用于电子、航天、汽车等领域。
在电子领域,它可以用于钻孔印刷电路板上的微小孔;在航天领域,它可以用于钻孔航天器上的附件孔;在汽车领域,它可以用于钻孔发动机零部件上的小孔。
激光钻孔机利用激光束的高能量和高聚焦性,通过将激光束聚焦到一个极小的点上,迅速将物质加热至高温和气化,从而实现钻孔的目的。
它具有高速、高精度和可调节的优点,被广泛应用于各个领域。
激光钻孔机的发展将为人们的生产和科研工作带来更多便利和创新。
- 1、下载文档前请自行甄别文档内容的完整性,平台不提供额外的编辑、内容补充、找答案等附加服务。
- 2、"仅部分预览"的文档,不可在线预览部分如存在完整性等问题,可反馈申请退款(可完整预览的文档不适用该条件!)。
- 3、如文档侵犯您的权益,请联系客服反馈,我们会尽快为您处理(人工客服工作时间:9:00-18:30)。
雷射成孔的商用机器,市场上大体可分为:紫外线的Nd :YAG雷射机(主要供应者为美商ESI公司;红外线的C02雷射机(最先为Lumonics,现有日立、三菱、住友等;以及兼具UV/IR之变头机种(如Eecellon之2002型等三类。
前者对3mil以下的微孔很有利,但成孔速度却较慢。
次者对4~8mil的微盲孔制作最方便,量产速度约为YAG机的十倍,后者是先用YAG头烧掉全数孔位的铜皮,再用CO2头烧掉基材而成孔。
若就行动电话的机手机板而言,CO2雷射对欲烧制4~6mil的微盲孔最为适合,症均量产每分钟单面可烧出6000孔左右。
至於速度较的YAG雷射机,因UV光束之能量强且又集中故可直接打穿铜箔,在无需“开铜窗”(Conformal Mask 之下,能同时烧掉铜箔与基材而成孔,一般常用在各式’对装载板” (Package Substrste 4mil以下的微孔,若用於手机板的4~6mil 微孔似乎就不太经济了。
以下即就雷射成孔做进一进步的介绍与讨论。
、雷射成孔的原理
雷射光是当:射线”受到外来的刺激,而增大能量下所激发的一种强力光束,其中红外光或可见光者拥有热能,紫外光则另具有化学能。
射到工作物表面时会发生反射(Refliction吸收(Absorption及穿透(Transmission等三种现象,其中只有被吸收者才会发生作用。
而其对板材所产生的作用又分为热与光化两种不同的反应,现分述於下:
1、光热烧蚀Photothermal Ablation
是指某雷射光束在其红外光与可见光中所夹帮的热能,被板材吸收后出现熔融、气化与气浆等分解物,而将之去除成孔的原理,称为“光热烧蚀”。
此烧蚀的副作用是在孔壁上的有被烧黑的炭化残渣渣(甚至孔缘铜箔上也会出现一圈高熟造成的黑氧化铜屑,需经后制程Desmear清除,才可完成牢固的盲孔铜壁。
2、光化裂蚀Photochemical Ablation
是指紫外领域所具有的高光子能量(Phot on Energy可将长键状高分子有机物的化学键(Chemical Bond予以打断,於是在众多碎粒造成体积增大与外力抽吸之下,使板材
被快速移除而成孔。
本反应是不含熟烧的’冷作” (Cold Proces s孔壁上不至
产生炭化残渣。
3、板材吸光度
由上可知雷射成孔效率的高低,与板材的吸光率有直接关系。
电路板板材中铜皮、玻织布与树脂三者的吸收度,民因波长而有所不同。
前二者在UV 0.3mu以下区域的吸收率颇高,但进入可见光与IR后即大幅滑落。
至於有机树脂则在三段光谱中,都能维持於相当不错的高吸收率。
4、脉冲能量
实用的雷射成孔技术,是利用断续式(Q-switch光束而进行的加工,让每一段光敕(以微秒us计量以其式(Pulse能量打击板材,此等每个Pulse可俗称为一枪所拥有的能量,又有多种模式(Mode,如单光束所成光点的GEMOO单束光点的能量较易聚焦集中故多用於钻孔。
多束光点不但还需均匀化且又不易集中成为小光点,一般常用於雷射直接成像技术(LDI或密贴光罩(Contact Mask等制程。
5、精确定位系统
a、小管区式定位
以日立微孔机械”公司(Hitachi via Machine,最近由日立精工”而改名之
RF/CO2钻孔机为例,其定位法是采’电流计式反射镜”(Galva no meter and Mirr 本身的X.Y.定位,加上机种台之XY台面(XY Table定位等两种系统合作而成。
后者是将大板面划分成许多小“管区”最大为50mm见方,一般为精确起见多采用30mm见方,工作中可XY移动台面以交换管区。
前者是在单一管区内,以两具
Galva nometer的XY微动,将光点打到板面上所欲对准的靶位而成孔。
当管区内的微孔全部钻妥后,即快速移往下一个管区再继续钻孑L。
所谓的Galva nometer是一种可精确微动±0°以下的铁制品,磁铁或线圈式所组合的直流马达,再装配上镜面即可做小角度的转动反射,而将雷射光束加以快速(2~4ms 折射而定位。
但此种系统也有一些缺点,如:①所打在板面上的光束不一定都很垂直,多少会呈现
一些斜角,因此还需再加一种’远心透镜” (Telecentric Lens来改正斜光,使尽
可能的垂直於孔位;②电流计式反射镜系统所能涵盖的区域不大,最多只能管到
50mm*50mm,故还须靠XY Table来移换管区。
其管区越小当然定位就越精准,但相对的也就牺牲了量产的时间;③大板面上管区的交接无法达到完全的天衣无缝,免不了会出现间隙或重叠等接坏错误” (Abutment Errors对高密度布孔的板子可能会发生漏钻孔或位失准等故障。
此时可加装自动校正系统以改善管区的更换,或按布孔的密度而机动自行调整管区的大小与外形。
b、全板面定位
除了上述的“Galvo XY”与“小管区移换”式的定位外,还可将Galvo XY之镜面另装在一组线性马达(Liner Motor上,令其中做全板面的X向移动。
别将台面加装线性马达而只做Y移动,如此将可免除接坏错误。
此法与传统机械钻孔机的钻轴X左右移动,加上台面丫前后动的定位方式相同。
此法可用於UV/YAG光束能
较强者之定位,对线外线C02光束能较弱者,则因其路径太长能量不易集中而反倒不宜。
二、二氧化碳C02雷射成孔的不同制程
1、开铜窗法Conformal Mask
是在内层Core板上先压RCC然后开铜窗,再以雷射光烧除窗内的基材即可完成微盲孑L。
详情是先做FR-4的内层核心板,使其两面具有已黑化的线路与底垫(Target
Pad,然后再各压贴一张“背胶铜箔” (RCC此种RCC (Resin Coated
Copper Foil中之铜箔为0.5 OZ,胶层厚约80~100um(3~4mil。
可全做成B-stage也可分别做成B-stage与C-stage等两层。
后者於压贴时其底垫上(Garget Pad的介质层厚度较易控制,但成本却较贵。
然后利用CO2雷射光,根据蚀铜底片的座标程式去烧掉窗内的要树脂,即可挖空到底垫而成微盲孔。
此法原为“日立制作所”的专利,一般业者若要出货到日本市场时,可能要小心法律问题。
2、开大铜窗法Large Conformal mask
上述之成孔孔径与铜窗口径相同,故一旦窗口位置有所偏差时,即将带领盲孔走
位而对底垫造成失准(Misregistration的问题。
此等铜窗的偏差可能来自板材涨缩与影像转移之底片问题,大板面上不太容易彻底解决。
所谓’开大窗法”是将口径扩大到比底垫还大约2mil左右。
一般若孔径为6mil 时,底垫应在10miL左右,其大窗口可开到12mil。
然后将内层板底垫的座标资料交给雷射使用,即可烧出位置精确对准底垫的微盲孔。
也就是在大窗口备有余地下,让孔位获得较多的弹性空间。
於是雷射光是得以另按内层底垫的程式去成孔,而不必完全追随窗位去烧制明知已走位的孔。
3、树脂表面直接成孔法
本法又可细分为几种不同的途径,现简述如下:
a、按前述RCC+Core的做法进行,但却不开铜窗而将全部铜箔咬光,若就制程本身而言此法反倒便宜。
之后可用CO2雷射在裸露的树脂表面直接烧孔,再做PTH 与化铜电铜以完孔与成线。
由於树脂上已有铜箔积而所踩出的众多微坑,故其后续成垫成线之铜层抗撕强度(Peel Strength应该比感光成孔(Photo Via板类靠高锰酸钾对树脂的粗化要好得很多。
但此种牺牲铜皮而粗麻树脂表面的做法,仍不知真正铜箔来得更为抓地牢靠。
本法优点虽可避开影像转移的成本与工程问题,但却必须在
高锰酸钾’除胶渣”方面解决更多的难题,最大的危机仍是在焊垫附著可靠度的不
b、其他尚有采用:①FR-4胶片与铜箔代替RCC的类似做法:②感光树脂涂布后压著牺牲性铜箔的做法;③干膜介质层与牺牲性铜箔的压贴法;④其他湿膜树脂涂布与牺牲性铜箔法等,皆可全部蚀铜得到坑面后再直接烧孔。
c、超薄铜皮直接烧穿法
内层核心板两面压贴背胶铜箔后,可采半蚀法” (Half Etching各其原来0.5OZ (17um的铜皮咬薄到只剩5um左右,然后再去做黑氧化层与直接成孔。
因在黑面强烈吸光与超薄铜层,以及提高CO2雷射的光束能量下,将可如YAG 雷射
般直接穿铜与基材而成孔,不过要做到良好的半蚀”并不容易。
於是已有铜箔业者在此可观的商机下,提供特殊的“背铜式超薄铜皮”如日本三井之可撕性UTC。
其做法是将UTC棱面压贴在核心板外的两面胶层上,再撕掉厚支持用的“背铜层,,即可得到具有超薄铜皮(UTC的HDI半成品。
随即在续做黑化的铜面上完成雷射盲孔,并还可洗耳恭听掉黑化层进行PTH化铜与电铜。
此法不但可直接完成微孔,而且在细线制作方面,也因基铜之超薄而大幅提升其良率,当然这种背铜式可撕性的UTC ,其价格一定不会便宜。