风扇叶片注射模具设计
汽车风扇件注射模具设计

汽车风扇件注射模具设计LG GROUP system office room 【LGA16H-LGYY-LGUA8Q8-LGA162】汽车风扇件注射模具设计高分子材料科学与工程丁风英摘要:家庭轿车的普及率越来越高,轿车上一些易损的零部件需求量逐年增加。
而轿车上的塑料零部件品种多、精度高、形状复杂、塑料变形复杂。
本文介绍了轿车风扇这个典型的汽车塑料制品通过模具设计过程,重点介绍了浇注系统、成型零件、合模导向机构、脱模机构以及冷却系统的设计。
关键词:注射模;分型面;汽车风扇;模具设计Mold design of automobile fanAbstract : With the increasing high penetration rate of family cars, Variety some of the vulnerable parts demand increases every year. But plastic parts of cars are Variety, high precision, complex shapes, plastic deformation complicated. This article introduces auto plastic products by using die design series of process , and focus on gating system, molding parts, mold clamping oriented institutions,molding mechanism,cooling system design.key words:injection mold;parting surface;automobile fan;die design.1 引言合理的冷却系是提高发动机寿命的关键,汽车发动机冷却风扇是保证发动机正常工作的一个重要部件,它的制作质量直接影响发动机的冷却效果和工作噪音的大小。
电风扇叶片注塑模设计开题报告 (83)

毕业设计(论文)开题报告题目: 电风扇叶片注塑模设计图1扇叶三维模型图2 风扇扇叶二维主视图图3 轮毂二维图图4 风扇叶片二维左视图因塑料风扇叶片尺寸较大,形状复杂,故采用单型腔模。
且由于其壁厚较薄,外观精度要求较高,设计的浇道、浇口须具有快速充模、流动均匀的特点[17]。
方案一:采用单分型面一模一腔(如图5)侧边浇筑方式(如图6),将浇筑点设计成平缝式并将浇筑点选在扇叶顶部的边锋处浇筑完成后成型出一个扇叶模型。
图5 单模单腔注射模图6 侧缝浇筑方式方案二:采用双分型面一模一腔(如图7)点浇筑系统(如图8),此方法采用双分型面模具,并采用点浇筑系统,可以在脱模的同时将成型好的模型和浇筑余料分开来[18]。
图7 双分型面单腔注射模图8针点浇口设计综合分析[19]:由于家用电风扇是常用设备需要大量生产,故应选产量高,生产周期短的方案二。
三本课程的重点及难点:(1)家庭电风扇叶片造型设计(2)工艺分析及电风扇叶片材料选择(3)电风扇叶片三维造型设计(4)电风扇注塑模具成型系统结构设计(5)电风扇注塑模具导向系统结构设计(6)电风扇注塑模具冷却系统结构设计(7)电风扇注塑模具脱模系统结构设计四工作方案及进度计划:闰土机械外文翻译成品某宝dian 第1周-第3周:查阅资料,完成基础知识的积累和开题报告。
第4周-第6周:扇叶模具的几何尺寸计算。
第7周-第10周:三维建模软件对零件进行建模。
第11周-第13周:模具机构各个部分的具体设计。
第14周-第15周:完成毕业论文。
注:1)正文:宋体小四号字,行距20磅,单面打印;其他格式与毕业论文要求相同。
2)开题报告由各系集中归档保存。
3)开题报告引用参考文献注释格式可参照附录E“毕业设计(论文)参考文献样式”执行。
不进入正文,可以作为附件放在开题报告后面。
参考文献[1] 张洪峰.塑料模具设计与制造[J].高等教育出版社,2008,(4):60-62.[2] 罗继相.浅析我国模具行业现状及发展趋势和对策[J].模具技术,2001,03. (6):59-60.[3] 唐仁奎.许艳英注塑模具技术现状与发展趋势[J].科技风,2010,12:20-22.[4] 周永泰.中国塑料模具发展现状与出口期景[J]. 塑料制造,2008,(8):56-62.[5] 宋玉恒. 塑料注射模具设计[J].北京:航空工业出版社,1994,(7):45-47.[6] 屈华昌,李华光,陆飞剑等.关于塑料成型工艺与模具设计[J].高等教育出版社,2003,(8):35-38.[7] 张洪峰.塑料模具设计与制造[J].北京:高等教育出版社,2008,(7):67-69.[8] 周平,王瑞.浅谈我国模具发展[J].模具技术,2007,(4):23-27.[9] 曹延安.中国模具行业的现状与前景[J].金属加工,2012.(9):46-48.[10] 张荣清.模具设计与制造[M].高等教育出版社,2003,(5):60-63.[11] 江恩惠.注塑模具的发展回顾[J].广西轻工业,2009,(21):13-17.[12] 王忠洲.国内外模具发展概况[J].四川工业学院,2001,(15):107-110.[13] 石媛媛.论模具发展的市场与展望[J].现代模具,2010,02,(18):246-246.[14] 王大为.提高冷冲模使用寿命的工艺研究[J],机械工程与自动化.2004,02,(29):73-75.[15] 李健,石厚龙.模具使用寿命的影响及对策[J],金属加工(冷加工).2008,12,(14):46-47.[16] 许振山.塑料模具如何归类[J],材料工业.2009,(9):57-60.[17] Yu Tongmin , Li Guanhua . DESIGN TECHNOLOGY FOR INJECT10N MOLD RARTINGSURFACE BASED ON CASES AND KNOWLEDGE. GHINESE JOURNAL OF MECHANICAL ENGINEERING.2005,4,(18):609-613.[18] CHENG Xue wen, LI De-qun. Development of Integrated Simulation System for PlasticInjection Molding . CADDM. 2005,1,(15):9-16.[19] Bo Scensson, Fredrik Danielsson, Bengt Lennartson. An efficient algorithm for press lineoptimisatiom. The International Journal of Advanced Manufacturing Technology.2013,1,(89):78-80.。
电风扇叶片塑料模具设计说明

第1章注射模可行性分析1.1注射模设计的特点塑料注射模塑能一次性地成型形状复杂、尺寸精确或嵌件的塑料制品。
在注射模设计时。
必须充分注意以下三个特点:(1)塑料熔体大多属于假塑料液体,能剪切变稀。
它的流动性依赖于物料品种、剪切速率、温度和压力。
因此须按其流变特性来设计浇注系统,并校验型腔压力及锁模力。
(2)视注射模为承受很高型腔压力的耐压容器。
应在正确估算模具型腔压力的基础上,进行模具的结构设计。
为保证模具的闭合、成型、开模、脱模和侧抽芯的可靠进行,模具零件和塑件的刚度与强度等力学问题必须充分考虑。
1.2注射模组成凡是注射模,均可分为动模和定模两大部件。
注射充模时动模和定模闭合,构成型腔和浇注系统;开模时定模和动模分离,取出制件。
定模安装在注射机的固定板上,动模则安装在注射机的移动模板上。
根据模具上各个零件的不同功能,可由一下个系统或机构组成。
(1)成型零件指构成型腔,直接与熔体相接触并成型塑料制件的零件。
通常有凸模、型芯、成型杆、凹模、成型环、镶件等零件。
在动模和动模闭合后,成型零件确定了塑件的内部和外部轮廓尺寸。
(2)浇注系统将塑料熔体由注射机喷嘴引向型腔的流道称为浇注系统,由主流道、分流道、浇口和冷料井组成。
(3)导向与定位机构为确保动模与定模闭合时,能准确导向和定位对中,通常分别在动模和定模上设置导柱和导套。
深腔注射模还须在主分型面上设置锥面定位,有时为保证脱模机构的准确运动和复位,也设置导向零件。
(4)脱模机构是指模具开模过程的后期,将塑件从模具中脱出的机构。
(5)侧向分型抽芯机构带有侧凹或侧孔的塑件,在被脱出模具之间,必须先进行侧向分型或拔出侧向凸模或抽出侧型芯。
1.3塑料风叶设计与分析风叶是利用一定空间曲面的叶片,通过主体的高速旋转产生风能。
以前,大都是采用金属片材,经过模压制成风叶片。
然后与风叶主体固定安装成风叶。
由于模压叶片和装配等方面的原因,往往风叶的静、动平衡难以达到设计要求。
电风扇叶注塑模设计

4 电风扇叶注塑模设计4.1 注塑模设计的基本流程传统方法的注塑模设计是在二维环境下进行,从图4.1中可以看出,传统的模具制造工艺路线只是典型的串行流程,任何其中一部分没有完成都会影响下面的工作,相互之间的制约性太大,这样的结果就是生产周期的延长,人工进行的工作量非常大,而且做工粗糙、精度不高,在CAD/CAM技术高速发展的今天,传统方法终将被取而代之。
基于UG 的注塑模具的设计是在三维环境下进行的,这用方法的采用不仅提高了生成型芯和型腔零件的速度和准确度还可以进行造型设计,还能完成模具的总装配,大大缩短了模具设计周期并及时发现模具设计中的错误,有效地避免工人重复劳动[16]。
图4.1传统方式的注塑模具设计过程图4.2 基于UG的注塑模设计工程4.2 注塑模具的基本结构设计4.2.1 扇叶材料的分析风扇为人们日常生活常用品,需大批量生产,又与人们紧密接触,所以扇叶的材料必须无毒无害,同时考虑没有很高的强度要求,收缩率方面也无特殊要求,故选择ABS材料进行注塑生产。
ABS具有良好的成型加工型,制品表面光洁度高,且具有良好的涂装性和染色性,可电镀成多种光泽[17]。
塑料ABS具有以下性能:(1)冲击强度极好,耐磨性优良,尺寸的稳定性好。
(2)从热学性能上来看热变形温度为85℃左右,制品经退火处理以后还可提高10℃左右。
在-40℃时仍能表现出一定的韧性,可在-40℃到85℃的温度范围内长期使用。
(3)ABS的电绝缘性较好,并且几乎不受温度、湿度和频率的影响。
(4)ABS流动性好,易溢料,具有优良的化学稳定性、不吸水,是易成型加工的材料可用于注塑。
4.2.2 分型面的选择分型面是指上、下两模芯互相接触的表面,而分型面的设计在电风扇叶的注塑模设计中是非常重要的。
分型面一般是在确定浇注位置或被称为进料口的位置后再选择。
但在分析各种分型面方案的优缺点之后,也有可能需要重新调整浇注位置。
分型面选择原则有两个,首先要考虑到是塑件在开模时尽可能留在动模部分,同时由于塑件有曲面扇叶,所以也要尽可能留在动模部分。
第11章风扇叶模具设计
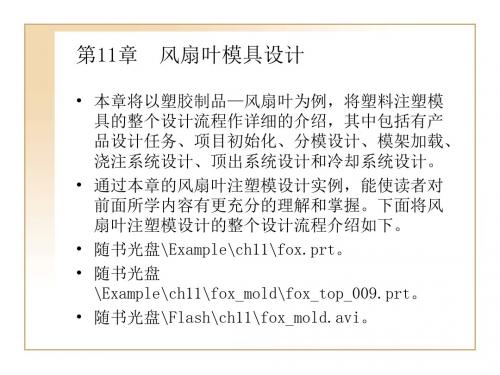
• 本章将以塑胶制品—风扇叶为例,将塑料注塑模 具的整个设计流程作详细的介绍,其中包括有产 品设计任务、项目初始化、分模设计、模架加载、 浇注系统设计、顶出系统设计和冷却系统设计。
• 通过本章的风扇叶注塑模设计实例,能使读者对 前面所学内容有更充分的理解和掌握。下面将风 扇叶注塑模设计的整个设计流程介绍如下。
• 使用“注塑模向导”工具条上的“腔体”工具在 模具定模部分中创建出浇注系统组件的空腔。
11.6 创建顶出系统
• 本例产品无内、外侧凹或侧孔特征,所以顶出系 统的创建仅仅是加载并修剪顶杆。
11.6.1 加载顶杆
• 为使制件能平稳地推出,顶杆的分布应尽量均匀。 加载顶杆的操作步骤如下:
11.6.2 修剪顶杆
11.4.2 调整模腔
• 由于“模架管理”对话框无模架的平移变换功能, 所以只能调整模腔。调整模腔过程包括模具坐标 系的重定义和工件的参数编辑。操作步骤如下:
11.4.3 创建空腔
• 模架加载后,为了便于后续的设计,需先创建出 模腔在动、定模板上的空腔。操作步骤如下:
11.5 创建浇注系统
• 风扇叶模具的浇注系统组件包括主流道、分流道 和浇口。但由于模具采用的是单点浇口进料,因 此不设分流道。
11.3.4 抽取区域面及自动补孔
• 产品的MPV模型验证完成后,接着就可以抽取型芯、型腔区 域面和自动修补模型的破孔了。
• 1. 抽取型芯、型腔区域面 • 2. 自动修补破孔
11.3.5 创建型腔和型芯
• 虽然前面创建了主分型面,但它并不是MW默认的分型面,因此还 要进行MW分型面的创建,然后才能自动分割出型腔和型芯。
11.5.1 创建主流道
• 模具的主流道主要为标准件浇口衬套,同时加载 用于定位注射机机嘴的定位环标准件。
家用电风扇叶片注塑模具设计开题报告
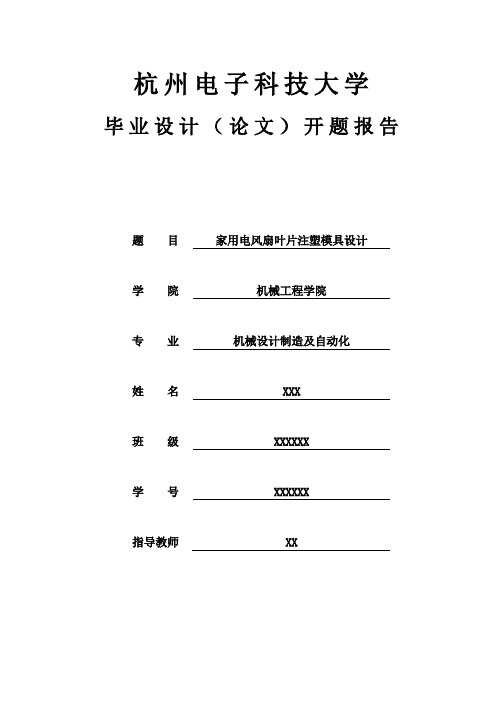
杭州电子科技大学毕业设计(论文)开题报告题目家用电风扇叶片注塑模具设计学院机械工程学院专业机械设计制造及自动化姓名XXX班级XXXXXX学号XXXXXX指导教师XX一、 综述本课题国内外研究动态,说明选题的依据和意义 国内外研究动态注塑模具是生产各种工业产品的重要工艺装备, 随着塑胶模具设计工业的迅速发 展以及塑胶制品在航空、航太、电子、机械、船舶和汽车等工业部门的推广应用,产 品对模具的要求越来越高, 传统的塑胶模具设计方法已无法适应产品更新换代和提高 质量的要求。
电脑辅助工程(CAE)技术已成为塑胶产品开发、模具设计及产品加工 中这些薄弱环节的最有效的途经。
美国上市公司 Moldflow 公司是专业从事注塑成型 CAE 软体和谘询公司,自 1976 年发行了世界上第一套流动分析软体以来,一直主导塑胶成型 CAE 软体市场。
近几年,在汽车、家电、电子通讯、化工和日用品等领域得到了广泛应用。
利用 CAE 技术可以在模具加工前,在电脑上对整个注塑成型过程进行类比分析, 准确预测熔体的填充、保压、冷却情况,以及制品中的应力分布、分子和纤维取向分 布、制品的收缩和翘曲变形等情况,以便设计者能尽早发现问题,及时修改制件和模 具设计,而不是等到试模以后再返修模具。
这不仅是对传统塑胶模具的设计方法一次 突破,而且对减少甚至避免模具返修报废、提高制品质量和降低成本等,都有着重大 的技术经济意义。
塑胶模具设计不但要采用 CAD 技术,而且还要采用 CAE 技术。
这是发展的必然 趋势。
注塑成型分两个阶段,即开发/设计阶段(包括产品设计、模具设计和模具制 造)和生产阶段(包括购买材料、试模和成型) 。
传统的注塑方法是在正式生产前, 由于设计人员凭经验与直觉设计模具,模具装配完毕后,通常需要几次试模,发现问 题后,不仅需要重新设置工艺参数,甚至还需要修改塑料模具设计制品和塑胶模具的 设计,这势必增加生产成本,延长产品开发周期。
模具毕业设计55风扇叶片注射模具设计

模具毕业设计55风扇叶片注射模具设计一、设计背景和目的风扇作为现代生活中必不可少的电器之一,其叶片的设计和制造对于风扇的性能和使用效果具有重要影响。
因此,设计一款优质、高效的55风扇叶片注射模具对于提高风扇叶片的生产效率和质量具有重要意义。
本设计旨在设计一款能够满足产品需求的注射模具,通过优化模具设计和材料选择,提高模具的使用寿命和生产效率,并保证产品的质量。
二、设计步骤和流程1.研究分析:首先对现有55风扇叶片的设计进行详细研究,并分析其结构和生产工艺。
2.模具结构设计:根据风扇叶片的形状和尺寸,设计模具的整体结构,包括模具的上模、下模和侧模的形状和尺寸等。
3.模具材料选择:根据模具的使用寿命要求和生产效率要求,选择合适的模具材料,如优质钢材或耐磨合金材料等。
4.模具加工工艺:确定模具的加工工艺和加工设备,包括模具的精度要求、加工配件的尺寸要求等。
5.模具生产和试模:根据设计要求制造模具,并进行试模,测试模具的性能和生产效果。
6.模具调试和优化:根据试模结果进行模具的调试和优化,改进模具的结构和工艺参数,提高模具的生产效率和质量。
7.模具维护和保养:制定模具的维护保养计划,定期对模具进行保养和维修,延长其使用寿命。
三、设计要求和技术方案1.叶片形状设计:根据55风扇叶片的要求,设计叶片的外形和内部结构,保证叶片的强度和风力输出效果。
2.注射模具结构设计:根据叶片形状设计模具的上模、下模和侧模等,确保注射过程中的材料流动和成型效果。
3.模具材料选择:选择优质的钢材或耐磨合金材料,提高模具的硬度和使用寿命。
4.模具加工工艺:根据设计要求确定模具的加工工艺和加工设备,保证模具的精度和质量。
5.模具试模和调试:进行模具试模和调试,测试模具的生产效率和成型质量,进行必要的参数调整和优化。
6.模具维护和保养:制定模具的维护保养计划,包括定期润滑、清洁和维修等,延长模具的使用寿命。
四、设计成果和预期效果根据以上设计流程和技术方案,预计可以设计出一款满足生产需求的55风扇叶片注射模具,具备以下特点和效果:1.提高生产效率:优化模具设计和加工工艺,提高模具的开模速度和成型效率,提高生产效率。
风扇叶片注射模具设计8页
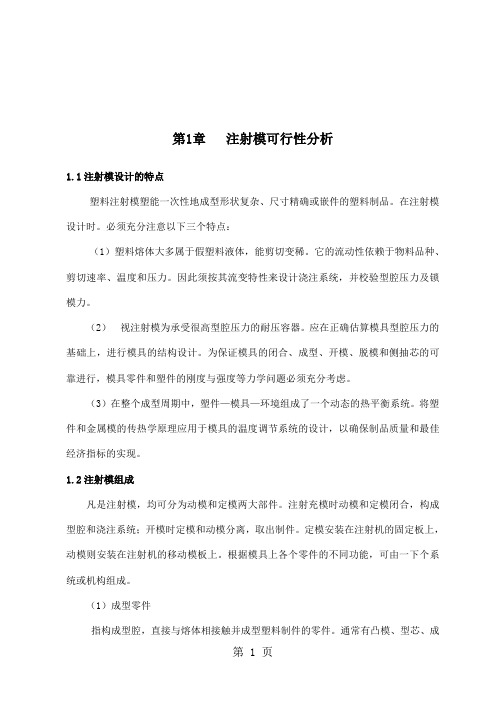
第1章注射模可行性分析1.1注射模设计的特点塑料注射模塑能一次性地成型形状复杂、尺寸精确或嵌件的塑料制品。
在注射模设计时。
必须充分注意以下三个特点:(1)塑料熔体大多属于假塑料液体,能剪切变稀。
它的流动性依赖于物料品种、剪切速率、温度和压力。
因此须按其流变特性来设计浇注系统,并校验型腔压力及锁模力。
(2)视注射模为承受很高型腔压力的耐压容器。
应在正确估算模具型腔压力的基础上,进行模具的结构设计。
为保证模具的闭合、成型、开模、脱模和侧抽芯的可靠进行,模具零件和塑件的刚度与强度等力学问题必须充分考虑。
(3)在整个成型周期中,塑件—模具—环境组成了一个动态的热平衡系统。
将塑件和金属模的传热学原理应用于模具的温度调节系统的设计,以确保制品质量和最佳经济指标的实现。
1.2注射模组成凡是注射模,均可分为动模和定模两大部件。
注射充模时动模和定模闭合,构成型腔和浇注系统;开模时定模和动模分离,取出制件。
定模安装在注射机的固定板上,动模则安装在注射机的移动模板上。
根据模具上各个零件的不同功能,可由一下个系统或机构组成。
(1)成型零件指构成型腔,直接与熔体相接触并成型塑料制件的零件。
通常有凸模、型芯、成型杆、凹模、成型环、镶件等零件。
在动模和动模闭合后,成型零件确定了塑件的内部和外部轮廓尺寸。
(2)浇注系统将塑料熔体由注射机喷嘴引向型腔的流道称为浇注系统,由主流道、分流道、浇口和冷料井组成。
(3)导向与定位机构为确保动模与定模闭合时,能准确导向和定位对中,通常分别在动模和定模上设置导柱和导套。
深腔注射模还须在主分型面上设置锥面定位,有时为保证脱模机构的准确运动和复位,也设置导向零件。
(4)脱模机构是指模具开模过程的后期,将塑件从模具中脱出的机构。
(5)侧向分型抽芯机构带有侧凹或侧孔的塑件,在被脱出模具之间,必须先进行侧向分型或拔出侧向凸模或抽出侧型芯。
(6)温度调节系统为了满足注射工艺对模具温度的要求,模具设有冷却或加热额的温度调节系统。
- 1、下载文档前请自行甄别文档内容的完整性,平台不提供额外的编辑、内容补充、找答案等附加服务。
- 2、"仅部分预览"的文档,不可在线预览部分如存在完整性等问题,可反馈申请退款(可完整预览的文档不适用该条件!)。
- 3、如文档侵犯您的权益,请联系客服反馈,我们会尽快为您处理(人工客服工作时间:9:00-18:30)。
第1章注射模可行性分析1.1注射模设计的特点塑料注射模塑能一次性地成型形状复杂、尺寸精确或嵌件的塑料制品。
在注射模设计时。
必须充分注意以下三个特点:(1)塑料熔体大多属于假塑料液体,能剪切变稀。
它的流动性依赖于物料品种、剪切速率、温度和压力。
因此须按其流变特性来设计浇注系统,并校验型腔压力及锁模力。
(2)视注射模为承受很高型腔压力的耐压容器。
应在正确估算模具型腔压力的基础上,进行模具的结构设计。
为保证模具的闭合、成型、开模、脱模和侧抽芯的可靠进行,模具零件和塑件的刚度与强度等力学问题必须充分考虑。
(3)在整个成型周期中,塑件—模具—环境组成了一个动态的热平衡系统。
将塑件和金属模的传热学原理应用于模具的温度调节系统的设计,以确保制品质量和最佳经济指标的实现。
1.2注射模组成凡是注射模,均可分为动模和定模两大部件。
注射充模时动模和定模闭合,构成型腔和浇注系统;开模时定模和动模分离,取出制件。
定模安装在注射机的固定板上,动模则安装在注射机的移动模板上。
根据模具上各个零件的不同功能,可由一下个系统或机构组成。
(1)成型零件指构成型腔,直接与熔体相接触并成型塑料制件的零件。
通常有凸模、型芯、成型杆、凹模、成型环、镶件等零件。
在动模和动模闭合后,成型零件确定了塑件的内部和外部轮廓尺寸。
(2)浇注系统将塑料熔体由注射机喷嘴引向型腔的流道称为浇注系统,由主流道、分流道、浇口和冷料井组成。
(3)导向与定位机构为确保动模与定模闭合时,能准确导向和定位对中,通常分别在动模和定模上设置导柱和导套。
深腔注射模还须在主分型面上设置锥面定位,有时为保证脱模机构的准确运动和复位,也设置导向零件。
(4)脱模机构是指模具开模过程的后期,将塑件从模具中脱出的机构。
(5)侧向分型抽芯机构带有侧凹或侧孔的塑件,在被脱出模具之间,必须先进行侧向分型或拔出侧向凸模或抽出侧型芯。
(6)温度调节系统为了满足注射工艺对模具温度的要求,模具设有冷却或加热额的温度调节系统。
模具冷却,一般在模板内开设冷却水道,加热则在模具内或周边安装点加热元件,有的注射模须配备模温自动调节装置。
(7)排气系统为了在注射充模过程中将型腔内原有气体排出,常在分型面处开设排气槽。
小型腔的排气量不大,可直接利用分型面排气,也可利用模具的顶杆或型芯与配合孔之间间隙排气。
大型注射模须预先设置专用排气槽。
1.3塑料风叶设计与分析风叶是利用一定空间曲面的叶片,通过主体的高速旋转产生风能。
以前,大都是采用金属片材,经过模压制成风叶片。
然后与风叶主体固定安装成风叶。
由于模压叶片和装配等方面的原因,往往风叶的静、动平衡难以达到设计要求。
经过较长时间的,由于涂层刮伤或脱落,以产生锈蚀,而且风叶的颜色单调,色泽不佳,不适合现代化(宾馆,大厦)等的通风排气和生活的需要。
塑料风叶的优点在与:可以一次注射成型,不须装配、校正,省能省电;重量轻、惯性小,色彩丰富,色泽好,具有良好的动平衡性(塑料风叶叶片良好的弹性,在高速旋转过程中能适度地自动调节叶片的相对位置,使叶片处于良好的平衡状态)和装潢效果。
图1-1风扇立体图塑料风叶如图1-1所示与金属材料风叶设计有相似的一面,但差异也很大,这是塑料本身和注射成型特点所决定的,由于风叶叶面是空间曲面,设计时应考虑模具的制造技术和制造能力,严格说,风叶叶片的形状应根据空气动力学原理来设计,但这样设计会使叶片形状复杂,给模具设计与制造带来困难,一般塑料风叶设计在保证一定风量情况下,采用简化设计风叶叶片的方法,如采用空间螺旋面、模拟曲面等。
叶片的厚度应内厚外薄,逐渐过渡,以提高叶片的结构强度和刚度保证使用性能。
主体部分设计要保证风叶的安装和定位,因此中心轴设计有嵌件,并且轮毂外还设计了一个安装定位的缺口。
1.4注射性能分析(1)注射成型工艺的可行性分析:本塑件形状复杂,壁厚不均,尺寸精度要求较高,而且有较高的表面质量和尺寸稳定性的要求,因此对模具和设备的要求也较高。
而注射成型方法有如下几个优点:a:形状:几乎没有复杂性限制,容许模具内有不同塑料的成型型腔;b:尺寸:塑件可小到不足1克,大到几十千克,没有限制;c:材料:在一定温度范围内具有适宜流动性的热塑性塑料;d:精度:可注射高精度的塑件,有较好表面质量和尺寸稳定性;e:生产率:中等,循环时间主要由塑件壁厚决定,最短可在十几秒内,可增加每模的型腔数来提高生产率。
由以上塑件的特点和注射成型工艺的优点,分析可知:该塑件适合于采用注射成型方法。
(2)表面粗糙度:由塑件外观可知,塑件的外表面要求较高,因此其表面粗糙度取Ra0.4mm,而其内表面由于是复读机的内部,为顾客视线所不及,故不影响其外观视觉质量,从简化加工工艺和节约加工成本的角度考虑,其内表面选用的表面粗糙度为Ra0.8mm。
一般情况下,模具粗糙度低于塑件1~2个等级,故取型腔表面粗糙度为Ra0.2um,而型芯表面粗糙度为Ra0.4um。
(3)尺寸精度:按SJ1372—1978标准,塑料件尺寸精度分为8级。
本塑件所用材料为AS塑料,由此查塑料模具设计手册可知,本塑件宜选用5级精度。
零件具体尺寸及其公差值可详见零件图。
塑件尺寸精度于模具的制造精度密切相关,尤以小型精密塑件为甚。
从模具制造精度对塑件精度的影响可知,模具制造允许误差和塑件尺寸公差之间具有对应的关系,由塑件零件图可得,模具精度等级为IT8。
(4)脱模斜度:该塑件采用的塑料是AS,而AS的成型收缩率较小(0.2-0.6%),而且塑件较复杂,对型芯的包紧面积也较大,所以应取较大的脱模斜度。
为保证壁厚的均匀一致,因此取塑料件的内外表面的脱模斜度一致。
再由零件设计图纸要求可知α=5。
(5)壁厚:由图纸可知,该塑件有许多中不同的壁厚,轮毂壁较厚,风叶壁厚较薄,因此要注意风叶可能会翘曲,不能在风叶处设计推杆。
(6)加强筋:为了确保风扇中心嵌件与塑件外径的同轴度在外侧设计了三个加强筋,以防变形。
(7)圆角:从塑件可知,该塑件内外表面的转折处加强筋的根部等处都设计了圆角。
其采用圆角不仅降低了应力集中系数,提高了抗冲击、抗疲劳能力,而且改善了塑料熔体的流动充模性能,减少了流动阻力。
降低了局部的残余应力,防止开裂和翘曲,也使塑料件外形流畅美观。
而且成型模具型腔也有了对应的圆角,提高了成型零件的强度。
1.5材料选择1.5.1塑料介绍塑料(Plastics)是以有机高分子化合物为基础,加入若干其他材料(添加剂)制成的固体材料。
塑料的优点:塑料的强度较小,有较高的比强度。
塑料还具有较高的电绝缘和热绝缘性,良好的耐磨性和耐腐蚀性,以及优异的成型工艺性。
塑料的缺点:强度,硬度较底,易老化等。
1.5.2分析塑料材料该塑件为风扇叶片,有以下特点:(1)它所处的工作环境较好,处于室温下,不承受冲击载荷,也不处于酸、碱、盐性环境中;(2)产量大,用于一般的日常生活中,故要求此塑件材料质优而价廉,且对人体不产生任何毒副作用。
(3)内部结构较复杂成型较困难。
(4)叶片是空间曲面成型和模具制造都很困难。
(5)要求要有较美丽的外观,很好的绝缘性。
因此我初步选择采用通用塑料。
通用塑料分为聚乙烯(PE)、聚氯乙烯(PVC)、聚苯乙烯(PS)、聚丙烯(PP)、ABS 塑料等品种,多用于一般工农业生产和日常生活之中,具有价格低等特点。
(a)聚乙烯PE:是由乙烯单体聚合而成的。
特点:采用不同的聚合条件可得到不同性质的聚合物:有高压PE、中压PE、低压PE三种。
高压PE:由于有较低的密度、相对分子质量、结晶度,故质地柔软,由于含有较高的相对分子质量、密度、结晶度,故质地坚硬,耐寒性能良好,在-70℃时还保持柔软,化学稳定性很高,能耐酸、碱及有机溶剂,吸水性极小有跟突出的电气性能和良好的耐辐射性等。
缺点:是力学强度不高,热变形温度很低,故不能承受较高的载荷和不能在较高的温度下正常工作。
(b )聚苯乙烯PS :聚苯乙烯略早于聚丙烯问世,其原料十分丰富,是目前最广泛应用的材料之一。
聚苯乙烯的密度为1.04~1.16g/cm 3,比聚氯乙烯小而大于聚丙烯和聚乙烯。
聚苯乙烯遇火会自燃。
聚苯乙烯的代号为(PS ),其分子结构式为:聚苯乙烯的主链上有结构庞大的苯环,故柔顺性差,质地脆硬,抗冲击性能差,敲打时发出类似金属的响声。
机械强度低于硬质聚氯乙烯,尤其是相对分子量较小的品种强度更差,聚苯乙烯属于非结晶型聚合物。
聚苯乙烯具有良好的可塑流动性和较小的成型收缩率,是成型工艺最好的塑料品种之一,容易制造形状复杂的制品。
聚苯乙烯无色透明,透光性仅次于有机玻璃,容易着色,常用于制造要求透明或颜色鲜艳的制品。
聚苯乙烯具有很小的吸水率,在潮湿的环境中尺寸变化很小,适用于制造要求尺寸稳定的制品,如仪表仪器壳体等。
聚苯乙烯具有优良的电绝缘性能,尤其是在高频条件下的介电损耗仍然很小,是优良HH C H C n的高频绝缘材料。
聚苯乙烯的主要缺点是脆性大,形状复杂的制品成型后存在较大的内应力时,常会在使用中自行开裂。
为改善聚苯乙烯的脆性,加入少量的聚丁烯可明显降低脆性,提高冲击韧性。
这种塑料称为高冲击聚苯乙烯。
(c)ABS它是苯乙烯-丁二烯-丙烯腈的共聚物,综合性能较好,冲击韧度、力学强度较高,尺寸稳定,耐化学性,电气性能好。
易于成形和机械加工,与372有机玻璃的熔接性能好,可作双色成形塑件,且表面可镀铬。
(d)AS塑料是丙烯腈——苯乙烯的聚合物。
注塑的高透明、抗静电、优良的尺寸稳定性,具有良好的流动性能,耐热耐化学性、耐冲击、高强度。
用于汽车零件,如灯罩反光片代表面板;工业部件,如计算器面板,琴键等;家用电器部件,如电视机保护镜,风扇叶片,电器外壳等和一般家庭器皿、文教用品、日用品。
1.6材料的确定通过以上分析结合塑料本身的特点以及模塑成型的独特性,如成型热收缩,冷却时的变形、翘曲、实效变形,不具有金属风叶那样可冷校正等等,因此,塑料风叶的选材既要保证风叶的使用性能和便于提高风叶形位精度,又要便于模塑成型。
若采用结晶或半结晶性的塑料,在模素过程中,则易产生在流动方向上的取向,在冷却过程中,由于结晶和取向,是塑料制品各方向上的收缩程度有很大的差异;再则冷却不够均匀和其他因素的影响,必然产生收缩应力,以使制品变形,而且制品后变形亦较大,不能保证所要求的形位尺寸,从而降低了风叶的精度和使用性能,因此,以采用聚苯乙烯、ABS、AS等非结晶塑料为佳,其收缩率相对较小。
聚乙烯塑料由于脆性大,耐冲击能力差使用中易开裂,一般不采用。
ABS和AS塑料性能是合适的,其中ABS价格较高,因此,目前大部分用AS塑料。
根据满足使用要求以及塑模成型条件等选择台湾大东树脂化工有限公司生产的AS塑料。
商品名称:爱塑先——SAN型号:777性能及用途:AS技术指标项目实验方法ASTM777熔体指数(g/10min)D——1238 1.1密度(g/cm³) D——792 1.07热变形温度(ºC)D——648 99软化点(ºC)D——1525 110引张强度(MPa)D——638 71冲击强度(KJ/m²)D——256 0.8弯曲强度(MPa)D——790 109项目实验方法ASTM777延伸率(%)D——638 3.2绝缘耐力(KV/mm)D——149 20电阻率(Ω·m)D——257 >10(16)硬度(M)D——785 80成型收缩率(mm/mm)D——955 0.004吸水率% D——570 0.3第2章成型零部件设计2.1成型零件的结构设计构成型腔的零件统称为成型零件,它主要包括凹模,凸模、型芯、镶块各种成型杆,各种成型环由于型腔直接与高温高压的塑料相接触,它的质量直接关系到制件质量,因此要求它有足够的强度、刚度、硬度、耐磨性以承受塑料的挤压力和料流的磨擦力和足够的精度和表面光洁度,以保证塑料制品表面光高美观,容易脱模,一般来说成型零年都应进行热处理,使其具有HRC50以上的硬度,如成型产生腐蚀性气体的塑料如聚氯已烯等。