不良品原因分析程序
维修不合格品分析维修控制程序

维修不合格品分析维修控制程序维修不合格品分析是指对维修过程中出现的不合格品进行分析,并采取相应的措施进行改进和控制,以提高维修质量和客户满意度。
维修控制程序是指对维修过程进行控制的一系列程序和措施,包括产前、产中和产后的控制环节。
下面将从维修不合格品分析和维修控制程序两个方面进行详细的介绍。
一、维修不合格品分析1.不合格品的定义和分类不合格品是指在维修过程中未达到设定要求或不能正常使用的产品或部件。
不合格品可分为外观不良、功能不全、尺寸偏差等多个方面。
对于每种不合格品都需要进行详细的分析和具体的改进措施。
2.不合格品的分析方法(1)5W1H分析法:通过分析不合格品的何时、何地、何种情况、何原因、何程度以及如何解决等问题来确定不合格品的具体原因和改进方案。
(2)事故树分析法:通过构建事故树来分析不合格品发生的各个环节,从而找到引起不合格品的根本原因。
(3)五力模型分析法:通过对影响维修过程的五个要素(供应商、顾客、竞争对手、新进产品和替代产品)进行分析,找到导致不合格品出现的具体原因。
3.不合格品的改进措施(1)设立质量目标:对维修过程中出现的不合格品进行定量目标的设定,例如不合格品率降低到百分之一以下。
(2)措施制定:根据分析结果制定相应的改进措施,例如加强员工培训、采用检测设备提高产品质量、改进工艺流程等。
(3)持续改进:定期评估改进措施的效果,并根据评估结果对措施进行修改和优化。
1.产前控制(1)设立质量标准:明确维修产品的质量标准,例如外观要求、尺寸精度等。
(2)供应商管理:对供应商进行评估和管理,确保供应商提供的产品和材料符合质量要求。
(3)工艺准备:制定和修订维修工艺文件,确保维修过程的每个环节都能够按照要求进行。
2.产中控制(1)过程控制:通过对维修过程中各个环节的控制和监督,确保维修产品符合质量标准。
(2)设备管理:定期对使用的维修设备和工具进行检查、校准和维护,确保其正常工作。
(3)培训和教育:对参与维修过程的员工进行培训和教育,提高其技术水平和质量意识。
不良品处理流程和方法
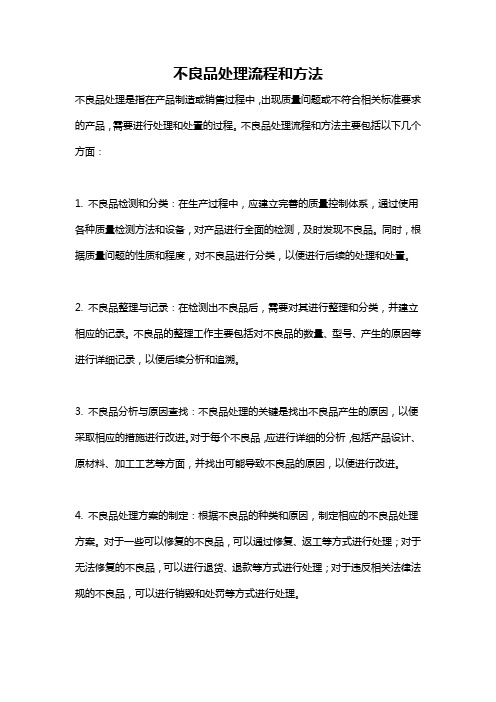
不良品处理流程和方法不良品处理是指在产品制造或销售过程中,出现质量问题或不符合相关标准要求的产品,需要进行处理和处置的过程。
不良品处理流程和方法主要包括以下几个方面:1. 不良品检测和分类:在生产过程中,应建立完善的质量控制体系,通过使用各种质量检测方法和设备,对产品进行全面的检测,及时发现不良品。
同时,根据质量问题的性质和程度,对不良品进行分类,以便进行后续的处理和处置。
2. 不良品整理与记录:在检测出不良品后,需要对其进行整理和分类,并建立相应的记录。
不良品的整理工作主要包括对不良品的数量、型号、产生的原因等进行详细记录,以便后续分析和追溯。
3. 不良品分析与原因查找:不良品处理的关键是找出不良品产生的原因,以便采取相应的措施进行改进。
对于每个不良品,应进行详细的分析,包括产品设计、原材料、加工工艺等方面,并找出可能导致不良品的原因,以便进行改进。
4. 不良品处理方案的制定:根据不良品的种类和原因,制定相应的不良品处理方案。
对于一些可以修复的不良品,可以通过修复、返工等方式进行处理;对于无法修复的不良品,可以进行退货、退款等方式进行处理;对于违反相关法律法规的不良品,可以进行销毁和处罚等方式进行处理。
5. 不良品处理的实施与验收:根据制定的不良品处理方案,对不良品进行处理。
在处理过程中,需要严格按照相应的程序和要求进行操作,确保处理的合规性和可行性。
处理完成后,还需要对处理结果进行验收,确保不良品得到有效处理。
6. 不良品处理结果的分析与改进:对不良品处理的结果进行分析和评估,总结经验教训,找出不足之处。
在不良品处理过程中,应及时反馈处理结果,并采取相应的改进措施,以避免类似问题再次发生。
以上是不良品处理的基本流程和方法。
在实际操作中,还需要根据具体的情况和要求进行调整和补充。
另外,为了提高不良品处理的效率和效果,可以借助信息化工具,建立不良品处理数据库,实现不良品处理过程的信息共享和追溯。
不良品管理制度及流程
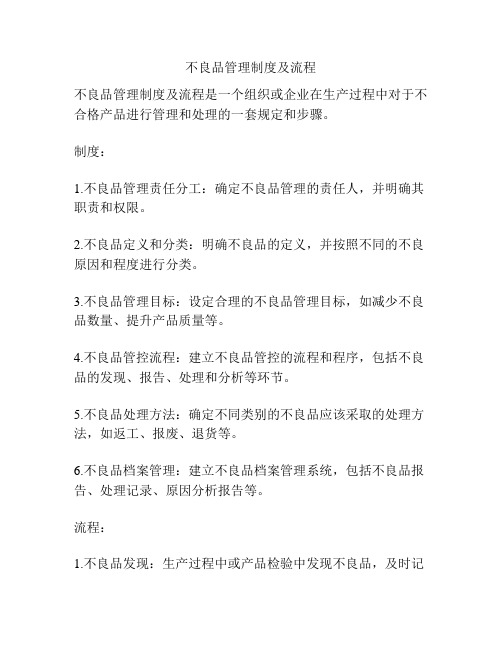
不良品管理制度及流程
不良品管理制度及流程是一个组织或企业在生产过程中对于不合格产品进行管理和处理的一套规定和步骤。
制度:
1.不良品管理责任分工:确定不良品管理的责任人,并明确其职责和权限。
2.不良品定义和分类:明确不良品的定义,并按照不同的不良原因和程度进行分类。
3.不良品管理目标:设定合理的不良品管理目标,如减少不良品数量、提升产品质量等。
4.不良品管控流程:建立不良品管控的流程和程序,包括不良品的发现、报告、处理和分析等环节。
5.不良品处理方法:确定不同类别的不良品应该采取的处理方法,如返工、报废、退货等。
6.不良品档案管理:建立不良品档案管理系统,包括不良品报告、处理记录、原因分析报告等。
流程:
1.不良品发现:生产过程中或产品检验中发现不良品,及时记
录和报告。
2.不良品报告:负责不良品管理的责任人收到不良品报告后,进行初步审核与登记,并通知相关部门。
3.不良品处理审核:相关部门对不良品进行处理方法的审核,并指定责任人进行处理。
4.不良品处理:责任人按照处理方法对不良品进行处理,包括返工、报废、退货等。
5.不良品分析:责任人对不良品进行原因分析,找出不良品产生的根本原因,制定对策预防类似问题再次发生。
6.不良品管理评估:定期评估不良品管理的效果,并进行相应的改进。
以上是不良品管理制度及流程的一般步骤,具体的实施可以根据组织或企业的实际情况进行调整和完善。
不合格品控制程序及处理流程

不合格品控制程序及处理流程文件编号:1.目的:对不合格品加以标识、隔离、风险评估、重新处理,以防止非预期的使用或流入客户手中。
为对品质异常能及时反应处理、预防消除异常原因,以维持品质系统正常运作。
2.范围:针对来料、在制品及包装出货等各个阶段的不合格品。
3.定义:不合格品:不符合产品标准、技术规范或合同要求的产品。
返工:为使不合格品符合要求而对其采取的措施。
返修:为使不合格品满足预期用途而对其采取的措施。
挑选:对不合格品加以挑选,以区别等级。
报废:无法挑选处理并不可能进行返工或返修的不良品及维修成本高于制作制作成本的不良品。
退货:质量部检验材料、半成品、成品等有品质异常不满足需求状况时,将产品整批退还给供应商或制造单位,并要求处理的情形。
特采:于进检、生产过程或最终成品发现不合格品,因客户生产需求急迫,客户担当或业务部代表征得客户同意,或投入后不影响产品功能、构造能力、特殊外观要求及应用功能性,不造成人身安全,可满足最终客户使用品质的不合格品,做特殊接收标识,等同让步接收。
降级降档:因产品检验不符合标注定义要求,而采取更低标准确认接收、降级处理的状况。
4.职责:4.1生产部4.1.1负责对生产过程不合格品隔离作业及相应的标识。
4.1.2执行对品质异常发生时不合格品的应急处理要求。
4.1.3按照技术及质量提供的方案执行不合格品的返工、返修、挑选等作业。
4.1.4负责生产原因及品质异常之分析改善。
4.2质量部4.2.1负责对不合格品处置的协调,包含来料不合格、制程不合格、客户反馈不合格等。
4.2.2定义不合格品的区分、隔离及标识方式。
4.2.3评估定义不合格品的挑选方式及标准。
4.2.4品质异常发生时,不合格品紧急处理方式要求。
4.2.5对品质异常的分析与改善要求。
4.3技术部4.3.1品质异常发生时的应急处理方案拟定。
4.3.2对品质异常的分析与改善要求。
4.3.3对返工、返修作业方式的定义。
4.4其他部门4.4.1其他部门负责履行本部门的职责予以协助。
产品不良分析报告

不良现象
现象分析
序号
1 2 3 4 5
1 2
LOGO
REC 无音不良
盖印
E421BB E4102B E4118B E3B23B E4118B
DCR测试
SPK(欧姆)
6.9 7.0 7.0
REC(欧姆)
无反应 无反应 无反应
6.9
无反应
7.0
无反应
测定 DCR时: Part 1 : SPK OK Part 2 : REC NG
分析内容
STEP 1:观察不良试料的外观;
LOGO
原因分析`
NO.1
NO.2
NO.3
NO.4
NO.5
经确认 : 除 NO.4 的UV 胶未与 F-PCB分离外,其他 4 PCS都有胶与 F-PCB分离的现象,并且有3 pcs分离现象特别严重。
分析内容
LOGO
STEP 2:REC 单品确认;
将 锡点 上部的UV 胶去除后, 测定DCR : 无反应 判定结果 : REC 单品出现无音
原因分析
NO.1
NO.2
2 3 4 5
盖印
E421BB E4102B E4118B E3B23B E4118B
DCR测试 - R E C( 欧姆)
无反应 无反应 无反应 无反应 无反应
分析内容
LOGO
,
STEP 3:REC 单品不良原因确认; -- > 为防止拆分造成单品状态的破坏,使用 甲苯 ( TO ) 对单品进行浸泡,浸泡完毕后显微镜观察状态如下:
不良品的处理流程及注意事项
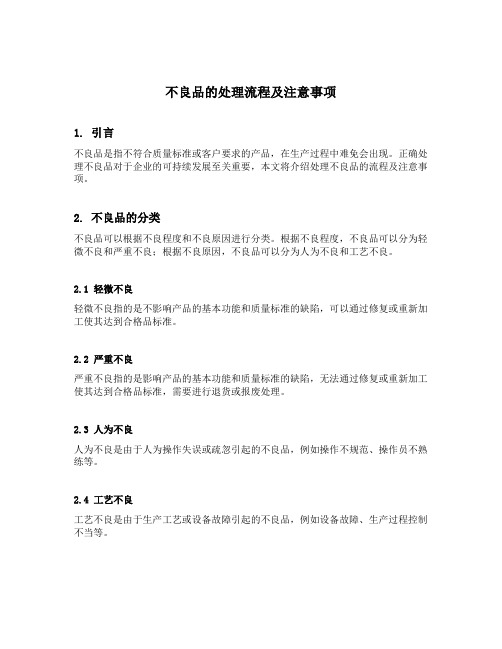
不良品的处理流程及注意事项1. 引言不良品是指不符合质量标准或客户要求的产品,在生产过程中难免会出现。
正确处理不良品对于企业的可持续发展至关重要,本文将介绍处理不良品的流程及注意事项。
2. 不良品的分类不良品可以根据不良程度和不良原因进行分类。
根据不良程度,不良品可以分为轻微不良和严重不良;根据不良原因,不良品可以分为人为不良和工艺不良。
2.1 轻微不良轻微不良指的是不影响产品的基本功能和质量标准的缺陷,可以通过修复或重新加工使其达到合格品标准。
2.2 严重不良严重不良指的是影响产品的基本功能和质量标准的缺陷,无法通过修复或重新加工使其达到合格品标准,需要进行退货或报废处理。
2.3 人为不良人为不良是由于人为操作失误或疏忽引起的不良品,例如操作不规范、操作员不熟练等。
2.4 工艺不良工艺不良是由于生产工艺或设备故障引起的不良品,例如设备故障、生产过程控制不当等。
3. 不良品的处理流程正确的不良品处理流程可以最大程度地减少损失和影响,以下是一个常用的不良品处理流程:3.1 检测和识别在生产过程中需要对产品进行全面的检测和识别,及时发现不良品。
可以通过设立检测点或检测工艺,使用检测设备和工具,进行抽样检测等方法。
3.2 记录和分类对每个发现的不良品进行记录,并根据不良程度和不良原因进行分类。
记录需要包括不良品的数量、照片、不良原因等信息,以便后续处理和分析。
3.3 制定处理方案根据不同的不良品情况,制定针对性的处理方案。
轻微不良可以通过修复或重新加工来达到合格品标准;严重不良需要进行退货或报废处理。
3.4 处理不良品根据制定的处理方案进行相应的操作。
对于轻微不良,可以进行修复或重新加工;对于严重不良,需要按照退货或报废的程序进行处理。
3.5 分析原因并改进处理完不良品后,需要对不良原因进行分析和总结。
通过分析原因,及时采取措施改进生产过程,避免同类问题的再次发生。
4. 不良品处理的注意事项在处理不良品时,还需要注意以下事项:4.1 及时处理发现不良品后,需要及时进行处理,避免不良品的数量和影响进一步扩大。
车间不合格品管理流程

车间不合格品管理流程一、概述车间不合格品管理流程是为了保证产品质量,提高生产效率,减少不良品产生所制定的一系列管理流程。
该流程包括不合格品的发现、处理、分析和改进,旨在通过科学的管理方法,及时发现和解决不合格品问题,确保产品质量符合标准要求。
二、流程步骤1. 不合格品发现1.1 质检员在生产过程中发现不合格品,即将住手生产,并记录不合格品的数量、型号、规格、生产日期等相关信息。
1.2 质检员将不合格品标记,并按照规定的程序将其送至不合格品区域,确保不合格品与合格品分开存放。
2. 不合格品处理2.1 不合格品责任人接收不合格品,并进行初步判断,确定是否为真正的不合格品。
2.2 若不合格品为误判或者可修复的缺陷,责任人将其送至维修区域进行修复,并在修复后进行再次检验,确保质量达标。
2.3 若不合格品无法修复或者无法满足产品质量要求,责任人将其进行报废处理,并填写相应的报废记录。
3. 不合格品分析3.1 不合格品责任人对每一个不合格品进行分析,确定不合格品产生的原因。
3.2 不合格品责任人将分析结果进行记录,并提交给相关部门进行进一步的讨论和改进措施的制定。
3.3 相关部门根据不合格品分析结果,制定改进措施,并进行实施。
4. 不合格品改进4.1 根据不合格品分析结果,制定改进计划,并明确责任人和完成时间。
4.2 责任人按照计划进行改进工作,并记录改进过程中的关键环节和措施。
4.3 改进工作完成后,进行效果评估,确保改进措施的有效性。
4.4 改进措施的效果评估结果及时反馈给相关部门,并进行总结和归档,为以后的类似问题提供参考。
5. 不合格品预防5.1 不合格品责任人根据不合格品分析和改进结果,提出预防措施,并进行实施。
5.2 责任人对预防措施的实施效果进行监控和评估,确保问题的预防和再次发生的几率降低。
5.3 相关部门对不合格品预防措施进行复盘,总结经验教训,并进行知识分享,提升全员的质量意识和技能水平。
不良品的控制流程及如何防止不良品的产生

不良品的控制流程及如何防止不良品的产生?工业物流通过将企业订单管理、库存、运输、仓储管理、物料处理以及包装管理优化成有机整体,使得物流过程能与供应链整体保持同步,有利于降低物流成本、缩短订单处理时间、减少整体库存水平。
所谓不良品,是指企业生产的产品中不符合质量标准的产品,它包括废品、返修品和超差利用品三类产品。
加强不良品管理,一方面能降低生产成本,提高企业的经济效益;另一方面,对保证产品质量,生产用户满意的产品,实现较好的社会效益也起着重要作用。
不良品的控制流程1、识别不良品:判断产品合格与否的依据或标准。
1.产品标准;2.客户要求;3.工艺文件;4.检验文件;5.样板或有效的封样;6.上级的交代与叮嘱。
2、标识不良品检验状态的标识•标识“待处理”或“不合格”的标识。
•生产班组:不合格的半成品与原材料要标明“待处理”或“不合格”的标识。
•检验员在随机卡、流程卡或“返工单”的相应项目标栏内盖检验章,作为“不合格”标识。
•其作用是:具有可追溯性。
•最终检验:不合格牌标识或注明不合格现象,如(少工序、少孔等)。
3、隔离不良品要求:与正常的合格品明确隔离。
•红色胶盘/无聊框•专门独立的不良品架•划分不合格区域,不良品房子不良品区域内•生产区的摆放与其他产品不同,以示区别,然后按要求拉到维修或返工返修区处理•定时安排人员到不良品区进行确认与数量的登记4、记录不良品•在规定的检验报告上正确记录不良品的型号、批次、检验日期、检验依据、不良品数量、检验结果•检验报告按规定予审核与批准•流程1.进货检验:填写检验单→按规定的程序反馈2.生产过程:首件、制程巡检表→巡检报告3.最终检验:检验报告→成品入库检验报告5、评审不良品o进货检验:经检验主管以上人员签署处置意见(必要时要组织技术部、生产、供应链、相关部门进行评审)o过程检验:对批量不良品,质量管理部组织相关部门和相关人员进行评审o最终检验:质控部负责人审批处置结论,必要时,技术部参与评审6、处置不良品▪进货不良品的处置退货;让步接收;要求供方采取相关的纠正预防措施;对连续多批不合格,某批大量严重不合格的供方,将安排人员对其审厂并对以后批次加严检验。
- 1、下载文档前请自行甄别文档内容的完整性,平台不提供额外的编辑、内容补充、找答案等附加服务。
- 2、"仅部分预览"的文档,不可在线预览部分如存在完整性等问题,可反馈申请退款(可完整预览的文档不适用该条件!)。
- 3、如文档侵犯您的权益,请联系客服反馈,我们会尽快为您处理(人工客服工作时间:9:00-18:30)。
不良品原因分析程序
为提高公司产品质量,既要对质量形成过程严格规划,仔细监控,细心巡查,又要对生产中产生的不良品的形成原因进行监控分析,找出发生不良的原因,对症下药,解决生产中的短板因素,有助于提高整体的质量水平。
不良品产生原因大致如下:
1.管理因素:对质量管理的体系运作不熟悉,各部门职责不清,实
际管理人员对于质量管理实际操作不熟练,对于现场发生的问题不了解等等
2.人员因素:质检人员及工人培训不足,不了解质量形成过程中自
己应负的责任,对工作马马虎虎,技术能力不足等等
3.工艺方面:对于客户的要求不能严格执行,对于工艺过程不了解,
对产品的具体工艺和生产过程质量控制点不熟悉
4.原辅材料:对于材料的具体规格不了解,对材料质量把关不严,
材料存放和检验不规范
5.生产过程:对生产中的人机各方面因素控制不力,生产中只注重
数量而不管质量的现象
6.质检方面:质检标准执行不力,过程检验没有起到相应的作用等
等。
针对相关产品质量产生不良的具体分析过程如下:
一般在生产过程中会有企业自己的质检程序,质检环节参与质量管理,同时客户会安排质检人员参与生产全程的检验,或者会有第三方
检验质量。
因此,在全流程质检过程中,会有各个不良品的检验标签-不良贴指示出不良所在以及检验报告,公司可以根据报告内容基本确定不良原因所在。
根据报告和不良贴的位置,首先确认问题发生的环节,是在生产的某道工序或是在各个生产环节出现问题。
然后根据问题所在查找以上原因,相应对问题原因采取对应的管理措施,以求改善或者消灭问题再次发生的可能性,防患于未然。
对于经常出现的问题,要从管理上找原因,通过人员配置,体系运作的高度去认识,加强培训和考核,从根本上解决问题。