磁控溅射法沉积TCO薄膜的电源技术
磁控溅射镀膜技术综合介绍
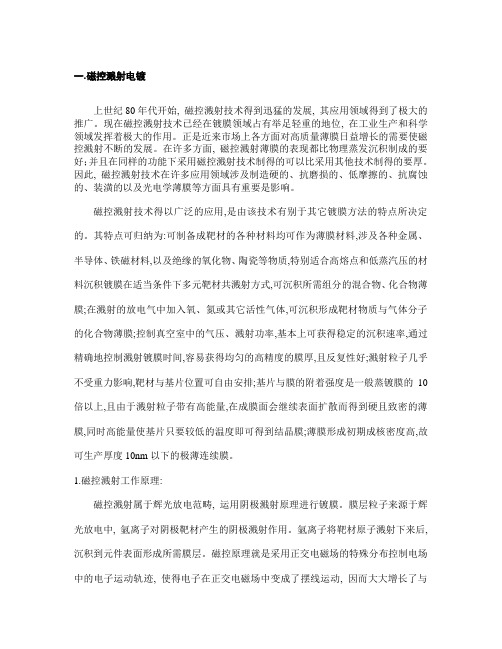
一.磁控溅射电镀上世纪80年代开始, 磁控溅射技术得到迅猛的发展, 其应用领域得到了极大的推广。
现在磁控溅射技术已经在镀膜领域占有举足轻重的地位, 在工业生产和科学领域发挥着极大的作用。
正是近来市场上各方面对高质量薄膜日益增长的需要使磁控溅射不断的发展。
在许多方面, 磁控溅射薄膜的表现都比物理蒸发沉积制成的要好;并且在同样的功能下采用磁控溅射技术制得的可以比采用其他技术制得的要厚。
因此, 磁控溅射技术在许多应用领域涉及制造硬的、抗磨损的、低摩擦的、抗腐蚀的、装潢的以及光电学薄膜等方面具有重要是影响。
磁控溅射技术得以广泛的应用,是由该技术有别于其它镀膜方法的特点所决定的。
其特点可归纳为:可制备成靶材的各种材料均可作为薄膜材料,涉及各种金属、半导体、铁磁材料,以及绝缘的氧化物、陶瓷等物质,特别适合高熔点和低蒸汽压的材料沉积镀膜在适当条件下多元靶材共溅射方式,可沉积所需组分的混合物、化合物薄膜;在溅射的放电气中加入氧、氮或其它活性气体,可沉积形成靶材物质与气体分子的化合物薄膜;控制真空室中的气压、溅射功率,基本上可获得稳定的沉积速率,通过精确地控制溅射镀膜时间,容易获得均匀的高精度的膜厚,且反复性好;溅射粒子几乎不受重力影响,靶材与基片位置可自由安排;基片与膜的附着强度是一般蒸镀膜的10倍以上,且由于溅射粒子带有高能量,在成膜面会继续表面扩散而得到硬且致密的薄膜,同时高能量使基片只要较低的温度即可得到结晶膜;薄膜形成初期成核密度高,故可生产厚度10nm以下的极薄连续膜。
1.磁控溅射工作原理:磁控溅射属于辉光放电范畴, 运用阴极溅射原理进行镀膜。
膜层粒子来源于辉光放电中, 氩离子对阴极靶材产生的阴极溅射作用。
氩离子将靶材原子溅射下来后,沉积到元件表面形成所需膜层。
磁控原理就是采用正交电磁场的特殊分布控制电场中的电子运动轨迹, 使得电子在正交电磁场中变成了摆线运动, 因而大大增长了与气体分子碰撞的几率。
用高能粒子(大多数是由电场加速的气体正离子)撞击固体表面(靶), 使固体原子(分子)从表面射出的现象称为溅射。
TCO技术——精选推荐

TCO技术TCO玻璃技术调查⼀、薄膜太阳能电池对TCO玻璃的要求1.1薄膜电池对TCO玻璃的⼀般要求1.光谱透过率为了能够充分地利⽤太阳光,TCO镀膜玻璃要保持相对较⾼的透过率。
对于TCO玻璃,光透过率越⼤越好。
2.导电性能TCO薄膜的导电原理是在原本导电能⼒很弱的本征半导体中掺⼊微量的其他元素,使半导体的导电性能发⽣显著变化。
这些微量元素被称为杂质,掺杂后的半导体称为杂质半导体。
氧化铟锡(ITO)透明导电玻璃就是将锡元素掺⼊到氧化铟中,提⾼导电率,它的导电性能在⽬前是最好的,最低电阻率达10-5Ωcm量级。
3.雾度为了增加薄膜电池半导体层吸收光的能⼒,光伏⽤TCO玻璃需要提⾼对透射光的散射能⼒,这⼀能⼒⽤雾度(Haze)来表⽰。
雾度即为透明或半透明材料的内部或表⾯由于光漫射造成的云雾状或混浊的外观。
以漫射的光通量与透过材料的光通量之⽐的百分率表⽰。
⼀般情况下,普通镀膜玻璃要求膜层表⾯越光滑越好,雾度越⼩越好,但光伏⽤TCO玻璃则要求有⼀定的光散射能⼒,雾度值的⼤⼩根据吸光效率来确定。
⼀般公认的散射理论认为接近光线波长的颗粒会促进向前散射,所以在光伏⾏业要求提供粒径是100-500nm的颗粒来达到要求的雾度⽔平。
⽬前,雾度控制⽐较好的商业化TCO玻璃是AFG的PV-TCO玻璃,雾度值⼀般为11%~15%。
其不包含散射时的直接透过率曲线。
4.激光刻蚀性能薄膜电池在制作过程中,需要将表⾯划分成多个长条状的电池组,这些电池组被串联起来⽤以提⾼输出能效。
因此,TCO玻璃在镀半导体膜之前,必须要对导电膜进⾏刻划,被刻蚀掉的部分必须完全除去氧化物导电膜层,以保持绝缘。
刻蚀⽅法⽬前有化学刻蚀和激光刻蚀两种,但由于刻蚀的线条要求很细,⼀般为⼏⼗微⽶的宽度,⽽激光刻蚀具有沟槽均匀,剔除⼲净,⽣产效率快的特点。
5.耐候性与耐久性TCO镀膜⼀般都使⽤“硬膜”镀制⼯艺,膜层具有良好的耐磨性、耐酸碱性。
光伏电池在安装上以后,尤其是光伏⼀体化建筑安装在房顶和幕墙上时,不适宜进⾏经常性的维修与更换,这就要求光伏电池具有良好的耐久性,⽬前,⾏业内通⽤的保质期是⼆⼗年以上。
0093.磁控溅射制备TCO薄膜及其在SHJ太阳电池的应用-石建华
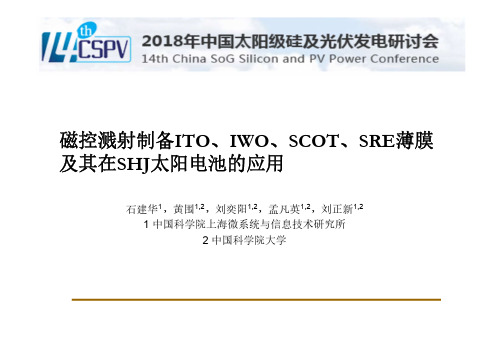
磁控溅射制备ITO、IWO、SCOT、SRE薄膜及其在SHJ太阳电池的应用石建华1,黄围1,2,刘奕阳1,2,孟凡英1,2,刘正新1,21 中国科学院上海微系统与信息技术研究所2 中国科学院大学内容I.SHJ太阳电池研究背景II.高效SHJ太阳电池用TCO薄膜研究进展III.ITO\IWO\SCOT\SRE光电性能研究及应用IV.小结特点:完美全面积非晶薄膜钝化----高开压(Voc )完美双面对称结构及低温工艺----超薄柔性化双面受光----发电效率增益超过15%N 型晶体硅衬底----无PID\LID量产推广初期----设备/辅材价格昂贵、经验缺乏SHJ 太阳电池研究背景Silicon heterojunction solar cell(SHJ)SHJ 基本结构Perovskite/SHJ tandem 1985199019952000202020252030叠层转化效率超过30%指日可待!N o r m a l i z e d a b s o r p t i o nTCO1e qN02(p e c N Conductivity( ) 1/N eFree carrier absorption(FCA) N 矛盾!高迁移率TCO 材料成为首选磁控溅射系统自行设计,具有以下几个特点:、磁力线分部可调,3、样品与磁力线夹角可调(与上海福宜真空设备有限公司产学研结合)Ref功函数失配形成的肖特基势垒会严重阻碍载流子的传输,而界面缺陷层导致严重的复合小结1.SP技术可制备高迁移率、低电阻率TCO薄膜材料2.ITO薄膜中,Sn有效掺杂率与掺杂源浓度有关3.In2O3基的TCO薄膜掺杂种类影响生长方式、结晶度、成键类型4.TCO/非晶硅界面状态决定SHJ太阳电池转化效率5.应用于高效SHJ太阳电池的TCO薄膜需要进一步关注薄膜制备方法特别是初期成膜方式对界面的影响感谢聆听!中国科学院上海微系统与信息技术研究所新能源技术中心。
磁控溅射薄膜淀积工艺原理

磁控溅射薄膜淀积工艺原理
磁控溅射薄膜淀积工艺是一种物理气相沉积(PVD)的方法,其工作原理可以简要概述为以下几个步骤:
1. 电子加速和电离: 在高真空的环境下,入射离子(通常为氩离子,Ar+)
在电场的作用下轰击靶材。
与此同时,电子在飞向基片的过程中与氩原子发生碰撞,使其电离产生新的Ar+离子和电子。
2. 电子束缚和二次电子发射: 新产生的电子在电场和磁场的作用下产生漂移,形成一种类似于摆线的运动轨迹。
在环形磁场的情况下,这些电子会在靶表面附近做圆周运动。
这个过程中,二次电子被束缚在靠近靶表面的等离子体区域内,并且在该区域中电离出大量的Ar+来轰击靶材。
3. 靶材溅射和薄膜形成: Ar+离子在电场的作用下加速飞向阴极靶,并以高
能量轰击靶表面,使靶材发生溅射。
溅射出的中性靶原子或分子沉积在基片上形成薄膜。
4. 温度控制: 由于二次电子的能量很低,传递给基片的能量很小,因此基片
的温升较低。
这使得磁控溅射工艺具有沉积温度低、基片温升低的优点。
磁控溅射的优点包括沉积温度低、沉积速度快、所沉积的薄膜均匀性好,成分接近靶材成分等。
这种工艺在高精度、高性能薄膜制备领域具有广泛应用。
《磁控溅射法制备透明导电氧化物薄膜及其性能研究》
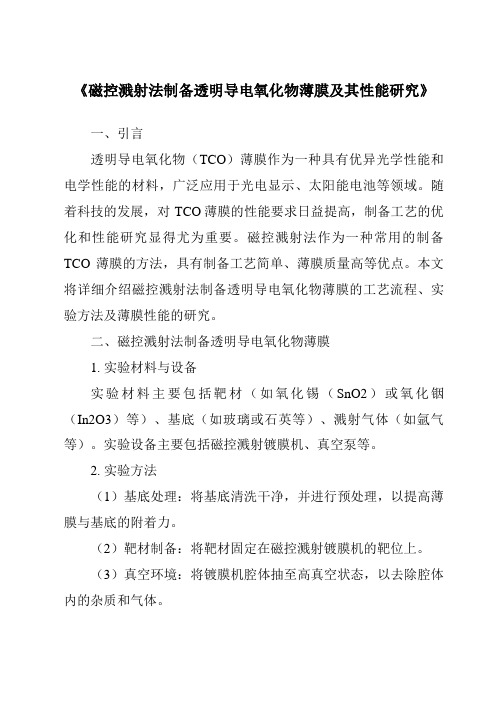
《磁控溅射法制备透明导电氧化物薄膜及其性能研究》一、引言透明导电氧化物(TCO)薄膜作为一种具有优异光学性能和电学性能的材料,广泛应用于光电显示、太阳能电池等领域。
随着科技的发展,对TCO薄膜的性能要求日益提高,制备工艺的优化和性能研究显得尤为重要。
磁控溅射法作为一种常用的制备TCO薄膜的方法,具有制备工艺简单、薄膜质量高等优点。
本文将详细介绍磁控溅射法制备透明导电氧化物薄膜的工艺流程、实验方法及薄膜性能的研究。
二、磁控溅射法制备透明导电氧化物薄膜1. 实验材料与设备实验材料主要包括靶材(如氧化锡(SnO2)或氧化铟(In2O3)等)、基底(如玻璃或石英等)、溅射气体(如氩气等)。
实验设备主要包括磁控溅射镀膜机、真空泵等。
2. 实验方法(1)基底处理:将基底清洗干净,并进行预处理,以提高薄膜与基底的附着力。
(2)靶材制备:将靶材固定在磁控溅射镀膜机的靶位上。
(3)真空环境:将镀膜机腔体抽至高真空状态,以去除腔体内的杂质和气体。
(4)溅射镀膜:在磁控溅射镀膜机中,通过调节溅射功率、气体流量、基底温度等参数,实现TCO薄膜的制备。
三、薄膜性能研究1. 光学性能通过紫外-可见光谱仪测试TCO薄膜的透光率,分析薄膜的光学带隙、光学常数等性能。
同时,还可以通过SEM(扫描电子显微镜)观察薄膜的表面形貌,分析薄膜的光散射性能。
2. 电学性能采用四探针法或霍尔效应测试仪等设备测试TCO薄膜的电阻率、载流子浓度和迁移率等电学性能参数。
通过分析这些参数,可以评估TCO薄膜的导电性能和稳定性。
四、结果与讨论1. 实验结果通过磁控溅射法制备的TCO薄膜具有较高的透光率和较低的电阻率,满足光电显示、太阳能电池等领域的应用需求。
此外,薄膜的表面形貌良好,光散射性能较低。
在实验过程中,通过调整溅射功率、气体流量、基底温度等参数,可以实现对TCO薄膜性能的优化。
2. 结果讨论(1)溅射功率对TCO薄膜性能的影响:随着溅射功率的增加,薄膜的结晶性和致密度提高,从而提高了薄膜的透光率和导电性能。
磁控溅射制备硅薄膜太阳能电池片制造设备的技术创新

磁控溅射制备硅薄膜太阳能电池片制造设备的技术创新随着全球对清洁能源的需求越来越高,太阳能电池作为可再生能源的重要组成部分之一,其制备技术也得到了持续的改进和创新。
其中,磁控溅射技术作为制备硅薄膜太阳能电池片的关键步骤之一,其技术创新也成为研究的热点之一。
本文将就磁控溅射制备硅薄膜太阳能电池片制造设备的技术创新进行详细探讨。
磁控溅射技术是一种利用高能量离子轰击固体靶材使其表面达到蒸发实现薄膜沉积的技术。
在硅薄膜太阳能电池片制造中,磁控溅射技术被广泛应用于制备透明导电薄膜和抗反射膜。
然而,传统的磁控溅射技术存在一些问题,如薄膜致密性不佳、薄膜结晶度不高等,制约了硅薄膜太阳能电池片的性能提升。
近年来,研究人员对磁控溅射技术进行了不断的改进和创新,以提高硅薄膜太阳能电池片的制造效率和性能。
首先,研究人员改进了靶材的制备方法,采用了更加纯净且均匀的靶材,减少了杂质对薄膜质量的影响。
其次,在磁控溅射过程中,优化了离子轰击能量和角度,使得薄膜得以更加均匀地沉积在衬底上,并提高了薄膜的致密性和结晶度。
除此之外,研究人员还通过控制溅射工艺参数,实现了硅薄膜太阳能电池片的复合制备。
例如,采用双靶溅射技术,相比于传统单靶溅射技术,可以实现更高的沉积速率和更好的薄膜质量。
此外,还有磁控溅射辅助化学反应和后处理方法等,通过进一步优化薄膜的结构和性能。
此外,随着纳米技术的发展,一些研究人员尝试将磁控溅射技术与纳米材料相结合,实现硅薄膜太阳能电池片的纳米化制备。
通过在纳米尺度上调控薄膜的结构和特性,可以进一步提高硅薄膜太阳能电池片的光电转换效率和稳定性。
例如,研究人员利用纳米银颗粒作为辅助材料,实现了硅薄膜太阳能电池片的纳米化制备,并获得了较高的光电转换效率。
总的来说,磁控溅射制备硅薄膜太阳能电池片制造设备的技术创新是为了提高制备效率和薄膜质量,进一步推动硅薄膜太阳能电池片在能源领域的应用。
通过改进靶材制备方法、优化溅射工艺参数、采用复合制备技术和结合纳米材料的方法,研究人员不断改进磁控溅射技术,提高了硅薄膜太阳能电池片的性能和稳定性。
磁控溅射法制备高质量铁电薄膜及其应用研究

磁控溅射法制备高质量铁电薄膜及其应用研究随着科学技术的不断发展,磁控溅射法成为制备高质量铁电薄膜的一种重要方法。
铁电薄膜在各种电子器件中具有重要的应用,因此磁控溅射法制备高质量铁电薄膜及其应用研究备受关注。
一、磁控溅射法的基本原理磁控溅射法是一种在高真空环境下制备表面涂层的物理气相沉积方法。
它利用磁场将电子束产生的气体离子输送到靶材表面,使得靶材表面原子挥发并随后沉积在基底上。
磁控溅射法制备铁电薄膜时,可以控制靶材的组分并在不同的气氛下进行,从而实现对铁电薄膜成分、结构的调控。
二、磁控溅射法制备高质量铁电薄膜的优势磁控溅射法制备铁电薄膜具有许多优势。
首先,它能够制备具有多种组分的铁电薄膜,以及利用掺杂技术或复合材料制备具有不同性能的铁电薄膜。
其次,磁控溅射法制备铁电薄膜的工艺条件相对简单,适用于批量生产。
最重要的是,磁控溅射法可以制备高光学质量、高结晶性、低缺陷密度的铁电薄膜,在较宽的温度范围内呈现良好的铁电性能,可应用于机电耦合、传感器、存储器、微电子器件等领域。
三、铁电薄膜的应用研究铁电薄膜在各种电子器件中具有重要的应用,如存储器、传感器、电容器、可再生能源等领域。
在存储器中,铁电薄膜具有非易失、高密度、高速性能,是替代磁存储的重要方向。
在传感器方面,铁电薄膜具有良好的应变灵敏度和压电转换特性,可用于生物医学、工业监测等领域。
此外,铁电薄膜还有望在可再生能源、锂离子电池等领域得到更加广泛的应用。
四、磁控溅射法提高铁电薄膜的性能及其未来发展虽然磁控溅射法制备铁电薄膜的性能已经得到很大的提高,但仍存在一些挑战。
首先,由于电荷分布和电场分布的不均匀性,容易出现铁电失活现象。
其次,铁电薄膜的介电性能易受厚度限制及表面掺杂的影响。
因此,未来需要进一步研究如何在磁控溅射法制备铁电薄膜的过程中有效地解决这些问题,以提高铁电薄膜的性能。
总之,在不断发展的现代科技中,磁控溅射法制备高质量铁电薄膜的研究是非常重要的。
磁控溅射设备构造及其沉积薄膜原理
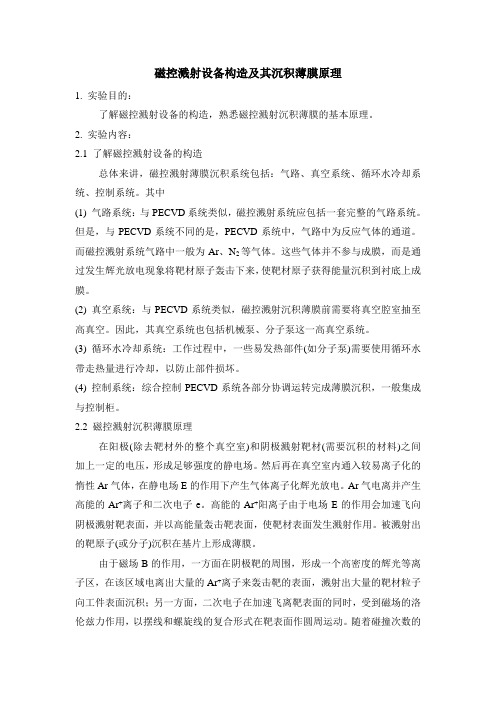
磁控溅射设备构造及其沉积薄膜原理1. 实验目的:了解磁控溅射设备的构造,熟悉磁控溅射沉积薄膜的基本原理。
2. 实验内容:2.1 了解磁控溅射设备的构造总体来讲,磁控溅射薄膜沉积系统包括:气路、真空系统、循环水冷却系统、控制系统。
其中(1) 气路系统:与PECVD系统类似,磁控溅射系统应包括一套完整的气路系统。
但是,与PECVD系统不同的是,PECVD系统中,气路中为反应气体的通道。
而磁控溅射系统气路中一般为Ar、N2等气体。
这些气体并不参与成膜,而是通过发生辉光放电现象将靶材原子轰击下来,使靶材原子获得能量沉积到衬底上成膜。
(2) 真空系统:与PECVD系统类似,磁控溅射沉积薄膜前需要将真空腔室抽至高真空。
因此,其真空系统也包括机械泵、分子泵这一高真空系统。
(3) 循环水冷却系统:工作过程中,一些易发热部件(如分子泵)需要使用循环水带走热量进行冷却,以防止部件损坏。
(4) 控制系统:综合控制PECVD系统各部分协调运转完成薄膜沉积,一般集成与控制柜。
2.2 磁控溅射沉积薄膜原理在阳极(除去靶材外的整个真空室)和阴极溅射靶材(需要沉积的材料)之间加上一定的电压,形成足够强度的静电场。
然后再在真空室内通入较易离子化的惰性Ar气体,在静电场E的作用下产生气体离子化辉光放电。
Ar气电离并产生高能的Ar+离子和二次电子e。
高能的Ar+阳离子由于电场E的作用会加速飞向阴极溅射靶表面,并以高能量轰击靶表面,使靶材表面发生溅射作用。
被溅射出的靶原子(或分子)沉积在基片上形成薄膜。
由于磁场B的作用,一方面在阴极靶的周围,形成一个高密度的辉光等离子区,在该区域电离出大量的Ar+离子来轰击靶的表面,溅射出大量的靶材粒子向工件表面沉积;另一方面,二次电子在加速飞离靶表面的同时,受到磁场的洛伦兹力作用,以摆线和螺旋线的复合形式在靶表面作圆周运动。
随着碰撞次数的增加,电子的能量逐渐降低,到达基片后的能量很小,故基片的温升较低。
- 1、下载文档前请自行甄别文档内容的完整性,平台不提供额外的编辑、内容补充、找答案等附加服务。
- 2、"仅部分预览"的文档,不可在线预览部分如存在完整性等问题,可反馈申请退款(可完整预览的文档不适用该条件!)。
- 3、如文档侵犯您的权益,请联系客服反馈,我们会尽快为您处理(人工客服工作时间:9:00-18:30)。
磁控溅射法沉积TCO薄膜的电源技术1前言透明导电氧化物薄膜(TCO薄膜)有着广泛的用途,如作为LCD、OLED显示器面板的电极,作为触摸屏的感应电极,作为薄膜太阳能电池的电极以及作为LED芯片前电极等[1]。
目前,主要的TCO薄膜有氧化铟锡(ITO)、氧化锡(SnO2)、氧化锌铝(AZO)三种[2],其中SnO2薄膜是最早应用的TCO薄膜,但由于其光电特性相对较差,目前主要应用在一些较低端的使用领域。
ITO薄膜是目前光电特性最好,使用范围最广的TCO薄膜,但其同时存在使用稀有元素In,生产成本较高、In元素有毒、在氢等离子工艺氛围中性能退化等缺点。
近年来,成本低、性能优良、无毒害的ZnO:Al(AZO)薄膜[3]得到了广泛的关注与研究,有希望替代ITO薄膜。
因此,ITO与AZO材料是当前研究和生产的最主要的TCO材料。
目前,产业界制备ITO、AZO薄膜主要是采用磁控溅射镀膜技术[4][5]。
磁控溅射技术基于等离子技术,通常是在存在高电势差的靶(阴极)与阳极之间注入气体(一般为Ar气),通过等离子辉光放电实现对气体原子的离化,电场与磁场对离子加速和变向,进而轰击靶材表面,导致靶材原子被轰击到空间中,溅射在一块衬底材料上聚集形成薄膜[6]。
对于磁控溅射装置,磁控溅射电源决定了磁控溅射工艺过程等离子体状态,对镀膜工艺和膜层生长质量起着至关重要的作用[7]。
随着生产和科技不断发展,用户对产品质量性能的要求越来越高。
所以要求磁控溅射镀膜设备具有良好的可靠性、稳定性,有较高的镀膜效率和镀膜质量。
本文将主要描述磁控溅射ITO、AZO两大主要TCO薄膜的核心电源技术的发展现状、最新进展以及未来面临的挑战。
2磁控溅射TCO薄膜的电源技术发展概述2.1磁控溅射直流电源磁控溅射电源类型有直流电源、中频电源和射频电源。
其中中频电源与射频电源成本较高,且沉积速率偏慢,尤其是射频电源沉积速率慢且由于驻波效应等,不适宜进行大面积镀膜,因此在制备大面积TCO薄膜技术领域应用较少。
TCO薄膜制备以直流磁控溅射技术为主。
直流磁控电源简单可靠、工作稳定、功率大、沉积速率快。
直流电源主要有恒流、恒压、恒功率等控制模式以恒流磁控溅射直流电源系统为例,其基本原理如图1所示。
电路由主电路部分和控制部分组成。
电网输入单相交流电,通过工频整流,电感电容整流后为直流电。
功率电子器件在控制电路的控制下将直流转换为脉冲交流电。
经高频变压器,将交流脉冲升压。
然后通过二极管整流和电感滤波输出直流。
控制部分由PWM控制、IGBT驱动、恒流控制、过流保护等部分组成。
普通直流电源虽然已在在磁控溅射TCO薄膜生产中大量应用,但仍然存在很多缺点:(1)TCO镀膜过程容易生成不导电物质,随着溅射过程中带电离子在不导电物质上的沉积,会形成弧光放电斑点[8]。
尤其是AZO镀膜过程,弧光放电斑点时时刻刻大量存在,容易导致薄膜出现斑点、孔洞、变性等各种缺陷,导致膜层质量不高,生产良率低。
(2)由于电弧出现的频率与磁控溅射功率成正比,因此,限制了磁控溅射功率进一步的增大,即限制了镀膜生产速率进一步的提高。
(3)磁控溅射过程等离子密度低。
被溅射物质的离化程度极低,导致晶格缺陷、高残余应力以及薄膜与衬底表面结合差[9]。
(4)由于被溅射物质离化程度低,被溅射物质只能直线运动,覆盖区域浅,无法对复杂构造物体表面全面镀膜,这一点远差于多弧离子镀技术,制约了磁控溅射技术的应用空间[10]。
2.2磁控溅射脉冲电源磁控溅射脉冲电源的一个不可比拟的优点,是可以抑制溅射靶面的弧光放电。
通过一定的频率输出脉冲电流,使镀膜过程绝缘层上积累的正电荷,在形成弧光放电条件之前被中和掉。
脉冲溅射技术实现的关键在于大功率脉冲电源[11]。
为了在正半周内完全中和负半周中靶面绝缘层表面积累正电荷,脉冲电压必须具有一定的波形参数。
Schiller等通过计算指出,脉冲电压的频率应为数10kHz[12]。
进一步的大量实验研究表明,脉冲磁控溅射电源的脉冲频率设计在中频10kHz-200kHz时,可以有效防止靶材电弧放电及稳定反应溅射沉积工艺,实现高速沉积、高质量反应薄膜。
如图2所示,为一种脉冲电源系统的基本结构。
主要包括三相整流及控制电路,逆变及控制电路,保护电路等。
三相电源经整流电路整流后,变成脉动的直流电,然后由R、C 网络滤波后送至全桥逆变器,在控制电路的控制下与LCC串联、并联电路谐振,输出变压器与并联电容相并联,并隔离驱动负载。
图2 磁控溅射脉冲电源原理示意图虽然磁控溅射脉冲电源具备了灭弧的功能,能有效提升磁控溅射制备TCO薄膜的工艺质量,但其仍存在一些缺点:(1)价格昂贵。
稳定可靠的大功率脉冲电源造价昂贵,为普通直流电源一倍以上。
(2)维护成本高。
(3)无法解决传统磁控溅射过程等离子密度低,成膜质量一般,不具备复杂结构表面镀膜功能的问题。
针对这些问题,在最新的磁控溅射电源技术进展中逐步提出了解决方案。
3. 磁控溅射TCO电源最新技术3.1具备快速灭弧补偿功能的直流电源针对在TCO薄膜直流磁控溅射过程中(尤其是AZO镀膜)存在大量弧光放电现象的问题,为降低电源成本,一个新的重要发展方向是采用带快速灭弧功能的直流电源。
这种电源的最关键技术是3点:①当弧光放电发生时能在早期迅速检测到做出合理判断。
②在识别出弧光放电情况后能迅速切断电源而灭掉电弧;③在切断电源后,恢复磁控放电。
在此基础上,通过采用补偿技术,可进一步减少灭弧后残余能量的影响,精细优化镀膜质量。
目前主要有3种不同的电弧监测方法[13]:(1)基于弧光放电电流探测的检测方法在输出电流Iout超过用户设定电流阈值Ix时作出反应(图3)。
侦测时间取决于设定的阈值,通常为300ns。
关断时间大约为1.5μs。
中断时间和恢复时间可以分别设定在0ms~80ms或者0ms~100ms。
图3 基于电流检测弧光放电的原理图(2)基于弧光放电时的电压检测方法当电压超过用户设定的阈值时监测器开始工作,电压低于用户设定的阈值时监测器触发。
(3)基于电压电流结合的检测方法当输出电压低于用户设定的电压阈值而电流高于用户设定的电流阈值时监测器工作。
在快速检测和切断灭弧的系统基础上,电源具备灭弧补偿技术可进一步提升工艺的可靠性。
这种技术的基本原理,是当电弧被检测到以及关断电源以后,给电源电缆施加一个正电压,使电缆上的负电压很快消失,可以进一步减小监测出电弧以后传送到溅射阴极上的剩余能量,优化镀膜质量。
如图4所示,为一种灭弧补偿装置的原理。
在正常工作时,电容C被充电。
发生电弧时,快速切换开关SS打开,电容对电缆施加一个正的电压。
电源与阴极之间的感应能量可以通过公式E=(LI2)/2计算出来。
假设电缆电感为每米L=1μH,那么对10m长的电缆和电流为I=100A的电弧,能量为50mJ。
图4 灭弧补偿装置原理示意图增加补偿装置以后的电弧监测系统可以再实现快速关断的同时,显著减小电弧能量到1mJ/kW以下。
Dirk Ochs等人实验研究了采用补偿装置的电源在镀AZO薄膜过程的实际效用。
如图5所示,在AZO溅射过程中的一次电弧发生时,电流从工艺中的10A上升到约30A。
大约2μs后电源关断,电流下降。
又过了7μs后电流下降到大约0A。
具备补偿装置的电源其电流下降得更迅速。
电流下降到零的时间不足1μs。
这样显著减小了输送到电弧的能量,使其低于1mJ/kW。
图5 电弧发生时具备补偿装置(CL)及不具备补偿装置的电流波形对比在同样的工艺下,Dirk Ochs[14]对具备灭弧补偿功能的直流电源和普通脉冲电源(脉冲电源的频率为50kHz,占空比为75%)进行了对比。
在玻璃上沉积460nm厚的AZO膜层并检测其透光率。
结果显示,对应两种工艺的透光率完全一样。
两种样品都在真空下350℃退火15min,退火后,短波段下的透光率稍微上升,而长波段的透过率下降。
同样,两种工艺下的结果一样。
两种沉积工艺下的电阻率对比也显示了相似的结果。
因此,采用有效的快速电弧关断恢复技术的新型直流电源技术,相比脉冲直流电源技术性能相当,成本更低,具备广阔的发展空间。
这种技术的主要缺点是,仍然无法解决传统磁控溅射过程溅射物质离化率低,成膜质量一般,不具备复杂结构表面镀膜功能的弱点。
此外,由于大功率化制造成本较高,可靠性较低,也制约了其大功率化发展。
3.2模块化磁控溅射电源为了提高磁控溅射电源性能,同时降低成本、提高系统可靠性和降低设备的稼动率,业界采用了电源模块化的概念。
电源系统可按单台20kw或30kw或其它功率值设计成一个模块。
模块之间组合堆栈(主/从设计)。
各模块机架可完全分离,便于用户以后的扩容或减容,使用非常方便,故障处理简单方便,有利于提高生产效率。
模块化技术的引入,进一步的推广了磁控溅射电源的应用。
3.3 HPPMS专用脉冲直流电源上文介绍的各种磁控溅射电源虽然都有不少优点,但始终无法解决传统磁控溅射过程中溅射物质原子的离化率极低的弱点。
高功率脉冲磁控溅射技术(HPPMS)[15]是近年来新兴的重要发展方向,它通过HPPMS 专用电源可以大幅提升溅射物质原子的离化率[16][17]。
通过外加电场和磁场可大幅增强对溅射物质成膜工艺过程的精确控制,可以制备更加精细可靠的薄膜,可以实现更复杂结构外表的全方位可控镀膜,同时,充分有效的离子轰击衬底,可实现低温镀膜,实现在塑料柔性衬底材料镀膜。
在这一领域,Kouznetsov等[15]率先取得重要突破,他通过实验证实在Cu的溅射过程中引入这种高脉冲电流,获得了比传统直流溅射高两个数量级的离子密度,其溅射物质离化率高达70%。
离子流大小比传统磁控溅射高2-3个数量级,改善效果十分明显,具有革命性的意义。
实现HPPMS技术的关键之一在于电源,其必须可以提供高功率密度的脉冲波(通常为几kW/cm2左右),同时保证施加在靶上的平均功率密度与传统直流磁控溅射相当(几W/cm2左右)[18],以防止阴极过热导致靶材、磁铁、靶体过热损坏。
目前,一些研究机构和公司已经研制出各种HPPMS电源装置,应用在实验室及生产线上,这些装置的基本结构原理相似,如图6所示。
一台直流电源用以给脉冲发生部分的电容器组充电,脉冲发生部分与磁控溅射阴极直接连接。
电容器组的充电电压从几100V到几1000V不等。
脉冲发生部分通过斩波电路将直流电压、电流变换成频率和脉宽均可调的脉冲电压和电流。
斩波电路使用IGBT模块,将IGBT作为开关串联在直流回路中,通过触发脉冲控制半导体开关的通断,进而控制了脉冲电压的输出。
图6 HPPMS电源的基本架构图Kouznetsov等人研究表明,输出脉冲的脉宽在5ms -5000ms,频率在10Hz-10kHz范围时,靶的电流密度峰值可达到数A/cm2量级,比传统直流磁控溅射电流密度高3个数量级。