塑胶成型常见问题分析
塑胶件常见缺陷不良分析及对策讲解
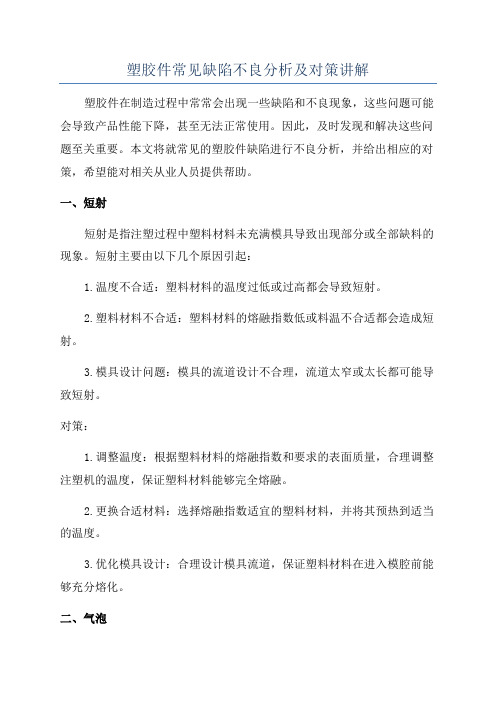
塑胶件常见缺陷不良分析及对策讲解塑胶件在制造过程中常常会出现一些缺陷和不良现象,这些问题可能会导致产品性能下降,甚至无法正常使用。
因此,及时发现和解决这些问题至关重要。
本文将就常见的塑胶件缺陷进行不良分析,并给出相应的对策,希望能对相关从业人员提供帮助。
一、短射短射是指注塑过程中塑料材料未充满模具导致出现部分或全部缺料的现象。
短射主要由以下几个原因引起:1.温度不合适:塑料材料的温度过低或过高都会导致短射。
2.塑料材料不合适:塑料材料的熔融指数低或料温不合适都会造成短射。
3.模具设计问题:模具的流道设计不合理,流道太窄或太长都可能导致短射。
对策:1.调整温度:根据塑料材料的熔融指数和要求的表面质量,合理调整注塑机的温度,保证塑料材料能够完全熔融。
2.更换合适材料:选择熔融指数适宜的塑料材料,并将其预热到适当的温度。
3.优化模具设计:合理设计模具流道,保证塑料材料在进入模腔前能够充分熔化。
二、气泡气泡是指塑胶件表面或内部出现的小气孔或气泡。
气泡可能导致产品外观不良或性能下降。
气泡的产生主要有以下几个原因:1.塑料材料中含有挥发性成分:一些塑料材料中含有挥发性成分,如果注塑温度过高,这些挥发性成分就会挥发出来形成气泡。
2.模具表面不洁净:如果模具表面不干净或有油污等杂质,气泡就会在塑料注入过程中被吸附在塑料中形成。
3.注塑机压力过高:注塑机压力过高会导致空气被压进模具中,形成气泡。
对策:1.调整注塑温度:根据塑料材料的特性,合理调整注塑温度。
温度过高易导致气泡产生,温度过低则容易短射。
2.模具清洁:保持模具表面干净,定期对模具进行清洗,去除杂质和油污。
3.控制注塑机压力:根据塑料材料的特性和模具的要求,合理控制注塑机的压力,避免空气进入模具。
三、热处理不当塑胶件经过热处理后,如果处理不当,可能导致产品性能下降或出现变形等问题。
常见的热处理问题有:1.温度不合适:热处理时,温度不合适会导致产品硬度不均匀或过硬。
塑胶成型不良分析
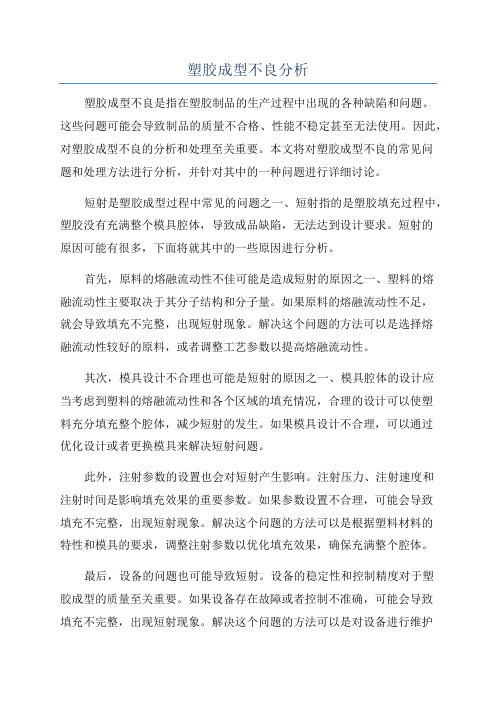
塑胶成型不良分析塑胶成型不良是指在塑胶制品的生产过程中出现的各种缺陷和问题。
这些问题可能会导致制品的质量不合格、性能不稳定甚至无法使用。
因此,对塑胶成型不良的分析和处理至关重要。
本文将对塑胶成型不良的常见问题和处理方法进行分析,并针对其中的一种问题进行详细讨论。
短射是塑胶成型过程中常见的问题之一、短射指的是塑胶填充过程中,塑胶没有充满整个模具腔体,导致成品缺陷,无法达到设计要求。
短射的原因可能有很多,下面将就其中的一些原因进行分析。
首先,原料的熔融流动性不佳可能是造成短射的原因之一、塑料的熔融流动性主要取决于其分子结构和分子量。
如果原料的熔融流动性不足,就会导致填充不完整,出现短射现象。
解决这个问题的方法可以是选择熔融流动性较好的原料,或者调整工艺参数以提高熔融流动性。
其次,模具设计不合理也可能是短射的原因之一、模具腔体的设计应当考虑到塑料的熔融流动性和各个区域的填充情况,合理的设计可以使塑料充分填充整个腔体,减少短射的发生。
如果模具设计不合理,可以通过优化设计或者更换模具来解决短射问题。
此外,注射参数的设置也会对短射产生影响。
注射压力、注射速度和注射时间是影响填充效果的重要参数。
如果参数设置不合理,可能会导致填充不完整,出现短射现象。
解决这个问题的方法可以是根据塑料材料的特性和模具的要求,调整注射参数以优化填充效果,确保充满整个腔体。
最后,设备的问题也可能导致短射。
设备的稳定性和控制精度对于塑胶成型的质量至关重要。
如果设备存在故障或者控制不准确,可能会导致填充不完整,出现短射现象。
解决这个问题的方法可以是对设备进行维护和保养,确保设备正常运行。
此外,定期检查和校准设备的控制系统,确保精度和稳定性。
综上所述,塑胶成型不良是塑胶制品生产过程中常见的问题。
对于短射这一问题,其原因可能包括原料、模具设计、注射参数和设备等方面。
为了解决短射问题,可以选择合适的原料,优化模具设计,调整注射参数以及维护设备等措施。
塑胶件常见的缺陷产生原因及解决办法

塑胶件常见的缺陷产生原因及解决办法一、设计方面的缺陷:1.不合理的尺寸设计:塑胶件的尺寸设计不合理可能导致尺寸偏差过大、尺寸不一致等问题。
解决方法是根据塑胶件的具体用途和要求进行合理的尺寸设计,并进行合适的工艺分析和模流分析。
2.没有考虑到材料的特性:不同塑料材料具有不同的热胀冷缩系数、熔融温度等特性,设计时没有考虑到这些特性可能导致尺寸偏差、变形等问题。
解决方法是根据塑料材料的特性进行合适的设计和模具制造选型。
3.模具设计问题:模具设计不合理或者制造质量不过关可能导致塑胶件的缺陷问题。
解决方法是进行合理的模具设计,并选择专业的模具制造厂家。
4.不合理的壁厚设计:塑胶件的壁厚设计不合理可能导致塑胶件变形、收缩不均匀等问题。
解决方法是根据塑胶件的材料特性和实际使用要求进行合理的壁厚设计。
二、材料方面的缺陷:1.材料质量问题:不合格的原料质量可能导致塑胶件出现异味、颜色不均匀等问题。
解决方法是选择合格的塑料原料供应商,并进行原料的严格检验。
2.材料混合不均匀:塑料材料在加工过程中没有充分混合均匀可能导致塑胶件的颜色不均匀等问题。
解决方法是进行充分的原料预处理和混炼,确保塑料材料的均匀性。
3.熔体温度不均匀:塑料材料在注塑过程中温度不均匀可能导致塑胶件尺寸偏差、表面气泡等问题。
解决方法是调整注塑机的温度控制系统,确保熔体温度均匀稳定。
三、工艺方面的缺陷:1.注塑工艺参数设置不当:注塑过程中,如射胶压力、射胶速度、冷却时间等工艺参数设置不当可能导致塑胶件出现尺寸偏差、气泡、表面缺陷等问题。
解决方法是根据塑料的特性和产品要求进行合理的工艺参数设置。
2.模具温控不均匀:模具温度不均匀可能导致塑胶件出现收缩不一致、尺寸偏差等问题。
解决方法是进行模具温度分析和温控系统的优化。
可以采用热流道模具、快速温度控制系统等技术手段解决问题。
3.模具保养不当:模具的使用寿命长,如果没有进行定期的保养和维修可能导致塑胶件出现模纹、模具磨损等问题。
塑胶件常见不良状况及形成原因、改善对策
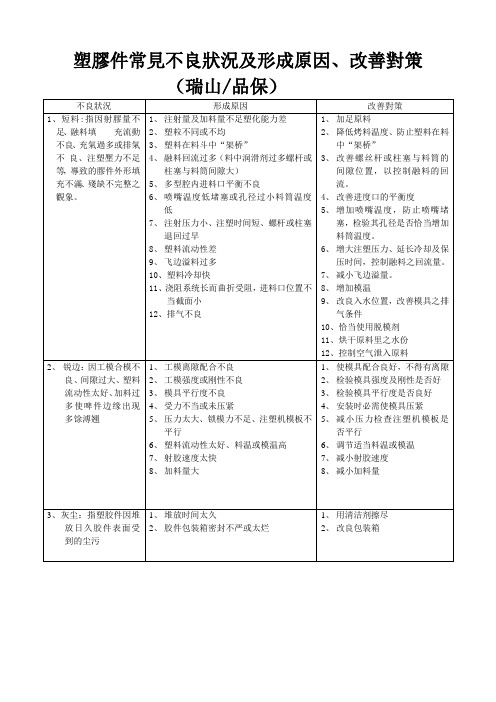
1、模具设计不合理,胶件出模时受力不当
2、胶件因冷却及保压时间不够而引起的收缩性变形
3、包装方式不当或包装胶袋及纸箱不合理保存时间太长或堆放不合理而引起的变形
1、改良模具设计,使之合理
2、延长冷却及保压时间即延长啤塑周期
3、改良包装材料(纸箱胶袋)改善合理的包装方式
6、调节适当料温或模温
7、减小射胶速度
8、减小加料量
3、灰尘:指塑胶件因堆放日久胶件表面受到的尘污
1、堆放时间太久
2、胶件包装箱密封不严或太烂
1、用清洁剂擦尽
2、改良包装箱
4、油垢:指工模防锈油污及脱模剂所致的油污,表现为黄色或黑色斑,一般可用布擦掉
1、工模因停机时所加防锈油及脱模剂在开啤尚时未洗干净
塑膠件常見不良狀況及形成原因、改善對策
(瑞山/品保)
不良狀況
形成原因
改善對策
1、短料:指因射膠量不足、融料填充流動不良、充氣過多或排氣不良、注塑壓力不足等,導致的膠件外形填充不滿、殘缺不完整之觀象。
1、注射量及加料量不足塑化能力差
2、塑粒不同或不均
3、塑料在料斗中“架桥”
4、融料回流过多(料中润滑剂过多螺杆或柱塞与料筒间隙大)
5、模具排气不良
6、模温低
7、注塑时间速度太快
8、模具型腔内有水分,油脂或脱模剂不当
9、加料端空气混入
10、料气死角
1、烤干原料里水分
2、降低料温
3、加大压力
4、螺杆不得过早退回
5、改善模具之排气条件
6、增加模温
7、减小注塑速度
8、保证模具型腔不得有水分,油脂。使用适当脱模剂
9、禁止加料端空气泄入
塑胶成型常见不良原因分析及对策
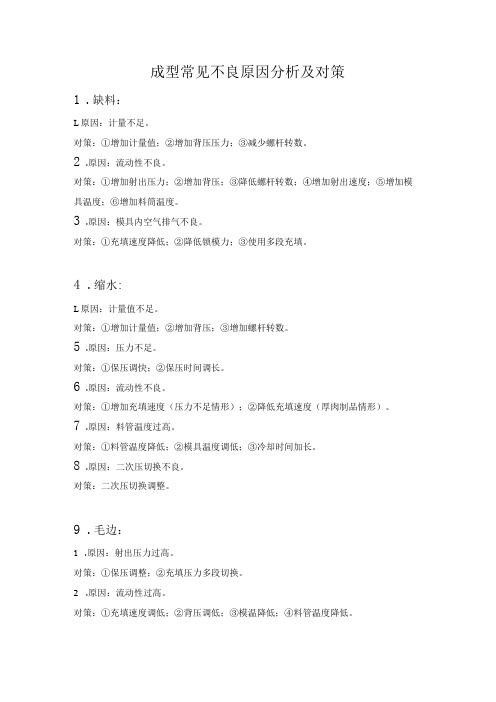
成型常见不良原因分析及对策1.缺料:L原因:计量不足。
对策:①增加计量值;②增加背压压力;③减少螺杆转数。
2.原因:流动性不良。
对策:①增加射出压力;②增加背压;③降低螺杆转数;④增加射出速度;⑤增加模具温度;⑥增加料筒温度。
3.原因:模具内空气排气不良。
对策:①充填速度降低;②降低锁模力;③使用多段充填。
4.缩水:L原因:计量值不足。
对策:①增加计量值;②增加背压;③增加螺杆转数。
5.原因:压力不足。
对策:①保压调快;②保压时间调长。
6.原因:流动性不良。
对策:①增加充填速度(压力不足情形);②降低充填速度(厚肉制品情形)。
7.原因:料管温度过高。
对策:①料管温度降低;②模具温度调低;③冷却时间加长。
8.原因:二次压切换不良。
对策:二次压切换调整。
9.毛边:1.原因:射出压力过高。
对策:①保压调整;②充填压力多段切换。
2.原因:流动性过高。
对策:①充填速度调低;②背压调低;③模温降低;④料管温度降低。
3.原因:二次压切换不良。
对策:①提前切换二次压;②减少计量值。
4.原因:模内空气排出不良。
对策:①充填速度降低;②多段射出;③型缔力调低。
5.原因:锁模力不足,模具密合不够。
对策:锁模力增大。
4.气泡:1.原因:计量时空气进入。
对策:①背压调高;②螺杆转数调低;③进料段温度降低;④降低加热筒后段温度。
2.原因:加热筒内部异常发热。
对策:①增加背压;②减少螺杆转数。
3.原因:松退量过多。
对策:①松退量减少;②松退速度减小。
4.原因:体积收缩。
对策:①增加背压;②延长保压时间;③增高模具温度;④降低料管温度;⑤降低充填速度(厚肉制品情形);⑥增加充填速度(压力不足情形)。
5.原因:模具内空气排出不良。
对策:①降低充填速度;②多段射出;③降低锁模力。
6.气纹:1.原因:速度过快或压力过大。
对策:降压或减速。
2.原因:料温过低。
对策:提高前段温度。
对策:提升模具温度。
4.原因:浇口或太小或太大。
对策:模具改善。
塑胶注塑不良的分析以及处理措施

尺寸标准
对比设计图纸,检查塑胶制品的关键 尺寸是否在允许的公差范围内。
性能标准
根据塑胶制品的具体用途,评估其物 理性能和化学性能是否满足使用要求 。
安全标准
确保塑胶制品在使用过程中不会对人 体造成伤害,符合相关国家和地区的 法律法规。
检测与评估工具
放大镜
用于观察塑胶制品的细 微缺陷。
卡尺
用于测量塑胶制品的尺 寸。
注射压力、温度、时间等参数设置不合理, 影响塑料的流动和成型。
塑料材料问题
塑料材料性能不佳,如收缩率大、流动性差 等,导致成型不良。
模具保养不当
模具保养不善,如清洁不彻底、润滑不足等 ,影响塑料的流动和成型。
02
塑胶注塑不良的检测与评估
检测方法
目视检测
通过观察塑胶制品的外观,检 查是否存在缺料、缩水、气泡
02
塑胶注塑不良的原因多种多样,如模 具设计不合理、塑料材料选择不当、 注塑工艺参数设置不正确等。针对不 同类型的不良现象,需要采取不同的 处理措施。本文对各种不良现象进行 了分类和总结,并详细介绍了相应的 处理方法,有助于提高生产效率和产 品质量。
03
本文还对塑胶注塑技术的发展趋势进 行了展望。随着科技的不断发展,新 型塑料材料和加工技术不断涌现,注 塑技术将朝着高效、环保、智能化的 方向发展。未来,注塑技术将更加注 重节能减排、提高生产效率、降低成 本等方面,为工业生产带来更多的便 利和效益。
案例三:某产品内部气孔问题
总结词
内部气孔是指产品内部存在大小不一的气孔,影响产品的机械性能和外观。
详细描述
气孔通常分布在产品内部,形状不规则。可能的原因包括塑料原料中含有水分或挥发性物质、模具排气不良、塑 料熔体流动不均匀等。
塑胶常见不良及解决方法

塑胶常见不良及解决方法塑胶是一种常见的材料,广泛应用于各种行业和领域。
然而,由于塑胶的特性以及制造过程中的一些问题,常常会出现一些不良现象。
本文将重点介绍一些常见的塑胶不良及其解决方法。
1.氣泡:塑膠制品中常見的一種不良現象是氣泡,這會在成品表面或内部形成小气囊。
气泡的形成是由于塑胶熔融时含有的空气或挥发物没有充分释放出来。
解决方法包括降低加工温度、增加熔体压力、增加注射速度和使用抗气泡添加剂等。
2.热胀冷缩:塑胶制品在温度变化下会发生热胀冷缩,导致尺寸变化。
这可能会导致配件无法正常连接或安装。
为了解决这个问题,可以采用材料改性或加工工艺改进,如增加冷却时间、降低注射温度等。
3.白化:白化是指塑胶制品表面或内部出现白色斑点或条纹。
这种现象通常是由于塑胶在注射过程中发生气泡聚集或制品未达到均匀熔融所致。
解决方法包括优化注射工艺、增加熔体压力、使用抗白化添加剂等。
4.热裂纹:热裂纹是指在塑胶产品成型过程中出现的裂纹现象。
这通常是由于塑胶在成型过程中存在过大的应力集中,导致塑胶产生裂纹。
解决方法包括改变模具设计、增加冷却时间、预混塑胶料等。
5.变色:变色是指塑胶制品在使用或储存过程中出现颜色变化。
这可能是由于塑胶材料受到光、热、氧化等外界因素的影响所致。
解决方法包括选择适当的防褪色添加剂、合理储存塑胶制品等。
6.毛刺:毛刺是指塑胶制品表面出现不平整、刺状的小颗粒。
这通常是由于模具表面不平整或注射工艺不当所导致的。
解决方法包括优化模具设计、控制注射压力、调整注射速度等。
7.缩水:缩水是指塑胶制品在冷却过程中发生体积收缩。
这可能导致尺寸偏离设计要求。
解决方法包括优化塑胶成型工艺、增加冷却时间和选择合适的材料等。
8.潜伏期延长:有些塑胶在使用一段时间后会发生不良现象,如变形、断裂等。
这可能是由于塑胶受到环境因素、应力或热老化的影响导致的。
解决方法包括选择合适的材料、控制加工温度、降低应力等。
总结起来,塑胶制品的不良现象可能是由于材料、工艺或环境等多种因素造成的。
塑胶制品常见问题成因及解决办法
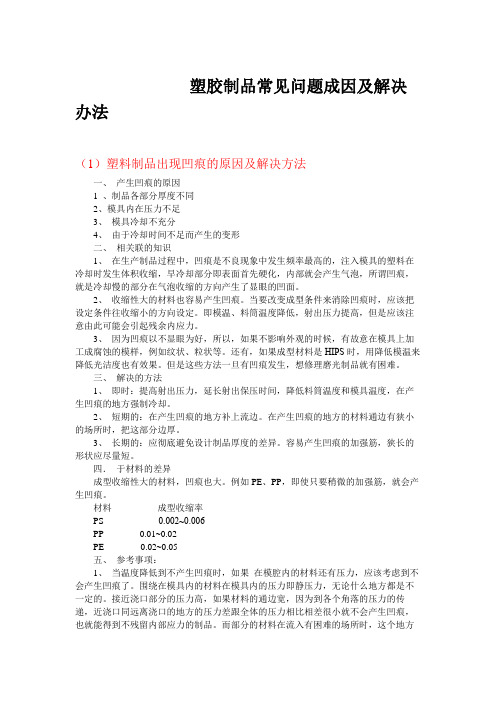
塑胶制品常见问题成因及解决办法(1)塑料制品出现凹痕的原因及解决方法一、产生凹痕的原因1 、制品各部分厚度不同2、模具内在压力不足3、模具冷却不充分4、由于冷却时间不足而产生的变形二、相关联的知识1、在生产制品过程中,凹痕是不良现象中发生频率最高的,注入模具的塑料在冷却时发生体积收缩,早冷却部分即表面首先硬化,内部就会产生气泡,所谓凹痕,就是冷却慢的部分在气泡收缩的方向产生了显眼的凹面。
2、收缩性大的材料也容易产生凹痕。
当要改变成型条件来消除凹痕时,应该把设定条件往收缩小的方向设定。
即模温、料筒温度降低,射出压力提高,但是应该注意由此可能会引起残余内应力。
3、因为凹痕以不显眼为好,所以,如果不影响外观的时候,有故意在模具上加工成腐蚀的模样,例如纹状、粒状等。
还有,如果成型材料是HIPS时,用降低模温来降低光洁度也有效果。
但是这些方法一旦有凹痕发生,想修理磨光制品就有困难。
三、解决的方法1、即时:提高射出压力,延长射出保压时间,降低料筒温度和模具温度,在产生凹痕的地方强制冷却。
2、短期的:在产生凹痕的地方补上流边。
在产生凹痕的地方的材料通边有狭小的场所时,把这部分边厚。
3、长期的:应彻底避免设计制品厚度的差异。
容易产生凹痕的加强筋,狭长的形状应尽量短。
四.于材料的差异成型收缩性大的材料,凹痕也大。
例如PE、PP,即使只要稍微的加强筋,就会产生凹痕。
材料成型收缩率PS 0.002~0.006PP 0.01~0.02PE 0.02~0.05五、参考事项:1、当温度降低到不产生凹痕时,如果在模腔内的材料还有压力,应该考虑到不会产生凹痕了。
围绕在模具内的材料在模具内的压力即静压力,无论什么地方都是不一定的。
接近浇口部分的压力高,如果材料的通边宽,因为到各个角落的压力的传递,近浇口同远离浇口的地方的压力差跟全体的压力相比相差很小就不会产生凹痕,也就能得到不残留内部应力的制品。
而部分的材料在流入有困难的场所时,这个地方有高的压力,其他地方的压力降低就会产生凹痕。
- 1、下载文档前请自行甄别文档内容的完整性,平台不提供额外的编辑、内容补充、找答案等附加服务。
- 2、"仅部分预览"的文档,不可在线预览部分如存在完整性等问题,可反馈申请退款(可完整预览的文档不适用该条件!)。
- 3、如文档侵犯您的权益,请联系客服反馈,我们会尽快为您处理(人工客服工作时间:9:00-18:30)。
塑膠成型常見問題對策分析
壹 . 缺料
原因狀態解決對策備註
一. 材料充填不足 1. 射出壓力未到達最高設定值. 1. 增加射出壓力.
2. 增加射出速度.
3. 增加模溫.
4. 增加料筒溫度.
5. 檢查膠口尺寸.
6. 檢查流道尺寸.
7. 檢查噴嘴溫度.
8. 檢查噴嘴大小.
2. 射出壓力己到達最高設定值. 1. 延長射出行程.
2. 增加保持壓力.
3. 增加保持時間.
3. 螺桿已到達最前端. 1. 延長射出行程.
2. 檢查螺桿.
二. 排氣不良 1. 缺料位於塑膠流路末端. 1. 改善排氣效果.
2. 減低射出速度.
2. 缺料位於其它部分. 1. 改善排氣效果.
2. 增加射出壓力..
3. 增加缺料部分厚度.
三. 包封現象 1. 於產品中心(不在邊緣) 1. 增加排氣點.
2. 增加射出壓力.
3. 改變膠口位置.
4. 增加溢流區,改變塑膠流動方向.
四. 遲滯現象 1.膠口附近較薄處肋缺料 1. 增加厚度.
2. 增加射出速度.
3. 增加模溫.
4. 增加料溫.
5. 增加保持壓力.
6. 改變膠口位置.
7 .增加擾流設計.
貳. 毛邊.溢料
原因狀態解決對策備註
一. 過度充填 1. 毛邊出現在澆口附近. 1. 降低射出速度.(尤其通過澆口時的速度)
2. 毛邊出現在分離面(parting)且已飽和. 1. 降低計量長度.(提高切換到飽壓)
2. 降低射出速度(尤其是切換飽壓前之速度)
3. 減低模溫.
4. 減低料溫.
5. 減低保持壓力.
3. 膠口附近凹陷但又發生毛邊. 1. 降低計量長度.(提高切換到飽壓)
2. 降低射出速度(尤其是切換飽壓前之速度)
3. 減低模溫.
4. 減低料溫.
5. 嘗試以上各對策消除毛邊後延長保持時間.
二. 因流阻太大使模腔內壓(cavaty pressure) 1. 毛邊又短射.(或流路末端凹陷) 1. 增加模溫.
2. 增加料溫
3. 增加射速.
4. 增加肉厚.
5. 改善塑膠料之流動性.
三. 鎖模力(clamping forcc)不足 1. 無過飽和現象. 1. 提高鎖模力.
四. 吻合面間隙太大 1. 特定位置 1. 修復模具.
五. 模板變形 1. 提早切換至飽壓.
2. 減低飽壓.
3. 提高模板強度及剛性.
參. 凹陷.縮水與真空泡
原因狀態解決對策備註
一. 填充量不足 1. 全面性凹陷. 1. 延長計量行程.
2. 檢查螺桿逆止環.
3. 增加射出速度.
4. 增加保持壓力.
5. 增加流道或澆口尺寸.
6. 增加模溫.
7. 增加料溫.
2. 凹陷出現在流路末端或薄的部位. 1. 增加保持壓力(尤其是初期)
2. 提高料筒(cylinder barrel)溫度.
3. 增加模溫.
4. 增加射出速度.
5. 檢查膠口位置(由厚向薄射出)
二. 有效時間不足 1. 凹陷出現在膠口或厚的部位 1. 延長保持時間.
2. 減低模溫.
3. 減低料溫.
4. 減少膠口斷面積.
三. 表面固化太慢 1. 厚位出現凹陷或光澤 1. 減低模溫
註:表層未凝固成堅固之固化層時,當中心收縮時會將表面向內收縮成凹陷,甚至由內向外擴散熱量會將表面層再熔解而生光澤,相反的在厚的部份如果表層足夠堅固則中心部的收縮會形成真空泡. 2. 減低料溫.
3. 塑流通過厚肉區時減速使固化層較厚.
4. 調整肉厚(如肋部減薄,厚薄變緩).
5. 使用低收縮之塑料
6. 添加發泡劑於塑料.
"備註:第1.2.3項會增加真空泡的發生機率"
四. 冷卻時間太短 1.凹陷或真空泡是在開模取出後才發生. 1. 減低模溫.
2. 減低料溫.
3. 增加冷卻時間.
肆. 噴痕
原因狀態解決對策備註
發生在塑膠流動斷面由小急遽變大的位置;當塑膠由小斷面進入大斷面如速度沒有適當降低,則塑膠像噴射般向前進,這些塑膠溫度冷卻後與後來流入之塑膠無法均勻融和而形成外觀之不良. 1. 減低射出速度.
2. 增加模溫.
3. 增加料溫.
4. 變更膠口位置.
5. 增加膠口斷面積.
6. 避免射料方向由上向下.
伍. 結合線
原因狀態解決對策備註
塑膠射出時兩股以上的膠流相遇,壓力與溫度不足,相遇膠流之圓形先端無法融合,而形成表面的溝狀痕跡. 1. 增加射出速度.
2. 增加模溫.
3. 增加料溫.
4. 增加保持壓力.
5. 變更膠口位置.
6. 檢查排氣效果. 陸. 波紋
原因狀態解決對策備註
當膠流進入較冷的模腔,由於冷卻速度快,使得靠近模璧部分之塑膠成固化,這固化層妨礙了後續流動之塑膠貼近模璧;但此固化層受流動壓力拉伸延展,又受到膠流之壓力相互擠壓,相互作用一再重演在成品外觀上流下一成層層之波浪狀. 1. 增加射出速度.
2. 增加射出壓力.
3. 增加模溫.
4. 增加料溫.
5. 避免流道太小
柒. 氣泡
原因狀態解決對策備註
射出時塑膠料包含太多氣體或混合了空氣,則成品內部或接近表面會有空氣之現象. 1. 降低鬆退速度或減小鬆退量.
2. 提高背壓.
3. 檢查塑膠料狀態.
4. 檢查可塑化機構.
5. 檢查計量長度是否太長.
捌. 燒焦
原因狀態解決對策備註
射出進行中因排氣不及,氣體受到絕熱壓縮產生極高溫度而將塑膠料燒黑. 1. 產生於流路末端 1. 減低射出速度.
2. 改善排氣效果.
3. 減低鎖模力.
2. 產生於包封處 1. 調整肉厚.
2. 改變膠口位置.
3. 減低射出速度.
4. 減低鎖模力.
5. 增加排氣點.
玖. 冷卻痕
原因狀態解決對策備註
在射出過程中,於噴嘴的先端或膠口部分產生冷卻,這些冷卻料在被射出時如未被擋在流道系統的冷料井或者是再熔解,則在膠口附近留一長條的流痕. 1. 增加噴嘴孔徑.
2. 增加噴嘴溫度.
3. 減低鬆退量.
4. 檢討模具系統流道的設計.
5. 降低射出到膠口之速度.
拾. 膠口周圍的霧狀
原因狀態解決對策備註
在膠口(尤其為小膠口)周圍高分子配向的凝固層(強度較弱).如在高速的流動場中,受分子鍊被拉開而形成一些小缺孔,很多小缺孔構成膠口周圍的霧狀痕跡. 1. 減低射速度.
2. 增加膠口的斷面積.
3. 改變膠口位置.
4. 增加模溫.
5. 減低料溫.
拾壹. 表層剝落
原因狀態解決對策備註
成品的表面層在塑膠料流動和固化速度不同的情形下,一層一層的堆積所形成,如果因塑膠料含有不均勻的成份或受過高切段力及過熱所破壞則層與層間之熔合就不足而產生剝落. 1. 檢查塑膠料是否含有太水份.
2. 增高模溫.
3. 減低射出速度.
4. 減低料溫.
5.檢查塑膠機的性能及設定條件.
6. 檢查塑膠料之色劑或添加物是否相容.
7.檢查塑膠料之是否混入其它材質.
拾貳. 黑點
原因狀態解決對策備註
1.塑膠料含有雜質或其它不相容物質. 1.檢查塑膠料是否含有雜質.
2. 降低回收料的添加比例.
3. 檢查塑膠料之色劑或添加物是否相容.
2. 塑膠料在製造過程中受到污染. 1. 檢查送料管路及烘料筒.
2. 清潔螺桿及加熱筒.
3. 清潔熱流道及噴嘴.
3. 塑膠料在製造過程中受到破壞. 1. 減低料溫.
2. 減低塑膠料在加熱管內停流時間.
拾參. 焦紋
原因狀態解決對策備註
塑膠料因熱受損分子量會降低或發生熱分解,使成品外觀出現銀色或棕色的紋狀瑕疵,同時也會降低強度. 1. 減低料溫.
2. 減低塑膠料在加熱管內停留時間
3. 減低射出速度.
4. 增加噴嘴孔徑.
拾肆. 濕紋
原因狀態解決對策備註
塑膠料在儲存或加工中,如吸收水份,則在高溫加工時所形成之水氣會受流動推擠到模璧而形成成品表面條狀的痕跡. 1. 檢查塑膠材料的乾燥度.
2. 提高背壓.
3. 檢查模璧表面是否含有水份.
4. 檢查材料之包裝與儲存.
拾伍. 氣痕
原因狀態解決對策備註
在射出過程中,氣體來不及排出被推往表面或在進料後鬆退,吸入空氣而在射出時被推往膠口之附近. 1. 出現在膠口附近. 1. 降低鬆退速度或行程.
2. 使用可閉噴嘴.
2. 出現在其它部分. 1. 減低射出速度
2. 增加被壓.
3.改變膠口位置.
4.設計時避免尖角及凹凸太深之形狀.
拾陸. 光澤與光澤差異
原因狀態解決對策備註
塑膠成型品之表面光澤決定於模具表面加工及射出成形之冷卻速率或收縮差異所產生的表面狀態. 1.模具打光面光澤不足. 1. 模面再打光.
2. 增加射出速度.
3. 增加模溫.
4. 增加料溫.
2. 咬花面光澤不足. 1. 調整咬花面.
2. 減低射出速度.
3. 減低模溫.
4. 減低料溫.
3. 接合線處的光澤差異. 1. 改變膠口位置.
2. 增加射出速度.
3. 增加模溫.
4. 孔部周圍的光澤差異. 1. 改變膠口位置.
2. 調整孔部型狀.
5. 肋部或厚駁差異急變處. 1. 增加保持壓力.
2. 足夠的保持時間.
3. 降低通過問題處之速度.
4. 調整厚薄變化,使其變化趨緩.
6.在頂針或滑塊處光澤差異. 1. 檢查模溫之差異.
2. 避免模腔內壓力過高.
/simple/?t38705.html。