热镀锌线立式连续退火炉炉辊安装调整技术
热镀锌处理线的工艺流程以及相关设备描述

热镀锌处理线的工艺流程以及相关设备描述热镀锌处理线的工艺流程以及相关设备描述随着世界经济的发展,市场对于钢板的热镀锌需求数量日益增多,同时对于钢板的热镀锌质量要求也越来越高,这就对热镀锌处理线的工艺水平要求越来越严格,所以,近些年对于热镀锌钢板的连续退火技术的工艺要求以及相关设备有了明显的改善。
文章针对热镀锌生产线的工艺流程及处理方法,以及连续退火炉相关设备的组成作简要说明。
1、热镀锌连续退火技术发展简析随着世界经济的发展,工业生产水平的日益进步,市场对于钢板防腐性能的要求逐渐提高,钢板防腐已成为工业生产中重要的研究方向,采用带钢表面进行金属镀层的方法防止带钢腐蚀,其金属镀层原料来源广泛,具有较强的成本优势,广泛应用于工业生产中。
当前工业生产中最为普遍的金属镀层方位有电镀法和热镀法。
镀锌板用途广泛,主要应用于环境较为恶劣的户外,所以对镀层的厚度有着较高的要求。
另外,金属镀层相当于带钢表面产生阳极保护,镀层厚度增加将延长钢板使用寿命,此时对镀层均匀性的要求不是很严格,热镀锌产品正好能够满足以上要求。
传统的电镀锌尽管镀层较为均匀,表面没有明显缺陷,同钢板紧密结合,其厚度相当于普通热镀锌厚度的1/5至1/7,但其成本相对较高,市场使用较少。
目前,常见的钢板镀金属方法仍是热镀锌。
从上世纪30年代,波兰人森吉米尔发明的连续热镀锌技术被沿用至今,具有其自身较为独特的工艺方法。
其特点是通过采用直火加热的方法将带钢表面油脂烧掉,并使带钢表面发生氧化,之后在还原气氛中通过此用辐射管间接加热的方式,对带钢进行加热处理,将之前的氧化膜取出,是带钢表面活化,以合适的温度进入锌锅,完成带钢表面的镀锌。
2、生产工艺2.1 工艺流程热镀锌生产工艺流程:冷轧卷→开卷机→五辊矫直机→测厚仪→双层切头剪→半自动窄搭接焊机→清洗段→入口活套→连续退火炉→锌锅→气刀→小锌花或合金化炉→镀后冷却段→镀层测厚仪→水淬槽→热风干燥→光整机→拉矫机→化学处理→热风干燥→出口活套→静电涂油→卷取机。
经验谈:如何安装与调整镀锌线立式连续退火炉炉辊

经验谈:如何安装与调整镀锌线立式连续退火炉炉辊(2006/11/20 13:25)(引用地址:/lyxx/default.asp)目录:公司动态浏览字体:大中小邯钢冷轧厂镀锌线立式连续退火炉与2004年6月开始设备安装,2005年6月28日烘炉检查完毕。
由比利时DREVER公司设计,并负责设备安装监理、调试。
炉辊的安装是炉子安装中最重要、最复杂、要求最高的部分。
炉辊的安装质量,决定了板带在炉内的运行情况。
这就意味着:炉辊的安装质量,决定了镀锌线生产的连续性。
炉子结构和主要参数适合生产CQ、DQ、DDQ、HSS和FH材质的钢板。
包括退火炉和冷却塔。
所配备设备的主要特性有:预热段能够利用加热段排放废气的余热加热钢带,多功能的加热和均热段采用全辐射管加热,喷冷段可以向均衡段提供横向温度均匀的板带,均衡段能够保持和均匀带钢温度,并且在镀锌部分和喷冷段之间提供一个缓冲空间,出口段包括一套热张紧辊,它为进入锌锅的带钢提供高张力以保证带钢通过气刀时的稳定性,锅后冷却段采用空气冷却,终冷段用于降低水淬之前的带钢温度,水冷段包括喷淋系统、水淬槽、挤干辊和干燥器。
炉内有转向辊17根,张力辊2根,张力计辊3根,纠偏辊2套(4根),导向辊4根,电加热器6套。
冷却塔上有挤干辊4根,水淬槽辊1根,导向辊2根。
炉内气体为95﹪氮气与5﹪氢气的混和气体。
炉辊的安装和调整1 确定辊子几何轴线点的步骤主钢结构安装、调整完成后,在辊子所在的每个水平线上,确定出几何轴线点,以确保辊子沿炉子轴线上处在精确位置。
这项工作必须由一名有经验的测量员来承担。
开始工作前,测量员必须作预备报告。
几何轴线用一根在两个支撑臂之间拉紧的钢丝来表示,支撑臂支撑焊接在主钢结构上。
安排这些支撑位置时,测量员会给出明确的说明。
这些支撑不能给炉子其它部件的安装带来阻碍。
支撑臂和钢丝将置于操作侧。
钢丝的位置通过每根辊子的轴心,并距每根棍子轴承座100mm。
一旦几何中心线确定后,测量员将提交一份最终报告,详细描述辊子及其它与他布置的中心线相关的零部件的位置。
现代热镀锌机组连续退火技术

张摘要随着社会的发展进步,对热镀锌钢板的要求越来越高。
因此近年来热镀锌钢板的连续退火技术发展变化很大,本文详细介绍了热镀锌连续退火工艺的发展变化、现代热镀锌连退火设备及其控制,对现代热镀锌连续退火技术作了一个全面的阐述。
关键词现代热镀锌连续退火技术CONTINUOUS ANNEALING TECHNOLOGY FORMODERN HOT GALVANIZING LINEZhang Hong(Wuhan Iron & Steel Design and Research Institute)Abstract Demands for hot galvanized steel sheets are ever increasing with the progress of the society, therefore the technology in this field has seen an amazing advance. The present paper reviews and discusses in detail the changes and progress in the continuous annealing technology for the hot galvanizing line as well as its related control and equipments.Keywords modern hot galvanizing continuous annealing technology1 热镀锌机组连续退火技术的发展热镀锌板主要用于建筑、家电,汽车等行业,以前在数量上建筑业是第一大用户,随着人们对汽车质量的要求越来越高,热镀锌板开始大量用于汽车面板、内板、底盖等,而且使用比例越来越大。
目前发达国家用于汽车行业的热镀锌板占其总产量的40%以上。
汽车用板对表面质量,焊接性,着漆性,粘附性有严格要求,同时由于使用部位的不同,对原板的深冲性能,强度也有更高的要求。
介绍连续热镀锌线的退火炉工艺以及节能技术
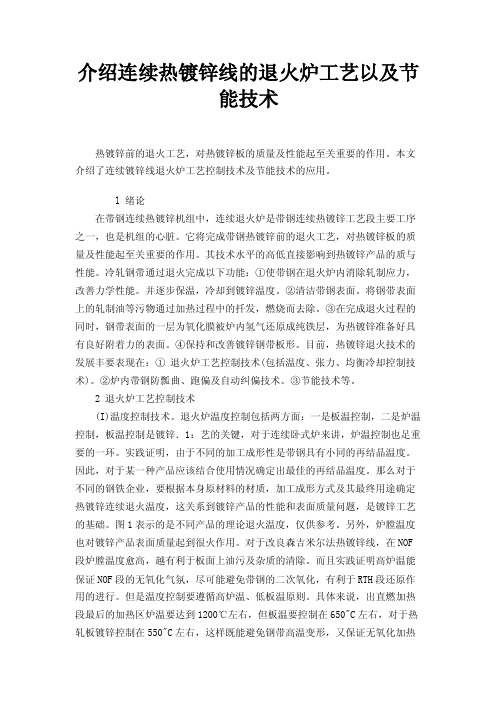
介绍连续热镀锌线的退火炉工艺以及节能技术热镀锌前的退火工艺,对热镀锌板的质量及性能起至关重要的作用。
本文介绍了连续镀锌线退火炉工艺控制技术及节能技术的应用。
l 绪论在带钢连续热镀锌机组中,连续退火炉是带钢连续热镀锌工艺段主要工序之一,也是机组的心脏。
它将完成带钢热镀锌前的退火工艺,对热镀锌板的质量及性能起至关重要的作用。
其技术水平的高低直接影响到热镀锌产品的质与性能。
冷轧钢带通过退火完成以下功能:①使带钢在退火炉内消除轧制应力,改善力学性能。
并逐步保温,冷却到镀锌温度。
②清洁带钢表面。
将钢带表面上的轧制油等污物通过加热过程中的扦发,燃烧而去除。
③在完成退火过程的同时,钢带表面的一层为氧化膜被炉内氢气还原成纯铁层,为热镀锌准备好具有良好附着力的表面。
④保持和改善镀锌钢带板形。
目前,热镀锌退火技术的发展丰要表现在:①退火炉工艺控制技术(包括温度、张力、均衡冷却控制技术)。
②炉内带钢防瓢曲、跑偏及自动纠偏技术。
③节能技术等。
2 退火炉工艺控制技术(I)温度控制技术。
退火炉温度控制包括两方面:一是板温控制,二是炉温控制,板温控制是镀锌.1:艺的关键,对于连续卧式炉来讲,炉温控制也足重要的一环。
实践证明,由于不同的加工成形性是带钢具有小同的再结晶温度。
因此,对于某一种产品应该结合使用情况确定出最佳的再结晶温度。
那么对于不同的钢铁企业,要根据本身原材料的材质,加工成形方式及其最终用途确定热镀锌连续退火温度,这关系到镀锌产品的性能和表面质量问题,是镀锌工艺的基础。
图1表示的是不同产品的理论退火温度,仅供参考。
另外,炉膛温度也对镀锌产品表面质量起到很火作用。
对于改良森吉米尔法热镀锌线,在NOF 段炉膛温度愈高,越有利于板面上油污及杂质的清除。
而且实践证明高炉温能保证NOF段的无氧化气氛,尽可能避免带钢的二次氧化,有利于RTH段还原作用的进行。
但是温度控制要遵循高炉温、低板温原则。
具体来说,出直燃加热段最后的加热区炉温要达到1200℃左右,但板温要控制在650"C左右,对于热轧板镀锌控制在550"C左右,这样既能避免钢带高温变形,又保证无氧化加热气氛。
连续镀锌线退火炉炉膛温度控制
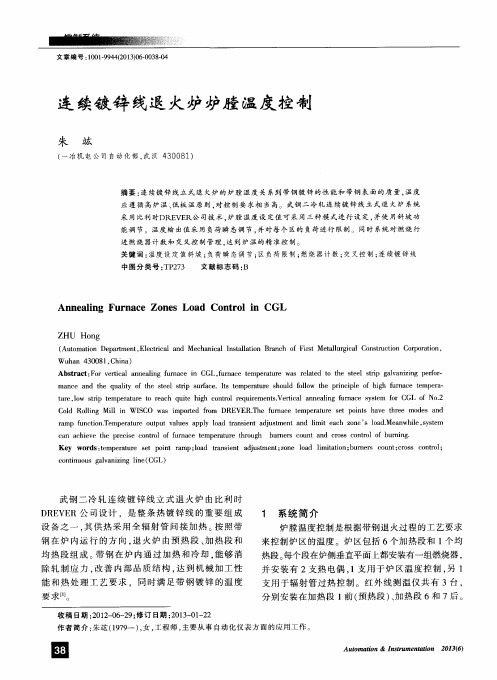
Ke y w o r d s : t e mp e r a t u r e s e t p o i n t r a m p ; l o a d t r a n s i e n t a d j u s t m e n t ; z o n e l o a d l i m i t a t i o n ; b u ne r r s c o u n t ; c r o s s c o n t r o l ;
进 燃 烧 器计 数 和 交 叉控 制 管 理 . 达 到 炉 温 的精 准控 制 。
关键词 : 温 度 设 定值 斜坡 ; 负 荷 瞬 态调 节 ; 区负荷 限 制 ; 燃烧器计数; 交叉控制; 连续镀锌线
中 图分 类 号 : T P 2 7 3 文 献标 志码 : B
An ne a l i n g Fur na c e Zo ne s Lo a d Co nt r o l i n CGL
文章 编号 : 1 0 0 1 — 9 9 4 4 ( 2 0 1 3 ) 0 6 - 0 0 3 8 — 0 4
连 续镀 锌 线退火 炉炉膛 温度控制
朱 骇
( 一冶 机 电公 司 自动 化 部 , 武汉 4 3 0 0 8 1 )
摘要 : 连 续 镀 锌 线 立 式 退 火炉 的炉 膛 温度 关 系到 带钢 镀 锌 的 性 能 和 带 钢 表 面 的 质 量 , 温度
c a n a c hi e v e t h e pr e c i s e c o nt r o l o f f u r n a c e t e mpe r a t u r e t h r o u g h b ur ne r s c o u n t a n d c r o s s c o n t r o l o f b u ni r n g.
连续退火机组退火炉内的纠偏技术应用

刘 洪 张 华 连 退 机 退 炉 的 偏 术 爱 续 火组 火 内纠技 应
即使带 钢 在转 向辊 上 无 侧 向滑 移 , 遇 到带 在
:: :
张 力 , 使带 钢在 辊面 上 向张力 小 的右侧滑 , 促 带钢在 辊 面 上 的右 移 量 更 加增 大 。不过 , 炉 因
・
l 2・
梅 山科技
2 1 年第 3期 01
连 续 退火 机 组 退 火 炉 内的 纠 偏技 术 应 用
刘 洪 张 爱华 20 3 ) 10 9
( 山钢 铁 公 司冷轧 厂 南京 梅
摘
要: 主要 针 对连 续退 火机 组退 火炉 内带钢 跑偏 的原 因进 行 了分析 , 并介 绍 了退 火炉 中
( o o igPa t f i a o C l R ln ln o s nI n& Sel o , aj g 1 0 9 d l Me h r te C . N ni 0 3 ) n 2
Ke r y wo ds: e ito se rn ol a ne lng f r a e d v a in;t e i g r l ; n a i u n c
钢镰刀弯时也会 出现带钢偏斜进入转 辊
匕 下转向辊相距较远 , 向纠偏辊摆角又不大 , 转 偏
辊偏摆而使带钢在辊面上产生太大滑移量 , 通常
可 以只考 虑螺旋 纠偏 作用 。
e
羹 窑 妻 篓 霎霎
前 力F 张 (ห้องสมุดไป่ตู้ a
篡灵 幂 摆 对 钢 处 力 响 小,般 会因! 差 后 带 各 张 影 较 一 不 窒 羹
冷轧 板 带产 品是 广泛应 用 于 国 民经济各 部 门
的重 要原 材料 , 几 年来 , 近 随着 汽车 板 、 电 、 装 家 包
立式退火炉炉辊安装调整技术探讨
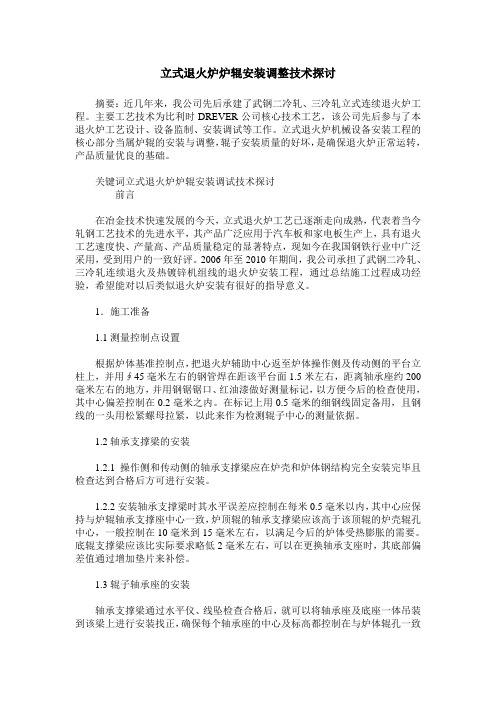
立式退火炉炉辊安装调整技术探讨摘要:近几年来,我公司先后承建了武钢二冷轧、三冷轧立式连续退火炉工程。
主要工艺技术为比利时DREVER公司核心技术工艺,该公司先后参与了本退火炉工艺设计、设备监制、安装调试等工作。
立式退火炉机械设备安装工程的核心部分当属炉辊的安装与调整,辊子安装质量的好坏,是确保退火炉正常运转,产品质量优良的基础。
关键词立式退火炉炉辊安装调试技术探讨前言在冶金技术快速发展的今天,立式退火炉工艺已逐渐走向成熟,代表着当今轧钢工艺技术的先进水平,其产品广泛应用于汽车板和家电板生产上,具有退火工艺速度快、产量高、产品质量稳定的显著特点,现如今在我国钢铁行业中广泛采用,受到用户的一致好评。
2006年至2010年期间,我公司承担了武钢二冷轧、三冷轧连续退火及热镀锌机组线的退火炉安装工程,通过总结施工过程成功经验,希望能对以后类似退火炉安装有很好的指导意义。
1.施工准备1.1测量控制点设置根据炉体基准控制点,把退火炉辅助中心返至炉体操作侧及传动侧的平台立柱上,并用∮45毫米左右的钢管焊在距该平台面1.5米左右,距离轴承座约200毫米左右的地方,并用钢锯锯口、红油漆做好测量标记,以方便今后的检查使用,其中心偏差控制在0.2毫米之内。
在标记上用0.5毫米的细钢线固定备用,且钢线的一头用松紧螺母拉紧,以此来作为检测辊子中心的测量依据。
1.2轴承支撑梁的安装1.2.1操作侧和传动侧的轴承支撑梁应在炉壳和炉体钢结构完全安装完毕且检查达到合格后方可进行安装。
1.2.2安装轴承支撑梁时其水平误差应控制在每米0.5毫米以内,其中心应保持与炉辊轴承支撑座中心一致,炉顶辊的轴承支撑梁应该高于该顶辊的炉壳辊孔中心,一般控制在10毫米到15毫米左右,以满足今后的炉体受热膨胀的需要。
底辊支撑梁应该比实际要求略低2毫米左右,可以在更换轴承支座时,其底部偏差值通过增加垫片来补偿。
1.3辊子轴承座的安装轴承支撑梁通过水平仪、线坠检查合格后,就可以将轴承座及底座一体吊装到该梁上进行安装找正,确保每个轴承座的中心及标高都控制在与炉体辊孔一致的位置上,且保持在1毫米以内的误差,其垂直度满足图纸要求,而后用500牛米的力矩锁紧底座螺母,并在轴承支撑梁及底板上做好中心标记。
连续退火炉的施工要点

浅谈连续退火炉的施工要点摘要:冷轧立式连续退火炉的工艺比较复杂,施工过程中需要特别注意的问题较多。
本文从立式连续退火炉施工过程中的工艺钢结构、炉壳、辐射管及炉辊设备安装和炉体气密性试验等四个方面,浅要分析了连续退火炉施工过程中的要点。
关键词:退火炉;炉体;炉壳;施工要点连续退火机组主要用于轧后带钢的再结晶退火,以消除冷加工硬化,产品主要用于建筑、家电、汽车等行业。
我国第一条连续退火机组是宝钢在1989年从新日铁引入的2030mmcapl线。
连续退火机组工艺线上的退火炉分为立式炉和卧式炉两种。
相比于结构简单的卧式炉,立式炉的结构复杂得多,施工难度更大,其施工要点也就更值得研究总结。
连续退火机组立式炉的设备一般由炉体设备、炉内设备、炉外设备三部分组成。
从整体来说,立式连续退火炉设备安装的施工要点主要体现在炉子工艺钢结构、炉壳、辐射管、炉辊和炉子气密性试验上。
笔者就宝钢1750mmcal为例对这几个方面的施工要点进行分析与探讨。
从工艺上来说,退火一般分为9段:分别为喷气预热段、辐射管加热段、均热段、缓冷段、闪冷段、过时效段1、过时效段2、最终冷却段及水淬塔段。
生产时连续退火炉段工艺速度可达420m/min。
一、炉子工艺钢结构的施工要点因连续退火炉的工艺特点,炉子工艺钢结构及其平台的安装与炉壳安装、风机、热交换器、管道施工等必须穿插进行,一层结构一层设备,整个退火炉的安装期间呈现高空立体交叉作业状态。
工艺钢结构的安装要分别从入口和出口向炉中安装,这样可以把安装过程中的误差在炉中消除,能够更好地保证安装精度。
为了减少高空作业和确保施工安全,一般把炉体两侧的工艺钢结构柱子及梁预拼装成“井”字形框架。
再进行整体吊装作业。
吊装作业主要利用厂房内的桥式起重机进行,由于主厂房内桥式起重机数量有限,退火炉施工又为多点作业,行车使用频繁,需另配置数台汽车吊配合钢结构拼装作业。
作为整个退火炉工艺钢结构安装的基础,钢结构下段立柱及横梁的各项安装精度都应严格按设计要求和规范来进行,然后进行地脚螺栓的一次灌浆,待强度达到后进行立柱的精找和下部横梁的连接,使底层结构形成刚性框架,最后再进行柱、梁的找正找平。
- 1、下载文档前请自行甄别文档内容的完整性,平台不提供额外的编辑、内容补充、找答案等附加服务。
- 2、"仅部分预览"的文档,不可在线预览部分如存在完整性等问题,可反馈申请退款(可完整预览的文档不适用该条件!)。
- 3、如文档侵犯您的权益,请联系客服反馈,我们会尽快为您处理(人工客服工作时间:9:00-18:30)。
热镀锌线立式连续退火炉炉辊安装调整技术作者:包佳侯剑谷媛媛杨春福
来源:《中国科技纵横》2014年第09期
【摘要】热镀锌立式连续退火炉炉辊安装主要包括轴承支撑梁,炉辊轴承座,炉辊辊盖,膨胀节,炉辊,炉辊轴承等几部分的安装。
炉辊的安装是炉子安装中最重要,最复杂,要求最高的部分。
炉辊安装结构复杂,小件散件多,设备布局紧凑,安装精度要求高。
其安装质量决定了钢带在炉内的运行情况。
这就意味着炉辊的安装质量,决定了镀锌线生产的连续性。
本文详细阐述了扬子江1420冷轧工程(即沙钢)热镀锌线立式连续退火炉炉辊安装调整的方法,过程中的要点,及应该注意的事项。
【关键词】热镀锌退火炉炉辊
1 引言
中国二十冶施工的连续退火炉是世界上安装质量优良的炉子,施工进度相当快,有着多年丰富的经验,达到了国内外先进水平。
曾在国内外多个钢厂完成过大型冷轧连续退火机组的安装及冷轧连续退火炉的改造工作,进行过早期和换代后两种不同类型连续退火炉的安装,编制过安装工法和检查标准。
在此,我们对热镀锌线立式连续退火炉的炉辊安装及调整技术进行总结,希望其能对此后类似的工程施工有所帮助。
2 设备概况
炉辊安装是整个退火炉安装过程中至关重要的部分,其安装质量决定了能否保证镀锌线的连续生产,通常是炉体最精密的安装工作,也是气密性、炉辊单体试车的紧前工作,影响到退火炉的烘炉。
炉辊调整的精度也直接影响到炉体带钢的纠偏调整,对后期炉体内带钢的顺直通过影响重大。
因此炉辊调整是否精确,调整速度快慢,将直接影响到整个热镀锌线的总工期。
炉辊设备主要由辊子,传动装置及辊子附件组成,辊子附件包括轴承座,轴承,膨胀节等。
3 炉辊的安装及调整
3.1 示意图(图1)
3.2 安装前提条件
(1)炉区主体钢结构安装完成;(2)确定所有螺栓终紧并达到规定扭矩值;(3)炉壳安装、焊接完成,并通过现场外方专家及监理验收检查并确认合格。
(4)炉区结构安装完成,验收后,在钢结构平台上设置炉辊安装、调整、验收用的辅助点及参考线(确认所有结构
螺栓已经终紧,并达到螺栓扭矩要求;(5)技术说明:底(顶)层参考线标高比炉辊标高高200mm;两侧参考线距炉体中心各为1970mm。
3.3 安装驱动侧、操作侧轴承支撑梁
(1)根据操作侧炉辊窗口中心标高进行调整和验收;(2)验收需要测量的内容及允许误差值如下:1)检查内容:炉辊中心到轴承梁距离(操作侧),技术要求值为±2mm;2)检查内容:两侧间距(驱动侧),技术要求值为±2mm;3)检查内容:横梁到参考线水平距离(操作侧),技术要求值为±2mm;4)检查内容:横梁到参考线水平距离(驱动侧),技术要求值为±2mm。
3.4 对驱动侧炉辊辊盖进行调整定位
(1)将驱动侧辊盖取下,先进行保温工作;(2)根据操作侧炉辊窗口中心标高进行定位、调整、验收。
验收后将炉辊盖与炉壳接触处的角钢外侧进行焊接。
(3)验收需要测量的内容及允许误差值如下:1)检查内容:炉辊盖中心标高(驱动侧),技术要求值为±2mm;2)检查内容:炉辊盖中心标高(操作侧),技术要求值为±2mm;3)检查内容:炉辊盖水平距离(驱动侧),技术要求值为±2mm;4)检查内容:炉辊盖水平距离(操作侧),技术要求值为±2mm。
3.5 安装驱动侧炉辊轴承座
(1)对轴承座的标高、垂直度和与辅助线的平行度进行调整、验收。
(2)验收需要测量的内容及允许误差值如下:1)检查内容:轴承座中心标高(驱动侧),技术要求值为±0~-
1mm;2)检查内容:轴承座中心标高(操作侧),技术要求值为±0~+2mm;3)检查内容:轴承座垂直度(驱动侧),技术要求值为±1mm/m;4)检查内容:轴承座垂直度(操作侧),技术要求值为±1mm/m;5)检查内容:轴承座平行度(驱动侧),技术要求值为
±1mm/m;6)检查内容:轴承座平行度(操作侧),技术要求值为±0.5mm/m。
3.6 安装驱动侧炉辊膨胀节
(1)安装顶部驱动侧膨胀节时,必须根据图纸,将轴承座侧标高比炉壳侧的标高调整高出+12mm,并保证辊盖的垂直度。
(2)将安装完膨胀节的轴承座进行调整、验收,完成后将炉辊盖角钢的另一侧进行焊接。
3.7 预装操作侧炉辊辊盖
(1)安装操作侧炉辊盖时,如果螺栓孔全部合适,仅安装角上的4个螺栓即可。
(2)调整辊盖标高及垂直度。
验收后将炉辊盖与炉壳接触处的角钢外侧进行焊接。
(3)焊接后,将
角钢外侧点焊处用磨光机将临时焊点磨开,取下,进行保温工作。
(4)保温后重新安装至原位。
(5)验收表格:与驱动侧验收表格相同。
3.8 预装操作侧轴承座
(1)对轴承座的标高、垂直度、与炉体轧制线平行度进行调整、验收;(2)验收后,将定位块与支撑梁连接处焊接3点,予以定位,便于再次安装;(3)在辊盖上、轴承座上,进行编号,以便再次安装时进行对号入座;(4)取下操作侧轴承座;(5)验收表格:同驱动侧轴承座验收表格相同。
3.9 安装炉辊
用外方提供的专用吊装工具将炉辊从操作侧安装至炉内。
3.10 安装操作侧膨胀节、轴承座、轴承
(1)技术说明:1)先将轴承座复位、调整;2)将膨胀节两侧螺栓拧紧;3)安装轴承、调整轴承间隙;4)测量轴承到轴套外侧、炉辊端部几何尺寸;5)安装轴承锁紧螺母;6)对调整后的轴承间隙及几何尺寸进行验收;7)安装炉辊外部端盖;8)验收后,将炉辊盖角钢外部进行焊接。
(2)验收图(图2):
(3)验收需要测量的内容及允许误差值如下:1)检查内容:a值(驱动侧),技术要求值为±1mm;2)检查内容:轴承间隙(驱动侧),技术要求值为0.1~0.15mm;3)检查内容:b值(驱动侧),技术要求值为±2mm;4)检查内容:c值(操作侧),技术要求值为
±5mm;5)检查内容:轴承间隙(操作侧),技术要求值为0.1~0.15mm;6)检查内容:E 值(出口)(操作侧),技术要求值为0~0.15mm;7)检查内容:D值(入口)(操作侧),技术要求值为0~0.15mm;8)检查内容:A值(上侧)(操作侧),技术要求值为0~0.15mm;9)检查内容:B值(下侧)(操作侧),技术要求值为0~0.15mm。
2.11 安装炉辊传动装置
(1)技术要求:安装、调整驱动侧传动装置,调整电机、联轴器、炉辊之间的同心度。
(2)验收图(图3):
(3)验收需要测量的内容及允许误差值如下:1)检查内容:法兰间距(L),技术要求值为±1mm;2)检查内容:同心度,技术要求值为0.2mm。
3 设备安装和调整过程中的注意事项
(1)注意炉体中心线的复测,因为炉体结构节点主要由螺栓连接,最终完成螺栓的紧固后,应重新复测炉体中心线和标高点。
(2)炉辊轴承装配完毕后,需要将轴承的锁紧螺母用专用工具紧固完毕后,方可进行炉辊验收。
紧固数据及工具应有炉辊设计单位提供。
(3)炉辊的验收工作必须一步一步进行,每步验收完毕后,需要验收方确定数据后,再进行下步验收,避免发生返工工作。
参考文献:
[1]工程测量规范(GB50026-2007).
[2]机械设备安装工程施工及验收通用规范(GB50231-2009).。