SMC片状模压成型工艺
smc模压成型工艺流程

SMC模压成型工艺流程SMC模压成型是一种常见的复合材料成型工艺,被广泛应用于汽车、航天、建筑等领域。
SMC(Sheet Molding Compound)是一种预浸有树脂的增强复合材料,主要由玻璃纤维、石墨、填料和热固性树脂等组成。
在SMC模压成型过程中,首先将预制好的SMC 预浸料加热软化,然后通过模具形成所需的零部件形状,最终在加热和压力的作用下固化成型,达到产品设计要求。
以下是SMC模压成型的工艺流程。
SMC模压成型工艺流程1. 准备工作在SMC模压成型之前,需要准备好所需的模具、预浸SMC料、加热设备以及压力设备等。
确保所有设备运行正常,符合操作规范。
2. 加热预浸料将预制的SMC料放入加热设备中,经过加热软化,使树脂充分熔化,增强纤维得到活化,便于后续成型。
3. 模具装配将加热后的SMC料放入模具中。
模具需要根据所需产品的设计图纸来选择,并确保模具表面干净平整,涂抹模具脱模剂以防粘连。
4. 模压成型开始进行模压成型工艺,将已经装配好的SMC料模具置于压力设备中,通过加压使SMC料充分填充模具腔体,并且确保均匀分布。
5. 施加压力在模具内加入适当的压力,使SMC料在热固化过程中得到充分压实,以确保产品密度和强度。
6. 加热固化通过加热设备对模具中的SMC料施加恒定的温度,使树脂充分固化,增强纤维和填料得到固定,从而形成产品的稳定结构。
7. 冷却脱模待SMC料在模具中充分固化后,关闭加热设备,待产品冷却至室温。
然后打开模具,取出成型产品,进行后续的修整和表面处理。
8. 检验和包装对成型的产品进行外观检验、尺寸检测以及性能测试,确保产品符合设计要求。
最后对产品进行包装,以防止在运输和储存过程中受到损坏。
以上就是SMC模压成型的工艺流程,通过严谨的操作和控制,可以生产出高质量的复合材料制品,满足各行业对材料性能和外观要求的不断提升。
SMC片状模压成型工艺

18
填料
z 填料按其化学成分可分为四类:氧化硅及硅酸盐类(石棉、 滑石粉、瓷土、氧化硅、硅藻土等);碳酸盐类(碳酸钙);硫 酸盐类(硫酸钡、硫酸钙等);氢氧化物类(氢氧化铝)。
z 多数情况下填料用量占SMC配方总量的1/3以上。
CaCO3
遮盖性好,改善制品 表面性能。
类型 I II
性能 颗粒尺寸/μm 吸油值
19
SMC模塑料常用引发剂的特性
性能
状态
70℃
半衰期,/h
90 ℃ 110 ℃
130 ℃
150 ℃
固化温度,℃
用量,%
贮存期,室温
BPO 糊状 1.4 1.2 0.13
/ / 107~149 2 1周
引发剂 TBP 液体 / 7 6 0.7 /
121-149 1
2月
DCP 粉未
/ / 2.3 2.3 0.26 125~149 2 >3月
29
内脱模剂
对于SMC,粘模是一个严重的问题,因此须在配方中加 入内脱模剂。它们通常为长链脂肪酸及其盐类,受热熔化并 作为第二相流到模具表面、从而阻止了不饱和聚酯树脂与金 属模具表面发生亲合作用。所选用脱模剂的熔点低于固化温 度,以保证其在树脂固化前已熔化。其加入量一般为0.5 %~2%。
常用的内脱模剂: 硬脂酸 硬酯酸锌 硬酯酸钙 硬酯酸镁
加热固化
膨胀
降温脱模
收缩
收缩
极小收缩
消除了体积收缩引起的内应力
产生微分离
21
UP固化过程中的体积变化
热膨胀
热收缩 固化结束(141℃)
固化收缩和热收 缩(141℃)
冷却 初期体积
树脂膨胀2.8% 树脂收缩7.1%
SMC片状模压料生产工艺

SMC片状模压料生产工艺
1、SMC片状模压料的原料准备
2、SMC片状模压料的混合加工
混合系统是SMC片料生产的重要环节,一般选用混合机作为混合系统的核心设备,除了混合各原料外,还要保证混合均匀,减少可能存在的沉淀物,以确保SMC片料的质量。
3、SMC片状模压料的挤出加工
挤出机是SMC片料的重要机械设备,挤出机具有多种功能,既有混合物加热/冷却,又能将混合物挤出成片状的SMC片料,挤出机的功能决定着SMC片料质量的高低。
4、SMC片状模压料的烘干加工
烘干是SMC片料加工的重要一环,烘干的作用是使SMC片料质量更稳定,提高其制品的稳定性。
一般采用滚筒烘干机烘干,其烘干温度和时间等因素均与SMC片料质量息息相关。
二、SMC。
SMC模压成型工艺过程
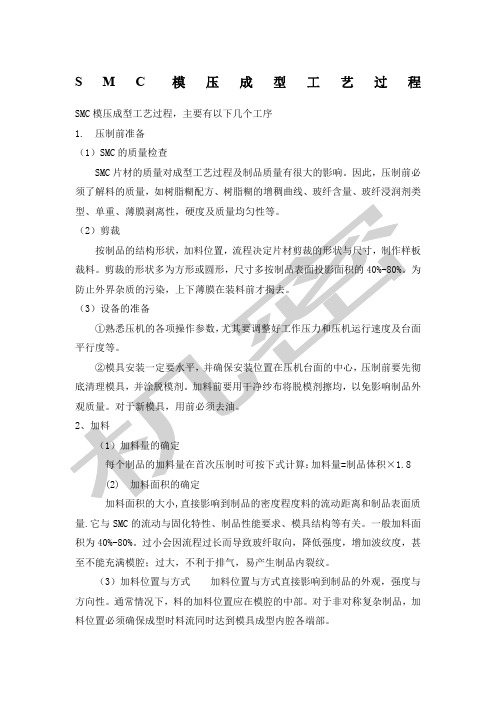
S M C模压成型工艺过程SMC模压成型工艺过程,主要有以下几个工序1. 压制前准备(1)SMC的质量检查SMC片材的质量对成型工艺过程及制品质量有很大的影响。
因此,压制前必须了解料的质量,如树脂糊配方、树脂糊的增稠曲线、玻纤含量、玻纤浸润剂类量.它与SMC的流动与固化特性、制品性能要求、模具结构等有关。
一般加料面积为40%-80%。
过小会因流程过长而导致玻纤取向,降低强度,增加波纹度,甚至不能充满模腔;过大,不利于排气,易产生制品内裂纹。
(3)加料位置与方式加料位置与方式直接影响到制品的外观,强度与方向性。
通常情况下,料的加料位置应在模腔的中部。
对于非对称复杂制品,加料位置必须确保成型时料流同时达到模具成型内腔各端部。
加料方式必须有利于排气。
多层片材叠合时,最好将料块按上小下大呈宝塔形叠置。
另外,料块尽量不要分开加,否则会产生空气裹集和熔接区,导致制品强度下降。
(4)其他在加料前,为增加片材的流动性,可采用100℃或120℃下预热操作。
这一点对成型深拉形制品尤其有利。
3、成型并。
SMC增稠程度越高,所需成型压力也越大。
成型压力的大小与模具结构也有关系。
垂直分型结构模具所需的成型压力低于水平分型结构模具。
配合间隙较小的模具比间隙较大的模具需较高压力。
外观性能和平滑度要求高的制品,在成型时需较高的成型压力。
总之,成型压力的确定应考虑多方面因素。
一般来说,SMC成型压力在3-7Mpa之间。
(3)固化时间SMC在成型温度下的固化时间(也叫保温时间)与它的性质及固化体系、成型温度、制品厚度和颜色等因素有关。
固化时间一般按40s/mm计算。
对3mm以上厚制品,有人认为每增加4mm,固化时间增加1min。
4、压机操作加计理方便;③操作环境清洁、卫生,改善了劳动条件;④流动性好,可成型异形制品;⑤模压工艺对温度和压力要求不高,可变范围大,可大幅度降低设备和模具费用;⑥纤维长度40~50mm,质量均匀性好,适宜于压制截面变化不大的大型薄壁制品;⑦所得制品表面光洁度高,采用低收缩添加剂后,表面质量更为理想;⑧生产效率高,成型周期短,易于实现全自动机械化操作,生产成本相对较低。
SMC模压成型工艺过程
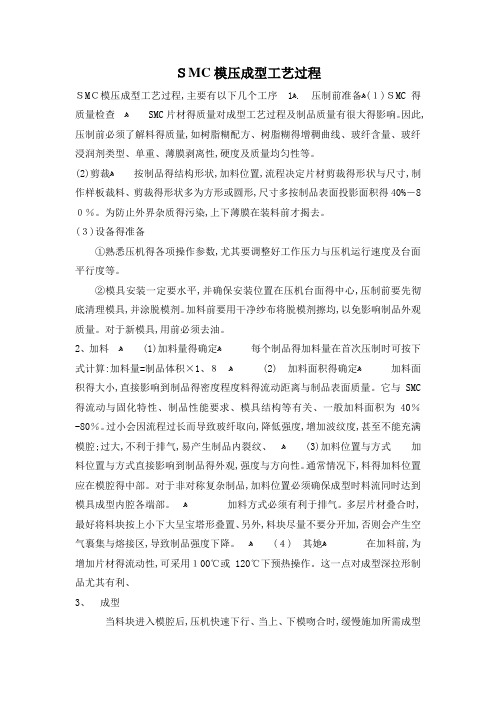
SMC模压成型工艺过程SMC模压成型工艺过程,主要有以下几个工序ﻫ1. 压制前准备ﻫ(1)SMC得质量检查ﻫSMC片材得质量对成型工艺过程及制品质量有很大得影响。
因此,压制前必须了解料得质量,如树脂糊配方、树脂糊得增稠曲线、玻纤含量、玻纤浸润剂类型、单重、薄膜剥离性,硬度及质量均匀性等。
(2)剪裁ﻫ按制品得结构形状,加料位置,流程决定片材剪裁得形状与尺寸,制作样板裁料、剪裁得形状多为方形或圆形,尺寸多按制品表面投影面积得40%-80%。
为防止外界杂质得污染,上下薄膜在装料前才揭去。
(3)设备得准备①熟悉压机得各项操作参数,尤其要调整好工作压力与压机运行速度及台面平行度等。
②模具安装一定要水平,并确保安装位置在压机台面得中心,压制前要先彻底清理模具,并涂脱模剂。
加料前要用干净纱布将脱模剂擦均,以免影响制品外观质量。
对于新模具,用前必须去油。
2、加料ﻫ(1)加料量得确定ﻫ每个制品得加料量在首次压制时可按下式计算:加料量=制品体积×1、8ﻫ(2) 加料面积得确定ﻫ加料面积得大小,直接影响到制品得密度程度料得流动距离与制品表面质量。
它与SMC 得流动与固化特性、制品性能要求、模具结构等有关、一般加料面积为40%-80%。
过小会因流程过长而导致玻纤取向,降低强度,增加波纹度,甚至不能充满模腔;过大,不利于排气,易产生制品内裂纹、ﻫ(3)加料位置与方式加料位置与方式直接影响到制品得外观,强度与方向性。
通常情况下,料得加料位置应在模腔得中部。
对于非对称复杂制品,加料位置必须确保成型时料流同时达到模具成型内腔各端部。
ﻫ加料方式必须有利于排气。
多层片材叠合时,最好将料块按上小下大呈宝塔形叠置、另外,料块尽量不要分开加,否则会产生空气裹集与熔接区,导致制品强度下降。
ﻫ(4) 其她ﻫ在加料前,为增加片材得流动性,可采用100℃或120℃下预热操作。
这一点对成型深拉形制品尤其有利、3、成型当料块进入模腔后,压机快速下行、当上、下模吻合时,缓慢施加所需成型压力,经过一定得固化制度后,制品成型结束。
SMC模压成型工艺介绍

共聚物
PVAc
0.25
线
收
缩 率
0.20
0.16
低收缩剂的种类、用量与线收缩 率的关系
1
2 1-氯醋共聚物;2-聚苯乙烯; 3-聚乙烯
3
0.01
15 20 25 30 添加量(重量份)
.29.
SMC的组分及其性能
无机填料
属惰性物质 作用: 1、降低材料成本;
2、改善制品性能。 缺点: 随填料加入量增加,树脂糊粘度
若缩短贮存SMC的启用 0
期,可将其在45℃烘房内进行
0
1
23 45
时间(h)
稠化,若延长贮存期,应在较
低的温度(小于25℃)下存放。
树脂增稠与温度的关系
.20.
SMC的组分及其性能
(4)增稠机理
两个阶段 第一阶段
金属氧化物或氢氧化物与聚酯端基- COOH进行酸碱反应,生成碱式盐。
O
C OH + MO
使用时除去薄膜,按尺寸裁剪,然后进行模压成型。
.2.
SMC的特点与种类
SMC具有的特点:
1) 制品的重现性好, SMC的制造不易受操作者和外界条 件的影响 2) 加工制品操作处理方便,不粘手 3) 作业环境清洁,大大改善了劳卫环境 4) 片材质量均匀,适宜压制截面变化不大的大型薄壁制品 5) 树脂和玻璃纤维可以流动,可成型带肋条和凸部的制品 6) 成型的制品表面光洁度高 7) 生产效率高、成型周期短、成本低
细度: 粒径要求小于120μm(120目)。 88μm(170目,水泥细度) 60μm(200目)
颗粒太粗容易分离沉淀;太细、吸油率高,树脂用量大。
油吸附量: 填料被亚麻仁油润湿的质量百分比。
SMC模压成型工艺过程
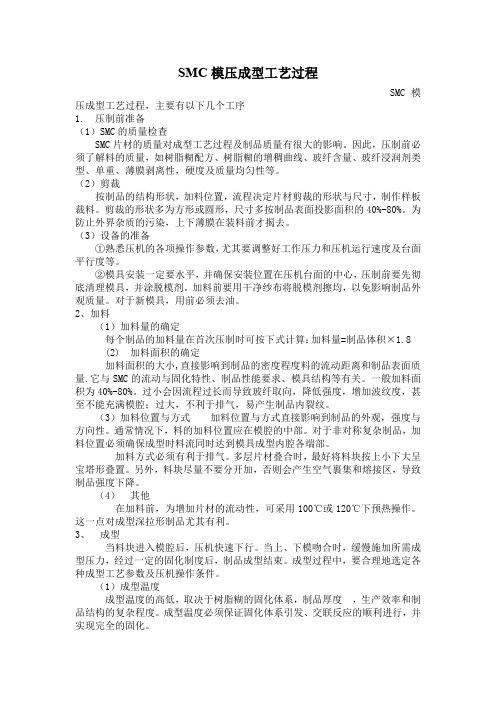
SMC模压成型工艺过程SMC模压成型工艺过程,主要有以下几个工序1. 压制前准备(1)SMC的质量检查SMC片材的质量对成型工艺过程及制品质量有很大的影响。
因此,压制前必须了解料的质量,如树脂糊配方、树脂糊的增稠曲线、玻纤含量、玻纤浸润剂类型、单重、薄膜剥离性,硬度及质量均匀性等。
(2)剪裁按制品的结构形状,加料位置,流程决定片材剪裁的形状与尺寸,制作样板裁料。
剪裁的形状多为方形或圆形,尺寸多按制品表面投影面积的40%-80%。
为防止外界杂质的污染,上下薄膜在装料前才揭去。
(3)设备的准备①熟悉压机的各项操作参数,尤其要调整好工作压力和压机运行速度及台面平行度等。
②模具安装一定要水平,并确保安装位置在压机台面的中心,压制前要先彻底清理模具,并涂脱模剂。
加料前要用干净纱布将脱模剂擦均,以免影响制品外观质量。
对于新模具,用前必须去油。
2、加料(1)加料量的确定每个制品的加料量在首次压制时可按下式计算:加料量=制品体积×1.8(2) 加料面积的确定加料面积的大小,直接影响到制品的密度程度料的流动距离和制品表面质量.它与SMC的流动与固化特性、制品性能要求、模具结构等有关。
一般加料面积为40%-80%。
过小会因流程过长而导致玻纤取向,降低强度,增加波纹度,甚至不能充满模腔;过大,不利于排气,易产生制品内裂纹。
(3)加料位置与方式加料位置与方式直接影响到制品的外观,强度与方向性。
通常情况下,料的加料位置应在模腔的中部。
对于非对称复杂制品,加料位置必须确保成型时料流同时达到模具成型内腔各端部。
加料方式必须有利于排气。
多层片材叠合时,最好将料块按上小下大呈宝塔形叠置。
另外,料块尽量不要分开加,否则会产生空气裹集和熔接区,导致制品强度下降。
(4)其他在加料前,为增加片材的流动性,可采用100℃或120℃下预热操作。
这一点对成型深拉形制品尤其有利。
3、成型当料块进入模腔后,压机快速下行。
当上、下模吻合时,缓慢施加所需成型压力,经过一定的固化制度后,制品成型结束。
SMC产品工艺流程

SMC产品工艺流程一.SMC的成型工艺流程压制前准备(模具升温、压机工艺参数设定)——SMC片材裁料——模具投料——保压——脱模——加工(去废边等)——成品。
⑴压制前准备(模具升温、压机工艺参数设定):通常模具温度一般来说是到130°~150°之间,成型压力为5~10兆帕,相当于每平方厘米施加50公斤到100公斤的压力,压力非常高。
⑵SMC片材裁料:裁剪SMC片材,为模具投料做准备。
⑶模具投料:经过严格的重量计算,将SMC片材投入模具中,通常投料面积在50%-90%之间。
⑷保压:模具闭合后,保持高温高压,通常保持时间根据产品要求不同在2-10分钟之间。
⑸脱模:控制压机模具开启,将产品从模具中起出。
⑹加工:剪裁废边,打磨模具边缘与缝隙间的毛刺。
⑺得出半成品半成品按照一定规律进行码放,经质检合格的产品转运入库。
二.科逸SMC模压生产工艺参数三.提高SMC制品的条件与方法SMC配件的模压质量,取决于压机设备、模具、工艺参数以及作业人员素质等因素。
科逸SMC模压件质量的优异稳定,不仅仅来自于对制造工艺和生产管理手段的严格控制,更重要的主要是科逸在生产的各个方面都有良好的积累。
首先,在压机设备上,卫浴SMC部品对于压机要求十分严格。
模压时需要对产品施加的压力为50-100公斤/平方厘米。
所以面积越小的产品需要的压力就小,面积较大的部件,如防水盘、壁板、浴缸、顶板等才需要压力更大的压机。
所以卫浴企业拥有单台压机最大压力值越大,产品就可以做的越大。
反之,就无法提供完善的产品。
其次,SMC部件的模压工艺,决定了对生产过程中的各个方面都必须精确,包括对压机的水平定位,压机滑块上下移动速度,模具精度等等方面。
生产时模具内每一个区域的压力、温度,甚至是开闭模具瞬间的压力都要平均准确。
这就要求SMC部件压机、模具精度都极高,远超其他行业,压机、模具的数量规模和精度是一个整体浴室企业保障产品质量、丰富产品门类的关键设备。
- 1、下载文档前请自行甄别文档内容的完整性,平台不提供额外的编辑、内容补充、找答案等附加服务。
- 2、"仅部分预览"的文档,不可在线预览部分如存在完整性等问题,可反馈申请退款(可完整预览的文档不适用该条件!)。
- 3、如文档侵犯您的权益,请联系客服反馈,我们会尽快为您处理(人工客服工作时间:9:00-18:30)。
SMC树脂糊的组成
树脂 引发剂
填料 低收缩添加剂
化学增稠剂 内脱模剂 着色剂
不饱和聚酯(间苯型UP、邻苯型UP) 过氧化物(BPO、TBP) CaCO3 热塑性树脂粉 MgO 硬酯酸金属盐 染料
15
SMC的工艺特点和地位
操作方便,易实现自动化,生产效率高,改善了湿法成型的 作业环境和劳动条件; 通过改变组分的种类与配比,可改变成型工艺和制品性能; 通过改变填料的种类与加入量,可降低成本或使制品轻量化; 成型流动性好,可成型结构复杂的制件或大型制件; 制品尺寸稳定性好,表面平滑,光泽好,纤维浮出少,从而 简化了后处理工序; 增强材料在生产与成型过程中均无损伤,制品强度高,可进 行轻型化结构设计。
19
SMC模塑料常用引发剂的特性
性能
状态
70℃
半衰期,/h
90 ℃ 110 ℃
130 ℃
150 ℃
固化温度,℃
用量,%
贮存期,室温
BPO 糊状 1.4 1.2 0.13
/ / 107~149 2 1周
引发剂 TBP 液体 / 7 6 / / 2.3 2.3 0.26 125~149 2 >3月
树脂糊
无捻粗纱 切割,沉降 玻璃毡
上薄膜 浸渍,收卷
树脂糊
下薄膜
制片过程
稠化
包装
11
12
SMC的特点
① SMC能与金属材料相抗衡。 ② SMC与增强热塑性塑料相比, SMC的成型周期短,成型设备
投资低, SMC制品不易变形,机械性能与热变形温度较高。 耐化学药品性优.且价格较低。 ③ SMC与一般热塑性塑料相比,前者物理机械性能是后者无法 比拟的。 ④ SMC与BMC相比,尽管BMC可注塑,但它只适于短纤维的 加工,若需要制造高强度的材料则仍需使用SMC。 ⑤ SMC与手糊/喷射玻璃钢材料相比,无论在成型周期、工作 环境、成本及制品外观质量上都比手糊/喷射制品更优。
17
填料
在SMC中加入填料,可降低成本,减少收缩率,调节粘 度,赋予材料某些特殊性能。
填料的选择,需考虑:①颗粒大小,②油吸附量,③触变 现象。
这三种因素都与填料颗粒的表面有关,如油吸附量(指填料 被亚麻仁油润湿的质量百分比)。填料的油吸附量是比表面积 的函数,填料间空隙的增加,比表面积增大,其油吸附量就 大。油吸附量小的填料,在树脂中的用量百分比就可增加。 因此,在片状模塑料中,往往要求填料具有较低的油吸附量。
第四章 模压成型
课前复习
从制造商的角度,试分析: 1、手糊成型的优点? 2、手糊成型的不足?
1
发展思路
基本上是手工操 作,劳动强度大
产品质量 稳定性差
制品的力学性能 有溶剂, 不
较其它方法低
够“绿色”
尽量采用 机械化生 产方式。
采用模具 来生产。
加压生产.
采用“干 法”生产。
3
手糊工艺的优点与不足之处
2.0
23
10~40
6~16
水合氧化铝(ATH) 阻燃,改善制品耐水 性和电绝缘性能。
100
80
LOI, %
价格
60
中等 低
40 20
0 0 100 200 300 400
ATH用量(质量份) 20
低收缩添加剂
控制收缩率是通过在不饱和聚酯树脂中加入一定量的 热塑性聚合物来实现。
热塑性树脂 UP树脂
7
模压成型的类型
短纤维料模压法 毡料模压法 碎布料模压法 层压模压法 缠绕模压法 织物模压法 片状模塑料模压法 ……
6
片状模塑料
SMC汽车配件 SMC原料
8
SMC原料生产
团状模塑料
BMC原料
采用BMC制备的高压 电器元件
9
10
BMC生产现场
SMC流程示意
UP树脂
固化剂 增稠剂
树脂体系
颜,填料 低收缩剂
加热固化
团状模塑料(Bulk Molding Compound,BMC):与 SMC 相似,两者的主要区别在于模压料的形态和制备工艺不同。 制备方法是将树脂和增强材料等用捏和机捏和均匀,经增稠 后制得团状模塑料。
BMC 中纤维含量较少,纤维长度较短,一般为 5 ~ 20 mm,填料含量比 SMC 大。因此,BMC 制品的强度低于 SMC制品。BMC 适合于压制小型的异型制品。
14
树脂
不饱和聚酯树脂(UP)是SMC的最基本配方材料。根据其 化学结构上的差异通常可分为通用型、间苯型、双酚A型三 大类。在SMC生产中,最常用的是邻苯型和间苯型不饱和聚 酯树脂。
用邻苯二甲酸二烯丙基酯(DAP)、间苯二甲酸二烯丙基酯 (DAIP)、三聚氰酸三烯丙基酯(TAC)等烯丙基类单体代替苯 乙烯作为交联剂,可以明显地提高制品的耐热性能、耐候性 能和尺寸稳定性能。同时,由于这类单体低的挥发性,改善 了环境条件,并且还延长了SMC的贮存期。
优点
①是复合材料成型最基本 的方法,或者说是一种“万 能”方法。能够成型任意形 状、任意大小的制品;
②设备简单、投资少;
③一般情况下不需要加压 操作,工艺最为简单。
不足
① 劳动强度大、生产效率低、速 度慢、生产周期长;
② 产品质量受操作人员技能水平 及制作环境条件的影响,故产品质 量稳定性差;
③制品的力学性能较其它方法低;
18
填料
z 填料按其化学成分可分为四类:氧化硅及硅酸盐类(石棉、 滑石粉、瓷土、氧化硅、硅藻土等);碳酸盐类(碳酸钙);硫 酸盐类(硫酸钡、硫酸钙等);氢氧化物类(氢氧化铝)。
z 多数情况下填料用量占SMC配方总量的1/3以上。
CaCO3
遮盖性好,改善制品 表面性能。
类型 I II
性能 颗粒尺寸/μm 吸油值
16
引发剂
选择引发剂需考虑两个因素:模压料的贮存稳定性和 固化温度。
过氧化二苯甲酰(BPO)作为引发剂具有反应温度范围广、 模压时对温度控制并不苛求的优点,但是SMC的长期贮存 稳定性较差。
用过氧化苯甲酸叔丁酯(TBP)作引发剂,SMC具有较长 期的贮存稳定性,但在压制时需要较高的固化温度。
过氧化二异丙苯(DCP)的性能基本上类似于TBP。
④不够“绿色”,有一定污染。
2
模压成型
(Compression Molding )
树脂体系 增强纤维 模具 压机
模压料
4
模具及压机
5
模塑料
片状模塑料(Sheet Molding Compound,SMC):不饱和 聚酯树脂浸渍短切纤维或毡片,经增稠后制得薄片状模塑料。 在生产时,只需将片状模塑料裁剪、叠合后放入模具中热压, 就可得到制品。