SMT不良原因分析
SMT不良产生原因及对策

SMT不良产生原因及对策SMT(Super Multi-vision Test)不良产生原因及对策是电子制造行业中一个重要的话题。
在电子制造过程中,SMT是一种常用的组装技术,它涉及到大量的元件的高速表面安装。
然而,在实践中,SMT不良很常见,它可能会导致产品质量下降、生产效率降低以及成本增加。
因此,了解不良产生的原因,并采取相应的对策,对于提高SMT生产的质量和效率至关重要。
1.材料问题:SMT使用的元件和焊料可能存在质量问题。
元件可能存在焊盘偏移、引脚损坏、尺寸不一致等问题。
焊料可能存在含波点、气孔等质量问题。
2.设备问题:SMT设备的故障或不当使用也可能引起不良。
设备的加热、输送、贴装等环节可能存在问题,导致元件无法准确地安装在PCB上。
3.操作问题:操作人员操作不当、技术不到位也是不良产生的原因之一、操作人员可能存在操作失误、程序设置错误、参数调整不当等问题。
为了解决SMT不良的问题,可以采取以下对策:1.强化质量管理:确保元件和焊料的质量。
从可靠的供应商购买元件和焊料,并对其进行严格的质量检查。
对于质量问题严重的供应商,需要采取相应的措施,如更换供应商。
2.维护和保养设备:定期对SMT设备进行维护和保养,以确保其正常运行。
培训操作人员,让他们掌握设备的正确使用方法,并确保操作人员具备相关的技术能力。
3.检查和修正操作问题:建立操作规程,并进行培训,确保操作人员按照规程操作。
同时,建立检查机制,及时发现和纠正操作问题。
定期举行会议,分享操作问题和经验,以便全员学习和提高。
4.强化数据分析和改进活动:建立良好的数据收集和分析体系,及时发现生产过程中的问题,并采取改进措施。
定期评估数据,评估改进措施的效果,及时调整和完善。
5.推行持续改进:将持续改进的理念贯穿于整个SMT生产过程中。
不断寻找不良产生的原因,通过改进工艺流程、优化设备和培训操作人员等方式,降低不良的发生率。
总结起来,SMT不良产生的原因有材料问题、设备问题和操作问题等。
SMT不良原因及对策

3、上料员上料方向上反;
3、上料前对材料方向进行确认;
4、FEEDER 压盖变开导致,元件供给时方向; 4、维修或更换 FEEDER 压盖;
5、机器归正件时反向;
5、修理机器归正器;
6、来料方向变更,盘装方向变更后程序未变 6、发现问题时及时修改程序;
更方向;
7、Q、V 轴马达皮带或轴有问题。
7、检查马达皮带和马达轴。
11、检查 783 或驱动箱风扇;
12、MPA3 吸咀定位锁磨损导致吸咀晃动造成 12、更换 MAP3 吸咀定位锁。
贴装偏移。
1、PCB 焊盘上有惯穿孔; 2、钢网开孔过小或钢网厚度太薄; 3、锡膏印刷时少锡(脱膜不良); 4、钢网堵孔导致锡膏漏刷。
1、原材料不良; 2、规正器不顺导致元件夹坏; 3、吸着高度或贴装高度过低导致; 4、回焊炉温度设置过高; 5、料架顶针过长导致; 6、炉后撞件。
3、回焊炉升温过快导致;
3、调整回流焊升温速度 90-120sec;
4、元件贴装偏移导致;
4、调整机器贴装座标;
5、钢网开孔不佳(厚度过厚,引脚开孔过长, 5、重开精密钢网,厚度一般为 0.12mm-0.15mm;
开孔过大);
6、锡膏无法承受元件重量;
6、选用粘性好的锡膏;
7、钢网或刮刀变形造成锡膏印刷过厚;
4、锡膏中有异物;
4、印刷过程避免异物掉过去;
5、炉温设置过高或反面元件过重;
5、调整炉温或用纸皮垫着过炉;
6、机器贴装高度过高。
6、调整贴装高度。
错件
1、机器贴装时无吹气抛料无吹气,抛料盒毛 1、检查机器贴片吹气气压抛料吹气气压抛料盒毛刷;
刷不良;
2、贴装高度设置过高元件未贴装到位;
SMT产品常见不良及其原因分析_产品不良的分类

SMT产品常见不良及其原因分析_产品不良的分类SMT 产品常见不良及其原因分析_产品不良的分类SMT 常见不良及其原因分析一. 主要不良分析主要不良分析.锡珠(Solder Balls):1. 丝印孔与焊盘不对位,印刷不精确,使锡膏弄脏PCB 。
2. 锡膏在氧化环境中暴露过多、吸空气中水份太多。
3. 加热不精确,太慢并不均匀.4. 加热速率太快并预热区间太长。
5. 锡膏干得太快。
6. 助焊剂活性不够。
7. 太多颗粒小的锡粉。
8. 回流过程中助焊剂挥发性不适当。
锡球的工艺认可标准是:当焊盘或印制导线的之间距离为0.13mm 时,锡珠直径不能超过0.13mm ,或者在600mm平方范围内不能出现超过五个锡珠。
锡桥(Bridge solder):1. 锡膏太稀, 包括锡膏内金属或固体含量低、摇溶性低、锡膏容易榨开.2. 锡膏颗粒太大、助焊剂表面张力太小.3. 焊盘上太多锡膏.4. 回流温度峰值太高等.开路(Open):1. 锡膏量不够.2. 组件引脚的共面性不够.3. 锡湿不够(不够熔化、流动性不好) ,锡膏太稀引起锡流失.4. 引脚吸锡(象灯芯草一样) 或附近有联机孔. 引脚吸锡可以通过放慢加热速度和底面加热多、上面加热少来防止.5. 焊锡对引脚不熔湿, 干燥时间过长引起助焊剂失效、回流温度过高/时间过长引起氧化.6. 焊盘氧化, 焊锡没熔焊盘.墓碑(Tombstoning/Part shift):墓碑通常是不相等的熔湿力的结果,使得回流后组件在一端上站起来, 一般加热越慢,板越平稳,越少发生。
降低装配通过183° C 的温升速率将有助于校正这个缺陷。
空洞:是锡点的X 光或截面检查通常所发现的缺陷。
空洞是锡点内的微小“气泡”, 可能是被夹住的空气或助焊剂。
空洞一般由三个曲线错误所引起:不够峰值温度;回流时间不够;升温阶段温度过高。
造成没挥发的助焊剂被夹住在锡点内。
这种情况下,为了避免空洞的产生,应在空洞发生的点测量温度曲线,适当调整直到问题解决。
SMT制程不良原因及改善对策

▪ 13、将网孔向相反方向锉大;
集团管理咨询项目
© 公司版权所有 2008
空焊
▪ 14、机器贴装高度设置不当; ▪ 15、锡膏较薄导致少锡空焊; ▪ 16、锡膏印刷脱膜不良。 ▪ 17、锡膏使用时间过长,活性剂挥发掉; ▪ 18、机器反光板孔过大误识别造成; ▪ 19、原材料设计不良; ▪ 20、料架中心偏移; ▪ 21、机器吹气过大将锡膏吹跑; ▪ 22、元件氧化; ▪ 23、PCB贴装元件过长时间没过炉,导致活性
▪ 6、调整升温速度90-120秒; ▪ 7、用助焊剂清洗PCB; ▪ 8、对PCB进行烘烤; ▪ 9、调整元件贴装座标;
▪ 12、MARK点误照造成元件打偏,导致空焊; ▪ 10、调整印刷机;
▪ 13、PCB铜铂上有穿孔;
▪ 11、松掉X、Y Table轨道螺丝进行调整;
▪ 12、重新校正MARK点或更换MARK点;
集团管理咨询项目
© 公司版权所有 2008
直立
▪ 产生原因
▪ 改善对策
▪ 1、铜铂两边大小不一产生拉力不均; ▪ 2、预热升温速率太快; ▪ 3、机器贴装偏移; ▪ 4、锡膏印刷厚度不均; ▪ 5、回焊炉内温度分布不均; ▪ 6、锡膏印刷偏移; ▪ 7、机器轨道夹板不紧导致贴装偏移; ▪ 8、机器头部晃动; ▪ 9、锡膏活性过强; ▪ 10、炉温设置不当; ▪ 11、铜铂间距过大; ▪ 12、MARK点误照造成元悠扬打偏; ▪ 13、料架不良,元悠扬吸着不稳打偏; ▪ 14、原材料不良; ▪ 15、钢网开孔不良; ▪ 16、吸咀磨损严重; ▪ 17、机器厚度检测器误测。
过长,开孔过大); ▪ 6、锡膏无法承受元件重量; ▪ 7、钢网或刮刀变形造成锡膏印刷过厚; ▪ 8、锡膏活性较强; ▪ 9、空贴点位封贴胶纸卷起造成周边元件
SMT贴片制程不良原因及改善对策

SMT制程不良原由及改良对策:空焊,短路,直立, 缺件,锡珠,翘脚,浮高,错件,冷焊 , 反向,反白 / 反面,偏移,元件损坏,少锡,多锡,金手指粘锡,溢胶。
一、空焊产生原由1, 锡膏活性较弱;2, 钢网开孔不好;3, 铜铂间距过大或大铜贴小元件;4, 刮刀压力太大;5, 元件脚平坦度不好(翘脚, 变形)6, 回焊炉预热区升温太快;7,PCB铜铂太脏或许氧化;8,PCB板含有水份;9, 机器贴装偏移;10, 锡膏印刷偏移;11, 机器夹板轨道松动造成贴装偏移;12,MARK点误照造成元件打偏,致使空改良对策1, 改换活性较强的锡膏;2, 开设精准的钢网;3, 未来板不良反应于供应商或钢网将焊盘间距开为;4, 调整刮刀压力;5, 将元件使用前作检视并修整;6, 调整升温速度 90-120 秒;7, 用助焊剂冲洗 PCB;8, 对 PCB进行烘烤;9, 调整元件贴装座标;10, 调整印刷机;11, 松掉 X,Y Table 轨道螺丝进行调整;12, 从头校订 MARK点或改换 MARK点;焊;13,PCB铜铂上有穿孔;13, 将网孔向相反方向锉大;14, 机器贴装高度设置不妥;14, 从头设置机器贴装高度;15, 锡膏较薄致使少锡空焊;15, 在网网下垫胶纸或调整钢网与PCB间距;16, 锡膏印刷脱膜不良。
16, 开精细的激光钢钢,调整印刷机;17, 锡膏使用时间过长,活性剂挥发掉;17, 用新锡膏与旧锡膏混淆使用;18, 机器反光板孔过大误辨别造成;18, 改换适合的反光板;19, 原资料设计不良;19, 反应 IQC联系客户;20, 料架中心偏移;20, 校订料架中心;21, 机器吹气过大将锡膏吹跑;21, 将贴片吹气调整为cm2;22, 元件氧化;22, 吏换OK之资料;23,PCB贴装元件过长时间没过炉,致使23, 实时将PCB‘A 过炉,生产过程中避活性剂挥发;免聚积;24, 机器轴皮带磨损造成贴装角度偏信24, 改换Q1或Q2皮带并调整松紧度;移过炉后空焊;25, 流拉过程中板边元件锡膏被擦掉造25, 将轨道磨掉,或将PCB转方向生产;成空焊;26, 钢网孔拥塞漏刷锡膏造成空焊。
SMT常见不良原因分析
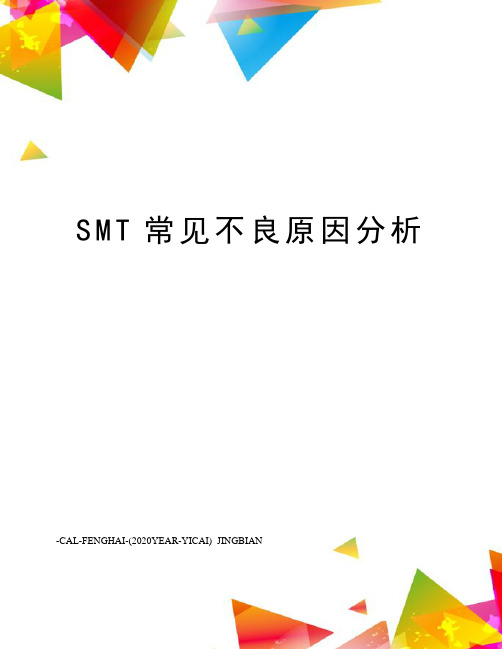
S M T常见不良原因分析-CAL-FENGHAI-(2020YEAR-YICAI)_JINGBIANSMT常见不良原因分析一.锡球:1.印刷前,锡膏未充分回温解冻并搅拌均匀。
2.印刷后太久未回流,溶剂挥发,膏体变成干粉后掉到油墨上。
3.印刷太厚,元件下压后多余锡膏溢流。
4.REFLOW时升温过快(SLOPE>3),引起爆沸。
5.贴片压力太大,下压使锡膏塌陷到油墨上。
6.环境影响:湿度过大,正常温度25+/-5,湿度40-60%,下雨时可达95%,需要抽湿。
7.焊盘开口外形不好,未做防锡珠处理。
8.锡膏活性不好,干的太快,或有太多颗粒小的锡粉。
9.锡膏在氧化环境中暴露过久,吸收空气中的水分。
10.预热不充分,加热太慢不均匀。
11.印刷偏移,使部分锡膏沾到PCB上。
12.刮刀速度过快,引起塌边不良,回流后导致产生锡球。
P.S:锡球直径要求小于0.13MM,或600平方毫米小于5个.一. 锡球:压缩空气水分含量大 1.2. 焊膏有没有做过SOLDER BALL TEST 和HOT SLUMP TEST.3. 要区分是SOLDER BALLING 还是SOLDER BEADING.4. PROFILE是否恰当, 找到适合的proifle , 难!5. DEK 参数是否得当, 印刷后高度, SUPPORT PIN OR SUPPORT BLOCK 放置准确.6. PD准确,tolerance 恰当.二、立碑:1.印刷不均匀或偏移太多,一侧锡厚,拉力大,另一侧锡薄拉力小,致使元件一端被拉向一侧形成空焊,一端被拉起就形成立碑。
2.贴片偏移,引起两侧受力不均。
3.一端电极氧化,或电极尺寸差异太大,上锡性差,引起两端受力不均。
4.两端焊盘宽窄不同,导致亲和力不同。
5.锡膏印刷后放置过久,FLUX挥发过多而活性下降。
6.REFLOW预热不足或不均,元件少的地方温度高,元件多的地方温度低,温度高的地方先熔融,焊锡形成的拉力大于锡膏对元件的粘接力,受力不均匀引起立碑。
SMT贴片不良的原因及改善对策

SMT贴片不良的原因及改善对策空焊1、锡膏活性较弱;1、更换活性较强的锡膏;2、钢网开孔不佳;2、开设精确的钢网;3、铜铂间距过大或大铜贴小元件;3、将来板不良反馈于供应商或钢网将焊盘间距开为0.5mm;4、刮刀压力太大;4、调整刮刀压力;5、元件脚平整度不佳(翘脚、变形)5、将元件使用前作检视并修整;6、回焊炉预热区升温太快;6、调整升温速度90-120秒;7、PCB铜铂太脏或者氧化;7、用助焊剂清洗PCB;8、PCB板含有水份;8、对PCB进行烘烤;9、机器贴装偏移;9、调整元件贴装座标;10、锡膏印刷偏移;10、调整印刷机;11、机器夹板轨道松动造成贴装偏移;11、松掉X、Y Table轨道螺丝进行调整;12、MARK点误照造成元件打偏,导致空焊;12、重新校正MARK点或更换MARK点;13、PCB铜铂上有穿孔;13、将网孔向相反方向锉大;14、机器贴装高度设置不当;14、重新设置机器贴装高度;15、锡膏较薄导致少锡空焊;15、在网网下垫胶纸或调整钢网与PCB间距;16、锡膏印刷脱膜不良。
16、开精密的激光钢钢,调整印刷机;17、锡膏使用时间过长,活性剂挥发掉;17、用新锡膏与旧锡膏混合使用;18、机器反光板孔过大误识别造成;18、更换合适的反光板;19、原材料设计不良;19、反馈IQC联络客户;20、料架中心偏移;20、校正料架中心;21、机器吹气过大将锡膏吹跑;21、将贴片吹气调整为0.2mm/cm2;22、元件氧化;22、吏换OK之材料;23、PCB贴装元件过长时间没过炉,导致活性剂挥发;23、及时将PCB'A过炉,生产过程中避免堆积;24、机器Q1.Q2轴皮带磨损造成贴装角度偏信移过炉后空焊;24、更换Q1或Q2皮带并调整松紧度;25、流拉过程中板边元件锡膏被擦掉造成空焊;25、将轨道磨掉,或将PCB转方向生产;26、钢网孔堵塞漏刷锡膏造成空焊。
26、清洗钢网并用风枪吹钢网。
SMT贴片制程不良原因及改善对策

SMT制程不良原因及改善对策:空焊,短路,直立,缺件,锡珠,翘脚,浮高,错件,冷焊,反向,反白/反面,偏移,元件破损,少锡,多锡,金手指粘锡,溢胶;
一、空焊
产生原因
改善对策
1,锡膏活性较弱;
1,更换活性较强的锡膏;
2,钢网开孔不佳;
2,开设精确的钢网;
3,铜铂间距过大或大铜贴小元件;
19,原材料设计不良;
19,反馈IQC联络客户;
20,料架中心偏移;
20,校正料架中心;
21,机器吹气过大将锡膏吹跑;
21,将贴片吹气调整为cm2;
22,元件氧化;
22,吏换OK之材料;
23,PCB贴装元件过长时间没过炉,导致活性剂挥发;
23,及时将PCB‘A过炉,生产过程中避免堆积;
24,机器轴皮带磨损造成贴装角度偏信移过炉后空焊;
1,钢网开孔过大或厚度过厚;
1,开钢网时按标准开网;
2,锡膏印刷厚过厚;
2,调整PCB与钢网间距;
3,钢网底部粘锡;
3,清洗钢网;
4,修理员回锡过多
4,教导修理员加锡时按标准作业;
十六,金手指粘锡
产生原因
不良改善对策
1,PCB未清洗干净;
1,PCB清洗完后经确认后投产;
2,印刷时钢网底部粘锡导致;
2,清洗钢网,并用高温胶纸把金手指封体;
1,生产前先对材料进行检查,有NG品修好后再贴装;
2,规正座内有异物;
2,清洁归正座;
3,程序设置有误;
3,修改程序;
4,MK规正器不灵活;
4,拆下规正器进行调整;
七,浮高
产生原因
不良改善对策
1,PCB板上有异物;
- 1、下载文档前请自行甄别文档内容的完整性,平台不提供额外的编辑、内容补充、找答案等附加服务。
- 2、"仅部分预览"的文档,不可在线预览部分如存在完整性等问题,可反馈申请退款(可完整预览的文档不适用该条件!)。
- 3、如文档侵犯您的权益,请联系客服反馈,我们会尽快为您处理(人工客服工作时间:9:00-18:30)。
钢网磨损,张力不够:
更换钢网。
印刷不良之原因探讨及改善
印刷移位之主要原因分析改善:
坐标调整不当(移位):
调整印刷参数﹕ OFFSET X﹕ OFFSET Y﹕ OFFSET θ﹕(一般不作调整)
PCB 定位不良﹕
检查支撐BLOCK&支撐PIN有无变形,高度是否一致﹐檢查支撐BLOCK &支撐PIN下面是否有异物﹒支撑处有无元件.夹边正常否.
案例分析
验证过程: 实测锡膏厚度, 使用同一张钢网同一机器印锡: SUNGWEI(松维) PCB锡膏厚度 180~190um, KINYIP(建业) PCB锡膏厚度180~190um.
实测银孔高度 SUNGWEI(松维) 50~70um; KINYIP(建业) 30~50um; 实际的印锡情况,发现CN101印锡连锡绝大部分都出现 在银孔旁边的焊盘炉后的不良也同样。
(3) 焊料量不足与虚焊或断路(开路)
原因分析 预防对策 a 整体焊膏量过少原因:①模板厚度 ①加工合格的模板,模板喇叭口向下,增 或开口尺寸不够;开口四壁有毛刺; 加模板厚度或扩大开口尺寸。 喇叭口向上,脱模时带出焊膏。②焊 ②更换焊膏。 膏滚动(转移)性差。③刮刀压力过 ③采用不锈钢刮刀。 大,尤其橡胶刮刀过软,切入开口, ④调整印刷压力和速度。 带出焊膏。④印刷速度过快。 膏原因:①模板漏孔被焊膏堵塞或个 别开口尺寸小。②导通孔设计在焊盘 上,焊料从孔中流出。 能与相对应的焊盘接触。 能完全与焊膏接触。 ⑤调整基板、模板、刮刀的平行度。 洗模板底面。如开口尺寸小,应扩大开 口尺寸。 ②修改焊盘设计 装,人工贴装时不要碰伤引脚。 ②大尺寸 PCB 再流焊时应采用底部支撑。 b 个别焊盘上的焊膏量过少或没有焊 ①清除模板漏孔中的焊膏,印刷时经常擦
a PCB 设计——两个焊盘尺寸大小不 按照 Chip 元件的焊盘设计原则进行设计, 对称,焊盘间距过大或过小,使元件 注意焊盘的对称性、焊盘间距 = 元件长度 的一个端头不能接触焊盘。 两个电极的长度+K(0.25±0.05mm) b 贴片质量——位置偏移;元件厚度 提高贴装精度,精确调整首件贴装坐标,连 设置不正确;贴片头 Z 轴高度过高 续生产过程中发现位置偏移时应及时修正 (贴片压力小) ,贴片时元件从高处 贴装坐标。设置正确的元件厚度和贴片高 扔下造成。 度。 C 元件质量——焊端氧化或被污染。 严格来料检验制度,严格进行首件焊后检 元件端头不润湿或端头电极脱落、 元 验,每次更换元件后也要检验,发现端头问 件外形和尺寸不一致。 字符、阻焊膜或氧化等) 量不一致 动;风量过大。 g 温度曲线,升温速度过快 题及时更换元件。 盘上的丝网、字符可用小刀轻轻刮掉。 板底面。如开口过小,应扩大开口尺寸。 和出口处导轨衔接高度和距离是否匹配。 人 工放置 PCB 要轻拿轻放。调整风量。 调整温度曲线 d PCB 质量——焊盘被污染 (有丝网、 严格来料检验制度, 对已经加工好 PCB 的焊 e 印刷工艺——两个焊盘上的焊膏 清除模板漏孔中的焊膏, 印刷时经常擦洗模 f 传送带震动会造成元器件位置移 传送带太松,可去掉 1~2 节链条;检查入口
主要内容
常见印锡不良现象分类
引起印锡不良的五大要素
各种印锡不良之原因探讨及改善
典型案例共享.
SMT常见印锡不良现象主要有以下几种:
印刷短路(连锡) 印刷移位 印刷拉尖少锡
锡膏印刷偏厚
锡膏印刷偏薄
锡膏塌陷
印刷OK
影响印刷质量的五大因素:
机器:设备故障,参数设置等
搅拌再使用;更换锡膏。 检查温/湿度是否超标.如有,反馈相关人员处理.
钢网不良(开口粗糙不平滑):
更换钢网;反馈相关人员处理(重开钢网). .
印刷不良之原因探讨及改善
印刷拉尖少锡之主要原因分析改善: 刮刀变形或硬度不够:
更换刮刀.
PCB与STENCIL之间的间隙太大:
检查SANP OFF设置是否异常,一般为0. 重做钢网高度.
(5) 焊点桥接或短路——桥接又称连桥
桥接原因分析 预防对策 a 焊锡量过多:可能由于模板厚度 ①减薄模板厚度或缩小开口或改变开口形状; 与开口尺寸不恰当; 模板与印制板 ② 调整模板与印制板表面之间距离,使接触并 表面不平行或有间隙。 好,印刷后塌边,焊膏图形粘连。 c 印刷质量不好,焊膏图形粘连 d 贴片位置偏移 使图形粘连。 f 由于贴片位置偏移,人工拨正后 提高贴装精度,减少人工拨正的频率。 使焊膏图形粘连。 g 焊盘间距过窄 修改焊盘设计。 提高印刷精度并经常清洗模板 提高贴装精度, 平行。 b 由于焊膏黏度过低,触变性不 选择黏度适当、触变性好的焊膏
PCB MARK不良﹕
检查此PCB的MARK﹐擦拭该MARK﹐调整识别参数;选取其它 MARK,重做TEACH VISION.
印刷不良之原因探讨及改善
印刷移位之主要原因分析改善:
STENCIL & SQUEEGEE
HEIGHT设置不当 :
检查PCB上表面与STENCIL下表面是否刚好紧贴,STENCIL有无 变形. 重做STENCIL&SQUEEGEE HEIGHT.
(5) 焊点桥接或短路
(6) 焊锡球 (7) 气孔、空洞 (8) 吸料现象 (9) 锡丝
(14) 冷焊、焊点扰动
(15)焊锡裂纹
(16) 焊盘露铜
(17) 爆米花现象 (18) 其它
(1) 焊膏熔化不完全——全部或局部焊点周围有未熔化的残留焊膏
焊膏熔化不完全的原因分析 流时间短,造成焊膏熔化不充分。 预防对策 膏熔点高 30℃ ~40 ℃左右,再流时间为 30s~60s。 b 再流焊炉——横向温度不均匀。一 适当提高峰值温度或延长再流时间。尽 般发生在炉体较窄,保温不良的设备 量将 PCB 放置在炉子中间部位进行焊接。 c PCB 设计——当焊膏熔化不完全发 1 尽量将大元件布在 PCB 的同一面,确实 生在大焊点,大元件、以及大元件周 排布不开时,应交错排布。 围、或印制板背面有大器件。 2 适当提高峰值温度或延长再流时间。 d 红外炉——深颜色吸热多,黑色比 为了使深颜色周围的焊点和大体积元器 白色约高 30℃~40℃,PCB 上温差大。 件达到焊接温度,必须提高焊接温度。 e 焊膏质量问题——金属粉含氧量 不使用劣质焊膏;制订焊膏使用管理制 高;助焊性能差;或焊膏使用不当: 度:如在有效期内使用;从冰箱取出焊 没有回温或使用回收与过期失效焊膏 膏,达到室温后才能打开容器盖;回收 的焊膏不能与新焊膏混装等。 a 温度低——再流焊峰值温度低或再 调整温度曲线,峰值温度一般定在比焊
支撑PIN设置不合理﹕
检查PIN的分布是否均匀及高度是否一致.重新设置。
锡膏太少或钢网网孔堵塞:
及时添加锡膏,做到少量多次. 定时清洁钢网及抽查印锡质量.
பைடு நூலகம்
锡膏粘在刮刀上﹕
检查锡膏量是否过多;遵循少量多次原则添加. 检查锡膏粘度是否超标,更换锡膏.
案例分析
07.08.02. L15线生产产品JW7U(H55N)时,CN101 炉后连锡严重,不良率高达10%.经查为印锡偏厚/短路导致. 不良现象如下图所示: 连锡不良
元件引脚间距小(0.4mm或以下),而脱网速度过快: 使用SLOW SNAP OFF ;降低SLOW SNAP OFF的值﹐並增大
SNAP OFF DELAY的值﹒
印刷不良之原因探讨及改善
印刷拉尖少锡之主要原因分析改善:
印刷参数设置不当(速度,压力,擦拭等):
依据实际生产情况,正确设置相关参数.
c 器件引脚共面性差,翘起的引脚不 运输和传递 SOP 和 QFP 时不要破坏外包 d PCB 变形,使大尺寸 SMD 器件引脚不 ①PCB 设计要考虑长、宽和厚度的比例。
(4) 立碑和移
吊桥和移位原因分析
预防对策
位——又称吊桥、
墓碑现象、曼哈 顿现象;移位是 指元器件端头或 引脚离开焊盘的 错位现象。
反馈客户”银孔过高”的问题 ,推动客户改善。
回流焊焊接过程
自定位效应(self alignment)
SMT回流焊接中 常见的焊接缺陷分析与预防对策
(1) 焊膏熔化不完全 (2) 润湿不良 (3) 焊料量不足与虚焊 (4) 立碑和移位 (10) 元件裂纹缺损 (11) 元件端头镀层剥落 (12) 元件侧立 (13) 元件贴反
e 贴片压力过大, 焊膏挤出量过多, 提高贴片头 Z 轴高度,减小贴片压力。
总结:在焊盘设计正确、模板厚度及开口尺寸正确、焊膏质量没有问题的情况下, 应通过提高印刷和贴装质量来减少桥接现象。
(6) 焊锡球— —又称焊料球、 焊锡珠。是指 散布在焊点附 近的微小珠状 焊料。
产生焊锡球的原因分析
预防对策
STENCIL擦拭不良:
检查擦拭参数设置是否正确;擦拭纸是否干净适合;检查擦拭 系统是否正常;是否需要添加清洗剂。
STENCIL 及SQUEEGEE高度设置不当:
( 设置的标准?如何检查?)重新设置STENCIL 及SQUEEGEE高度。
钢网底部有杂物或所贴胶纸太厚及卷起不良:
清洁钢网,重新按工艺要求封钢网。
SMT不良原因分析
• 印刷不良原因分析 • 回流焊不良原因分析
BU2 Engineering Department
前 序
在SMT的生产中,常会面临诸多的品质缺陷,而通常这些缺 陷有70—80%是由于印锡不良引起,要降低制程不良,提高 产品直通率,减少重工,就要求我们及时对印锡不良之原因 作出正确判断并采取有效措施,控制不良产生.
人员: 技能 态度 责任心
印刷 NG品
材料:锡膏,PCB, 钢网, 刮刀,PIN等
环境: 温度,湿度