维修性设计与分析-作业
维修性测试性和可用性

(3)便于使用外部测试设备进行检验测试。与自动测试设备或通用仪器 旳接口简朴、兼容性好,专用测试设备少,设有足够旳测试点和检验 通道。
测试性、可靠性与维修性三者旳关系十分亲密,因为具有良好测 试性旳产品将改善其维修性,直接降低故障检测及隔离时间,进而降 低维修时间;任何不能被检测出旳故障状态旳存在将直接影响产品旳 可靠性。测试性好旳产品可及时检测出故障,排除故障,进而提升产 品旳可用性。
三、测试性基本概念
2.测试性定性定量要求 b.测试性定量要求
故障检测率 r FD
三、测试性基本概念
r 故障隔离率 FI
三、测试性基本概念
故障虚警率 r FA
三、测试性基本概念
3.测试性设计与分析
a.测试方案
b.测试性分配与估计
测试性定性设计
硬件设计中旳一般测试性考虑。例如,在设计产品时合理地划分功能和 构造单元,最佳每个功能划分在一种模块单元里,将构造单元划分为 LRU和SRU或更小旳组件,以便于在不同旳场合进行故障检测与隔离。 又如,应优先选用便于测试且故障模式已经有充分描述旳集成电路或组 件。
d.测试点旳选择与配置 测试点选择与配置旳一般原则:
(1)测试点选择应从系统级到SRU级。测试点选配应尽量适应原位检 测旳需要。在产品旳内部还应配置合适数量供维修使用旳测试点。
(2)应在满足故障检测隔离要求旳条件下,使测试点尽量地少。当测试 点旳设置受限制时,应优先配置其故障会影响安全和任务成功旳单元 旳测试点、故障率高旳单元旳测试点。就故障检测与隔离相比,应优 先配置检测用测试点。
提升产品旳固有可用度既能够经过提升产品旳可靠性水平,即 增大MTBF,也能够经过提升维修性水平,即降低MTTR来实现。 提升产品旳使用可用度,一方面要努力提升产品旳固有可用度,另 一方面要努力提升产品旳维修保障水平,尽量降低多种影响及时维 修旳延误时间等。
维修分析报告
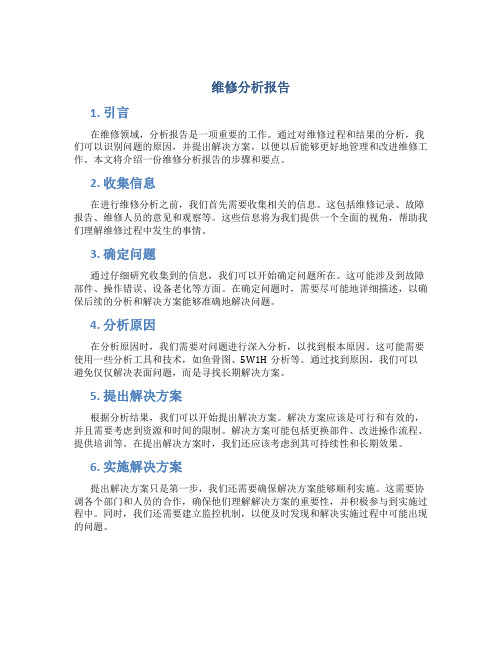
维修分析报告1. 引言在维修领域,分析报告是一项重要的工作。
通过对维修过程和结果的分析,我们可以识别问题的原因,并提出解决方案,以便以后能够更好地管理和改进维修工作。
本文将介绍一份维修分析报告的步骤和要点。
2. 收集信息在进行维修分析之前,我们首先需要收集相关的信息。
这包括维修记录、故障报告、维修人员的意见和观察等。
这些信息将为我们提供一个全面的视角,帮助我们理解维修过程中发生的事情。
3. 确定问题通过仔细研究收集到的信息,我们可以开始确定问题所在。
这可能涉及到故障部件、操作错误、设备老化等方面。
在确定问题时,需要尽可能地详细描述,以确保后续的分析和解决方案能够准确地解决问题。
4. 分析原因在分析原因时,我们需要对问题进行深入分析,以找到根本原因。
这可能需要使用一些分析工具和技术,如鱼骨图、5W1H分析等。
通过找到原因,我们可以避免仅仅解决表面问题,而是寻找长期解决方案。
5. 提出解决方案根据分析结果,我们可以开始提出解决方案。
解决方案应该是可行和有效的,并且需要考虑到资源和时间的限制。
解决方案可能包括更换部件、改进操作流程、提供培训等。
在提出解决方案时,我们还应该考虑到其可持续性和长期效果。
6. 实施解决方案提出解决方案只是第一步,我们还需要确保解决方案能够顺利实施。
这需要协调各个部门和人员的合作,确保他们理解解决方案的重要性,并积极参与到实施过程中。
同时,我们还需要建立监控机制,以便及时发现和解决实施过程中可能出现的问题。
7. 评估效果在解决方案实施一段时间后,我们需要对其效果进行评估。
这可以通过对维修记录和故障报告的分析来实现。
评估的结果将帮助我们判断解决方案的有效性,并决定是否需要进一步改进或调整。
8. 总结和结论维修分析报告的最后一步是总结和结论。
在这一步中,我们将对整个维修过程进行总结,并得出结论。
我们还可以提出一些建议和建议,以便在将来的维修工作中改进。
结论维修分析报告是一个复杂而重要的过程。
维修性设计与分析
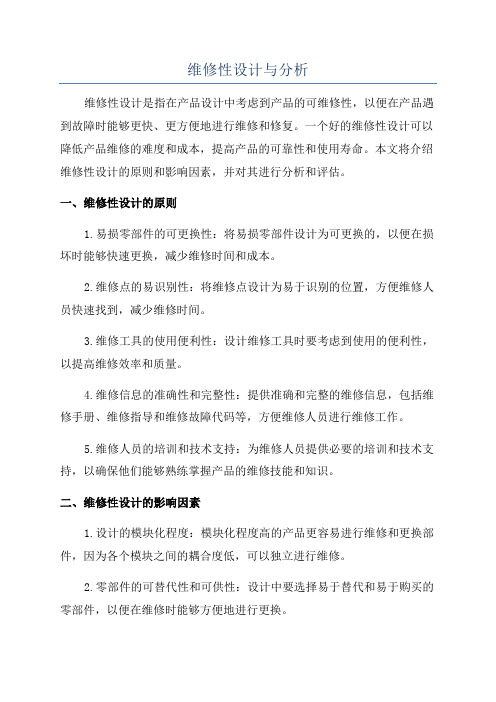
维修性设计与分析维修性设计是指在产品设计中考虑到产品的可维修性,以便在产品遇到故障时能够更快、更方便地进行维修和修复。
一个好的维修性设计可以降低产品维修的难度和成本,提高产品的可靠性和使用寿命。
本文将介绍维修性设计的原则和影响因素,并对其进行分析和评估。
一、维修性设计的原则1.易损零部件的可更换性:将易损零部件设计为可更换的,以便在损坏时能够快速更换,减少维修时间和成本。
2.维修点的易识别性:将维修点设计为易于识别的位置,方便维修人员快速找到,减少维修时间。
3.维修工具的使用便利性:设计维修工具时要考虑到使用的便利性,以提高维修效率和质量。
4.维修信息的准确性和完整性:提供准确和完整的维修信息,包括维修手册、维修指导和维修故障代码等,方便维修人员进行维修工作。
5.维修人员的培训和技术支持:为维修人员提供必要的培训和技术支持,以确保他们能够熟练掌握产品的维修技能和知识。
二、维修性设计的影响因素1.设计的模块化程度:模块化程度高的产品更容易进行维修和更换部件,因为各个模块之间的耦合度低,可以独立进行维修。
2.零部件的可替代性和可供性:设计中要选择易于替代和易于购买的零部件,以便在维修时能够方便地进行更换。
3.维修的诊断和监测工具:产品设计中要考虑到维修的诊断和监测工具的使用,以方便对产品故障进行快速定位和修复。
4.维修过程的简化和标准化:设计中要将维修过程简化和标准化,减少维修步骤和操作,提高维修效率和质量。
5.维修环境的考虑:考虑到维修环境的特殊性,例如温度、湿度、尘埃和振动等因素,以确保维修人员能够在艰苦的环境下进行维修工作。
三、维修性设计的分析和评估在产品设计阶段,可以使用一些工具和方法对维修性进行分析和评估。
常用的方法包括故障模式与影响分析(FMEA)、可靠性、可维修性和可用性分析等。
使用故障模式与影响分析(FMEA)可以对产品设计中可能发生的故障进行分析和评估,以确定可能导致故障的原因、故障的后果和相应的控制措施。
机械系统的可维护性与维修性分析

机械系统的可维护性与维修性分析机械系统的可维护性与维修性对于设备的运行和维护都至关重要。
在设计和选择机械系统时,应当考虑这些因素,以确保系统的长期稳定运行和高效维护。
本文将分析机械系统的可维护性与维修性,并提出相应的改善措施。
1. 可维护性分析可维护性是指机械系统设计是否便于进行维护和保养。
一个可维护性良好的机械系统能够减少维护成本和停机时间,提高设备的可靠性和可用性。
首先,机械系统的可维护性与系统的模块化设计密切相关。
模块化设计可以将整个机械系统划分为多个模块,每个模块可以独立维护。
这样一来,在出现故障或需要更换部件时,只需对特定模块进行处理,而不会影响整个系统的正常运行。
其次,机械系统的维护性还与易损部件的设计和选择有关。
合理的易损部件设计可以延长其使用寿命,减少更换的频率。
同时,选择可靠的易损部件供应商也能够提高维护的便利性和效率。
另外,操作人员的培训和使用说明书的完善也是提高机械系统可维护性的重要因素。
操作人员应当接受专业培训,掌握正确的维护方法并能够快速识别和排除故障。
同时,详细的使用说明书能够为操作人员提供操作指南和故障排除方法,提高维护的准确性和效率。
2. 维修性分析维修性是指机械系统出现故障时的修复难易程度。
一个易于维修的机械系统能够快速恢复正常运行,减少停机时间和生产损失。
首先,机械系统的维修性与部件的可更换性有关。
当出现故障时,能够方便地更换故障部件可以节省修复时间。
因此,在设计机械系统时,应当考虑到部件的易更换性,并提供相应的拆卸接口和固定装置。
其次,机械系统的维修性还与故障诊断和故障排除的便利性有关。
设备应当配备完善的故障诊断系统和故障排除方法。
这样一来,当出现故障时,操作人员能够快速准确地诊断和解决问题,提高维修的效率。
同时,维修工具的适用性和维修材料的供应情况也影响着机械系统的维修性。
正确选择维修工具能够提高维修效率和准确性,而维修材料的供应要及时可靠,以确保维修过程的顺利进行。
机械设计中的机械设计可维修性分析

机械设计中的机械设计可维修性分析机械设计的可维修性是指机械产品在出现故障或需要维护时,方便快捷地进行维修和保养的程度。
在机械设计过程中,考虑和优化机械产品的可维修性是至关重要的。
本文将对机械设计中的可维修性进行分析,并提出一些提高机械产品可维修性的方法和策略。
一、维修性设计原则1.模块化设计:将机械产品划分为不同的模块,使得维修和更换某个部件时,只需更换对应的模块,而不需要整体更换机械产品。
模块化设计可以提高维修效率和降低维修成本。
2.易拆卸性设计:采用易拆卸的连接方式,如螺纹连接、插销连接等,方便拆卸和组装机械产品。
同时,在设计时考虑到维修人员的操作需求,确保拆卸和组装的便捷性。
3.易检修性设计:合理布局机械产品的各个部件,提供足够的空间,方便维修人员进行检查和维修操作。
同时,在设计时考虑维修时所需的工具和设备,以便维修人员能够方便地进行维修工作。
4.易替换性设计:采用标准化零部件,确保故障部件的替换更换能方便快捷地进行。
同时,在设计时要考虑到所使用的零部件的可靠性和可获取性。
二、提高机械产品可维修性的方法和策略1.合理使用材料:在机械产品的设计中选择合适的材料,具有良好的耐磨性、耐腐蚀性和耐高温性,以降低机械产品的故障率,并减少维修的次数和维修的难度。
2.维修性评估和测试:在机械产品设计完成后,进行维修性评估和测试,以评估机械产品的维修性能,并及时发现和解决维修性能方面的问题。
3.培训维修人员:为维修人员提供专业的培训,提高其维修技能和维修操作的熟练程度。
同时,将维修人员的经验和反馈纳入机械产品的改进和优化,以提高机械产品的维修性能。
4.定期维护保养:建立定期维护保养制度,进行机械产品的定期检查和保养,及时发现和解决潜在的问题,确保机械产品的正常运行和延长使用寿命。
三、案例分析以某型号工业机器人为例,对其维修性进行分析。
该机器人采用模块化设计,各个部件之间采用标准化连接方式,方便更换和维修。
机械设计中的可靠性与维修性分析
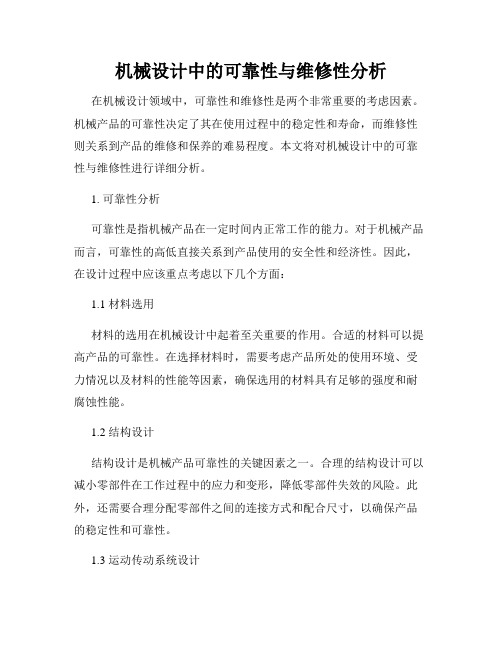
机械设计中的可靠性与维修性分析在机械设计领域中,可靠性和维修性是两个非常重要的考虑因素。
机械产品的可靠性决定了其在使用过程中的稳定性和寿命,而维修性则关系到产品的维修和保养的难易程度。
本文将对机械设计中的可靠性与维修性进行详细分析。
1. 可靠性分析可靠性是指机械产品在一定时间内正常工作的能力。
对于机械产品而言,可靠性的高低直接关系到产品使用的安全性和经济性。
因此,在设计过程中应该重点考虑以下几个方面:1.1 材料选用材料的选用在机械设计中起着至关重要的作用。
合适的材料可以提高产品的可靠性。
在选择材料时,需要考虑产品所处的使用环境、受力情况以及材料的性能等因素,确保选用的材料具有足够的强度和耐腐蚀性能。
1.2 结构设计结构设计是机械产品可靠性的关键因素之一。
合理的结构设计可以减小零部件在工作过程中的应力和变形,降低零部件失效的风险。
此外,还需要合理分配零部件之间的连接方式和配合尺寸,以确保产品的稳定性和可靠性。
1.3 运动传动系统设计运动传动系统是机械产品中常见的关键组成部分。
在设计过程中,需要根据产品的工作要求和使用寿命,选择合适的传动方式和传动元件。
同时,还需要注意传动链路的设计,减小传动效率损失和传动误差,提高产品的可靠性。
2. 维修性分析维修性是指机械产品在出现故障或需要保养时能够方便、快捷地进行维修和保养的能力。
良好的维修性设计可以减少产品的停机时间和维修成本,提高设备的可用性。
以下是维修性设计的一些重要考虑因素:2.1 模块化设计模块化设计是提高产品维修性的有效手段之一。
将机械产品分解为多个独立的模块或部件,每个模块可以独立进行维修或更换。
这样在出现故障时只需要更换具体的模块而无需对整个产品进行维修,大大缩短了维修时间。
2.2 易损部件设计针对机械产品中容易出现故障的部件,设计时可以采用易损部件的形式。
易损部件可以在出现故障时方便地进行更换,减少了维修的难度和成本。
同时,还可以提供易损部件的备件,进一步提高产品的可用性。
车辆系统维修性分析及维修性指标
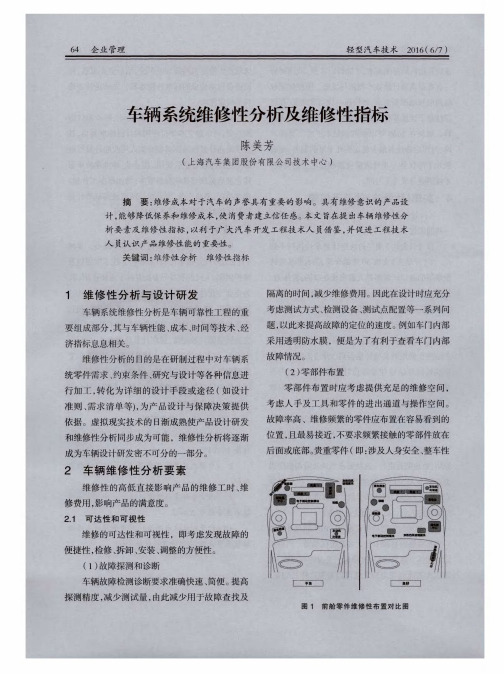
地减 少或 消除 维修人 员 可能遇 到 的危 险 。
维修 性分 析并 没有 一种 简单 的独 特 的技 术 或
以 下 为 某 个 车 型 的 前 舱 零 件 维 修 性 布 置 对 方法 ,它一般 采用 定性与定 量分 析相结 合 的方 法 :
比 ,右 侧 的布置 明显优 于左 侧 ,见 图 1。
减少零部件的品种 、规格数 ,也将降低对维修保障 出关键性 因素或薄弱环节 ,提出具体的设计准则。
资源 的要求 。
(c)运用寿命周期费用分析 ,确定设计 因素对
1)通用设 计 &简化 设计
维修成本 的影响。
零件 设计 时应 考虑 最 大 限度 地 采用 最简 单 的
(d)比较 分 析 。将新 产 品 与类 似产 品相 比较 ,
2.4 防 错 措 施 要 从产 品结构设 计 上采 取措 施 消除发 生 差错
的可能性 ,保证关键性的维修 作业做到 “错不 了”,“不会错 ”,“不 怕错 ”。比如 涉及 安全 的部件 如果能实体互换应能功能互换 ,以免安装差错引
4 车辆 系统/部 件 维修 策 略
在 车 辆研制 过 程 中 ,需将 上述 维修性 分 析要 素按系统 /部件情况进一步展开 ,对各种维修性 需求信息进行罗列 ,转化为详细的车辆系统 /部 件设计准则 ,为产品开发提供维修设计依据。
互换 的单元能实体互换。
行检测 。
2.3 环 境 因 素 环境 要 素指 为保 障 和维护 维修 工作 得 以顺 利
开展 的因素 ,例如温度 、湿度、空气洁净度 、维修时 的光度等。特殊的环境需求会增加维修成本 ,减低 工作效率增加差错 ,好 的维修性应使用尽可能少 的技术和设备 ,无论在那里进行保养或修理 ,其质 量 和性 能都 应 能恢复 到设计 水平 。
维修性分析方案

第1篇
维修性分析方案
一、前言
本方案旨在针对现有设备或系统的维修性问题进行深入分析,提出合理、高效的维修性优化措施,确保设备或系统在运行过程中的可靠性与稳定性。本方案遵循国家相关法律法规,并结合行业最佳实践,力求为委托方提供专业、人性化的维修性解决方案。
二、项目背景
随着科技的发展,各类设备或系统在工业、医疗、交通等领域的应用越来越广泛。在设备或系统的全寿命周期内,维修性分析是保证设备正常运行、降低维修成本、提高设备使用效率的重要环节。然而,在实际操作过程中,维修性问题往往成为制约设备或系统性能的瓶颈。为提高设备或系统的维修性,特制定本方案。
二、项目背景
在当今社会,设备或系统的高效运行对各行各业至关重要。然而,维修性问题往往成为影响设备性能的关键因素。为提高维修效率、降低维修成本、保障设备正常运行,特制定本维修性分析方案。
三、目标与原则
1.目标:
-提高设备或系统的维修性,降低维修频率;
-缩短维修时间,提高维修工作效率;
-降低维修成本,提升设备可靠性。
六、实施与评估
1.实施:
-按照本方案制定的具体措施,分阶段、分步骤推进;
-建立项目实施团队,明确责任分工,确保项目顺利实施;
-定期召开项目会议,及时解决实施过程中遇到的问题。
2.评估:
-设立评估指标,包括维修成本、维修时间、故障率等;
-定期对维修性优化措施进行效果评估,确保方案实施效果;
-根据评估结果,调整优化措施,持续改进维修性。
-加强维修团队建设,提高团队协作能力。
3.维修管理优化:
-制定合理的维修策略,降低维修成本;
-完善维修计划,提高维修工作效率;
-优化维修资源配置,提高维修质量。
- 1、下载文档前请自行甄别文档内容的完整性,平台不提供额外的编辑、内容补充、找答案等附加服务。
- 2、"仅部分预览"的文档,不可在线预览部分如存在完整性等问题,可反馈申请退款(可完整预览的文档不适用该条件!)。
- 3、如文档侵犯您的权益,请联系客服反馈,我们会尽快为您处理(人工客服工作时间:9:00-18:30)。
பைடு நூலகம் 作业
5. 在某项试验评价时,可采用5天或7天的试验周期,但其工作时间 OT度为10h,且TCM=60h、TPM=5h、ALDT=22h。求对应的使 用可用度Ao的值,并分析试验周期的选择对Ao的影响。
6. Ao与系统本身、综合保障和使用环境等因素都有关系的参数,因 此它是进行系统各种参数分析的有用工具。试导出以OT、TT、Ao、 TPM和每次发生故障后不能工作的时间DTF(含延误时间)等参 数与MTBF间的函数关系式。(假设预防性维修的延误时间 (ALDT)为0)。如果假设Ao=0.8,TT=90(天),每次任务40h,期 间共执行23次任务,DTF=24h,TPM=100h,求对应MTBF。
作业
1. 维修性要求包括哪些方面,列举各方面的几项常用要求? 你认为应怎样提要求(考虑哪些因素)。
2. 维修停机时间包括哪三方面?维修性设计可控的是哪部 分?其它方面让你考虑,如何解决。
3. 何为可用度?使用可用度、固有可用度、可达可用度度 表示什么含义?分析这些概念的工程意义。
4. 经初步验证,某系统Ao=0.66,但用户希望最少达到 Ao=0.75。为此需改变进行维修的方法,以便通过降低 修复维修时间TCM来提高Ao值。设(OT+ST)=168h、 TPM=5h、ALDT=22h,试求为达到Ao=0.75,TCM应 限制在多大?