各种机加工工时计算表
超级详细的机加工工时计算表格,值得收藏!
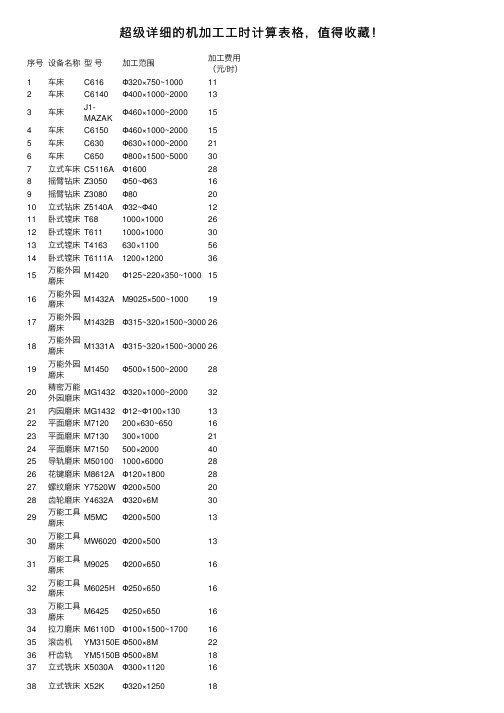
超级详细的机加⼯⼯时计算表格,值得收藏!序号设备名称型号加⼯范围加⼯费⽤(元/时)1车床C616Φ320×750~100011 2车床C6140Φ400×1000~2000133车床J1-MAZAKΦ460×1000~2000154车床C6150Φ460×1000~200015 5车床C630Φ630×1000~200021 6车床C650Φ800×1500~500030 7⽴式车床C5116AΦ160028 8摇臂钻床Z3050Φ50~Φ6316 9摇臂钻床Z3080Φ8020 10⽴式钻床Z5140AΦ32~Φ4012 11卧式镗床T681000×100026 12卧式镗床T6111000×100030 13⽴式镗床T4163630×110056 14卧式镗床T6111A1200×12003615万能外园磨床M1420Φ125~220×350~10001516万能外园磨床M1432A M9025×500~10001917万能外园磨床M1432BΦ315~320×1500~30002618万能外园磨床M1331AΦ315~320×1500~30002619万能外园磨床M1450Φ500×1500~20002820精密万能外园磨床MG1432Φ320×1000~200032 21内园磨床MG1432Φ12~Φ100×13013 22平⾯磨床M7120200×630~65016 23平⾯磨床M7130300×100021 24平⾯磨床M7150500×200040 25导轨磨床M501001000×600028 26花键磨床M8612AΦ120×180028 27螺纹磨床Y7520WΦ200×50020 28齿轮磨床Y4632AΦ320×6M3029万能⼯具磨床M5MCΦ200×5001330万能⼯具磨床MW6020Φ200×5001331万能⼯具磨床M9025Φ200×6501632万能⼯具磨床M6025HΦ250×6501633万能⼯具磨床M6425Φ250×65016 34拉⼑磨床M6110DΦ100×1500~170016 35滚齿机YM3150EΦ500×8M22 36杆齿轨YM5150BΦ500×8M18 37⽴式铣床X5030AΦ300×112016 38⽴式铣床X52KΦ320×12501838⽴式铣床X52KΦ320×12501839⽴式铣床XA5032Φ320×12501840卧式铣床X63WΦ400×16002441滑枕铣床XS5646/1Φ425×20002842⽜头刨床B665650×8001443⽜头刨床B650650×8001144液压⽜头BY60100900~100016刨床B690900~10001645液压⽜头刨床46龙门刨床B2016A900~10002847龙门刨床B2020A2000~60005048杆床B5032200~3201249拉床L614040T1550划线钳⼯Φ200×6501551装配钳⼯Φ200×6503052模具钳⼯Φ200×6503053加⼯中⼼Φ200×6508054线切割Φ200×650955焊⼑Φ200×6507机加⼯⽅法报价表格(范例)⼀般件、⼩批量时的单个计价⽅法加⼯⽅法⼩类和基本参数参数1 参数2和单位价格钻孔单个孔 L/d≤2.5 d≤25 X*d元'L=孔深,d=孔径' 25≤d<>元L/d>2.5 d≤25 X*d元(*L/d/2.5)25≤d<>元(*L/d/2.5)孔径公差<>对应基价的倍数 X倍孔距公差<>对应基价的倍数 X倍单个孔加⼯的最低价格 X元附带攻丝钢件 X*d元d=螺纹直径铸铁件 X*d元L=螺纹长度铝件加不锈钢丝套费⽤ X*d元不加丝套费⽤ X*d元铜件 X*d元批量优惠批量>200个孔且<>个孔对应基价的倍数 X倍批量>10000个孔对应基价的倍数 X倍车类加⼯光轴加⼯'L=轴长,d=轴径,D=⽑坯轴径' ⼀般精度 L/d≤10 X*D*L元 L/d>10 X*D*L元(*L/d/10)精度<0.05 l>元L/d>10 X*D*L元(*L/d/10)带锥度轴 L/d≤10 X*D*L元L/d>10 X*D*L元(*L/d/10)阶梯轴对应光轴基价的倍数 X倍⼀般精度的丝杠对应光轴基价的倍数 X倍法兰盘类零件 d≤430 X*D元d=法兰外径,D=⽑坯直径 d>430 X*D元圆螺母零件 X*D元d=圆螺母外径,D=⽑坯直径六⾓螺母零件 X*D元d=六⾓螺母外径,D=⽑坯直径轴套类零件(直径⼩于100径长⽐⼩于2) 'd<100,d>元d=轴套外径,L=轴套长度'd<100,d>2' X*D元(*d/L/2)修补轴承座(台)类零件 't<><><>元't=磨损量,d=轴承外径,B=轴承座宽度''t<2,d>40或B>25' X元(*d/40*B/25)需要上中⼼架的对应上述基价的倍数 X倍铣床加⼯⼀般键槽L=键槽长度,B=键槽宽度位置度公差7级以下的 L/B≤10 X*B元L/B>10 X*B元(*L/B/10)最低价 X元位置度公差7级和以上的对应上述基价的倍数 X倍硬度>HRC40的材料加⼯对应上述基价的倍数 X倍⼀般花键 L/d≤5 X*d元L=键槽长度,d=轴径 L/d>5 X*d元(*L/d/5)最低价 X元⼀般齿轮类Z=齿数,m=模数⼀般圆柱直齿轮 X*Z*m元斜齿轮,伞齿轮,变位齿轮对应上述基价的倍数 X倍铣⼀般平⾯每mm2 X元铣沉孔每个 X*d元d=孔径最低价 X元刨床加⼯平⾯每mm2 X元t=刨削深度磨削加⼯⼀般精度内、外圆 t=磨削深度每mm2 X元⼀般精度平⾯ t=磨削深度每mm2 X元⼀般精度成形磨 t=磨削深度每mm2 X元⾼精度、⼩粗糙度对应上述基价的倍数 X倍线切割⼀般零件S=切断⾯积每mm2 X元慢⾛丝每mm2 X元要穿丝每个穿丝孔 X元电⽕花⼀般零件S=切断⾯积每mm2 X元每处最低价 X元电焊 L=焊接长度焊条成本(各种焊条不同:碳钢、不锈钢、铸铁、有⾊⾦属等⽤)每条 X元焊缝长度每mm价格(与材料和焊缝种类有关) X*L元⽓割⼀般板件S=切割⾯积每mm2 X元等离⼦切割⼀般碳钢每mm2 X元不锈钢每mm2 X元剪板机⼀般板件S=剪切⾯积⼀般碳钢t≤8 每mm2 X元⼀般碳钢8<><>每mm2 X元t=板厚铝板t≤12 每mm2 X元铜板t<>每mm2 X元特别加急件与加班件特别加急件定义为:第⼀时间安排为某特定客户维修或制造紧急零件。
车床加工基本时间计算参考表

工时定额的组成:1.批量加工的单件加工工时=基本时间+辅助时间+布置工作地时间+休息与生理需要的时间2.单件加工时:在以上的基础上加上相应的准备时间3.单件工时定额Td:单件时间td=tj+tf+tb+tx◆ 基本时间tj: 直接改变对象尺寸、开关、相对位置、状态或材料性质所用时间;◆ 辅助时间tf: 为实现工艺过程必须进行的各种辅助动作所用时间。
如装卸工件、操作要、改变切削用量、试切和测量工件、引进及退回刀具等动作所用时间。
辅助时间的的确定方法随生产类型不同而不同。
大批大量生产时,为了使辅助时间规定得合理,须将辅助动作分解成单一动作,再分别查表求得各分解动作的时间,最后予以综合;对于中批生产则可根据以往的统计资料确定;在单件小批生产中,一般用基本时间的百分比进行估算。
基本时间和辅助时间的总和称为作业时间◆ 布置工地时间tb:作班内照管工作地所耗的时间,调整更换刀具、修整砂轮、润滑擦试机床、清理切屑等。
一般按作业时间的2%~5%估算。
◆ 休息和生理时间tx:工作班内满足生理需要所耗的时间。
一般按作业时间的2%估算。
以上四部分时间总和就是单件时间td=tj+tf+tb+tx注意:因本厂每天有30分钟的休息时间,所以休息与生理需要时间tx不需计算在内;布置工地时间tb:车工,铣工按4%计算。
所以单件时间td=tj+tf+tb 组成在成批生产中,每一批工件的开始和终了时,工人需要做以下工作:A、开始时,要熟悉工艺文件,领取毛坯、材料,领取和安装刀具和夹具,调整机床及其他工艺装备等;B、终了时,要拆下和归还工艺装备,送交成品等。
这两部分所用时间叫做准备时间tz,设有N件产品,那分摊到每一个工件上的准备时间为tz/N,将这部分时间加到单件时间上去。
成批生产的单件核算时间:th=td+tz/N大批大量生产时,每个工作地始终完成某一道固定工序,tz/N接近0,故不考虑。
th=td。
4.缩减辅助时间。
在单件时间中占的比重较大。
常用机加工工时成本计算表
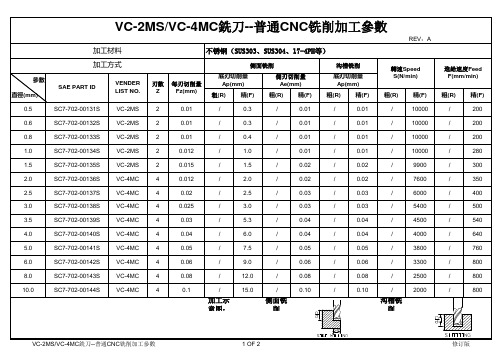
VC-2MS
2
0.015
/
1.5
/
0.02
/
0.02
/
9900
SC7-702-00136S
VC-4MC
4
0.012
/
2.0
/
0.02
/
0.02
/
7600
SC7-702-00137S
VC-4MC
4
0.02
/
2.5
/
0.03
/
0.03
/
6000
SC7-702-00138S
VC-4MC
4
0.025
/
3.0
VC-2MS/VC-4MC銑刀--普通CNC铣削加工參數
2 OF 2
0 修订版
粗(R) / / / / / / / / / / / / / /
精(F) 200 200 200 280 300 350 400 500 540 640 760 800 800 800
VC-2MS/VC-4MC銑刀--普通CNC铣削加工參數
1 OF 2
0 修订版
參數 直徑(mm)
0.5 0.6 0.8 1.0 1.5 2.0 2.5 3.0 3.5 4.0 5.0 6.0 8.0 10.0
/
10000
SC7-702-00132S
VC-2MS
2
0.01
/
0.3
/
0.01
/
0.01
/
10000
SC7-702-00133S
VC-2MS
2
0.01
/
0.4
/
0.01
/
0.01
/
机加工工时的计算

序号
设备名称
型号
加工范围
1 车床
C616
Φ320×750~1000
2 车床
C6140 Φ400×1000~2000
3 车床
J1-MAZAK Φ460×1000~2000
4 车床
C6150 Φ460×1000~2000
5 车床
C630
Φ630×1000~2000
6 车床
C650
Φ800×1500~5000
2车 床加 工类
一般 精度 光轴 加工 长径 比不 大与 10的 按加 工件 毛坯 尺寸
*0.2 收费 (最 底5 元)
长径 比大 于10 的按 一般 光轴 基价* 长径 比数 *0.15
精度 要求 在 0.05
MM 以内 的或 要求 带锥 度的 以一 般光 轴基 价*2 收取
一般 阶梯 轴 (风 机 轴, 泵 轴, 减速 器 轴, 砂轮 轴, 电机 轴, 主轴 等)
一般 镗孔 加工 按孔 直径 *0.25 收取
4带 锯加 工类
一般 圆 钢, 厚壁 管, 方钢 截 断, 按每 平方 分米 5元 计算 (最 低5 元)
一般 钢板 切 断, 分 条, 开角 按每 平方 分米 10元 (最 低10 元)
5线 切割 加工
一般 零件 按切 断面 积 (平 方毫 米) *0.00 8元 收费 。需 要穿 丝的 零件 每穿 丝孔 加价 5元
20 精密万能外园磨床 MG1432 Φ320×1000~2000
21 内园磨床
MG1432 Φ12~Φ100×130
22 平面磨床
M7120 200×630~650
23 平面磨床
M7130 300×1000
工时计算方法大全(各机床工时、各工序工时)
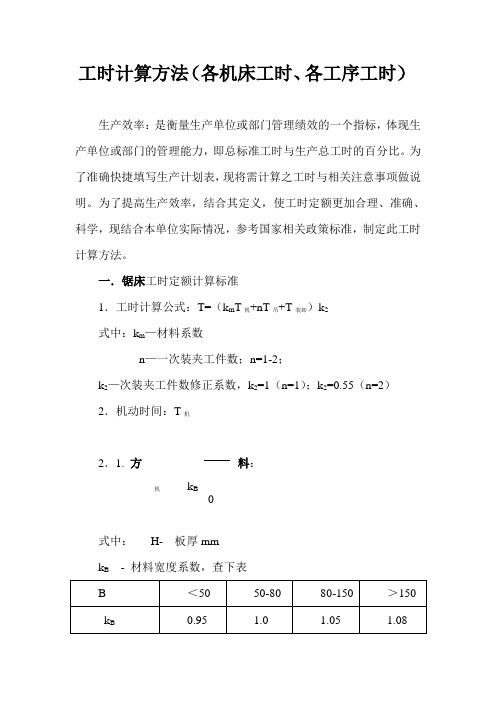
工时计算方法(各机床工时、各工序工时)生产效率:是衡量生产单位或部门管理绩效的一个指标,体现生产单位或部门的管理能力,即总标准工时与生产总工时的百分比。
为了准确快捷填写生产计划表,现将需计算之工时与相关注意事项做说明。
为了提高生产效率,结合其定义,使工时定额更加合理、准确、科学,现结合本单位实际情况,参考国家相关政策标准,制定此工时计算方法。
一.锯床工时定额计算标准1.工时计算公式:T=(k m T 机+nT 吊+T 装卸)k 2 式中:k m —材料系数n —一次装夹工件数;n=1-2;k 2—次装夹工件数修正系数,k 2=1(n=1);k 2=0.55(n=2) 2.机动时间:T 机 2.1. 方料:式中: H- 板厚mm k B - 材料宽度系数,查下表T 机=k BH22.2.棒料:式中D —棒料外径 mm2.3. 管料:式中d 0—管料内径;mm2.4..方管:式中:H—方管外形高mm ;H 0—方管内腔高mm ; B 0—方管内腔宽mm ;3.吊料时间:4.装卸料时间及其它时间:T机=D24T 机=D —d 02 2410000T 机=H—H 0*B 0208000T吊=L 1000 T装卸LD综上所述:方料:T=(0.12+n0.0519H+0.001L )k 2-0.00013 H 0*B 0 (min ) 圆料:T=(0.12+n0.0429D+0.001L )k 2-0.0001 d 02 (min ) n —一次装夹工件数;n=1-2;k 2—次装夹工件数修正系数,k 2=1(n=1);k 2=0.55(n=2)二.剪板冲压折弯工时定额计算标准1..剪板工时定额计算方法剪板单件工时定额:a —每块工时系数、见表b —剪角次数剪板工时系数表=0.12+1800840T =k *a+b a3注:准备工时按100件基数计算,每件0.2,共计200分剪板毛刺工时:T=0.3 + 处理长度/400剪板校正T校=k*T材料系数K=1~1.52.冲压每冲一次工时3..折弯工时定额计算方法折弯工时定额:t2=Σa i折弯工时定额系数表注:规格栏中,为折弯长度,a为每折一刀的工时(理论计算:每刀0.15分×折1.5=0.225+0.2=0.425→0.5)↓准备工时三.风割焊接工时定额计算标准1.风割工时公式:修磨工时含补焊工时: T 修磨 = T 风割 /22.焊接单件工时: T 焊接=T 工件装卸+T 点焊+ T 全焊 2.1 装卸工件工时:T 工件装卸=(T 01+0.2n )B式中:T 01—装卸基本工时;(取T 01=0.2); n-- 工件数 B-- 重量系数(见表)2.2. 点焊单件工时:T 点焊= T 02+0.1J+0.1N式中:T 02—点焊基本工时;J —点焊数;N —点焊时工件翻转次数;2.3. 全焊单件工时:T 全焊= T 03+0.1M+0.1N+L Σ/200+0.2NC 式中:T 03—全焊基本工时;M —焊缝段数;N —全焊时工件翻转次数;L Σ--焊缝长 NC---焊接参数调节次数注:小件装卸与点焊工时合并,统称点焊工时; 重量系数(B )T风割=风割长度×3+1.5V1、飞溅按焊接工时的二分之一计算+0.12、校正按焊接工时的二分之一计算+0.13、有辅助工帮助表卸模,从焊接工时中分取三分之一4、焊接有准备工时按每项20分钟5、点焊螺母按0.5分钟一个四.钻床工时定额1、T=kT机+ T装卸其中k—难度系数有工差要求k=1.5 有深度要求k=1.1 扩孔及攻丝k=0.82、机动时间:T机注:L/D≥8时,须另增排屑时间60%。
机加工工时计算表

平面--铣削范围(长 X 宽)mm
<50X50
<50X100
<100X100
<100X150
<100X200
TR
TC
TR
TC
TR
TC
TR
TC
TR
TC
0.3
0.5
0.7
0.9
1.2
1.7
1.9
2.5
2.5
3.3
0.2
0.3
0.5
0.7
0.8
1.2
1.2
1.7
1.6
2.3
0.2
0.3
0.3
0.5
0.5
0.9
内腔轮廓--铣削范围(长X宽)mm
时间 刀具直徑(mm)
SAE PART ID
<50X50
粗
精
1.0
SC7-702-00071S
8.3
8.3
1.5
SC7-702-00072S
3.7
3.7
2.0
SC7-702-00073S
2.1
2.2
2.5
SC7-702-00074S
1.3
1.4
3.0
SC7-702-00075S
4002銑刀--普通CNC铣削加工标准时间(min)
<50X100
TR
TC
1.1
1.5
0.7
1.0
0.5
0.8
0.3
0.7
TR:粗加 工时间/次
塑胶类(ESD225、ESD420、Derlin等)
平面--铣削范围(长 X 宽)mm
<100X100
机械零件加工工时计算公式

0.3
500.00 10
>硬质合金端铣、周精铣平面、凸台、凹槽理论工时计算<
零件参数 材料种类 材料硬度 HBS
加工特征类型
刀具、机床参数
灰铸铁 刀具直径 mm
300.0
150-225 刀具齿数
18
平面 走刀路径长度
430.00
表面粗糙度要求Ra
加工余量 mm
3.00
0.8
工件速度
5
工作台充满系数
0.25
工件要求尺寸精度
0.02
推荐磨削参数
15 0.3 0.15 0.04600 12.80
0.80 0.80
1.4
>>>>>>>高速钢半精铣平面、凸台、凹槽理论工时计算<<<<<<<
材料种类 材料硬度 HBS 加工特征类型 走刀路径长度 mm
零件、刀具参数 铝镁合金 刀具类型
1、该表 中每一种 加工方式 的理论工 时为单道 工步的切 削时间, 仅用于参 考,总的 切削时间 为所有工 步切削时 间的总和
2、总加 工成本可 以参考以 下计算公 式: C总 = 单位时 间机床的 切削成本 * 切削时 间 + 单位 时间机床 非切削成 本 * 所有 装夹、换 刀等动作 时间 + 其 它非加工 费用
车间内某 一工序的 生产率限 制了整个 车间的生 产率的提 高时,该 工序的刀 具寿命要 选得低 些;当某 工序单位 时间内所 分担到的 全厂开支 M较大 时,刀具 寿命也应 选得低些 。
大件精加 工时,为 保证至少 完成一次 走刀,避 免切削时 中途换 刀,刀具 寿命应按 零件精度 和表面粗 糙度来确 定。
机械加工工种定额、工时(车、铣、镗)切削用量参考表(工时计算)

定额工时参照表
硬质合金车刀粗车外圆端面的进给量(参考值)
硬质合金外圆车刀精车的进给量(参考值) mm/r
注:1、加
工断续表面
及有冲击的
工件时,表
内进给量应
乘系数K=
0.65~
0.75;
2、在
无外皮加工
时,表内进
给量应乘第
数K=1.1;
3、加工耐热钢及其合金时,进给量不大于
0.6mm/r; 4、加工调质钢时,乘以系数K=0.8;
6、可转位刀片的允许最大进给量不应超过其刀尖圆弧半径数值的80%。
工件材 2、表中较小 3、 5、加工淬硬钢时,进给量应减小.当钢的硬度为44~56HRC时,乘系数K=0.7;当钢的硬度为57~62HRC时,乘系数K=0.5。
7、rε=0.5mm,用于12×12以下刀杆,rε=1mm,用于30×30以下刀杆,rε=2mm,用于30×45及以上刀杆。
车不锈钢的常用切削用量
铣刀每齿进给量fz的推荐值
或手动
和三面刃削速度及进给量均应适当减
小。
- 1、下载文档前请自行甄别文档内容的完整性,平台不提供额外的编辑、内容补充、找答案等附加服务。
- 2、"仅部分预览"的文档,不可在线预览部分如存在完整性等问题,可反馈申请退款(可完整预览的文档不适用该条件!)。
- 3、如文档侵犯您的权益,请联系客服反馈,我们会尽快为您处理(人工客服工作时间:9:00-18:30)。
1200.00 0.833333333
0.2-0.3 0.15 26.0 1379
>>>>>>>往复式平面粗磨理论工时计算<<<<<<<
零件参数
砂轮、机床参数
工件材料
淬火钢 砂轮直径 mm
400
磨削形式
零件装置在夹具中或用千 分表校准
**当加工孔径较大 时,ap取大值;加 工孔径较小,且加 工精度要求较高 时,ap取小值
钢、铸钢 刀具材料 精镗 刀具类型 5 刀具直径 mm 20 推荐切削参数范围 0.6-1.2 1.00 8 509 请输入实际切削参数 3.00 0.60 1.00 600.00 0.3
刀具参数
硬质合金 镗刀块 5.00
4.00 20 1273
>>>>>>>高速钢铰刀铰孔理论工时计算<<<<<<<
零件参数
材料种类
材料性能
孔直径 mm
铰
刀具直径 mm 待加工孔深度 mm
切削深度 mm 铰削余量 mm 实际每转进给量 实际主轴转速 理论工时 min
推荐切削参数 中硬铸铁 铰削余量 mm
175HBS 每转进给量 f mm 6.00 切削速度 m/min 6.0 主轴转速 10.0
材料种类 孔直径 mm
深度 mm
钻
零件参数
不锈钢 刀具直径 mm
12.50 每转进给量 mm
20.00
切削速度 主轴转速
m/min
请输入实际切削参数
推荐切削参数范围 8 ~ 20
0.12 27 688
刀具直径
8.00
实际每转进给量
0.12
实际主轴转速
1000.00
钻
理论工时 min
**孔直径为待加工 孔直径,即最终加 工得到的孔直径
选择刀具 寿命时可 考虑如下 几点:
根据刀具 复杂程度 、制造和 磨刀成本 来选择。 复杂和精 度高的刀 具寿命应 选得比单 刃刀具高 些。
对于机夹 可转位刀 具,由于 换刀时间 短,为了 充分发挥 其切削性 能,提高 生产效 率,刀具 寿命可选 得低些, 一般取 15-30min 。
对于装刀 、换刀和 调刀比较 复杂的多 刀机床、 组合机床 与自动化 加工刀 具,刀具 寿命应选 得高些, 尤应保证 刀具可靠 性。
车间内某 一工序的 生产率限 制了整个 车间的生 产率的提 高时,该 工序的刀 具寿命要 选得低 些;当某 工序单位 时间内所 分担到的 全厂开支 M较大 时,刀具 寿命也应 选得低些 。
大件精加 工时,为 保证至少 完成一次 走刀,避 免切削时 中途换 刀,刀具 寿命应按 零件精度 和表面粗 糙度来确 定。
0.166666667
>>>>>>>镗孔理论工时计算<<<<<<<
材料种类 加工阶段 加工余量 mm 孔深度 mm
零件参数
镗
切削深度 ap mm 每转进给量 f mm
切削速度 m/min
主轴转速
刀具齿数 实际切削深度 实际每转进给量 实际主轴转速 理论工时 min *镗杆以镗套支承 时,V取中间值; 镗杆悬伸时,V取 小值
2.0
40.00 每转进给量 mm
0.3
100.00 切削速度 m/min
10
6.00 主轴转速
80
请输入实际切削参数
实际切削深度 实际每转进给量 实际主轴转速 理论工时 min
**锥面车削加工长 度为锥面母线长度
**工件直径为上道 工序所留尺寸
5.00 0.10 800.00 2.5
>>>>>>>硬质合金钻头钻孔理论工时计算<<<<<<<
刀具寿命
切削用量 三要素对 刀具寿命 影响的大 小,按顺 序为v、f 、ap。因 此,从保 证合理的 刀具寿命 出发,在 确定切削 用量时, 首先应采 用尽可能 大的背吃 刀量;然 后再选用 大的进给 量;最后 求出切削 速度。
加工表面 粗糙度
精加工 时,增大 进给量将 增大加工 表面粗糙 度值。因 此,它是 精加工时 抑制生产 率提高的 主要因素 。
1、该表 中每一种 加工方式 的理论工 时为单道 工步的切 削时间, 仅用于参 考,总的 切削时间 为所有工 步切削时 间的总和
2、总加 工成本可 以参考以 下计算公 式: C总 = 单位时 间机床的 切削成本 * 切削时 间 + 单位 时间机床 非切削成 本 * 所有 装夹、换 刀等动作 时间 + 其 它非加工 费用
3、如果 表中须输 入的前提 参数与实 际有区 别,可以 在理论工 时的基础 上乘以难 度系数, 推荐难度 系数为
1.0~3.0
>>>>>>>硬质合金车刀车外、内圆理论工时计算<<<<<<<
零件参数
材料种类 工件直径 mm 加工长度 mm 车 直径余量 mm
推荐切削参数范围
高锰钢Mn13% 切削深度 mm
0.87
K2=
1.4
切削参数 选择原 则:
切削用量 不仅是在 机床调整 前必须确 定的重要 参数,而 且其数值 合理与否 对加工质 量、加工 效率、生 产成本等 有着非常 重要的影 响。
所谓“合 理的”切 削用量是 指充分利 用刀具切 削性能和 机床动力 性能(功 率、扭 矩),在 保证质量 的前提 下,获得 高的生产 率和低的 加工成本 的切削用 量。
砂轮耐用度(T) S
900
加工面长度 mm
400.00 纵向进给量与砂轮宽度比值
0.6
加工面宽度 mm
300.00 工作台充满系数
0.25
平面磨
工件速度 m/min
6
推荐磨削参数
磨削余量 mm
0.3
磨削公差 f mm
0.15
单行程磨削深度
0.042000
理论工时 min
5.2
**时间为工作台单
行程
磨削深度修正系数 K1=
二 刀具寿 命的选择 原则
切削用量 与刀具寿 命有密切 关系。在 制定切削 用量时, 应首先选 择合理的 刀具寿 命,而合 理的刀具 寿命则应 根据优化 的目标而 定。
一般分最 高生产率 刀具寿命 和最低成 本刀具寿 命两种, 前者根据 单件工时 最少的目 标确定, 后者根据 工序成本 最低的目 标确定。
一 制订切 削用量时 考虑的因 素
切削加工 生产率
在切削加 工中,金 属切除率 与切削用 量三要素 ap、f、v 均保持线 性关系, 即其中任 一参数增 大一倍, 都可使生 产率提高 一倍。
然而由于 刀具寿命 的制约, 当任一参 数增大 时,其它 二参数必 须减小。 因此,在 制订切削 用量时, 三要素获 得最佳组 合,此时 的高生产 率才是合 理的。