神经网络的研究和应用(英文文献)
神经网络简介abstract( 英文的)
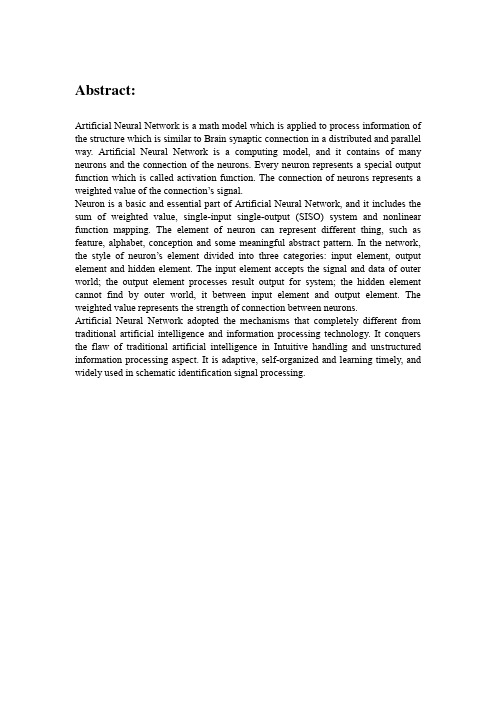
Abstract:Artificial Neural Network is a math model which is applied to process information of the structure which is similar to Brain synaptic connection in a distributed and parallel way. Artificial Neural Network is a computing model, and it contains of many neurons and the connection of the neurons. Every neuron represents a special output function which is called activation function. The connection of neurons represents a weighted value of the connection’s signal.Neuron is a basic and essential part of Artificial Neural Network, and it includes the sum of weighted value, single-input single-output (SISO) system and nonlinear function mapping. The element of neuron can represent different thing, such as feature, alphabet, conception and some meaningful abstract pattern. In the network, the style of neuron’s element divided into three categories: input element, output element and hidden element. The input element accepts the signal and data of outer world; the output element processes result output for system; the hidden element cannot find by outer world, it between input element and output element. The weighted value represents the strength of connection between neurons.Artificial Neural Network adopted the mechanisms that completely different from traditional artificial intelligence and information processing technology. It conquers the flaw of traditional artificial intelligence in Intuitive handling and unstructured information processing aspect. It is adaptive, self-organized and learning timely, and widely used in schematic identification signal processing.。
神经网络的应用论文
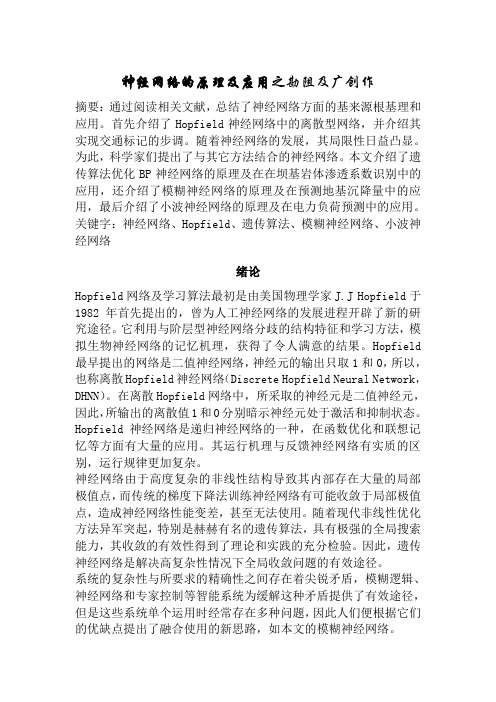
神经网络的原理及应用之勘阻及广创作摘要:通过阅读相关文献,总结了神经网络方面的基来源根基理和应用。
首先介绍了Hopfield神经网络中的离散型网络,并介绍其实现交通标记的步调。
随着神经网络的发展,其局限性日益凸显。
为此,科学家们提出了与其它方法结合的神经网络。
本文介绍了遗传算法优化BP神经网络的原理及在在坝基岩体渗透系数识别中的应用,还介绍了模糊神经网络的原理及在预测地基沉降量中的应用,最后介绍了小波神经网络的原理及在电力负荷预测中的应用。
关键字:神经网络、Hopfield、遗传算法、模糊神经网络、小波神经网络绪论Hopfield网络及学习算法最初是由美国物理学家J.J Hopfield于1982年首先提出的,曾为人工神经网络的发展进程开辟了新的研究途径。
它利用与阶层型神经网络分歧的结构特征和学习方法,模拟生物神经网络的记忆机理,获得了令人满意的结果。
Hopfield 最早提出的网络是二值神经网络,神经元的输出只取1和0,所以,也称离散Hopfield神经网络(Discrete Hopfield Neural Network,DHNN)。
在离散Hopfield网络中,所采取的神经元是二值神经元,因此,所输出的离散值1和0分别暗示神经元处于激活和抑制状态。
Hopfield神经网络是递归神经网络的一种,在函数优化和联想记忆等方面有大量的应用。
其运行机理与反馈神经网络有实质的区别,运行规律更加复杂。
神经网络由于高度复杂的非线性结构导致其内部存在大量的局部极值点,而传统的梯度下降法训练神经网络有可能收敛于局部极值点,造成神经网络性能变差,甚至无法使用。
随着现代非线性优化方法异军突起,特别是赫赫有名的遗传算法,具有极强的全局搜索能力,其收敛的有效性得到了理论和实践的充分检验。
因此,遗传神经网络是解决高复杂性情况下全局收敛问题的有效途径。
系统的复杂性与所要求的精确性之间存在着尖锐矛盾,模糊逻辑、神经网络和专家控制等智能系统为缓解这种矛盾提供了有效途径,但是这些系统单个运用时经常存在多种问题,因此人们便根据它们的优缺点提出了融合使用的新思路,如本文的模糊神经网络。
神经网络参考文献列表

神经网络参考文献[1] B. Widrow and M. A. Lehr, “30 years of adaptive neural networks: Perceptron,madaline, and backpropagation,” Proc. IEEE, vol. 78, pp. 1415-1442, Sept.1990.[2] Jian Hua Li, Anthony N. Michel, and Wolfgang Porod. “Analysis and synthesisof a class neural networks: Linear systems operating on closed hypercube,”IEEE Trans. Circuits Syst., 36(11):1405-1422, November 1989.[3] R. P. Lippmann, “An introduction to computing with neural nets,” IEEEAcoustics, Speech and Signal Processing Magazine, 2(4):4-22, April 1987.[4] S. Grossberg, E. Mingolla, and D. Todovoric,“A neural network architecture forpreattentive vision,” IEEE Trans. Biomed. Eng., 36:65-83, 1989.[5] Wang, D.and Arbib, M. A., “Complex temporal sequence learning based onshort-term memory,” Proc. IEEE, vol. 78, pp. 1536-1543, Sept. 1990.[6] Amari, S.-i., “Mathematical foundations of neurocomputing,” Proc. IEEE, vol.78, pp. 1443-1463, Sept. 1990.[7] Poggio, T. and Girosi, F., “Networks for approximation and learning,” Proc.IEEE, vol. 78, pp. 1481-1497, Sept. 1990.[8] Barnard, E., “Optimization for training neural nets,” IEEE Trans. NeuralNetwork, vol. 3, pp. 232-240, Mar. 1992.[9] Kohonen, T., “The self-organizing map,” Proc. IEEE, vol. 78, pp. 1464-1480,Sept. 1990.[10] Hagan, M.T. and Menhaj, M.B., “Training feedforward networks with theMarquardt algorithm,” IEEE Trans. Neural Network, vol. 5, pp. 989-993, Nov.1994.[11] Pei-Yih Ting and Iltis, R.A., “Diffusion network architectures forimplementation of Gibbs samplers with applications to assignment problems,”IEEE Trans. Neural Network, vol. 5, pp. 622-638, July 1994.[12] Iltis, R. A. and Ting, P.-Y., “Computing association probabilities using parallelBoltzmann machines,” IEEE Trans. Neural Network, vol. 4, pp. 221-233, Mar.1993.[13] R. Battiti, “First and second order methods for learning: Between steepestdescent and Newton's method,” Neural Computation, vol. 4, no. 2, pp. 141-166, 1992.[14] G. A. Carpenter and S. Grossberg, “A massively parallel architecture for aself-organizing neural pattern recognition machine,” Computer Vision, Graphics, and Image Processing, vol. 37, pp. 54-115, 1987.[15] C. Charalambous, “Conjugate gradient algorithm for efficient training ofartificial neural networks,” IEEE Proceeding, vol. 139, no. 3, pp. 301-310, 1992.[16] M. A. Cohen and S. Grossberg, “Absolute stability of global pattern formationand parallel memory storage by competitive neural networks,” IEEE Trans. on Systems, Man, and Cybernetics, vol. 13, no. 5, pp. 815-826, 1983.[17] J. L. Elman, “Finding structure in time,” Cognitive Science, vol. 14, pp. 179-211,1990.[18] K. Fukushima, S. Miyake and T. Ito, “Neocognitron: A neural network modelfor a mechanism of visual pattern recognition,” IEEE Trans. on Systems, Man, and Cybernetics, vol. 13, no. 5, pp. 826-834, 1983.[19] K. Fukushima, “Neocognitron: A hierarchical neural network capable of visualpattern recognition,” Neural Networks, vol. 1, pp. 119-130, 1988.[20] S. Geman and D. Geman, “Stochastic relaxation, Gibbs distributions, and theBayesian restoration of images,” IEEE Trans. on Pattern Analysis and Machine Intelligence, vol. 6, pp. 721-741, 1984.[21] S. Grossberg, “How does the brain build a cognitive code?,” PsychologicalReview, vol. 87, pp. 1-51, 1980.[22] M. Heywood and P. Noakes, “A framework for improved training of sigma-pinetworks,” IEEE Transactions of Neural Networks, vol. 6, no. 4, pp. 893-903, 1995.[23] J. J. Hopfield, “Neural networks and physical systems with emergent collectivecomputational properties,” Proceedings of the National Academy of Sciences, vol. 79, pp. 2554-2558, 1982.[24] J. J. Hopfield, “Neurons with graded response have collective computationalproperties like those of two-state neurons,” Proceedings of the National Academy of Sciences, vol. 81, pp. 3088-3092, 1984.[25] J. J. Hopfield and D. W. Tank, “'Neural computation of decisions inoptimization problems,” Biological Cybernetics, vol. 52, pp. 141-152, 1985.[26] K. M. Hornik, M. Stinchcombe and H. White, “Multilayer feedforward networksare universal approximators,” Neural Networks, vol. 2, no. 5, pp. 359-366, 1989.[27] R. A. Jacobs, “Increased rates of convergence through learning rate adaptation,”Neural Networks, vol. 1, no. 4, pp. 295-308, 1988.[28] R. A. Jacobs, M. I. Jordan, S. J. Nowlan, and G. E. Hinton, “Adaptive mixturesof local experts,” Neural Computation, vol. 3, pp. 79-87, 1991.[29] T. Kohonen, “Correlation matrix memories,” IEEE Transactions on Computers,vol. 21, pp. 353-359, 1972.[30] B. Kosko, “Bidirectional associative memories,” IEEE Transactions on Systems,Man, and Cybernetics, vol. 18, no. 1, pp. 49-60, 1988.[31] D. J. C. MacKay, “A practical bayesian framework for backproagationnetworks,” Neural Computation, vol. 4, pp. 448-472, 1992.[32] A. N. Michel and J. A. Farrell, “Associative memories via artificial neuralnetworks,” IEEE Control Systems Magazine, April, pp. 6-17, 1990.[33] A. K. Rigler, J. M. Irvine and T. P. Vogl, “Rescaling of variables inbackpropagation learning,” Neural Networks, vol. 4, no. 2, pp. 225-229, 1991. [34] D. E. Rumelhart, G. E. Hinton, and R. J. Williams, “Learning representations byback-propagating errors,” Nature, vol. 323, pp. 533-536, 1986.[35] D. F. Specht, “Probabilistic neural networks,” Neural Networks, vol. 3, no. 1, pp.109-118, 1990.[36] D. F. Specht, “A General regression neural network,” IEEE Transactions onNeural Networks, vol. 2, no. 6, pp. 568-576, 1991.[37] D. W. Tank and J. J. Hopfield, “Simple 'neural' optimization networks: An A/Dconverter, signal decision circuit and a linear programming circuit,” IEEE Transactions on Circuits and Systems, vol. 33, no. 5, pp. 533-541, 1986.[38] T. P. Vogl, J. K. Mangis, A. K. Zigler, W. T. Zink, and D. L. Alkon,“Accelerating the convergence of the backpropagation method,” Biological Cybernetics, vol. 59, pp. 256-264, Sept. 1988.[39] P. J. Werbos, “Backpropagation through time: What it is and how to do it,”Proceedings of the IEEE, vol. 78, pp. 1550-1560, Oct. 1990.[40] B. Widrow and R. Winter, “Neural nets for adaptive filtering and adaptivepattern recognition,” IEEE Computer Magazine, pp. 25-39, March 1988.[41] R. J. Williams and D. Zipser, “A learning algorithm for continually running fullyrecurrent neural networks,” Neural Computation, vol. 1, pp. 270-280, 1989. [42] A. Waibel, Tl Hanazawa, G. Hinton, K. Shikano and K. J. Lang, “Phonemerecognition using time-delay neural networks,” IEEE Transactions on Acoustics, Speech and Signal Processing, vol. 37, pp. 328-339, 1989.[43] Linske, R., “Self-organization in a perceptual network,” IEEE ComputerMagazine, vol. 21, pp. 105-117, March 1988.[44] Carpenter, G.A. and Grossberg, S., “The ART of adaptive pattern recognition bya self-organizing neural network,” IEEE Computer Magazine, vol. 21, pp. 77-88,March 1988.[45] Fukushima, K., “A neural network for visual pattern recognition,” IEEEComputer Magazine, vol. 21, pp. 65-75, March 1988.[46] Kohonen, T., “The 'neural' phonetic typewriter,” IEEE Computer Magazine, vol.21, pp. 11-22, March 1988.。
卷积神经网络机器学习外文文献翻译中英文2020
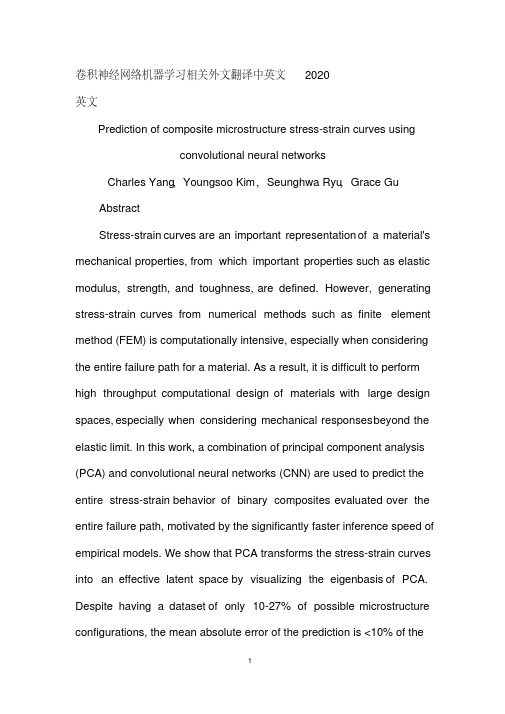
卷积神经网络机器学习相关外文翻译中英文2020英文Prediction of composite microstructure stress-strain curves usingconvolutional neural networksCharles Yang,Youngsoo Kim,Seunghwa Ryu,Grace GuAbstractStress-strain curves are an important representation of a material's mechanical properties, from which important properties such as elastic modulus, strength, and toughness, are defined. However, generating stress-strain curves from numerical methods such as finite element method (FEM) is computationally intensive, especially when considering the entire failure path for a material. As a result, it is difficult to perform high throughput computational design of materials with large design spaces, especially when considering mechanical responses beyond the elastic limit. In this work, a combination of principal component analysis (PCA) and convolutional neural networks (CNN) are used to predict the entire stress-strain behavior of binary composites evaluated over the entire failure path, motivated by the significantly faster inference speed of empirical models. We show that PCA transforms the stress-strain curves into an effective latent space by visualizing the eigenbasis of PCA. Despite having a dataset of only 10-27% of possible microstructure configurations, the mean absolute error of the prediction is <10% of therange of values in the dataset, when measuring model performance based on derived material descriptors, such as modulus, strength, and toughness. Our study demonstrates the potential to use machine learning to accelerate material design, characterization, and optimization.Keywords:Machine learning,Convolutional neural networks,Mechanical properties,Microstructure,Computational mechanics IntroductionUnderstanding the relationship between structure and property for materials is a seminal problem in material science, with significant applications for designing next-generation materials. A primary motivating example is designing composite microstructures for load-bearing applications, as composites offer advantageously high specific strength and specific toughness. Recent advancements in additive manufacturing have facilitated the fabrication of complex composite structures, and as a result, a variety of complex designs have been fabricated and tested via 3D-printing methods. While more advanced manufacturing techniques are opening up unprecedented opportunities for advanced materials and novel functionalities, identifying microstructures with desirable properties is a difficult optimization problem.One method of identifying optimal composite designs is by constructing analytical theories. For conventional particulate/fiber-reinforced composites, a variety of homogenizationtheories have been developed to predict the mechanical properties of composites as a function of volume fraction, aspect ratio, and orientation distribution of reinforcements. Because many natural composites, synthesized via self-assembly processes, have relatively periodic and regular structures, their mechanical properties can be predicted if the load transfer mechanism of a representative unit cell and the role of the self-similar hierarchical structure are understood. However, the applicability of analytical theories is limited in quantitatively predicting composite properties beyond the elastic limit in the presence of defects, because such theories rely on the concept of representative volume element (RVE), a statistical representation of material properties, whereas the strength and failure is determined by the weakest defect in the entire sample domain. Numerical modeling based on finite element methods (FEM) can complement analytical methods for predicting inelastic properties such as strength and toughness modulus (referred to as toughness, hereafter) which can only be obtained from full stress-strain curves.However, numerical schemes capable of modeling the initiation and propagation of the curvilinear cracks, such as the crack phase field model, are computationally expensive and time-consuming because a very fine mesh is required to accommodate highly concentrated stress field near crack tip and the rapid variation of damage parameter near diffusive cracksurface. Meanwhile, analytical models require significant human effort and domain expertise and fail to generalize to similar domain problems.In order to identify high-performing composites in the midst of large design spaces within realistic time-frames, we need models that can rapidly describe the mechanical properties of complex systems and be generalized easily to analogous systems. Machine learning offers the benefit of extremely fast inference times and requires only training data to learn relationships between inputs and outputs e.g., composite microstructures and their mechanical properties. Machine learning has already been applied to speed up the optimization of several different physical systems, including graphene kirigami cuts, fine-tuning spin qubit parameters, and probe microscopy tuning. Such models do not require significant human intervention or knowledge, learn relationships efficiently relative to the input design space, and can be generalized to different systems.In this paper, we utilize a combination of principal component analysis (PCA) and convolutional neural networks (CNN) to predict the entire stress-strain c urve of composite failures beyond the elastic limit. Stress-strain curves are chosen as the model's target because t hey are difficult to predict given their high dimensionality. In addition, stress-strain curves are used to derive important material descriptors such as modulus, strength, and toughness. In this sense, predicting stress-straincurves is a more general description of composites properties than any combination of scaler material descriptors. A dataset of 100,000 different composite microstructures and their corresponding stress-strain curves are used to train and evaluate model performance. Due to the high dimensionality of the stress-strain dataset, several dimensionality reduction methods are used, including PCA, featuring a blend of domain understanding and traditional machine learning, to simplify the problem without loss of generality for the model.We will first describe our modeling methodology and the parameters of our finite-element method (FEM) used to generate data. Visualizations of the learned PCA latent space are then presented, a long with model performance results.CNN implementation and trainingA convolutional neural network was trained to predict this lower dimensional representation of the stress vector. The input to the CNN was a binary matrix representing the composite design, with 0's corresponding to soft blocks and 1's corresponding to stiff blocks. PCA was implemented with the open-source Python package scikit-learn, using the default hyperparameters. CNN was implemented using Keras with a TensorFlow backend. The batch size for all experiments was set to 16 and the number of epochs to 30; the Adam optimizer was used to update the CNN weights during backpropagation.A train/test split ratio of 95:5 is used –we justify using a smaller ratio than the standard 80:20 because of a relatively large dataset. With a ratio of 95:5 and a dataset with 100,000 instances, the test set size still has enough data points, roughly several thousands, for its results to generalize. Each column of the target PCA-representation was normalized to have a mean of 0 and a standard deviation of 1 to prevent instable training.Finite element method data generationFEM was used to generate training data for the CNN model. Although initially obtained training data is compute-intensive, it takes much less time to train the CNN model and even less time to make high-throughput inferences over thousands of new, randomly generated composites. The crack phase field solver was based on the hybrid formulation for the quasi-static fracture of elastic solids and implementedin the commercial FEM software ABAQUS with a user-element subroutine (UEL).Visualizing PCAIn order to better understand the role PCA plays in effectively capturing the information contained in stress-strain curves, the principal component representation of stress-strain curves is plotted in 3 dimensions. Specifically, we take the first three principal components, which have a cumulative explained variance ~85%, and plot stress-strain curves in that basis and provide several different angles from which toview the 3D plot. Each point represents a stress-strain curve in the PCA latent space and is colored based on the associated modulus value. it seems that the PCA is able to spread out the curves in the latent space based on modulus values, which suggests that this is a useful latent space for CNN to make predictions in.CNN model design and performanceOur CNN was a fully convolutional neural network i.e. the only dense layer was the output layer. All convolution layers used 16 filters with a stride of 1, with a LeakyReLU activation followed by BatchNormalization. The first 3 Conv blocks did not have 2D MaxPooling, followed by 9 conv blocks which did have a 2D MaxPooling layer, placed after the BatchNormalization layer. A GlobalAveragePooling was used to reduce the dimensionality of the output tensor from the sequential convolution blocks and the final output layer was a Dense layer with 15 nodes, where each node corresponded to a principal component. In total, our model had 26,319 trainable weights.Our architecture was motivated by the recent development and convergence onto fully-convolutional architectures for traditional computer vision applications, where convolutions are empirically observed to be more efficient and stable for learning as opposed to dense layers. In addition, in our previous work, we had shown that CNN's werea capable architecture for learning to predict mechanical properties of 2Dcomposites [30]. The convolution operation is an intuitively good fit forpredicting crack propagation because it is a local operation, allowing it toimplicitly featurize and learn the local spatial effects of crack propagation.After applying PCA transformation to reduce the dimensionality ofthe target variable, CNN is used to predict the PCA representation of thestress-strain curve of a given binary composite design. After training theCNN on a training set, its ability to generalize to composite designs it hasnot seen is evaluated by comparing its predictions on an unseen test set.However, a natural question that emerges i s how to evaluate a model's performance at predicting stress-strain curves in a real-world engineeringcontext. While simple scaler metrics such as mean squared error (MSE)and mean absolute error (MAE) generalize easily to vector targets, it isnot clear how to interpret these aggregate summaries of performance. It isdifficult to use such metrics to ask questions such as “Is this modeand “On average, how poorly will aenough to use in the real world” given prediction be incorrect relative to some given specification”. Although being able to predict stress-strain curves is an importantapplication of FEM and a highly desirable property for any machinelearning model to learn, it does not easily lend itself to interpretation. Specifically, there is no simple quantitative way to define whether two-world units.stress-s train curves are “close” or “similar” with real Given that stress-strain curves are oftentimes intermediary representations of a composite property that are used to derive more meaningful descriptors such as modulus, strength, and toughness, we decided to evaluate the model in an analogous fashion. The CNN prediction in the PCA latent space representation is transformed back to a stress-strain curve using PCA, and used to derive the predicted modulus, strength, and toughness of the composite. The predicted material descriptors are then compared with the actual material descriptors. In this way, MSE and MAE now have clearly interpretable units and meanings. The average performance of the model with respect to the error between the actual and predicted material descriptor values derived from stress-strain curves are presented in Table. The MAE for material descriptors provides an easily interpretable metric of model performance and can easily be used in any design specification to provide confidence estimates of a model prediction. When comparing the mean absolute error (MAE) to the range of values taken on by the distribution of material descriptors, we can see that the MAE is relatively small compared to the range. The MAE compared to the range is <10% for all material descriptors. Relatively tight confidence intervals on the error indicate that this model architecture is stable, the model performance is not heavily dependent on initialization, and that our results are robust to differenttrain-test splits of the data.Future workFuture work includes combining empirical models with optimization algorithms, such as gradient-based methods, to identify composite designs that yield complementary mechanical properties. The ability of a trained empirical model to make high-throughput predictions over designs it has never seen before allows for large parameter space optimization that would be computationally infeasible for FEM. In addition, we plan to explore different visualizations of empirical models-box” of such models. Applying machine in an effort to “open up the blacklearning to finite-element methods is a rapidly growing field with the potential to discover novel next-generation materials tailored for a variety of applications. We also note that the proposed method can be readily applied to predict other physical properties represented in a similar vectorized format, such as electron/phonon density of states, and sound/light absorption spectrum.ConclusionIn conclusion, we applied PCA and CNN to rapidly and accurately predict the stress-strain curves of composites beyond the elastic limit. In doing so, several novel methodological approaches were developed, including using the derived material descriptors from the stress-strain curves as interpretable metrics for model performance and dimensionalityreduction techniques to stress-strain curves. This method has the potential to enable composite design with respect to mechanical response beyond the elastic limit, which was previously computationally infeasible, and can generalize easily to related problems outside of microstructural design for enhancing mechanical properties.中文基于卷积神经网络的复合材料微结构应力-应变曲线预测查尔斯,吉姆,瑞恩,格瑞斯摘要应力-应变曲线是材料机械性能的重要代表,从中可以定义重要的性能,例如弹性模量,强度和韧性。
(完整版)人工神经网络在认知科学的研究中的应用状况毕业设计开题报告外文翻译
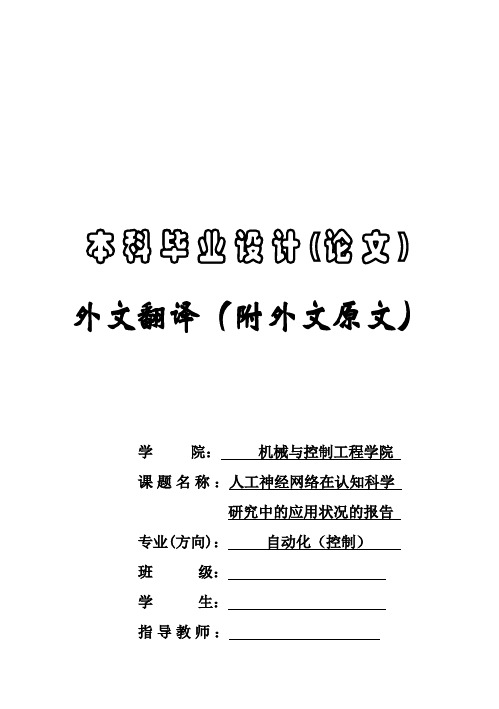
本科毕业设计(论文) 外文翻译(附外文原文)学院:机械与控制工程学院课题名称:人工神经网络在认知科学研究中的应用状况的报告专业(方向):自动化(控制)班级:学生:指导教师:日期:水下运载工具模糊逻辑控制器的简单设计方法K. Ishaque n, S.S.Abdullah,S.M.Ayob,Z.Salam(Faculty of Electrical Engineering, Universiti Teknologi Malaysia, UTM 81310, Skudai, Johor Bahru, Malaysia )摘要:模糊逻辑控制器(FLC)的性能是由其推理规则决定的。
在大多数情况下,FLC 会使用很多算法,以使其控制功能的精确性得到增强。
不过运行大型的算法需要很多的计算时间,这使得安装使用的FLC必须有快速和高效的性能。
本文描述一种水下运载工具模糊逻辑控制器的简单设计方法(FLC),水下运载工具也被称为深度下潜救援运载工具(DSRV)。
这一方法使控制器成为单输入模糊逻辑控制器(SIFLC),其省略了普通模糊逻辑控制器中将双输入FLC(CFLC)转变成单输入FLC的步骤。
SIFLC使推理法则得到简化,主要是简化了控制参数的转化过程。
控制器是在MATLAB/SIMULINK程序平台上使用航海系统模拟器(MSS)来模拟状况的,其以此达到简化的目的。
在仿真中,波动的干扰提交到DSRV中。
在SIFLC上显示出相同输入系统的Mamdani和Sugeno类型的相同反应,而且SIFLC只需要非常小的转换。
在两个量级间,他的执行时间是少于CIFLC的。
关键词:模糊逻辑控制器;距离符号法;单输入模糊逻辑控制;水下运载工具电子工程系,teknologi malaysia大学,UTM81310,Skudai,johor bahru,malaysia 1引言无人水下运载工具是一个自动的,像水下机器人设备一样能完成水下任务(例如搜索和营救操作,考察,监视,检查,维修和保养)的设备。
神经元网络的研究与应用

神经元网络的研究与应用神经元网络(neural network)也被称为神经网络,是指一种模拟人脑神经元和神经元之间相互作用的计算模型,同时也是一种机器学习技术,被广泛应用于人工智能领域中。
神经元网络能够通过大量的数据训练,对复杂问题进行分类、预测和优化等任务。
一、神经元网络的基本结构神经元网络的基本结构由许多神经元构成,这些神经元之间通过连接形成了神经元网络。
而这些神经元网络的连接方式可以是前向连接、反馈连接、自适应连接等多种形式。
每个神经元接收多个输入信号并将它们求和,然后通过激活函数(如sigmoid函数、ReLU函数等)来计算自己的输出信号。
这个输出信号又连接到其他的神经元中,形成了一个多层的神经元网络。
二、神经元网络在机器学习中的应用神经元网络在机器学习中的应用非常广泛,常见的应用包括但不限于以下领域:1. 图像分类神经元网络可以进行图像分类和目标识别等任务。
比如,卷积神经网络(Convolutional Neural Network,CNN)可以提取图像中的特征,将图像分为不同的类别。
2. 语音识别神经元网络可以对人类说话的语音进行识别,将语音转换成文字(Speech-to-Text)或语音需要表达的意思(Natural Language Processing,NLP)。
3. 自动驾驶神经元网络可以对路况进行分析,捕捉场景中的交通标志、车辆、行人等,并做出自动驾驶的决策。
4. 金融预测神经元网络可以预测股票的价格走势、货币的涨跌等,帮助投资人进行投资决策。
三、神经元网络的发展历程神经元网络的研究自20世纪50年代开始。
早期的神经元网络主要包括感知器(Perceptron)和自适应线性元件(Adaline)。
这些神经元网络被用来解决二分类问题和线性回归问题。
到了20世纪80年代,随着BP算法(Back Propagation Algorithm)的引入,多层神经元网络的训练变得可行。
BP算法基于误差反向传递的原理,通过反向传播误差来调整每个神经元之间的权重,从而使神经元网络产生更好的分类效果。
神经网络 论文

神经网络论文以下是一些关于神经网络的重要论文:1. "A Computational Approach to Edge Detection",作者:John Canny,论文发表于1986年,提出了一种基于神经网络的边缘检测算法,被广泛应用于计算机视觉领域。
2. "Backpropagation Applied to Handwritten Zip Code Recognition",作者:Yann LeCun et al.,论文发表于1990年,引入了反向传播算法在手写数字识别中的应用,为图像识别领域开创了先河。
3. "Gradient-Based Learning Applied to Document Recognition",作者:Yann LeCun et al.,论文发表于1998年,介绍了LeNet-5,一个用于手写数字和字符识别的深度卷积神经网络。
4. "ImageNet Classification with Deep Convolutional Neural Networks",作者:Alex Krizhevsky et al.,论文发表于2012年,提出了深度卷积神经网络模型(AlexNet),在ImageNet图像识别竞赛中取得了重大突破。
5. "Deep Residual Learning for Image Recognition",作者:Kaiming He et al.,论文发表于2015年,提出了深度残差网络(ResNet),通过引入残差连接解决了深度神经网络训练中的梯度消失和梯度爆炸问题。
6. "Generative Adversarial Networks",作者:Ian Goodfellow etal.,论文发表于2014年,引入了生成对抗网络(GAN),这是一种通过博弈论思想训练生成模型和判别模型的框架,广泛应用于图像生成和增强现实等领域。
纺织专业 人工神经网络 中英文 外文 资料 文献 原文和翻译

纺织专业人工神经网络中英文外文资料文献原文和翻译Textile Research Journal ArticleUse of Artificial Neural Networks for Determining the LevelingAction Point at the Auto-leveling Draw FrameAssad Farooq1and Chokri CherifInstitute of Textile and Clothing Technology, TechnischeUniversität Dresden. Dresden, GermanyAbstractArtificial neural networks with their ability of learning from data have been successfully applied in the textile industry. The leveling action point is one of the important auto-leveling parameters of the drawing frame and strongly influences the quality of the manufactured yarn. This paper reports a method of predicting the leveling actionpoint using artificial neural networks. Various leveling action point affecting variables were selected as inputs for training the artificial neural networks with the aim to optimize the auto-leveling by limiting the leveling action point search range. The Levenberg Marquardtalgorithm is incorporated into the back-propagation to accelerate the training and Bayesian regularization is applied to improve the generalization of the networks. The results obtained are quite promising. Key words: artificial neural networks, auto-lev-eling, draw frame, leveling action point。
- 1、下载文档前请自行甄别文档内容的完整性,平台不提供额外的编辑、内容补充、找答案等附加服务。
- 2、"仅部分预览"的文档,不可在线预览部分如存在完整性等问题,可反馈申请退款(可完整预览的文档不适用该条件!)。
- 3、如文档侵犯您的权益,请联系客服反馈,我们会尽快为您处理(人工客服工作时间:9:00-18:30)。
network is shown as follows:
x1
w11 w12
y1
v11 v12
o1
x2
y2
o2
# xn1n1
y3
m# w2m m
wn1m
ym
#n v1n2 2
v3n2
on2
vmn2
Figure 1 The standard structure of a typical three-layer feed-forward network
1462
III. IMPROVEMENT OF THE STANDARD BP NEURAL NETWORK ALGORITHM
The convergence rate of the standard BP algorithm is slow, and the iterations of the standard BP algorithm are much, they all have negative influences on the rapidity of the control system. In this paper, improvement has been made to the learning rate of the standard BP algorithm to accelerate the training speed of the neural network.
From formula (1), the learning rate η influences the
weight adjustment value ǻW(n), and then influences the convergence rate of the network. If the learning rate η is too
small, the convergence rate will become very slow; If the learning rate η is too big, the excessive weight adjustment
will cause the convergence process oscillates around the minimum point. In order to solve the problem, the momentum term is added behind the formula (1):
Yan Li
School of Automation Northwestern Polytechnical
University Xi’an,China liyan@
Kairui Zhao
School of Automation Northwestern Polytechnical
University Xi’an,China zhaokairui@
II. STUCTURE AND ALGORITHM OF THE STANDARD BP NEURAL NETWORK
A. Structure of the BP neural network
The standard structure of a typical three-layer feed-forward
For the standard BP algorithm, the formula to calculate the weight adjustment is as follows:
ΔW ( n)
=
−η
∂E
∂W (n)
(1)
In formula (1), η represents the learning rate; ǻW(n)
Research and Application on Improved BP Neural Network Algorithm
Rong Xie
School of Automation Northwestern Polytechnical
University Xi’an,China xierong2005@
In order to accelerate the convergence speed of the neural networks, the weight adjustment formula needs to be further improved.
Although the BP neural network has mature theory and wide application, it still has many problems, such as the convergence rate is slow, the iterations are much, and the realtime performance is not so good. It is necessary to improve the standard BP neural network algorithm to solve there problems and achieve optimal performance.
Xinmin Wang
School of Automation Northwestern Polytechnical
University Xi’an,China wxmin@
Abstract—As the iterations are much, and the adjustment speed is slow, the improvements are made to the standard BP neural network algorithm. The momentum term of the weight adjustment rule is improved, make the weight adjustment speed more quicker and the weight adjustment process more smoother. The simulation of a concrete example shows that the iterations of the improved BP neural network algorithm can be calculated and compared. Finally, choosing a certain type of airplane as the controlled object, the improved BP neural network algorithm is used to design the control law for control command tracking, the simulation results show that the improved BP neural network algorithm can realize quicker convergence rate and better tracking accuracy.
E
=
¦ Ek
=
¦ ¦ 1
2
ei2k
ε
(r) p,k
(r
=
0,1,
2)
E < Emax
ωk ← ωk−1 +ηΔωk v j ← v j−1 +ηΔv j
Figure 2 Flow chart of the standard BP neural network algorithm
978-1-4244-5046-6/10/$26.00 c 2010 IEEE
According to the different types of the neuron connections, the neural networks can be divided into several types. This paper studies feed-forward neural network, as the feed-forward neural network using the error back propagation function in the weight training process, it is also known as back propagation neural network, or BP network for short [2,3]. BP neural network is a core part of the feed-forward neural network, which can realize a special non-linear transformation, transform the input space to the output space.
represents the weight adjustment value of the nth iterations; E(n) represents the error of the nth iterations; W(n) represents the connection weight of the nth iterations.
Keywords— improved BP neural networ˗ weight adjustment˗ learning rate˗ convergence rate˗ momentum term
I. INTRODUCTION
Artificial neural network (ANN) is developed under the basis of researching on complex biological neural networks. The human brain is constituted by about 1011 highly interconnected units, these units called neurons, and each neuron has about 104 connections[1]. Imitating the biological neurons, neurons can be expressed mathematically, the concept of artificial neural network is introduced, and the types can be defined by the different interconnection of neurons. It is an important area of the intelligent control by using the artificial neural network.