传动轴总成及零件设计
传动轴设计及应用解读

• 准等速万向节:是指输入轴和输出轴以近似等速传递运动 的万向节。双联式万向节、凸块式万向节和三销轴式万向 节等为准等速万向节。主要用于转向驱动桥。
• 等速万向节:等速万向节是指输入轴和输出轴以等速传递 运动的万向节。球笼式万向节和球叉式万向节等为等速万 向节。主要用于轿车和驱动桥。 • 挠性万向节:挠性万向节依靠其中弹性零件的弹性变形来 保证在相交两轴间传动时不发生干涉。它能减小传动系的 扭转振动、动载荷和噪声,结构简单,使用中不需润滑, 一般用于两轴间夹角不大和很小轴向位移的万向传动场合。
传动轴的动平衡
• 传动轴总成不平衡是传动系弯曲振动的一个激 励源,当高速旋转时,将产生明显的振动和噪 声。所以传动轴装配后必须100%进行动平衡 检验,并在传动轴两端焊平衡片校正不平衡量, 其剩余不平衡量不应低于GB 9293中规定的G40 平衡品质等级。 • 影响传动轴动平衡品质的因素: 1、万向节十字轴的轴向间隙; 2、传动轴滑动花键副中的间隙; 3、传动轴总成两端连接处定心精度; 4、高速回转时传动轴的弹性变形。
传动轴额定载荷的确定
• • 传动轴的额定载荷是根据车型的配置参数计算出来的。先按发动机最大扭矩 计算,再按车轮的最大附着力计算,取二者中的小值作为额定扭矩。 1、按发动机最大扭矩计算: Mg=Memax×ik1×ip1/n 式中 Mg—按发动机最大扭矩计算时传动轴承受的扭矩,N.m Memax—发动机最大扭矩,N.m ik1 —变速箱一档速比 ip1 —分动箱低档速比 n —使用分动器低档时的驱动轴数目 2、按车轮最大附着力计算: Mφmax=G×rk×ψ/io 式中 Mφmax—按附着力计算时传动轴承受的扭矩,N.m G—满载时驱动轴上的载荷,N rk —车轮的滚动半径,m ψ —轮胎与地面的附着系数(在良好的沥青路面上取0.8) io —减速器速比
传动轴的设计及校核

第一章轻型货车原始数据及设计要求发动机的输出扭矩:最大扭矩285.0N·m/2000r/min;轴距:3300mm;变速器传动比: 五挡1 ,一挡7.31,轮距:前轮1440毫米,后轮1395毫米,载重量2500千克设计要求:第二章万向传动轴的结构特点及基本要求万向传动轴一般是由万向节、传动轴和中间支承组成。
主要用于在工作过程中相对位置不节组成。
伸缩套能自动调节变速器与驱动桥之间距离的变化。
万向节是保证变速器输出轴与驱动桥输入轴两轴线夹角的变化,并实现两轴的等角速传动。
一般万向节由十字轴、十字轴承和凸缘叉等组成。
传动轴是一个高转速、少支承的旋转体,因断改变的两根轴间传递转矩和旋转运动。
重型载货汽车根据驱动形式的不同选择不同型式的传动轴。
一般来讲4×2驱动形式的汽车仅有一根主传动轴。
6×4驱动形式的汽车有中间传动轴、主传动轴和中、后桥传动轴。
6×6驱动形式的汽车不仅有中间传动轴、主传动轴和中、后桥传动轴,而且还有前桥驱动传动轴。
在长轴距车辆的中间传动轴一般设有传动轴中间支承.它是由支承架、轴承和橡胶支承组成。
传动轴是由轴管、伸缩套和万向此它的动平衡是至关重要的。
一般传动轴在出厂前都要进行动平衡试验,并在平衡机上进行了调整。
因此,一组传动轴是配套出厂的,在使用中就应特别注意。
图 2-1 万向传动装置的工作原理及功用图 2-2 变速器与驱动桥之间的万向传动装置基本要求:1.保证所连接的两根轴相对位置在预计范围内变动时,能可靠地传递动力。
2.保证所连接两轴尽可能等速运转。
3.由于万向节夹角而产生的附加载荷、振动和噪声应在允许范围内。
4.传动效率高,使用寿命长,结构简单,制造方便,维修容易等第三章轻型货车万向传动轴结构分析及选型由于货车轴距不算太长,且载重量2.5吨属轻型货车,所以不选中间支承,只选用一根主传动轴,货车发动机一般为前置后驱,由于悬架不断变形,变速器或分动器输出轴轴线之间的相对位置经常变化,根据货车的总体布置要求,将离合器与变速器、变速器与分动器之间拉开一段距离,考虑到它们之间很难保证轴与轴同心及车架的变形,所以采用十字轴万向传动轴,为了避免运动干涉,在传动轴中设有由滑动叉和花键轴组成的伸缩节,以实现传动轴长度的变化。
传动轴基本知识

传动轴基本知识(图)一、传动轴总成简介传动轴总成图传动轴,英文PROPELLER(DRIVING)SHAFT。
在不同轴心的两轴间甚至在工作过程中相对位置不断变化的两轴间传递动力。
传动轴按其重要部件万向节的不同,可有不同的分类。
如果按万向节在扭转的方向是否有明显的弹性可分为刚性万向节传动轴和挠性万向节传动轴。
前者是靠零件的铰链式联接传递动力的,后者则靠弹性零件传递动力,并具有缓冲减振作用。
刚性万向节又可分为不等速万向节(如十字轴式万向节)、准等速万向节(如双联式万向节、三销轴式万向节)和等速万向节(如球笼式万向节、球叉式万向节)。
等速与不等速,是指从动轴在随着主动轴转动时,两者的转动角速率是否相等而言的,当然,主动轴和从动轴的平均转速是相等的。
主、从动轴的角速度在两轴之间的夹角变动时仍然相等的万向节,称为等速万向节或等角速万向节。
它们主要用于转向驱动桥、断开式驱动桥等的车轮传动装置中,主要用于轿车中的动力传递。
当轿车为后轮驱动时,常采用十字轴式万向节传动轴,对部分高档轿车,也有采用等速球头的;当轿车为前轮驱动时,则常采用等速万向节,等速万向节也是一种传动轴,只是称谓不同而已。
在发动机前置后轮驱动(或全轮驱动)的汽车上,由于汽车在运动过程中悬架变形,驱动轴主减速器输入轴与变速器(或分动箱)输出轴间经常有相对运动,此外,为有效避开某些机构或装置(无法实现直线传递),必须有一种装置来实现动力的正常传递,于是就出现了万向节传动。
万向节传动必须具备以下特点:a、保证所连接两轴的相对位置在预计范围内变动时,能可靠地传递动力;b、保证所连接两轴能均匀运转。
由于万向节夹角而产生的附加载荷、振动和噪声应在允许范围内;c、传动效率要高,使用寿命长,结构简单,制造方便,维修容易。
对汽车而言,由于一个十字轴万向节的输出轴相对于输入轴(有一定的夹角)是不等速旋转的,为此必须采用双万向节(或多万向节)传动,并把同传动轴相连的两个万向节叉布置在同一平面,且使两万向节的夹角相等。
金工实习-传动轴设计
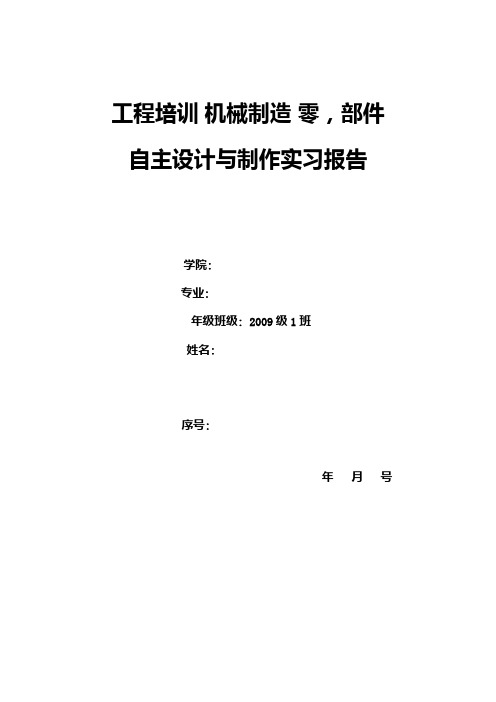
工程培训机械制造零,部件自主设计与制作实习报告学院:专业:年级班级: 2009级1班姓名:序号:年月号毛坯:ф65×270毛坯制造方法:零件材料为45钢.考虑到零件材料的综合性能及材料成本和加工成本,保证零件工作的可靠,采用锻造。
加工工艺流程卡:实习总结:光阴似箭,为期三周的金工实习转眼间结束了。
为期不长的“金工实习”课落下了帷幕。
在这三周的时间里面,每天过的都是那么的充实,因为每天都是按固定的时间上课,我们就直接称“上班”这就让我们对真实生产中的工作有了更加贴切的称呼和体验。
经过老师的经验讲解和自己的动手操作,让我们获得了机械制造的基础知识,了解了机械制造的一般操作,提高了自己的操作技能和动手能力,而且加强了理论联系实际的锻炼,提高了工程实践能力,培养了工程素质。
以下是一些心得体会。
一安全知识生产首要问题是安全问题,其次才是效率的问题。
在实习的第一天老师就给我门上了安全知识教育课,讲了一些不安全操作的事例,了解了各个工种都要注意的安全问题,比如不能在操作时嬉戏打闹、长头发要盘起来,不能穿拖鞋等等。
在各个工种里面还有更多的安全要求,钳工允许戴手套但车工的就一定不能戴手套,焊接的还要戴面罩…在未发生安全事故前,许多人对安全教育不重视,认为太烦琐,太枯燥。
一旦发生了事故,事后诸葛亮就很多。
我们在车间里,听老师讲解有关工业安全方面的知识,我才明白工业安全的重要性,工业安全知识是工业高层管理人员和开发人员的必备知识,对于草拟或一个企业的安全条例,减少工业污染,防火防爆等方面来说是非常重要的知识,如果不掌握的话,不但会被人斥为无知,有时还会发生重大事故。
所以安全总是第一位的,我们深深牢记于心,做起事来认真,严肃。
这些知识在整个实习过程中都运用到了。
也是因为我们有了这些知识才使我们安全地学习了很多课本上没有的东西,保证了实习的顺利结束。
二专业名词的认识在实习工程中,我门还接触了很多陌生的专业名词。
传动轴设计[整理版]
![传动轴设计[整理版]](https://img.taocdn.com/s3/m/65cff7c627fff705cc1755270722192e44365855.png)
传动轴设计1概述在汽车传动轴系或其它系统中,为了实现一些轴线相交或相对置经常变化的转轴之间的动力传递,必须采用万向传动装置。
万向传动装置一般由万向节和传动轴组成,当距离较远时,还需要中间支承。
在汽车行业中把连接发动机与前、后轴的万向传动装置简称传动轴。
传动轴设计应能满足所要传递的扭矩与转速。
现轻型载货汽车多采用不等速万向节传动轴。
2传动轴设计2.1传动轴万向节、花键、轴管型式的选择根据整车提供发动机的最高转速、最大扭矩及变速箱提供的一档速比,及由后轴负荷车轮附着力,计算得扭矩,由两者比较得出的最小扭矩来确定传动轴的万向节、花键、轴管型式。
a按最大附着力计算传动轴的额定负荷公式:Mψmax=G·r k·ψ/i oG满载时驱动轴上的负荷r k车轮的滚动半径ψ车轮与地面的附着系数i o主减速器速比b按发动机最大扭矩计算传动轴的额定负荷公式:Mψmax =M·i k1·i p/nM 发动机最大扭矩i k1变速器一档速比i p 分动器低档速比n 使用分动器时的驱动轴数按《汽车传动轴总成台架试验方法》中贯定选取以上二者较小值为额定负荷。
考虑到出现最大附着力时的工况是紧急制动工况此时的载荷转移系数为μ因此实际可利用最大附着力矩:M ψmaxo = M max ·μ传动轴的试验扭矩:由汽车设计丛书《传动轴和万向节》中得知:一般总成的检查扭矩为设计扭矩的1.5-2.0倍。
传动轴设计中轴管与万向节的设计扭矩也应选取1.5-2.0倍的计算扭矩,以满足整车使用中的冲击载荷。
轴管扭转应力公式:τ=16000DM π(D 4-d 4)<[τ] =120N/ mm2D 轴管直径; d 轴管内径;M 变速箱输出最大扭矩;花键轴的扭转应力:τ=16000M πD 23<[τ] =350N/ mm 2D 2花键轴花键底径;D 2=27.667mm 。
Z 花键齿数 m 花键模数M变速箱输出最大扭矩;传动轴花键齿侧的挤压应力:δ=2×TΨ×Z×m×L×Z×m在25-50N.mm2推荐范围内Ψ各齿载荷不均系数;Z花键齿数;L花键齿的最短工作长度长度;m花键模数;2.2传动轴的临界转速计算传动轴的临界转速。
花键传动轴零件加工工艺及夹具设计

花键传动轴零件加工工艺及夹具设计花键传动轴是一种机械传动零件,主要功能是在传动时,可以解决两轴间的同步问题,与普通传动方式相比,其具有传动精度高、传动效率高、安装方便等优点。
本篇文章将介绍花键传动轴零件的加工工艺及夹具设计。
一、加工工艺1. 材料选择花键传动轴通常采用45#钢材料加工而成,其硬度约在HRC28~32之间,具有较好的可加工性、焊接性和热处理性能。
2. 工艺流程首先,将原料切割成所需长度,然后进行粗车加工,形成整体形状。
接下来,边丝锥加工花键槽,并加工防止滑动的卸荷槽。
最后,进行细车、磨削和表面处理等工序。
3. 注意事项在加工过程中,需要注意以下几点:(1)精度要求高花键传动轴的加工过程中要求精度高,尤其是花键槽的加工要求较为困难,因此在加工过程中需要采用高精度的设备进行加工。
(2)刀具选择在车削车辆时需要选择合适的刀具,确保零件尺寸和形状的精度达到设计要求。
(3)热处理在花键传动轴加工完成后,需要进行热处理,以提高材料硬度和强度,从而保证零件的耐久性和使用寿命。
二、夹具设计1. 夹具种类花键传动轴的加工需要使用多种夹具,包括粗车夹具、丝锥加工夹具、细车加工夹具和磨削夹具等。
2. 夹具设计原则(1)夹紧力均匀夹具需要保证夹紧力均匀,以防止零件变形或损坏。
(2)跳动控制夹具需要设计成具有调节功能,可以控制零件的跳动,在加工中保证加工精度和质量。
(3)夹口尺寸合适夹具的夹口尺寸需要与零件的尺寸和形状相匹配,以确保零件的稳定性。
(4)易于操作夹具需要设计成易于操作和安装,方便操作人员的使用和维护。
夹具需要选择耐磨损、硬度高、稳定性好的材料制作,以提高夹具的使用寿命和加工质量。
三、总结因为花键传动轴的加工要求较高,需要采取相应的加工工艺和夹具设计,以保证零件的精度和质量。
在实际生产中,需要根据具体的需求和加工工艺,灵活运用各种加工设备和技术,提高加工效率和质量。
浅谈传动轴设计和研究

车辆工程技术121机械电子0 概述 在汽车行驶过程中,传动轴高速运转,任何外部激励都有可能引起传动轴的振动和噪声,进而影响整车的NVH。
NVH 性能指标是消费者直观感知项目之一,控制好NVH 性能的传动轴,提升驾乘舒适性,由此可见传动轴设计和研究非常重要。
1 传动轴工作原理及设计要求1.1 传动轴工作原理 在汽车行业中把连接变速器和驱动桥的万向传动装置简称传动轴。
汽车传动轴总成一般由万向节、中间支撑、滑动花键、轴管及其两端的花键和万向节叉组成,常见结构示意图如图1所示。
汽车传动轴总成主要用于车辆行驶过程中,在相对位置不断改变的两个零部件间传递扭矩和旋转运动,其本身的长度和万向夹角在一定范围内不断变化。
图11.2 传动轴设计要求 (1)保证所连接的两根轴相对位置在预计范围内变动时,能可靠地传递动力。
(2)传动轴设计应能满足所要传递的扭矩与转速,保证所连接两轴尽可能等速运转。
(3)传动轴的长度和夹角及它们的变化范围,由汽车总布置设计决定。
设计时应保证在传动轴长度处在最大值时,花键套与花键轴有足够的配合长度,而在长度处于最小时,两者不顶死。
传动轴夹角大小会影响万向节十字轴和滚动轴承的寿命、万向传动效率和十字轴的不均匀性。
由于万向节夹角而产生的附加载荷、振动和噪声应在允许范围内。
(4)传动效率高,使用寿命长,结构简单,制造方便,维修容易等。
2 传动轴设计 (1)传动轴扭矩的选用,根据整车提供发动机的最高转速、最大扭矩和变速箱提供的一档速比、后轴负荷车轮附着力,通过理论公式计算得出。
(2)传动轴长度的确定。
1)多根传动轴传动时各传动轴长度的确定。
多根传动轴传动设计原则,与驱动桥分动器相连的传动轴为长度可变化的伸缩传动轴,其余传动轴为中间传动轴。
中间传动轴与变速器输出轴或中间传递轴之间夹角不能大于3°;伸缩传动轴两端的夹角,满载状态时不能大于5°,特殊情况最大不能大于8°。
设计过程中,在传动轴最高转速小于0.7倍传动临界转速前提下,尽可能选用较长的伸缩传动轴,以减小伸缩传动轴夹角。
传动轴布置及校核方法

传动轴布置及校核方法传动轴是机械传动系统中常用的一种零件,主要用于将发动机的动力传递给机械设备。
它是由两个或多个轮毂和中间的轴段组成。
传动轴的布置和校核是确保传动系统正常运转的重要环节。
本文将介绍传动轴布置的基本原则和校核方法。
1.直线布置:传动轴的布置尽量直线,轴段尽量缩短。
直线布置能减小传动轴的弯曲和振动,提高传动效率和传动精度。
同时,采用直线布置还能节省空间,简化传动系统结构。
2.曲线布置:若传动轴无法直线布置(例如传动装置之间相隔较远),可以采用曲线布置。
曲线布置需要考虑轴段的弯曲和转角对传动轴的影响,避免过大的转角和弯曲造成传动轴的过分弯曲和疲劳。
传动轴的校核方法主要包括静力学校核和疲劳校核。
1.静力学校核:静力学校核是指通过计算、分析传动轴在工作负载下的受力情况,来判断传动轴是否具有足够的强度。
静力学校核时需要考虑传动轴的受力情况、材料强度、线性和非线性变形等因素。
常用的静力学校核方法包括弹性力学计算、有限元分析等。
2.疲劳校核:疲劳校核是指通过计算、分析传动轴在长时间循环工作下的疲劳寿命,来判断传动轴是否具有足够的疲劳强度。
疲劳校核时需要考虑传动轴的应力集中情况、材料的疲劳性能、循环载荷和工作条件等因素。
常用的疲劳校核方法包括应力异常修正法、极限剩余应力法、伤害积累理论法等。
在传动轴的校核过程中,需要根据具体的传动方式、传动功率、传动比等因素来选择适当的校核方法和工具。
同时,还需要根据传动轴的实际情况和工作条件,合理选择材料、尺寸和制造工艺,以确保传动轴具有足够的强度、刚度和疲劳寿命。
总之,传动轴布置和校核是机械传动系统设计中重要的环节。
通过合理布置和科学校核,可以保证传动系统的正常运行和稳定工作。
- 1、下载文档前请自行甄别文档内容的完整性,平台不提供额外的编辑、内容补充、找答案等附加服务。
- 2、"仅部分预览"的文档,不可在线预览部分如存在完整性等问题,可反馈申请退款(可完整预览的文档不适用该条件!)。
- 3、如文档侵犯您的权益,请联系客服反馈,我们会尽快为您处理(人工客服工作时间:9:00-18:30)。
传动轴总成及零件设计一、设计目标:1、产品的安全性:保证所设计的产品对使用者及车辆是安全的、可靠的。
即在传动轴整个使用寿命周期内,不发生断裂、脱落等可导致人体或车辆伤害的故障。
2、用户满意的性能:a,传递扭矩的能力。
b,运动范围:转速、万向节摆角、长度伸缩量、回转空间。
c,用户满意的使用寿命:一般要求十字轴及滚针轴承寿命十万公里以上、滑动花键及叉子等其他主要零件,二十万公里以上。
国外先进厂家已达到整个总成使用寿命三十万公里以上。
d,便于使用保养,连接方式便于装拆,密封、润滑可靠,使用成本低。
e,制造成本低,性价比高。
3、满足一般设计要求:标准化、系统化、通用化。
对于设计者耒说,保证产品的安全性是头等重要的,设计不允许存在安全隐患。
用户需要的必要性能也应充分满足。
二、失效模式和安全性:传动轴可能发生断裂、脱落、扭曲、磨损等失效,有些失效方式可危及人体及车辆安全,如断裂、脱落;有些失效方式不会危及人体和車辆,如花键磨损、十字轴磨损。
我们设计的传动轴应不发生危及人体及車辆安全的故障。
因此,传动轴总成及零件的设计失效模式,应该是:万向节或花键付磨损达到限值而失效。
在使用期内不允许发生冲击断裂、疲劳断裂等一类故障。
即使在非常规冲击下,也只允许轴管扭曲,其他零件不应断裂。
根据设计失效模式,提出一个传动轴强度设计原则---按疲劳强度设计,即零件危险奌应力值应小于疲劳强度,并且按屈服强度计祘的安全系数应不小于离合器后备系数。
但是,零件疲劳强度是一个受材料、热处理、零件结构、零件表面状态等多个因素影响的复杂问题,很难具体确定它的数值。
经过传动轴专业人员在设计、使用、改进传动轴中的长期积累,形成了一套传动轴零件强度设计的安全系数,或应力限值的经验数据,可供设计时参考。
最终还是要通过试验验证,证明已达到要求的疲劳寿命才能定型。
必须强调说明,不同吨位、不同用途的汽車传动轴,安全系数或应力限值是不同的。
所以,最好的办法是把设计的传动轴零件应力值,与公认是成功的同类型、相同用途的传动轴零件应力值作比较,使处于同一应力水平上。
同样,定型也必须通过试验验证,确保达到要求的疲劳寿命。
三、总成及主要零件的设计计祘:传动轴的设计计祘,应采用《汽車设计》中介绍的公式,这是传动轴行业通用的,只有采用相同的计祘公式,其结果才具有可比性。
不要用一般机械设计手册中介绍的公式。
1、总成临界转速:N=0.12*10^9*((D^2+d^2)^1/2)/L^2其中:D:轴管外径;d:轴管内径;L:两万向节中心距。
安全系数:k=临界转速N / 传动轴最高工作转速n k>1.5只有制造精度高,动平衡精度高的传动轴,才允许采用低的安全系数。
临界转速安全系数过小,可引发灾难性事故,务必谨慎。
在上述公式中,将传动轴简化为轴管进行临界转速的计祘,存在误差。
经过激振法测试传动轴临界转速验证,证明公式计祘出耒的数值偏大。
用旋转法测量包含了传动轴的几何位置偏差,更符合实际,其数值可能比激振法测得的还要小一些。
在使用过程中,由于磨损间隙增大,临界转速会变小。
过小的临界转速安全系数,不能保证传动轴平稳工作。
2、十字轴:a)危险截面弯曲应力:b=32D*p*h/(π(D^4-d^4))其中:D:十字轴轴径;P=M最大/2R:轴颈上作用力;h:作用力到危险截面距离;d:轴颈内油孔直径;R:十字轴作用力半径;π:圆周率。
其数值大小决定十字轴的疲劳断裂寿命。
应使十字轴的疲劳寿命大于使用寿命,保证安全性。
危险截面弯曲应力许用值,轻中型汽车十字轴,小于等于350Par;重型小于等于300Par;超重型小于等于250Par;特重型小于等于200Par。
b)滚针与轴颈的挤压应力:b=272((1/D+1/d针)*4.6P/(i针*L针))^1/2其中:D:十字轴轴径;d针:滚针轴径;P:十字轴轴颈上作用力;i针:滚针根数;L针:滾针有效长度。
挤压应力决定十字轴表面的接触疲劳。
应力太高会产生早期压痕及剝落,引起接触疲劳而过早失效。
耳孔同轴度,轴承支承刚度等都能影响应力分布的均匀性,对接触疲劳影响很大。
带凸度的滾针轴承可以减少耳孔同轴度、耳孔受载荷变形的敏感性,改善应力分布,显著提高万向节使用寿命。
3、滑动花键轴:a)花键轴扭转应力:T=16M最大*10^3/(π*d^3)其中:π:圆周率;d:花键齿根圆直径。
它决定花键轴的扭转疲劳寿命,其应力值应小于它的扭转疲劳强度,保证安全性。
扭转应力允许值小于等于240Par,安全系数2左右。
b)花键挤压应力:b=8M最大*10^3/((Dl^2-D2^2)i*L)其中:Dl:外花键大径;D2:内花键小径;i:花键齿数;L:花键啮合长度。
它对花键磨合影响较大。
应力太大引起拉毛擦伤等早期故障,使用寿命显著降低。
花键磨合性能还和花键表面粗糙度、硬度金相是否匹配、润滑是否充分、密封是否可靠有关。
挤压应力是一个基本条件。
许用值应小于等于20Par。
有些资料介绍十字轴轴颈及花键的平均使用压力计算,作为使用寿命的一个基本条件。
在计算中使用了传动轴平均使用扭矩的概念。
由于使用寿命影响因素很多,计算的意义不大。
4、轴管:扭转应力:丅=l6M最大*D*10^3/(π(D^4-d^4))其中:D:轴管外径;d:轴管内径;π:圆周率。
它决定了轴管受冲击扭矩的能力和扭转疲劳寿命,应使应力值小于扭转疲劳强度值,并且能承受离合器的打滑扭矩而无扭曲变形。
一般许用值为100par。
5、叉子的强度计祘比较复杂,其危险截面一般受弯、扭、拉压的复合作用,而且结构形状变化大,局部应力集中不可避免。
借助电脑进行有限元分析,控制高应力奌的应力值在疲劳强度以下,就可以保证零件的安全性。
一般调质钢叉子,疲劳强度为300Par左右。
6、突缘连接螺栓:a)螺栓与孔有较大间隙:依靠螺栓拉力使突缘面紧密贴合,可产生的摩擦力矩,就是它能传递的最大扭矩。
传递M最大所需要的螺栓拉力P=2M最大*10^3/(D*f*n)其中:D:螺栓孔分布圆直径;n:螺栓数;f:摩擦系数,干的钢表面约为0.14至0.20。
螺栓强度条件:P=(πd^2)/4*[b]其中:π:圆周率;d:螺纹底径;[b]:螺栓许用拉应力,不同强度等级的螺栓是不同的。
产生上述螺栓拉力所需的拧紧力矩M=P*d中/2*tg(a+p)其中:d中:螺纹中径;a:螺纹平均升角;p:螺栓付摩擦角,等于arctg(f/cos(e/2)),e为螺纹角;P:单个螺栓所受拉力。
b)配合螺栓:无间隙或小间隙配合,螺栓受剪切来传递扭矩。
传递M最大时螺栓所受的切向力丅=2M最大*10^3/(D*k*n)其中:D:螺栓孔分布圆直径;k:螺栓工作不均衡系数,一般可取0.75;n:螺栓数。
螺栓强度条件:丅=(πd**2)/4*[t]其中:π:圆周率;d:螺杆直径;[t]螺栓许用剪切应力,不同强度等级的螺栓是不同的。
c)突缘连接面间有键或键齿,靠键或键齿受剪切传递扭矩,按键或键齿进行计祘就可以了。
传动轴连接螺栓计祘,一般要求同时满足拉力条件和切力条件,以保证可靠连接。
7、滚针轴承:许用压力[P]=790*z*L*d/(n轴承^(1/3))其中:Z:滾针数;L:滚针有效长度;d:滚针直径;n轴承:滚针轴承当量转速,等于发动机额定转速/一档速比*万向节角的正切。
应满足[P]>M最大/(R*cosa)。
国外,传动轴的寿命设计主要是万向节的寿命计算,有一套标准的算法。
四、传动轴总成及零件的结构类型:经过一个多世纪的发展和使用,十字轴万向传动轴已成为非常成熟的产品,它的结构已定型,主要考虑生产条件和使用维修的便利性。
1、开式传动轴得到普遍应用,闭式传动轴已不多见,但仍在一些汽車中使用,如太脱拉汽車传动轴。
2、管式传动轴因为刚性高,重量轻,具有较高的临界转速,有利于运转平稳。
3、內滑式传动轴、外滑式传动轴有各自的优势。
4、突缘连接较为普遍,但端叉连接也不少。
端叉的形式有多种,如短套管叉,叉形突缘;用翼形轴承的,用普通滚针轴承由U形螺栓、轴承盖连接的,用端盖轴承的,式样较多。
端叉连接方式减少了传动轴系的零件,减轻了重量,降低了制造成本,有些结构装拆很方便,有一定的比较优势。
5、万向节轴承的定位方式,有內卡式、外卡式、端盖或压板式、注塑等。
要攷虑万向节轴向间隙的调整,间隙在0.01至0.06为好。
间隙过大,十字轴窜动,动平衡不稳定;过盈或零间隙会引起十字轴端面烧蚀,使万向节寿命显著降低。
6、中间支承的设计应攷虑它的频率特性。
具有低频特性的中间支承有利于降低振动和噪声,以20几Hz为好。
7、对形状复杂的零件,如叉类零件,应进行结构优化,满足强度、刚度条件下,减轻重量,避免局部应力集中。
五、传动轴的使用寿命:传动轴的使用寿命取决于万向节寿命和花键付寿命。
设计上主要是控制挤压应力,防止早期失效。
但使用寿命受工况、维护保养条件影响很大。
设计仅提供一定使用寿命的必要条件。
六、试验验证要奌:1、安全性、可靠性验证:a)总成静扭试验:失效形式应是轴管严重扭曲。
轴管屈服扭矩应大于离合器打滑时的传动轴扭矩。
b)零件静扭试验:十字轴断裂扭矩应为最大工作扭矩的3.5倍以上,屈服扭矩应为最大工作扭矩的3倍以上。
花键轴屈服扭矩应2倍以上。
叉子零件失效扭矩都必需在3.5倍以上。
C)扭转疲劳试验:根据使用里程寿命要求不同,疲劳寿命也不同。
如十字轴使用里程以十万公里为目标,疲劳寿命几十万次(有限寿命)可以了,花键付、叉子、轴管,使用里程以二十万公里以上为目标,疲劳寿命应达二百万次(无限寿命)d)总成冲击试验:失效形式是轴管扭曲,其他零件无损坏。
安全性可靠性的理想状态,就是疲劳寿命大于使用寿命,并能经受工作中的正常冲击,在非常冲击载荷下只出现轴管扭曲,而无零件断裂。
2、运动特性验证:a)万向节摆角a:应在2a圆锥角内转动无干涉。
b)滑动花键伸缩量。
C) 总成最大迴转直径。
d)其他要求,如运动阻力(矩)、游动间隙等。
3、万向节、花键付磨损试验:不出现压印、剝落、拉伤、烧蚀等早期故障。
试验数据反映了产品设计、制造、材料热处理等诸多因素的综合影响,是更可信的产品信息。
但是任何一个产品特性,都具有隋机性、分散性,遵守数理统计规律。
特别是与安全性有关的特性,最需要关注的是它的下限值,就是只有千分之一的可能性,也是一类事故。
所以必须通过不太大的样本试验,获得多亇数据,通过科学的方法进行数据处理,求出期望值和方差,才有可能估计出下限值,正确判断产品的安全性。
这是需要不断完善,长期努力的。
2002.3.27.。