铝合金铸造出现气孔的原因分析与解决办法
铝压铸件产生气孔的可能原因精选版

铝压铸件产生气孔的可能原因Document serial number【KKGB-LBS98YT-BS8CB-BSUT-BST108】铝压铸件产生气孔的可能原因(供参考)一.人的因素:1.脱模剂是否喷得太多因脱模济发气量大,用量过多时,浇注前未燃尽,使挥发气体被包在铸件表层。
所以在同一条件下,某些工人操作时会产生较多的气孔的原因之一。
选用发气量小的脱模济,用量薄而均匀,燃净后合模。
2未经常清理溢流槽和排气道3开模是否过早是否对模具进行了预热各部位是否慢慢均匀升温,使型腔、型芯表面温度为150℃~200℃。
4刚开始模温低时生产的产品有无隔离5如果无预热装置时是否使用铝合金料慢速推入型腔预热或用其它方法加热6是否取干净的铝液,有无将氧化层注入压室7倒料时,是否将勺子靠近压室注入口,避免飞溅、氧化或卷入空气降温等。
8金属液一倒入压室,是否即进行压射,温度有无降低了。
9冷却与开模,是否根据不同的产品选择开模时间10有无因怕铝液飞出(飞水),不敢采用正常压铸压力更不敢偿试适当增加比压。
11操作员有无严格遵守压铸工艺12有无采用定量浇注如何确定浇注量二.机(设备、模具、工装)的因素:主要是指模具质量、设备性能。
1压铸模具设计是否合理,会否导致有气孔压铸模具方面的原因:1.浇口位置的选择和导流形状是否不当,导致金属液进入型腔产生正面撞击和产生旋涡。
(降低压射速度,避免涡流包气)2.浇道形状有无设计不良3.内浇口速度有无太高,产生湍流4.排气是否不畅5.模具型腔位置是否太深6.机械加工余量是否太大穿透了表面致密层,露出皮下气孔压铸件的机械切削加工余量应取得小一些,一般在左右,既可减轻铸件重量、减少切削加工量以降低成本,又可避免皮下气孔露出。
余量最好不要大于,这样加工出来的面基本看不到气孔的,因为有硬质层的保护。
2排气孔是否被堵死,气排不出来3?冲头润滑剂是否太多,或被烧焦这也是产生气体的来源之一。
4?浇口位置和导流形状,有无金属液先封闭分型面上的排溢系统5内浇口位置是否不合理,通过内浇口后的金属立即撞击型壁、产生涡流,气体被卷入金属流中6?排气道位置不对,造成排气条件不良5?溢气道面积是否够大,是否被阻塞,位置是否位於最后充填的地方模具排气部位是否经常清理避免因脱模剂堵塞而失去排气作用。
压铸件气孔的成因和解决办法
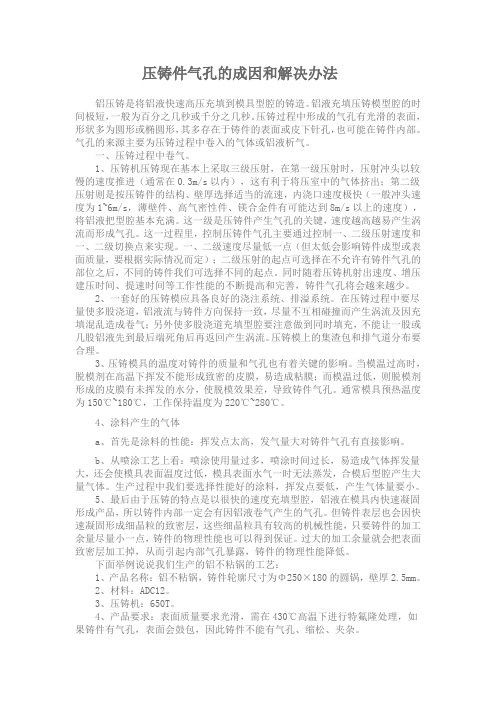
压铸件气孔的成因和解决办法铝压铸是将铝液快速高压充填到模具型腔的铸造。
铝液充填压铸模型腔的时间极短,一般为百分之几秒或千分之几秒。
压铸过程中形成的气孔有光滑的表面,形状多为圆形或椭圆形,其多存在于铸件的表面或皮下针孔,也可能在铸件内部。
气孔的来源主要为压铸过程中卷入的气体或铝液析气。
一、压铸过程中卷气。
1、压铸机压铸现在基本上采取三级压射,在第一级压射时,压射冲头以较慢的速度推进(通常在0.3m/s以内),这有利于将压室中的气体挤出;第二级压射则是按压铸件的结构、壁厚选择适当的流速,内浇口速度极快(一般冲头速度为1~6m/s,薄壁件、高气密性件、镁合金件有可能达到8m/s以上的速度),将铝液把型腔基本充满。
这一级是压铸件产生气孔的关键,速度越高越易产生涡流而形成气孔。
这一过程里,控制压铸件气孔主要通过控制一、二级压射速度和一、二级切换点来实现。
一、二级速度尽量低一点(但太低会影响铸件成型或表面质量,要根据实际情况而定);二级压射的起点可选择在不允许有铸件气孔的部位之后,不同的铸件我们可选择不同的起点。
同时随着压铸机射出速度、增压建压时间、提速时间等工作性能的不断提高和完善,铸件气孔将会越来越少。
2、一套好的压铸模应具备良好的浇注系统、排溢系统。
在压铸过程中要尽量使多股浇道,铝液流与铸件方向保持一致,尽量不互相碰撞而产生涡流及因充填混乱造成卷气;另外使多股浇道充填型腔要注意做到同时填充,不能让一股或几股铝液先到最后端死角后再返回产生涡流。
压铸模上的集渣包和排气道分布要合理。
3、压铸模具的温度对铸件的质量和气孔也有着关键的影响。
当模温过高时,脱模剂在高温下挥发不能形成致密的皮膜,易造成粘膜;而模温过低,则脱模剂形成的皮膜有未挥发的水分,使脱模效果差,导致铸件气孔。
通常模具预热温度为150℃~180℃,工作保持温度为220℃~280℃。
4、涂料产生的气体a、首先是涂料的性能:挥发点太高,发气量大对铸件气孔有直接影响。
铝合金压铸件中产生气孔的原因分析

铝合金压铸件中产生气孔的原因分析摘要:铝合金压铸件中气孔是比较常见的缺陷问题,不仅对压铸件的美观造成不良影响,也会导致压铸件质量受到影响,为此需要合理分析铝合金压铸件中气孔产生的主要原因,并采取有效的措施进行控制。
铝合金压铸件气孔产生与原材料的选择、压铸工艺的控制、压铸机选择和涂料因素等密切相关,因此需要格外重视其压铸时的原材料、压铸工艺合理控制,挑选性能优质合格的压铸机和涂料,更好的保证其压铸质量。
关键词:铝合金压铸件;气孔;原因气孔是铝合金压铸件中最常出现的缺陷问题,大多出现在铝合金压铸件的表面或者皮下针孔,也有部分气孔可能在铸件内部。
气孔对铝合金压铸件的质量具有一定负面影响,不仅影响了构件的美观,同时过多的气孔也会使其质量大打折扣,不利于铝合金压铸件在后续使用中发挥良好的作用,甚至可能导致安全问题。
因此,分析其气孔产生原因,并探讨有效的处理对策是比较重要的内容。
一、铝合金压铸件产生气孔原因1、原材料因素原材料因素是铝合金压铸件产生气体的重要因素之一。
铝合金压铸件的原材料质量和性能会在一定程度上影响其气孔产生,研究显示,铝合金压铸件的合金液在加工中很容易受到原材料自身含氢量因素的影响从而析出气体,进而导致气孔出现,影响其质量。
在铝液中有85%的气体含量为氢气,因此含氢量较高的合金锭也比较容易在加工中出现气孔问题。
原材料的气孔问题不仅受到其内部性质的影响,导致合金锭表面潮湿的水蒸气,加工回炉料脏且油污较多,以及溶剂潮湿等,也都是原材料处理阶段气孔出现的主要原因,应该结合实际情况进行客观分析[1]。
图1 铝合金压铸件气孔2、压铸过程产生气孔压铸过程产生气孔是铝合金压铸件气孔产生的主要条件。
铝合金压铸件在压铸过程中的工艺技术会在很大程度上影响到其气孔的产生,研究显示气孔的产生通常与压铸工艺的参数有关,与模具的结构也有一定关联,此外在压铸过程中由于管控不当卷入气体,也会导致气孔出现。
铝合金压铸件在压铸过程中产生的气体,多由于压室、浇注系统、型腔与大气相通,并且在压铸时金属液以高压、高速填充相关。
铝合金焊接气孔产生的原因及解决方法

铝合金焊接气孔产生的原因及解决方法以铝合金焊接气孔产生的原因及解决方法为标题,本文将从气孔的形成原因、影响因素、解决方法等方面进行探讨。
一、气孔的形成原因1. 气体溶解度:铝合金焊接过程中,焊缝区域受到高温,气体在熔化池中容易溶解,当焊接材料凝固时,溶解的气体迅速析出形成气孔。
2. 氧化物和气体:铝合金表面常存在氧化物和气体,当焊接时没有进行适当的预处理,氧化物和气体会进入焊缝区域,造成气孔的形成。
3. 杂质和污染物:铝合金焊接前,如果没有进行彻底的清洁处理,焊接材料会受到杂质和污染物的影响,从而导致气孔的产生。
4. 焊接参数不合理:焊接电流、焊接速度、焊接温度等参数设置不当,会导致焊接熔池中的气体无法充分逸出,从而形成气孔。
二、影响因素1. 铝合金成分:铝合金的成分对气孔形成有一定影响,一般来说,铝合金中硅、铁等元素的含量越高,气孔的产生越容易。
2. 焊接方法:不同的焊接方法对气孔的产生也有影响,例如手工电弧焊、氩弧焊、激光焊等,焊接过程中的温度和气体环境都不同,会影响气孔的形成。
3. 焊接设备和工艺:焊接设备的性能和焊接工艺的选择都会对气孔的产生产生影响,例如焊接电流、焊接速度、焊接电极材料等。
4. 焊接环境:焊接环境中的湿度、气氛等因素也会对气孔的产生产生一定影响,潮湿的环境和含有大量氧气的环境都会增加气孔的形成。
三、解决方法1. 优化焊接工艺:合理选择焊接方法、设备和工艺参数,根据具体的铝合金材料和焊接要求进行调整,确保焊接过程中的温度、电流和速度等参数控制在合适范围内。
2. 预处理:在焊接前对铝合金材料进行充分的清洁处理,去除氧化物和污染物,减少杂质的影响。
3. 使用惰性气体保护:在焊接过程中,使用惰性气体进行保护,如氩气,可以有效减少氧气进入焊缝区域,减少气孔的产生。
4. 合理焊接顺序:在多道焊接时,合理安排焊接顺序,避免后续焊缝的气体进入前面焊缝,造成气孔的形成。
5. 加热预热和后热处理:对于一些特殊的铝合金材料,可以通过加热预热和后热处理等方式,改善焊接过程中的温度分布,减少气孔的产生。
铝合金铸造常见缺陷与对策

铝铸件常见缺陷及整改办法铝铸件常见缺陷及整改办法1、欠铸(浇不足、轮廓不清、边角残缺):形成原因:(1)铝液流动性不强,液中含气量高,氧化皮较多。
(2)浇铸系统不良原因。
内浇口截面太小。
(3)排气条件不良原因。
排气不畅,涂料过多,模温过高导致型腔内气压高使气体不易排出。
防止办法:(1)提高铝液流动性,尤其是精炼和扒渣。
适当提高浇温和模温。
提高浇铸速度。
改进铸件结构,调整厚度余量,设辅助筋通道等。
(2)增大内浇口截面积。
(3)改善排气条件,增设液流槽和排气线,深凹型腔处开设排气塞。
使涂料薄而均匀,并待干燥后再合模。
2、裂纹:特征:毛坯被破坏或断开,形成细长裂缝,呈不规则线状,有穿透和不穿透二种,在外力作用下呈发展趋势。
冷、热裂的区别:冷裂缝处金属未被氧化,热裂缝处被氧化。
形成原因:(1)铸件结构欠合理,收缩受阻铸造圆角太小。
(2)顶出装置发生偏斜,受力不匀。
(3)模温过低或过高,严重拉伤而开裂。
(4)合金中有害元素超标,伸长率下降。
防止方法:(1)改进铸件结构,减小壁厚差,增大圆角和圆弧R,设置工艺筋使截面变化平缓。
(2)修正模具。
(3)调整模温到工作温度,去除倒斜度和不平整现象,避免拉裂。
(4)控制好铝涂成份,成其是有害元素成份。
3、冷隔:特征:液流对接或搭接处有痕迹,其交接边缘圆滑,在外力作用下有继续发展趋势。
形成原因:(1)液流流动性差。
(2)液流分股填充融合不良或流程太长。
(3)填充温充太低或排气不良。
(4)充型压力不足。
防止方法:(1)适当提高铝液温度和模具温度,检查调整合金成份。
(2)使充填充分,合理布置溢流槽。
(3)提高浇铸速度,改善排气。
(4)增大充型压力。
4、凹陷:特征:在平滑表面上出现的凹陷部分。
形成原因:(1)铸件结构不合理,在局部厚实部位产生热节。
(2)合金收缩率大。
(3)浇口截面积太小。
(4)模温太高。
防止方法:(1)改进铸件结构,壁厚尽量均匀,多用过渡性连接,厚实部位可用镶件消除热节。
铝合金缸盖皮下气孔的分析与解决

易 长 ,严 烯 ,陈俊 星 ( 柳 州五菱柳机动 力有 限公 司,广西 柳 州 5 4 5 0 0 5 )
摘要 :为探 寻重力铸造铝合金 缸盖皮下气孔缺 陷发生的原 因,利用质量分析法和模 流软件 ,结 合 现场生产 实际情 况,从人 、机 、料 、法 、环等方 面分析 了缸盖皮下气孔缺 陷的影响 因素,明 确 了模 具排气通道 不够及未设 置主动抽气装置 、砂 芯吸潮是主要影 响因素 ,提 出了针对 性的预
( L i u z h o u Wu l i n g Mo t o r s C o . , L t d . , L i u z h o u 5 4 5 0 0 5 , Gu a n g x i , C h i n a )
Ab s t r a c t :T o e x p l o r e t h e r e a s o n s f o r s u b s u r f a c e b l o wh o l e o f a l u mi n u m a l l o y c y l i n d e r h e a d b y g r a v i t y c a s t i n g . t h e q u a l i t y me t h o d a n d mo l d l f o w s o f t wa r e c o mb i n e d wi t h t h e a c t u a l p r o d u c t i o n s i ua t t i o n wa s u s e d t o a n a l y z e t h e i n lu f e n c i n g f a c t o r s f o r s u b s u r f a c e b l o wh o l e o f c y l i n d e r h e a d f r o m t h e a s p e c t s o f
铝合金焊接气孔产生的原因及解决方法
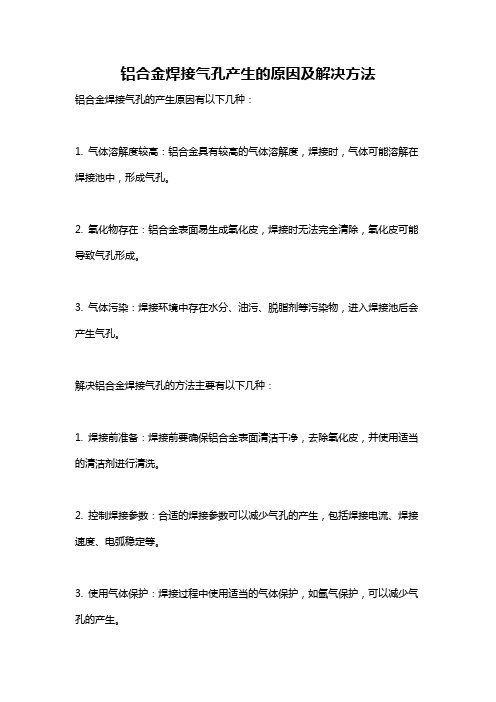
铝合金焊接气孔产生的原因及解决方法
铝合金焊接气孔的产生原因有以下几种:
1. 气体溶解度较高:铝合金具有较高的气体溶解度,焊接时,气体可能溶解在焊接池中,形成气孔。
2. 氧化物存在:铝合金表面易生成氧化皮,焊接时无法完全清除,氧化皮可能导致气孔形成。
3. 气体污染:焊接环境中存在水分、油污、脱脂剂等污染物,进入焊接池后会产生气孔。
解决铝合金焊接气孔的方法主要有以下几种:
1. 焊接前准备:焊接前要确保铝合金表面清洁干净,去除氧化皮,并使用适当的清洁剂进行清洗。
2. 控制焊接参数:合适的焊接参数可以减少气孔的产生,包括焊接电流、焊接速度、电弧稳定等。
3. 使用气体保护:焊接过程中使用适当的气体保护,如氩气保护,可以减少气孔的产生。
4. 选择合适的焊接材料:合适的焊丝和焊剂可以有效降低气孔的产生。
5. 严格控制焊接环境:避免焊接环境中存在水分、油污、脱脂剂等污染物。
总之,减少铝合金焊接气孔的关键是从焊接前的准备工作开始,包括清洁表面、选择合适的焊接参数和材料,以及控制焊接环境,保证焊接质量。
铝合金压铸件气孔产生原因及解决办法

铝合⾦压铸件⽓孔产⽣原因及解决办法 2008-12-13 13:28:51压铸件缺陷中,出现最多的是⽓孔。
⽓孔特征。
有光滑的表⾯,形状是圆形或椭圆形。
表现形式可以在铸件表⾯、或⽪下针孔、也可能在铸件内部。
(1)⽓体来源1)合⾦液析出⽓体—a与原材料有关b与熔炼⼯艺有关2)压铸过程中卷⼊⽓体—a与压铸⼯艺参数有关b与模具结构有关3)脱模剂分解产⽣⽓体—a与涂料本⾝特性有关b与喷涂⼯艺有关(2)原材料及熔炼过程产⽣⽓体分析铝液中的⽓体主要是氢,约占了⽓体总量的85%。
熔炼温度越⾼,氢在铝液中溶解度越⾼,但在固态铝中溶解度⾮常低,因此在凝固过程中,氢析出形成⽓孔。
氢的来源:1)⼤⽓中⽔蒸⽓,⾦属液从潮湿空⽓中吸氢。
2)原材料本⾝含氢量,合⾦锭表⾯潮湿,回炉料脏,油污。
3)⼯具、熔剂潮湿。
(3)压铸过程产⽣⽓体分析由于压室、浇注系统、型腔均与⼤⽓相通,⽽⾦属液是以⾼压、⾼速充填,如果不能实现有序、平稳的流动状态,⾦属液产⽣涡流,会把⽓体卷进去。
压铸⼯艺制定需考虑以下问题:1)⾦属液在浇注系统内能否⼲净、平稳地流动,不会产⽣分离和涡流。
2)有没有尖⾓区或死亡区存在3)浇注系统是否有截⾯积的变化?4)排⽓槽、溢流槽位置是否正确?是否够⼤?是否会被堵住?⽓体能否有效、顺畅排出?应⽤计算机模拟充填过程,就是为了分析以上现象,以作判断来选择合理的⼯艺参数。
(4)涂料产⽣⽓体分析涂料性能:如发⽓量⼤对铸件⽓孔率有直接影响。
喷涂⼯艺:使⽤量过多,造成⽓体挥发量⼤,冲头润滑剂太多,或被烧焦,都是⽓体的来源。
(5)解决压铸件⽓孔的办法先分析出是什么原因导致的⽓孔,再来取相应的措施。
1)⼲燥、⼲净的合⾦料。
2)控制熔炼温度,避免过热,进⾏除⽓处理。
3)合理选择压铸⼯艺参数,特别是压射速度。
调整⾼速切换起点。
4)顺序填充有利于型腔⽓体排出,直浇道和横浇道有⾜够的长度(>50mm),以利于合⾦液平稳流动和⽓体有机会排出。
- 1、下载文档前请自行甄别文档内容的完整性,平台不提供额外的编辑、内容补充、找答案等附加服务。
- 2、"仅部分预览"的文档,不可在线预览部分如存在完整性等问题,可反馈申请退款(可完整预览的文档不适用该条件!)。
- 3、如文档侵犯您的权益,请联系客服反馈,我们会尽快为您处理(人工客服工作时间:9:00-18:30)。
铝合金铸造出现气孔的原因分析与解决办法核心提示:简单来说,气孔分两类,一类是析出性气孔,即铝液在凝固过程中因气体溶解度的变化而析出,老大在这方面说的很详细;另一类就是卷入性气孔,与铝液无关,主要是铝液填充过程中因紊流包卷在产品中的空气及涂料或型腔内未干的水分。
卷入性气孔主要与浇排系统的合理性密切相关,只有涂料和水,纯属操作不当。
至于说在喷丸后出现,应该主要与高速转换点的位置关联密切。
问题1:材料ACD12铝合金压铸件在机加工或喷砂后出现较多气孔的问题,这一技术上问题困扰着我们回复:1 设备抽真空设备是什么设备啊?压铸件的气孔问题好像还没有办法解决只能通过调节压铸参数,模温和修改相关的模具温度使气孔在一个合理的等级范围2 一.人的因素:1.脱模剂是否噴得太多? 因脱模济发气量大,用量过多时,浇注前未燃尽,使挥发气体被包在铸件表层。
所以在同一条件下,某些工人操作时会产生较多的气孔的原因之一。
选用发气量小的脱模济,用量薄而均匀,燃净后合模。
2未经常清理溢流槽和排气道?3开模是否过早? 是否对模具进行了预热?各部位是否慢慢均匀升温,使型腔、型芯表面温度为150℃~200℃。
4刚开始模温低时生产的产品有无隔离?5如果无预热装置时是否使用铝合金料慢速推入型腔预热或用其它方法加热?6是否取干净的铝液,有无将氧化层注入压室? 7倒料时,是否将勺子靠近压室注入口,避免飞溅、氧化或卷入空气降温等。
8金属液一倒入压室,是否即进行压射,温度有无降低了?。
9冷却与开模,是否根据不同的产品选择开模时间?10有无因怕铝液飞出(飞水),不敢采用正常压铸压力?更不敢偿试适当增加比压。
?11操作员有无严格遵守压铸工艺?12有无采用定量浇注?如何确定浇注量?二.机(设备、模具、工装)的因素: 主要是指模具质量、设备性能。
1压铸模具设计是否合理,会否导致有气孔?压铸模具方面的原因:1.浇口位置的选择和导流形状是否不当,导致金属液进入型腔产生正面撞击和产生旋涡。
(降低压射速度,避免涡流包气)2.浇道形状有无设计不良?3.内浇口速度有无太高,产生湍流?4.排气是否不畅? 5.模具型腔位置是否太深?6.机械加工余量是否太大?穿透了表面致密层,露出皮下气孔?压铸件的机械切削加工余量应取得小一些,一般在0.5mm左右,既可减轻铸件重量、减少切削加工量以降低成本,又可避免皮下气孔露出。
余量最好不要大于0.5mm,这样加工出来的面基本看不到气孔的,因为有硬质层的保护。
2排气孔是否被堵死,气排不出来?3冲头润滑剂是否太多,或被烧焦?这也是产生气体的来源之一。
4浇口位置和导流形状,有无金属液先封闭分型面上的排溢系统?5内浇口位置是否不合理,通过内浇口后的金属立即撞击型壁、产生涡流,气体被卷入金属流中 ? 6排气道位置不对,造成排气条件不良?5溢气道面积是否够大,是否被阻塞,位置是否位於最后充填的地方? 模具排气部位是否经常清理?避免因脱模剂堵塞而失去排气作用。
6模温是否太低? 7流道转弯是否圆滑?适当加大内浇口?8有无在深腔处开设排气塞,或采用镶拼形式增加排气?9有无因压铸设计不合理,形成有难以排气的部位?10溢流口截面积总和有无小于内浇口截面积总和的60%,排渣效果差?11有无在在满足成型良好的条件下,增大内浇口厚度以降低填充速度?12有无内浇口速度过高,湍流运动过剧,金属流卷入气体严重 ?13有无内浇口截面积过小,喷射严重 ?14有无顺序填充以利于型腔气体排出,直浇道和横浇道有足够的长度?三.材料的因素:1有无做好供应商的原材料的成分控制?铁含量多少?(要求在0.7以下)2铝的纯度有无保证?3二次料(水口料)使用是否过多,并且没有做好除渣动作?4又无在生产过程中在铝液内加入过多废料渣包,浇注时连同氧化皮一起倒入?5本公司有无控制废材料的二次使用比例?如何执行?谁检查?6重要客户产品的铝液中是否可以加入废料?7试试改变新料与回炉料的比例?8炉料是否干净?四.方法的因素: 主要指压铸参数、操作工艺。
1有无根据不同的产品选择工艺参数?(压铸铝液温度630-670ºC)合理选择压铸工艺参数,特别是压射速度。
调整高速切换起点。
2有无减少脱模济含水量?有无采用发气量小的脱模剂?3合金熔炼温度是否过高?4铝液温度如何测定?温度计准确否?5有无根据产品及时调整压射速度和慢压射速度快压射速度的转换点?6有无大机器压铸小零件,压室的充满度过小?五.环境因素: 压铸环境是否空气湿度大?一般情况下,周围空气中的氢气含量并不多,但空气中如果相对湿度大,则会增加铝液中气体的溶解度,形成季节性气孔,如在雨季,由于空气湿度大,铝合金熔炼时针孔产生的现象就严重些。
当然,空气湿度大时,铝合金锭、熔炼设备、工具等也会因空气潮湿而增加表面水分的吸附量,因此更应注意采取有力预热烘干防护措施,以减少气孔的产生。
名词解释与铝压铸小资料一.名词解析:1气孔:特征--铸件表皮下,聚集气体鼓胀所形成的泡。
2针孔:通常是指铸件中小于1mm的析出性气孔,多呈圆形,不均匀分布在铸件整个断面上,特别是在铸件的厚大断面和冷却速度较小的部位。
根据铝合金析出性气孔的分布和形状特征,针孔又可以分为三类①,即:(1) 点状针孔(2) 网状针孔(3) 综合性气孔:3精炼铝合金在熔炼过程中,去除非金属夹杂物(各种固态氧化物)和气体的工序,一般称为“精炼”。
4压铸工艺上的“时间” 是填充时间、增压建压时间、持压时间及留模时间,“时间”在压铸工艺上是至关重要的。
二.小资料1铝比重:纯铝2.71g/cm3 ;压铸铝合金2.6-2.71g/cm3;合金铝熔解范围520-600℃;压铸温度范围670-710℃。
2如何防止吸气?⑴水气:它来自炉气,未经充分干燥的炉料、精炼剂、复盖剂、变质剂,未经充分干燥的炉衬、坩埚及工具上的涂料,以及残留在坩埚、工具和炉料上的含水溶剂,这些水气与铝反应为:2AL+3H2O→←AL2O3+6H 产生氢,氢以原子态进入铝液。
⑵油污来自带有油脂的炉料及工具,油脂与铝反应生成氢。
⑶炉料上带有含水腐蚀物。
减少铝合金液吸收气体,合金原材料应妥善存放,防止受潮。
使用前需充分预热烘干;对熔炼坩埚、工具都应充分预热以去除水汽后再使用。
为了清除铝合金液中的气体,所有铝合金液浇注之前都必须进行除气精炼。
3通氮精炼法(又称惰性气体除气法) 基本原理:将氮气通过一定的工艺装置进入铝液的底部,氮以气泡的形式从铝液的底部向上浮起时,由于在气泡和铝液接触的界面上存在氢的分压差,气泡内氢的分压很低,在氢分压趋于平衡的过程中,合金液中的氢就不断地进入气泡,当气泡上升到液面后,氢即随之逸入大气中,气泡在上升的过程中,同时吸附氧化渣及其固定杂质,使之一起上浮到液面。
惰性气体在使用前应将其冷凝脱水,以防止水分进入铝液。
精炼质量好,气孔必然少。
4模具温度要获得质量稳定的优质铸件,必须将模具温度严格控制在最佳的工艺范围内。
这就必须应用模具冷却加热装置,以保证模具在恒定温度范围内工作,铝合金:200-260℃。
5铝合金生产实践证明,氢是唯一能大量溶解于铝或铝合金中的气体,铝合金中溶解度最大的气体。
6铝合金精练时加入精练剂要按比例,精练剂一般是铝合金0.3%,除气时间不够;方法一:采用无缝钢管,插入铝液底部20cm处用氮气或氩气喷吹精练剂,精练喷完后,氮气或氩气再吹15-20分钟(熔炼铝合金 5吨情况下)精练后镇静10-15分钟,扒掉铝渣,用过滤网过滤浇注;7各种铸造有色金属都有吸收气体的特性,处在熔炼或保温过程中的合金液,随合金温度的升高,所吸收气体的溶解度迅速增加。
因此,除正确控制整个熔炼浇注工艺外,应尽量减少合金液在高温下保温,避免合金液过热,对极易吸合的合金,采取在覆盖剂保护下熔炼。
这样才能避免气孔、针孔的产生。
8为了减少铝合金的氧化,除选择适当的熔炼用炉外,压铸生产中应采用保温炉保温,切忌边熔化,边压铸生产,尽可能减少搅拌,保持液面氧化膜完整,避免合金液不必要的过热和尽量缩短合金在保温炉中的时间9在压铸时,压室型腔内的部分气体(约30%)不能从型腔内排出,而被卷入金属液中,在填充过程中会产生反压力返使流速下降,造成铸件冷隔、欠铸、气孔、疏松等缺陷。
为了消除由此而产生的铸件缺陷,故模具上一定要设置排气槽。
排气槽一般与溢流槽配合,设置在溢流槽后端,在有些情况下也可在型腔的部位单独布置排气槽。
10合金熔化温度越高,熔化时间和熔化后铝液保持时间越长,氢在铝液中扩散就越充分,铝液吸氢量就越大,出现针孔的几率就越大。
有人曾做试验,铝液存放时间越长,铝合金内含气量近似成比例增加。
11针孔是铝合金铸件中容易出现的且对铸件品质造成一定影响的一种铸造缺陷,氢是造成针孔的主要原因(有的资料介绍,铝液中所溶解的气体中80%-90%是氢),而氢的主要来源是水蒸气分解所产生的。
因此,铝合金在熔炼过程中造成水蒸气产生的原因,也就是直接影响针孔形成的主要因素。
12铝合金熔炼时,由于氢气溶解到铝液中需要一个过程,因此加强熔炼过程的控制,对控制铝合金吸气量是大有文章可做的。
生产实践表明,铝液吸氢是在表面进行的,它不仅与铝液表面的分压有关,还与合金熔炼温度、熔炼时间等有较大的关系。
合金熔化温度越高,熔化时间和熔化后铝液保持时间越长,氢在铝液中扩散就越充分,铝液吸氢量就越大,出现针孔的几率就越大。
有人曾做试验,铝液存放时间越长,铝合金内含气量近似成比例增加。
因此,我们在大量生产条件下,为了减少铝合金熔炼时吸收氢气,一定要严格执行铝合金熔炼工艺规程。
13金属炉料或回炉料带入的油污、有机物、盐类熔剂等与铝液反应也能生成氢。
14目前,为了消除铝合金铸件针孔,最常用的办法是在熔化过程中用氯盐和氯化物除气,用氯气、氮气除气,用真空除气,用超声波除气,过滤除气等方法。
采用氯盐和氯化物除气剂除气时,要用钟罩将除气剂压入坩埚底部100mm,沿坩埚直径1/3处(距坩埚内壁)的圆周匀速移动。
为了不使铝液大量喷溅,除气剂可分批加入,除气结束除渣。
15表面气孔、气泡可通过喷砂发现,内部气孔、气泡可通过X光透视或机械加工发现气孔、气泡在X光底片上呈黑色。
16除氢的“防、排、除” 防”:就是要防止水分及各种污物进入坩埚或熔炉中。
“排”:就是要排除铝液中的氧化夹杂和氢气,因为只有有效去除悬浮在铝液中的弥散状的夹杂物(主要是Al2O3),才能防止铝液增氢,消除去氢障碍,从而获得纯净的铝液,浇出合格的铸件。
“渣既尽,气必除”说的就是这个意思。
“溶”:就是要使铝液中的氢在凝固时能部分地或者全部地固溶在合金组织中,不致在铸件中形成气孔。
17据介绍模具最佳温度应控制在浇人温度的40%。
铝合金压铸模温度为80℃。
模具温度在这一范围内有利于获得优质高产铸件。