热轧钢管生产技术资料
热轧钢管生产工艺流程
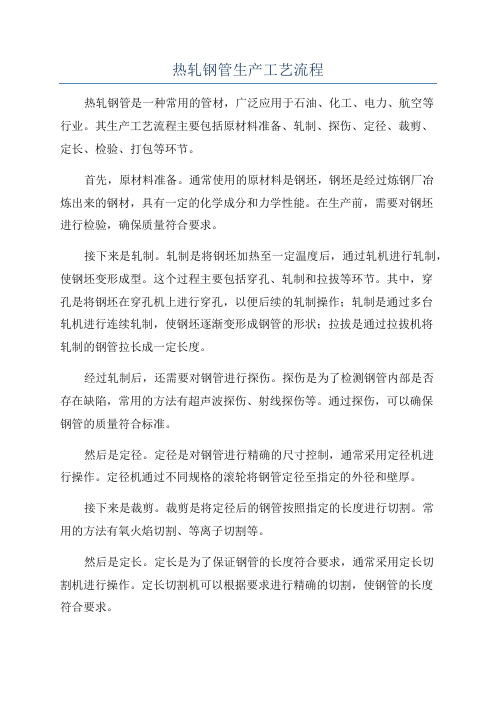
热轧钢管生产工艺流程热轧钢管是一种常用的管材,广泛应用于石油、化工、电力、航空等行业。
其生产工艺流程主要包括原材料准备、轧制、探伤、定径、裁剪、定长、检验、打包等环节。
首先,原材料准备。
通常使用的原材料是钢坯,钢坯是经过炼钢厂冶炼出来的钢材,具有一定的化学成分和力学性能。
在生产前,需要对钢坯进行检验,确保质量符合要求。
接下来是轧制。
轧制是将钢坯加热至一定温度后,通过轧机进行轧制,使钢坯变形成型。
这个过程主要包括穿孔、轧制和拉拔等环节。
其中,穿孔是将钢坯在穿孔机上进行穿孔,以便后续的轧制操作;轧制是通过多台轧机进行连续轧制,使钢坯逐渐变形成钢管的形状;拉拔是通过拉拔机将轧制的钢管拉长成一定长度。
经过轧制后,还需要对钢管进行探伤。
探伤是为了检测钢管内部是否存在缺陷,常用的方法有超声波探伤、射线探伤等。
通过探伤,可以确保钢管的质量符合标准。
然后是定径。
定径是对钢管进行精确的尺寸控制,通常采用定径机进行操作。
定径机通过不同规格的滚轮将钢管定径至指定的外径和壁厚。
接下来是裁剪。
裁剪是将定径后的钢管按照指定的长度进行切割。
常用的方法有氧火焰切割、等离子切割等。
然后是定长。
定长是为了保证钢管的长度符合要求,通常采用定长切割机进行操作。
定长切割机可以根据要求进行精确的切割,使钢管的长度符合要求。
接下来是检验。
检验是对钢管进行各项性能指标的检测,包括化学成分、力学性能、尺寸精度等。
只有通过检验合格的钢管才能进入下一环节。
最后是打包。
根据客户要求,将合格的钢管进行打包,以便运输和使用。
综上所述,热轧钢管的生产工艺流程主要包括原材料准备、轧制、探伤、定径、裁剪、定长、检验、打包等环节。
通过这些环节,可以确保热轧钢管的质量和尺寸符合要求,以满足客户的需求。
热轧无缝钢管的生产方法

50
3~1
4~
16
尔格轧 锭
辊 式 斜 尔 格 轧 ~720 70
40
~28
机组
轧穿孔 机
方
压
锭或多 力穿孔
棱锭 和 斜 轧
连 延伸
铸管坯
顶
方
压
顶
17
3~2
4~
14
管机组 坯
力 穿 孔 管机 ~1200 20
30
~16
和斜轧
延伸
圆
斜
坯
轧穿孔
热
圆
压
挤
25
2
4~
~2
挤压机 锭 、 方 力 穿 孔 压机 ~1425
热轧无缝钢管的生产方法
热轧无缝钢管的生产方法有热轧(包括挤压) 、焊接、冷加工
三中类型。
热轧无缝钢管。在生产过程中将实心管培(或钢锭)穿孔并轧制
成具有特殊规格的形状、尺寸和性能的钢管。整个过程有三个主要变
形工序:穿孔,将实心坯穿孔成空心毛管;轧管,将毛管扎成接近要
求尺管的荒管;定减径,将荒管不带芯棒轧制成具体要求的尺寸精度
~33
组
连 轧穿孔 浮动和
铸圆坯 机 桶 形 限 动
辊 或 锥 (MPM、
形辊 PQF)
连
推
限
48
3~4
6~
铸方坯 轧 穿 孔 动
~426 0
40
机
(PPM)
和延伸
机
三
圆
二
三
21
2~5
4~
8~
辊轧管 轧坯 辊 式 斜 辊 轧 管 ~250 0
40
13.5
机组
连 轧或三 机
管坯准备——《热轧无缝钢管实用技术》
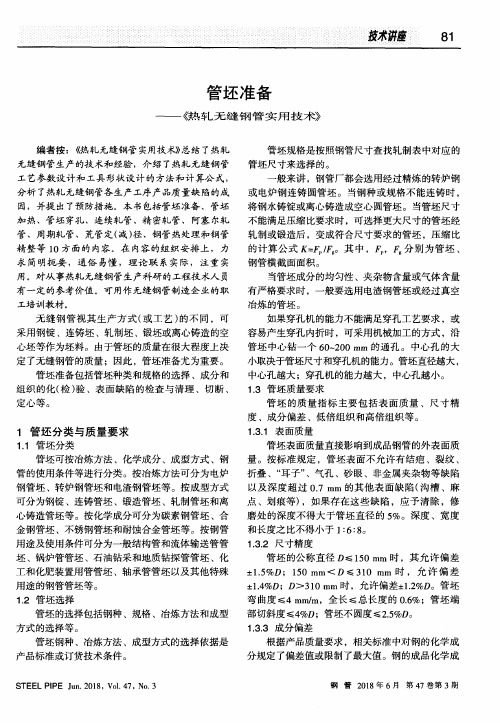
如果 穿 孔机 的能 力不 能满 足穿 孔工 艺要 求 ,或
采用钢锭 、连铸坯 、轧制坯 、锻坯或离心铸造的空 容易产生穿孔内折时 ,可采用机械加工 的方式 ,沿
心坯等作为坯料 。由于管坯的质量在很大程度上决 管 坯 中心 钻 一 个 60~200 mm 的通 孔 。 中 C,:/L的大
定 了无缝 钢 管 的质量 ;因此 ,管坯 准备 尤 为重要 。 小取决 于管坯 尺寸 和穿 孔机 的能力 。管坯直径 越大 ,
管 坯准 备包 括管 坯种 类 和规格 的选 择 、成 分 和 中心孔越 大 ;穿孔 机 的能 力越 大 ,中 C,:/L越小 。
组 织 的化 (检 )验 、表 面 缺 陷 的检 查 与 清理 、切 断 、 1.3 管 坯质 量要 求
定 心等 。
管 坯 的质 量 指 标 主 要 包 括 表 面 质 量 、尺 寸 精
用。对从事热轧无缝钢管生产科研 的工程技术人 员
当管坯成分的均匀性 、夹杂物含量或气体含量
有一定的参考价值。可用作无缝钢管制造企业的职 有 严格 要求 时 ,一般 要选 用 电渣钢 管坯 或 经过 真 空
工培训教 材 。
冶 炼 的管坯 。
无 缝 钢 管 视 其 生 产 方 式 (或 工 艺 )的不 同 ,可
一 般来讲 ,钢管厂都会选用经过精炼 的转炉钢
分析 了热轧 无缝钢 管各 生 产工序 产 品质 量缺 陷的成 或电炉钢连铸 圆管坯。当钢种或规格不能连铸时 ,
轧管工艺技术(1)——《热轧无缝钢管实用技术》

78技术讲座轧管工艺技术(I)-《热轧无缝钢管实用技术》轧管工序的主要任务是将芯棒穿入毛管内孔,在外部工具(轧辐或银模)的作用下,压缩毛管的外径和壁厚,从而获得尺寸和质量符合要求的荒管。
按轧管机的结构和金属变形方式的不同,可将轧管机分为纵轧管机和斜轧管机。
纵轧管机主要有连轧管机、顶管机(CPE)、自动轧管机、周期轧管机、挤压管机和径向锻管机等;斜轧管机主要有阿塞尔(Assel)轧管机、狄塞尔(Diescher)轧管机、精密(Accu Roll)轧管机、斜轧扩管机和行星轧管机等。
轧管机按机架数量的多少,可分为单机架轧管机和多机架轧管机。
单机架轧管机有自动轧管机、阿塞尔轧管机、狄塞尔轧管机、精密轧管机、周期轧管机、挤压管机、径向锻管机和行星轧管机等。
多机架轧管机有连轧管机和顶管机等。
目前,使用最为广泛的是限动芯棒连轧管机和精密轧管机,其次是周期轧管机、阿塞尔轧管机、挤压管机和顶管机。
行星轧管机还处在推广应用阶段。
1连轧管工艺技术1.1连轧管机概况连轧管法是将经过润滑后的长芯棒穿入毛管内孔,芯棒和毛管一同连续通过多个呈串列布置的轧车昆孔型,将毛管轧制成符合尺寸和质量要求的荒管的一种轧管方法。
早在1843年,就有人开始研究连轧管法,历经几代人对连轧管工艺、芯棒操作方式、机架数、机架形式和传动方式等方面的研究和生产实践,连轧管技术日臻成熟,连轧管机已成为当今业界首选的无缝钢管轧机。
连轧管机的最大延伸系数可达3.5-6.0,荒管最大出口速度可达5~7m/so其主要特点是生产能力大,生产效率高;所轧制的荒管长度长,产品质量好,规格范围广等。
连轧管机按机架型式不同,可分为二辘式连轧管机和三银式连轧管机;按芯棒操作方式的不同,可分为全浮动芯棒连轧管机、限动芯棒连轧管机和半浮动(也称半限动)芯棒连轧管机。
限动芯棒连轧管机的芯棒循环可分为芯棒在线回退和线外循环两种。
二辐式连轧管机由两个轧槽组成孔型,相邻机架的轧银呈90。
轧管工艺技术(Ⅴ)——《热轧无缝钢管实用技术》

热轧钢管生产工艺

热轧钢管生产工艺
热轧钢管是将钢坯通过加热至高温状态后,在轧机中进行轧制加工而成的管材。
热轧钢管生产工艺包括以下几个步骤:
1. 钢坯准备:选用适合的钢坯作为原料,一般为钢坯长条状,需要经过切割、锯断等工艺进行处理。
2. 坯料加热:将钢坯加热至适当的温度,一般为1100℃以上,以便在轧制过程中使钢坯达到塑性变形的要求。
3. 轧制加工:将加热至高温状态的钢坯送入轧机中,经过多道次的轧制,逐步压制出所需尺寸和形状的钢管。
4. 缩径:为了获得更加精确的直径尺寸,制造高精度的钢管,需要通过缩径工艺进行处理。
该工艺是在钢管的一端注入高压液体,使钢管内部受到液体的压力作用,从而缩小钢管的直径。
5. 冷却:在轧制完毕后,将钢管进行快速冷却,以提高钢管的物理性能和机械性能。
6. 修边:通过修边工艺,去除热轧钢管两侧的毛刺,使钢管的两侧光滑整齐。
7. 检测:对热轧钢管进行各项检测,包括尺寸、化学成分和力学性能等方面的检测,以确保热轧钢管的质量和安全性。
8. 成品:经过检测合格的热轧钢管,根据不同的要求,可以进
行颜色标识、喷涂和打包等工艺,最终成为成品,供应给用户使用。
总结:热轧钢管生产工艺主要包括钢坯准备、坯料加热、轧制加工、缩径、冷却、修边、检测和成品处理等过程。
每个步骤都非常关键,对于最终的钢管质量和性能有着重要影响,因此需要严格控制和管理。
热轧钢管工艺以及原理
热轧钢管工艺以及原理
热轧钢管是一种经过热轧工艺加工的钢管产品。
它具有较高的强度和耐腐蚀性,广泛应用于石油、化工、航空、建筑、机械等各个领域。
热轧钢管的生产过程主要包括钢坯预处理、热轧加工、冷却、裁切、检验、打包等多个环节。
其中热轧加工是整个生产过程的核心部分,通过高温加热、轧制、冷却等步骤,将钢坯变形成为所需的钢管形状。
热轧钢管的原理是利用高温下钢材的塑性变形性能,使钢坯逐渐变形成为钢管。
在热轧过程中,钢坯首先经过预热处理,然后进入轧机,在高温状态下被多次轧制成为所需的钢管形状。
随后,经过水冷或空冷等方式进行冷却处理,使其达到所需的物理性能要求。
总之,热轧钢管的工艺以及原理都是相对复杂的,需要通过科学的生产流程和现代化的生产设备来保证产品质量和生产效率。
- 1 -。
热轧无缝钢管生产作业指导书
热轧无缝钢管生产作业指导书
涉及到各个环节
一、拉延工序
1、拉延原料准备
无缝钢管拉延,原料应按规定的质量要求,采用热轧棒材,经质量检
查及连轧后,存放于拉延车间中,以备拉延使用。
2、拉延机械设备状况检查
在开始拉延前,应检查拉延机械设备的安全及工作状况,并进行必要
的保养添加,使其处于良好的使用状态。
3、拉延前的检查
拉延的原料应检查其质量状况,并按工作内容画出产品的组织构架图,确定各拉延参数,包括拉延速度、拉延压力、前后拉延冷却温度等,以便
保证优质生产。
4、拉延
拉延时,设有专人用计算机指令控制,把无缝钢管拉延在压辊上,拉
延过程中要控制好参数,以经济合理,保证拉延质量,生产优质钢管。
5、拉延完工
拉延完毕,产品经检查合格后,以电动卷取机将成品卷取至卷取车上,转移到冷却工序。
二、冷却工序
1、冷却设备状况检查
冷却前,应检查冷却设备的安全及运行状况,并进行必要的保养,使其处于良好的使用状况。
2、冷却管子。
钢管的热轧和热拔技术
钢管的热轧和热拔技术随着钢管的广泛应用,钢管的生产技术也不断地发展与完善。
其中,热轧和热拔两种技术备受关注,它们能够提高钢管的质量、强度和耐久性,进一步延长其使用寿命,为各行各业提供了更加可靠的产品。
那么,这两种技术分别是什么,有何不同之处呢?热轧是指将金属压制成板材或棒材的加工方法之一,其原理是在高温状态下,将未加工的钢坯经过压轧变形成为规定尺寸、截面形状的钢材。
热轧的加工温度一般在1000℃以上,使钢材表面生成一层氧化铁皮,以保护内部钢材。
热轧相对于冷轧,钢材板件强度更高,耐腐蚀性能更好,但表面质量较差,容易出现划痕、铝屑等问题。
由于热轧制造钢材所需温度较高,所以其能够制造的规格较大,大多用于制作钢板、管材、I型钢、H型钢等需求规模大的钢材。
而热拔是指把冷拔的钢材加热到一个高温,然后利用拉力将该钢材从坯料中拉出来。
热拔相对于冷拔,生产效率更高,而且因为钢材加热后变形容易,生产出的产品质量较好。
热拔制造的钢材,由于其冷加工程度较小,板材的长宽比为1:1或接近1:1,能够制造规格较小、较薄的板材,表面质量优良,广泛应用于电器、汽车、电子、机械、航空航天等领域。
此外,热拔还可以制造带有特殊形状、材料、壁厚、精度的管材、棒材,甚至可以制造出光滑无缝的钢管,提高了钢管的质量和可靠性。
总之,热轧和热拔都是一种将钢材加工成规定尺寸、截面形状的技术,两种技术各自有其独特性和适用范围。
在实际应用中,需要根据不同的需求,选择合适的钢材加工方法。
无论是热轧还是热拔,都有着其独特的生产地位和工艺流程。
钢管作为一种重要的结构材料,随着市场对于质量要求的不断提高,也将有更多的应用场景。
热轧和热拔作为两种重要的加工技术,必将在钢管生产上逐渐得到广泛推广应用。
热轧无缝钢管生产作业指导书
热轧无缝钢管生产作业指导书一、作业概述二、工艺流程1.准备工作:确认原材料、设备、工具等准备就绪。
2.加热:将钢坯加热至适宜的温度。
3.穿孔:使用穿孔机进行穿孔操作,将加热后的钢坯穿孔形成管壳。
4.轧制:通过轧制机进行连续轧制,逐步将管壳轧制成无缝钢管。
5.剪切:使用剪板机对轧制好的无缝钢管进行定长剪切。
6.修边:使用修边机对剪切好的无缝钢管进行修边操作。
7.检测:对修边好的无缝钢管进行各项质量检测。
8.包装:将检测合格的无缝钢管进行包装,便于运输。
三、设备操作1.加热炉操作:将钢坯放入加热炉中,按照设定的温度和时间进行加热操作。
2.穿孔机操作:将加热后的钢坯放入穿孔机中,按照设定的穿孔参数进行穿孔操作。
3.轧制机操作:将穿孔后的管壳放入轧制机中,按照设定的轧制参数进行连续轧制操作。
4.剪板机操作:将轧制好的无缝钢管放入剪板机中,按照设定的剪切长度进行剪切操作。
5.修边机操作:将剪切好的无缝钢管放入修边机中,按照设定的修边参数进行修边操作。
四、质量控制1.加热温度控制:根据不同材质的钢坯,设定适宜的加热温度,确保钢坯能够达到轧制要求的塑性。
2.穿孔控制:根据穿孔工艺要求,确保穿孔机的穿孔参数(如冷却剂、穿孔速度等)稳定可靠。
3.轧制参数控制:根据不同规格的无缝钢管,设定合适的轧制参数,确保成品的外径、壁厚等尺寸满足要求。
4.剪切长度控制:根据客户需求,设定剪切机的剪切参数,确保无缝钢管的长度准确。
5.修边质量控制:通过定期检查修边机刀具的状态,保证修边质量符合标准要求。
6.检测控制:对每批修边好的无缝钢管进行必要的质量检测,包括外表检查、尺寸测量、化学成分分析等。
五、安全注意事项1.操作人员应穿戴好个人防护装备,如安全帽、防护手套、防护眼镜等。
2.加热炉操作时,应保持周围环境整洁,防止杂物堆积引发火灾。
3.设备操作过程中,应注意安全距离,避免人员伤害。
4.对于异常情况,如设备故障、电路异常等,应及时报告维修部门处理。
- 1、下载文档前请自行甄别文档内容的完整性,平台不提供额外的编辑、内容补充、找答案等附加服务。
- 2、"仅部分预览"的文档,不可在线预览部分如存在完整性等问题,可反馈申请退款(可完整预览的文档不适用该条件!)。
- 3、如文档侵犯您的权益,请联系客服反馈,我们会尽快为您处理(人工客服工作时间:9:00-18:30)。
钢管生产技术要求管坯对管坯的质量要求:对管坯质量要求的严格程度与钢管品种、用途和穿孔方法有关。
对普通用途钢管的管坯质量要求可放宽些,而对重要用途钢管和高合金钢管的管坯质量要求必须严格。
应力状态条件较好或变形量较小的穿孔方法,在不影响钢管性能的条件下,对管坯表面质量和内部质量的要求可以略为低些。
应力状态条件较差的二辊斜轧穿孔,如果穿孔变形量较大,则对管坯表面质量和内部质量都要严格要求。
总之,管坯技术条件是以保证钢管质量和生产过程顺利进行为依据来确定的,并将随穿孔方法不同而有所变化,随钢管的技术条件提高而提高。
各种管坯的技术条件可查阅标准和技术协议。
例如一般自动轧管机组对管坯的要求如下:(1)管坯直径Dp偏差见表1。
管坯任何部位的弯曲度≤6mm/m,管坯端面切斜度≤6~8mm,管坯端面压扁度≤8%Dp;(2)管坯表面不得有裂纹、发纹、结疤、鳞层、折迭、非金属夹杂和缩孔的残余。
不允许有高度或深度超过0.5mm的小沟纹、麻点、耳子及高度超过1mm 的双面耳子。
管坯缺陷清理深度不超过0.05Dp;(3)管坯低倍组织:不允许有≥1级的缩孔残余、气泡、反皮、白点和裂缝。
对于一般碳素结构钢管坯,其一般疏松≤3级、中心疏松≤3级、偏析≤3级、皮下气泡≤2。
160管坯:合格范围157.5~161.5管坯检查和表面清理由于冶炼、铸锭等因素带来的缺陷,不仅在轧制过程中不能完全消除因而残留在管坯上,而且在轧坯过程中还会产生新的缺陷,所以要完全避免管坯缺陷是不可能的。
因此,须对管坯进行严格检查和彻底清理表面缺陷,这是确保钢管质量和提高成材率的重要措施。
为了暴露管坯表面缺陷,以便于检查,通常先采用酸洗、剥皮等方法去除管坯表面氧化铁皮。
现代热轧钢管车间多采用无损探伤检查(常用超声波自动探伤仪)来代替人工检查,这不但显著地提高了工作效率、改善劳动条件,而且提高了检查的质量。
表面清理的方法有砂轮磨修、火焰清理、风铲清理和机械剥皮等。
现代热轧管车间主要采用以下清理方法:(1)中、低碳钢多采用高效率的表面火焰清理法,其工艺是逐根检查或无损探伤———火焰清理———喷丸清除残渣并使表面光洁;(2)高碳钢和合金钢采用砂轮磨修;(3)重要用途钢管和高合金管坯采用整根剥皮———检查———局部磨修。
虽然剥皮清理金属消耗大、成本高,但由于能提高钢管质量和成材率,故经济上还是合算的。
由于对钢管的技术要求不断提高,国外有些工厂对全部管坯进行剥皮清理(外径车去2~6mm),以保证钢管质量。
管坯切断当管坯供应长度大于生产计划要求长度时,须设置管坯切断工序。
生产所需的管坯长度按下式计算:psh cc c c c p F K S S D L L n L ))((-∆+=π式中p L ——生产所需要的钢坯长度,mm ; p F ——管坯横断面积,mm 2c n ——每根热轧管的倍尺数(一根热轧管切成c n 根成品管); c c S D •——成品管外径与壁厚,mm ; c L ——成品管定尺长度,mm ;L ∆——切头切尾(包括切口)长度,mm 。
一般L ∆=200~500mm ,sh K ——考虑管坯加热时烧损的系数,其值与钢种、炉子型式和加热操作有关。
通常环形炉sh K =0.98~0.99,斜底连续式加热炉sh K =0.97~0.98。
对于Ф139.7×7.72×12000的钢管,切头切尾取700mm ,烧损系数取0.98。
则: Lp =〔3.14×(1×12000+700)×(139.7-7.72)×7.72〕/(0.98×3.14×80×80) ≈2144加热制度管坯加热制度内容包括加热温度jr t 、加热时间jr τ和加热速度等工艺参数的确定。
管坯加热温度的确定:加热温度是指管坯的出炉温度。
决定斜轧穿孔时管坯加热温度的基本依据是:保证毛管的穿出温度ch t 在该钢种的塑性最好的温度范围内。
碳素钢的塑性最好的温度一般是低于固相线100~150℃。
但对合金钢和高合金钢,依靠相图确定是困难的,尤其是研制新的钢号钢管时,用热扭转法或用测定临界压缩率的方法来确定各种合金钢最好塑性的温度范围,并以此范围作为该钢种的穿出温度ch t 范围。
加热温度确定确定管坯加热温度还须考虑以下因素:(1)防止产生过烧缺陷,各种钢种的过烧温度见表2。
对于过热敏感性大的合金钢,在允许范围内加热温度和穿出温度取下限,以防止出现分层和内折缺陷;(2)须考虑管坯的质量状况。
例如,压缩比小的管坯,其低倍组织较差、非金属夹杂物聚集程度大,易产生过热,其加热温度和穿出温度应比同钢种正常情况略低些。
同理a 相级别大的1Cr18Ni9Ti 钢管坯,加热温度也应略低于正常情况;(3)须考虑终轧温度对钢管组织性能的影响。
对于亚共折钢的终轧温度不应低于GS 线(Ac3);对于过共析钢的终轧温度应低于ES 线(Acm )而高于SK 线(Ac1);(4)加热温度确定时应考虑成品管的规格。
一般轧制厚壁管时轧件在轧制过程中温降较小,加热温度可稍低些。
而薄壁管加热温度应稍高些;(5)加热温度确定时要考虑到顶头材质和型式。
用钼基顶头穿制不锈钢时,由于顶头不用水冷,加热温度要比用水冷顶头穿孔时低80~90℃。
用水冷顶头穿孔时加热温度要高些。
加热速度确定管坯加热过程一般分为低温和高温两个阶段。
低温阶段是加热一些合金钢和高合金钢的关键,这是因为这些钢在低温阶段导热性差、塑性低,若采用过快的加热速度会产生加热裂纹甚至破碎。
其原因是:(1)过快的加热速度将使管坯内外温差增加,导致金属体积膨胀不一致而产生较大的应力。
显然,管坯直径愈大;导热性愈差;加热速度愈快,产生的温差应力也愈大;(2)管坯因前道工序加工不良(如冷却不当等),在管坯内部存在着残余应力,尤其是加热冷锭时钢锭内部存在较大的铸造应力,使产生裂纹的敏感性增加;(3)钢加热到300~500℃范围将出现“蓝脆”现象,显著降低钢的塑性和强度;(4)当加热到Ac 1时钢将产生相变,金属体积变化不一致而产生组织应力。
在低温阶段这些应力的迭加,将有可能破坏金属的连续性而产生加热裂纹。
因此在低温阶段应采用较低的加热速度,这虽然使加热时间增加,但由于温度低不会过多增加金属氧化和产生其它加热缺陷。
高温阶段是指金属被加热到700~800℃以上时,金属的塑性显著提高,故可采用较快的加热速度,以提高炉子的加热能力、减少氧化和脱碳等加热缺陷。
高温阶段的主要问题是如何保证管坯加热均匀、改善金属的组织结构,减少氧化、脱碳和防止过热、过烧。
其中加热温度均匀是生产工艺中很关键的问题。
管坯加热不均将带来毛管壁厚不均、内外表面缺陷以及轧制过程不能顺利进行,如出现不咬入、轧卡等生产故障。
因此,在加热阶段结束,要有一定的保温时间(均热),这对加热大直径管坯尤为重要。
加热制度加热时间:管坯加热时间可以按经验式估算:p jr jr D K •=τjr τ——加热时间,min ;K——单位管坯直径的加热时间(即加热速度),min/cm直径(边长);jrD——管坯直径(方坯以边长计),cm。
p定径前钢管再加热温度一般在900~1100℃之间。
由于定减径后出来的是热轧成品钢管,因此在确定再加热温度时要考虑到产品的组织性能和表面质量,同时还应考虑钢管的轧后冷却方式,故各种产品的再加热温度不尽相同。
τ可按下式估算:当采用步进式再加热炉加热钢管时,加热时间jrS DSD jr •-=2.2τ 式中 D——被加热钢管外径,mm;S——被加热钢管壁厚,mm。
当热装温度为700℃时,应将上式计算的结果减少30%左右。
斜轧穿孔 穿孔变形区为了使穿孔时能顺利咬入管坯和顺利抛出毛管,在进行工具设计和轧机调整时,要保证:(1)管坯在穿孔准备区内不与导板接触,或者至少管坯先与轧辊接触形成一定的变形区长度(约30~70mm )后再与导板接触,以保证二次咬入的实现;(2)毛管离开变形区的程序为毛管先脱离顶头,再脱离导板,最后离开轧辊。
调整参数(1)轧制线管坯——毛管中心运行轨迹为穿孔轧制线。
实际上穿孔机顶杆的轴线即为轧制线,可通过调整定心辊来实现。
(2)送进角(又称前进角)α二辊卧式斜轧穿孔机的送进角是指轧辊轴线与轧制线在包含轧制线的垂直平面上投影的夹角。
二辊立式斜轧穿孔机的送进角是上述两线在水平面上投影的夹角。
其它斜轧机按此概念类推。
送进角是斜轧中最积极的工艺参数。
(3)机器中心线即穿孔机本身的中心线。
有的机组上为使穿孔过程稳定,以及考虑到下导板更换方便等因素,将轧制线调整得比机器中心线低3~6mm ,使管坯贴紧下导板。
(4)轧辊间距B ck指两轧辊的轧制带之间(即孔喉处)的轧辊间距。
(5)导板间距L ck指两导板过渡带工作面间距。
(6)穿孔机孔型椭圆度系数ξckckB L =ξ (7)管坯总直径压下量p D ∆和总压缩率εck p p B D D -=∆ %100⨯∆=pp D D ε(8)顶头前压下量dq D ∆和顶头前压缩率dq εdq p dq B D D -=∆13tan )5.0(2βL C B B ck dq -+=%100⨯∆=pdq dq D D ε斜轧穿孔速度的计算毛管出口速度:x g ch xch n D V αηπsin 60= y g ch ych n D V αηπcos 60=y mchpch D D n αηcos =yxm ch D nZ ηηαπtan =式中:xch V ——毛管轴向出口速度(又称穿孔速度),mm/s ; ych V ——毛管切向出口速度,mm/s ; pch n ——毛管出口转速,rpm ;ch Z ——毛管出口1/n 螺距,mm ;x η——轴向滑动系数,又称轧制效率或穿孔效率; y η——切向滑动系数;D m 、D ch ——毛管外径及出口截面处轧辊直径,mm 。
当已知轴向出口速度后,可根据秒体积流量不变原则,求出变形区任一截面上的管坯――毛管的轴向速度xx V 和1/n 螺距x Z 为xch m xx px V F V F =x pxm g ch xch px m xx F F n D V F F V ηαπsin 60==αηηπtan px xxx px xch m x D D nF D F Z =如果忽略扭转的影响pch px n n =,则αηηπtan m ypx xm x D nF F Z =式中:m F ——毛管断面积,mm 2;px F ——变形区内任一截面上管坯—毛管断面积,mm 2。
滑移系数的确定:在穿孔和其它斜轧过程中,变形区中的金属滑动情况是很复杂的,目前对x η和y η值只能估算。
根据实测,切向滑移系数y η接近于1,因此工程计算中取y η≈1。