车身RPS设计指导书
车身下车体RPS定位标准化应用
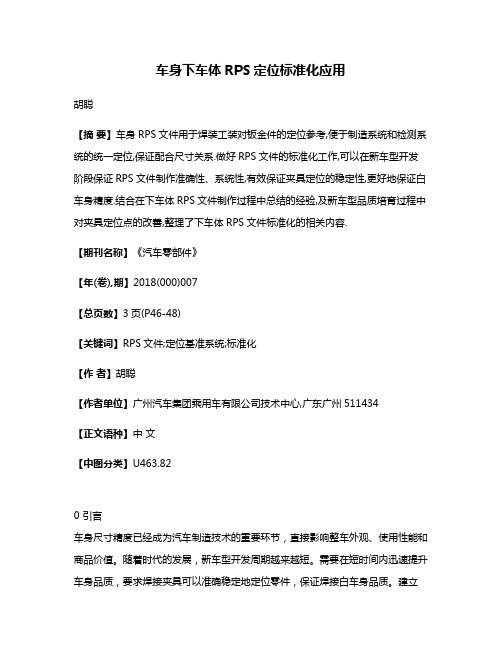
车身下车体RPS定位标准化应用胡聪【摘要】车身RPS文件用于焊装工装对钣金件的定位参考,便于制造系统和检测系统的统一定位,保证配合尺寸关系.做好RPS文件的标准化工作,可以在新车型开发阶段保证RPS文件制作准确性、系统性,有效保证夹具定位的稳定性,更好地保证白车身精度.结合在下车体RPS文件制作过程中总结的经验,及新车型品质培育过程中对夹具定位点的改善,整理了下车体RPS文件标准化的相关内容.【期刊名称】《汽车零部件》【年(卷),期】2018(000)007【总页数】3页(P46-48)【关键词】RPS文件;定位基准系统;标准化【作者】胡聪【作者单位】广州汽车集团乘用车有限公司技术中心,广东广州511434【正文语种】中文【中图分类】U463.820 引言车身尺寸精度已经成为汽车制造技术的重要环节,直接影响整车外观、使用性能和商品价值。
随着时代的发展,新车型开发周期越来越短。
需要在短时间内迅速提升车身品质,要求焊接夹具可以准确稳定地定位零件,保证焊接白车身品质。
建立RPS标准化文件可以系统准确地定位零件,高效解决品质问题,达成量产质量要求。
1 RPS理论RPS是德语单词Referenz-Puckt-System(定位点系统)的缩写,叫做定位基准系统。
规定一些从开发到制造、检测直至批量装车各环节所有涉及到的人员共同遵循的定位点。
RPS系统作用主要体现在下面3个方面:(1)避免由于基准点变换造成零件尺寸公差加大;(2)工装直接采用定位点调整,不需要其他辅助工具;(3)模具、夹具、检具统一按照同一系统定位。
2 定位延续和统一不同工序的基准要一直沿用到下道工序,避免由于基准点的变换造成零件尺寸公差加大。
原则上后工序都是沿用前工序使用的基准。
零件检具上的定位基准需要跟该零件下一工序焊接夹具上的定位基准保持一致。
案例:图1是机舱分总成焊接时前纵梁的定位孔,图2是地板总成焊接时前机舱的定位孔,在连续的两个焊接工序中,后工序会沿用前工序定位基准。
车身RPS培训

目的:RPS是为实现汽车功能需要设置的,关 注的是尺寸链 功能:RPS为模、夹、检具共同使用 基准:RPS有相对基准
N-2-1原则
刚性零部件
圆孔-长圆孔 圆孔-圆孔
门内板等包边定位孔径建议根据零件大小选用¢16、¢20其中一种
白车身孔数据通用标准
将高精度的装配孔/点设为定位孔/点,以保证 其最终定位精度; 零件定位孔所在面需为平面设计,不可在曲 面上; 定位孔处零件刚性相对较好; 尽可能避开焊点位置; 杜绝定位孔径向受力; 降低装配难度。 孔的坐标位置要取整数
产品 工艺 制造
公差链X向
门外板
门铰链
后门外板 1 加强板
铰链
螺母板
1
螺母板 B柱加强板
2
侧围外板
3
装配完 成的白 车身
不仅仅是车身的钣金件,所有的装配件都需 要有RPS
定位孔之间的距离应该大于该件在此平面最 大距离的三分之二
厚度不可忽略 零件定位精度会差,螺母位置精确 螺母会受损伤
承受强度较高的零件 直边长度大于2mm 设置时需要注意料厚方向
共用定位孔少用 两零件的孔距公差不一 上下工序间此孔重复使用,配合精度要求越来 越高
形状相似零件的定位孔孔距要求长度不一,避免错装; 模具包边的零件定位孔建议采用翻边孔,以提高孔对销 的导向作用; 在焊接装配定位时要考虑定位销运动方向上有5mm的定 位销运动空间;随销直径的增大,运动空间相应增大; 横梁类的零件定位孔设置不要放在槽体的中心,防止零 件装反; 减少零件的上定位,即减少翻销的使用
基准面、装配面、焊接面
汽车零部件设计时考虑到RPS系统问题

汽车零部件设计时考虑到RPS系统问题作者:武嘉明孙磊来源:《中国科技博览》2015年第17期[摘要]长期以来,大量的尺寸偏差给汽车制造企业带来重大损失,不仅严重影响零件的性能发挥,而且导致零件报废的频率增加,使汽车的成本增加。
尺寸偏差还给整车匹配带来间隙和平度的不合格等大的麻烦。
零件尺寸精度的保证是每一个汽车制造企业追求的质量目标。
随着汽车工业技术的进步和业内人士思想观念的转变,零件尺寸精度的保证已不再仅仅是生产部门和质量保证部门的事情,而是从产品开发阶段就开始考虑了。
RPS系统就是基于这种思想被发明出来并被世界各大汽车公司投入到使用当中。
[关键词]汽车零部件设计;RPS系统中图分类号:U463.82+1.07 文献标识码:A 文章编号:1009-914X(2015)17-0202-01在汽车零部件设计时,为了使RPS系统在实际生产当中发挥作用,必须遵守下面五条规则:(1)3-2-1规则。
一个刚体的来行移动和转动共有6个自由度。
限制其6个自由度,刚体才能保持平衡。
按照3-2-1规则,保持刚体平衡状态需要6个定位点,如图1所示:其中:3个定位点在Z方向,2个定位点在Y方向,1个定位点在X方向,3-2-1规则由此得来。
这些点就是RPS系统的定位点,称为RPS点。
但是对于大的刚度不足的零件,在保障了3-2-1规则的前提下,还需要附加定位点来保证零件的平衡状态,如图2所示。
图中RPS5fz是附加定位点,它的命名与主RPS点相似,但定位方式用小写字母表示。
(2)坐标平行规则在测量和加工时,零件的放置必须保证能够获得精确的结果。
下面通过两种定位系统来分析坐标平行规则的重要性。
如图3所示。
可以看出倾斜放置会导致测量结果不准确。
这里出现在Z方向的测量偏差。
其实零件在Z 方向是正确的。
同时还可以看出测量得到的X方向的偏差也是不正确的。
因为,定位点应当是与坐标轴平行的。
不过在有些零件上是找不到与坐标轴平行的平面做RPS点的,这时在不影响功能的基础上应当设计出平行于坐标轴的平面作为RPS点。
车身汽车车身设计与开发(完整版)
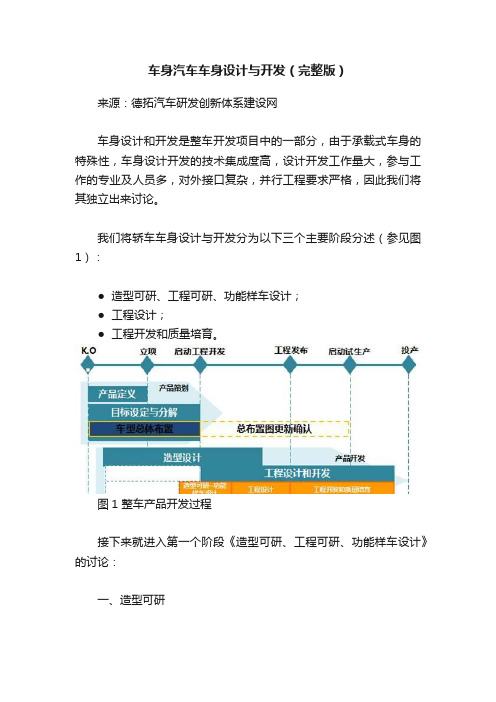
车身汽车车身设计与开发(完整版)来源:德拓汽车研发创新体系建设网车身设计和开发是整车开发项目中的一部分,由于承载式车身的特殊性,车身设计开发的技术集成度高,设计开发工作量大,参与工作的专业及人员多,对外接口复杂,并行工程要求严格,因此我们将其独立出来讨论。
我们将轿车车身设计与开发分为以下三个主要阶段分述(参见图1):●造型可研、工程可研、功能样车设计;● 工程设计;● 工程开发和质量培育。
图1 整车产品开发过程接下来就进入第一个阶段《造型可研、工程可研、功能样车设计》的讨论:一、造型可研当总布置给出了初步控制硬点图、造型给出了内外CAS面(3D数字化表面),车身即要进行造型的可行性研究(简称造型可研)。
业界将造型师称为Designer——设计师,他们是真正的概念和创意的提出者,因而在开发中享有至高的权威。
但是造型师的创意是需要工程实现的,因此作为它的技术支撑——车身部门首先要分析其创意的整体和各个局部实现的方式和代价,即可行性,这一工作就是造型可研。
该阶段车身主要从事几何绘制和分析:—选择相关部件的结构形式(也是车身部件的创意和构想);—绘制部件的断面、确定连接关系、对空间布置进一步细化,即做layout;—将白车身的主要断面放进内外CAS面之间,确定主要断面是否得到了保证;—进行法规满足性分析。
对于几何空间不够,造型元素实现的代价太大,法规不满足等都需要和造型部门协商、调整。
我们以结构选型举例:图2是前格栅的安装方案比较示意。
有安装在发动机罩上,也有安装在保险杠或车身上。
其中安装在机罩上还有嵌入式和与金属板连接式。
这些方案的美学效果、结构重量、制造成本都不一样。
因此类似的结构方案都要和造型敲定,以便造型能实现美学期望并锁定分缝线,车身确定大体结构及安装关系,项目认可成本,商品认可竞争力。
图2 前格栅安装方式对于一个成熟、积累较多经验的车身设计团队,结构选型的过程十分简单。
造型在效果图中表达清楚了,车身及相关部门明确一下是曾经某车的结构沿用就算定了。
RPS详解

1. RPS定位系统图1RPS起源于大众公司,是德语REFERENZPUCKTSYSTEM的缩写,英文名称为Reference Point System。
通常主定位方式为3-2-1法则,某些零件需要添加辅助定位则为N-2-1法则。
这种系统与以往定位点不同之处在于定位点的一致性上,不采用RPS定位系统时零件和总成的定位往往是单独考虑的,定位点在零件分总成和总成上并不能保证一致,这样的话在公差累积中由于定位点的不同会额外的计入一部分公差从而降低精度。
如下图2所示,对于左边的零件如果在单件时使用绿色的定位点定位,而在焊接分总成时采用红色的定位点定位,那么在两次定位过程中会产生误差。
图2RPS在GD&T图纸上的表示方法各个公司也有不同,通常情况下针对检具的RPS要区分主辅定位,区分方法可以通过编号,字母大小写,以及图示方法。
下图3是一种对应全局坐标的主辅定位图示。
个人认为图示方法较为系统化和方便辨识。
图3RPS定位点的具体选择往往由经验丰富的专家负责进行,同时也不是尺寸公差一家之言,而是需要冲压,焊装,总装,尺寸公差,以及产品设计部门共同制定。
这样做的主要目的是为保证定位一致性以及可行性。
可行性是考虑到某些位置也许对于公差累积是有利的但是在产品设计或夹具制造过程中无法实现。
具体选择标准通常是经验考虑,下图4简单列举了几种情况。
一般来说定位孔的选择主要是考虑其在零件上的位置,同时孔轴心尽量与零件平面垂直;定位面尽量选择正向平面,对于重要的定位孔基面及定位面若曲率较大应作出定位凸台;考虑整个零件的尺寸主定位点应尽量分散但不要太靠近边缘,对于中等尺寸零件定位点距边缘的距离应在整个长度的1/6左右。
当然随着冲压和焊接技术的提高,很多原来被认为不适合定位的位置也变得可以用作定位了,总的来说定位点的选择越来越多样化也越来越“随意”。
下载 (20.27 KB)2009-7-29 17:03为了最大限度的减小在汽车制造过程中所产生的系统累积误差,欧洲和北美的很多汽车企业,尤其是德国的汽车企业,都采用了一种叫做参考点系统或者近似参考点系统的理论,以保证汽车在设计、制造和检验过程中采用统一的定位基准。
三维RPS、MCP在新车型开发中的应用

随着我国汽车市场的发展,汽车换代不断加快,汽车开发周期不断缩短,同时要求车身尺寸质量水平同步提升。
现代汽车制造中,普遍采用车身制造综合误差指数CII(Continuous Improvement Indicator)来控制车身制造质量,即2mm工程。
2mm(6σ)应用于汽车工业不仅可以实现经济的汽车制造,同时也是国家制造技术水平的综合反映。
自从RPS、MCP引进国内汽车市场后,经过近年来的不断发展,成为汽车行业内产品开发和工艺开发最为重要的基础技术之一。
RPS、MCP理论的充分应用与完善,以及焊装SE水平、冲压件制造、夹具设计制造水平的提高,极大地推动了国内车身制造水平的发展。
然而在新车型开发过程中,车身零件RPS、MCP的设计,采用传统二维的设计形式,设计周期长、效率低,若需调整优化较为繁琐,且需要设计人员有较好的三维空间能力,影响了RPS、MCP的设计、评审等工作的开展。
如何提升RPS、MCP工作开展的效率,缩短设计周期,业内一直都在探索。
目前,结合已开发新车型的尝试,三维设计形式的RPS、MCP将很好地解决此问题,以下将进行阐述。
RPS、MCP设计流程1.RPS、MCP概述RPS(Reference Point System)即定位基准点系统,规定了汽车产品制造各环节(包括模具、夹具、检具、装具及测量等)统一的基准系统。
以前后统一、上下继承的形式,保证各个环节上由定位基准变换所产生的尺寸偏差最小的车身基准点系统。
RPS的应用优势在于,从设计到生产各个环节中的基准尽量统一,从而减小制造误差,提高车身制造精度。
MCP(Master Control Point)即主要控制点,是产品(冲压件、分总成件、总成件及白车身)质量控制的主要基准点及焊接夹具的基准点,在新车型设计阶段同步完成,可使产品质量波动最小化。
MCP贯穿新车型产品设计、冲压、焊接以及白车身检测等生产的整个过程。
三维RPS、MCP设计遵循了二维RPS、MCP设计的设计原则,采三维RPS、MCP在新车型开发中的应用田飞,周海波,臧永志上海锐镁新能源科技有限公司杭州分公司 浙江杭州 310002摘要:分析介绍了同步工程中RPS、MCP设计的一般流程、设计原则及内容,提出二维设计在设计过程中出现的问题,结合实践经验,展示了新型三维设计在RPS、MCP设计中的应用,并结合实际案例进一步说明了三维RPS、MCP在设计中存在的优势。
轿车车身的设计与开发流程说明书
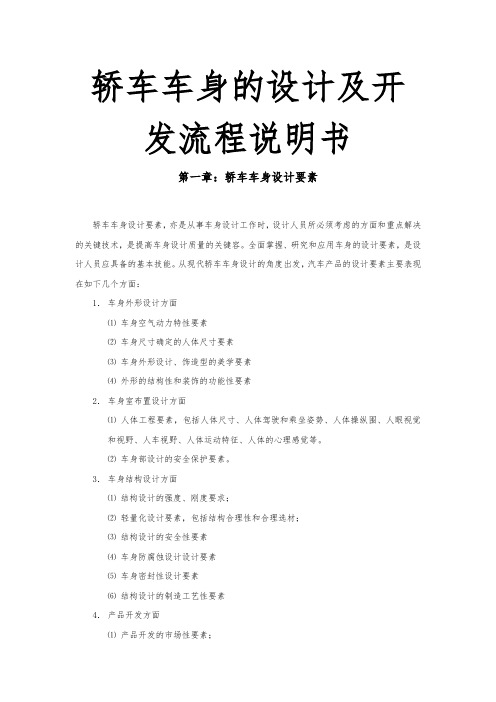
轿车车身的设计及开发流程说明书第一章:轿车车身设计要素轿车车身设计要素,亦是从事车身设计工作时,设计人员所必须考虑的方面和重点解决的关键技术,是提高车身设计质量的关键容。
全面掌握、研究和应用车身的设计要素,是设计人员应具备的基本技能。
从现代轿车车身设计的角度出发,汽车产品的设计要素主要表现在如下几个方面:1.车身外形设计方面⑴车身空气动力特性要素⑵车身尺寸确定的人体尺寸要素⑶车身外形设计、饰造型的美学要素⑷外形的结构性和装饰的功能性要素2.车身室布置设计方面⑴人体工程要素,包括人体尺寸、人体驾驶和乘坐姿势、人体操纵围、人眼视觉和视野、人车视野、人体运动特征、人体的心理感觉等。
⑵车身部设计的安全保护要素。
3.车身结构设计方面⑴结构设计的强度、刚度要求;⑵轻量化设计要素,包括结构合理性和合理选材;⑶结构设计的安全性要素⑷车身防腐蚀设计设计要素⑸车身密封性设计要素⑹结构设计的制造工艺性要素4.产品开发方面⑴产品开发的市场性要素;⑵系列化产品发展要素;⑶生产、工艺继承性要素。
第二章:整车开发流程随着汽车设计技术及手段的发展特别是现代工程技术方法的飞速进步,日益成熟的CAD/CAE/CAM一体化产品开发技术在轿车车身设计领域的应用,轿车设计方逐步由传统的设计方法向着以大大缩短产品开发周期和提高产品设计精度方面转变。
一般来说,整车开发时间为三年,由于市场竞争的日趋激烈,为抢夺有限的市场资源,整车开发时间逐渐缩短,更新换代非常平凡,稍微大一点的公司每年基本上要推出1款新车,有些汽车生产公司一年还有好几辆,以前的开发流程已经不能满足现代社会汽车设计的要求,根据最新的时间概念,设计一款全新的轿车,从项目成立到小批量生产,最快的大概只需18个月的时间了。
一、第一项目开发流程图:从时间的需求角度来说,大致时间安排如下(从立项日开始):天天30天75天120天140天190天240天310天360天480天500天540天600天二、第二项目开发流程图:从主要节点出发注:此处Test/试验包括一下部分(当然,这些试验不可能在较短的时间完成):1.安全气囊的匹配试验2.电喷系统、ABS、匹配试验3.排气系统、悬挂系统、转向、制动等系统匹配试验4.整车碰撞试验,国家强检及3C认证试验5.相关零部件的性能、寿命试验第三章:项目开发流程1、项目策划阶段1.1在项目概念批准之前,项目经理应协助销售公司市场部做好市场调研,提交《新产品市场调研报告》。
基于车身功能角度的RPS设计

基于车身功能角度的RPS设计姜珍;张迎杰;赫立远【摘要】本文从车身功能角度介绍RPS设计需注意的内容,举例分析了RPS一致性准则对车身精度产生的重要影响;介绍了功能分析在车身RPS设计过程中的关键作用,并以实例介绍了在设计、生产中RPS一致性不良将对车身精度产生的重要影响。
【期刊名称】《汽车制造业》【年(卷),期】2016(000)017【总页数】2页(P68-69)【关键词】设计过程 RPS 车身功能一致性精度【作者】姜珍;张迎杰;赫立远【作者单位】华晨汽车工程研究院【正文语种】中文【中图分类】U463.82本文从车身功能角度介绍RPS设计需注意的内容,举例分析了RPS一致性准则对车身精度产生的重要影响;介绍了功能分析在车身RPS设计过程中的关键作用,并以实例介绍了在设计、生产中RPS一致性不良将对车身精度产生的重要影响。
RPS系统就是规定一些从开发到制造、检查直至批量装车等各环节所有涉及到的人员共同遵循的定位点及其公差要求。
在车身焊装生产过程中,白车身零部件的正确定位和夹紧是车身装配的基础,是整个车身制造质量的保证。
由于RPS系统由国外引入,大家对于RPS的根本来源不是特别清晰,在其制作过程中仅仅从RPS的设计原则并结合自己以往参与的项目经验便设定了RPS。
这样虽然可以解决实际生产中的一些问题,但是由于大家并没有深刻地理解RPS的设定原则,故在制作RPS的过程中会丢失一些更宝贵的东西,因此,无法在前期设计阶段就规避一些由于RPS设定而引起的现场问题。
本文结合我公司新车型开发过程中设定RPS时所遇到的问题来深入剖析RPS的设定原则。
1.RPS设计过程的功能需求在我公司一款新车型的RPS设定过程中,按照传统的RPS设定准则,对于门总成的RPS设定会按照“3-2-1”原则将RPS定在门内板上,如图1所示。
设定RPS后,会通过门总成RPS设计一款装具对生产线上门总成进行装配,并对设计提出的质量特性进行校核。
- 1、下载文档前请自行甄别文档内容的完整性,平台不提供额外的编辑、内容补充、找答案等附加服务。
- 2、"仅部分预览"的文档,不可在线预览部分如存在完整性等问题,可反馈申请退款(可完整预览的文档不适用该条件!)。
- 3、如文档侵犯您的权益,请联系客服反馈,我们会尽快为您处理(人工客服工作时间:9:00-18:30)。
II
Q/IAT‧SJ 29-2008
车身RPS设计指导书
1 范围
本设计指导书描述了阿尔特(中国)汽车技术有限公司车身设计开发中,RPS系统的设 计原理,过程及应用。
本设计指导书适用于车身系统的设计和开发。
2 目的
为了有效的控制因定位系统产生的公差,保证零部件尺寸精度,实现整车装配高品质。
3 术语和定义
图 15 零件上没有与坐标面平行的平面做定位点
9
Q/IAT‧SJ 29-2008 这时在不影响功能的基础上应当设计出平行于坐标面的平面作为RPS点,如图16所示。 在零件上压出 与坐标面平行 的平面
图 16 压出与坐标轴平行的平面 5.3 统一性原则 5.3.1 RPS系统的主旨是通过避免基准转变来保证制造工艺过程的可靠性和可以重复利用 的精确性。 5.3.2 RPS系统的统一性规则要求从产品开发阶段直到批量生产,RPS点的使用贯彻始终。 当然不是所有的RPS点都一直使用下去,那样的话在总成零件上 就会有许多点是重复的。 5.3.3 下面从纵梁到地板总成的焊接流程来看RPS点按统一性原则的运用。
图 17 焊接前RPS点分布情况 5.3.3.1 图17是总成焊接前各零件RPS点的分布情况。
10
Q/IAT‧SJ 29-2008
5.3.3.2 图18是第一道焊接工序后RPS点重新确定的情况。可以看到地板总成上有3个RPS 点是沿用合成前零件上已有的:总成上的RPS1点是单件左纵梁上的RPS1点,总成上的RPS3 点是单件前地板上的RPS3点,总成上的RPS4点是单件右纵梁上的RPS点。
5.1 3-2-1原则 5.1.1 一个刚体的平行移动和转动共有6个自由度。限制其6个自由度,刚体才能保持平衡。 按照3-2-1规则,保持刚体平衡状态需要6个定位点,如图4所示,其中:
a) 3个定位点在 Z 方向; b) 2个定位点在 Y 方向; c) 1个定位点在 X 方向。 3-2-1规则由此得来。这些点就是RPS系统的定位点,称为RPS点。
图 18 第一道焊接工序后RPS点重新确定的情况 5.3.3.3 图中各RPS点是完全遵循地板总成的功能要求确定下来的:地板有固定前端框架、 座椅、踏板、后轴、付车架以及与侧围连接的功能。 5.3.3.4 图19是地板总成焊接完成后RPS点再一次重新确定的情况。可以看到总成上的 RPS1、RPS2、RPS3、RPS4以及附加RPS点RPS7、RPS8都是从前一步延续使用的,只不过是重 新排序。
3.1 RPS系统 Reference Points System 是规定一些从开发到制造、检测,直到批量装车各个环节,所有涉及到的人员共同遵
循的定位点及公差要求。 3.2
模板 Template 模板是将结构标准化的具体体现形式。 3.3 名义尺寸 Nominal Dimension 名义尺寸是公称尺寸在标准中的规定,指在零件坐标系中,一个点相对于基准点的距 离。
定位系统1
定位系统2
图 11 两种定位系统 将合格的零件放到两种定位系统中,似乎看不出有什么不同,见图12。
7
Q/IAT‧SJ 29-2008
定位系统1
定位系统2
图 12 将合格的零件,如图13所示,2个零件在X方向存在偏差——它们比合格零件 做短了。
定位系统1
图 19 地板总成焊接完成后RPS点再一次确定的情况
11
Q/IAT‧SJ 29-2008 5.3.4 RPS系统的统一性规则还要求所有工艺流程中的输送装置原则上都要使用RPS点作
为支点,如图20所示。
图 20 输送装置使用RPS点作为支点 5.3.5 RPS点的设定是从车身到各大分总成(如下车身、侧围、顶盖)再到各级小总成直 到单件儿进行的。 5.4 尺寸标注原则 5.4.1 在图纸中尺寸一般是从整车坐标线引出和标注的,往往不标注实际尺寸。这种标注 方式会造成推算尺寸公差的增大,如图21所示。 5.4.2 在零件图纸中画出整车坐标是有意义的--这可以确定零件在整车中的位置,这是零 件设计过程中重要的基础。可是对于零件的制造和测量,采用整车坐标会带来很多困难。 RPS系统要求建立起零件自身的坐标系--零件坐标系,并以此作为基础。
3
Q/IAT‧SJ 29-2008 3个旋转自由度
3个平移自由度
定位点
图 4 刚体的6个自由度
5.1.2 对于没有孔的零件,6个RPS点是必须的。而有孔的零件往往将孔设定为RPS点。一 个圆孔可以限定2个自由度,如图5所示。图中给出的RPS点限定了3个自由度,因此本例子 中只有4个RPS点。
这个圆孔限定了X,Y方向的平移
图 5 带孔零件RPS点限定的自由度
这个平面作为Z方向的1个定位点,和孔 被定义为一个RPS点
4
5.1.3 RPS点的标注,见图6。
Q/IAT‧SJ 29-2008
平面定位方向 平面定位点标记字 孔限位方向 孔定位点标记字母 带有序号的RPS点名称 图 6 RPS点的标注
对定位方式标记字母的含义说明如下: H,h = 孔/销定位 F,f = 平面/棱边/球面/顶点定位 T,t = 理论点
用 RPS点作定位
图 3 加工时不用模板
4.3 RPS点是模具、工装、检具的定位点 为了实现统一的定位技术规则,必须保证模具、工装、检测工具都按照RPS点来制造。
5 RPS系统的五大原则 为了使RPS系统在实际当中发挥作用,必须遵守下面五条原则: a) 3-2-1原则; b) 坐标平行原则; c) 统一性原则; d) 尺寸标注原则; e) RPS尺寸图。
12
Q/IAT‧SJ 29-2008
尺寸AB的公差是+/-0.4,因 为点A和点B从坐标线引出的尺寸 都有+/-0.2的公差
图 21 从整车坐标线引出尺寸线 5.4.3 零件坐标系是以整车坐标系为基础建立起来的,有下面两种建立方式:
a) 通过在整车坐标系中平移建立,这是通常的情况,如图 22 描述了通过在整车坐标 系中平移建立零件坐标系的情形;
图 22 在整车坐标系中平移建立零件坐标 b) 通过在整车坐标系中旋转建立,这是特殊的情况,如图 23,则描述了通过在整车
坐标系中旋转建立零件坐标系的情况。
13
Q/IAT‧SJ 29-2008
图 23 通过在整车坐标系旋转建立零件坐标系 5.5 通过平移建立零件坐标系的尺寸标注规则 5.5.1 按照零件特性选择三个与整车坐标轴平行的平面并求其交点,这个交点定义为 RPS 系统的基准点。基准点相对于整车坐标没有公差,零件尺寸以基准点为起点标注。 5.5.2 尺寸标注必须符合零件功能要求,对于重要尺寸要给出直接尺寸。例如安装在翼子 板上的转向灯罩的装配要求准确的孔距,如图 24,不仅尺寸要准确,尺寸公差也要满足功 能的要求。两个固定孔在翼子板上的位置并不很重要(转向灯在翼子板上位置公差在 1mm 时是不易被察觉的),因此它们的位置公差可以较大而对功能没有影响。
5
Q/IAT‧SJ 29-2008
图 7 大面积的刚度不足零件需要附加定位点
5.1.5 3-2-1规则适用于任何形状的零件。但是特殊形状的刚体,会使此规则产生例外。
例 1:球体,只需要3个定位点即达到平衡,旋转对轮廓没有改变,如图8所示。 例 2:旋转体,需要5个定位点即达到平衡,绕中心轴的旋转,外形不发生改变,如图9所示。 例 3:铰接零件需要达到平衡时,将其中一个设为固定件进行RPS设定,另外的铰接件,根据需要增 加RPS定位点。因此此部件需要的定位点多于6个,必须有附加的定位才能达到平衡状态,如图10所示。
6
图 8 球体只需要3个定位点
图 9 旋转体需要5个定位点
Q/IAT‧SJ 29-2008
图 10 铰接零件需要的定位点多于6个 5.2 坐标平行原则 5.2.1 在测量和加工时,零件的放置必须保证能够获得精确的结果。下面通过两种定位系 统的对比来分析坐标平行规则的重要性。图11所示为两种定位系统。
a) 加工时基准点发生变换
步骤1):用孔A定位钻出孔B和孔D
公差 A…B = +/-0.1
A…D = +/-0.1
步骤2):用孔D定位钻孔C (这时基准由孔A变为孔D)
公差 D…C = +/-0.1
孔B、孔C距离公差结果
A…B = +/-0.1
A…D = +/-0.1
D…C = +/-0.1
B…C = +/-0.3
上面例子给我们的提示是:为避免基准变换,必须事先规定好在制造和测量过程中的
基准点。而且不允许各部门自作主张随意确定基准点进行加工。
4.2 避免了模板的使用
模板的使用有很大的局限性,并且增加了加工时间。规定工装用RPS点调准,那么加工
就变成是直接的了,模板不再作为辅助定位工具,参见图3。
2
Q/IAT‧SJ 29-2008
大写字母表示主RPS点的定位方式,小写字母表示附加定位点的定位方式。 小写字母x,y,z表示RPS点的限位方向。 5.1.4 但对于大面积的刚度不足的零件,在保障了3-2-1规则的前提下,还需要附加的定 位点来保证零件的平衡状态,如图7所示。 图中RPS5fz是附加定位点,它的命名与主RPS点相似,但定位方式用小写字母表示。
I
Q/IAT‧SJ 29-2008
前言
本设计指导书是充分借鉴国内外汽车设计行业对车身设计中RPS系统建立过程的技术 要求,和本公司已经开发各车型的宝贵经验,结合公司现有的实际情况及未来发展的需要 编写而成的。
本设计指导书由阿尔特(中国)汽车技术有限公司技术委员会提出。 本设计指导书由阿尔特(中国)汽车技术有限公司技术委员会批准。 本设计指导书由阿尔特(中国)汽车技术有限公司技术管理部归口管理。 本设计指导书由阿尔特(中国)汽车技术有限公司白车身设计部起草。 本设计指导书主要起草人:孟晓光。
Q/IAT