延迟焦化工艺流程
延迟焦化工艺参数优化及操作控制

化气,并使汽油的蒸汽压合格;柴油需要加氢精
制;蜡油可作为催化裂化原料或燃料油。
二、主要工艺参数
焦化装置的工艺参数包括加热炉、焦炭塔温度、压力、循 环比以及分馏、吸收、放空系统操作温度、压力等。 主要控制指标是加热炉、焦炭塔温度与压力及循环比。
1.操作温度
焦化装置操作温度一般指加热炉出口温度或焦炭塔温度,一般控 制在493-502℃。
0.105-0.141MPa或更低,循环比降到0.05,焦化液体收率
可提高3%,焦炭产率降低2%。 福斯特-惠勒公司典型焦化装置的设计压力为0.103MPa, Lummus公司典型低压焦化装置焦炭塔压力亦为0.103MPa,
Kellog公司典型设计压力为0.1-0.141MPa.
④加工高沥青质渣油时,为了减少弹丸焦(shot-coke)的 生成;
⑤加热炉燃烧工况不佳,需增加循环比,减缓炉管结焦。
降低循环比的影响:
①单程(零循环比)或低循环比焦化,液体收率高,焦炭收率低; ②单程或低循环比使焦化蜡油变重、质量变差,残炭与重金属含
量增加,其残炭可高达1.9%,会影响下游催化裂化及加氢裂化 装置。
(3) 可高循环比方案
通过循环油泵抽出分馏塔底含焦粉的循环油,以一定比例混入 加热炉进料缓冲罐。
特点:
①采用分馏塔底循环油代替新鲜原料渣油成分馏塔底与焦炭塔高温油气 换热,由于循环油中胶质、沥青质含量低,其结焦倾向降低,用于提 高蒸发段温度的低循环比操作。 ②该方案中的循环油既可使用分馏塔换热、洗涤段冷凝下来的循环油, 也可用蜡油或柴油馏分,实现选择性馏分油循环。 ③塔底循环油经塔外换热器循环回流,可控制塔底温度,减缓塔底结焦
(2) 大陆-菲利浦斯公司低循环比+馏分油循环方案
延迟焦化工艺流程
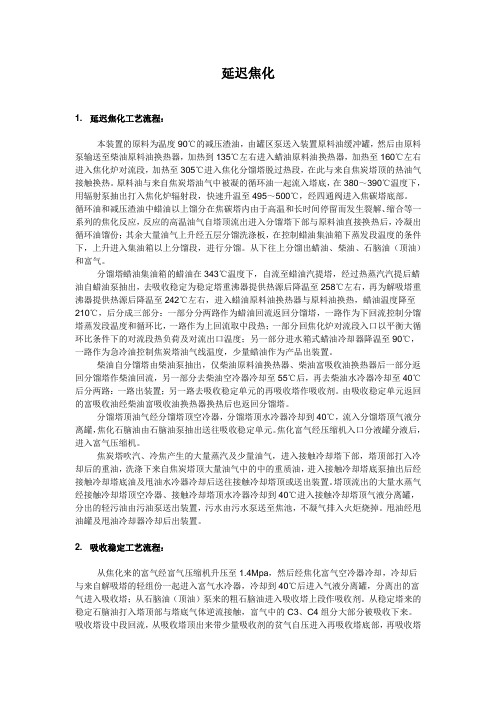
延迟焦化1. 延迟焦化工艺流程:本装置的原料为温度90℃的减压渣油,由罐区泵送入装置原料油缓冲罐,然后由原料泵输送至柴油原料油换热器,加热到135℃左右进入蜡油原料油换热器,加热至160℃左右进入焦化炉对流段,加热至305℃进入焦化分馏塔脱过热段,在此与来自焦炭塔顶的热油气接触换热。
原料油与来自焦炭塔油气中被凝的循环油一起流入塔底,在380~390℃温度下,用辐射泵抽出打入焦化炉辐射段,快速升温至495~500℃,经四通阀进入焦碳塔底部。
循环油和减压渣油中蜡油以上馏分在焦碳塔内由于高温和长时间停留而发生裂解、缩合等一系列的焦化反应,反应的高温油气自塔顶流出进入分馏塔下部与原料油直接换热后,冷凝出循环油馏份;其余大量油气上升经五层分馏洗涤板,在控制蜡油集油箱下蒸发段温度的条件下,上升进入集油箱以上分馏段,进行分馏。
从下往上分馏出蜡油、柴油、石脑油(顶油)和富气。
分馏塔蜡油集油箱的蜡油在343℃温度下,自流至蜡油汽提塔,经过热蒸汽汽提后蜡油自蜡油泵抽出,去吸收稳定为稳定塔重沸器提供热源后降温至258℃左右,再为解吸塔重沸器提供热源后降温至242℃左右,进入蜡油原料油换热器与原料油换热,蜡油温度降至210℃,后分成三部分:一部分分两路作为蜡油回流返回分馏塔,一路作为下回流控制分馏塔蒸发段温度和循环比,一路作为上回流取中段热;一部分回焦化炉对流段入口以平衡大循环比条件下的对流段热负荷及对流出口温度;另一部分进水箱式蜡油冷却器降温至90℃,一路作为急冷油控制焦炭塔油气线温度,少量蜡油作为产品出装置。
柴油自分馏塔由柴油泵抽出,仅柴油原料油换热器、柴油富吸收油换热器后一部分返回分馏塔作柴油回流,另一部分去柴油空冷器冷却至55℃后,再去柴油水冷器冷却至40℃后分两路:一路出装置;另一路去吸收稳定单元的再吸收塔作吸收剂。
由吸收稳定单元返回的富吸收油经柴油富吸收油换热器换热后也返回分馏塔。
分馏塔顶油气经分馏塔顶空冷器,分馏塔顶水冷器冷却到40℃,流入分馏塔顶气液分离罐,焦化石脑油由石脑油泵抽出送往吸收稳定单元。
延迟焦化工艺流程

延迟焦化工艺流程延迟焦化工艺是一种重要的炼油工艺,它能够将石油原油转化为高附加值的产品,如汽油、柴油和航空燃料等。
在延迟焦化工艺中,原油经过一系列的热裂解和重整反应,最终得到所需的产品。
本文将对延迟焦化工艺流程进行详细介绍。
首先,原油进入延迟焦化装置后,经过预热和预处理,进入裂解炉。
在裂解炉中,原油在高温和催化剂的作用下,发生裂解反应,将大分子烃类分解为小分子烃类。
这些小分子烃类是后续生产汽油和柴油的重要原料。
接下来,裂解产物进入分馏塔,经过分馏过程,将不同碳链长度的烃类分离出来。
在分馏塔中,轻质烃类如汽油被分离出来,而重质烃类如柴油则被留在塔底。
这一步骤是为了得到不同种类的产品,以满足市场的需求。
随后,分馏得到的产品进入催化重整装置。
在催化重整装置中,轻质烃类经过重整反应,得到高辛烷值的汽油。
这种汽油具有良好的抗爆性能,适合用于汽车和飞机的燃料。
最后,催化重整得到的汽油和分馏得到的柴油经过精制处理,去除杂质和硫化物,得到高品质的成品油。
这些成品油可以直接用于市场销售,也可以作为化工原料进一步加工。
延迟焦化工艺流程是一个复杂的过程,需要严格控制各个环节的操作参数,以确保产品质量和生产效率。
同时,还需要注重设备的维护和安全管理,确保生产过程安全稳定。
只有做好这些工作,才能保证延迟焦化工艺的顺利进行,为炼油企业创造更大的经济效益。
总之,延迟焦化工艺流程是炼油行业中的重要工艺之一,它能够将原油转化为高附加值的产品,满足市场需求。
在实际生产中,需要严格控制各个环节的操作,确保产品质量和生产效率。
同时,还需要注重设备的维护和安全管理,以保障生产过程的安全稳定。
希望本文的介绍能够对延迟焦化工艺有所了解,对相关行业人士有所帮助。
延迟焦化工艺流程

延迟焦化工艺流程延迟焦化工艺流程是一种能够将重质石油馏分转化为具有高热值和高炭素含量的焦炭的技术。
它是对传统的焦化工艺进行改进和优化,以减少生产焦炭过程中的环境污染和能源浪费。
延迟焦化工艺流程具有高效节能、环保低污染和资源综合利用的特点,在石油化工行业被广泛应用。
1.原料准备:在延迟焦化工艺中,主要原料为重质石油馏分,通常是从石油精炼过程中得到的渣油。
这些渣油首先被送入预处理装置,经过脱硫、脱水和脱盐等处理,以提高其炭含量和降低硫、氮等杂质的含量。
2.煤炭炭化:预处理后的渣油与煤炭混合后,进入煤气化炉进行炭化反应。
煤炭炭化过程中,渣油中的碳分子与煤炭中的碳分子发生化学反应,生成焦炭和煤气。
同时,煤炭中的含硫化合物也得到部分转化或吸附,以减小煤气中硫化物的含量。
3.煤气净化:产生的煤气含有一定的杂质,如硫化物、苯、酚等。
煤气进入净化装置,经过除硫、除苯等处理,使煤气中的有害物质达到排放标准,同时,其中的一部分能源也得到回收利用,用于工艺过程中的煤气加热等。
4.焦炭冷却:经过煤气净化后,煤气中的焦油被分离出来,作为石油化工原料的补充。
随后,焦炭经过冷却装置,使其温度降低至环境空气温度,以保证焦炭的质量和可收回的热能。
1.高效节能:延迟焦化工艺能够充分利用原料中的热能和化学能,使其转化为焦炭和煤气,减少能源浪费。
同时,延迟焦化过程中产生的煤气也能够回收利用,用于工艺过程中的能源供应。
2.环保低污染:延迟焦化工艺通过净化装置等设备对煤气中的有害物质进行处理,使得煤气排放达到环境保护要求。
此外,延迟焦化过程中采用的高效脱硫等技术能够显著降低硫化氢等有害气体的排放。
3.资源综合利用:延迟焦化工艺能够将废弃的重质石油馏分转化为焦炭和煤气,提高了资源的综合利用率。
同时,工艺中产生的焦油和焦炭也能够作为石油化工原料的补充,实现循环利用。
总之,延迟焦化工艺流程是一种高效、环保、资源综合利用的工艺,在石油化工行业有着广泛的应用和发展前景。
延迟焦化工艺流程

延迟焦化工艺流程
《延迟焦化工艺流程》
延迟焦化工艺流程是指在焦炉内将原料煤进行加热、热解、焦化等过程时,采用特定的操作方式和工艺条件,以延长煤在高温条件下的停留时间,达到提高焦炭质量和产量的目的。
在延迟焦化工艺流程中,关键是要掌握好加热速度、保持时间和降温速度。
首先,原料煤要缓慢加热至高温。
经过一定时间的保温,再逐渐升高温度,直至煤体内的挥发分和焦油完全被释放出来。
这样能够避免过快的加热导致焦炭内部形成裂缝或者其他缺陷,影响焦炭的质量。
同时,延长保温时间还能够增加焦炭的焦化程度,提高焦炭的强度和耐磨性。
另外,降温速度也是延迟焦化工艺中需要重视的一点。
在高温煤炭热解后,如果降温速度过快,可能会导致焦炭表面和内部温度差过大,形成热应力,影响焦炭的质量。
因此在降温过程中要采取逐步降温的方式,使焦炭内外温度均匀,减少热应力的产生。
延迟焦化工艺流程通过合理控制加热、保温和降温过程,可以提高焦炭的质量和产量,降低生产成本,对于煤炭加工行业具有重要的意义。
随着技术的不断进步和创新,延迟焦化工艺流程也将不断完善,为煤炭生产带来更多的经济和环保效益。
延迟焦化操作规程
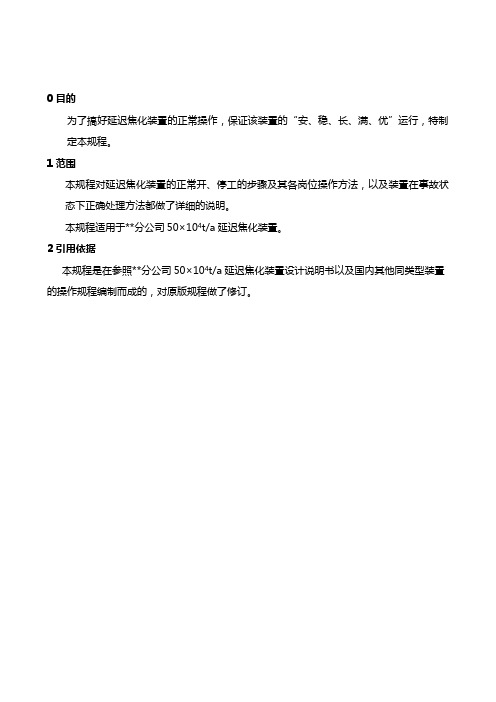
0目的为了搞好延迟焦化装置的正常操作,保证该装置的“安、稳、长、满、优”运行,特制定本规程。
1范围本规程对延迟焦化装置的正常开、停工的步骤及其各岗位操作方法,以及装置在事故状态下正确处理方法都做了详细的说明。
本规程适用于**分公司50×104t/a延迟焦化装置。
2引用依据本规程是在参照**分公司50×104t/a延迟焦化装置设计说明书以及国内其他同类型装置的操作规程编制而成的,对原版规程做了修订。
一装置简介1.概述延迟焦化装置由中国石化北京设计院设计,中国石化第四建设公司主要施工,于1999.3.29一次开车成功。
装置占地22500m2,包括加热炉1台、塔5座、容器39台、压缩机1台、冷换设备41台、通用机械81台、电梯1台、水力除焦设备2套、5000 m3原料罐3座、1000 m3甩油罐1座。
1.1设计依据(1)**炼油厂改建工程50×104t/a延迟焦化装置初步设计文件L8204-12。
(2)关于**炼油厂改建工程50×104t/a延迟焦化装置初步设计的批复,中石化(1996)建设字287号。
(3)**炼油厂与中国石化北京设计院签定的合同书:“**炼油厂改建工程50×104t/a 延迟焦化装置,合同号:44-96039”。
1.2设计规模装置设计加工能力50×104t/a,年开工时数8000小时。
1.3主要技术特点(1)采用无单独开工循环线的无堵焦阀焦炭塔开工暖塔工艺流程。
(2)采用油水分离的单塔两段接触冷却塔,缓和塔底油带水,塔顶冷凝水带油的现象。
(3)水力除焦操作过程采用PLC安全自保连锁控制,保证了水力除焦操作的安全性。
(4)采用有井架水力除焦技术。
(5)按照初步设计的批复意见,装置不设重蜡油系统,但对分馏塔预留重蜡油抽出口。
1.4物料平衡本装置设计加工能力50×104t/a,年开工时数8000小时,循环比0.4。
物料平衡表1.5本装置产生的压缩焦化气体出装置后去车用液化气装置。
延迟焦化流程图及相关数据总结

1. 延迟焦化工艺在炼油厂重油深加工中作用
世界重油加工能力构成
2. 延迟焦化工艺特点--产品的灵活性焦炭塔压力及不同渣油焦化产品收率
2. 延迟焦化工艺特点--通过调节温度、压力和循环比等参数增加操作弹性
二. 延迟焦化工艺流程
典型的延迟焦化工艺流程-可调循环比焦化工艺流程
典型的延迟焦化工艺流程--CONOCO焦化零自然循环原则流程
放空系统流程
延迟焦化装置放空系统流程图
放空系统流程-美国ABB Lunnns公司延迟焦化装置放空流程
焦炭处理系统流程--直接装车
延迟焦化装置操作压力对产品收率的影响
焦化产品
12.0 12.4
0.7936 0.7923
1.4 1.3
焦炭塔压力对焦化馏出油产率的影响
联合循环比(TPR)对焦化液体产品收率的影响
联合循环比对大庆减压渣油焦化产品收率的影响
焦化工艺参数优化
延迟焦化产品收率及焦化重瓦斯油的质量比较
焦化工艺参数优化
生产加氢裂化原料的延迟焦化装置产品收率
项目
氮含量,ppm 庚烷不溶物,ppm 康氏残炭值,%(质) 特性因数,(K) 分馏试验,℃
10%(体)
50%(体)
干点
项目
焦化产品收率
干气,%(体)
液化气,%(体)
石脑油,%(体)
焦化轻瓦斯油,%(体) 焦化重瓦斯油,%(体) 焦炭,%(质)
焦化重瓦斯油性质
相对密度
镍+钒,ppm
康氏残炭值,%(质)。
延迟焦化工艺流程

延迟焦化工艺流程
延迟焦化是一种重要的煤炭加工工艺,它可以将煤炭转化为高附加值的产品,如焦炭和煤焦油。
延迟焦化工艺流程是一个复杂的过程,涉及到多种化学和物理反应。
本文将详细介绍延迟焦化工艺流程的各个步骤,以及其在煤炭加工中的重要性。
首先,延迟焦化工艺流程的第一步是原料的准备。
在这一步骤中,煤炭被破碎和研磨,以便于后续的处理。
然后,煤炭被混合和预热,以提高其可塑性和流动性。
这些步骤对于后续的焦化过程非常重要,因为它们可以影响最终产品的质量和产量。
接下来,煤炭被送入延迟焦化炉进行焦化。
在焦化炉中,煤炭经过高温热解,产生焦炭和煤焦油。
这一步骤需要严格控制温度和气氛,以确保产生高质量的产品。
此外,焦化炉的设计和操作也对最终产品的质量有着重要的影响。
在焦化过程中,煤炭中的挥发性物质被释放出来,形成焦炭和煤焦油。
焦炭是一种重要的工业原料,广泛用于冶金和化工行业。
而煤焦油则可以提炼出多种有机化合物,如苯、酚和萘等,具有很高的经济价值。
除了焦炭和煤焦油之外,延迟焦化过程还会产生焦炭气。
焦炭气中含有大量的一氧化碳和氢气,可以作为燃料或化工原料使用。
因此,合理利用焦炭气可以提高整个生产过程的经济效益。
总的来说,延迟焦化工艺流程是一个复杂而重要的煤炭加工过程。
通过严格控制每个步骤,可以获得高质量的焦炭和煤焦油,提高煤炭资源的利用效率和附加值。
同时,合理利用焦炭气也可以提高生产过程的经济效益。
因此,对延迟焦化工艺流程的研究和优化具有重要的意义,可以推动煤炭加工技术的进步,促进煤炭产业的可持续发展。
- 1、下载文档前请自行甄别文档内容的完整性,平台不提供额外的编辑、内容补充、找答案等附加服务。
- 2、"仅部分预览"的文档,不可在线预览部分如存在完整性等问题,可反馈申请退款(可完整预览的文档不适用该条件!)。
- 3、如文档侵犯您的权益,请联系客服反馈,我们会尽快为您处理(人工客服工作时间:9:00-18:30)。
石油化学工程系 炼油工艺教研室
制作:张远欣
2
本章目录
第一节 概述 第二节 减粘裂化 第三节 焦炭化 小结 思考题
3
1.渣油的 热反应特性;
应知内容
2.反应热 和反应速率
3.焦化过程;
4.减粘裂化过程 及影响因素
4
1.各种烃类的热 反应及其规律;
2.(延迟)焦化的定 义、原料、产物 及影响因素;
6
复习
从石油中提炼出各种燃料 、润滑油和其它产品的基本途 径是:将原油按沸点分割成不 同馏分,然后根据油品使用要 求,除去馏分中的非理想组分 ,或经化学反应转化成所需要 的组分,从而获得合格石油产 品。
7
直馏轻馏分太少
存在问题
将原油中重质馏分油甚至 渣油转化成轻质燃料,这
就需要进行二次加工
热加工即是一种二次加工过程, 是指利用热的作用,使油料起 化学反应达到加工目的的工艺
焦炭化过程(简称焦化)是以贫氢的重油,如减渣、裂化渣油等为原料, 在高温(500~550℃)下进行深度的热裂化和缩合反应的热加工过程 工业化的焦炭化过程主要有延迟焦化、流化焦化和灵活焦化等工艺。 焦化过程是一种渣油轻质化过程,它的优点是可以加工残炭值及金属 含量很高的劣质渣油,主要缺点是焦炭产率高及液体产物的质量差
简称焦化,是以减压渣油为原料, 在常压液相下进行长时间深度热裂 化反应。其目的是生产焦化汽油、 柴油、催化裂化原料(焦化蜡油) 和工业11用石油焦。
返回 本节
二、热破坏加工化学反应
(一)裂解反应
C-C键断裂 吸热反应 较容易
C-H键断裂 吸热反应 较困难
各种烃裂解反应容易程度排序:
大分子烷烃、小分子烷烃、环烷烃、大芳烃、小芳烃
方法。
8
热加工过程
9
第一节 概述
热加工是指利用热的作用,使油料起化学 反应达到加工目的的工艺方法。
石油馏分及重、残油在高温下主要发生两 类反应:
•原油重质组分通过 缩合反应将碳集中
于更重组分,甚至 焦炭;
缩合反应 (放热)
裂解反应 (吸热)
一、热破坏加工过程分类 二、热破坏加工化学反应
通过裂解反应将氢 集中于轻组分,以 达到重组分转化为
族的烃类之间的相互作用也促进了生焦反应
3.渣油在热过程中可发生相分离
渣油是一种胶体分散体系
14
返回
本节
第二节 减粘裂化
减粘裂化是以常压重油或减压渣油为原料进行浅 度热裂化反应的一种热加工过程。主要目的是为了 减小高黏度燃料油的黏度和倾点,改善其输送和燃 烧性能。
一、原料和产品 二、减粘裂化工艺流程 三、操作因素分析
23
裂化温度:裂化温度随原料 油性质和要求的转化深度而 定。
裂化压力:应尽量选用较 低压力,这对简化工艺和减 少设备结焦有利。
反应时间:炉式减粘裂化的操作温度高, 反应时间只有1~3min;塔式减粘裂化 的操作温度低,需要的反应时间长。 提高反应温度和延长反应时间都可以 提高减粘转化率。
24
第三节 焦炭化
带烷基侧链的芳烃在受热条件下主要是发生断侧链或脱 烷基反应
13
三、渣油热反应的特点
1.渣油的热反应比单体烃更明显地表现出平行-顺序反应
的特征;
汽油和中间馏分油的产率会出现最大值
气体和焦炭随着反应深度的增大而单调的增大
2.渣油热反应时容易生焦;
▪分散相:沥青质胶束
▪指导生产
▪分散介质:饱和份等
除了由于渣油含有较多的胶质和沥青质外,不同
应会内容
3.延迟焦化工艺流 程,原料的来源及
特点;
4.减粘裂化的定义、 目的、原料及主要
反映条件。
5
核心知识点
热加工过程是早期发展起来的加工 工艺,随着石油工业的发展,重质劣 质石油的加工越来越受到重视,促使 热加工过程(如焦化)重新受到了人们的 青睐。本章重点介绍热加工的机理、 反应及焦化过程的工艺流程和特点。
轻组分的目的。
三、渣油热反应的特点 10
返回 本章
一、热破坏加工过程
▪热裂化是以常压重油、减压馏分油、焦 化蜡油和减压渣油等重质组分为原料,在 高温(450~550℃)和高压(3~5MPa) 下裂化生成裂化汽油、裂化气、裂化柴油 和燃料油。
(一)热裂化 (二)减粘裂化 (三)焦碳化
▪减粘裂化是在较低的温度(450~ 490℃)和压力(0.4~0.5MPa)下 使直馏重质燃料油经浅度裂化以降低 其黏度和倾点,达到燃料油的使用要 求。
20
与炉式减粘裂化相比, 塔式减粘反应温度低、 停留时间长
反应塔式减粘裂化工艺流程图
21
三、操作因素分析
1.原料 组成和性
质
2.裂化温 度
影响因素
3.裂 化压 力
4.反 应时 间
22
返回 本节
原料组成和性质的影响
原料沥青质含量、残炭值、 黏度、硫含量、氮含量及 金属含量越高,越难裂化。
蜡含量越高,原料越重,减粘 效果越明显。
(二)缩烃或烯烃
芳烃和烯烃缩合成大分子芳烃
缩合反应总趋势为:
芳烃,烯烃(烷烃→烯烃)→缩合产物→胶质、沥青质→炭青质
(三)渣油的热反应
12
返回
本节
芳香烃的缩合
2
CH3 2
2
+ H2
▪脱氢缩合
CH2 CH2
+ H2
+ 2 H2
▪继续脱氢生成 焦碳
减粘重瓦斯油性质主要与原料油性质有关,介于直馏 VGO和焦化重瓦斯油的性质之间,其芳烃含量一般比直馏 VGO高。
减粘渣油可直接作为重燃料油组分,也可通过减压闪蒸 拔出重瓦斯油作为催化裂化原料。
18
二、减粘裂化工艺流程
反应温度: 400~450℃ 反应压力: 4~5atm
19 炉式减粘裂化工艺原理流程 返回 本节
15
返回
本章
一、原料和产品
▪ 1.原料油 ▪ 常用的减粘裂化原料油有常压重油、减压渣油和 脱沥青油。 ▪ 原料油的组成和性质对减粘裂化过程的操作和产 品分布与质量都有影响 ▪ 主要影响指标有原料的沥青质含量、残炭值、特 性因数、黏度、硫含量、氮含量及金属含量等。
16
返回
本节
▪ 2.产品 减粘裂化气体产率较低,约为2%左右,一般不再分出
液化气(LPG),经过脱除H2S后送至燃料气系统。 减粘石脑油组分的烯烃含量较高,安定性差,辛烷值
约为80,经过脱硫后可直接用作汽油调合组分; 重石脑油组分经过加氢处理脱除硫及烯烃后,可作催
化重整原料; 也可将全部减粘石脑油送至催化裂化装置,经过再加
工后可以改善稳定性,然后再脱硫醇。
17
减粘柴油含有烯烃和双烯烃,故安定性差,需加氢处理才 能用作柴油调和组分。