数控车床刀片切削参数
6150数控车床技术参数
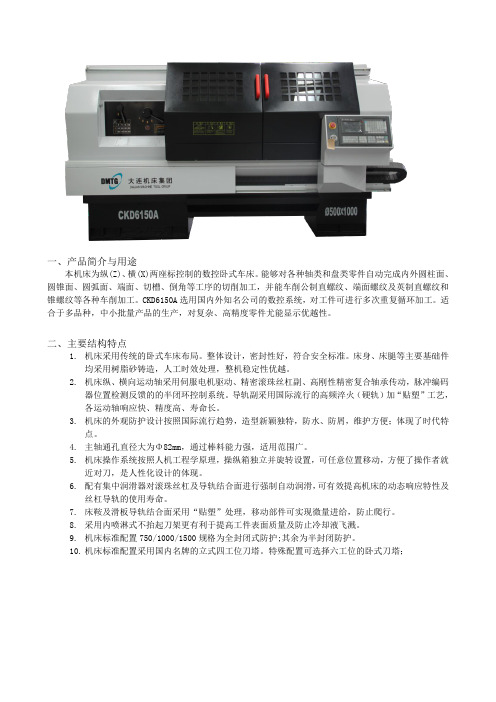
一、产品简介与用途本机床为纵(Z)、横(X)两座标控制的数控卧式车床。
能够对各种轴类和盘类零件自动完成内外圆柱面、圆锥面、圆弧面、端面、切槽、倒角等工序的切削加工,并能车削公制直螺纹、端面螺纹及英制直螺纹和锥螺纹等各种车削加工。
CKD6150A选用国内外知名公司的数控系统,对工件可进行多次重复循环加工。
适合于多品种,中小批量产品的生产,对复杂、高精度零件尤能显示优越性。
二、主要结构特点1.机床采用传统的卧式车床布局。
整体设计,密封性好,符合安全标准。
床身、床腿等主要基础件均采用树脂砂铸造,人工时效处理,整机稳定性优越。
2.机床纵、横向运动轴采用伺服电机驱动、精密滚珠丝杠副、高刚性精密复合轴承传动,脉冲编码器位置检测反馈的的半闭环控制系统。
导轨副采用国际流行的高频淬火(硬轨)加“贴塑”工艺,各运动轴响应快、精度高、寿命长。
3.机床的外观防护设计按照国际流行趋势,造型新颖独特,防水、防屑,维护方便;体现了时代特点。
4.主轴通孔直径大为Φ82mm,通过棒料能力强,适用范围广。
5.机床操作系统按照人机工程学原理,操纵箱独立并旋转设置,可任意位置移动,方便了操作者就近对刀,是人性化设计的体现。
6.配有集中润滑器对滚珠丝杠及导轨结合面进行强制自动润滑,可有效提高机床的动态响应特性及丝杠导轨的使用寿命。
7.床鞍及滑板导轨结合面采用“贴塑”处理,移动部件可实现微量进给,防止爬行。
8.采用内喷淋式不抬起刀架更有利于提高工件表面质量及防止冷却液飞溅。
9.机床标准配置750/1000/1500规格为全封闭式防护;其余为半封闭防护。
10.机床标准配置采用国内名牌的立式四工位刀塔。
特殊配置可选择六工位的卧式刀塔;三、主要技术参数1. 技术规格床身上最大工件回转直径≥φ500 mm刀架上最大工件回转直径≥φ280 mm最大工件长度≥1000mm最大加工长度≥930 mm最大车削直径≥φ500 mm主轴中心高≥250 mm床身导轨宽度≥400 mm2. 主传动标准配置主电动机(双速电机)≥6.5/8Kw主轴通孔直径≥φ82 mm主轴孔锥度前端Ф90mm 1:20主轴头≥C8主轴前端轴承内径≥φ120mm主轴转速范围≥35~1600 r/min3. 尾座装置•• 尾座套筒直径≥φ75mm尾座套筒行程≥150 mm尾座套筒锥孔锥度莫氏5号4.进给系统刀架最大行程横向(X) ≥280 mm••• 纵向(Z) ≥935mm滚珠丝杠直径×螺距横向(X)≥φ20×4 (mm)纵向(Z)≥φ40×6 (mm)••• 横向切削力(连续)横向(X)≥2500 N’••••纵向切削力(连续)纵向(Z)≥5000 N横向快速进给≥4000mm/min 纵向快速进给≥8000mm/min 切削进给范围≥0.01~500mm/r定位精度横向(X)≤0.03 mm纵向(Z)≤0.040mm(<500~1000)≤0.045mm(<1000~1500)≤0.050mm(≥1500)重复定位精度横向(X)≤0.012 mm纵向(Z)≤0.016mm(<500~1000)≤0.020 mm(<1000~1500)≤0.025 mm(≥1500)工件加工精度≤IT6~ IT7工件表面粗糙度≤Ra1.65.刀架装置标准配置:电动立式四工位刀架刀架电机功率≥180 W转速≥1500 r/min 刀杆截面25×25 mm重复定位精度≤0.008 mm换刀时间 (单工位) ≤3s6. CNC控制系统FANUC 0i Mate-MD数控系统,具有完善可靠的联锁、安全保护和故障自诊断报警等功能。
数控车床技术参数
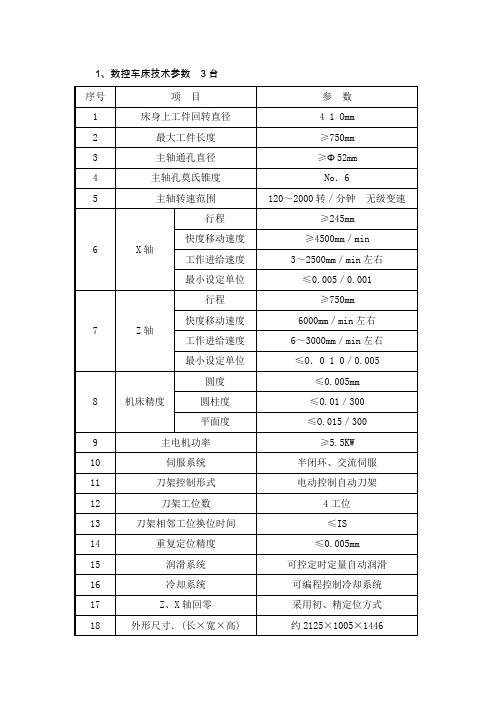
12
刀架工位数
4工位
13
刀架相邻工位换位时间
≤IS
14
重复定位精度
≤0.005mm
15
润滑系统
可控定时定量自动润滑
16
冷却系统
可编程控制冷却系统
17
Z、X轴回零
采用初、精定位方式
18
外形尺寸.(长×宽×高)
约2125×1005×1446
l9
控制系统配置
FANUC—Oi中文界面
注:要求配置相匹配的机床减震垫铁。
22
配置相匹配防震垫铁及活顶针、卡盘等附件
3、二氧化碳气体保护焊机主要技术参数:NBC--250A型1台
序号
项目
参数
1
输入电源
三相380V±10%50HZ
2
额定输入电流
14A
3
额定输入容量
9.2KVA
4
最大工作电压
27V
5
额定焊接电流
60-250A
6
额定负载持续率
60%
7
适用焊丝直径
0.8/1.0
8
No.6
11
进纹范围
l一192mm
13
英制螺纹范围
2—24tpi
l4
模数螺纹范围
O.25~48
15
径节螺纹范围
1—96DP
16
横刀架行程
320rnm
17
小刀架移动行程
140mm
18
床尾主轴最大行程
150mm
19
床尾主轴直径
Φ75mm
20
床尾主轴孔锥度
No.5
21
主电机
7.5KW
常用刀具的切削参数

常用刀具的切削参数1.钻头:钻头是一种旋转式刀具,通常用于在硬材料上钻孔。
切削速度是指钻头每分钟旋转圈数,一般以转/分钟(RPM)为单位。
切削速度的选择将受到材料类型和钻头直径的影响。
对于大型孔径和脆性材料,较低的切削速度可能更合适。
进给量是指每转刀具在轴向(沿钻孔方向)上移动的距离。
进给量的选择将受到钻头直径和材料类型的影响。
较大直径的钻头可能需要较大的进给量。
切削深度是指钻头在一次进给中的轴向深度。
如果切削深度太大,可能会导致钻头断裂或切削不洁净。
切削深度的选择还将受到材料类型和钻头直径的影响。
2.铣刀:铣刀是一种回转和前进运动刀具,常用于平面加工、开槽和切割。
切削速度是指铣刀每分钟旋转圈数,同样以转/分钟(RPM)为单位。
切削速度的选择将受到材料类型、铣刀材料和刀具直径的影响。
进给量是指铣刀在工件表面上移动的距离。
较大的进给量将导致更高的切削速度,但也可能影响切削表面的质量。
切削深度是指铣刀在一次运动中与工件表面的最大距离。
切削深度的选择将受到材料类型和铣刀直径的影响。
3.车刀:车刀是一种在工件上进行旋转切削的刀具,常用于车削和车削加工。
切削速度是指车刀每分钟旋转圈数,仍然以转/分钟(RPM)为单位。
切削速度的选择将受到材料类型、车刀材料和刀具直径的影响。
进给量是指车刀在工件上移动的距离。
较大的进给量可以提高生产效率,但也可能影响切削表面的质量。
切削深度是指车刀与工件表面的最大距离。
切削深度的选择将受到材料类型和车刀直径的影响。
4.锯片:锯片是一种用于切割材料的刀具,常用于金属、木材和塑料加工。
切削速度是指锯片每分钟旋转圈数,仍然以转/分钟(RPM)为单位。
切削速度的选择将受到材料类型、锯片材料和刀具直径的影响。
进给量是指锯片在工件上移动的距离。
较大的进给量可以提高切割速度,但也可能导致切割表面质量的下降。
切削深度是指锯片与工件表面的最大距离。
切削深度的选择通常由锯片的直径和材料类型确定。
数控车床CK6140主要参数
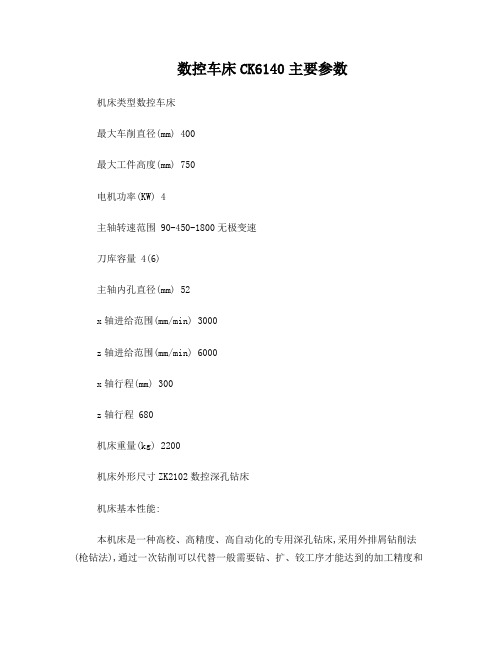
数控车床CK6140主要参数机床类型数控车床最大车削直径(mm) 400最大工件高度(mm) 750电机功率(KW) 4主轴转速范围 90-450-1800无极变速刀库容量 4(6)主轴内孔直径(mm) 52x轴进给范围(mm/min) 3000z轴进给范围(mm/min) 6000x轴行程(mm) 300z轴行程 680机床重量(kg) 2200机床外形尺寸ZK2102数控深孔钻床机床基本性能:本机床是一种高校、高精度、高自动化的专用深孔钻床,采用外排屑钻削法(枪钻法),通过一次钻削可以代替一般需要钻、扩、铰工序才能达到的加工精度和表面粗糙度。
本机床采用数控系统控制,不但有单动功能,它还具有自动循环的功能。
该机床整体精密铸造床身,精密滚柱丝杆、直线导轨转动,具有刚性强、加工效率高、运动平稳、精度保持性好;有足够的静态、动态、热态刚度,防护装置安全可靠;所选用控制和驱动系统精度高、可靠性好、响应速度快。
机床使用操作,维修方便,造型美观。
四、机床主要技术参数1.钻孔直径范围 4-25mm2.最大钻孔深度 1500mm3.钻杆箱主轴转速范围(无级) 500-5000r/min4.拖板进给速度范围(无级) 10mm-500mm/min5.拖板快速移动范围 3m/min6.切削冷却液最大压力(可调) 10Mpa7.切削冷却液最大流量(可调) 100L/min8.进给电机额定扭矩(交流伺服电机) 11Nm9.钻杆箱交流伺服主轴电机功率 4Kw10.主轴中心至T型槽工作台面的高度 220mm12.机床总功率约 18kW13.钻孔长径比≦12014.机床总重(约) 5T15.机床总外观尺寸(长x宽x高) 5200x3300x1800 XD-40立式数控铣床主要技术参数:1、工作台工作台规格长×宽(mm) 800×400T型槽尺寸槽宽(mm) 18H7×130×3(中央T型槽) 工作台最大载重(kg) 3002、坐标范围X坐标(mm) 600Y坐标(mm) 400Z坐标(mm) 540主轴中心线距Z向导轨面距离(mm) 460主轴断面距工作台上平面距离(mm) 150--6903、进给X、Y、Z向切削进给速度(mm/min) 1—5000X、Y、Z向快速进给速度(m/min) 20(X、Y) 15(Z) 主轴最高转速(r/min) 5000(8000可选)4、主轴系统主轴功率(kW) 7.5/11(SIEMENS系统:7/9.25)主轴锥孔NO.40 主轴前支承直径(mm) Φ70主轴轴承润滑方式油脂润滑5、精度定位精度(mm) (国标) X、Z:0.020 Y:0.016重复定位精度(mm) (国标) X、Z:0.008 Y:0.0066、加工能力最大钻孔直径(mm) Φ22最大镗孔直径(mm) Φ100主轴最大扭矩Nm 71(FANUC主轴电机)58.9(SIEMENS主轴电机)70.1(武汉华中数控主轴电机)主轴额定扭矩Nm 48.4(FANUC主轴电机)44.6(SIEMENS主轴电机)47.8(武汉华中数控主轴电机)7、设计制造标准符合ISO标准8、工作电源AC380V±10%;50HZ9、工作环境温度8—40度湿度≤80% 气压0.5Mpa10、其它机床轮廓尺寸(mm) 2110×2170×2780机床占地面积m2 6.4主机重量(kg) 6000。
数控机床加工的切削用量

单元4数控机床加工的切削用量教学目的1、了解数控机床的运动(主运动、进给运动);2、了解数控机床加工刀具的角度及其作用;3、了解数控机床加工中有关切削层的参数及其作用;4、了解数控机床加工中的切削用量及其选用原则。
5、掌握常用不同材料零件在粗加工、半精加工和精加工时的切削用量选用;教学重点1、数控机床加工刀具的角度及其作用;2、数控加工中粗加工、半精加工和精加工时的切削用量选择;教学难点1、刀具的角度及其作用;2、切削用量选用教学方法讲练结合教学内容一、车削加工与刀具1. 车削加工原理在普通车床和一般数控车床上,可以进行工件的外表面、端面、内表面以及内外螺纹的加工。
对于车削中心,除上述各种加工外,还可进行铳削、钻削等加工。
从上述介绍可以看出:在切削过程中,刀具和工件之间必须具有相对运动,这种相对运动称为切削运动。
根据切削运动在切削过程中的作用不同可以分为主运动、和进给运动。
各种机床的主运动和进给运动参见下表。
主运动是指机床提供的主要运动。
主运动使刀具和工件之间产生相对运动,从而使刀具的前刀面接近工件并对工件进行切削。
在车床上,主运动是机床上主轴的回转运动,即车削加工时工件的旋转运动。
2)进给运动进给运动是指由机床提供的使刀具与工件之间产生的附加相对运动。
进给运动与主运动相配合,可以形成完整的切削加工。
在普通车床上,进给运动是机床刀架(溜板)的直线移动。
它可以是纵向的移动(与机床主轴轴线平行),也可以是横向的移功(与机床主轴轴线垂直),但只能是一亇方向的移动。
在数控车床上,数控车床可以同时实现两亇方向的进给,从而加工出各种具有复杂母线的回转体工件。
在数控车床中,主运动和进给运动是由不同的电机来驱动的,分别称为主轴电机和坐标轴伺服电机。
它们由机床的控制系统进行控制,自动完成切削加工。
2. 切削用量切削用量是指机床在切削加工时的状态参数。
不同类型的机床对切削用量参数的表述也略有不同,但其基本的含义都是一致的,如下图所示。
数控机床用刀具系统参数介绍讲述
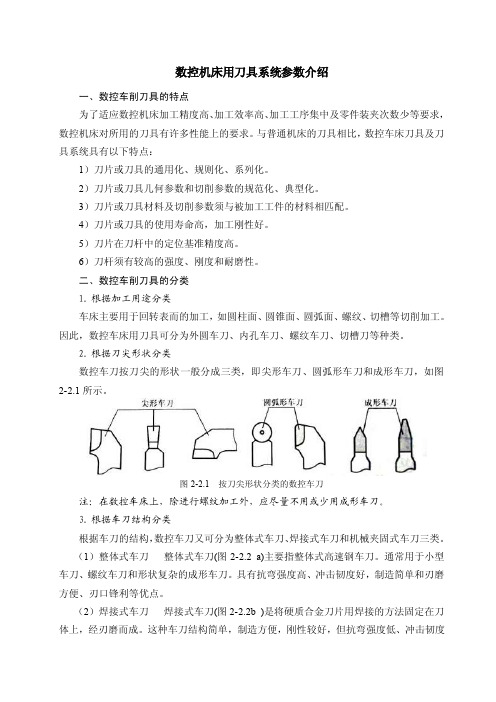
数控机床用刀具系统参数介绍一、数控车削刀具的特点为了适应数控机床加工精度高、加工效率高、加工工序集中及零件装夹次数少等要求,数控机床对所用的刀具有许多性能上的要求。
与普通机床的刀具相比,数控车床刀具及刀具系统具有以下特点:1)刀片或刀具的通用化、规则化、系列化。
2)刀片或刀具几何参数和切削参数的规范化、典型化。
3)刀片或刀具材料及切削参数须与被加工工件的材料相匹配。
4)刀片或刀具的使用寿命高,加工刚性好。
5)刀片在刀杆中的定位基准精度高。
6)刀杆须有较高的强度、刚度和耐磨性。
二、数控车削刀具的分类1.根据加工用途分类车床主要用于回转表而的加工,如圆柱面、圆锥面、圆弧面、螺纹、切槽等切削加工。
因此,数控车床用刀具可分为外圆车刀、内孔车刀、螺纹车刀、切槽刀等种类。
2.根据刀尖形状分类数控车刀按刀尖的形状一般分成三类,即尖形车刀、圆弧形车刀和成形车刀,如图2-2.1所示。
图2-2.1 按刀尖形状分类的数控车刀注:在数控车床上,除进行螺纹加工外,应尽量不用或少用成形车刀。
3.根据车刀结构分类根据车刀的结构,数控车刀又可分为整体式车刀、焊接式车刀和机械夹固式车刀三类。
(1)整体式车刀整体式车刀(图2-2.2 a)主要指整体式高速钢车刀。
通常用于小型车刀、螺纹车刀和形状复杂的成形车刀。
具有抗弯强度高、冲击韧度好,制造简单和刃磨方便、刃口锋利等优点。
(2)焊接式车刀焊接式车刀(图2-2.2b )是将硬质合金刀片用焊接的方法固定在刀体上,经刃磨而成。
这种车刀结构简单,制造方便,刚性较好,但抗弯强度低、冲击韧度差,切削刃不如高速钢车刀锋利,不易制作复杂刀具。
(3)机械夹固式车刀机械夹固式车刀(图2-2.2c)是将标准的硬质合金可换刀片通过机械夹固方式安装在刀杆上的一种车刀,是当前数控车床上使用最广泛的一种车刀。
a)b)c)图2-2.2 按刀具结构分类的数控车刀a)整体式车刀b)焊接式车刀c)机械夹固式车刀三、数控车削刀具的材料常用的数控刀具材料有高速钢、·硬质合金、涂层硬质合金、陶瓷、立方氮化硼,金刚石等。
数控车床参数

参数 φ 400mm φ 200mm φ 200mm 四工位 850mm φ 53mm
A1-6 7.5kw 150-2400 r/min (手卡 1600) φ 60mm 140mm 莫氏 4 号 220mm 850mm 3.8/7.6 m/min
4 20×20mm 0.012/0.016mm IT6-IT7 2490×1360×1510mm 1990/2290kg 2770×1660×2200mm
沈阳数控车床 CAK4085di 技术参数
项目 床身上最大回转直径 滑板上最大回转直径 滑板上最大切削直径 最大加工长度 主轴通孔直径 主轴头型式 主电机功率(变频)
主轴转速
尾台套筒直径 尾台套筒行程 尾台套筒锥孔 X 轴最大行程 Z 轴最大行程 快移速度(X/Z 轴) 刀架刀位数 刀具安装尺寸 X/Z 轴重复定位精度 加工精度 机床外形尺寸(长×宽×高) 机床净重/毛重 包装箱尺寸(长×宽×高)
机床净重
参数 410mm(16")
Φ 230mm 230mm 1000mm 5m/min 8m/min 200-2800r/min Φ 52 MT No.6 8" or 5c 四工位 1.0/1.5KW
(伺服电机) 20×20mm 0.001mm 0.001mm 0.0075/0.01mm ≤Ra0.8μ m(有色金属)≤Ra1.6μ m(钢件) 3.7KW(5HP) 2370×1200×1415mm
2200kg
浙江凯达数控车床 CK6140s/1000 技术参数
Байду номын сангаас
项目 床身上最大回转直径 刀架上最大回转直径 横向最大行程(X 轴)
最大工件长度 X 轴快速进给 Z 轴快速进给 主轴转速范围(无级) 主轴通孔直径
1-3常用的切削参数名词定义及算法

3常用的切削参数名词定义及算法切削深度ap:在机床、工件和刀具刚度允许的情况下,ap就等于加工余量,这是提高生产率的一个有效措施。
为了保证零件的加工精度和表面粗糙度,一般应留一定的余量进行精加工。
数控机床的精加工余量可略小于普通机床。
单位为mm切削宽度L:一般L 与刀具直径 d 成正比,与切削深度成反比。
经济型数控机床的加工过程中,一般L的取值范围为:L=(0.6~0.9)d。
单位为mm切削速度Vc:切削速度是指刀具在去除公件余量时的移动速度。
单位为m/min 或者mm/min.Vc=π*D*N/1000主轴转速N:是指机床主轴转动的速度,车床是工件转动,铣床是刀具转动。
单位为n/min每转进给f:是指刀具在切削时每转一圈的移动距离,单位为mm/Nf=Vc/N每齿进给fz:在切削过程中刀具转动一圈时每刃的切削厚度,单位为mm/刃fz=Vc/(N*刃数)线速度:线速度就是刀片和工件接触位置的相对速度对于车床来说,是刀具不动(进给速度在这里可以忽略不计)工件旋转,所以工件和刀具的接触位置的速度就是切削线速度,即:V=π*D*n/1000,其中π是圆周率,D是刀具和工件接触点的旋转直径,n是主轴转速。
n的单位是转/分,D的单位是毫米,最终结果V的单位是米/分。
对于加工中心来说,是工件不动,刀具旋转,所以刀尖的速度就是线速度,计算公式同样是:V=π*D*n/1000,其中π是圆周率,D是刀尖位置的实际旋转直径,n是主轴转速。
从这两个计算公式可以看出线速度和进给F以及切深是无关的。
由于作为刀片,切削的线速度是最重要的参数之一,因此在刀具的说明书上,针对不同的切削要求都会给出相应的切削线速。
- 1、下载文档前请自行甄别文档内容的完整性,平台不提供额外的编辑、内容补充、找答案等附加服务。
- 2、"仅部分预览"的文档,不可在线预览部分如存在完整性等问题,可反馈申请退款(可完整预览的文档不适用该条件!)。
- 3、如文档侵犯您的权益,请联系客服反馈,我们会尽快为您处理(人工客服工作时间:9:00-18:30)。
数控车床刀片切削参数
数控车床刀片的切削参数包括以下几个方面:
1. 等效切削速度(Vc):数控车床刀片的等效切削速度是指刀具在进行切削时对工件表面每分钟实际移动的线速度。
等效切削速度与切削材料、刀具材料、转速和进给速度等因素有关。
2. 进给速度(F):进给速度是指工件在切削过程中每分钟所移动的距离,即工件进给速率。
进给速度与刀具的几何形状、切削材料和刀具材料等有关。
3. 切削深度(Ap):切削深度是指刀具在进行切削时,每次切削所能切掉的工件材料厚度。
切削深度与刀具材料、刃数、切削参数等参数有关。
4. 切削宽度(Ae):切削宽度是指刀具在每次切削时所能切削的工件材料的宽度。
切削宽度与刀具材料、刃数、切削参数等参数有关。
5. 转速(n):转速是指数控车床刀具所使用的高速旋转的速度。
转速与切削材料、刀具材料、等效切削速度等因素有关。
6. 切割力(Fc):切割力是指数控车床刀具在切削时对工件及刀具的作用力。
切割力与切削材料、刀具材料、切削参数等参数有关。