常用的几种铝合金熔体除碱技术简介
铝及铝合金的熔体净化(baidu)

夹杂物的生成途径主要是: • 从炉村中吸收杂质; • 从熔剂和熔炼添加剂中吸收杂质; • 从炉气中反应并吸收杂质; • 从炉料及炉渣中吸收杂质。
•夹杂物的危害
并不是熔体中的所有异物都是有害夹杂。金属中 非金属异质点的形态和大小,对金属性质有重要影 响。细小,弥散均匀分布的夹杂颗粒,在金属凝固 时,可以成为结晶的异质核心,同时也可以阻碍晶 粒的长大,起到细化晶粒的作用。所以高纯铝较一 般的工业纯铝更容易形成粗大晶粒。
• 非金属夹杂的种类很多,按其化学成分可分为氧 化物(FeO,SiO2,Al2O3,TiO2,MgO,ZnO等);氮化 物(AlN,ZrN,TiN等);硫化物(Ni3S2,CeS,Cu2S 等);氯化物(NaCl,KCl,MgCl2等);氟化物 (CaF2,NaF等);硅酸盐(Al2O•SiO2等)。这些 夹杂以不同形态和大小分布在金属熔体中,对金 属性能产生不同影响。
铝及铝合金的熔体净化
• 有色金属及其合金熔体在熔炼过程存在气体、各 种非金属夹杂物等,影响金属的纯洁度,往往会使 产品产生气孔、夹杂、疏松、裂纹等缺陷,影响铸 锭的加工性能及制品强度、塑性、抗蚀性、阳极 氧化性和外观质量。同时,在有色金属中除气体 和非金属夹杂之外,还含有少量的金属杂质,如 铝合金的钠、钙等低熔点金属。钠在含镁量高的 镁-铝系合金中易引起热裂敏感性,合金热轧时易 产生开裂,通常称之谓“钠脆性”,此外还影响 熔体的流动性和铸造性。
Al中Al2O3夹杂物的形态(两维)
Al中Al2O3夹杂物的形态(三维)
AlN
采用先进的测渣方法捕捉到的夹渣
Refractories
采用先进的测渣方法捕捉到的夹渣
• 夹杂物的来源与危害 • 杂质的吸收和积累主要是熔炼过程中,金属熔体
铝合金化学清洗方案

铝合金化学清洗方案铝合金是一种常用的材料,应用范围广泛,但在使用过程中容易受到污染,如油脂、氧化物等,这些污染会影响铝合金的使用寿命和美观度。
因此,对铝合金进行清洗非常重要。
本文将介绍几种铝合金化学清洗方案。
氢氧化钠清洗氢氧化钠盐(NaOH)是一种不危险化学品,可用于清洗铝合金表面。
该清洗方案的工作原理是利用氢氧化钠强烈的碱性,与表面氧化物发生化学反应,使其迅速分解,达到清除的目的。
具体操作步骤如下:1.准备氢氧化钠溶液,将适量的NaOH加入足够的水中制成0.1~3%的氢氧化钠溶液。
2.将铝合金件放入氢氧化钠溶液中浸泡2~10分钟,时间长短视铝合金表面的污染程度而定。
3.将铝合金件从溶液中取出,用水冲洗干净,然后用干净的棉布擦干。
使用该清洗方案需要注意的是,溶液使用后需立即丢弃,不可重复使用,因为溶液中的氢氧化钠会与空气中的二氧化碳反应生成碳酸钠,失去清洗效果。
同时,氢氧化钠具有腐蚀性,需佩戴防护手套,并注意安全使用。
氧化铝清洗氧化铝(Al2O3)是铝合金表面产生的一种氧化物,可用于化学清洗。
该清洗方案的工作原理是通过氯化铵和氮的协同作用,将铝合金表面的氧化铝还原为铝金属,起到清洁作用。
具体操作步骤如下:1.准备清洗溶液,将氯化铵和氮气充分混合,搅拌均匀,制成清洗溶液。
2.将铝合金件放入清洗溶液中浸泡2~10分钟。
3.将铝合金件从溶液中取出,用干净的棉布擦干。
使用该清洗方案需要注意的是,清洗溶液中切勿有水分,因为水分会使氯化铵与氮气反应生成盐酸和氨气,对人体及环境有害。
同时,该清洗方案对铝合金件有腐蚀性,需进行耐腐蚀实验后确定适合清洗的铝合金种类。
氧化磷酸清洗氧化磷酸(H3PO4)是一种较强腐蚀性的化学品,可用于清洗铝合金表面,清除铝合金表面的氧化物和污垢,并使其表面形成微粒状膜。
具体操作步骤如下:1.准备清洗溶液,将适量的氧化磷酸溶解在足够的水中,制成0.5~10%的氧化磷酸溶液。
2.将铝合金件放入溶液中浸泡,浸泡时间一般为2~10分钟。
铝的熔炼净化

铝及铝合金的熔炼及净化铝合金的熔炼是一个繁杂的过程,它包括铝合金的熔化、合金化、成分调整和净化处理等工艺。
大体说来要经过以下程序:烘炉---- 使炉体充分干燥,防止使用时释放出水气而导致氢含量增加,特别是新炉更应彻底烘烤。
洗炉---- 如果炉子不是熔化某一合金专用的,从一种合金转到不同牌号的另一种合金时应彻底清洗,以免不同牌号合金的元素相互污染。
特别是熔炼某些高品位的合金制品时,应格外注意。
配料---- 优化配料,节省新料的用量。
这就要求废料严格按品位分类保管,存放处应保持清洁、干燥,切勿把水或其他杂物混入废料中。
来路不明的废料成分复杂,一般需复化后使用。
装炉---- 装料速度要快,减少热量散失。
先装小料、碎料,再装大块料。
易熔的在下,难溶的在上。
为防止炉料的烧损,有时要撒些覆盖剂在炉料上面。
熔化---- 其核心就是如何提高热效率,加快熔化速度,减少铝的烧损。
这已成为一个专门研究课题。
扒渣---- 如果浮渣较多,粘度较大,应加入适量打渣剂,减少渣中铝含量,松散铝渣容易扒出。
搅拌---- 搅拌有两个作用,一是使成分均匀,二是使温度均匀。
分析---- 确定熔体中已有的合金元素含量,取样应有代表性,真实性。
合金化—根据分析结果,不足的按计算量加入合金元素,超量的—如果不太多的话,可加铝冲淡分析---- 再次分析是为了确认合金化后的铝中,各合金元素是否达到要求。
没达到的组分要补足。
精练---- 此时应加入精练剂、打渣剂进行炉内净化处理。
如果静止后直接浇注,此时可加细化剂。
倒炉---- 熔炼好的铝熔体转移到静止炉中保温,熔化炉中喷撒清炉剂,除去炉壁和底部积渣。
炉外精练--- 铝熔体由静止炉出来,经由旋转除气、泡沫陶瓷板过滤等直达铸造台。
在铝熔体进入除气箱前加入AlTiB杆晶粒细化剂。
第一部分添加剂与铝合金的熔炼合金种类的多样性在纯铝中加入一定量不同种类的合金元素,就可以配制成各种不同的铝合金。
大多数金属元素在铝中的溶解度随温度升高而增加。
铝及铝合金熔体净化处理

铝及铝合金熔体净化处理铝料的表面都有一层厚薄不均的氧化膜,有时还吸附水分,夹杂灰沙,粘有油污,涂有油漆等。
在熔化时,铝料在高温环境中进一步氧化,氧化膜厚度增加,并与气氛中的水分起化学反应,生成氧化铝和氢,使氧化夹杂和气体含量增加。
所以,铝料熔化以后,必需进行净化处理,以清除铝液内部的杂质和气体。
用于净化铝液的物质统称为熔剂。
熔剂在室温多数是固体或气体,也有各别熔剂是液体,如CCl4。
固体熔剂的优点是体积小,容易运输和储存,但都具有较强的吸湿性,必需密封包装。
为了提升固体熔剂的净化效果,可将熔剂压紧成紧密小块用铝箔包裹,放入长柄的钻孔容器内插入熔池底部。
对以NaCl和KCl的混合盐为基体的熔剂,可先按配比将混合盐熔化后,加入难熔组分,例如Na3AlF6,经搅拌冷却后注入密封铁箱内。
熔剂使用前应存放在室温较高的干燥地点,如熔炉旁,以防受潮。
在熔炉内施加覆盖熔剂,可以减少熔化消耗,阻止铝液从炉膛气氛中汲取气体,但覆盖熔剂的耗用量大(约相当于铝料重量的10%),使生产成本提升,中小型铝加工厂一般不采纳。
净化熔剂的使用通常是在铝料熔化以后将按配比混合的粉状熔剂撒在熔池表面,然后用长柄工具搅动铝液促使灰渣上浮。
在搅动过程中,部分熔剂加入熔池内部,与铝液发生化学反应,生成不溶于铝的气态物质,在气泡上升过程中起除气和除灰的作用。
使用较多的一种熔剂是2份冰晶石与1份氯化铵混合的粉末,其净化铝液时的化学反应如下:Na3AlF6+Al→2AlF3+3NaNH4Cl+2Al→AlN+AlCl+2H2AlF3+2Al→3AlFAlCl3+2Al→3AlCl6AlF+3O2→2Al2O3+2AlF36AlCl+3O2→2Al2O3+2AlCl3以上化学反应中所生成的Al2O3,AlN和H2,连同铝液中原有的Al2O3和H2一起被AlF3和AlCl3气泡带出液面。
有时也用Na2SiF6作为熔剂,但其净化效果不如Na3AlF6。
铝及铝合金的熔体净化及晶粒细化

铝及铝合金的熔体净化和晶粒细化摘要:综述了铝合金熔体净化的技术特点,重点分析了气泡浮游法、过滤法、熔剂法等几种常见的熔体吸附净化方法的工作原理和工艺改进,介绍了新型的旋转脉冲喷吹工艺、超声波净化工艺和电磁净化工艺,并展望了熔体净化工艺研究发展的趋势;综述了晶粒细化剂的发展历史及细化剂的细化机理和各种细化剂的比较,并着重介绍了新一代的Al-Ti-C晶粒细化剂。
关键词:铝合金;熔体净化;细化剂;细化机理1综述近年来铝合金材料大致向两个方向发展:一是发展高强高韧等高性能铝合金新材料,以满足航空航天等军事工业和特殊工业部门的需要;二是发展一系列可以满足各种条件用途的民用铝合金新材料。
与国外相比,我国铝合金研究的整体水平还比较落后,基础理论研究和技术装备水平及其完善程度都与国外的差距很大。
目前,铝合金研究的重点之一是研究和采用各种先进的熔体净化与变质处理方法,去除铝液中的气体和夹杂物,降低杂质含量,提高铝熔体的纯度,细化铝的晶粒从而改善铝合金的性能。
这也是可持续发展战略中废铝回收亟待解决的技术难题。
熔体净化是保证铝合金材料冶金质量的关键技术,引起企业界的广泛关注。
铝合金熔体净化的目的,主要是降低熔体中的含气量和非金属夹杂物含量。
对熔体纯洁度的要求,一般铝合金制品的含气量应小于0.15ml/100gAl,特殊的航空材料要求在0.10ml/100gAl以下;钠含量应在5ppm以下;非金属夹杂物不允许有1~5Lm尺寸的颗粒和聚集物,夹杂物含量越低越好。
可见,对铝合金熔体的纯洁度要求是非常严格的。
要达到上述要求,需采用各种先进的净化处理技术。
铝及其合金组织的微细化,可显著提高铝材的力学性能和加工工艺性能。
晶粒细化处理是使铝及其合金组织微细化,获取优质铝锭,改善铝材质量的重要途径。
铝加工工业的迅速发展促进了各种铝晶粒细化剂的开发与生产。
本文将在初步总结和分析国内外熔体净化和晶粒细化剂生产实践及文献资料的基础上,较全面地讨论各种铝合金熔体净化技术及其发展趋势,讨论各种晶粒细化剂及发展趋势。
铝合金熔体净化工艺概述

陶瓷泡沫是近年来发展起来的新型陶瓷过滤材料,它是由氧 化铝和氧化铬等组成的陶瓷浆料,借助聚氨酯泡沫成型,再经干 燥、烧结而成。孔隙率高达 80%~90%。它的特点是使用方便, 过滤效果好,过滤时不需要很高的压头,价格便宜。
但陶瓷泡沫较脆,易破损,通常只能使用一次。为了增加过 滤效果,可采用双级过滤法,如DFU法等。
3、熔剂法
熔剂法是将熔剂加入到熔体内部,通过一系列物理化学作用,达到除气 除杂的目的。
熔剂的除杂能力是由熔剂对熔体中氧化夹杂物的吸附作用和溶解作用以 及熔剂与熔体之间的化学作用所决定的。因为氧化夹杂物是不被铝液润湿的, 二者之间的界面张力很小。
熔剂吸附熔体中的氧化夹杂后,能使系统的表面自由能降低,因此,熔 剂具有自动吸附氧化夹杂的能力,这种吸附作用是熔剂除杂的主要原因。熔 剂和夹杂物之间的界面张力愈小,而溶剂和金属的界面张力及铝液和夹杂物 之间的界面张力愈大,则熔剂的吸附性愈好,除杂作用愈强。
5、提高铝熔体净化效果的主要途径
避免片面追求低氢含量的倾向,才有利于开发研制更为有效的铝液净化新 技术。
在以除杂为主的净化方法中,过滤法一般是在除气后浇注前进行的(如 过滤网安放在浇口或流槽等处),其除杂机理主要是机械的和物理的作用, 对悬浮在熔体中微细夹杂的排除作用并不显著,并且该法难以实现先排杂后 除气的原则;
熔剂对氧化物的溶解作用是由熔剂的本性所决定的,通常,当熔剂的分 子结构与某些氧化物的分子结构相近或化学性质相近时,在一定温度下可以 产生互溶。
熔剂的除气作用主要表现在三个方面: 1)随络合物的除去而除去被氧化夹杂所吸收的部分络合氢; 2)熔剂产生分解或与熔体相互作用时形成气态产物,进行扩
散除氢,如产生AlCl3、N2、CO2和SiF4等; 3)由于熔体表面氧化膜被溶解而使得溶解的原子氢向大气扩
铝合金熔体净化工艺

铝合金熔体净化工艺3Ξ上海交通大学 蒋海燕ΞΞ 孙宝德 倪红军 丁文江摘 要 分析总结了各种铝合金熔体净化方法的技术特点,并简要介绍了最新发展的新工艺。
在旋转喷吹除氢的基础上,提出了一种脉冲进气法,可使喷吹出的气泡尺寸减小至μm 级,大大提高了气泡在熔体中的比表面积,与传统的恒压进气方式相比较,脉冲进气法可增加进气压力,减小转子转速,使熔体液面平稳并可削弱合泡现象。
关键词:铝合金 净化 工艺中图分类号:TF111.18 文献标识码:A 文章编号:1001-2449(2001)02-0048-02图1 连续净化装置示意图1 熔体净化方法铝合金净化方法按其作用原理可分为吸附净化和非吸附净化两个基本类型。
吸附净化是指通过铝熔体直接与吸附剂(如各种气体、液体、固体精炼剂及过滤介质)相接触,使吸附剂与熔体中的气体和固态氧化夹杂物发生物理化学的、物理的或机械的作用,达到除气、除杂的目的。
属于吸附净化的方法有:吹气法、过滤法、熔剂法等等。
非吸附净化是指不依靠向熔体中加吸附剂,而通过某种物理作用(如真空、超声波、密度差等),改变金属2气体系统或金属2夹杂物系统的平衡状态,从而使气体和固体夹杂物从铝熔体中分离出来的方法。
属于非吸附净化方法的有:静置处理、真空处理、超声波处理等。
1.1 吹气法吹气法又称气泡浮游法,它是将惰性气体(如氮气、氩气等),通入到铝熔体内部,形成气泡,熔体中的氢在分压差的作用下扩散进这些气泡中,并随气泡的上浮而被排除,达到除气的目的。
气泡在上浮的过程中还能吸附部分氧化夹杂,起到除杂的作用[1,2]。
吹气法是20世纪70年代发展起来的铝熔体净化工艺[3],主要用于除氢,按其气体导入方式,可分为单管吹气法、多孔喷头吹气法、固定喷吹法、旋转喷吹法。
吹气法的效果一方面取决于惰性气体的性质和纯度,更主要的取决于气泡的大小和气泡在熔体中的分散程度,如果吹入的气泡直径越小,分布越均匀弥散,则气泡比表面积越大、熔体中的氢扩散进气泡的路程越短、气泡上浮越慢、除气率越高,另外,还取决于吹气时间、吹气压力、吹气温度等工艺参数[4,5]。
铝熔体净化处理方法分析
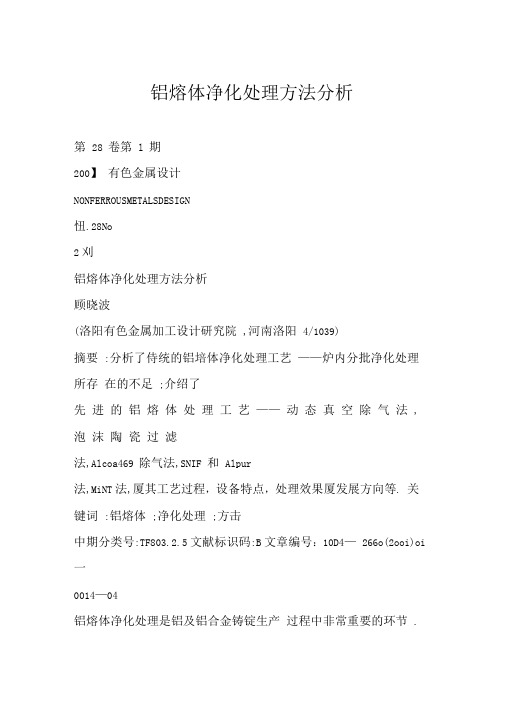
铝熔体净化处理方法分析第28 卷第l 期200】有色金属设计NONFERROUSMETALSDESIGN忸.28No2刈铝熔体净化处理方法分析顾晓波(洛阳有色金属加工设计研究院,河南洛阳4/1039)摘要:分析了侍统的铝培体净化处理工艺——炉内分批净化处理所存在的不足;介绍了先进的铝熔体处理工艺——动态真空除气法, 泡沫陶瓷过滤法,Alcoa469 除气法,SNIF 和Alpur法,MiNT法,厦其工艺过程,设备特点,处理效果厦发展方向等. 关键词:铝熔体;净化处理;方击中期分类号:TF803.2.5文献标识码:B文章编号:10D4—266o(2ooi)oi 一0014—04铝熔体净化处理是铝及铝合金铸锭生产过程中非常重要的环节.传统铝液净化处理工艺一般都是在保温炉内分批进行操作的, 普遍采用氮——氯混合气体,熔剂进行精炼.这种净化处理工艺,大多由人工操作, 除气率低,精炼不彻底,铝液在从保温炉向铸造机输送过程中,铝液会再次被污染,且工人劳动强度大,劳动环境差,污染严重, 对大容量的炉子.人工操作难以实现.随着航空用高质量铝合金,双零铝箔等高精制品的出现,对锭坯的质量要求越来越高,传统的铝液净化处理工艺已不能适应大规模生产,高质量锭坯的要求.为此,国内外有关人士经过长期摸索,做了大量的工作,开发出了先进的铝熔体净化处理新工艺——炉外铝熔体净化处理新工艺,即铝熔体在从保温炉向铸造机输送过程中,进行精炼,过滤处理, 可以高效去除熔体中的可溶和不溶的杂质 1 铝熔体净化目的1.1铝熔体中存在的杂质1.1.1氢铝及铝合金在熔炼过程中,氢极易溶解于液态铝中,在冶炼温度范围内,温度越高气体溶解度越高,特别是在固态一液态相变时,气体溶解度骤然增高,详见表 1.裹 1 氢在铝中的溶解度nd./10~在熔点温度时高于熔点温度时1.1.2 非金属夹杂铝熔体中存在的非金属夹杂物有:(1)氧化物:AI2,MgO,sjo2,A12等;(2)残余的细化剂Al—Ti—B 中间合金的粗大一 B 粒子;(3)耐火砖碎片,脱落的流槽和工具上的保护涂料.1.2铝熔体净化目的和要求熔体中存在的气体,各种夹杂物熔体中氢溶解度要求mlJl00g 以下,对于一些特殊要求0.15 〜0.2的制品, 应在0.1mlJl00g 以下.2 铝熔体净化机理铝熔体净化处理根据净化机理的不同, 可分为吸附净化和非吸附净化两大类.2.1 吸附净化靠精炼剂产生的吸附作用达到去除气体和氧化物夹杂的目的.2.1.1 惰性气体净化惰性气体是指与铝熔体及溶解的氢不起化学反应,叉不溶解于铝中的气体,通常使用氩气,氮气. 惰性气体刚吹人铝熔体中时,惰性气体气泡中氢的分压PH=0,惰性气体气泡和铝液的界面上有氢的压力差,使金属中的氢不断地扩散进惰性气体气泡中,惰性气体气泡浮出液面后,气泡中的氢随之逸出由于铝液和氧化物夹杂互不湿润,使夹杂与惰性气体气泡之间满足金—杂+金—气> —公式,根据热力学第二定律,铝液中的氧化物夹杂能自动吸附在惰性气体气泡上而被带出液面.由此可以得出结论,惰性气体气泡与铝熔体的接触面积越大,净化效果就越好.2.1.2 活性气体净化对于铝来说,活性气体主要是指氯气. 氯气本身不溶于铝中,但氯气和铝及溶于铝中的氢会发生如下反应: ck+H2—2Hcb 十3caz+2AI--~2AICt3+反应生成物HC1和alch(沸点183oC)均为气态,不溶于铝液,和未参加反应的氯气一起都能起精炼作用.氯气精炼效果虽好,但它对人体有害,污染环境,易腐蚀设备及加热元件,因此,在实际生产中大多用氮一氯混合气体进行精炼,以提高精炼效果,减少其危害作用.2.2 非吸附净化非吸附净化包括真空处理和机械过滤. 真空处理,主要是去除铝熔体中的氢,即在真空状态下,铝熔体的吸气倾向趋于零,而且溶解在铝液中的氢有强烈的析出倾向;机械过滤,是靠微孔过滤去除铝熔体中的不溶3 铝熔体净化处理新工艺铝熔体净化处理方法很多,归纳起来大致可分为三大类:(1)以除气为主的方法有ASV 公司的动态真空除气法;(2)以除不溶性夹杂物为主的凯撒公司的陶瓷管过滤法和柯那尔公司的泡沫陶瓷过滤法;(3)既可除气,又可去夹杂物的有英国铝业公司的FILD 法,美国铝业公司的A1.Coa469法,美国联合碳化物公司的SNIF法, 法国彼西涅公司的Alpur 法,美国联合铝业公司的MINT 法.3.1 除气为主的净化处理方法——动态真空障气洼动态真空除气是相对于静态真空除气而言的.在熔炼温度范围内,铝液表面有致密的Y—AJ203 膜存在,阻碍氢的析出.因此, 必须清除这层氧化膜的阻碍作用才能获得好的除气效果.静态真空除气是在真空处理的同时,在熔体表面撒上一层溶剂以便使氢气通过氧化膜除气,但从使用情况来看,除气效果并不好.1969 年,挪威ASV 公司开始采用动态真空除气工艺来净化铝液.动态真6 有色金属设计第28 卷空除气的工艺过程是先将真空炉抽成10m 的真空,然后打开进料口密封盖, 把从保温炉来的铝熔体借真空抽力喷人真空室内,喷人真空室内的熔体,呈细小弥散的液滴,因而,溶解在铝液中的氢能快速扩散出去,钠被蒸发燃烧掉.动态真空处理的除气速度,取决于氢的扩散速度和扩散面积, 为了提高除气速度,必须增大熔体与真空气氛的接触面积.使用结果表明,经动态真空处理后的铝熔体氢溶船度低于0.12 mL/100g.动态真空除气工艺的优点是:除气效果好,无公害,处理过程造渣少;缺点是:除其它有害杂质的效果差,不能实现连续处理,设备结构复杂,设备价格昂贵,而且设备的密封性难以保证.3.2除不溶性夹杂物为主的净化处理方法饱沫陶瓷过滤法泡沫陶瓷是近年发展起来的新型陶瓷过滤材料.柯那尔公司泡沫陶瓷过滤板是用氧化铝,氧化钙等制成的海绵状多孔板.用该工艺处理铝液的工艺过程是:在保温炉和铸造机之间的流槽上,放人该装置,将该装置加热到一定温度后,开始放流铸造,以实现铝熔体的连续过滤.过滤板的孔隙大小,形状以及板的厚度,对过滤的效果有很大的影响.一般板厚为50Hn孔隙率达85%9D%.这种工艺能过滤微量级的氧化物夹杂. 效果好而且成本低,设备结构简单,使用方便,适用于各种合金.事实证明,使用该装置后,3003 合金印刷板成品率提高了9%; 1145 合金电容器铝箔两次断头间的平均重量提高了45%;6063 台金建筑铝型材挤压速度提高20%.其缺点是该工艺本身不具有除氢功能,过滤板需定期更换,易破损, 常给生产带来麻烦.3.3既可除气,又可去夹杂物的净化处理方法3.3.1Alcoa469 除气法此工艺是美国铝业公司研究成功的铝液在线处理工艺,可实现铝液连续净化.见图 1.出口At+At+C]2固1Alcoa469 蝽体处理装置熔体 2 一氧化铝球 3 气体扩散器 4 一隔板该装置有 2 个处理室(称为两单元),采用氩一氯混台气体精练和氧化铝球过滤在此装置中,熔体先经粗过滤床过滤,再经细过滤床过滤流向铸造机.在 2 个过滤床的底部设有气体扩散器,气体的流向与熔体的流向相反并均匀分布到整个过滤床截面上经Alcoa469 法处理的铝液氢溶解度可控制在0.15mL/100g 以内,见表 2.袁2Alcoa469 装置除氢效果表AA铝{庄流量给气量氢溶解度/(?h '' )/(?h '' )/(?1130 '' g) 3.3.2SNIF 法和Alpur 法这两种方法都是利用快速旋转的石墨气体喷头使精练气体呈微细气泡喷出分散于熔体中,从而达到去除熔体中的氢和部分氧化物夹杂的目的.SNIF 法是美国联合碳化物公司发明的种在线式铝熔体处理装置.该装置是用惰性气体喷人快速旋转的石墨喷嘴,喷嘴是由锭子和转子组成,惰性气体从高速旋转的转第l 期麒晓渡:铝髂#净化处理方{ 盎分析子和锭子之间的缝隙(<5mm) 喷出,惰性气体变成极细的弥散气泡,由于转子高速旋转搅拌金属液,使得弥散气泡均匀分布在整个熔体中,增大了气体与熔体的接触面积,使可溶性氢更有效地进入气泡中,使之与气泡一起上浮排除,从而达到快速,高效地从熔体中清6710140 g 640】600756016—020006—0】l45—6250.30.1057O230156.5015—023009—01240—478 0.301260AJ.pm”法由法国彼西涅公司发明,1981 年1O 月取得专利.该方法与SNW 法除气工艺类似,但喷嘴设计与SNIF 不同,其结构更为简单.在喷头上有两种不同形式的通道,一种是径向排列的8条小通道(I〜 3 一),小通道同转动的中空心轴相通,喷人惰性气体;另一种为锥形排列的8 条大通道(帆一15rm n),通道中心交点与喷头转动轴同心,通道中心线与转动轴成45o 角,喷头上有4 个叶片,在高速转动下搅拌金属液,使气泡细小而分布均匀,它同时能搅动熔体进入喷嘴内使金属液与气充分混合,因此使净化效果提高.据资料介绍,除气效率可达75%.3.3.3M 法MINT 法是美国联合铝业公司研制, 1982 年以后开始在工业上使用.该方法是将熔体从装置上方成切线方向流入反应器内,并以螺旋状向下流动.在反应器底部装有高压气体喷嘴,喷入细小的氩一氯气泡, 气泡上浮,熔体向下流动,在漩涡流动作用下,把细小气泡均匀弥散分布到熔体中,把熔体中的氢除去.熔体从反应器底部流出, 通过上升管流入泡沫陶瓷过滤器,氧化物夹杂则被过滤掉.该装置用氩气加上0.5%一3%的氯气, 除氢效率可达48%一73%,见表4;金相低倍检查除氧化物夹杂的效率可达90%,见表 5..表4MINT 除氢效果表(下转菇*页J有色金属设计第28 卷应用,积累了一些实践经验,装置及规模也参考文献不断地向过滤法由于其本身不具有除气功能,生产上往往不单独使用;Alcm469 法由于要定期更换氧化铝球,使用前要加热过滤床.因此使用起来方便性较差;Mpur 与sN 装置除气效果好,使用方便,深受广大用户的青睐.Alpllr与SMF相比较,设备结构简单,价格便宜,处理箱内衬没有石墨材料,使用寿命长,炉内不用气体保护,清渣方便,生产上常将Mpur 和sN 与泡沫陶瓷过滤相结合,净化效果更好.MINT 结构最简单,没有同熔体接触的运动部件,占地面积小,更换合金品种方便,除渣效率高,更加适用于多合金生产的熔铸机组上使用. 当然,上述净化方法也存在着以下缺点:八、、-(1)由于装置处在保温炉和铸造机之间,拉长了保温炉和铸造机的距离,增加了不必要的面积;而且由于距离的拉长,除气箱一定要加热,增加了能耗. (2)在更换合金品种时,除气箱内的铝液要排放掉,给生产造成了很大的不方便. 而且,除气箱中的原有铝液将作为废品处理,增加了生产成本. 在有效地净化铝熔体的前提下如何解决上述问题,是摆在我们每个铝加工工作者面前的重要课题.国外目前正在研制开发的所谓紧凑型净化处理设备虽然较好地解决了上述问题,但密封及快速撇渣问题仍未解决. 我们相信,经过努力,在不远的将来,一定会使铝熔体净化处理工艺在节约资源,节能,环保及生产上取得突破性进展.。
- 1、下载文档前请自行甄别文档内容的完整性,平台不提供额外的编辑、内容补充、找答案等附加服务。
- 2、"仅部分预览"的文档,不可在线预览部分如存在完整性等问题,可反馈申请退款(可完整预览的文档不适用该条件!)。
- 3、如文档侵犯您的权益,请联系客服反馈,我们会尽快为您处理(人工客服工作时间:9:00-18:30)。
常用的几种铝合金熔体除碱技术简介
黄其
【摘要】The paper presented several common processes for removing alkali from aluminum melts,and it analyzed the source and harm of alkali metal in aluminum melts;it summarized respective advantages and disadvantages by comparing these processes,providing manufacturers with reference for selecting appropriate process to improve the quality of the melts.%简单介绍了几种用于铝合金熔体的除碱技术,分析了铝熔体中碱金属的来源及危害,并通过几种除碱技术的对比,得出各自的优缺点,便于生产厂家选择适合的除碱技术,提高熔体质量。
【期刊名称】《有色金属加工》
【年(卷),期】2016(045)004
【总页数】3页(P37-39)
【关键词】铝合金;熔体处理;碱金属;除碱
【作者】黄其
【作者单位】中色科技股份有限公司,河南洛阳471039
【正文语种】中文
【中图分类】TG243
铝合金熔体中会含有或多或少的气体、各种非金属夹杂物及其他有害金属,这些杂质的存在会直接影响到铝合金的品质,使铸锭产生如疏松、气孔、夹渣等缺陷,继
而对下游加工产品的力学性能、加工性能、抗腐蚀性能、表面处理性能及产品外观等造成不良影响。
为了克服上述不良影响,在铝合金熔铸生产中,熔体净化就变得极为重要。
而铝合金熔体除碱是熔体净化的重要组成部分,同时对于采用电解铝液直接配料的生产方式,除碱就变得十分必要。
本文分析了铝熔体中碱金属的来源及危害,对常用的几种铝合金熔体除碱技术进行简要介绍。
在铝合金熔铸生产中,碱金属主要是指锂、钠、钾元素,其来源主要有以下几种途径。
1.1 原料用铝
铝合金熔铸生产中,使用的电解铝液或者重熔用铝锭均来源于电解铝厂。
(1)钠(Na)。
在电解铝生产过程中,冰晶石(Na3AlF6)、氟化钠(NaF)等含钠介质的使用,使电解铝液中存在一定含量的钠,其含量可达80ppm,实际生产中钠含量则控制在30~60ppm[1];重熔用铝锭中钠含量一般在8~15ppm,个别达到23ppm[2];
钠元素主要来源于下列反应过程:
Na3AlF6
3XF+Al=3X+AlF3 (2,式中X代表碱金属)
(2)锂(Li)。
电解铝生产时,为改善电解质的化学物理或电化学性能,会添加CaF、LiF及MgF2等添加剂。
同时,多数情况下,电解铝原料氧化铝中本身即存在少量的Ca、Li及Mg元素[3];
(3)钾(K)。
主要来源于电解铝生产中生产原料及辅料中的杂质。
1.2 精炼剂
铝合金常用精炼剂中大部分都含有金属钠、钾离子,精炼剂组成成分主要为
Na3AlF6、NaCl、KCl及少量NaF等。
表1为某国产精炼剂各元素含量,其主要反应同式(1)、(2)。
1.3 变质剂
铝合金常用的变质剂为钠盐变质剂,其主要成分为NaF及NaCl,还含有部分
Na3AlF6及KCl,其主要反应同式(1)、(2)。
1.4 覆盖剂
一般铝合金熔体覆盖剂主要成分为NaCl及KCl。
考虑到NaCl、KCl在铝熔体中较为稳定,几乎不会与铝液反应产生钠离子,其将主要以化合物固体颗粒夹杂的形式存在于铝熔体中,覆盖剂内碱金属以离子形态进入铝熔体的影响可忽略不计。
碱金属元素中,锂元素可以用作铝合金强化元素,作用是降低铝合金密度,提高铝合金弹性模量。
其他情况下,碱金属元素是以杂质的形式在铝熔体中存在,这些杂质碱金属通过与其他杂质元素相互间的物理化学作用,将会改变材料的组织结构和相组成,从而影响铝合金的力学、加工、表面处理等一系列性能。
在铝熔体碱金属中,危害最大的是指钠元素(Na)。
钠元素对铝合金铸造的危害,主要包括两方面[4]:(1)增大铸造时铝合金粘度,增加铸造时铸锭拉裂倾向,破坏铸锭表面质量;(2)引起“钠脆”现象。
当铝合金中存在钠时,钠将会游离并最终吸附在枝晶或晶界上,使铝合金的脆性增加,导致铸造时出现裂纹,或者在下游深加工工艺如热轧时开裂。
“钠脆”现象对高镁合金危害尤为严重,为防止发生NaAlSi+Mg→Mg2Si+Na(游离)+Al反应,实际生产中不容许使用钠盐熔剂。
由于钠元素是主要的碱金属危害元素,因此铝熔体除碱的效果主要通过钠含量的变化为定量判断依据。
一般来说,铝合金熔体净化后,碱金属钠的含量应控制在
5ppm以内。
对Mg含量较高的Al-Mg系合金,Na的限制更加严格,5182合金中,几个ppm钠即可能导致热轧裂纹。
铝合金熔体除碱技术可以分为炉前除碱技术、炉内除碱技术和炉后除碱技术3种。
生产中可以根据所生产的合金品种选择一种或多种相结合的除碱技术,来确保控制熔体内的碱金属含量。
3.1 炉前除碱技术
电解铝液炉前预处理技术,是指在电解铝液进入炉子之前,使用炉外独立的设备进行除碱。
国外某几家公司生产的处理设备采用了该技术,并已在国外得到了广泛应用。
该设备由铝液包基座、氟化铝供应系统、转子系统及除尘系统组成。
除碱过程为,将专用的可开盖式密封铝液包输送至设备基座上,开启铝液包上盖后,除碱设备上带有转子系统的抬包盖盖住铝液包,转子系统以氩气为传输介质,将氟化铝喷入铝液包铝液中,使其在熔体内部均匀扩散而不影响到铝液表面。
通过反应
3X+AlF3=3XF+Al(X代表碱金属),将钠及锂、钾、钙金属带到熔体表面。
除碱后的铝熔体在注入炉子时,是通过压力将电解铝液从抬包接近底部的位置压出,且每次均会留一部分铝液在抬包内,因此抬包中浮在铝熔体表面的渣将不会进入炉子。
这一系统可以做到高效率除锂、钠、钾等碱金属以及钙金属,处理时间比在炉内除碱更快(每分钟使熔体内钠含量减半,如钠含量60ppm的熔体,可在5min内处
理至2ppm,即60ppm30ppm15ppm7.5ppm3.75ppm1.875ppm),同时也能
高效率除碳化物及氧化物,减少在炉子内处理的时间。
另外,相比较炉体内除碱过程中需要热能保持熔体温度,电解铝液炉前处理技术可以减少这部分能量消耗。
3.2 炉内除碱技术
铝熔铸生产过程中,能够做到除去铝熔体中碱金属的方法为在保温炉内使用氯气、含氯精炼剂(如六氯乙烷、四氯化碳等)或含氟化物精炼剂,对熔体进行精炼处理。
然而,在使用氯气、氯化物或者氟化物的过程中,会有浮出铝熔体的氯气气体,以及与碱金属反应后生成的氯气、氟化氢,受热气化的六氯乙烷、四氯化碳气体产生,
会严重损害炉子内衬,缩短炉子使用寿命;其次,会对生产操作人员产生职业病危害,导致慢性氟中毒、气管-支气管炎、肺炎或肺水肿等职业病;最后,炉内熔体净化处理无法保证精炼气体/精炼剂与铝熔体的充分接触,对铝合金熔体的除碱净化相当有限。
目前,炉内针对性的除碱处理(如氯气、六氯乙烷、四氯化碳)已很少运用,炉内净化的重点集中在炉内除氢、除渣工艺,在这些净化处理过程中如精炼剂中含有氯化物,则可以达到一定的除碱效果。
3.3 炉后除碱技术
炉后净化,即铝熔体在线净化技术。
该技术是在铝熔体出炉后、铸造前通过在线精炼装置对熔体进行精炼处理。
为了达到除碱目的,精炼气体中加入了氯气,其基本除碱原理为使用高压喷嘴将氮气、氯气混合气体或氩气、氯气混合气体喷入设备中铝熔体底部,细小的气泡在上浮过程中与铝熔体充分接触,发生化学反应2X++Cl2=2XCl(X代表碱金属),从而将钠、锂、钙等离子除去。
对于钠、锂、钙金属含量不超过10ppm的铝熔体,采用炉后除碱技术的除碱效果均能保证在5ppm内,甚至达到3ppm,如使用串联的两台在线精炼装置,除碱效果能够达到2ppm以下。
以上3种除碱技术的比较见表2。
随着电解铝液配料在铝熔铸生产中的推广,铝熔体除碱技术得到更多应用。
在现实生产中,生产厂家可以灵活地结合各种铝熔体净化技术,如当使用电解铝液配料生产铝合金铸锭时,可以使用炉前除碱+炉内除杂质+炉后除氢除杂的组合;当使用重熔用铝锭配料时,使用炉内除杂质+炉后除氢除碱除杂的组合,来提高铝熔体质量。
【相关文献】
[1] 武元,梁鲁清.电解铝液直接生产1235合金双零箔铸轧坯料的工艺研究与实践[J].铝加工,2015,(5):38.
[2] 黄世恒.Al-Mg合金钠脆问题工艺研究[J].企业技术开发,2014,33(12):135.
[3] 张芬萍,铝电解过程中的杂质及其控制[J].铝镁通讯,2015,(3):40.
[4] 迟福全,王立娟,彭先亮.Na元素对铝合金铸造性能的影响[J].轻合金加工技术,2002,30(8):14.
[5] 肖亚庆.铝加工技术实用手册[M].北京:冶金工业出版社,2004:。