多向模锻技术
《P91典型件多向模锻工艺数值模拟研究》范文

《P91典型件多向模锻工艺数值模拟研究》篇一一、引言多向模锻工艺作为一种先进的金属成形技术,近年来在制造业中得到了广泛应用。
P91典型件作为典型的复杂结构件,其制造过程中对多向模锻工艺的要求较高。
因此,本文旨在通过数值模拟的方法,对P91典型件多向模锻工艺进行研究,以期为实际生产提供理论依据和技术支持。
二、P91典型件概述P91典型件是一种具有复杂结构的金属构件,其材料为高温合金钢。
由于其结构的复杂性,传统工艺难以满足其制造要求。
多向模锻工艺具有较高的成形性能和优良的力学性能,因此被广泛应用于P91典型件的制造过程中。
三、多向模锻工艺原理及特点多向模锻工艺是一种通过多次模具变形,使金属材料在多个方向上发生塑性变形的工艺方法。
其特点包括成形性能高、力学性能优良、材料利用率高、生产效率高等。
在P91典型件的制造过程中,多向模锻工艺能够有效地解决传统工艺中存在的问题,提高产品的质量和生产效率。
四、数值模拟方法及模型建立本文采用有限元法进行数值模拟,建立了P91典型件多向模锻工艺的有限元模型。
模型中考虑了材料的非线性、弹塑性、热力耦合等特性,以及模具与材料之间的摩擦、传热等相互作用。
通过输入工艺参数和材料参数,对多向模锻过程进行数值模拟。
五、模拟结果分析模拟结果显示,多向模锻工艺在P91典型件的制造过程中具有较高的成形性能和优良的力学性能。
在模拟过程中,我们观察到了金属材料的流动规律、应力分布、温度变化等情况,并对模拟结果进行了详细的分析。
通过分析,我们发现多向模锻工艺能够有效地改善金属材料的流动性能,提高产品的力学性能和表面质量。
六、工艺参数优化及实验验证基于数值模拟结果,我们对多向模锻工艺的工艺参数进行了优化。
优化后的工艺参数包括模具温度、压力、速度等。
为了验证优化后的工艺参数的有效性,我们进行了实验验证。
实验结果表明,优化后的工艺参数能够显著提高P91典型件的成形性能和力学性能,满足实际生产的需求。
《P91典型件多向模锻工艺数值模拟研究》

《P91典型件多向模锻工艺数值模拟研究》篇一一、引言多向模锻工艺作为一种先进的金属塑性加工技术,广泛应用于航空、航天、汽车等领域的零件制造。
P91典型件作为其中的一种重要零件,其制造工艺的优化与改进对于提高产品质量、降低成本具有重要意义。
本文将针对P91典型件的多向模锻工艺进行数值模拟研究,以期为实际生产提供理论支持。
二、P91典型件概述P91典型件是一种典型的金属零件,具有复杂的几何形状和较高的性能要求。
其材料通常为合金钢,具有较高的强度和韧性。
在多向模锻工艺中,P91典型件的成型过程涉及到金属的流动、变形、传热等多个物理过程,因此需要进行详细的数值模拟研究。
三、多向模锻工艺数值模拟方法数值模拟是研究多向模锻工艺的重要手段,通过建立合理的有限元模型,可以模拟金属的流动、变形、传热等过程,从而预测和优化工艺参数。
本文将采用有限元法进行P91典型件多向模锻工艺的数值模拟研究。
四、模型建立与参数设置1. 几何模型:根据P91典型件的几何形状,建立相应的三维几何模型。
2. 材料模型:选择合适的材料模型,描述合金钢的力学性能和热物理性能。
3. 边界条件:设定模具与金属之间的摩擦条件、传热条件等。
4. 工艺参数:设定模具温度、锻造压力、锻造速度等工艺参数。
五、数值模拟结果与分析通过数值模拟,可以得到P91典型件多向模锻过程中的金属流动、变形、传热等结果。
以下是对模拟结果的分析:1. 金属流动:通过观察金属的流动情况,可以分析出成型过程中金属的充填情况、缺陷产生的原因等。
2. 变形情况:通过分析等效应力、应变等参数,可以了解P91典型件的变形情况,从而优化模具设计。
3. 传热过程:通过模拟传热过程,可以了解模具与金属之间的热量传递情况,从而优化模具的温度控制。
4. 工艺参数优化:根据模拟结果,可以调整模具温度、锻造压力、锻造速度等工艺参数,以获得更好的成型效果。
六、结论与展望通过对P91典型件多向模锻工艺的数值模拟研究,可以得到以下结论:1. 金属流动、变形、传热等过程的数值模拟可以为实际生产提供理论支持,有助于优化工艺参数和模具设计。
《P91典型件多向模锻工艺数值模拟研究》范文

《P91典型件多向模锻工艺数值模拟研究》篇一一、引言P91典型件作为机械制造中的重要构件,其制造工艺的优化与性能的提升一直是研究的热点。
多向模锻工艺作为一种先进的塑性加工技术,能够有效提升材料性能和优化内部结构。
本文针对P91典型件多向模锻工艺进行数值模拟研究,以期为实际生产提供理论依据和指导。
二、P91典型件材料特性及要求P91典型件是一种高强度合金钢构件,具有优异的力学性能和抗腐蚀性能。
其制造过程中要求材料具有较高的可塑性、流动性和成形性。
因此,选择合适的模锻工艺对于提高P91典型件的力学性能和降低生产成本具有重要意义。
三、多向模锻工艺原理及特点多向模锻工艺是一种利用多向压应力场对金属材料进行塑性变形的工艺方法。
该工艺具有以下特点:一是可以细化晶粒,提高材料的力学性能;二是可以改善材料的内部组织结构,提高抗疲劳性能;三是可以通过控制模具形状和变形过程,实现复杂零件的近净成形。
因此,多向模锻工艺在P91典型件制造中具有广阔的应用前景。
四、数值模拟方法及模型建立本文采用有限元法进行P91典型件多向模锻工艺的数值模拟。
首先,建立P91典型件的三维几何模型和有限元模型。
其次,根据实际生产过程中的模具形状、材料性质、摩擦条件等设定模拟参数。
最后,通过有限元软件进行模拟计算,分析多向模锻过程中材料的流动规律、应力应变分布以及成形质量等。
五、模拟结果与分析通过数值模拟,我们得到了P91典型件多向模锻过程中的材料流动、应力应变分布以及成形质量等关键信息。
分析结果表明:1. 在多向模锻过程中,材料流动均匀,无明显的流动不均现象;2. 应力应变分布合理,晶粒得到细化,提高了材料的力学性能;3. 成形质量良好,满足了P91典型件的制造要求。
六、结论与展望本文通过对P91典型件多向模锻工艺的数值模拟研究,得出以下结论:1. 多向模锻工艺可以有效提高P91典型件的力学性能和抗疲劳性能;2. 数值模拟方法为实际生产提供了理论依据和指导,有助于优化工艺参数和降低成本;3. 未来研究可进一步关注多向模锻工艺在复杂零件制造中的应用,以及与其他制造技术的结合。
《2024年P91典型件多向模锻工艺数值模拟研究》范文
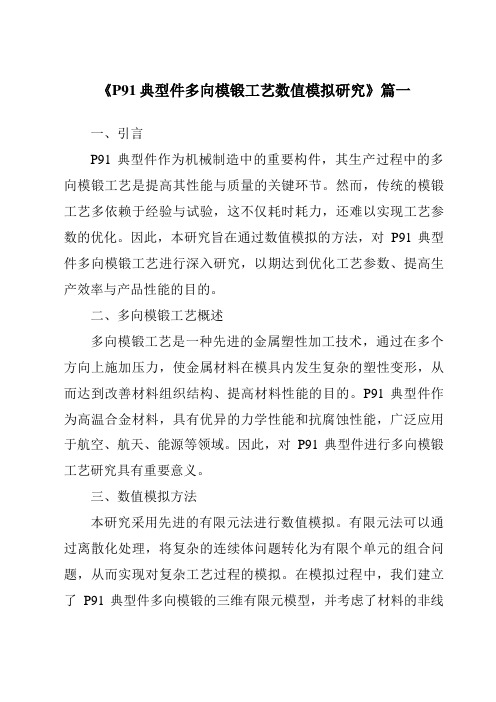
《P91典型件多向模锻工艺数值模拟研究》篇一一、引言P91典型件作为机械制造中的重要构件,其生产过程中的多向模锻工艺是提高其性能与质量的关键环节。
然而,传统的模锻工艺多依赖于经验与试验,这不仅耗时耗力,还难以实现工艺参数的优化。
因此,本研究旨在通过数值模拟的方法,对P91典型件多向模锻工艺进行深入研究,以期达到优化工艺参数、提高生产效率与产品性能的目的。
二、多向模锻工艺概述多向模锻工艺是一种先进的金属塑性加工技术,通过在多个方向上施加压力,使金属材料在模具内发生复杂的塑性变形,从而达到改善材料组织结构、提高材料性能的目的。
P91典型件作为高温合金材料,具有优异的力学性能和抗腐蚀性能,广泛应用于航空、航天、能源等领域。
因此,对P91典型件进行多向模锻工艺研究具有重要意义。
三、数值模拟方法本研究采用先进的有限元法进行数值模拟。
有限元法可以通过离散化处理,将复杂的连续体问题转化为有限个单元的组合问题,从而实现对复杂工艺过程的模拟。
在模拟过程中,我们建立了P91典型件多向模锻的三维有限元模型,并考虑了材料的非线性、热传导、接触摩擦等物理过程。
通过输入工艺参数,如模具形状、锻造温度、压力等,对模锻过程进行数值模拟。
四、模拟结果与分析1. 变形过程分析:通过数值模拟,我们可以观察到P91典型件在多向模锻过程中的变形情况。
在模具的作用下,材料发生复杂的塑性变形,逐渐充满模具型腔,实现了材料的致密化。
2. 应力应变分析:数值模拟结果还显示了P91典型件在模锻过程中的应力应变分布情况。
通过分析这些数据,我们可以了解材料在不同位置的变形程度和应力状态,为优化工艺参数提供依据。
3. 温度场分析:在多向模锻过程中,由于摩擦和塑性变形等原因,会产生大量的热量。
数值模拟可以分析这些热量的传递和分布情况,为控制锻造温度提供依据。
4. 工艺参数优化:通过对比不同工艺参数下的模拟结果,我们可以找到最优的工艺参数组合。
这些参数包括模具形状、锻造温度、压力等,可以在保证产品质量的同时,提高生产效率。
《P91典型件多向模锻工艺数值模拟研究》范文

《P91典型件多向模锻工艺数值模拟研究》篇一一、引言随着现代工业的快速发展,多向模锻工艺作为一种先进的金属塑性加工技术,在制造业中得到了广泛应用。
P91典型件作为典型的高温合金材料,其加工过程对于工艺参数的精准控制要求较高。
本文针对P91典型件的多向模锻工艺进行数值模拟研究,旨在通过模拟分析,为实际生产提供理论支持和优化方向。
二、多向模锻工艺概述多向模锻工艺是一种以模具为载体,通过多个方向的压制与流动来实现金属材料的塑形加工过程。
其特点在于能够在保证金属材料性能的同时,提高产品的精度和强度。
P91典型件作为一种高温合金材料,其多向模锻工艺的优化对于提高产品的性能和使用寿命具有重要意义。
三、数值模拟方法及模型建立本文采用有限元法进行数值模拟研究。
首先,根据P91典型件的几何特征和材料性能,建立合理的有限元模型。
然后,根据多向模锻工艺的特点,设定合理的材料模型、边界条件和加载条件。
最后,通过模拟软件进行数值模拟分析,观察金属材料的流动和变形过程。
四、模拟结果与分析1. 金属流动与变形过程:在多向模锻过程中,金属材料在模具的作用下发生流动和变形。
通过模拟分析,可以观察到金属材料的流动路径和变形程度,从而分析出工艺参数对产品性能的影响。
2. 应力应变分布:在多向模锻过程中,金属材料受到模具的压制和摩擦作用,产生应力应变。
通过模拟分析,可以观察到应力应变的分布情况,为优化工艺参数提供依据。
3. 工艺参数对产品性能的影响:通过改变模具形状、压制速度、摩擦系数等工艺参数,观察产品性能的变化。
分析各工艺参数对产品性能的影响程度,为实际生产提供优化方向。
五、结论与展望通过数值模拟研究,本文得出以下结论:1. P91典型件的多向模锻工艺过程中,金属材料的流动和变形受到模具形状、压制速度、摩擦系数等工艺参数的影响。
通过优化这些工艺参数,可以提高产品的精度和强度。
2. 在实际生产中,应根据产品的性能要求,合理选择模具形状、压制速度和摩擦系数等工艺参数。
多向模锻工艺及模具设计
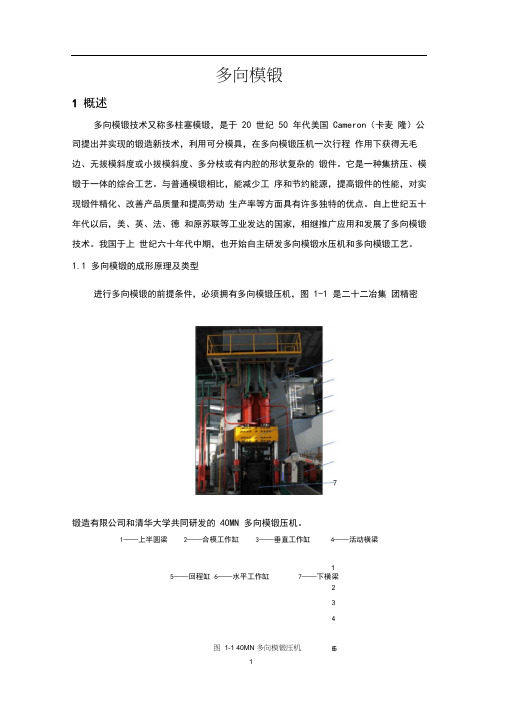
多向模锻1 概述多向模锻技术又称多柱塞模锻,是于20 世纪50 年代美国Cameron(卡麦隆)公司提出并实现的锻造新技术,利用可分模具,在多向模锻压机一次行程作用下获得无毛边、无拔模斜度或小拔模斜度、多分枝或有内腔的形状复杂的锻件。
它是一种集挤压、模锻于一体的综合工艺。
与普通模锻相比,能减少工序和节约能源,提高锻件的性能,对实现锻件精化、改善产品质量和提高劳动生产率等方面具有许多独特的优点。
自上世纪五十年代以后,美、英、法、德和原苏联等工业发达的国家,相继推广应用和发展了多向模锻技术。
我国于上世纪六十年代中期,也开始自主研发多向模锻水压机和多向模锻工艺。
1.1 多向模锻的成形原理及类型进行多向模锻的前提条件,必须拥有多向模锻压机,图1-1 是二十二冶集团精密锻造有限公司和清华大学共同研发的40MN 多向模锻压机。
1——上半圆梁2——合模工作缸3——垂直工作缸4——活动横梁15——回程缸6——水平工作缸7——下横梁234图1-1 40MN 多向模锻压机56由图1-1 可知,多向模锻压机和普通模锻压机有很大区别,机架在左右方向设计成一定角度,机架采用钢丝缠绕提供机架垂直方向和水平方向的预紧力多向模锻液压机可以在不同方向按不同顺序用冲头对闭式模具中坯料进行挤压,使其能很好的充满模具型腔。
锻造结束后模具分开,方便从模具型腔内取出锻多向模锻根据锻件的分模方式不同,可以分为三种类型:即垂直分模;水平分模;垂直与水平联合分模( 简称复合分模),见图1-2 所示。
由图可清楚看到这三种多向模锻的分模方式及其成形原理,如下:图1-2 多向模锻分模方式(1)垂直分模(2) 水平分模(3)复合分模(1) 垂直分模垂直分模是把左右模具固定在压力机的水平缸活塞上,将垂直冲头固定在垂直穿孔缸的活塞上,以水平缸活塞压紧左右模具,把坯料放入模具模腔中,用垂直冲头挤压坯料使坯料填满模具型腔。
锻造结束后,垂直冲头回程,水平缸回程打开左右模具,锻件从模具型腔中取出。
多向模锻

多向模锻多向模锻(又称为多柱塞模锻)基本上是在六十年代发展和推广起来的一项新工艺。
其工作原理是:在可分阴模闭合后(阴模闭合过程中毛坯可以产生变形,也可以不产生变形),几个冲头自不同方向同时或先后对毛坯进行挤压,从而在一次加热和压力机的一次行程中获得形状复杂的多分支锻件。
这一工艺实质上是挤压和模锻的综合过程,并且以挤压为主。
在毛坯变形过程中,既有部分金属平行于冲头运动方向(或者和冲头运动方向成一定的角度)产生流动。
采用这一工艺能够避免产生飞边,节约毛坯材料,减少模锻工序,并能够提高锻件精度和机械性能。
由于具有以上的优点,多向模锻工艺由起初只用于加工高合金钢、钛合金和镍合金等材料(这些材料价格昂贵,而且锻造温度范围狭窄,多次加热又会使材料的火耗增加),后来推广到一般钢材和有色金属;起初只用于加工火箭喷嘴、石油工业用阀体一类大型零件,后来推广到管子接头一类小型零件和批量很大、品种很多的汽车、拖拉机零件;起初只采用专门化的多柱塞液压机,后来推广到现在通用的机械压力机上采用多冲头模具。
这项工艺和专用设备虽然在第二次世界大战后即已出现,但是到六十年代才真正地发展和推广起来。
多向模锻一般都采用可分阴模,因此广义地说,也可以算是一种特殊形式的分模模锻。
但是分模模锻却不一定是多向模锻。
分模模锻是具有相当长的历史的,例如在平锻机上墩头基本上就属于这类工艺。
但是今年发展起来的分模模锻却不是简单地用于镦锻长杆零件的头部,而是用于模锻形状复杂、尺寸精确、没有飞边的锻件。
事实上,即使是平锻工艺,近年来也是有很大的变化。
大体上可以说,平锻工艺已经脱离了简单的墩头阶段,而是发展到制造复杂的精密锻件的阶段。
例如英国的Etchells 公司的水平分模平锻机就能锻出四联齿轮毛坯和带有多阶锥颈的法兰,西德Hasenclever公司的水平分模平锻机也能用棒料挤出异径轴套[1]。
所谓分模模锻就其本意来说是指当可分阴模闭合后,以一个冲头自一个方向对毛坯进行挤压的一种工艺过程。
多向模锻工艺及模具设计

多向模锻1 概述多向模锻技术又称多柱塞模锻,是于20世纪50年代美国Cameron(卡麦隆)公司提出并实现的锻造新技术,利用可分模具,在多向模锻压机一次行程作用下获得无毛边、无拔模斜度或小拔模斜度、多分枝或有内腔的形状复杂的锻件。
它是一种集挤压、模锻于一体的综合工艺。
与普通模锻相比,能减少工序和节约能源,提高锻件的性能,对实现锻件精化、改善产品质量和提高劳动生产率等方面具有许多独特的优点。
自上世纪五十年代以后,美、英、法、德和原苏联等工业发达的国家,相继推广应用和发展了多向模锻技术。
我国于上世纪六十年代中期,也开始自主研发多向模锻水压机和多向模锻工艺。
1.1 多多多多多多多多多多多多进行多向模锻的前提条件,必须拥有多向模锻压机,图1-1是二十二冶集团精密锻造有限公司和清华大学共同研发的40MN多向模锻压机。
1234567图1-1 40MN多向模锻压机1——上半圆梁2——合模工作缸3——垂直工作缸4——活动横梁5——回程缸6——水平工作缸7——下横梁由图1-1可知,多向模锻压机和普通模锻压机有很大区别,机架在左右方向设计成一定角度,机架采用钢丝缠绕提供机架垂直方向和水平方向的预紧力。
多向模锻液压机可以在不同方向按不同顺序用冲头对闭式模具中坯料进行挤压,使其能很好的充满模具型腔。
锻造结束后模具分开,方便从模具型腔内取出锻件。
多向模锻根据锻件的分模方式不同,可以分为三种类型:即垂直分模;水平分模;垂直与水平联合分模(简称复合分模),见图1-2所示。
由图可清楚看到这三种多向模锻的分模方式及其成形原理,如下:图1-2 多向模锻分模方式(1)垂直分模(2)水平分模(3)复合分模(1)垂直分模垂直分模是把左右模具固定在压力机的水平缸活塞上,将垂直冲头固定在垂直穿孔缸的活塞上,以水平缸活塞压紧左右模具,把坯料放入模具模腔中,用垂直冲头挤压坯料使坯料填满模具型腔。
锻造结束后,垂直冲头回程,水平缸回程打开左右模具,锻件从模具型腔中取出。
- 1、下载文档前请自行甄别文档内容的完整性,平台不提供额外的编辑、内容补充、找答案等附加服务。
- 2、"仅部分预览"的文档,不可在线预览部分如存在完整性等问题,可反馈申请退款(可完整预览的文档不适用该条件!)。
- 3、如文档侵犯您的权益,请联系客服反馈,我们会尽快为您处理(人工客服工作时间:9:00-18:30)。
多向模锻是在多向模锻液压机上进行分模模锻的一种精密锻造技术,其变形实质上是复合了挤压与模锻,且以挤压变形为主。
多向模锻在精化锻件、节约材料、改善产品质量,提高生产效率以及将模锻扩大应用到难成形材料的成形等方面具有许多优点和显著的经济效益。
与普通模锻及分模模锻相比,具有以下特点:
1、可成形内有多向空腔、外有凸凹变化的复杂模锻件。
内有空腔、无飞边,锻件形状和尺寸精度高,多数情况下可一火次完成锻造成形,可实现部分表面的少无切削加工,材料利用率高,切削加工量小,后续加工台时少、制造周期短。
2、锻件内在质量高。
金属材料处在高静液应力、大等效应变条件下成形,组织致密、材料缺陷易于弥合。
锻件的流线分布合理,有助于提高其力学性能。
从大量多向模锻件的低倍组织检验结果看出,多向模锻件的金属流线沿锻件轮廓分布流畅,有利于锻件力学性能的提高。
此外,因多向模锻不产生飞边,也没有因为切边而产生流线末端外露的问题,这对提高零件的抗应力腐蚀性能尤为重要。
3、坯料形状简单,制坯成本低廉。
火次少,通常为单模腔、一火成形,能耗低,模具投入少,生产效率高,生产成本低。
4、可将模锻工艺的应用范围扩大到温度较窄、塑性较低的材料。
5、模具结构简单、使用寿命长,对降低锻件成本有利。
1/ 1。