开式模锻工艺及模具设计
锻造工艺与模具设计-模锻成形工序分析

● 金属充满模膛后,多余金属由桥口流出,此 为第Ⅲ阶段。
13
一、开式模锻变形过程
●
第Ⅰ阶段:由开始模压到金属与模具侧壁接触为止
14
一、开式模锻变形过程
●
第Ⅱ阶段:第Ⅰ阶段结束到金属充满模膛为止
15
一、开式模锻变形过程
●
第Ⅲ阶段:金属充满模膛后,多余金属由桥口流出
16
二、开式模锻各阶段的应力应变分析
32
小飞边模锻
对某些形状的锻件,在模锻最后阶段,变形区集中 分布在分模面附近,远离分模面的部分不容易充满。
33
楔形飞边槽
主要依靠桥口斜面产生的水平分力阻止金属外 流,飞边部分金属消耗减少一倍;这种飞边与锻件 连接处较厚,切边较困难
34
扩张型飞边槽
在模锻的第一第二阶段,桥口部分对金属外流有一定阻力作用;而最 后阶段,对多余金属的外流无阻碍作用,可以较大程度的减小变形力,使 上下模压靠。
42
18
二、开式模锻各阶段的应力应变分析
●
第Ⅱ阶段
19
二、开式模锻各阶段的应力应变分析
第Ⅲ阶段: 主要是将多余金属排入飞边。此时流动界面已不存 在,变形仅发生在分模面附近的一个区域内,其它部位 则处于弹性状态;多于金属由桥口流出时阻力很大,使 变形抗力急剧增大
●
20
二、开式模锻各阶段的应力应变分析
6
控制金属的流动方向
各质点向着阻力最小方向移动, 因此依靠不同的工具,采取不同的加载方式在变形 体内建立不同的应力场实现对金属流动物体内方向的控 制
7
控制塑性变形区
主要靠利用不同工具在坯料内产生不同的应力状态, 使部分金属满足屈服准则,另一部分金属不满足屈服准 则,达到控制变形区的目的
锻造工艺及模具设计试卷及答案
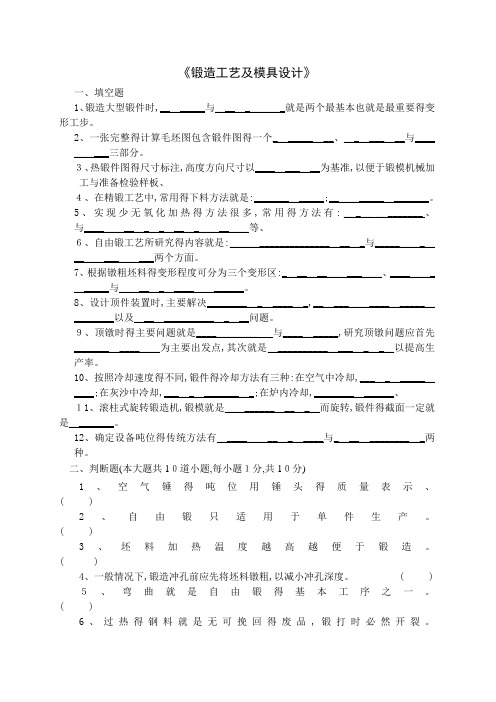
《锻造工艺及模具设计》一、填空题1、锻造大型锻件时,________与_________就是两个最基本也就是最重要得变形工步。
2、一张完整得计算毛坯图包含锻件图得一个__________、_________与_________三部分。
3、热锻件图得尺寸标注,高度方向尺寸以___________为基准,以便于锻模机械加工与准备检验样板、4、在精锻工艺中,常用得下料方法就是:_____________;_________________。
5、实现少无氧化加热得方法很多,常用得方法有:___________、与_______________________等、6、自由锻工艺所研究得内容就是:______________________与_____________________两个方面。
7、根据镦粗坯料得变形程度可分为三个变形区:______________、_____________与___________________。
8、设计顶件装置时,主要解决_________________,___________________________以及___________________问题。
9、顶镦时得主要问题就是________与__________,研究顶镦问题应首先______________为主要出发点,其次就是____________________以提高生产率。
10、按照冷却速度得不同,锻件得冷却方法有三种:在空气中冷却,________________;在灰沙中冷却,_______________;在炉内冷却,_______________、11、滚柱式旋转锻造机,锻模就是______________而旋转,锻件得截面一定就是________。
12、确定设备吨位得传统方法有________________与_______________两种。
二、判断题(本大题共10道小题,每小题1分,共10分)1、空气锤得吨位用锤头得质量表示、( )2、自由锻只适用于单件生产。
锻造工艺与模具设计-锤上模锻

带连皮的模锻件,不需绘出连皮的形状和尺寸。产品 图的主要轮廓线要用点划线在模锻件图上表示,便于表示 各部分的加工余量。
锻造工艺与模具设计-锤上模锻
6.3.6 锻件图和锻件技术条件
锻件图(冷)是在零件图基础上,加上余量、余块 或其它特殊留量后绘制的图,图中锻件外形用 粗实线表示,零件外形用双点划线表示。 锻件的公称尺寸与公差注在尺寸线的上面,而 零件的尺寸注在尺寸线的下面的括号内。
α大到一定值时,可自动脱模,但α太大将会增大 金属的消耗量和余量。
但是,为了便于出模,高度较小的锻件可采用较
大的斜度,这时,多消耗的金属量不大。如:
H<50mm,查到3°改为5°;H<30mm,查的3°
、5°一律改为7°。
锻造工艺与模具设计-锤上模锻
(2) 同一锻件上内模锻斜度要比外模锻斜度大。 (大小原则)原因在于锻件冷却时,外壁趋向离开模 壁,而内壁正相反。
锻造工艺与模具设计-锤上模锻
1、热锻件图设计
热锻件图是将冷锻件图的所有尺寸计入收缩 率而绘制的。钢锻件的收缩率取1.2%-1.5%; 钛合金锻件取0.5%-0.7%;铝合金锻件取 0.8%-1.0%;铜合金锻件取1.0%-1.3%;镁合 金锻件取0.8%左右。 加放收缩率时,对无坐标中心的圆角半径不 加放收缩率;对于细长的杆类锻件、薄的锻 件、冷却快或打击次数较多而终锻温度较低 的锻件,收缩率取小值;带大头的长杆类锻 件,可根据具体情况将较大的头部和较细杆 部取不同的收缩率。
状越复杂,见表6-2:
级别 代号 形状复杂系数值S 形状复杂程度
Ⅰ S1
0.63~1
简单
Ⅱ S2
0.32~0.63
一般
Ⅲ S3
0.16~0.32
开式模锻名词解释
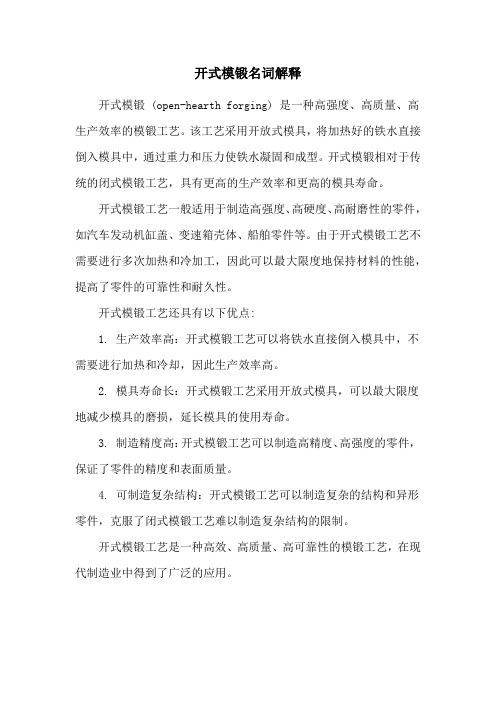
开式模锻名词解释
开式模锻 (open-hearth forging) 是一种高强度、高质量、高生产效率的模锻工艺。
该工艺采用开放式模具,将加热好的铁水直接倒入模具中,通过重力和压力使铁水凝固和成型。
开式模锻相对于传统的闭式模锻工艺,具有更高的生产效率和更高的模具寿命。
开式模锻工艺一般适用于制造高强度、高硬度、高耐磨性的零件,如汽车发动机缸盖、变速箱壳体、船舶零件等。
由于开式模锻工艺不需要进行多次加热和冷加工,因此可以最大限度地保持材料的性能,提高了零件的可靠性和耐久性。
开式模锻工艺还具有以下优点:
1. 生产效率高:开式模锻工艺可以将铁水直接倒入模具中,不需要进行加热和冷却,因此生产效率高。
2. 模具寿命长:开式模锻工艺采用开放式模具,可以最大限度地减少模具的磨损,延长模具的使用寿命。
3. 制造精度高:开式模锻工艺可以制造高精度、高强度的零件,保证了零件的精度和表面质量。
4. 可制造复杂结构:开式模锻工艺可以制造复杂的结构和异形零件,克服了闭式模锻工艺难以制造复杂结构的限制。
开式模锻工艺是一种高效、高质量、高可靠性的模锻工艺,在现代制造业中得到了广泛的应用。
轴套锻造开式模锻设计实例
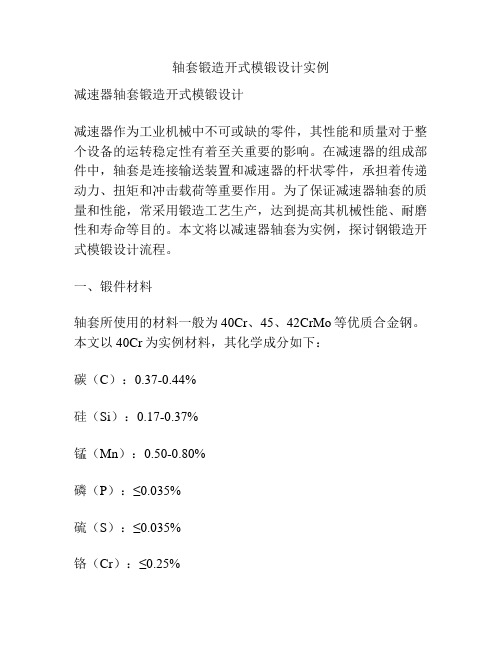
轴套锻造开式模锻设计实例减速器轴套锻造开式模锻设计减速器作为工业机械中不可或缺的零件,其性能和质量对于整个设备的运转稳定性有着至关重要的影响。
在减速器的组成部件中,轴套是连接输送装置和减速器的杆状零件,承担着传递动力、扭矩和冲击载荷等重要作用。
为了保证减速器轴套的质量和性能,常采用锻造工艺生产,达到提高其机械性能、耐磨性和寿命等目的。
本文将以减速器轴套为实例,探讨钢锻造开式模锻设计流程。
一、锻件材料轴套所使用的材料一般为40Cr、45、42CrMo等优质合金钢。
本文以40Cr为实例材料,其化学成分如下:碳(C):0.37-0.44%硅(Si):0.17-0.37%锰(Mn):0.50-0.80%磷(P):≤0.035%硫(S):≤0.035%铬(Cr):≤0.25%镍(Ni):≤0.30%铜(Cu):≤0.25%钛(Ti):≤0.03%二、减速器轴套锻造开式模锻设计1.几何形状根据减速器轴套的使用环境和需要承受的载荷,其外形一般为圆柱形或六角柱形。
在锻造时还要考虑到锻件的顶头和底部形状,以及长度和直径等因素。
2.工艺参数(1)锻件尺寸:按照轴套的直径和长度进行设计,为了加强锻后密度,通常根据几何形状确定最小直径。
(2)成形比(压缩比):成形比决定了锻件的形状变化程度,根据经验公式计算最大成形比为4.5左右。
(3)锻造温度:40Cr钢锻造温度介于1100℃-1150℃之间,需要掌握好适当的温度区间。
(4)锻压力:锻造轴套需要考虑其表面的光洁度,锤头选择较为适当,同时需要对于锻件的成形比做好压力控制。
(5)锻造速度:锻造速度一般控制在10mm/s左右,保证质量的同时还要考虑提高生产效率。
3.设计流程(1)绘制减速器轴套的三维图形,确定锻后的设计尺寸和形状。
(2)根据锻造材料的性质和工艺要求,选取适当的材质规格、定量计算,绘制出锻件的毛坯图。
(3)根据锻造工艺参数,进行强制计算,确定锻造产生的力和功。
材料成形工艺第六章 模锻工艺及锻模设计

(2)飞边槽尺寸的确定
1)吨位法。飞边槽具体尺寸根据锻锤吨位大小来选定(可查有关 手册),吨位法是从实际生产中总结出来的,应用简便,但未考 虑锻件形状复杂程度,因而准确性差。 2)计算法。计算法是采用经验公式计算飞边槽桥部高度,即 h=0.015A件或h=-0.09+23Q-0.01Q 式中,h是飞边桥部高度(mm);A件是锻件在分模面上的投影面 积(mm2);Q是锻件质量(kg)。然后根据计算得到的h值查相关 手册确定飞边槽其他尺寸。
第二节 锻件分类及锻件图设计
一、锻件的分类 二、表示锻件复杂程度的参数 三、锻件图的设计
第二节 锻件分类及锻件图设计
图6-2 拉臂锻件模锻工艺以及锻模的实例
一、锻件的分类
(1)短轴线类锻件 其特点是锻件高度方向的尺寸通常比其平面 图中的长、宽尺寸小,锻件平面图呈圆形、方形或近似圆形和 方形。 (2)长轴线类锻件 其特点是锻件的长度与宽度或高度的尺寸比 例较大。
一、开式模锻的变形特征 二、终锻模膛设计 三、预锻模膛设计
一、开式模锻的变形特征
1.开式模锻的变形过程分析 2.飞边槽的作用
1.开式模锻的变形过程分析
图6-10 开式模锻中金属变形过程及飞边槽的形式 a)开式模锻变形过程 b)飞边槽形式
1.开式模锻的变形过程分析
第Ⅰ阶段(镦粗变形) 毛坯在模膛中发生镦粗变形,对于某些 形状的锻件可能伴有局部压入变形。当被镦粗的毛坯与模膛侧 壁接触时,此阶段结束。这时变形金属处于较弱的三向压应力 状态,变形抗力也较小。
二、锻件的冷却方法
1.在空气中冷却 2.在干燥的灰砂中冷却 3.在炉内冷却
1.在空气中冷却
在空气中冷却的速度较快,适合合金化程度低、导热性及塑性 好的材料的中小锻件的锻后冷却。锻后一般是以单件直接散放 或成堆摆放在地面上,但不能放在潮湿地面上或金属板上,也 不要摆放在有穿堂风的地方,以免冷却不均匀或局部急冷引起 翘曲变形或开裂。
锻造工艺与模具设计
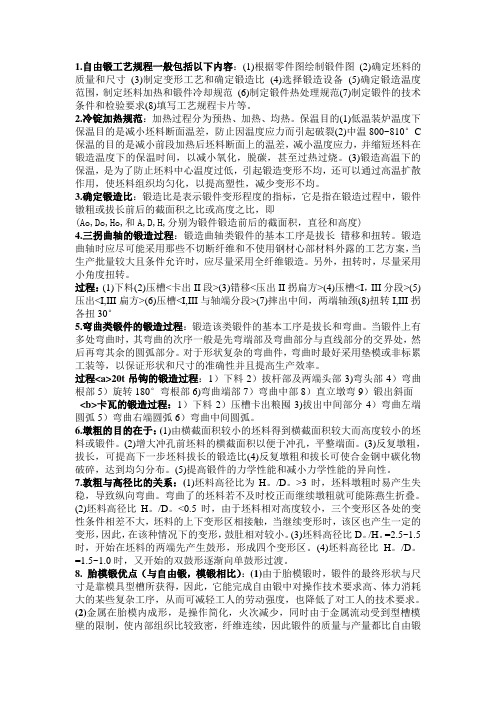
1.自由锻工艺规程一般包括以下内容:(1)根据零件图绘制锻件图(2)确定坯料的质量和尺寸(3)制定变形工艺和确定锻造比(4)选择锻造设备(5)确定锻造温度范围,制定坯料加热和锻件冷却规范(6)制定锻件热处理规范(7)制定锻件的技术条件和检验要求(8)填写工艺规程卡片等。
2.冷锭加热规范:加热过程分为预热、加热、均热。
保温目的(1)低温装炉温度下保温目的是减小坯料断面温差,防止因温度应力而引起破裂(2)中温800~810°C 保温的目的是减小前段加热后坯料断面上的温差,减小温度应力,并缩短坯料在锻造温度下的保温时间,以减小氧化,脱碳,甚至过热过烧。
(3)锻造高温下的保温,是为了防止坯料中心温度过低,引起锻造变形不均,还可以通过高温扩散作用,使坯料组织均匀化,以提高塑性,减少变形不均。
3.确定锻造比:锻造比是表示锻件变形程度的指标,它是指在锻造过程中,锻件镦粗或拔长前后的截面积之比或高度之比,即(Ao,Do,Ho,和A,D,H,分别为锻件锻造前后的截面积,直径和高度)4.三拐曲轴的锻造过程:锻造曲轴类锻件的基本工序是拔长错移和扭转。
锻造曲轴时应尽可能采用那些不切断纤维和不使用钢材心部材料外露的工艺方案,当生产批量较大且条件允许时,应尽量采用全纤维锻造。
另外,扭转时,尽量采用小角度扭转。
过程:(1)下料(2)压槽<卡出II段>(3)错移<压出II拐扁方>(4)压槽<I,III分段>(5)压出<I,III扁方>(6)压槽<I,III与轴端分段>(7)摔出中间,两端轴颈(8)扭转I,III拐各扭30°5.弯曲类锻件的锻造过程:锻造该类锻件的基本工序是拔长和弯曲。
当锻件上有多处弯曲时,其弯曲的次序一般是先弯端部及弯曲部分与直线部分的交界处,然后再弯其余的圆弧部分。
对于形状复杂的弯曲件,弯曲时最好采用垫模或非标累工装等,以保证形状和尺寸的准确性并且提高生产效率。
模锻成形工艺及模具设计特点

模锻成形工艺及模具设计特点锻锤的优点在于打击速度快,因而模具接触时间短,适合要求高速变形来填充模具的场合。
由于其快速、灵活的操作特性,其适应性非常强,有人成为“万能”设备,因而特别适用于多品种、小批量的生产。
模锻锤属于力大能小,能量可以累积,强冲击负荷和没有固定下死点的定能设备,锻锤的强冲击负荷和多次锻击成形特点,使金属在高度方向流动和填充良好,特别适用于生产薄平带筋的锻件。
锤锻主要工作特点(1)靠冲击力使金属变形,锤头在行程的最后,速度约4-9m/s(2)受力系统不是封闭的,冲击力通过下砧传给基础(3)单位时间内的打击次数多(1~10t模锻锤为40~100次/min)(4)锤头行程不固定(5)承受偏载能力和导向精度均较差(6)无顶出装置模锻工艺和模具设计特点(1)金属在各模膛中的变形是锤头的打击下逐步完成的,锤头的打击速度虽然快,但在打击中每一次的变形量较小(2)由于考冲击力使金属变形,可以利用金属的流动惯性,有利于金属填充模膛。
锻件上难充满的部分应尽量放在上模(3)在锤上可实现多种模锻工步,特别是对长轴类锻件进行滚压,拔长等制坯工步非常方便(4)由于模锻锤的导向精度不太高,工作时的冲击性质和锤头行程不固定等,因此模锻件的尺寸不太高(5)由于无顶出装置,锻件起模较困难,模锻斜度应适当大些(6)由于冲击力使金属变形,模具一般采用整体结构(7)由于靠冲击力使金属变形和锤头行程速度快,通常才用锁扣装置导向,较少采用导柱导套。
典型的锤模锻经过6个工序①镦粗:用来以减小坯料高度,增大横截面积(图中无镦粗工序)。
②拔长:将坯料绕轴线翻转并沿轴线送进,用来减小坯料局部截面,延长坯料长度。
③滚压:操作时只翻转不送进,可使坯料局部截面聚集增大,并使整个坯料的外表圆浑光滑。
④弯曲:用来改变坯料轴线形状。
⑤预锻:改善锻件成形条件,减少锻模膛的磨损。
⑥终锻:使锻件最终成形,决定锻件的形状和精度。
- 1、下载文档前请自行甄别文档内容的完整性,平台不提供额外的编辑、内容补充、找答案等附加服务。
- 2、"仅部分预览"的文档,不可在线预览部分如存在完整性等问题,可反馈申请退款(可完整预览的文档不适用该条件!)。
- 3、如文档侵犯您的权益,请联系客服反馈,我们会尽快为您处理(人工客服工作时间:9:00-18:30)。
– 可以近似认为,在模锻过程中,金属只在它所在径向平面 (称为流动平面)内沿高度和径向同时流动。
– 终锻前常采用镦粗或压扁制坯,以保证锻件成形质量。
15
第二节 模锻件的分类及表示锻件复杂程度的参数
一、模锻件的分类
二、表示模锻件复杂程度的参数
第二类为长轴线类锻件
• 其特点是:
– 锻件的长度与宽度或高度的尺寸比例较大。 – 按锻件外形、主轴线、分模特征,可分成直长轴线、弯曲 轴线和枝芽类及叉类锻件。
8
第一节 开式模锻的变形特征
1. 开式模锻的变形特征
2. 飞边槽的作用
1. 开式模锻的变形特征
• 第Ⅱ阶段(形成飞边) – 第Ⅰ阶段后期金属流动受到模膛壁的阻碍,坯料在垂直于作用力方向 的自由流动受到限制,继续压缩时,金属沿着平行于受力方向流向模 膛深处,又继续沿垂直于作用力方向流向飞边槽,形成少许飞边。 – 此时变形抗力明显增大,模膛内的金属处于较强的三向压应力状态。
13
第二节 模锻件的分类及表示锻件复杂程度的参数
一、模锻件的分类
二、表示模锻件复杂程度的参数
表6-1 锻件的分类
14
第二节 模锻件的分类及表示锻件复杂程度的参数
一、模锻件的分类
二、表示模锻件复杂程度的参数
第一类为短轴线类锻件
• 其特点是: – 锻件高度方向的尺寸通常比其平面图中的长、宽尺小,锻 件平面图呈圆形、方形或近似圆形和方形。 – 这类锻件模锻时,坯料的轴线与打击方向相同。
11
第一节 开式模锻的变形特征
1. 开式模锻的变形特征
2. 飞边槽的作用
2. 飞边槽的作用
• 1)造成足够大的横向阻 力,迫使金属充满模膛; • 2)容纳坯料上的多余金 属,起补偿与调节作用;
• 3)对于锤类设备上模锻, 缓冲模具撞击,提高锻模 寿命。
12
第二节 模锻件的分类及表示锻件复杂程度的参数
二、表示模锻件复杂程度的参数
• 模锻件形状对模锻时金属流动和变形力的影响很大,因此,必须 找出表示锻件形状复杂程度的参数。用锻件的体积与其外廓包容 体的体积之比来表示锻件复杂性的,而且比较准确地估计到偏离 主轴的那部分所带来的影响,即 S=V/Vb • 式中,S是形状复杂系数;V是锻件的体积;Vb是锻件外廓包容体 的体积。 • 当S=1~0.63之间时,形状复杂程度为较低的Ⅰ级,锻件形状简 单; • S=0.63~0.32时,形状复杂程度为Ⅱ级,为普通形状锻件; • S=0.32~0.16时,形状复杂程度为Ⅲ级,锻件形状较复杂; • S≤0.16时,形状复杂程度为Ⅳ级,锻件形状复杂。
– 这类锻件在模锻时,坯料的轴线与打击方向垂直。
– 可以近似地认为,金属基本上只在它所在的垂直于轴线的 平面(流动平面)内沿高度和宽度方向流动,而沿轴线方 向的流动很小,这是由于金属流动平面内的流动阻力比沿 轴线方向的流动阻力小。
16
第二节 模锻件的分类及表示锻件复杂程度的参数
一、模锻件的分类
二、表示模锻件复杂程度的参数
P
10
第一节 开式模锻的变形特征
1. 开式模锻的变形特征
2. 飞边槽的作用
1. 开式模锻的变形特征
• 第Ⅳ阶段(打靠) – 通常坯料体积略大于模膛容积,因此,当模膛完全充满后,尚须继续压 缩至上下模接触即打靠。 – 多余金属全部排入飞边槽,以保证高度尺寸符合要求。 – 这一阶段变形仅发生在分模面附近的区域内。 – 此阶段由于飞边厚度进一步减薄和冷却,多余金属由飞边槽桥口流出的 阻力很大,这时变形区处于最强的三向压应力状态,变形抗力也最大。 – 有研究表明,此阶段的压下量虽小于2mm,它消耗的能量却占总能量的 30%~50%。
一、模锻件的分类
二、表示模锻件复杂程度的参数
第二节 模锻件的分类及表示锻件复杂程度的参数
一、模锻件的分类 • 目的:
– 形状相似的锻件,模锻工艺流程、锻模结构基本相同。 – 为了便于拟订工艺规程设计锻件及锻模,应将各种形 状的模锻件进行分类。
• 方法:
– 按照锻件的外形和模锻时毛坯的轴线方向,把模锻件 分为短轴线类(圆饼类)和长轴线类
检验和热锻件图设计;热锻件图用于锻模设计与加工制造。
• 冷锻件图常称为锻件图。
19
第三节 锻件图的设计
1. 确定分模面
2. 确定机械加工余量和公差
3. 模锻斜度
4. 圆角半径
冷锻件图的设计内容
• 1. 确定分模面 – 确定分模位置最基本的原则是:保证锻件形状尽可能与零 件形状相同,容易从模腔中取出;此外应争取获得镦粗成 形。故此,锻件分模位置应选在具有最大水平投影尺寸的 位置上,如图6-2所示。
17
第二节 模锻件的分类及表示锻件复杂程度的参数
一、模锻件的分类
二、表示模锻件复杂程度2. 确定机械加工余量和公差
3. 模锻斜度
4. 圆角半径
5. 冲孔连皮
6. 技术条件
第三节 锻件图的设计
• 作用:工艺规程制订、锻模设计与加工、模锻生产过程及 锻件检验,都离不开锻件图。 • 锻件图分为冷锻件图和热锻件图,冷锻件图用于最终锻件
• 概念 : – 开式模锻是在锻件周围形成横向飞边的模锻; – 闭式模锻是在锻件周围不形成横向飞边仅形成小的纵向 飞边的模锻
7
第一节 开式模锻的变形特征
1. 开式模锻的变形特征
2. 飞边槽的作用
1. 开式模锻的变形特征(可分为四个阶段)
• 第Ⅰ阶段(镦粗变形) – 毛坯上端面同上模膛表面接触开始至毛坯被镦粗至鼓 形侧面同模膛侧壁接触为止。 – 变形金属处于较弱的三向压应力,P 较小。
1
120MN热模锻压力机锻造生产线(前轴)
下料 1250T剪床 加热(1240OC) 感应加热炉 辊锻制坯(二道) ø930辊锻机
模锻成形(弯、预、终)
切边
800T压床
校正压平
1600T液压机
120MN热模锻压力机
热处理 调质
清理
校正
酸洗
100T液压机
前轴成形过程动画
5
曲轴成形模拟动画
6
第一节 开式模锻的变形特征
P
9
第一节 开式模锻的变形特征
1. 开式模锻的变形特征
2. 飞边槽的作用
1. 开式模锻的变形特征
• 第Ⅲ阶段(充满型槽) – 飞边形成后,随着变形的继续进行,飞边逐渐减薄,形成阻力圈,使得 金属流向飞边槽的阻力急剧增大。当阻力大于金属流向模膛深处和圆角 处的阻力时,迫使金属继续向模膛深处和圆角处流动,直到整个模膛完 全充满为止。 – 此阶段变形金属处于更强的三向压应力状态,变形抗力急剧增大。