板带轧制工艺技术
1250热轧板带轧制规程设计

1250热轧板带轧制规程设计一、前言热轧板带是金属材料加工过程中常用的一种形式,具有广泛的应用领域。
为了保证产品质量和生产效率,制定一套科学合理的热轧板带轧制规程非常重要。
本文将介绍一种热轧板带轧制规程设计,旨在优化生产流程,提高生产效率。
二、制定背景以钢材为例,热轧板带是制造厚度在4.5mm及以下的钢材的重要工艺步骤。
因此,制定一套适用于厚度为4.5mm及以下的热轧板带轧制规程,对于提高钢材生产效率、保证产品质量起到重要作用。
三、规程设计要点1.轧制工艺设计:根据产品要求和材料特性,确定轧制工艺,包括轧制温度、轧制次数和轧制速度等。
轧制温度应根据材料的硬度和塑性选定,轧制次数和轧制速度应根据材料的厚度和要求的成品尺寸来确定。
2.设备选择与调试:根据热轧板带的设备和生产工艺要求,选购适当的轧机、辅助设备和检测设备。
同时,进行设备的调试和优化,保证轧制工艺的稳定和精确性。
3.质量控制:制定合理的质量控制方案,包括质量检测、质量评价和质量监控。
采用合适的检测工具,如超声检测、硬度检测等,对产品进行质量检测。
对于不合格品,进行返修或者剔除,以提高产品质量。
4.生产计划与调度:制定合理的生产计划和调度方案,根据市场需求和设备运行情况,合理安排生产任务。
及时调整生产计划和调度,以确保生产效率和产品质量。
5.工艺优化和持续改进:根据生产实践和市场需求,对热轧板带轧制规程进行优化和改进。
通过改变工艺参数,提高生产效率和产品质量。
同时,积极引进先进的生产工艺和设备,不断进行技术创新和改进。
四、总结与展望热轧板带轧制规程是保证产品质量和提高生产效率的重要手段。
本文提出了一种针对厚度为4.5mm及以下热轧板带的轧制规程设计。
通过制定合理的轧制工艺、选择适当的设备、实施质量控制、优化生产计划和调度,并进行工艺优化和持续改进,可以提高生产效率和产品质量,满足市场需求。
展望未来,可以进一步研究和发展轧制工艺和设备,提高轧制效率和产品质量,进一步提高热轧板带的应用范围和市场竞争力。
热轧板带工艺流程-初学者

热轧板带⼯艺流程-初学者热轧板带⼯艺流程----初学必看1.主轧线⼯艺流程简述板坯由炼钢连铸车间的连铸机出坯辊道直接送到热轧车间板坯库,直接热装的钢坯送⾄加热炉的装炉辊道装炉加热,不能直接热装的钢坯由吊车吊⼊保温坑,保温后由吊车吊运⾄上料台架,然后经加热炉装炉辊道装炉加热,并留有直接轧制的可能。
连铸板坯由连铸车间通过板坯上料辊道或板坯卸料辊道运⼊板坯库,当板坯到达⼊⼝点前,有关该板坯的技术数据已由连铸车间的计算机系统送到了热轧⼚的计算机系统,并在监视器上显⽰板坯有关数据,以便⼯作⼈员进⾏⽆缺陷合格板坯的核对和接收。
另外,通过过跨台车运来的⼈⼯检查清理后的板坯也需核对和验收,并输⼊计算机。
进⼊板坯库的板坯,由板坯库计算机管理系统根据轧制计划确定其流向。
常规板坯装炉轧制:板坯进⼊板坯库后,按照板坯库控制系统的统⼀指令,由板坯夹钳吊车将板坯堆放到板坯库中指定的垛位。
轧制时,根据轧制计划,由板坯夹钳吊车逐块将板坯从垛位上吊出,吊到板坯上料台架上上料,板坯经称量辊道称重、核对,然后送往加热炉装炉辊道,板坯经测长、定位后,由装钢机装⼊加热炉进⾏加热。
碳钢保温坑热装轧制:板坯进⼊板坯库后,按照板坯库控制系统的统⼀指令,由板坯夹钳吊车将板坯堆放到保温坑中指定的垛位。
轧制时,根据轧制计划,由板坯夹钳吊车逐块将板坯从保温坑取出,吊到板坯上料台架上上料,板坯经称量辊道称重、核对,然后送往加热炉装炉辊道,板坯经测长、定位后,由装钢机装⼊加热炉进⾏加热。
直接热装轧制:当连铸和热轧的⽣产计划相匹配时,合格的⾼温连铸板坯通过加热炉上料辊道运到称量辊道,经称重、核对,进⼊加热炉的装炉辊道,板坯在指定的加热炉前测长、定位后,由装钢机装⼊加热炉进⾏加热。
其中⼀部分通过卸料辊道运输的直接热装板坯需通过吊车吊运⼀次放到上料辊道后直接送⾄加热炉区。
如果炼钢⼚可以实现直接热装板坯由上料辊道运送,则可减少部分吊车吊运作业。
板坯经加热炉的上料辊道送到加热炉后由托⼊机装到加热炉内,加热到设定温度后,按轧制节奏要求由出钢机托出,放在加热炉出炉辊道上。
板带轧制工艺

板带轧制工艺一、轧制原理板带轧制工艺是一种通过一系列的轧制过程,将原料轧制成具有所需厚度、宽度和表面质量的板带材的工艺。
轧制过程中,轧件在轧辊的压缩下产生塑性变形,从而获得所需的形状、尺寸和性能。
二、轧机类型1.横轧机:横轧机是使轧件在平行于轧制方向上受到压缩,从而获得所需尺寸的轧制设备。
根据轧辊旋转方向的不同,横轧机可分为立式和卧式两种。
2.纵轧机:纵轧机是使轧件在垂直于轧制方向上受到压缩,从而获得所需尺寸的轧制设备。
这种轧机广泛应用于板带材的生产。
3.混合轧机:混合轧机同时具有横轧机和纵轧机的特点,可以同时进行横向和纵向的压缩,适用于复杂形状的轧制。
三、轧制原料板带轧制的原料可以是各种形状的坯料,如方坯、圆坯、钢板等。
原料的化学成分、显微组织、表面质量等都会影响最终产品的质量和性能。
四、轧制工艺参数1.压下量:压下量是轧制过程中轧件减薄的量,是影响轧件厚度的重要参数。
压下量的大小直接影响着最终产品的尺寸精度和性能。
2.轧制速度:轧制速度是指轧辊在单位时间内对轧件施加的压力,是影响轧制过程的重要参数。
适当提高轧制速度可以提高生产效率,但过高的速度会导致轧件表面质量下降。
3.轧制温度:轧制温度是指轧件在轧制过程中的温度,对轧件的塑性和变形抗力有重要影响。
合理控制轧制温度可以改善产品质量和提高生产效率。
五、轧制缺陷及控制1.裂纹:裂纹是板带材常见的缺陷之一,主要是由于轧制过程中温度变化过大或轧制压力过大引起的。
控制裂纹的方法包括合理控制轧制温度和压下量,以及选用合适的轧辊材质和热处理工艺。
2.折皱:折皱是指在板带材表面形成的局部隆起或弯曲的现象,主要是由于轧制过程中润滑不均匀或轧辊磨损严重引起的。
控制折皱的方法包括加强润滑管理、定期检查和更换轧辊等措施。
3.表面粗糙:表面粗糙是指板带材表面不光滑的现象,主要是由于原料表面质量差或热处理工艺不当引起的。
控制表面粗糙的方法包括加强原料质量管理、选用合适的热处理工艺和采用合适的轧制工艺参数等措施。
板带生产工艺5(热连轧带钢生产)课件

推动产业升级和转型
02
新技术应用将推动传统钢铁产业的升级和转型,实现绿色、智
能、高效的生产方式转变。
满足市场需求和推动经济发展
03
新技术应用将满足市场对高品质、高性能热连轧带钢的需求,
推动相关产业的发展和经济增长。
07
实践环节与案例分析
实践环节安排
实践环节目标
通过实践操作,加深对热连轧带钢生产工艺的理解,掌握 关键技术和设备操作。
原料切割
将原料按照轧制长度进行 切割,准备进入加热工序 。
原料加热
加热温度
控制加热温度在适当的范 围内,以保证轧制过程的 稳定性和产品质量。
加热时间
根据原料的厚度和加热温 度确定加热时间,确保原 料充分软化。
加热方式
采用连续式加热炉或步进 式加热炉进行加热,提高 加热效率。
加热质量与控制
温度均匀性
确保加热过程中温度分布均匀精度
对加热温度进行精确控制,以获 得稳定的轧制过程和产品质量。
氧化与脱碳
控制加热过程中的氧化和脱碳程 度,避免对产品质量造成影响。
04
轧制过程与控制
粗轧过程与控制
粗轧阶段
轧制速度
在粗轧阶段,带钢经过几道轧制后逐 渐成形,主要目标是控制带钢的宽度 和厚度,确保其满足后续精轧和成品 的要求。
热连轧带钢生产工艺流程
加热
将原料加热至轧制所需温度。
冷却
控制冷却速度,以获得所需的 金属组织和性能。
原料准备
选用合适的原料,进行表面清 理和切割。
轧制
通过多道次轧制,使原料逐渐 减薄和延伸,直至达到所需规 格。
精整
对轧制后的带钢进行表面处理 、矫直和切割等操作,以满足 产品要求。
板带轧制基础教程
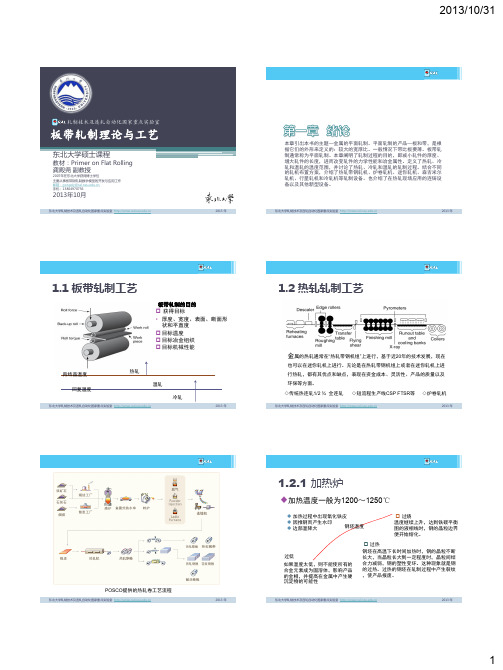
东北大学轧制技术及连轧自动化国家重点实验室
2013 年
1
2013/10/31
1.2.2 粗轧
板坯在粗轧机组轧制时温度较高,中间 坯可以完全再结晶,成为无应变的等轴 晶。通常情况下,粗轧出口处的组织对 于带钢位于精轧机组内时几乎没有任何 影响。
粗轧前除鳞 使用调宽压力机及立辊调宽 厚度由200-300mm轧制到30-50mm
2013 年
1.5 冷轧工艺
带钢表面的氧化铁皮通过酸洗去除,通常使用盐酸酸洗。酸洗之后进行压下轧制 ,即冷轧。
冷轧的目的:
更大程度地减小产品的厚度; 利用应变强化增加金属的强度; 增强产品几何尺寸的均匀性。
由冷轧后的平整机消除屈服平台
东北大学轧制技术及连轧自动化国家重点实验室
简单轧制过程
平面变形假设 平面仍为平面
东北大学轧制技术及连轧自动化国家重点实验室
2013 年
4
2013/10/31
2.2.2.1 平面变形假设
将板带轧制过程视为本质上的二维问题,相对于 厚度和长度而言,产品的宽度在轧制过程中未发 生较大的变化
冷轧
2013 年
1.2 热轧轧制工艺
金属的热轧通常在“热轧带钢机组”上进行,基于近20年的技术发展,现在
也可以在迷你轧机上进行。无论是在热轧带钢机组上或者在迷你轧机上进 行热轧,都有其优点和缺点,表现在资金成本、灵活性、产品的质量以及 环保等方面。 ◇传统热连轧1/2 ¾ 全连轧 ◇短流程生产线CSP FTSR等 ◇炉卷轧机
东北大学轧制技术及连轧自动化国家重点实验室
2013 年
本章对板带轧制过程做一般性的讨论。定义技术轧制系统的组成部分。引 用达芬奇的设计草图以及根据该草图制作的实验模型来说明什么是轧机。 针对轧制过程中的冶金现象作出描述,包括带钢准备进入辊缝、部分咬入 以及为稳定轧制状态下的行为。列出了与轧机、金属以及轧机和金属的接 触面相关的独立变量。给出了满足咬入条件的最小模型系数。详细讨论了 轧制过程数学模型中应用的一些简化建设:包括“平面变形假设”、“均 匀压缩假设”。给出了Nb钢、AISI1008钢和一种低碳冷轧钢的完全再结晶 纤维组织。
板带轧制工艺及理论
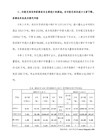
第二章 板带轧制工艺及理论1.板带钢产品的技术要求包括哪些方面?对板带钢产品的基本要求包括化学成分、几何尺寸、板形、表面、性能等几个方面。
(1)钢板的化学成分要符合选定品种的钢的化学成分(通常是指熔炼成分),这是保证产品性能的基本条件。
(2)钢板的外形尺寸包括厚度、宽度、长度以及它们的公差应满足产品标准的要求。
(3)钢板常常作为包复材料和冲压等进一步深加工的原材料使用,使用上要求板形要平坦。
在钢板的技术条件中对钢板的不平度提出要求,以钢板自由放在平台上,不施加任何外力的情况下,钢板的浪形和瓢曲程度的大小来度量。
(4)使用钢板作原料生产的零部件,原钢板的表面一般是工作面或外表面。
技术条件中通常要求钢板和钢带表面不得有气泡、裂纹、结疤、拉裂和夹杂,钢板和钢带不得有分层;钢板表面上的局部缺陷应用修磨的方法清除,清除部位的钢板厚度不得小于钢板最小允许厚度。
(5)根据钢板用途的不同,对钢板和钢带的性能要求不同,对性能的要求包括四个方面:力学性能、工艺性能、物理性能、化学性能。
对力学性能的要求包括对强度、塑性、硬度、韧性的要求;工艺性能包括冷弯、焊接、深冲等性能;材料使用时对物理性能有要求时在技术条件中提出,如电机和变压器用钢对磁感强度、铁磁损失等物理性能提出要求;材料使用时对化学性能有要求时在技术条件中提出,如不锈钢板钢带对防腐、防锈、耐酸、耐热等化学性能提出要求。
2.板带轧机的分类方法有几种?板带轧机的分类方法有按辊系分类、按轧辊驱动方式分类、按轧机组成分类、按轧机用途分类等多种分类方法。
(1)按辊系分类板带轧机按辊系分类是最常用、最基本的方式。
常用的轧机有二辊、三辊、四辊、六辊、八辊、十二辊、二十辊以及偏八辊、非对称式八辊、行星式轧机等,这些形式的轧机是由一对工作辊和多个支持辊构成。
(2)按轧辊驱动方式分类对称驱动方式:上、下工作辊,上、下中间辊,上、下支持辊;非对称驱动方式:一根工作辊,一根工作辊和一根支持辊;异步驱动:上、下辊异步传动,上、下工作辊异步传动。
板带轧制流程
板带轧制流程板带轧制呀,就像是一场神奇的变形之旅。
你看,一块原本方方正正、笨笨厚厚的金属坯料,最后能变成又薄又长的板带,这过程可老有趣了。
那这板带轧制到底是咋开始的呢?得先有原材料啊,就像咱做饭得先有米一样。
这原材料的质量可太重要了。
要是这金属坯料里面杂质多,就好比做饭的米都是坏的,那后面咋做都做不出好东西。
这坯料得是符合一定规格的,尺寸、成分都得合适,不然就像要拿不合适的砖头盖房子,肯定盖不牢。
有了坯料之后呢,就到加热这一步了。
加热就像是给金属坯料做热身运动,让它变得软乎乎的。
你想啊,大冬天的,你刚起床的时候身体是不是有点僵,活动活动就灵活多了,金属坯料加热也是这个理儿。
加热到合适的温度可不容易,温度低了,就像没活动开的人,不好塑形;温度高了呢,又容易出问题,就好比人运动过度会受伤一样。
接着就是轧制啦。
这轧制就像是一个超级大力士在压面团,不过这个“面团”可是金属的。
轧辊就像两个巨大的擀面杖,不停地把坯料压啊压。
这时候,轧辊之间的压力、轧制的速度,这些参数就像厨师做菜时候放调料的量一样,得拿捏得恰到好处。
压力小了,坯料就压不薄,就像你擀饺子皮,轻轻擀一下,皮还是厚厚的;压力太大呢,可能就会把坯料压坏了,就像你擀面皮的时候太用力,面皮破了,这金属坯料要是破了可就麻烦了。
轧制速度也不能乱定,太快了可能会出各种状况,就像开车开太快容易出事故一样,太慢呢,效率又太低,就像乌龟爬一样。
在轧制的过程中啊,还得不断地检测板带的厚度、宽度这些尺寸。
这就好比你做衣服的时候,得时不时量一量尺寸对不对。
要是尺寸不对,这板带做出来就不符合要求了。
这检测就像是板带轧制的小管家,时刻盯着呢。
要是发现厚度不对了,就得赶紧调整轧辊的间隙,就像你发现衣服缝歪了,得赶紧调整缝纫机的针脚位置一样。
轧制完了之后,还有后续的处理呢。
有的板带可能需要冷却,冷却就像是让刚刚跑完步的人歇一歇、降降温。
如果冷却不均匀,这板带就可能变形,就像人一边热一边冷容易生病一样。
科技成果——板带轧机板形控制技术
科技成果——板带轧机板形控制技术成果简介提高板带轧机板形质量的一个重要途径是采用新的板形控制技术。
目前普遍采用的诸如加大弯辊力、采用可移动中间辊等手段在提高了轧机板形控制能力的同时,也带来了轧辊剥落、辊耗增加等负面结果。
目前国内已经投产的板带轧机在板形控制方面均存在一些不足。
本成果在板形控制和辊形设计思想上实现了突破和创新,通过与宝钢和武钢等大型钢铁企业的合作,获得了板形质量明显提高的实际效果,年经济效益超亿元。
获得了包括国家科技进步一等奖、原冶金部科技进步一等奖在内的多项奖励。
技术主要内容1、板带轧机变接触轧制技术板带轧机变接触轧制简称VCR(Varying Contact Rolling),由与轧机形式相适应的辊形设计(“VCR变接触支持辊”、“均压型PPT中间辊”、“轴向移位变凸度工作辊”和“ASR非对称自补偿工作辊”)及配套的工艺制度、控制模型和带钢平坦度检测装置等多项技术所组成。
具有增强轧机对板形的调控能力、提高消化来料板形和规格波动能力、使机架间负荷分配趋于合理、保证轧制过程顺行、提高板形质量和生产率、实现超平材超薄材等极限难轧品种的轧制、降低轧辊及轴承消耗等效果。
武钢和宝钢等企业的冷热连轧机已采用了这项技术。
2、板带轧机板形控制模型板形控制模型与控制系统是现代化板带轧机的重要标志,是实现板形自动控制的关键。
通本单位自主开发了热连轧机板形自动控制模型、板形板厚解耦模型、冷连轧机的弯辊自动设定模型和板形控制目标生成模型,并成功应用于大型工业轧机,属于国内首创。
该技术的开发和应用,不仅提高了轧机板形自动控制的水平,改善了产品质量,提高了生产效率,同时也显示在板形控制这个国际前沿领域,我国的理论研究和技术开发已经达到了国际先进水平。
应用范围及效益本项技术不需要对设备进行大的改造,因此适合国内的各类四辊、六辊轧机,如常规四辊、HC、CVC、WRS、PC等薄带轧机以及中厚板轧机等。
我国已经投产和正在建设的宽带钢轧机和中厚板轧机有几十套,以年产200万吨的连轧机为例,通过提高板形质量,年经济效益可达千万元。
铝板带轧制过程
一、熔铸 二、热轧 三、铸轧 四、冷轧 五、精整
铝合金牌号简介
1系:99.00%以上工业纯铝,电导性、耐腐蚀性、焊 接性能好、强度低
2系:Al——Cu合金,强度高、耐热性能和加工性能 良好
3系:Al——Mn合金,耐腐蚀性能、焊接性能好、塑 性好
4系:Al——Si合金,耐磨性、高温性能好 5系:Al——Mg合金,耐腐蚀性焊接性能好、抗疲劳
熔铸过程步骤:配料——投料——熔化— —熔化后搅拌、扒渣——预分析取样—— 加合金调整成分,搅拌——精炼——静 置——导炉铸造
熔铸过程几个关键参数
熔炼时一般设置炉温1050℃,过程中需要监控 料温,控制金属温度不超过770℃
在735℃左右进行扒渣操作,该温度有利于渣 液分离
精炼一般采用二次精炼方式,一次精炼加固体 精炼剂,二次精炼采用气体精炼方式
厚度>2mm
1#清洗 (切边至 成品预留 1-2mm)
冷连轧 (切边)
2#清洗
冷轧
1mm≤厚度≤2mm
(切边至 成品预留
成退
≤1.6mm卷材
2#拉矫
入库
1-2mm)
3#清洗(切
>1.6mm卷材/0.4mm鑫美
纵剪
厚度<1mm 边至成品预
留1-2mm)
冷轧机示意图
冷轧机
变形过程示意图
冷轧机各部件简述
纺布、硅藻土、白土) 灭火系统:防止断带起火
冷轧机用轧制油简介
轧制油主要为了在铝箔与工作辊之间形成一层油膜, 避免两者直接接触,起到保护铝箔表面的作用;在 铝箔较薄时,通过冷却工作辊,起到控制板形的作 用
轧制油是基础油和添加剂的混合液体,属于易燃物 一般冷轧用轧制油基础油为90#、箔轧为80# 添加剂的作用是为了提高油膜强度 添加剂的成分一般为脂类、醇类与月桂酸的配比 添加剂是造成退火油斑的主要原因
铜板带是什么铜板带的生产工艺流程
铜板带是什么铜板带是什么铜板带其实就是对铜板和铜带的统称。
铜板是指经过轧制的板材,轧制包括了热轧和冷轧。
铜带是指厚度在0.06~1.5mm之间的铜轧制加工品。
铜板带可以根据不同的牌号分类,大致分为带、紫铜板带、类板带、类板带。
下面还可以细分。
那么铜板带生产的工艺会有哪些呢铜板带再生产中会有哪些工艺缺陷,我们又该如何解决呢铜板带的工艺流程知道了铜板带是什么,我们接着来了解下铜板带的生产工艺:1、铸锭热轧生产工艺:熔炼→铸造(立式半连铸或立式连铸)→(锯切)→加热→热轧→铣面→冷轧→热处理→精整→包装入库。
铸锭热轧法生产工艺是现阶段应用最广泛的的主流生产工艺。
2、水平连铸生产工艺:熔炼→水平连铸带坯→(退火)→铣面→冷轧→热处理→精整→包装入库水平连铸生产工艺用于生产热轧困难的的合金品种(如锡磷青铜、)等。
其工序短,生产成本低,设备占地面小。
现阶段生产合金的比较单一,结晶器损耗大,铸坯上下表面组织均一性难以控制。
3、上引连续铸造法生产工艺:熔炼→上引带坯→(铣面)→冷轧→热处理→精整→包装入库上引连续铸造法生产工艺是国内新开发的的短流生产工艺,用于生产紫铜。
其生产流程短,耗能低。
4、立弯连续铸造生产工艺:熔炼→立弯铸造→(热轧)→(铣面)→冷轧→热处理→精整→包装入库其生产效率高,生产流程短,能耗低。
5、辊轮式/双带连续铸造法生产工艺:熔炼→辊轮/双带连续铸造→(热轧)→冷轧→热处理→精整→包装入库辊轮式/双带连续铸造法生产工艺是在研发的的短流生产工艺。
其生产流程短,耗能低。
6、连续挤压法生产工艺:熔炼→上引铜杆→连续挤压→冷轧→热处理→精整→包装入库。
连续挤压法生产工艺主要生产铜排和铜扁线。
其带坯宽度及生产产品品种受到限制。
对铜板带是什么有所了解后,我们再来了解下铜板带的熔炼设备:1、熔炼炉:主要分为感应电炉和燃气竖炉。
熔炼炉的特点:(1)电炉体积小,重量轻、效率高、耗电少;(2)炉子周围温度低、烟尘少、作业环境好;(3)操作工艺简单、熔炼运行可靠;(4)加热温度均匀、烧损少、金属成分均匀;(5)铸件质量好、熔化升温快、炉温易控制、生产效高;(6)炉子利用率高、更换品种方便。
- 1、下载文档前请自行甄别文档内容的完整性,平台不提供额外的编辑、内容补充、找答案等附加服务。
- 2、"仅部分预览"的文档,不可在线预览部分如存在完整性等问题,可反馈申请退款(可完整预览的文档不适用该条件!)。
- 3、如文档侵犯您的权益,请联系客服反馈,我们会尽快为您处理(人工客服工作时间:9:00-18:30)。
钢板轧制设备及工艺复习题1钢板的品种按厚度如何分类其技术要求有哪些P3答:钢板的品种规格按厚度分为两大类,即厚板和薄板。
一般称厚度为4mm以上者为中厚板;4mm以下着为薄板。
钢板生产的技术要求:1、尺寸精度要求。
(钢板的尺寸精度主要指厚度精度。
厚度精度包括纵向厚差和横向厚差的允许范围。
)2、板型精度要求。
(板型精度是指板带钢的平直度,表示板带纵向、横向各部位是否产生波浪或瓢曲。
)3、表面质量要求。
4、性能要求。
2厚板、热轧带钢、冷轧带钢生产的工艺过程,各主要工序的作用答:厚板生产工艺过程由原料及轧前准备、轧制和精整三大部分组成。
板坯的加热工艺作用:提高塑性、降低变形抗力,使坯料便于轧制,并提高产品质量,增大金属收得率。
除磷作用:保证钢板的表面质量,去除在加热过程中的炉生氧化铁皮和轧制过程中生成的再生氧化铁皮,减少轧辊磨损和消耗减少换辊次数。
热机械控制工艺作用:控制奥氏体状态、相变产物及组织状态、细化铁素体晶粒、减少珠光体片层间距,实现钢板高强度、高韧性和焊接性能的统一,生产出优质厚板。
轧后冷却作用:改变钢板的金相组织和力学下性能。
热轧带钢生产过程包括坯料选择和轧前准备、粗轧、精轧和轧后精整四个大的阶段。
板坯的加热工艺作用、除磷作用同上。
定宽作用:改变板坯宽度,以满足热轧带钢品种规格不同宽度的需要。
冷轧带钢主要生产工艺过程,主要由酸洗、轧制、退火、平整、镀(涂)层和精整工序组成。
酸洗作用:采用物理和化学的方法将带钢表面上得氧化铁皮清除掉。
退火作用:(1)消除带钢冷轧时的加工硬化;(2)获得不同的力学性能。
平整作用:(1)使退火带钢平整后达到一定的力学性能要求;(2)消除材料的屈服平台;(3)改善带钢的板形;(4)根据用户的要求生产不同粗糙度的带钢。
3热机械控制工艺的实质P16答:热机械控制工艺,是将控制轧制和控制冷却工艺结合。
在合理的化学成分设计的基础上,通过控制板坯出炉温度、低温阶段累计压下率和温度、终轧温度、轧后冷却速度和终冷温度等工艺参数,已达到控制奥氏体状态、相变产物及组织状态、细化铁素体晶粒、减小珠光体片层间距,从而实现钢板高强度、高韧性和焊接性能的统一,生产出用常规的轧制和热处理相结合工艺无法生产出的优质厚板品种,满足用户要求。
4影响有载辊缝形状的因素有哪些P211轧辊的热凸度。
轧制时轧件的变形功所转化的热量、轧件与轧辊间摩擦所产生的热量,以及高温轧件所传递的热量都会使轧辊受热;而冷却水、空气及轧辊接触的零件会使轧辊冷却。
在轧制过程中,加热和冷却条件沿辊身长度是不均匀的,靠近辊颈部分受热少、冷却快,轧辊中部则相反。
故轧辊中部温度高,热膨胀大,使轧辊产生热凸度。
轧辊的如凸度可以采用沿轧辊辊身调节冷却水流量分布的方法加以控制。
2轧辊的磨损。
轧辊与轧件、工作辊与支承辊间的相互摩擦都会使轧辊产生磨损。
影响轧辊磨损的因素很多,如轧辊与轧件的材料与温度、轧制力与轧制速度、前滑和后滑数值、工作辊和支承辊的滑动量和滑动速度、轧辊和轧件的表面硬度和粗糙度等,而且轧辊的磨损量随时间而改变。
一般工作辊和支承辊的磨损规律是中部磨损大、两端磨损小,板坯边部温宿较低会造成边部的局部磨损。
(轧辊磨损的补偿方法包括:1)通过生产组织的方法补偿轧辊磨损的影响。
2)调整轧辊热凸度补偿轧辊磨损。
3)轧辊的弹性弯曲。
4)轧辊的弹性压扁。
5)轧辊的原始凸度。
)5.什么是板形常见的板形缺陷有哪几种板形调节手段有哪些液压弯辊的机理及应用答:板形精度是指板带钢的平直度,表示板带材纵横向各部位是否产生波浪或瓢曲。
P4常见板型缺陷有波浪或瓢曲(即单边浪、双边浪、中浪、肋浪和局部瓢曲)。
板型调节手段有:调整轧辊辊型,控制轧辊间有载辊缝形状,调节沿板宽压下量的分布,使延伸沿板宽分布均匀,达到钢板平直度的要求。
1)采用具有板型调节功能的新型厚板轧机。
2)采用板型快速调节方法:(1)液压弯辊。
(2)轧辊分段冷却。
(3)轧辊的倾辊调整。
P23原理:弯曲工作辊的方法改变工作辊挠度的机理主要是改变工作辊和支承辊之间互相弹性压扁量的分布曲线。
弯曲支承辊方法改变工作辊挠度的机理是弯辊力改变了支承辊的弯曲挠度。
应用:对于窄板轧机,采用弯曲工作辊方法比较好;而对于宽板轧机,采用弯曲支承辊的方法比较好。
通常宽板轧机采用弯曲支承辊和弯曲工作辊联合使用,可以更有效地控制板型。
(所谓液压弯辊,就是采用液压缸的压力,使工作辊或支承辊在轧制过程中产生附加弯曲,以此改变有载辊缝形状,保证钢板的平直度和断面形状合乎要求。
(液压弯辊方法有弯曲工作辊和弯曲支承辊。
))6制订厚板压下规程受哪些因素影响画简图说明制订厚板压下规程的一般规律P21答:影响厚板压下规程的因素可分为设备能力和产品质量两大方面。
设备能力对压下量的限制条件包括三个方面:咬入条件、轧辊强度和电机功率。
产品质量对压下规程的影响需要考虑下面几个因素:1、金属塑性。
2、钢板的几何精度。
3、实行热机械控制工艺时,必须按控制轧制要求来确定压下量,以保证对轧制阶段累计变形量的要求,确定钢板的金相组织和力学性能。
将整个轧制过程分为粗轧A和精轧B两个阶段。
粗轧开始阶段,由于轧件比较厚,又称咬入限制阶段A’。
在咬入条件、除磷和纵向辗平限制下,压下量不允许太大。
轧数道次后,咬入限制消除,可增大相对压下量ε(%),增大轧制力P,充分发挥轧辊强度和电机能力,迅速减小板坯厚度,缩短轧制周期,提高答:四辊可逆式机座是目前厚板轧机工作机座的主要机型。
它主要由机架、辊系、平衡装置、压下系统、弯辊装置和换辊装置等组成。
P33换辊过程:厚板轧机工作辊换辊,由机架内的活动轨道升起,托起下工作辊轴承座的滚轮,与操作侧固定轨道面成水平,由换辊小车将工作辊由窗口内拖出。
支承辊换辊则由两个液压缸推动滑架沿斜轨上升,将带有滚轮的托架升起,托起活动轨道与固定轨道成水平线重合,用换辊小车上的齿轮和轨道上的长齿条,将支承辊由窗口内移出。
P378.厚板剪切设备有哪几种看图说明厚板圆盘剪的结构组成和工作原理。
P43答:厚板的剪切设备有斜刃剪、滚切剪和圆盘剪。
主要结构:机架移动装置、刀盘侧向间隙调整机构、刀盘中心距调整机构、刀盘传动装置、上刀盘偏移机构、碎边机。
原理:圆盘剪的上下剪刃都是盘装的。
刀盘连续旋转,可以纵向连续剪切钢板和带钢。
9.传统热带钢轧机有哪几种类型说明各自的特点P98答:根据粗轧机组布置形式和工作制度的不同,传统热带钢连轧机可分为半连续式、全连续式和3/4连续式。
半连续式热带钢轧机的特点是:1由于粗轧机组设有1~2架可逆式机座,因此可以灵活的改变轧制道次和压下量,能适应多品种规格、小批量的产品订货;2粗轧机组的轧制周期一般比精轧机组长,因此产量比其他形式的热带钢连轧机低,一般在150~300万t/a;3生产线短,设备少,投资少。
全连续式热带钢轧机的特点是:1适用于品种规格范围小、批量大的订货;2年产量在300~600万t之间;3生产线长,设备多,投资大,生产上没有3/4连续式热带钢轧机有优势而很少建造。
3/4连续式热带钢轧机的特点是:1生产灵活性大,适于批量小、品种规格多的生产;2年产量在300万t以上;3生产线短,设备少,投资较少,近年来较广泛地被厂家采用。
10板坯定宽压力机的作用和结构组成P81答:定宽压力机作用:在板坯前进过程中,用侧压模块连续的进行大侧压量的调宽,改变带钢宽度,满足热轧带钢品种规格不同宽度需要。
结构组成:1、测压机构、对板坯进行侧压2、同步机构、使侧压模块在测压时与板坯同步,并在侧压结束时,将侧压模块拉回原位3、宽度调整机构,改变板坯宽度时,调整侧压模块开口度。
11 PC轧机和CVC轧机控制板型的原理,这两种轧机成一定的角度,通过改变交叉角控制轧辊的等效凸度,控制轧制带钢的板形和板凸度。
增加了轧辊交叉机构,以及由于轧辊交叉给轧机机构带来的相应变化。
CVC采用S型轧辊,上下轧辊的辊型相反布置,调节轧辊的轴向位置可以获得不同的辊缝形状。
保证轧出带材的板形和板凸度满足要求。
控制原理:轧辊轴向移动可以获得连续的凸度变化,同时配合以液压弯辊,具有良好的板形控制能力。
具有CVC技术所要求的工作辊轴向移动装置,以及具有较强的板厚、板凸度和板形控制能力的调整机构。
12带钢切头飞剪有哪几种形式各自的特点P155答:切头飞剪有曲柄式和转鼓(滚筒式)两种形式。
曲柄式切头飞剪特点:曲柄式切头飞剪的剪切机构属于四连杆机构,能够保证剪切过程中上、下剪刃接近做平行运动,同时在剪切区剪刃基本上垂直轧件,剪切断面的质量好,但这种机构的剪切机构的剪股和摆杆会摆动,动负荷冲击大,影响剪切速度提高。
另外切头和切尾用一把刀剪切,切口智能切成直线。
转鼓式切头飞剪有同周速和异周速两种形式。
同周速转鼓上下转鼓直径相同,转速相等,上下剪刃圆周速度相等。
转鼓绕转动中心旋转,东平衡性能好,可以提高剪切速度,但上、下剪刃不能垂直切入轧件,因此,剪切实质上不是完全切断,而是有很大拉断的成分,剪切质量不高。
异周速转鼓式切头飞剪特点(1)剪切特性好。
(2)剪刃的使用周期延长。
(3)转鼓的传动在操作侧增加了1对平衡齿轮。
13冷带钢轧机机座布置型式有哪几种P206答: 1、普通死四辊冷轧机,2、带有轧辊轴向移动机构的冷轧机。
3、采用特制滚动轴承多段支承辊的多辊轧机,4、改变轧辊凸度的轧机5、轧辊成对交叉的轧机6、异步轧制轧机。
14 HC轧机的原理及其系列轧机的命名答:原理:中间辊的轴向位置根据不同板宽进行调整,减小轧制带钢的边部减薄;减小或消除工作辊和支撑辊之间的有害接触区,明显增加液压弯辊的板形控制功能;采用比较小的工作辊直径,减少轧制道次或增加坯料厚度;中间辊的轴向移动和液压弯辊配合使用,增加了液压弯辊的板形控制能力。
命名:工程上通常把中间辊做轴向移动和工作辊设有液压弯辊的轧机称为HC轧机;把中间辊做轴向移动和工作辊、中间辊都设有液压弯辊的轧机称为UC轧制定厚板压下规程的一般规律A-粗轧阶段 B-精轧阶段机;把在UC轧机基础上再增设有工作辊做轴向移动的轧机称为UCMW轧机;把四辊轧机的工作辊做成可以轴向移动轧机称为HCW轧机。
15二十辊轧机辊系布置并说明各个辊子的作用以及板形调节原理。
答:布置图见P214。
工作辊:完成轧制过程;第一中间辊:轴向移动控制板形;第二中间辊:传动扭矩;外层支承辊:承受轧制压力,满足轧辊重磨的要求,特别是3列短圆柱轴承有比较厚的外环,装配时将直径较大的装在中间,以形成总体的辊凸度。
外层支撑辊各自作用:(1)B、C辊:承担轧制压力下和辊型径向调节功能;(2)F、G辊:承担轧制线高度补偿调节;(3)A、D、E、H辊:承担轧辊位置补偿。
调整:通过B、C辊及其压下机构完成压下调整。
二十辊轧机同时设有径向调整和轴向辊型调整机构。