手机锌合金外壳结构设计注意事项
手机外壳模具设计要点
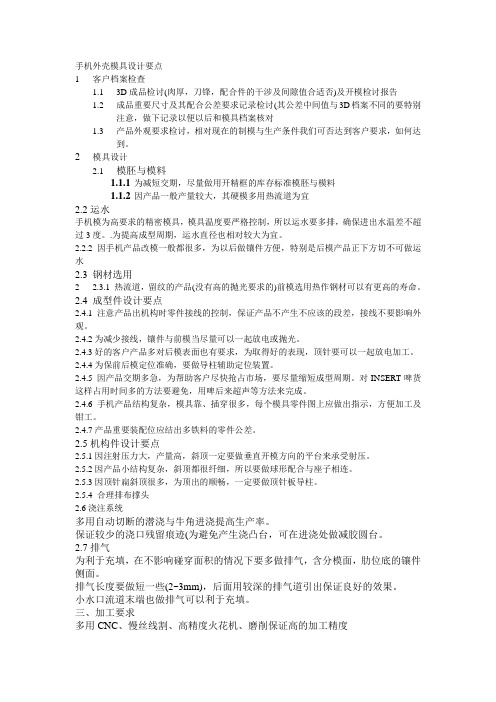
手机外壳模具设计要点1客户档案检查1.13D成品检讨(肉厚,刀锋,配合件的干涉及间隙值合适否)及开模检讨报告1.2成品重要尺寸及其配合公差要求记录检讨(其公差中间值与3D档案不同的要特别注意,做下记录以便以后和模具档案核对1.3产品外观要求检讨,相对现在的制模与生产条件我们可否达到客户要求,如何达到。
2模具设计2.1模胚与模料1.1.1为减短交期,尽量做用开精框的库存标准模胚与模料1.1.2因产品一般产量较大,其硬模多用热流道为宜2.2运水手机模为高要求的精密模具,模具温度要严格控制,所以运水要多排,确保进出水温差不超过3度。
.为提高成型周期,运水直径也相对较大为宜。
2.2.2因手机产品改模一般都很多,为以后做镶件方便,特别是后模产品正下方切不可做运水2.3 钢材选用2 2.3.1 热流道,留纹的产品(没有高的抛光要求的)前模选用热作钢材可以有更高的寿命。
2.4 成型件设计要点2.4.1注意产品出机构时零件接线的控制,保证产品不产生不应该的段差,接线不要影响外观。
2.4.2为减少接线,镶件与前模当尽量可以一起放电或抛光。
2.4.3好的客户产品多对后模表面也有要求,为取得好的表现,顶针要可以一起放电加工。
2.4.4为保前后模定位准确,要做导柱辅助定位装置。
2.4.5 因产品交期多急,为帮助客户尽快抢占市场,要尽量缩短成型周期。
对INSERT啤货这样占用时间多的方法要避免,用啤后来超声等方法来完成。
2.4.6手机产品结构复杂,模具靠、插穿很多,每个模具零件图上应做出指示,方便加工及钳工。
2.4.7产品重要装配位应结出多铁料的零件公差。
2.5机构件设计要点2.5.1因注射压力大,产量高,斜顶一定要做垂直开模方向的平台来承受射压。
2.5.2因产品小结构复杂,斜顶都很纤细,所以要做球形配合与座子相连。
2.5.3因顶针扁斜顶很多,为顶出的顺畅,一定要做顶针板导柱。
2.5.4 合理排布撑头2.6浇注系统多用自动切断的潜浇与牛角进浇提高生产率。
手机精密五金结构设计详解-新
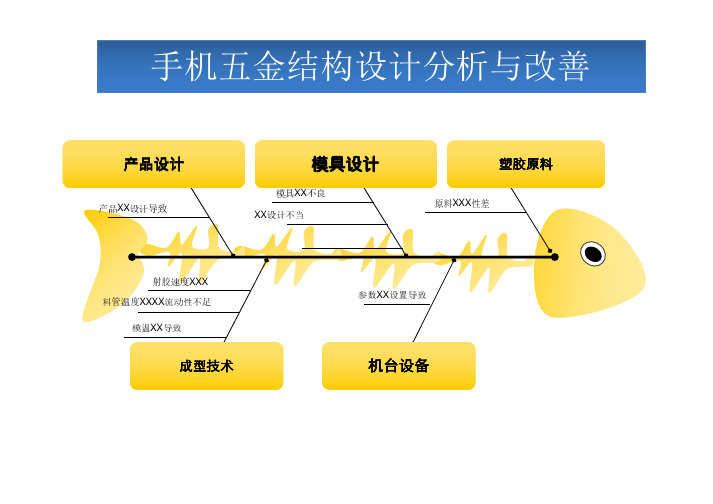
产品设计模具设计塑胶原料机台设备成型技术产品XX 设计导致模具XX 不良射胶速度XXX料管温度XXXX 流动性不足模温XX 导致参数XX 设置导致手机五金结构设计分析与改善五金的产品结构规范要求目的:为了规范我们在评审或者结构设计,并且更有利生产冲压模具的要求,下面提出一些关于产品结构设计的要求。
注明:t代表料厚。
1.模内注塑钢片的料厚不能小于0.3MM.2.模内注塑件最好不要采用铝件.模内注塑钢片的设计要求钢片的设计好坏直接影响模内注塑后的前壳的产品平面度,当然,产品的整体平面度也要看塑胶的结构,不能一概而论!注:1.产品的材料一般情况下用SUS304 ½ H ,SUS304 ¾ H.推荐SUS304 ½ H ,整形回弹小2.模内注塑钢片的料厚不能小于0.3MM.3.组装的钢片料厚不能小于0.2MM.2t 所示折弯的高度不能小于2t,小于的2t产品的强1.0所示双折弯的直伸位的高度不能小于1.0,小于1.0会压压不平,且影响产品的公差及尺寸,同时也可能会影响到模内注塑.所示过料孔要求要空间的情况下要做到果不能,最小也要做∮1.0(料厚在0.4),上做上C0.15,便于扣料.所示折弯中间的过料孔要求要空间的情况下要做到8-10MM所示无特别的要求,过料孔的孔间距要求1.如果钢片包在塑胶中间,过料孔间距为8-11MM.4MM 2.如要浮在表面,过料孔的间距为6-8MM.如果此折弯是在TP面上,为保证钢片的平面度,不影响保证在1.0MM左右,如果包在塑胶中间,平面度要求不高孔到边上的距离标准为1.5t,不能小于1t.2.5减重腰形孔规格要求为2.5X12MM左右.斜度为45度以上.1.00.3如果这是螺柱定位孔,此孔到折弯边上的距离不能小0.3,不然冲出来孔会变形,且会影响螺柱的烧焊钢片的大面积蚀刻不能超过0.15,最好是0.2会影响产品的平面度.这种结构对于产品的平面度是极不利的,模内注塑注1.0长方孔到边上的距离要求为1.0左右,不然模具的强度不够,另一方面产品也会变形.孔的长度为15-25MM1.0以上1.0左右过桥式拉料孔的规格.寸钢片的去硬力孔要求做花窗类,不然模塑注塑后会变形,且有响声.要求如下.料厚不能小于0.4MM.∮1.06.0以上120度R0.2以上深0.3-0.5过胶托包孔的要求.模内注塑钢片内R为清角(无R),外R为壁厚大小的以便模内注塑封胶.R=t+0.2此折弯上的R一般会是R=t+0.2,只能大不能小。
锌合金开发评审注意事项
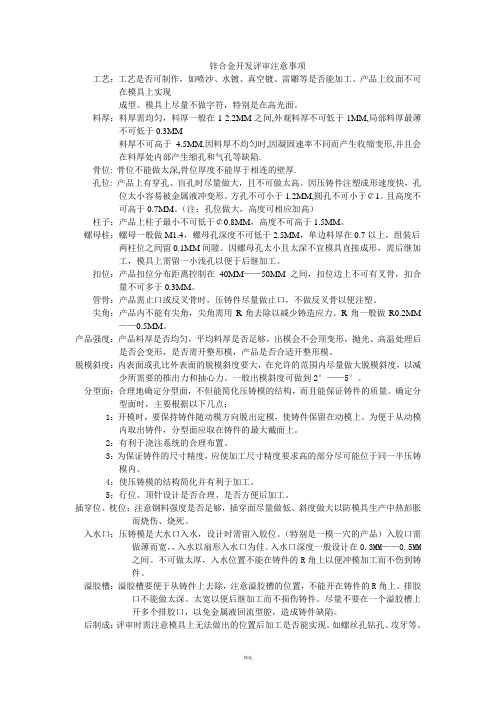
锌合金开发评审注意事项工艺:工艺是否可制作,如喷沙、水镀、真空镀、雷雕等是否能加工。
产品上纹面不可在模具上实现成型。
模具上尽量不做字符,特别是在高光面。
料厚:料厚需均匀,料厚一般在1-2.2MM之间,外观料厚不可低于1MM,局部料厚最薄不可低于0.3MM料厚不可高于4.5MM.因料厚不均匀时,因凝固速率不同而产生收缩变形,并且会在料厚处内部产生缩孔和气孔等缺陷.骨位: 骨位不能做太深,骨位厚度不能厚于相连的壁厚.孔位: 产品上有穿孔、盲孔时尽量做大,且不可做太高。
因压铸件注塑成形速度快,孔位太小容易被金属液冲变形。
方孔不可小于1.2MM,圆孔不可小于¢1。
且高度不可高于0.7MM。
(注:孔位做大,高度可相应加高)柱子:产品上柱子最小不可低于¢0.8MM,高度不可高于1.5MM。
螺母柱:螺母一般做M1.4,螺母孔深度不可低于2.5MM,单边料厚在0.7以上,组装后两柱位之间留0.1MM间隙。
因螺母孔太小且太深不宜模具直接成形,需后继加工,模具上需留一小浅孔以便于后继加工。
扣位:产品扣位分布距离控制在40MM——50MM之间,扣位边上不可有叉骨,扣合量不可多于0.3MM。
管骨:产品需止口或反叉骨时,压铸件尽量做止口,不做反叉骨以便注塑。
尖角:产品内不能有尖角,尖角需用R角去除以减少铸造应力。
R角一般做R0.2MM ——0.5MM。
产品强度:产品料厚是否均匀,平均料厚是否足够,出模会不会顶变形,抛光、高温处理后是否会变形,是否需开整形模,产品是否合适开整形模。
脱模斜度:内表面或孔比外表面的脱模斜度要大,在允许的范围内尽量做大脱模斜度,以减少所需要的推出力和抽心力。
一般出模斜度可做到2°——5°。
分型面:合理地确定分型面,不但能简化压铸模的结构,而且能保证铸件的质量。
确定分型面时,主要根据以下几点:1:开模时,要保持铸件随动模方向脱出定模,使铸件保留在动模上。
为便于从动模内取出铸件,分型面应取在铸件的最大截面上。
手机模内注塑五金设计要点

五金件厚度0.4
1.3 五金件结构在正常情况下,以4面有围筋骨结构.此结构不易变 形.也方便其与塑胶产品之间的定位.
做成3面或4面围筋骨,防止 产品翘曲变形.
1.4 塑胶产品与五金件的定位,可以通过扣位及侧面小孔将其与塑胶 产品定位.不易与产品分离.
此处侧壁圆孔定位 及扣位定位.
1.5 五金件的配合尽量形成碰穿结构.防止毛边的产生及五金件的划伤.尽 量将五金件与塑胶配合以碰穿形式设计.避免插入结构.
一.产品结构分析
1.1 首先在产品设计的同时,一定要对产品的结构进行可行性分 析,主要体现在五金件强度,五金件与塑胶件的定位,亦即五金件成型时 的定位孔设计等各方面都要进行整体综合分析. 1.2 五金件结构控制,一般来说模内注塑五金件的厚度控制在 0.3-0.4比较适中.0.2等都太单薄,容易翘曲变形.难以控制其五金产品精 度及注塑成型后产品的变形率.
模内注塑五金不宜太小在模 具上不好定位
非常感谢大家!
模内注塑五金钢片的分析报告
随着工业的不断发展,产品的要求愈来愈高,超薄手机市场需求量 愈来愈大.由此而来一些小型产品的薄胶位无法达到比较理想的状态, 难以打饱走胶.故在此种情况下,钢片模内注塑渐成主流.由于钢片可以 加工到0.2-0.4厚.将实现塑胶无法打饱的问题.但是随之而来的是由于 产品收缩而导致产品变形问题.现在众多厂家中解决产品变形问题已经 成为各公司的公关项目的难题. 通过学习及总结, 现对钢片模内注塑之问题点简易分析如下.
胶位厚薄均匀
二.模具设计应注意事项.
2.1 浇口位置布置均匀.要对称布置,让走胶平行.收缩平衡.避免因浇口位置 放置不均引起的产品收缩变形严重现象.
浇口位置要对称 分布.
2.2 在放产品收缩时,必须将五金件及塑胶件分开,单独放塑胶件收缩.且 纵横方向收缩不一致.长度方向收缩大些.宽度方向小些.(整体产品收缩 偏小)
手机锌合金外壳结构设计注意事项(精)

5、避空位做斜面后再 倒圆角,既美观又有利 于压铸。
6、电池盖的头部倒≥0.5mm 的圆角,避免装配时刮伤产 品。
7、热熔柱孔做成全圆角,有利 于压铸填充,减少气孔和裂纹。
十一、装配
1、装配间隙检查 a、扣位的扣合量0.20~0.25,一般先做0.20,实际装配时再根据情况加胶。 b、电池盖和底壳无装配处的装配间隙做到0.2以上,以免会刮花塑胶件 c、产品应设积油避空位 d、面壳和底壳的扣位处的二个扣合面应做成10度的斜面配合,以利于拆机
1、骨位厚度≥1mm, 2、骨位无装配关系的面的出模角度≥3°拔模量不小于0.1mm,有装配位的骨 位面一般按拔模量0.05mm计算, 3、骨位的根部在不影响装配时倒不小于0.5mm以上的圆角。 4、产品上尽量不要有太多的骨位,一般骨位间距离≥10mm,最小不要小于 3mm。
六、螺丝孔
1、M1.4的螺丝的旋合长度在1.5mm~3.0mm之间比较合适,一般情况做 2.0mm。 2、底孔深度=螺纹深度+ 1.5倍螺距( 0.45mm ) 。 3、螺丝柱外径一般做3.5mm,最小可做2.8mm,底部料厚≥ 0.8mm。 4,具体的尺寸见下图。
此位厚度0.6mm,宽2.15mm, 长49.2mm,压铸后产品严重变形。
此两处厚度0.55mm,宽2.0mm, 有强度要求,产品变形,易断。
此位厚度0.75mm,热熔孔边距 0.48mm,有强度要求,产品变形, 易断,无法生产。
此处料厚0.7mm,宽度 最小为0.566mm,产品 无问题。
五、骨位
此处R0.15MM,后加工抛光后会产生工 艺R角(R0.1—0.2) ,影响分型,开 模时取消R。
电池盖上的扣位对锌合金来 说作用不大,
四、料厚
手机结构设计注意事项

手机结构和按键设计注意事项1,平均壳体厚度≥1.2,周边壳体厚度≥1.42,壁厚突变不能超过1.6倍3,筋条厚度与壁厚的比例为不大于0.75,所有可接触外观面不允许利角,R ≥R0.34,止口宽0.65mm,高度≥0.8mm(保证止口配合面足够,挡住ESD)5,止口深度非配合面间隙0.15 止口配合面5度拔模,方便装配6,止口配合面单边间隙0.05 美工槽0.3X0.3,翻盖/主机均要设计。
设计在内斜顶出的凹卡扣壳体上。
(不允许设计在外滑块出的击卡扣壳体上,避免滑块破坏美工槽外观)7,死卡(最后拆卸位置)扣位配合≥0.7;活卡扣位配合0.5mm(详见图)8,卡扣位置必须封0.2左右厚度胶。
即增加了卡扣的强度也挡住了ESD9,扣斜销行位不得少于4mm.在此范围内应无其他影响行位运动的特征10,螺丝柱内孔φ2.2不拔模,外径φ3.8要加胶0.5度拔模,内外根部都要倒R 0.2圆角11,螺母沉入螺丝柱表面0.05 螺丝柱内孔底部要留0.3以上的螺母溶胶位,内部厚度≥0.8.根部倒圆角12,与螺丝柱配合的boss孔直径φ4,与螺丝柱配合单边间隙0.1(详见图14)13,boss孔位置要加防拆标签,壳体凹槽厚度0.114, 翻盖底(大LENS)与主机面(键帽上表面)间隙≥0.415,检查胶厚或薄的地方,防止缩水等缺陷(X\Y\Z方向做厚度检查)16,主机面连接器通过槽宽度按实际计算,连接器厚度单边加0.3MM17,主机连接器要有泡棉压住18,主机转轴到前螺丝柱间是否有筋位加强结构19,主机面转轴处所有利角地方要加R20,主机转轴胶厚处是否掏胶防缩水21,主机底电池底下面最薄≥0.6(公模要求模具开排气块)22,挂绳孔胶厚≥1.5X1.8,挂绳孔宽度≥1.523,翻盖缓冲垫太小时(V8项目),不采用双面胶粘,设计拉手,倒扣钩住壳体0.324,凡是形状对称,而装配时有方向要求的结构件,必须加防呆措施。
也就是其它任何方向都无法装配到位25,SIM卡座处遮挡片,在壳上对应处加筋压住遮光片,防止遮光片翘起影响SIM卡插入26,flip上、下壳体之间加上反卡位,防止壳体上下,左右外张,上下壳加支撑筋,防止上下按压,感觉壳体软(如附图所示,参考stella项目)27,双色喷涂件在设计时要考虑给喷漆治具留装卡的位置,0.6宽x0.5深的工艺槽28,双色喷涂分界处周边轮廓线尽量圆滑,曲线变化处R角≥0.529,双色喷涂的治具模具,要求是精密模具,一模一穴,治具注塑材料采用壳体基材相同30,做干涉检查31,PC料统一成三星PC HF-1023IM32,PCABS料统一成GE PCABS C1200HF33,弧面外观装饰件双面胶要求选用DIC8810SA(高低温/耐冲击性能好) 34,平面外观装饰件双面胶采用3M9495,或DIC8810SA(高低温/耐冲击性能好)35,双面胶最小宽度≥1.0(LENS位置最小1.2)36,可移动双面胶可选用3M9415(其粘性两面强度不同,弱面拆卸方便) 热熔胶采用?37,遇水后变色标签可选用3M5557(适用于防水标签)38,Foam最小宽度≥1.0mm PIFA天线下面连接器等需要压,采用EVA白色材质,吸波最少。
手机机壳结构评审设计要点
內容摘要:本教材是针对公司在机壳设计中遇到问题进行的总结,故一1.面、底壳之间螺丝柱距离保持在2.面、底壳止口间的间隙控制在出段差;3.SIM卡处须作斜面,直身面不能太高,否则卡难取;4.电池盖扣位厚度保持在5.中框叉骨与机壳的组装间隙喷油为0.08mm;6.手机设计时应考虑是否有喇叭孔、吊绳孔、RF塞孔;7.电池盖要考虑增加防磨点,防止机壳磨损8.产品外观如果蚀纹1.翻盖机上半部与下半部分的间隙标准为0.6mm,防止镜片与按键干涉;2.翻开时角度控制在160度左右;3.翻开面壳与中壳耳朵之间的间隙为4.排线槽的宽为壳不能干涉5.所有装配间隙正常在时底部要留0.15mm-0.5mm左右的间隙;6.转轴与壳体配合间隙为单边主),防止转动时有异响7.面壳转轴孔两侧必须倒斜角,且与中壳配合间隙为0.05mm;8.中壳垫要与面壳干涉以三:滑盖机1.整机组装0.25mm-0.3mm之间;滑板机应设计防磨条(增加手感顺滑),材料为POM ,且尽量大面积,如U 型防磨条(防止滑动有异影)。
2.滑板机应设计防磨条(增加手感顺滑),材料为POM ,且尽量大面积,如U 型防磨条(防止滑动有异影);滑板机防磨条与机壳的间隙为0.1mm。
3.面壳与中壳应设计边0.15mm;滑板机应设计四个缓冲垫,同时可调节合盖后,上下方有段差。
4.滑板机应设计四个缓冲垫,同时可调节合盖后,上下方有段差。
滑板滑动是,需考虑面壳下方不能与中壳有摩擦或干涉现象(特别当中壳按键为金属按键时)5.滑板滑动是,需考虑面壳下方不能与中壳有摩擦或干涉现象(特别当中壳按键为金属按键时)6.滑板处应做夹具遮喷;7.防磨条与机壳的间隙在8.设计时要考虑9.滑开后上滑块与下滑块按键上方应保证有距离;10.滑板定位孔要与机壳实配,防止组装偏位;11.主体壳的尺寸要尽量控制,滑板尺寸要求重要。
12.设计时需考虑面壳、中壳的强度,尽量避大面积碰穿位置,以免壳体成型产生变形。
手机外壳结构设计指引
⼿机外壳结构设计指引结构设计注意事项z PCBA-LAYOUT及ID评审是否OKz标准件/共⽤件z内部空间、强度校核:z根据PCBA进⾏⾼度,宽度(⽐较PCBA单边增加2.5~~3.0,或按键/扣位处避空)与长度分析。
z装配⽅式,定位与固定;z材料,表⾯⼯艺,加⼯⽅式,z成本,周期,采购便利性;塑料壳体设计1.材料的选取ABS:⾼流动性,便宜,适⽤于对强度要求不太⾼的部件(不直接受到冲击,不承受可靠性测试中结构耐久性测试的部件),如⼿机内部的⽀撑架(Keypad frame,LCD frame)等。
还有就是普遍⽤在要电镀的部件上(如按钮,侧键,导航键,电镀装饰件等)。
⽬前常⽤奇美PA-727,PA757等。
PC+ABS:流动性好,强度不错,价格适中。
适⽤于绝⼤多数的⼿机外壳,只要结构设计⽐较优化,强度是有保障的。
较常⽤GE CYCOLOY C1200HF。
PC:⾼强度,贵,流动性不好。
适⽤于对强度要求较⾼的外壳(如翻盖⼿机中与转轴配合的两个壳体,不带标准滑轨模块的滑盖机中有滑轨和滑道的两个壳体等,⽬前指定必须⽤PC材料)。
较常⽤GE LEXAN EXL1414和Samsung HF1023IM。
在对强度没有完全把握的情况下,模具评审Tooling Review时应该明确告诉模具供应商,可能会先⽤PC+ABS⽣产T1的产品,但不排除当强度不够时后续会改⽤PC料的可能性。
这样模具供应商会在模具的设计上考虑好收缩率及特殊部位的拔模⾓。
上、下壳断差的设计:即⾯刮(⾯壳⼤于底壳)或底刮(底壳⼤于⾯壳)。
可接受的⾯刮<0.15mm,可接受底刮<0.1mm,尽量使产品的⾯壳⼤于底壳。
⼀般来说,⾯壳因有较多的按键孔,成型缩⽔较⼤,所以缩⽔率选择较⼤,⼀般选0.5%。
底壳成型缩⽔较⼩,所以缩⽔率选择较⼩,⼀般选0.4%,即⾯壳缩⽔率⼀般⽐底壳⼤0.1%。
即便是两件壳体选⽤相同的材料,也要提醒模具供应商在做模时,后壳取较⼩的收缩率。
手机结构设计注意事项
手机结构设计注意事项及经验总结一、常出现的机构设计方面的问题。
1.Vibratorvibrator安装位置的选择很重要。
其一,要看装在哪儿振动效果最好;其二,最好vibrator 附近没有复杂的rib位,因为vibrator在ALT 时会有滑动现象,如碰到附近的rib位可能被卡住,致使来电振动失败。
2.吊饰孔由于吊饰孔处要承受15磅的拉力,所以housing的吊饰孔处的壁厚要保证足够的强度。
3.Sim card slot由于不同地区的sim card的大小和thickness有别,所以在进行sim card slot 的设计时,要保证最大、最厚的sim card能放进去,最薄的sim card能接触良好。
4.Battery connector有两种形式:针点式和弹簧片式。
前者由于接触面积小,有可能发生瞬间电流不够的现象而导致reset,但占用的面积小。
而后者由于接触面积大,稳定性较好,但占用的面积大。
5.薄弱环节XU在drop test时,手机的头部容易开裂。
主要是因为有结合线和结构复杂导致的注塑缺陷。
Front housing的battery cover button处也易于开裂,所以事先要通过加rib和倒角来保证强度。
6.和ID的沟通。
机构完成pcb的堆叠后将图发给ID,由于这关系到ID画出来的外形能否容纳所有的内部机构,所以在处理时要很小心。
Pcb上的所有的元件都要取正公差,所包含的元件要齐全,特别是那些比较大的元件;小处也不能忽略,比如sponge和lens的双面背胶等。
7.缩水常发生部位boss与外壳最好有0.8-1mm的间隙,要避免boss和外壳连在一起而导致缩水。
housing 上antenna部分,由于结构需要(要做螺纹),往往会比较厚。
8.前后壳不匹配95%情况下,手机的后壳都会大于前壳,所以要提醒模厂,让它在做模时,后壳取较小的收缩率。
这是因为两者的注塑条件不同,后壳需要较大的注塑压力。
锌合金手机压铸技术
锌合金手机压铸技术原文地址:/info/detail/65-45736.html文/东莞市石碣华丰五金厂/梁诗雅摘要:介绍手机外壳典型模具的流道设计和锌合金原料的科学使用,包括流道和溢流槽开设、原料型号的合理选择等,并对生产控制的办法进行了分析。
关键词:成本;原料;模具;锌合金压铸当手机已成为人们生活中必需品时,手机外观设计也随着时尚潮流日新月异,外壳材料从塑料改为合金压铸制造,赋予了手机更好的质感和金属光泽,使手机上了一个档次,又具有时代特色美感。
从2008年下半年以来,锌合金压铸的手机外壳大规模兴起,深圳和东莞区域形成制造手机配件的投资热点,大量以2~3台88T压铸机为主设备建厂生产经营,这些投资者大多数从塑料行业和五金行业转型而来,对压铸工艺较为生疏,本文将分析锌合金手机外壳压铸技术。
以塑胶和五金模为基础,琢磨压铸生产,随着时间推移至今,手机壳加工业经过约2年多的发展,从刚开始生疏的生产工艺,走向成熟的阶段,模具的设计、压铸参数的掌控、批锋的清除、抛光的熟练和表面处理的技术都有了不同的迈进,生产的成本也不断下控。
市场生意的高单价和高利润时期已过去,激烈的竞争,面对成本压力的创业者,坚持在锌合金压铸产品生产经营,自然步入变革时期,“生意价逼近生产成本”,这是使生产者面临的严峻考验。
那么,成本的有效控制是必然,成本则需从原材料、生产工序、自动化生产、节约人力资源、技术改革等过程来科学控制。
提高产量和稳定生产品质是有效控制成本的根源,主要表现有:(1)原材料的合理选用和充分利用;(2)模具技术的提高;(3)后加工工序的产品合格率的提升;(4)人力资源的控制;(5)表面处理的掌控。
1.模具的合理设计(1)名称:手机面盖;(2)产品:40g;(3)水口的总重量:约45g。
从生产的结果统计,如图1所示合理的模具唧咀、流道料位和冷料槽设计,使产品压铸生产毛坯的合格率达98%;生产炉渣可控于10%~15%,通常生产厂会产炉渣15%~30%;产品后加工:清理批锋容易,不需冲模,工序减少,节省人力资源,有效控制损耗,抛光工序加工方便,产量提高;图2所示是模具有缺陷的流道和浇口设计,后加工困难,产量低,成本高。
- 1、下载文档前请自行甄别文档内容的完整性,平台不提供额外的编辑、内容补充、找答案等附加服务。
- 2、"仅部分预览"的文档,不可在线预览部分如存在完整性等问题,可反馈申请退款(可完整预览的文档不适用该条件!)。
- 3、如文档侵犯您的权益,请联系客服反馈,我们会尽快为您处理(人工客服工作时间:9:00-18:30)。
此位厚度0.6mm,宽2.15mm, 长49.2mm,压铸后产品严重变形。
此两处厚度0.55mm,宽2.0mm, 有强度要求,产品变形,易断。
H 、锌合金件一般只适用手机的面壳和电池盖
二、出模角度分析改图
1、型腔表面的出模角度一般≥1.5°,拔模量≥0.05mm,拔模后小端尺寸≥0.5mm。 2、型芯表面的出模角度一般≥3°,拔模量≥0.1mm,拔模后小端尺寸≥0.8mm。 3、产品外观有直身位需做行位时,具体的情况可按照下表计算。
外表面α
内表面β
配合面 最小α
非配合 面
最小α
精度级 α
标准级 α
配合面 最小β
非配合面最 小β
精度级
β 标准级
β
0.17° 0.25° 1.9
2.9
0.25° 0.75°
3.8
5.8
H
H
h
h
备注:最小出模角度要求模具表面粗糙度在Ra0.1以上,单边拔模量最小值为0.03mm。
三、产品分型面的设计
1、产品分型面应设计成直线状或平面状,尽量采用缓慢过渡的形式,使金属 液流动平缓。
九、产品圆角
铸造圆角可使金属液流畅,气体容易排出,并可避免锐角而产生裂纹,下面是
几种需倒圆角情况。
1、此处圆角 ≥0.5mm。
2、这种结构的底部倒≥0.5mm 的圆角
3、产品外形的拐角 处需倒≥0.3mm的圆 角
4、此种结构需倒 ≥0.3mm的圆角
十、铸孔
1、铸孔一般≥Φ1.5mm; 2、外观表面不要做类似喇叭孔 ,否则抛光容易抛塔,去披风和抛光时不好清 除孔内垃圾; 2、铸孔与产品边的距离一般≥1.5mm,最小1.0mm。
线条间隔 ≥0.25mm
文字凸出绿色 面0.15mm
字框低于 产品面0.2mm
字体高度≥1.5mm
线条宽度≥0.2mm
八、网格纹
1、网格纹的造型要有利于模具制造和产品出模。 2、网格纹的深度一般做0.1mm,最深不要超过0.2mm。 3、网格纹的出模角度一般做10 °~ 15°,当底部只是角边时,角度≥90°。
锌合金
锌合金
1、评估工艺,锌合金常用的工艺有以下几种: A、水镀:镀白铬(银白色)、三价黑铬(浅锖色) B、真空镀:金黄色、黑色、浅枪(锖)色、深枪(锖)
色、玫瑰金、咖啡色 C、双色效果:双色镀可分为水镀双色镀和真空镀双色
镀,双色可分为同种颜色的不同效果和不同的两种颜色两 种情况。
D、烤漆:烤漆可以做黑色、银色、蓝色等多种颜色。 E、镭雕:镭雕一般在水镀和真空镀件表面。 F、机械拉丝:水镀和真空镀后可进行机械拉丝,拉丝 后需涂一层透明漆。 G、丝印和移印。
d、面壳和底壳的扣位处的二个扣合面应做成10度的斜面配合,以利于拆机
此处的二个扣合面做成10度 的斜面配合
电池盖和底壳无装 配处的间隙做到 0.2以上
螺丝长度
螺丝柱外径
螺丝装配示意图
底部料厚
>0.8
Ø1.2 C0.3X45°
100°
Ø1.4
底孔深度
ห้องสมุดไป่ตู้Ø1.1 压铸孔尺寸
压铸定位孔
七、文字、标志和图案
1、压铸件的文字、标志和图案,为了适应模具制造的特点,应做成凸纹。 2、文字字体高度不小于1.5mm,凸出高度0.15mm,线条最小宽度0.2mm,线条 最小间距大于0.3mm,出模角度为10°~15°。 3、标志和图案尽量做得简单、美观大方,尽量避免尖锐的利角。
六、螺丝孔
1、M1.4的螺丝的旋合长度在1.5mm~3.0mm之间比较合适,一般情况做 2.0mm。
2、底孔深度=螺纹深度+ 1.5倍螺距( 0.45mm ) 。 3、螺丝柱外径一般做3.5mm,最小可做2.8mm,底部料厚≥ 0.8mm。 4,具体的尺寸见下图。
过孔厚度 悬空距离
螺纹深度 底孔深度
5、避空位做斜面后再 倒圆角,既美观又有利 于压铸。
7、热熔柱孔做成全圆角,有利 于压铸填充,减少气孔和裂纹。
6、电池盖的头部倒≥0.5mm 的圆角,避免装配时刮伤产 品。
十一、装配
1、装配间隙检查 a、扣位的扣合量0.20~0.25,一般先做0.20,实际装配时再根据情况加胶。 b、电池盖和底壳无装配处的装配间隙做到0.2以上,以免会刮花塑胶件 c、产品应设积油避空位
此位厚度0.75mm,热熔孔边距 0.48mm,有强度要求,产品变形, 易断,无法生产。
此处料厚0.7mm,宽度 最小为0.566mm,产品 无问题。
五、骨位
1、骨位厚度≥1mm, 2、骨位无装配关系的面的出模角度≥3°拔模量不小于0.1mm,有装配位的骨 位面一般按拔模量0.05mm计算, 3、骨位的根部在不影响装配时倒不小于0.5mm以上的圆角。 4、产品上尽量不要有太多的骨位,一般骨位间距离≥10mm,最小不要小于 3mm。
2、分型面上小于0.3mm的R角,不利于设计浇注系统和排气系统,产品设计时 取消R,后加工抛光后会产生工艺R角。
此处R0.15MM,后加工抛光后会产生工
艺R角(R0.1—0.2) ,影响分型,开
模时取消R。
电池盖上的扣位对锌合金来 说作用不大,
四、料厚
1、产品的料厚应尽量均匀,均匀壁厚有利于金属液流动的平稳,曲面的截面 厚度过大变化易引起涡流现象而卷入气体产生气孔,并且料厚部位易产生缩孔、缩 松等缺陷。