(完整word版)设备设计与选型
引风机选型Microsoft Word 文档

一、Y4-73No28D引风机的产品简介本风机均为联轴器传动方式,分为D式和F式两种,20D及以下机号可订制整体支架,大大减少土建和安装工作量。
风机标配手动调风门,可采用手动调风门加电动执行器,或变频器实现风量和风压的调节。
1、 Y4-73No28D引风机的应用范围本风机主要适用于火力发电厂中2—670t/h蒸汽锅炉的引风系统。
也可用于各种除尘、脱硫‘脱硝、热能系统,输送的介质为烟气或热空气,一般不超过250℃。
超过250°需采用耐高温材料定制。
F传动方式的风机是为100~200MW火力发电机组配是在原生产的Y4-73-11№(20—29.5)D的基础上,重新设计的新型产品。
与原系列相比作了如下重大改进设计:1)将原风机悬臂支承(D式)的传动方式改为中间支承(F式)的传动方式,提高了风机动行中的稳定性;尤其对于引风机来说由于叶轮磨损和积灰以后影响转子的平衡,容易引起风机振动,这一改进尤为重要。
2)通过模型(叶轮外径D=1000mm)试验,增加了适应于该型风机的进气室,改原进风口的形状为偏心进风口。
过去风机生产厂不制造附带进气室,而各电厂自行配置的进气室多不能适应该风机的工作,容易引起进气涡流,使风机的机壳、进气室以及风道产生剧烈的振动,风机工作严重恶化,风量、压力、功率大幅度波动,使设备不能正常运行。
使用该系在引风机前,必须加装除尘装置,以尽可能减少进入风机中烟气的含尘量。
根据一般电厂的使用情况,所配除尘器效率不得低于85%。
3)在进气室的进口处装有5个翼形叶片调节风门,用以调节风机的特性,提高风机的调节效率,调节叶片的支撑处装有滚动轴承,转动灵活,使用可靠。
4)由于大部分送风机使用环境温度较高,轴承容易发热,因而新系列风机的轴承箱也和引风机一样采用水冷式。
5)新风机的轴承箱改进了轴封设计,并增加了放气塞,解决了漏油问题。
6)由于滚动轴承标准的改变,新风机调整了使用滚动轴承的型号,同时由于传动方式的改变、轴承受力情况更为合理,因而滚动轴承在使用中的问题大为减少。
设备工艺计算word版
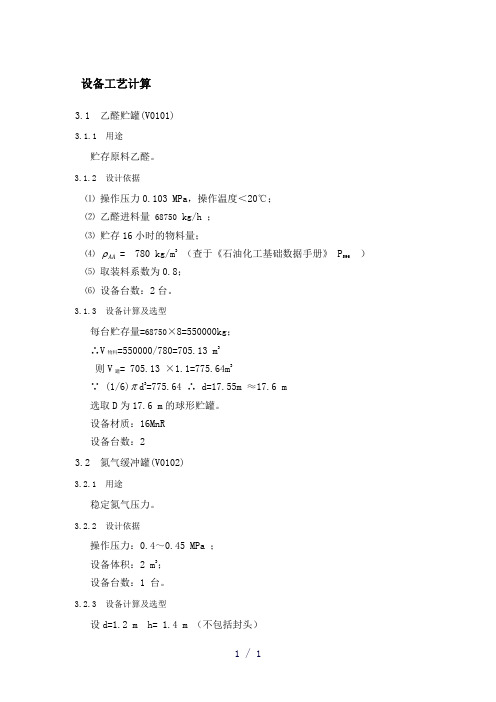
设备工艺计算3.1 乙醛贮罐(V0101)3.1.1 用途贮存原料乙醛。
3.1.2 设计依据⑴操作压力0.103 MPa,操作温度<20℃;⑵乙醛进料量68750 kg/h ;⑶贮存16小时的物料量;ρ= 780 kg/m3(查于《石油化工基础数据手册》 P596)⑷AA⑸取装料系数为0.8;⑹设备台数:2台。
3.1.3 设备计算及选型每台贮存量=68750×8=550000kg;=550000/780=705.13 m3∴V物料则V= 705.13 ×1.1=775.64m3罐∵ (1/6)πd3=775.64 ∴ d=17.55m ≈17.6 m选取D为17.6 m的球形贮罐。
设备材质:16MnR设备台数:23.2 氮气缓冲罐(V0102)3.2.1 用途稳定氮气压力。
3.2.2 设计依据操作压力:0.4~0.45 MPa ;设备体积:2 m3;设备台数:1 台。
3.2.3 设备计算及选型设d=1.2 m h= 1.4 m (不包括封头)设备材质:A 3F 设备台数:13.3 氧气缓冲罐(V0103)设备计算3.3.1 用途稳定氧气压力3.3.2 计算依据操作压力:0.4~0.45 MPa; 设备体积:4 m 3;设备台数:1 台。
3.3.3 设备计算及选型可设d=1.4 m h= 2.2 m (不包括封头) (查于《化工工艺设计手册》第三版(下) P 5-224 )3.4 触媒循环泵(P0101)设备计算3.4.1 用途把循环催化剂输送到氧化塔低部。
3.4.2 设计依据⑴ 循环催化剂体积流量F= 0.27 m 3/h ; ⑵ 操作温度40℃;⑶ 平均密度查《石油化工基础数据手册》 P 596~690,得到各物质的密度见表31 。
表31 40℃各物质的密度及组成组分 Mn(Ac)2 水 甲酸 醋酸 丁烯酸 三聚乙醛 亚乙基二醋酸酯密度, ㎏/m 3838 992.2 1192 1026 1005 1179 1098 质 量 , %1.191.020.2797.000.150.200.17ρ=∑i i x ρ= 838×1.19% + 992.2×1.02% + 1192×0.27% + 1026×97% +1005×0.15% + 1179×0.20% + 1098×0.17% = 1024.26 kg/m 3⑷ 出口段有90℃弯头6个,标准阀6个,回弯头16个,进口管长20 m , 换热器长20m ;入口段有标准阀6个,止逆阀1个,90℃弯头9个; Z a =7.5m Z b =1.5m △Z=6m ,u a =u b3.4.3 压头计算H=(Z a -Z b )+g P P b a ρ-+gu u ba 222-+h f ①(1)体积流量为 7940.22÷1024.26=7.75m 3/h且已知:P b =0.132 MPa P a =0.405 MPa △P=0.273 MPa(2)进口段流速V=u A=4πu d 2u =24d Vπ=36005.004.137.7542⨯⨯⨯ =1.10m/s Re=μρdu =0.05×1.10×1024.26÷(0.895×10-3) =62943.35 >4000 ∴是湍流无缝钢管绝对粗糙度为0.05 mm ②则相对粗糙度0.05/50=0.001 ∴λ=0.002 (柏拉修斯公式) ③ (3)出口段阻力计算:设进口管长20 m E0103换热器长20 m标准阀6个 le/d=300 90℃弯头6个 le/d=35 回弯头16个 le/d=75压头损失:h f1= ④= =0.001mH 2O(4)入口段压头损失: 设进口管长10 m标准阀6个 le/d=300(全) 止逆阀1个 le/d=100 90℃弯头9个 le/d=35h f2=h f2=1.8925.005.005.71101002.002⨯⨯+⨯)(=0.0006mH 2O1.8925.005.00.51604002.002⨯⨯+⨯)(g u d l l e 2)(2∑+λg u d l l e 2)(2∑+λ(5)进出口压力差△P=0.273 MPa△P/(ρg)=0.273×106/(1024.26×9.8)=27.20 mH2O (6)总压头计算:H= hf1+ hf2+△Z+△P/(ρg)=0.001+0.0006+27.20+6=33.2016 mH2O3.4.4 选型泵的选型见表32。
设备选型与布局设计

设备选型与布局设计设备选型与布局设计是一个重要的环节,对于各类工业和生产型企业来说,它决定了整个生产线的效率和生产能力。
在设备选型与布局设计中,需要考虑多个因素,如生产要求、工作流程、设备功能和性能等。
首先,设备选型需要根据生产需求和产品特性来确定。
生产需求涉及到产量、质量和生产周期等方面,而产品特性包括尺寸、重量、形状等。
通过分析生产需求和产品特性,可以确定所需设备的种类和性能。
其次,设备选型需要考虑工作流程。
不同工作流程对设备功能和性能的要求不同。
例如,在连续生产过程中,需要选用高效、稳定的设备,而在离散型生产中,需要选用适应多种产品加工的设备。
再次,设备选型还要考虑设备功能和性能。
功能包括设备的加工能力、自动化程度和安全性能等,性能包括设备的精度、稳定性和可靠性等。
通过评估设备的功能和性能,可以确定适合的设备供应商和型号。
最后,设备布局设计是设备选型的重要环节。
设备布局应根据生产工艺流程和工作空间来设计。
合理的设备布局可以最大限度地提高生产效率和工作效率,减少物料和人员的移动距离。
在设备布局设计中,需要考虑以下几个要点:1. 生产工艺流程:根据生产工艺流程进行设备的布置,确保生产过程的顺畅和连贯。
避免设备之间的冲突和瓶颈,提高整体生产效率。
2. 人员流动:考虑生产线上的人员流动,使操作人员可以方便地操作设备,并保证工作效率和人员安全。
3. 物料流动:考虑物料的输入和输出流程,确保物料的供应和运输畅通无阻。
合理规划物料存放区域,减少物料运输的时间和成本。
4. 安全考虑:在设备布局设计中,要考虑安全因素,合理设置紧急停机按钮、防护设施和紧急通道,保障操作人员的安全。
5. 设备维护和保养:考虑设备的维护和保养需求,确保设备能够正常运行。
预留足够的工作空间和维护通道,方便维修人员进行设备维护和保养。
综上所述,设备选型与布局设计是一个综合性的任务,需要综合考虑生产需求、工作流程、设备功能和性能等因素。
(完整word版)反应釜设计
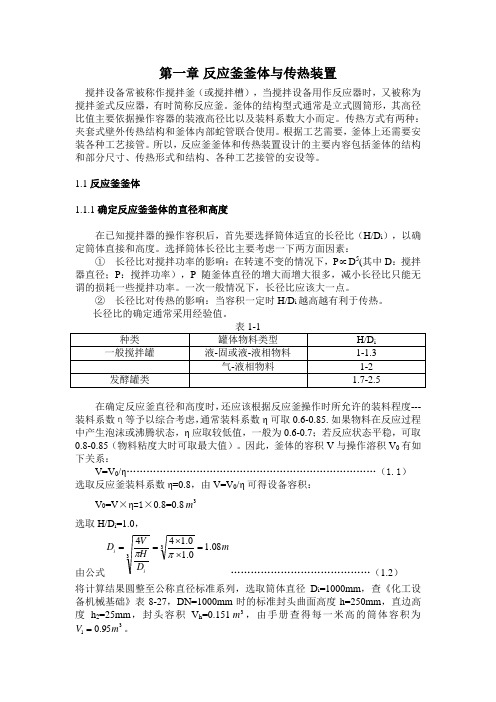
第一章 反应釜釜体与传热装置搅拌设备常被称作搅拌釜(或搅拌槽),当搅拌设备用作反应器时,又被称为搅拌釜式反应器,有时简称反应釜。
釜体的结构型式通常是立式圆筒形,其高径比值主要依据操作容器的装液高径比以及装料系数大小而定。
传热方式有两种:夹套式壁外传热结构和釜体内部蛇管联合使用。
根据工艺需要,釜体上还需要安装各种工艺接管。
所以,反应釜釜体和传热装置设计的主要内容包括釜体的结构和部分尺寸、传热形式和结构、各种工艺接管的安设等。
1.1反应釜釜体1.1.1确定反应釜釜体的直径和高度在已知搅拌器的操作容积后,首先要选择筒体适宜的长径比(H/D i ),以确定筒体直接和高度。
选择筒体长径比主要考虑一下两方面因素:① 长径比对搅拌功率的影响:在转速不变的情况下,P ∝D 5(其中D :搅拌器直径;P :搅拌功率),P 随釜体直径的增大而增大很多,减小长径比只能无谓的损耗一些搅拌功率。
一次一般情况下,长径比应该大一点。
② 长径比对传热的影响:当容积一定时H/D i 越高越有利于传热。
长径比的确定通常采用经验值。
在确定反应釜直径和高度时,还应该根据反应釜操作时所允许的装料程度---装料系数η等予以综合考虑,通常装料系数η可取0.6-0.85.如果物料在反应过程中产生泡沫或沸腾状态,η应取较低值,一般为0.6-0.7;若反应状态平稳,可取0.8-0.85(物料粘度大时可取最大值)。
因此,釜体的容积V 与操作溶积V 0有如下关系:V=V 0/η…………………………………………………………………(1.1) 选取反应釜装料系数η=0.8,由V=V 0/η可得设备容积:V 0=V ×η=1×0.8=0.83m 选取H/D i =1.0,由公式m D H V D ii 08.10.10.14433=⨯⨯==ππ……………………………………(1.2)将计算结果圆整至公称直径标准系列,选取筒体直径D i =1000mm ,查《化工设备机械基础》表8-27,DN=1000mm 时的标准封头曲面高度h=250mm ,直边高度h 2=25mm ,封头容积V h =0.1513m ,由手册查得每一米高的筒体容积为3195.0m V =。
(完整word版)雨水泵站设计说明书

目录设计说明书 3一、主要流程及构筑物 31。
1 泵站工艺流程 31。
2 进水交汇井及进水闸门 31.3 格栅 31。
4 集水池 41.5 雨水泵的选择 61。
6 压力出水池: 61。
7 出水闸门 61。
8 雨水管渠 61.9 溢流道 7二、泵房 72.1 泵站规模 72.2 泵房形式 72。
3 泵房尺寸 9设计计算书 11一、泵的选型 111.1 泵的流量计算 111.2 选泵前扬程的估算 111.3 选泵 111.4 水泵扬程的核算 12二、格栅间 142.1 格栅的计算 142.2 格栅的选型 15三、集水池的设计 163.1 进入集水池的进水管: 163。
2 集水池的有效容积容积计算 16 3.3 吸水管、出水管的设计 163.4 集水池的布置 17四、出水池的设计 174.1出水池的尺寸设计 174。
2 总出水管 17五、泵房的形式及布置 175。
1泵站规模: 175.2泵房形式 185.3尺寸设计 185.4 高程的计算 19设计总结 20参考文献 21设计说明书一、主要流程及构筑物1。
1 泵站工艺流程目前我国工厂及城市雨水泵站流程一般都采用以下方式:进入雨水干管的雨水,通过进水渠首先进入闸门井,然后进入格栅间,将杂物拦截后,经过扩散,进入泵房集水池,经过泵抽升后,通过压力出水池并联,由两条出水管排入河中。
出水管上设旁通管与泵房放空井相连,供试车循环用水使用。
1.2 进水交汇井及进水闸门1。
2。
1 进水交汇井:汇合不同方向来水,尽量保持正向进入集水池。
1。
2。
2 进水闸门:截断进水,为机组的安装检修、集水池的清池挖泥提供方便.当发生事故和停电时,也可以保证泵站不受淹泡.一般采用提板式铸铁闸门,配用手动或手电两用启闭机械.1.3 格栅1。
3.1 格栅:格栅拦截雨水、生活污水和工业废水中较大的漂浮物及杂质,起到净化水质、保护水泵的作用,也有利于后续处理和排放.格栅由一组(或多组)平行的栅条组成,闲置在进站雨、污水流经的渠道或集水池的进口处。
第章 总体方案设计与设备选型一

第一章总体方案设计与设备选型1.1 总体方案设计在进行具体的设备选型之前,需要对整个项目进行总体的方案设计。
首先需要确定项目的需求和目标,然后确定具体的技术方案和工程实施计划。
1.1.1 项目需求和目标根据项目需求和目标,可以确定出以下几个方面的要求:•系统的安全性:安全性可以通过数据加密、访问控制和备份恢复来实现,以防止可能的数据泄露或数据丢失。
•系统的可靠性:可靠性可以通过硬件冗余、负载均衡、备份和恢复机制来实现。
•系统的扩展性:由于系统是在未来可能会扩展的相应场景下进行设计的,因此,在实现系统的时候,需要考虑未来的扩展性。
•系统的易用性:系统需要让用户能够容易地使用,并且用户可以自已操作。
1.1.2 技术方案在项目需求和目标定义之后,需要选择适合的技术方案。
在选择技术方案的时候,需要考虑以下几个方面:•数据库选择:系统需要使用哪种类型的数据库,具体的技术方案会考虑扩展性、容错性、数据存储量和性能等方面。
•网络架构的选择:系统需要怎样进行集中管理和实现高可用性,具体的技术方案会考虑在不同场景下制定不同的网络拓扑结构,以及实现相关的负载均衡。
•软件架构的选择:为系统的不同模块选择合适的技术方案,以及在系统扩展的场景下选择合适的架构,以实现高效的可扩展性。
1.1.3 工程实施计划当技术方案确定之后,需要制定具体的工程实施计划,并考虑到时间、人力、资源等因素。
具体的工程实施计划可以以下几个方面为要点:•项目的章节划分和安排。
•不同模块的开发时间。
•人力的分布和配置。
•测试、验收和Deployment。
1.2 设备选型在确定了系统的总体方案设计之后,需要根据方案设计细节来进行设备的选型。
设备选型也需要考虑的方面有很多,下面着重介绍几个重要的方面:1.2.1 容量与负载设备选型需要考虑系统的容量和负载。
容量是指系统能够存储的数据量和处理能力。
负载是指设备运行时所产生的压力。
1.2.2 健壮性设备在运作中可能会遭受到一些意想不到、偶然的故障,因此设计的设备需要能够快速地进行智能反应并提供快速的解决方案。
引风机选型Microsoft Word 文档

一、Y4-73No28D引风机的产品简介本风机均为联轴器传动方式,分为D式和F式两种,20D及以下机号可订制整体支架,大大减少土建和安装工作量。
风机标配手动调风门,可采用手动调风门加电动执行器,或变频器实现风量和风压的调节。
1、 Y4-73No28D引风机的应用范围本风机主要适用于火力发电厂中2—670t/h蒸汽锅炉的引风系统。
也可用于各种除尘、脱硫‘脱硝、热能系统,输送的介质为烟气或热空气,一般不超过250℃。
超过250°需采用耐高温材料定制。
F传动方式的风机是为100~200MW火力发电机组配是在原生产的Y4-73-11№(20—29.5)D的基础上,重新设计的新型产品。
与原系列相比作了如下重大改进设计:1)将原风机悬臂支承(D式)的传动方式改为中间支承(F式)的传动方式,提高了风机动行中的稳定性;尤其对于引风机来说由于叶轮磨损和积灰以后影响转子的平衡,容易引起风机振动,这一改进尤为重要。
2)通过模型(叶轮外径D=1000mm)试验,增加了适应于该型风机的进气室,改原进风口的形状为偏心进风口。
过去风机生产厂不制造附带进气室,而各电厂自行配置的进气室多不能适应该风机的工作,容易引起进气涡流,使风机的机壳、进气室以及风道产生剧烈的振动,风机工作严重恶化,风量、压力、功率大幅度波动,使设备不能正常运行。
使用该系在引风机前,必须加装除尘装置,以尽可能减少进入风机中烟气的含尘量。
根据一般电厂的使用情况,所配除尘器效率不得低于85%。
3)在进气室的进口处装有5个翼形叶片调节风门,用以调节风机的特性,提高风机的调节效率,调节叶片的支撑处装有滚动轴承,转动灵活,使用可靠。
4)由于大部分送风机使用环境温度较高,轴承容易发热,因而新系列风机的轴承箱也和引风机一样采用水冷式。
5)新风机的轴承箱改进了轴封设计,并增加了放气塞,解决了漏油问题。
6)由于滚动轴承标准的改变,新风机调整了使用滚动轴承的型号,同时由于传动方式的改变、轴承受力情况更为合理,因而滚动轴承在使用中的问题大为减少。
活性炭吸附净化设备设计方案( word 版)

活性炭吸附净化设备设计方案1. 引言活性炭是一种广泛应用于工业和环境领域的吸附材料,具有良好的吸附性能和高度的表面活性。
活性炭吸附净化设备适用于处理废气、废水和有机物污染物的去除。
本文将介绍活性炭吸附净化设备的设计方案。
2. 设计目标活性炭吸附净化设备的设计目标包括但不限于以下几个方面: - 提供高效的吸附性能,达到净化要求; - 实现设备的稳定运行和长寿命; - 目标污染物的去除率达到要求; - 设备操作和维护简便。
3. 设计原理活性炭吸附净化设备的设计原理是利用活性炭材料对污染物进行吸附,从而达到净化的目的。
活性炭具有高度发达的孔结构和巨大的比表面积,能够有效吸附各种有机物和气体。
通过在设备中设置适当的流动路径和吸附床层,使气体或液体中的污染物与活性炭接触并吸附到活性炭表面,从而实现净化效果。
4. 设计步骤(1)确定处理介质:根据实际情况,确定要处理的废气或废水污染物的组成和浓度,以及处理量。
(2)选型活性炭:根据处理介质的特性和目标污染物的吸附性能要求,选择适合的活性炭材料。
考虑活性炭的孔径分布、比表面积、强度等指标。
(3)确定处理设备结构:设计活性炭吸附净化设备的结构,包括吸附床、进出气口、流动路径等。
要考虑介质的流动性、污染物的浓度以及设备操作和维护的便利性。
(4)计算吸附床层高度:根据目标污染物的浓度和去除率要求,计算吸附床层的高度。
考虑吸附床层中活性炭的用量和密度,以及污染物的吸附速度。
(5)确定进出口管道:根据设备的处理能力和处理介质的流量,确定进出口管道的直径和设计。
考虑流体的流速和压降。
(6)设备组装和测试:将各个部件组装到一起,并进行测试和调试。
确保设备能够正常运行和达到设计要求。
5. 设计优化活性炭吸附净化设备的设计可以通过以下方式进行优化: - 选择更高效的活性炭材料,提高吸附性能; - 优化吸附床层的高度和体积,使设备更稳定; - 设计合理的流动路径,提高介质的接触效果; - 增加附加设备,如预处理设备、再生装置等,提高设备的综合性能。
- 1、下载文档前请自行甄别文档内容的完整性,平台不提供额外的编辑、内容补充、找答案等附加服务。
- 2、"仅部分预览"的文档,不可在线预览部分如存在完整性等问题,可反馈申请退款(可完整预览的文档不适用该条件!)。
- 3、如文档侵犯您的权益,请联系客服反馈,我们会尽快为您处理(人工客服工作时间:9:00-18:30)。
设备设计与选型7.1全厂设备概况及主要特点全厂主要设备包括反应器6台,塔设备3台,储罐设备8台,泵设备36台,热交换器19台,压缩机2台,闪蒸器2台,倾析器1台,结晶器2台,离心机1台,共计80个设备。
本厂重型机器多,如反应器、脱甲苯塔、脱重烃塔,设备安装时多采用现场组焊的方式。
在此,对反应器、脱甲苯塔等进行详细的计算,编制了计算说明书。
对全厂其它所有设备进行了选型,编制了各类设备一览表(见附录)。
7.2反应器设计7.2.1概述反应是化工生产流程中的中心环节,反应器的设计在化工设计中占有重要的地位。
7.2.2反应器选型反应器的形式是由反应过程的基本特征决定的,本反应的的原料以气象进入反应器,在高温低压下进行反应,故属于气固相反应过程。
气固相反应过程使用的反应器,根据催化剂床层的形式分为固定床反应器、流化床反应器和移动床反应器。
1、固定床反应器固定床反应器又称填充床反应器,催化剂颗粒填装在反应器中,呈静止状态,是化工生产中最重要的气固反应器之一。
固定床反应器的优点有:①反混小②催化剂机械损耗小③便于控制固定床反应器的缺点如下:①传热差,容易飞温②催化剂更换困难2、流化床反应器流化床反应器,又称沸腾床反应器。
反应器中气相原料以一定的速度通过催化剂颗粒层,使颗粒处于悬浮状态,并进行气固相反应。
流态化技术在工业上最早应用于化学反应过程。
流化床反应的优点有:①传热效果好②可实现固体物料的连续进出③压降低流化床反应器的缺点入下:①返混严重②对催化剂颗粒要求严格③易造成催化剂损失3、移动床反应器移动床反应器是一种新型的固定床反应器,其中催化剂从反应器顶部连续加入,并在反应过程中缓慢下降,最后从反应器底部卸出。
反应原料气则从反应器底部进入,反应产物由反应器顶部输出,在移动床反应器中,催化剂颗粒之间没有相对移动,但是整体缓慢下降,是一种移动着的固定床,固得名。
本项目反应属于低放热反应,而且催化剂在小试的时候曾连续运行1000小时不发生失活,所以为了最大限度的发挥催化剂高选择性和高转化率的优势,减少催化剂损失,流程的反应器采用技术最成熟的固定床反应器。
7.2.3反应器体积计算本项目使用的是固定床列管式反应器,流体在床层内流动可视为平推流。
所以由于数据的匮乏,用平推流反应器来计算固定床反应器。
运用Aspen Plus进行反应器的设计如下:有文献查的甲苯甲醇烷基化的主反应表观活化能位67.79KJ/Kmol。
aspen plus中输入的动力学参数如图7-1所示:图7-1 aspen plus中输入的动力学参数aspen plus中输入的逆反应的动力学参数如图7-2所示:图7-2 aspen plus 中输入的逆反应的动力学参数Aspen plus 输出的结果如图7-3所示:图7-3 Aspen plus 输出的结果换成反应器的体积为:0.3152 ×π/4×10×20=15.59m 3催化剂一般装填整个反应器的50%~60%,此处我们选取50%装填量:317.315.059.15m V ==圆整体积,则反应器定型体积为:V=31.5m37.2.4反应器的直径和高度根据《工业催化》中规定,为了保证反应气流稳定,固定床反应器的长径比一般在6~12之间。
此处我们选取反应器长度:反应器直径=7,则:H=7D=14R=14R3R=0.90此处选取反应器直径D=1.80m,固定床反应器长度H=12.6m7.2.5反应器筒体壁厚的设计1、设计参数的确定(1)设计压力的相关确定设计压力p:P=(1.05~1.10)P1此处我们取:P=1.1P1=1.1×0.3MPa=0.33MPa(2)设计温度的相关确定该反应器操作温度为460℃,取设计温度500℃,则选用材质为0Cr18Ni10Ti 的高合金钢钢板。
取焊接接头系数=1.0φ(双面焊对接接头,100%无损探伤),则查化工设备设计手册可知材料在0Cr18Ni10Ti 500℃时的许用应力[σ]t =103MPa ;腐蚀裕量21mm C =。
2、筒体的壁厚计算厚度 []mm p D p c t ic 443.133.011034180033.02=-⨯⨯⨯=-=φσδ 设计厚度 δd =δ+C 2=1.443mm+1=2.443mm已知钢板腐蚀裕量C 2=1.7mm ;负偏差10.8C mm =,则:名义厚度 δn =δd +C 1=4.0mm (圆整)3、筒体封头设计反应釜的封头选用标准椭圆型封头(JB1154-73),内径与筒体相同,封头采用0Cr18Ni10Ti 的高合金钢钢板材料制造。
相关结构参数如下:公称直径DN=1800mm曲面高度H 1=525mm 直边高度H 2=30mm 内表面积F=4.65m 3容积V=1.1m 34、封头壁厚的设计对于标准椭圆形封头,其计算厚度按下式计算:[]20.5it pD t mm p σφ=-经计算得t=2.88mm7.3换热器设备设计7.3.1概述在不同温度的流体间传递热能的装置称为热交换器,简称换热器。
在换热器中至少要有两种温度不同的流体,一种流体温度高,放热;另一种流体温度低,吸热。
在工程实践中有时也会有两种以上流体参加换热的换热器,但其基本原理与前一致。
化工、石油、动力、食品等行业中广泛使用各种换热器,它们是上述这些行业的通用设备,占有十分重要的地位。
随着工业的迅速发展,能源消耗量不断增加,能源紧张已成为一个世界性问题。
为缓和能源紧张的状况,世界各国竞相采取节能措施,大力发展节能技术,已成为当前工业生产和人民生活中一个重要课题。
换热器在节能技术改造中具有很重要的作用,表现在两方面:一是在生产工艺流程中使用着大量的换热器,提高这些换热器效率,显然可以减少能源的消耗;另一方面,用换热器来回收工业余热,可以显著地提高设备的热效率。
7.3.2选型依据表7-1换热器的设计依据换热器包括过程流股的加热器,塔的再沸器和冷凝器。
根据工艺衡算和工艺物料的要求,掌握物料流量、温度、压力、化学性质、物性参数等特性,结合Aspen Energy Analyzer得出的有关设备负荷、传热面积、流程中的位置等来明确设计任务,选择换热器型式。
在设计过程中,需满足如下几个方面的要求:(1)合理地实现所规定的工艺条件。
(2)结构安全可靠。
(3)便于制造、安装、操作和维修。
(4)经济上合理。
7.3.3热量供应根据工艺条件,热蒸汽使用201℃(0.8MPa),450℃(4MPa)和545℃(12MPa)的饱和蒸汽,作为热公用工程。
同时,选择温度为25℃的冷却水作为冷公用工程。
一般情况下冷却水出口温度不高于35℃,避免结垢严重,高温端的温差不应小于20℃,低温端的温差不应小于5℃。
当在两工艺物流之间进行换热时,低温端的温差不应小于20℃。
当采用多管程、单壳程的管壳式换热器,并且用水作为冷却剂时,冷却水的出口温度不应高于工艺物流的出口温度。
7.3.4物流流程的选择对于高温物流一般走管程,从而节省保温层和减少壳体厚度,但是有时为了物料的散热,增强冷却效果,也可以使高温流体走壳程;对于压力较高的物流应该走管程;粘度较大的流体应该走壳程,在壳程可以得到较高的传热系数;对于压力降有特定要求的工艺物流应走管程,因管程的传热系数和压降计算误差较小;流量较小的物流应走壳程,易使物流形成湍流状态,从而增加传热系数;对于具有腐蚀性的物流走管程,否则对壳程和管程都会造成腐蚀;对于有毒流体宜走管程,使泄漏机会减少。
7.3.5换热管1、换热管规格在选择管道规格时,通常选用Φ19mm的管子;对于易结垢的物料,为方便清洗,采用外径Φ25mm或Φ38mm的管子;对于有气液两相流的工艺物流或者物流流量较大工艺物流,一般选用较大的管径。
2、管长在满足设计要求的前提下,尽量选用较短的管子,以降低压降。
3、管程数随着管程数增加,管内流速和传热系数均相应的增加,因此一般选在1~2或者4管程,不宜选用太高的管程数,以免压力降过大。
4、换热管中心距管心距为管径的1.25~1.5倍。
5、排列方式正三角形排列更为紧凑,管外流体的湍动程度高,给热系数大,而正方形排列的管束清洗方便,对易结垢流体更为适用,如将管束旋转45℃放置,也可提高给热系数。
6、折流板折流板可以改变壳程流体的方向,使其垂直于管束流动,获得较好的传热效果。
7、裕量对于工艺物流间的换热,留有40% −50%的裕量;对于工艺物流与公用工程间的换热,留有15% −25%的裕量。
直接使用Aspen Exchange Design & Rating进行辅助设计:对E0101选型结果如图7-4所示:图7-4 EDR软件选型结果7.4塔设备设计7.4.1设计依据表7-2塔设备设计依据7.4.2概述石化行业是国民经济中能耗较高的产业部门,其能耗占工业能耗接近1/5,占全国总能耗的14%左右。
而在化工生产中分离的能耗占主要部分,塔设备的投资费用占整个工艺设备费用的25.93%。
塔设备所耗用的钢材料重量在各类工艺设备中所占的比例也较多。
7.4.3塔型的选择塔主要有板式塔和填料塔两种,它们都可以用作蒸馏和吸收等气液传质过程,但两者各有优缺点,要根据具体情况选择。
(1)填料塔与板式塔的比较:a.板式塔。
塔内装有一定数量的塔盘,是气液接触和传质的基本构件;属逐级(板)接触的气液传质设备;气体自塔底向上以鼓泡或喷射的形式穿过塔板上的液层,使气液相密切接触而进行传质与传热;两相的组分浓度呈阶梯式变化。
b.填料塔。
塔内装有一定高度的填料,是气液接触和传质的基本构件;属微分接触型气液传质设备;液体在填料表面呈膜状自上而下流动;气体呈连续相自下而上与液体作逆流流动,并进行气液两相的传质和传热;两相的组分浓度或温度沿塔高连续变化。
综合考虑,本项目采用板式塔。
对T0101精馏塔用cup-tower进行筛板设计,塔板工艺参数图如图7-5所示图7-5 塔T0101塔板工艺参数图7-6 T0101塔板结构参数表7-3 T0101工艺计算结果工艺计算结果筛板设计单位正常操作90%操作110%操作1 空塔气速m/s 0.445 0.4378 0.44962 孔气速m/s 19.2875 19.126 19.43623 溢流强度m3/(h.m) 34.0717 30.5318 35.91734 板上液层高度m 0.0709 0.0713 0.0715 干板压降m液柱0.1177 0.1158 0.11966 雾沫夹带量Kg(L)/kg(V) 0.0004 0.0004 0.00047 降液管内液体高m 0.2542 0.2475 0.25928 降液管内线速度m/s 0.0733 0.0619 0.07419 流量参数0.0356 0.0356 0.0356 1液面梯度m 0.0001 0.0001 0.0001 1空板动能因子m/s(kg/m3)^0.5 0.8199 0.8065 0.8283 1孔动能因子m/s(kg/m3)^0.5 35.533 35.2355 35.807 1漏点气速m/s 6.2364 6.249 6.2387 1堰上液层高度m 0.0298 0.0277 0.0309 1总板压降m液柱0.1659 0.1641 0.16781降液管停留时间s 8.1856 9.6878 8.1026 1降液管液泛% 79.3203 76.9335 81.0074 1降液管底隙速度m/s 0.337 0.2818 0.3657 1稳定系数 3.0927 3.0607 3.1154负荷性能图参数1 操作点横坐标m3/h 62.3612 操作点纵坐标m3/h 26.4853 操作上限百分90.00%4 操作下限百分110.00%X液相体积流量m3/hY气相体积流量10^3*m3/h0-操作线1-液相下限线2-液相上限线3-漏液线4-雾沫夹带线5-液泛线表7-4 T0101塔板结构参数塔板结构参数塔盘信息1 塔径(m) 4.6 6 普通筛孔数(#)305152 板间距(m)0.6 7 普通筛孔密度2004.883 塔截面积(m2)16.619 8 进料位置(板数)114 开孔区面积15.2201 9 人孔位置(板数)3,11,195 开孔率(%) 2.31溢流区尺寸(两侧)1 降液管顶部宽0.192 8 降液管顶部面积0.23762 弯折距离(m)0.0703 9 降液管底部面积0.12053 降液管底部宽0.1217 1顶部堰长(m) 1.844 受液盘深度0.035 1底部堰长(m) 1.47655 受液盘宽度0.192 1进口堰高度(m)07.5储罐设备设计7.5.1设计依据表7-5储罐设备设计依据7.5.2储罐类型贮罐根据形状来划分,有方形贮罐、圆筒形罐、球形罐和特殊形贮罐(如椭圆形、半椭圆形)每种型式又按封头形式不同,分为若干种型式。