安钢炼铁厂高炉工艺简介
高炉炼铁工艺流程(简介) PPT

C CC R GP
BB B PG R
CCC RGP
BB B PG R
C
A
B
H
C
A
B
H
C
A
B
H
C
A
B
H
燃
B
B
B
F
B
B
B
B
B
B
B
B
B
烧
a
室
n
蓄
1
热
混
F
室
风
a n
室
热
2
B
M
B
M
B
M
B
M
风
总
热管
风
S t
4H S
H
3H S
H
2H S
H
1H S
H
阀
a c
BF 空 CO G 气 G 冷风阀
k
W
.
SW
S
SW
S
SW
S
混合器
N2
加压、流化气
高炉概况和工艺流程
项目
DC 1VS 2VS
处理煤气量 (m3/h) 700000 700000 700000
进口粉尘浓度 (g/m3) 13.5
5
0.1
出口粉尘浓度 (mg/m3) 5000
100
<10
TRT是 炉煤气余压透平发电
高炉节能回收重要措施,工
是通过高炉的高压并带有预
THANK YOU
柱,能储存一定量的渣、铁。 ⑵适应炉料下降和煤气上升的规律,减少炉料下降和煤气上升的阻
力,为顺行创造条件,有效的利用煤气的热能化学能,降低燃耗。 ⑶易于生成保护性的渣皮,有利于延长炉衬的寿命。
高炉炼铁工艺介绍
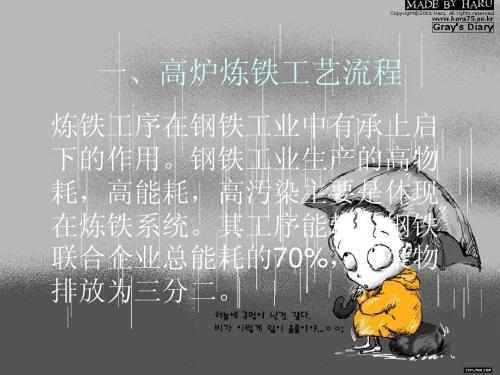
炼铁工序在钢铁工业中有承上启 下的作用。钢铁工业生产的高物 耗,高能耗,高汚染主要是体现 在炼铁系统。其工序能耗占钢铁 联合企业总能耗的70%,汚染物 排放为三分二。
1、原燃料通过主皮带上至高炉炉顶 装料设备,通过大钟或布料溜槽均 匀分布到炉喉
• 炉顶装料设备分为钟 式炉顶和无料钟炉顶
4、风口回旋区
• 焦炭在风口前,由于鼓风动能的作用在剧 烈的回旋运动中燃烧,形成一个半空状态 的焦炭回旋区
5、渣铁贮存区
• 炉缸下部,主要是液态渣铁以及浸入其中 的焦炭,铁滴穿过渣层以及渣铁界面后最 终完成必要的渣铁反应,得到合格的生铁
四、影响铁矿石还原的因素
• (1)矿石的气孔度和矿物组成。气孔度大而分布均匀的矿石还原性 好(气孔度大,矿石与煤气的接触面积大,特别是微气孔率,可以改 善气体的内扩散条件,提高内扩散速度。 • (2)矿石的粒度。相同质量的矿石,粒度越小与煤气的接触面积则 越大,煤气的用程度越好。 • (3)煤气温度。随着温度升高不论是界面化学反应还是扩散速度均 是加快的,同时在高温下活化分子数目增加,促进还原反应进行。 • (4)煤气压力。提高煤气压力使气体密度加大,增加了单位时间内 与矿石表面碰撞的还原剂的分子数,从而加快还原反应。 • (5)煤气中CO 和H2的浓度。从化学反应动力学看,提高煤气中CO 和H2浓度,既可提高还原过程中的内、外扩散速度,又可提高化学反 应速度,从而可以加快铁矿石的还原速度。 • (6)煤气流速。
5、炉缸
• 高炉燃料燃烧、渣铁反应和贮存及排放区 域,呈圆筒形。出铁口、渣口和风口都设 在炉缸部位,因此它也是承受高温煤气及 渣铁物理和化学侵蚀最剧烈的部位,对高 炉煤气的初始分布、热制度、生铁质量和 品种都有极重要的影响
高炉炼铁工艺简介2

14
hu
本
Top ring:炉顶钢圈(炉顶法兰)
h6
体
Offtake :排气管
结
Top cone:高炉炉头(炉顶锥
构 中
形部分) Armour(炉喉)钢砖 Stockline level:料线零位
英
Throat:炉喉,Stack:炉身
文
Belly:炉腰
对
Bosh:炉腹
照
Tuyere:鼓风口
Tuyere breast:风口中心
物形式为磁铁矿、赤铁矿、褐铁矿、菱铁矿。
主要含铁矿物(Chief Iron Bearing Minerals)
2019/8/5
24
磁铁矿(主要成分Fe3O4)
赤铁矿(主要成分Fe2O3)
假象“赤铁矿”:磁铁矿在自然界中被氧化, 化学成分上已由Fe3O4成为Fe2O3,在结晶 结构上保持磁铁矿的特征。通常以矿石中全 铁含量与FeO含量的比值判别磁铁矿受氧化 的程度。
鼓风机 热风炉
球团矿 烧结矿
焦炭
煤粉 熔剂 热风
高
炼铁工艺流程图
炉
水泥厂 铸铁机
2019/8/5
炉渣 铁水 高炉煤气 铸造生铁 炼钢生铁
放散 轧钢厂 转炉炼钢厂
6
由于高炉的效率高、能耗低,所以高炉生产的铁占 世界铁总产量的95%以上。
我国最大的高炉是宝钢3号高炉(4350m3)。世界
最大高炉达5000m3以上。
13
hu h
h6
3)、几个概念: (a)料线零位:是测
定料面高度的基础。
钟式炉顶:大钟开
启时大钟的底边;
无钟炉顶:炉喉钢
砖的转折点处或钢
砖顶部
高炉 - 转炉工艺 -回复

高炉- 转炉工艺-回复高炉和转炉是冶金工业中常见的两种主要炼铁工艺。
本文将逐步介绍高炉和转炉工艺的基本原理、流程和应用。
高炉是一种用于冶炼铁矿石生产生铁的设备。
其基本原理是利用冶金反应原则中的高温还原反应,将铁矿石中的铁氧化物还原为金属铁。
高炉内温度高达1500C以上,内部有两个截然不同的区域,即上部的还原区和下部的熔化区。
高炉的工艺流程可分为八个主要步骤,即装料、预热、炼铁、出铁、喷吹、煅烧、热风烧结和废气净化。
第一步是装料,通常使用优质的铁矿石、石灰石和焦炭作为原料。
这些原料经过预处理后,按一定的比例混合并送入高炉顶部。
第二步是预热,原料在高炉顶部受到恒定流量的热风预热,提高其温度,为后续的还原反应做准备。
第三步是炼铁,预热后的原料从高炉顶部逐渐下降,进入还原区。
在还原区内,焦炭通过供氧装置喷吹进入高炉底部,产生高温热风,促使铁矿石中的铁氧化物还原为金属铁。
第四步是出铁,炼铁过程产生的铁液通过高炉底部的出渣口排出,形成生铁产品。
第五步是喷吹,炼铁过程中,通过喷吹装置向高炉中喷入煤粉或气体,增加燃烧速度和温度,提高炉内反应效率。
第六步是煅烧,通过供气装置向高炉底部喷入空气或氧气,进一步增加炉内氧气含量,促使还原反应的进行,同时可以提高高炉产量和炉温。
第七步是热风烧结,使用高温热风对烧结矿进行预热,使其热态强度增加,为后续的转炉工艺做准备。
第八步是废气净化,高炉产生的废气经过除尘、脱硫等处理,以达到环保排放标准。
转炉是一种用于冶炼钢铁的设备,其基本原理是将生铁和一定量的废钢料放入转炉中,并通过高温氧化还原反应,消除生铁中的杂质,同时添加合适的合金和炉渣,使之成为合格的钢铁产品。
转炉的工艺流程可分为五个主要步骤,即装料、预热、碱性炼钢、脱硫炼钢和出钢。
第一步是装料,将生铁和废钢料按一定比例放入转炉中。
第二步是预热,转炉通过燃烧煤粉或气体,对炉内的原料进行预热,提高温度和反应效率。
第三步是碱性炼钢,通过抛石灰石向转炉中加入碱质,使炉内呈碱性,以增加炉渣和炉料的浮力,加快氧化反应速度,并吸附硫、磷等有害元素。
高炉炼铁工艺
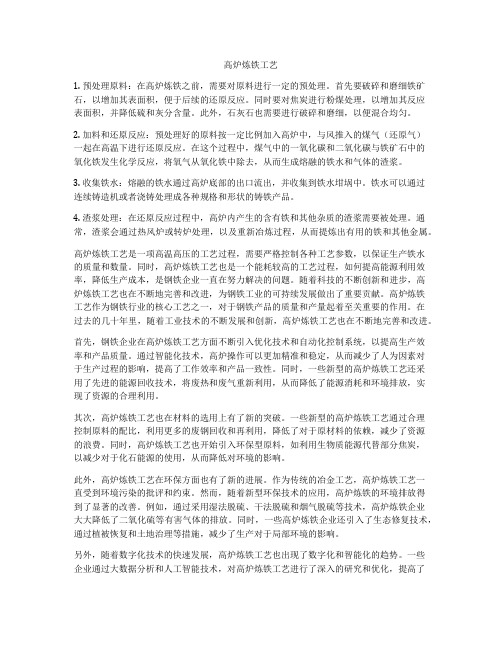
高炉炼铁工艺1. 预处理原料:在高炉炼铁之前,需要对原料进行一定的预处理。
首先要破碎和磨细铁矿石,以增加其表面积,便于后续的还原反应。
同时要对焦炭进行粉煤处理,以增加其反应表面积,并降低硫和灰分含量。
此外,石灰石也需要进行破碎和磨细,以便混合均匀。
2. 加料和还原反应:预处理好的原料按一定比例加入高炉中,与风推入的煤气(还原气)一起在高温下进行还原反应。
在这个过程中,煤气中的一氧化碳和二氧化碳与铁矿石中的氧化铁发生化学反应,将氧气从氧化铁中除去,从而生成熔融的铁水和气体的渣浆。
3. 收集铁水:熔融的铁水通过高炉底部的出口流出,并收集到铁水坩埚中。
铁水可以通过连续铸造机或者浇铸处理成各种规格和形状的铸铁产品。
4. 渣浆处理:在还原反应过程中,高炉内产生的含有铁和其他杂质的渣浆需要被处理。
通常,渣浆会通过热风炉或转炉处理,以及重新冶炼过程,从而提炼出有用的铁和其他金属。
高炉炼铁工艺是一项高温高压的工艺过程,需要严格控制各种工艺参数,以保证生产铁水的质量和数量。
同时,高炉炼铁工艺也是一个能耗较高的工艺过程,如何提高能源利用效率,降低生产成本,是钢铁企业一直在努力解决的问题。
随着科技的不断创新和进步,高炉炼铁工艺也在不断地完善和改进,为钢铁工业的可持续发展做出了重要贡献。
高炉炼铁工艺作为钢铁行业的核心工艺之一,对于钢铁产品的质量和产量起着至关重要的作用。
在过去的几十年里,随着工业技术的不断发展和创新,高炉炼铁工艺也在不断地完善和改进。
首先,钢铁企业在高炉炼铁工艺方面不断引入优化技术和自动化控制系统,以提高生产效率和产品质量。
通过智能化技术,高炉操作可以更加精准和稳定,从而减少了人为因素对于生产过程的影响,提高了工作效率和产品一致性。
同时,一些新型的高炉炼铁工艺还采用了先进的能源回收技术,将废热和废气重新利用,从而降低了能源消耗和环境排放,实现了资源的合理利用。
其次,高炉炼铁工艺也在材料的选用上有了新的突破。
安钢炼铁厂高炉工艺简介
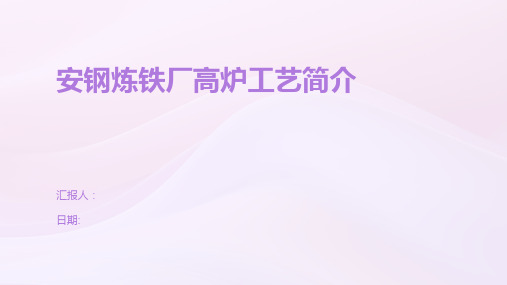
高炉炼铁工艺具有大规模、高效 、低成本等优点,是现代钢铁生 产的主要方法。
高炉炼铁工艺发展历程
古代高炉炼铁
古代炼铁技术采用竖炉或平炉, 以木炭为燃料,生产效率低下。
近代高炉炼铁
随着焦炭的广泛应用和技术的进步 ,近代高炉炼铁逐渐成为主流。
现代高炉炼铁
现代高炉炼铁技术不断改进,采用 大型化、自动化、高效化等手段, 进一步提高生产效率和产品质量。
配备必要的应急设施和器材,确保在事故发生时能够迅速投入使 用。
定期演练
定期组织应急演练,提高员工应对突发事件的能力和水平。
06
安钢炼铁厂高炉技术创新与发 展趋势
高炉技术创新成果及案例分享
高效长寿技术
通过采用先进的炉体结构和长寿技术,提高高炉寿命,减少停炉次 数和维修成本。
智能化控制技术
引入先进的自动化和智能化控制技术,实现高炉操作的精准控制和 优化,提高生产效率和产品质量。
02
安钢炼铁厂高炉设备与设施
高炉本体结构
01
02
03
炉壳
高炉的外壳,通常由钢板 和型钢焊接而成,具有保 护和支撑内部结构的作用 。
炉衬
高炉的内层结构,通常由 耐火材料砌筑而成,具有 保护炉壳和支撑炉料的作 用。
冷却设备
高炉的冷却设备包括冷却 壁、冷却水管等,用于控 制炉衬温度和防止炉衬烧 损。
炉顶设备与设施
挑战分析
随着技术的不断进步和应用,高炉生 产面临着新的挑战和问题,如设备更 新、技术升级、人才培养等。
THANKS
谢谢您的观看
炉顶装料设备
用于将炉料装入高炉顶部 的设备,包括布料器、探 尺等。
炉顶煤气处理设备
用于处理高炉煤气中携带 的粉尘和有害气体的设备 ,包括除尘器、洗涤塔等 。
高炉炼铁工艺

高炉炼铁工艺高炉炼铁是一种常见的冶金工艺,用于将生铁矿石转化为纯净的铁。
这种工艺采用高温和还原条件来实现铁矿石中的氧化铁还原为金属铁。
以下是高炉炼铁的基本工艺步骤:1. 铁矿石的预处理:铁矿石在进入高炉前需要进行一些预处理工作,包括破碎、磨粉和分类。
这些工作可以帮助提高炉内的氧化反应速度和还原效率。
2. 加料:铁矿石、焦炭和石灰石等原料按一定比例加入高炉中。
焦炭主要是提供还原剂,将铁矿石中的氧化铁还原为金属铁;石灰石主要是用于融化炉渣和吸收杂质。
3. 空气进风:高炉需要不断进风以供给氧气,促进焦炭的燃烧并提供裂解热。
同时,还需要加入一定的煤气或焦炉煤气作为还原剂,以保证炉内氧化铁的快速还原。
4. 矿石还原:在高温条件下,焦炭和煤气中的一氧化碳与氧化铁反应,生成二氧化碳和金属铁。
这些金属铁逐渐凝结成固体,并下沉至高炉底部。
5. 炉渣处理:金属铁下部的高炉炉渣是煤气和矿渣部分还原后生成的物质。
炉渣需要适当处理,以保证炉内温度和还原条件的稳定。
6. 铁水出流:通过炉底的出口,将炉内的铁水(金属铁)逐出高炉。
这些铁水会流进冷却池,凝固成板块状的生铁。
高炉炼铁工艺是一个高温高压的重工业过程,需要严格控制炉内的温度、气氛和物料流动。
通过这种工艺,铁矿石可以被转化为高品质的生铁,再经过一系列冶炼和精炼工序,最终得到各种铁合金和铁制品。
高炉炼铁是一个重要的冶金工艺,为现代工业提供了大量的生铁和铁合金。
虽然随着技术的不断发展,其他炼铁方法也得到了广泛应用,但高炉炼铁仍然是主要的铁矿石冶炼方法之一,其应用范围涵盖了钢铁工业、建筑材料工业和机械制造业等多个领域。
以下将详细介绍高炉炼铁工艺的特点、发展历程和应用前景。
高炉炼铁工艺的特点高炉炼铁工艺具有以下几个显著特点:1. 高温高压的特殊环境:高炉炼铁过程中,需要维持高温高压的炼铁环境。
通常高炉内温度达到1200摄氏度以上,高压和特殊气氛条件的维持对设备和操作人员的要求都非常高。
高炉炼铁工艺流程与主要设备概述
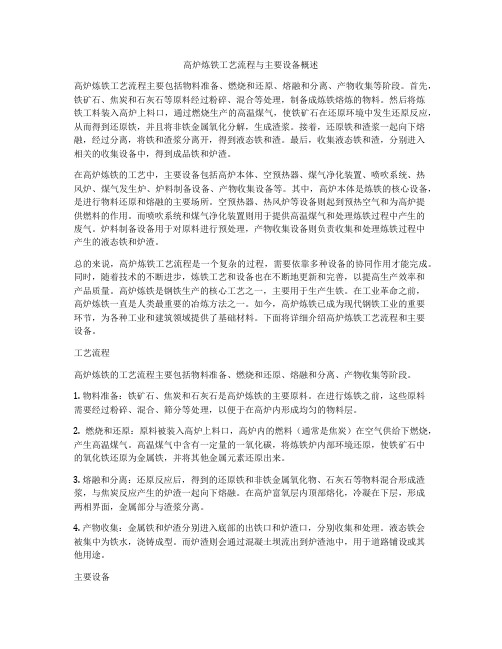
高炉炼铁工艺流程与主要设备概述高炉炼铁工艺流程主要包括物料准备、燃烧和还原、熔融和分离、产物收集等阶段。
首先,铁矿石、焦炭和石灰石等原料经过粉碎、混合等处理,制备成炼铁熔炼的物料。
然后将炼铁工料装入高炉上料口,通过燃烧生产的高温煤气,使铁矿石在还原环境中发生还原反应,从而得到还原铁,并且将非铁金属氧化分解,生成渣浆。
接着,还原铁和渣浆一起向下熔融,经过分离,将铁和渣浆分离开,得到液态铁和渣。
最后,收集液态铁和渣,分别进入相关的收集设备中,得到成品铁和炉渣。
在高炉炼铁的工艺中,主要设备包括高炉本体、空预热器、煤气净化装置、喷吹系统、热风炉、煤气发生炉、炉料制备设备、产物收集设备等。
其中,高炉本体是炼铁的核心设备,是进行物料还原和熔融的主要场所。
空预热器、热风炉等设备则起到预热空气和为高炉提供燃料的作用。
而喷吹系统和煤气净化装置则用于提供高温煤气和处理炼铁过程中产生的废气。
炉料制备设备用于对原料进行预处理,产物收集设备则负责收集和处理炼铁过程中产生的液态铁和炉渣。
总的来说,高炉炼铁工艺流程是一个复杂的过程,需要依靠多种设备的协同作用才能完成。
同时,随着技术的不断进步,炼铁工艺和设备也在不断地更新和完善,以提高生产效率和产品质量。
高炉炼铁是钢铁生产的核心工艺之一,主要用于生产生铁。
在工业革命之前,高炉炼铁一直是人类最重要的冶炼方法之一。
如今,高炉炼铁已成为现代钢铁工业的重要环节,为各种工业和建筑领域提供了基础材料。
下面将详细介绍高炉炼铁工艺流程和主要设备。
工艺流程高炉炼铁的工艺流程主要包括物料准备、燃烧和还原、熔融和分离、产物收集等阶段。
1. 物料准备:铁矿石、焦炭和石灰石是高炉炼铁的主要原料。
在进行炼铁之前,这些原料需要经过粉碎、混合、筛分等处理,以便于在高炉内形成均匀的物料层。
2. 燃烧和还原:原料被装入高炉上料口,高炉内的燃料(通常是焦炭)在空气供给下燃烧,产生高温煤气。
高温煤气中含有一定量的一氧化碳,将炼铁炉内部环境还原,使铁矿石中的氧化铁还原为金属铁,并将其他金属元素还原出来。
- 1、下载文档前请自行甄别文档内容的完整性,平台不提供额外的编辑、内容补充、找答案等附加服务。
- 2、"仅部分预览"的文档,不可在线预览部分如存在完整性等问题,可反馈申请退款(可完整预览的文档不适用该条件!)。
- 3、如文档侵犯您的权益,请联系客服反馈,我们会尽快为您处理(人工客服工作时间:9:00-18:30)。
2、工艺流程
4800m3高炉工艺布置图
3、主要工艺参数
序号 1 2 3 4 5 6 7 8 9 10 12 13 14 15 16 17 18 项目 有效容积 利用系数 焦比 煤比 富氧率 熟料率 烧结矿配比 球团矿配比 块矿配比 入炉矿品位 入炉风量 热风温度 炉顶温度 炉顶压力 渣铁比 日产生铁 年产生铁 单位 m3 t/(m3·d) kg/t铁 kg/t铁 1# 2200 2.36 350 169 5.10% 95% 80% 15% 4.50% 55.91% 4200 1185 150~260 0.21 368 5200 187 3# 4800 2.3 305 200 4% 86% 91% 75% 73.30% 16% 13% 9% 13.60% 59.20% 55.47% 7000 5800 1250 1250 150~260 150~250 0.25 0.22 310 365 10918 6500 382 237
1#、2#高炉,矿、焦槽单独设置,各用一条运 输胶带机(供矿皮带和供焦皮带),共用一条上 料主皮带,构成两个独立、并列的系统。
4.1矿焦槽系统
3#高炉,矿、焦槽呈双排布置,不设中间斗, 矿石、焦炭在槽下筛分称量后共用一条胶带机运 入上料主胶带输送机,然后运至高炉炉顶设备。
4#、5#高炉,矿、焦槽单独设置,矿石筛分 后经皮带机运输到两个矿石集中斗,焦炭由焦槽 直接进入焦炭集中斗,称量后装入料车,然后运 至高炉炉顶设备。
4.5炉体系统
4.5炉体系统
4.5.4炉底、炉缸内衬
2200m3 和2800m3 高炉采用陶瓷杯炭砖水冷炉底炉缸结构。 炉底中心下部立砌两层国产炭砖,其中下层为半石墨炭 砖,上层为微孔炭砖;上部砌两层低导热刚玉莫来石砖,炉 缸内侧砌低导热刚玉莫来石砖,外侧炉缸采用进口微孔炭 砖,在进口微孔炭砖与风口组合砖之间砌筑3层国产微孔炭 砖;在炉缸,炉底交接处采用加厚陶瓷质耐火材料和进口 微孔炭砖砌筑结构。 在风口区采用大块组合砖砌筑,以加强结构的稳定性; 铁口通道采用大块和小块相结合特殊组合砖结构。
4.5炉体系统
1)高径比:高炉越大,Hu/D越小,有利于改善高炉透 气性和减轻对高质量焦炭的过分依赖。
2)炉腰直径和炉腹角:厚壁和薄壁高炉内型尺寸差别 仅在炉腰直径,随着高炉内衬的侵蚀,炉腰直径将扩大,炉 身角、炉腹角减小,高炉透气性变好。 3)死铁层深度:死铁层深度随高炉容积变大而变深, 这将有效地减缓铁水环流对炉底炉缸耐火材料的冲刷,对提 高喷煤量、活跃炉缸、延长炉缸寿命均有利。
2# 2800 2.3 315 180 4.90%
m3/min ℃ ℃ Mpa kg/t t 万t
4、主要工艺系统
1)矿焦槽系统 2)上料系统 3)炉顶系统 4)煤气净化系统 5)炉体系统 6)出铁场系统 7)炉渣处理系统 8)送风系统 9)制粉喷吹系统 10)除尘系统
4.1矿焦槽系统
矿焦槽系统由矿槽、焦槽、给料筛分及称量 设备、胶带运输机、烧结及球团矿返矿仓、矿石 焦炭除铁器、碎焦分级及焦丁回收系统、通风除 尘设施、液压站及润滑系统等组成。
4.3炉顶系统
1#、2#、4#、5#高 炉采用串罐无料钟炉 顶。
4.3炉顶系统
3#高炉采用新型并 罐无料钟炉顶。
4.3炉顶系统
无钟炉顶具有良好的高压密封性能,灵 活的布料手段,能使高炉充分利用煤气能, 保持高炉顺行;同时运行可靠,易损部件少, 检修方便快捷。 可实现:定点布料,环形布料,扇形布料, 螺旋布料。
4.5炉体系统
4800m3高炉采用陶瓷垫炭砖水冷炉底炉缸结构。 炉底满铺砖第1层为国产超高导石墨砖,第2层为国产 高导热炭砖,第3、4层为引进微孔炭砖(引进SGL 3RD-N),第5、6层中心部分为陶瓷垫,陶瓷垫采用 国产塑性相结合刚玉砖,在陶瓷垫砖上及炉缸炭砖内 侧砌粘土砖(N-1)作为保护层。炉缸侧壁环形砖第 5—13 层采用引进超微孔炭砖(引进 SGL9RD-N), 第14—19层采用引进微孔炭砖(引进SGL 3RD-N)。
4.5炉体系统
4.5.2
4800m3高炉冷却设备及材质
冷却设备名称 比表面积 材质 高度(mm) 厚度(mm) 镶砖厚(mm) 数量(块) 管径(mm) 水流速(m/s) L1 球墨铸铁 36 φ 60×6 R-3 0.96 球墨铸铁 1940 240 100 46 φ 70×6 2.52 R-2 0.97 球墨铸铁 1940 240 100 48 φ 70×6 2.52 R-1 0.97 球墨铸铁 1940 240 100 52 φ 70×6 2.52 S-6 0.97 球墨铸铁 1940 240 100 52 φ 70×6 2.52 S-5 0.97 球墨铸铁 1940 240 100 52 φ 70×6 2.52 S-4 0.97 球墨铸铁 1940 240 100 56 钻孔 2.31 S-3 0.97 球墨铸铁 2600 120 球墨铸铁 2600 120 100 58 钻孔 2.31 S-1 1.10 球墨铸铁 2600 120 100 58 钻孔 2.31 B-3 1.10 球墨铸铁 1400 120 100 58 钻孔 2.31 B-2 1.10 球墨铸铁 1400 120 100 58 钻孔 2.31 B-1-2 1.10 铸铜板 52 铸铜 2.31 B-1-1 1.10 铸铜板 52 铸铜 2.31 风口段 1.10 灰铸铁 2350 240 0 58 φ 60×6 2.31 H-5 1.20 灰铸铁 2200 160 0 58 φ 70×6 2.31 H-4 1.00 灰铸铁 2200 160 0 58 φ 70×6 2.31 H-3 1.00 灰铸铁 1880 160 0 58 φ 70×6 2.31 H-2 1.00 灰铸铁 1880 160 0 58 φ 70×6 2.31 H-1 1.00 灰铸铁 1880 160 0 58 φ 70×6 2.31
4.4煤气净化系统
4000m3高炉全干式煤气净化系统流程图:
高炉煤气
旋风除尘器
布袋除尘器
TRT系统
净煤气管网
减压阀组
4.4煤气净化系统
高炉粗煤气除尘系统由煤气导出管、上 升管、下降管、重力除尘器及检修设施等构成。 从重力除尘器来的粗煤气,干法进入布袋除尘 器进行净化处理,湿法进入毕肖夫洗涤塔,除 尘后的净煤气经TRT(或调压阀组)后,送往 厂区净煤气总管。
78°41’24” 82°41’56”
个 个
2.32 28 3
2# 2800 11600 13000 8400 2400 4900 3500 2000 17500 2000 29900 78°41’24” 82°30’45” 2.3 30 3
3# 4747 14200 16300 10500 3600 5400 4500 2100 17800 2000 31800 76.866° 81.824° 1.95 38 4
4.5炉体系统
4800m3高炉炉体冷却水系统采用软水密闭循环冷却 系统,高炉软水冷却系统包括本体、风口小套,以及风口 中套、直吹管和热风炉系统阀门等的冷却。采用双循环系 统,即经炉体(内容包括:冷却壁水管、炉底)冷却后的 软水(称一次循环)经脱汽罐脱汽回泵房,由泵房分分流 一部分软水分两路加压,一路加压供风口小套冷却,另一 路加压供风口中套、直吹管、十字测温和热风炉系统阀门 等使用,二次加压水称二次循环;二次循环后的水与一次 循环后未加压的软水汇合后进膨胀罐和脱汽罐,然后进入 下一次循环。
4.4煤气净化系统
TRT
是将高炉炉顶有压煤气的压力能通过余压透平装置 回收、并将其转化成电能的装置,是一项既不消耗燃料、 又无污染的环保型节能措施。该装置具有以下三种功能: 1 ) 利用高炉煤气余压发电; 2) 利用透平的可调静叶控制高炉炉顶煤气压力; 3) 对煤气降温; TRT要考虑与高炉的匹配,使TRT的能量回收达到最大 化。
安阳钢铁集团股份有限公司
炼铁厂高炉系统工艺简介
杨
方
1、简介
安钢炼铁厂承担着为炼钢厂提供优质 铁水的任务。为了节能环保,淘汰落后 产能,炼铁厂去年淘汰了5座350m3小高 炉。现有高炉5座,其中1#高炉有效容 积2200m3 ,2#高炉有效容积2800m3 , 3#高炉有效容积4800m3 ,4#、5#高 炉有效容积450m3。
4.4煤气净化系统
布袋除尘器 4800高炉布袋除尘系统共设置16 个直径 6.0m 的布袋除尘器,采用双排并联对称布置, 由整体框架支撑。煤气主管采用分段变径,使 煤气匀速进入各个布袋除尘器。每个除尘器内 装425条布袋,每条布袋的直径160mm,长度 7.0m,单筒过滤面积约 1495m。
4.4煤气净化系统
α—炉腹角 β—炉身角 高炉有效高度: Hu=h1+h2+h3+h4+h5; 高炉有效容积: Vu=V1+V2+V3+V4+V5;
4.5炉体系统
项目 有效容积Vu 炉缸直径d 炉腰直径D 炉喉直径d1 死铁层高度h0 炉缸高度h1 炉腹高度h2 炉腰高度h3 炉身高度h4 炉喉高度h5 有效高度Hu 炉腹角α 炉身角β 高径比Hu/D 风口数 铁口数 单位 m3 mm mm mm mm mm mm mm mm mm mm 高炉内型参数 1# 2200 10600 12000 7900 2100 4500 3500 1850 16000 2000 27850
4.4煤气净化系统
高炉煤气
喷 淋 塔
4.5炉体系统
高炉本体由炉体框架平 台、炉壳、冷却设备、 耐火内衬、冷却水系统、 附属设备及检测仪表等 构成。
4.5炉体系统
4.5.1高炉内型
h0 —死铁层高度 h1 —炉缸高度 h2 — 炉腹高度 h3 —炉腰高度 h4 —炉身高度 h5 —炉喉高度 d —炉缸直径 d1 —炉喉直径 D—炉腰直径
4.4煤气净化系统