日本模具翻边孔自动计算公式(20160518205752)
冲压冲孔翻边高度计算公式

冲压冲孔翻边高度计算公式冲压工艺是制造业中常见的一种加工工艺,通过冲压设备对金属材料进行加工,可以实现复杂形状的加工需求。
在冲压过程中,冲孔和翻边是常见的操作步骤,而冲孔翻边的高度是一个重要的参数,直接影响产品的质量和性能。
因此,准确计算冲孔翻边高度是非常重要的。
冲压冲孔翻边高度的计算公式可以通过以下步骤得出:1. 冲孔直径,首先需要确定冲孔的直径,这个参数通常由设计要求确定,也可以根据产品的实际需要进行调整。
2. 材料厚度,冲孔翻边的高度与材料的厚度密切相关,因此需要准确测量材料的厚度。
3. 冲孔翻边比,冲孔翻边比是指冲孔直径与翻边高度之间的比值,通常情况下,冲孔翻边比为1:1,即冲孔直径等于翻边高度。
但在实际应用中,也会根据具体情况进行调整。
根据以上三个参数,可以得出冲压冲孔翻边高度的计算公式如下:翻边高度 = 冲孔直径 + 材料厚度冲孔翻边比。
通过这个公式,可以准确计算出冲孔翻边的高度,从而指导生产过程中的操作和调整。
在实际应用中,冲压冲孔翻边高度的计算公式可以根据具体情况进行调整和优化。
例如,对于不同的材料和冲孔形状,可能需要采用不同的修正系数,以提高计算的准确性和可靠性。
除了计算公式之外,冲压冲孔翻边高度的控制还需要考虑以下几个方面:1. 冲压设备的精度和稳定性,冲压设备的精度和稳定性直接影响冲孔翻边的质量和精度,因此需要定期检查和维护设备,确保其正常运行。
2. 模具设计和制造,冲孔翻边的质量和精度也与模具的设计和制造有关,因此需要选择合适的模具材料和加工工艺,确保模具的精度和耐用性。
3. 操作人员的技术水平,冲压操作人员的技术水平和经验也会影响冲孔翻边的质量,因此需要加强培训和管理,提高操作人员的技术水平。
总之,冲压冲孔翻边高度的计算公式是冲压加工中的重要参数,通过合理的计算和控制,可以实现产品质量和生产效率的提高。
同时,也需要注意设备、模具和操作人员等方面的管理和优化,以保证冲压加工的稳定性和可靠性。
设计计算翻边、翻孔
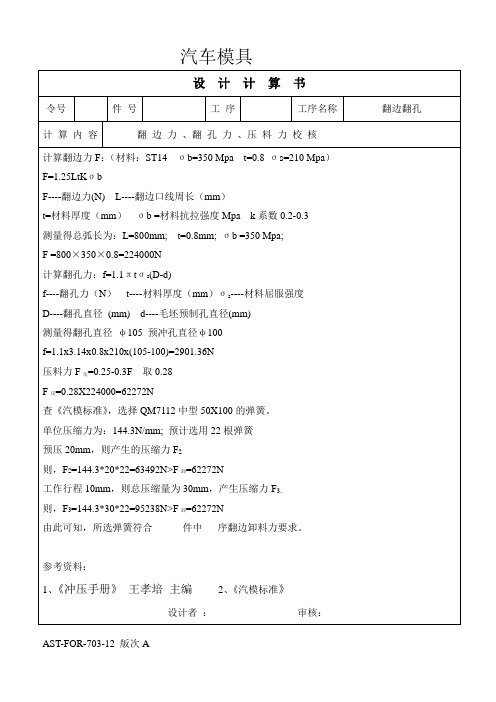
计算翻孔力:f=1.1πtσs(D-d)
f----翻孔力(N)t----材料厚度(mm)σs----材料屈服强度
D----翻孔直径(mm) d----毛坯预制孔直径(mm)
测量得翻孔直径φ105预冲孔直径φ100
f=1.1x3.14x0.8x210x(105-100)=2901.36N
汽车模具
设计计算书
令号
件号
工序
工序名称
翻边翻孔
计算内容
翻边力、翻孔力、压料力校核
计算翻边力F:(材料:ST14σb=350 Mpa t=0.8σs=210 Mpa)
F=1.25LtKσb
F----翻边力(N) L----翻边口线周长(mm)
t=材料厚度(mm)σb =材料抗拉强度Mpa k系数0.2-0.3
压料力F压=0.25-0.3F取0.28
F压=0.28X224000=62272N
查《汽模标准》,选择QM73N/mm;预计选用22根弹簧
预压20mm,则产生的压缩力F2
则,F2=144.3*20*22=63492N>F卸=62272N
工作行程10mm,则总压缩量为30mm,产生压缩力F3。
则,F3=144.3*30*22=95238N>F卸=62272N
由此可知,所选弹簧符合件中序翻边卸料力要求。
参考资料:
1、《冲压手册》王孝培主编2、《汽模标准》
设计者:审核:
AST-FOR-703-12版次A
翻孔模设计
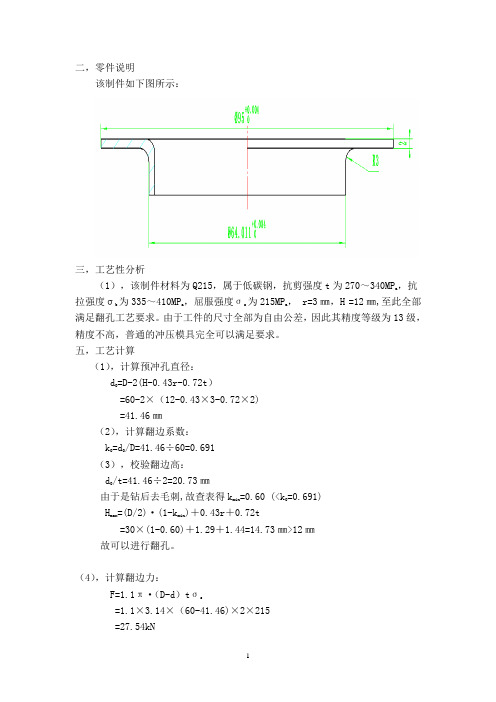
二,零件说明该制件如下图所示:三,工艺性分析(1),该制件材料为Q215,属于低碳钢,抗剪强度t 为270~340MP a ,抗拉强度σb 为335~410MP a ,屈服强度ζs 为215MP a , r=3㎜,H =12㎜,至此全部满足翻孔工艺要求。
由于工件的尺寸全部为自由公差,因此其精度等级为13级,精度不高,普通的冲压模具完全可以满足要求。
五,工艺计算(1),计算预冲孔直径: d 0=D-2(H-0.43r-0.72t )=60-2×(12-0.43×3-0.72×2) =41.46㎜(2),计算翻边系数: k 0=d 0/D=41.46÷60=0.691 (3),校验翻边高: d 0/t=41.46÷2=20.73㎜由于是钻后去毛刺,故查表得k min =0.60 (<k 0=0.691) H max =(D/2)·(1-k min )+0.43r +0.72t=30×(1-0.60)+1.29+1.44=14.73㎜>12㎜ 故可以进行翻孔。
(4),计算翻边力:F=1.1π·(D-d )t ζs=1.1×3.14×(60-41.46)×2×215 =27.54kN由于工作行程较长,翻边力必须处于许用负荷曲线之内,一般总的翻边力小于或等于压力机公称压力的50%~60%,且根据闭合高度,故查《材料成形设备》表2-2选J23-10其相关参数为:最大封闭高度:160㎜,工作台尺寸:200㎜×200㎜因为制件是简单的环形件,故压力中心为其几何中心(圆心)。
(5),计算凸凹模工作尺寸及公差:由于在翻孔过程中存在回弹现象,即翻口位置的孔径比凸模的外径尺寸要小,故为保证孔尺寸,凸、凹模按照孔的尺寸的上偏差加工。
由于制件精度采用IT13级,故凸模制造公差采用IT7级,制件翻边处的内孔尺寸D为60,则其公差Δ为0.011㎜,为使翻边回弹小,垂直度好,翻边的凸凹模间隙小于工件厚度以使其稍微变薄根据壁厚查资料得Z/2=2㎜凸模直径Dt =(D+Δ)-δt=60.011-0.012㎜凹模为孔加工,故应比凸模的低一级为IT9,即凹模孔径Da =(Dt+Z)+δa=64.011+0.004㎜六,主要零件的设计(1),凹模设计:由推件器尺寸及翻边件的翻边高的大小确定凹模的厚度H为45㎜,其刃口圆角半径与制件圆角相等为r=3㎜。
翻边的预冲孔如何计算
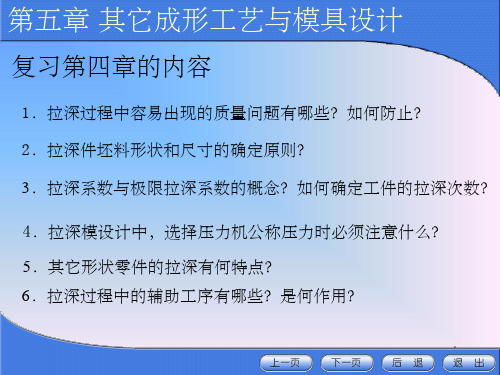
D
极限翻边系数 Kmin 见表5.3.1
翻边后竖边边缘的厚度,可按下式估算:
t t d t K
D
.
11
第五章 其它成形工艺与模具设计
第三节 翻边
一、内孔翻边(续)
1.圆孔翻边(续)
(2)翻边的工艺计算
1)平板坯料翻边的工艺计算
预冲孔直径d
d D 2 (H 0 .4r 3 0 .7t)2
.
1
第五章 其它成形工艺与模具设计
内容简介:
在掌握冲裁、弯曲、拉深成形工艺与模具设计的基础 之上,本章介绍其它成形工艺特点和模具结构特点。涉及 胀形、翻边、缩口、校形等成形工序的变形特点、工艺与 模具设计特点。
学习目的与要求:
1. 了解胀形、翻边、缩口、校形等工序的变形特点; 2. 了解胀形模、翻边模、缩口模、校形模的结构特点。
重点:
胀形、翻边工序的变形特点、工艺计算和模具结构特点。
难点:
翻边工序的变形特点、工艺计算。
.
2
第五章 其它成形工艺与模具设计
本章目录
第一节 概述 第二节 胀形 第三节 翻边 第四节 缩口 第五节 旋压 第六节 校形
.
3
第五章 其它成形工艺与模具设计
第一节 概述
在冲压生产中,通过板料的局部变形来改变毛坯的形状和
F pA
胀形单位面积压力p可用下式计算:
p
1.15zx
2t dm a
x
式中
zx ――胀形变形区实际应力,近似估算时取 zx ≈ b(材料的抗拉强度)
.
10
第五章 其它成形工艺与模具设计
第三节 翻边
翻边: 在模具的作用下,将坯料的孔边缘或外边缘冲制成竖立边
圆孔翻边系数

圆孔翻边系数关于圆孔翻边系数,一般有以下三种方法来表达:圆孔翻边的定义:在内径为圆形或近似圆形的管坯的两端用机器磨成相应尺寸的锥面,或在孔内按照管子公称直径加工出台阶来,或在内孔底部开椭圆型翻边槽,使管坯在挤压过程中形成两个对称的台阶或锥面,从而在焊缝和外壁间产生环向分布的应力,以补偿管坯的尺寸。
圆孔翻边的设计要求相关计算:内圆或外圆翻边系数为t=1+1/3(1+1/6)所以有一定限度,如果工件是小管,孔的加工比较容易,管子可采用冷轧管、热轧管、异型管等,而且易于加工制造,生产率也高。
若工件尺寸大,则需先车后钻,即先车锥孔再钻锥面,先钻锥面再车锥孔,这样就不好控制车削量。
在管材切断时由于会产生径向缩孔、扩径、弯曲、螺旋弯曲、扭曲等缺陷,所以需用尖刀在管材上切出具有一定精度的圆孔。
在外圆翻边加工中,为了保证其质量,需根据不同的要求,合理地选择加工方法和工艺参数。
例如,为了保证尺寸精度和粗糙度,常用手工电弧打底,液压冲孔翻边;为了满足表面粗糙度要求,还应该进行研磨、抛光等精加工工序。
1、通过修整锥面来提高翻边系数是十分有效的方法,常用的方法有两种:一种是圆周法,另一种是端面接触法,它们是按照先车削外圆,再车锥面的顺序逐步加工的。
2、将锥面加工到所需尺寸的最后几个小圆(即锥角)时,再加工孔的锥面,然后磨平小圆孔与锥面的接触部位,提高翻边系数。
但应注意到磨平小圆孔与锥面接触部位时,由于存在间隙,这里的加工精度不如上述方法那样高。
因此,当只能在某些地方才允许用此方法时,应慎重选用。
3、这些加工方法适用于内外孔翻边,大直径锥孔翻边多采用端面接触法。
4、用扩孔法来降低翻边系数是一种被普遍采用的方法。
即先把工件外圆车到锥孔底部,留一段长度的孔用手工电弧放电加工。
然后再用铣床加工出锥孔的锥角,从而获得高的翻边系数。
用激光加工锥孔翻边的方法可省去复杂的扩孔工序,而且锥面光滑无毛刺。
圆孔翻边加工有哪些特点?圆孔翻边是连接头连接中较为重要的一道工序,有着不可替代的作用,它关系着连接头连接的质量、强度以及经济性等问题。
铸造技术及计算公式理论 《东芝机械株式会社》(著)
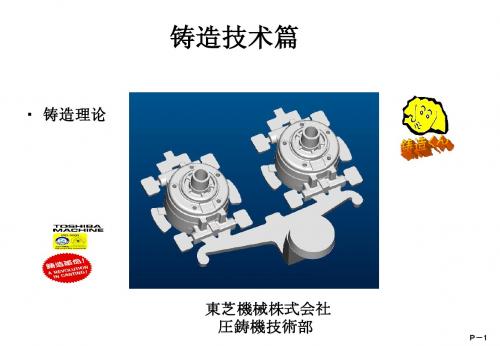
1)充填時間=0.01×2×2=0.04sec ( 係数) 700 2)高速速度= 38.5 × 0.04 × 2.6 = 175㎝/s = 1.75m/s 気泡 射出油壓缸剖面積=(π/4)×12.52=123㎝2
( 係数) 3)模具界限速度 = 550 ×
(1.3)2 × 123 × 100 ( 38.5 )
。
低速速度
低速速度是在 內沒有空氣 入的 下 速。
空 的
程
低速速度的
低速速度
例題 柱塞直徑:φ70 mm 鑄入重量:900 g 空打行程:337 mm
柱塞剖面積 =(π/4)×72 = 38.5㎝2
溶湯比重:2.6 g/cm3 900
1)料管充填率 = 38.5 × 33.7 × 2.6
×100 % = 27 %
增壓
壓製凝固產品。 溶湯凝固前加壓。 (昇壓時間) 昇壓時間) 縮小鑄巢,增加模具的密實性。 (鑄造壓力) 鑄造壓力)
將從湯勺注入料管內的溶湯運送至澆口。 這時,溶湯表面不會發生波紋, 且可從排氣口排放料管內的空氣, 以防止空氣進入溶湯內。 但是,如果速度太慢,就會發生凝固。
(低速速度) 低速速度)
铸造技术篇
・ 铸造理论
東芝機械株式会社 圧鋳機技術部 圧鋳機技術部
P-1 P-1
压铸( Cast) 1. 压铸(Die Cast)的定義 將溶湯(熱溶液)壓入精密的模具內 以高精度大量生產優良鑄肉之鑄造物的鑄造方式,及以此種方式製造的產 將溶湯(熱溶液)壓入精密的模具內,以高精度大量生產優良鑄肉之鑄造物的鑄造方式,及以此種方式製造的產品即稱 為澆鑄。 日本澆鑄協會) 為澆鑄。(社團法人 日本澆鑄協會) 全自動循環的運轉(壓鑄機) 2. 全自動循環的運轉(壓鑄機) 脫模劑噴霧 → 鎖模 → 3. 澆鑄是一種鑄造法 合金溶湯(熱溶液)凝固之前,高速將模穴內的空氣替換溶湯,以高壓使其凝固的方法。 合金溶湯(熱溶液)凝固之前,高速將模穴內的空氣替換溶湯,以高壓使其凝固的方法。
翻边的预冲孔如何计算

第五章 其它成形工艺与模具设计
第二节 胀形
一、胀形的变形特点
当坯料外径(wài jìnɡ)与成形直径的比值D/d>3时,其成形完 全依赖于直径为d的圆周以内金属厚度的变薄实现表面积的增大而成 形。胀形的变形(biàn Nhomakorabeaíng)区
精品资料
第五章 其它成形(chénɡ xínɡ)工艺与模 具第二设节计 胀形
第五章 其它成形工艺与模具设计
复习(fùxí)第四章的内容
1.拉深过程中容易出现的质量问题(wèntí)有哪些?如何防止?
2.拉深件坯料形状和尺寸的确定原则?
3.拉深系数与极限拉深系数的概念?如何确定工件的拉深次数? 4.拉深模设计中,选择压力机公称压力时必须注意什么?
5.其它形状零件的拉深有何特点? 6.拉深过程中的辅助工序有哪些?是何作用?
精品资料
行计算。
精品资料
冲制M5以下的小螺孔
第五章 其它(qítā)成形工艺与模具设计
第三节 翻边
四、翻边模结构
内孔翻边模
内、外缘(wài yuán)同时翻边的模具
落料、拉深、冲孔、翻边复合模
精品资料
第五章 其它成形工艺与模具设计
作业(zuòyè)布置:
思考(sīkǎo)与练习题1、2、6。
精品资料
第五章 其它成形(chénɡ xínɡ)工艺与模具 设计
按变形的性质分
伸长(shēn chánɡ)类翻边
压缩类翻边
1.伸长(shēn chánɡ)类翻边
变形程度
伸
b Rb
应在坯料的两端对 坯料的轮廓线做必要的
修正
a)伸长类平面翻边
b)伸长类曲面翻边
精品资料
冲压模具翻孔预冲孔的计算

冲压模具翻孔预冲孔的计算冲压模具设计中的翻孔和预冲孔是常见的操作,用于加工板材或金属工件上的孔洞。
本文将介绍冲压模具翻孔和预冲孔的计算原理和方法。
1.翻孔的计算方法:翻孔是通过模具的冲击作用将材料冲出一定形状的孔洞,其计算方法如下:(1)计算翻孔的直径:翻孔的直径可以根据翻边高度和材料厚度来计算,一般来说,翻孔直径应为翻边高度的1.5到2倍。
(2)计算翻孔的深度:翻孔的深度可以根据翻边高度和钢板的硬度来计算,一般来说,翻孔的深度应为翻边高度的1.5到2倍。
2.预冲孔的计算方法:预冲孔是在冲压模具中先冲制一个小直径的孔洞,然后再进行下一步的冲裁操作,其计算方法如下:(1)计算预冲孔的直径:预冲孔的直径可以根据材料的厚度和孔洞形状来计算,一般来说,预冲孔的直径应为材料厚度的0.6到1倍。
(2)计算预冲孔的间距:预冲孔的间距可以根据模具的结构和冲裁方式来计算,一般来说,预冲孔的间距应保持在材料厚度的2到3倍。
3.翻孔和预冲孔的计算实例:假设要设计一个冲压模具用于加工厚度为2mm的钢板上的孔洞,根据上述的计算方法,可以进行如下计算:(1)翻孔的计算:根据翻边高度的要求,假设翻边高度为5mm,则翻孔的直径应为7.5mm到10mm之间。
根据钢板的硬度,可以计算出翻孔的深度应为7.5mm 到10mm之间。
(2)预冲孔的计算:根据材料的厚度,假设预冲孔的直径为1.2mm到2mm之间。
根据模具的结构和冲裁方式,假设预冲孔的间距为4mm到6mm之间。
以上仅为一个简单的计算实例,实际的冲压模具设计需要考虑更多的因素,如材料的性质、模具的结构和冲裁方式等。
因此,在进行冲压模具翻孔和预冲孔的计算时,需要根据具体情况进行综合考虑和计算。
在冲压模具设计中,翻孔和预冲孔的计算是非常重要的一步,直接影响到模具加工的质量和效率。
因此,在进行冲压模具翻孔和预冲孔的计算时,需要充分考虑材料的性质、模具的结构和冲裁方式等因素,并进行合理的计算和优化。