模具翻边设计
模具翻边的设计
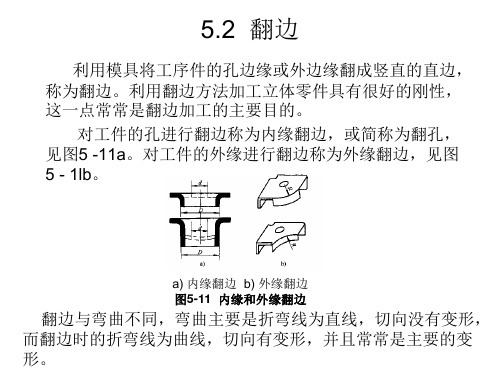
5.2 翻边
Hmax=0.5D(1- Kfmin )+0.43 rd +0.72t (5-13)
如果翻边直壁高度H小于一次翻边的极限高度 Hmax,则只要算出预孔直径d0,按d0冲预孔后就 可以直接达到翻边高度。 如果翻边件直壁的高度超过了一次翻边极限高 度,则该件便不能一次完成翻边。这时,可采取多 次翻边(两次之间可安排退火软化工序)、对变形区 进行加热翻边等工艺方法。当翻边件直壁高度较大 时,比较好的工艺方法是先用平板毛坯拉深成带宽 凸缘的圆筒形件,在底部冲底孔后再进行翻边,使 翻出的直径与拉深件直径相同,以达到要求的翻边 高度。具体计算如下。
5.2 翻边
确定非圆孔翻边的底孔形状和尺寸,一般仍按 弯曲展开计算。但由于切向变形的不均匀性,如果 取等宽的毛坯,翻边后直壁端头不可能平齐。如果 考虑非圆孔各段之间的相互影响,修正变形区宽度, 将使底孔形状变得不规则,给底孔的制备造成不必 要的困难,而且也很难准确修正。因此,对一般要 求的非圆孔翻边件,可以不考虑底孔形状的修正问 题。只有当翻边高度要求严格时,才考虑修正变形 区宽度。这时,可先按弯曲展开计算直线段c的翻边 宽度Bc,取凹弧段a的翻边宽度Ba为Bc的1.05~1.1倍。 凸弧段b的翻边宽度可利用拉深圆筒形件的毛坯直径 计算公式求得。最后,需考虑三者间的相互影响, 将底孔形状修正光滑。
5.2 翻边
4.翻边凸模的形状: 图5-12所示为用平头凸模翻边,当凸模圆角 半径rp较小时,变形过分集中于底孔边缘,容易 引起开裂。随着值的增大,直至采用球形、抛 物面形或锥形凸模,变形将得到分散,可减小 底孔边缘开裂的可能性,因而允许采用较小的 翻边系数。 表5-4给出了低碳钢的极限翻边系数Kfmin , 从中可以看出上述因素对其值的影响程度。
冲压模具毕业设计 翻边模的设计

基本内容及拟解决的主要问题:
1)设计落料模具
2)设计液压拉深模具
3)设计翻边模具
4)设计卷边模具
落料模具的设计主要是为了得到圆形板料的设计,根据逆向设计和理论要求,确定圆形板料的尺寸,根据圆形板料的尺寸来设计落料模具。在落料模设计的过程中,对板料的利用率进行计算,使其符合经济实用的要求[4]。在对落料模的设计中,根据其它相关类似模具的设计,落料模设计成通用的落料模结构。同时对落料冲压力进行计算来选择相对应的压力机。根据设计的数据,利用Solidworks软件画出三维模型。
Analysis of the complexity of the shade of such a shape, thin-walled parts of the structural characteristics.Easy for die-casting in the formation of cracks, lack of defects in the tensile properties of the process, and in accordance with the requirements of theoretical analysis and data based on the use of Solidworks 3D solid modeling software, and the provisions of unknown size. Then calculated using the three-dimensional entities, the quality of parts, in accordance with Solidworks software to design parts of the quality of the target plate thickness the diameter of the circular blank. According to the original blank diameter to determine the number of dimensions for the design and follow-up to provide a basis for research. At the same time, the use of Solidworks software or other three-dimensional software model of the stamping feasibility analysis and design, use of software related to shade Mold mold design.
冲孔翻边模具设计1
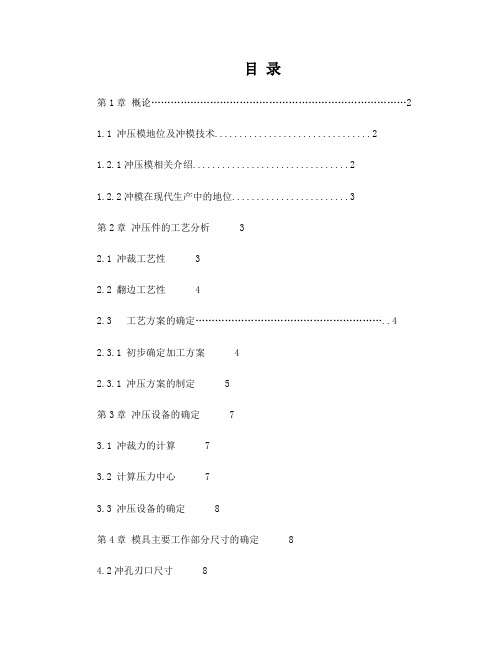
目录第1章概论 (2)1.1 冲压模地位及冲模技术 (2)1.2.1冲压模相关介绍 (2)1.2.2冲模在现代生产中的地位 (3)第2章冲压件的工艺分析 32.1 冲裁工艺性 32.2 翻边工艺性 42.3 工艺方案的确定 (4)2.3.1 初步确定加工方案 42.3.1 冲压方案的制定 5第3章冲压设备的确定 73.1 冲裁力的计算 73.2 计算压力中心 73.3 冲压设备的确定 8第4章模具主要工作部分尺寸的确定 84.2冲孔刃口尺寸 84.3 翻边刃口尺寸 9第5章模具结构和主要零部件设计 105.1 模架的选择 105.2冲孔凸模的设计 105.3 凹凸模的设计 115.4 翻边凹模的设计 115.5 其他部件的设计 12第六章装配图装配 126.1 装配图 13第一章概论1.1引言日常生产、生活中所使用到的各种工具和产品,大到机床的底座、机身外壳,小到一个胚头螺丝、纽扣以及各种家用电器的外壳,无不与模具有着密切的关系。
模具的形状决定着这些产品的外形,模具的加工质量与精度也就决定着这些产品的质量。
因为各种产品的材质、外观、规格及用途的不同,模具分为了铸造模、锻造模、压铸模、冲压模等非塑胶模具,以及塑胶模具。
随着科学技术的进步和工业生产的迅速发展,冲压加工技术的应用愈来愈广泛,模具成形已成为当代工业生产的重要手段。
1.2冲压模地位及我国冲压技术1.2.1冲压模相关介绍冷冲压:是在常温下利用冲模在压力机上对材料施加压力,使其产生分离或变形,从而获得一定形状、尺寸和性能的零件的加工方法。
冲压可分为五个基本工序:冲裁、弯曲、拉深、成形和立体压制。
冲压模具:在冷冲压加工中,将材料(金属或非金属)加工成零件(或半成品)的一种特殊工艺装备,称为冷冲压模具(俗称冷冲模)。
冲压模按照工序组合分为三类:单工序模、复合模和级进模。
复合模与单工序模相比减少了冲压工艺,其结构紧凑,面积较小;冲出的制件精度高,工件表面较平直,特别是孔与制件的外形同步精度容易保证;适于冲薄料,可充分利用短料和边角余料;适合大批量生产,生产率高,所以得到广泛应用,但模具结构复杂,制造困难。
翻边模具
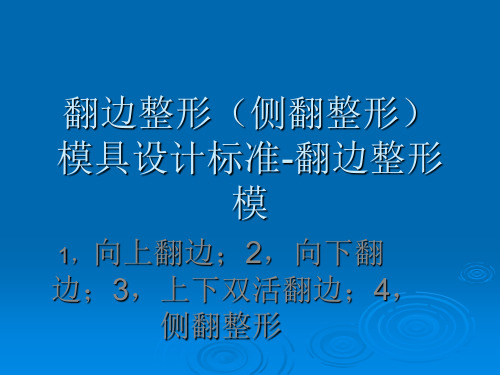
1,向上翻边;2,向下翻
边;3,上下双活翻边;4, 侧翻整形
1,向上翻边:
下模+托料芯
上模
常规上翻:示例:AC274,V102 标准上翻机构:示例:AB455 非标上翻机构:示例:AB455
2,向下翻边:
下模
上模+压料芯
事例:AC251,V338
3,上下双活翻边:
事例6:AA734:滑车为直推形式。 (兼两侧平推三功能)
下模+托料芯
上模+压料芯
事例:AC861,V342
4,侧翻整形:
事例1:V013:滑车为侧推平推形 式,侧翻边为吊翻,侧翻
事例2:AC22229:滑车为滚轴形 式
事例4:AB818: 滑车为拉车形式 (侧翻驱动器为固定在下模和在滑 车上两种形式)
事例5:T748: 滑车为拉车形式,带 侧压料芯。
第5章 翻边模设计讲解
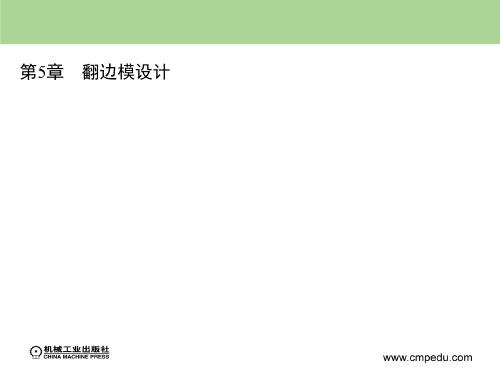
5.2 翻边镶件
图5-13 避开毛坯变厚部分的接合面
5.2.3 凸、凹模镶件尺寸 翻边凸、凹模镶件的尺寸,参考修边模刃口镶件的结构尺寸比例, 同时还要注意: 1)翻边凸模镶件的形状尺寸,在保证镶件的强度和刚度的同时, 要保证在凹模镶件离开后,能顺利地取出翻边件。
5.2 翻边镶件
2)设计翻边凹模镶件的前端形状尺寸时,要考虑到翻边部分毛坯 的变形特点。 3)在交接部位的翻边凹模镶件应有足够的运动空间。 5.2.4 凸、凹模镶件的交接 当翻边轮廓是连续的,如外缘轮廓形状的翻边、窗口封闭内形的 翻边等,一般由一个方向运动来完成翻边是不可能的,而是由两 个或两个以上不同的运动方向的翻边凹模镶件进行翻边,这就需 要考虑不同方向运动的凹模镶件的交接问题。
5.1 翻边模典型结构
(6)汽车覆盖件窗口封闭向外翻边的斜楔翻边模 翻边后制件包在 凸模上,无法取出,必须将凸模做成活动可分的,翻边时缩小成 翻边形状,而翻边凹模是扩张向外翻边的。 5.1.2 翻边凸模的扩张结构 汽车覆盖件向内的翻边一般都是沿着覆盖件的轮廓,翻边加工结 束后翻边件包在凸模上的,无法取出,必须将翻边凸模做成活动 可分的。在压力机滑块行程向下翻边以前,利用斜楔的作用将缩 着的翻边凸模扩张成翻边形状后即停止不动,在压力机滑块行程 继续向下时翻边凹模进行翻边。翻边以后凹模在弹簧的作用下回 程,然后翻边凸模靠弹簧的作用返回原位,取出制件。翻边凸模 的扩张行程以能取出翻边制件为准,这种结构称为翻边凸模的扩 张结构,俗称翻边凸模的开花结构。
内孔翻边模具毕业设计说明书[管理资料]
![内孔翻边模具毕业设计说明书[管理资料]](https://img.taocdn.com/s3/m/59d118d8915f804d2a16c101.png)
2009届毕业设计内孔翻边模具设计论文作者姓名:__ __所在院系:__机电工程学院_____ 所学专业:数控技术指导老师:_ _论文完成时间:_2009年 5 月 6 日___目录内容摘要 ....................................................................... 错误!未定义书签。
关键词 ........................................................................... 错误!未定义书签。
Abstract .......................................................................... 错误!未定义书签。
Key word ....................................................................... 错误!未定义书签。
1 引言 (3)2 工艺分析 (3)3 工艺方案的确定 (3)4 工艺设计与计算 (4)预翻孔直径的计算及成型次数的判断 (4)凸凹模间隙大小及凸凹模的工作尺寸及公差 (5)压边力、翻孔力以及压力性能参数的计算 (5)模具结构原理与主要零部件的设计与选择 (6)模具结构原理 (6)主要零部件的设计与选择 (7)凸模和凹模的工艺设计与加工 (9)模具设计过程辅助工序 (13)5 模具总体结构与工作原理 (13)参考文献 (14)致谢 (15)内容摘要:本设计为内孔翻边(翻孔)模具的设计,其主要功能是沿冲压件内孔周围将材料翻成侧立凸缘,此工序是冲压生产中最常见的工序,尤其在汽车,拖拉机领域应用广泛。
在模具设计过程中,在预翻孔直径计算与判断可否一次成形上,凸凹模间隙的计算,凹模过渡圆弧大小的选择以及压料力、翻孔力的计算与校核、压力机的选择,模具主要零件的选择等方面上都做了详尽的分析,并设计了整套内控翻边模具。
4.翻边 翻边整形 翻孔设计规范
目录1 翻边的分类.......................................................22 垂直翻边.........................................................23 水平斜楔翻边和倾斜斜楔翻边.......................................284 下平面图.........................................................385 上平面图.........................................................426 剖面图...........................................................487 向视图...........................................................498 零件图...........................................................499 模具的常用材料及与热处理要求.....................................5010 标准件的选用规则.................................................5211 图面尺寸标准规则.................................................531 翻边的分类翻边按冲压方向分可分为垂直翻边、水平斜楔、翻边和倾斜翻边。
2 垂直翻边垂直翻边分为平板类翻边和拉延成形类翻边。
2.1 平板类翻边(压弯)平板类翻边(压弯)分为平板直线压弯,曲线翻边和翻孔。
2.1.1平板直线压弯平板直线压弯的展开计算: L=e1+e2+e3+en+R1e+R2e+Rne 式中:L :展开长度;e1、en :各段走线段长度;R1e :压弯圆角的中性层展开长度。
冲压模具毕业设计翻边模设计
刃口尺寸的调整方法:根据冲压件的尺寸和形状,以及冲压机的压力和速度,进行适当的调整
刃口尺寸的确定注意事项:刃口尺寸的确定要符合冲压件的尺寸和形状,以及冲压机的压力和速度,以保证冲压件的质量和生产效率。
刃口尺寸的确定原则:根据冲压件的尺寸和形状,以及冲压机的压力和速度来确定
刃口尺寸的计算方法:根据冲压件的尺寸和形状,以及冲压机的压力和速度,利用公式进行计算
材料处理:对材料进行热处理、表面处理等,提高材料的耐磨性、耐腐蚀性和抗疲劳性
翻边模的工艺参数设计
PART FIVE
冲压工艺方案的确定
确定冲压工艺方案的目的:提高生产效率,降低成本,保证产品质量
冲压工艺方案的选择:根据产品形状、尺寸、材料等因素选择合适的冲压工艺方案
冲压工艺方案的设计:包括模具设计、冲压设备选择、冲压工艺参数设定等
退火:将模具材料加热到一定温度后保温一定时间,消除应力,提高塑性和韧性
调质:将模具材料加热到一定温度后保温一定时间,然后冷却,提高硬度和韧性
渗碳:将模具材料加热到一定温度后渗入碳元素,提高表面硬度和耐磨性
模具材料的选用原则
材料强度:应满足模具的使用寿命要求
材料硬度:应与冲压件的硬度相匹配
材料耐磨性:应具有良好的耐磨性,减少磨损
冲压工艺方案的优化:根据生产实际情况,对冲压工艺方案进行优化和改进,以提高生产效率和产品质量。
冲裁间隙的确定
冲裁间隙的定义:冲裁过程中,冲头和被冲材料之间的最小距离
冲裁间隙的确定方法:经验公式法、试验法、计算机模拟法等
冲裁间隙的确定原则:保证冲裁质量、提高生产效率、降低成本等
冲裁间隙的影响因素:材料性质、冲头形状、冲压速度等
寿命预测的重要性:合理预测模具寿命,有助于优化生产工艺,降低生产成本,提高产品质量。
翻边模设计
第5章 翻边模设计
5.2 翻边镶件
5.2.5 凸、凹模镶件材料 2.翻边凹模的材料 在大批量生产中,应设计成镶件结构。 通常,翻边凹模镶块采用T10A(产量小时)或 Crl2Mov(产量大量或曲线轮廓处),热处理硬 度为58~62HRC。
第5章 翻边模设计
5.2 翻边镶件
5.2.4 凸、凹模镶件的交接
翻边凹模镶件的交接处常采用空开法或重复法两种处理方法。
图5-14 空开法凹模镶件交接实例
第5章 翻边模设计
5.2 翻边镶件
5.2.4 凸、凹模镶件的交接
图5-15 重复法凹模镐件交接实例
第5章 翻边模设计
5.2 翻边镶件
5.2.5 凸、凹模镶件材料
第5章 翻边模设计
5.1.4翻边时的压料
图5-2 翻边时的压料部位
ቤተ መጻሕፍቲ ባይዱ
第5章 翻边模设计
5.1.5 翻边模的导向 翻边模的导向方式可选择导柱导套导向、导 板导向、导块导向等多种导向方式。 当修边件不太大,侧向力较小时,可选用两 个或四个导柱导套导向,结构简单,制造方便。 若翻边时的侧向力较大,选用导块导向或背 靠块导向,还可辅以导柱导向。
图5-4 斜楔翻边模加工的翻边件举例
第5章 翻边模设计
5.1.6翻边模的出件 在斜楔模中常用的退件机构
图5-5 气缸退件器图 1 -退件器 2-制动螺钉 3-气缸
第5章 翻边模设计
5.1.6 翻边模的出件 在斜楔模中常用的退件机构
图 5-6 退件器与定位装置连接在气缸上退件 1 -退件器 2-连接器 3-衬垫 4-活动定位装置 5-气缸 6-限位 器
第5章 翻边模设计
5.1.7 翻边模典型结构示例
图5-9 单向斜楔和上模滑动斜楔组合和斜楔结构 1、3 –斜楔滑块 2-斜楔传动器
内外缘翻边模具设计(精)
二二一五八九一一五一结束语历经近一个月的毕业设计即将结束敬请各位老师对我的设计过程作最后检在这次毕业设计中通过参考查阅各种有关模具方面的资料请教工厂中极具经验的模具设计人员和工人师傅以及各位老师有关模具方面的问题特别是模具在实际中可能遇到的具体问题使我在这短暂的时间里对模具的认识有了一个落料模模具设计的成型方法成型零件的设计成型零件的加工工艺主要工艺参数的计算模具的总体结构设计及零部件的设计等都有了进一步的理解和掌握
1.1本课题的意义、目的、研究范围及要达到的要求
在现代产品生产中,模具由于其加工效率高,互换性好,节约原材料,所以得到很广泛的应用。随着现代化工业和科学技术的发展,模具的应用越来越广泛,其适应性也越来越强。已成为工业国家制造工艺水平的标志和独立的基础工业体系。
另外,采用模具进行成形加工,是少、无切削的主要工装,在大批、大量加工中,可使材料利用率达90%或以上。
Key words die design cross nesting blanking Die
第1章引言
大学四年的本科学习即将结束,毕业设计是其中最后一个环节,是对以前所学的知识及所掌握的技能的综合运用和检验。随着我国经济的迅速发展,采用模具的生产技术得到愈来愈广泛的应用。
- 1、下载文档前请自行甄别文档内容的完整性,平台不提供额外的编辑、内容补充、找答案等附加服务。
- 2、"仅部分预览"的文档,不可在线预览部分如存在完整性等问题,可反馈申请退款(可完整预览的文档不适用该条件!)。
- 3、如文档侵犯您的权益,请联系客服反馈,我们会尽快为您处理(人工客服工作时间:9:00-18:30)。
5.2 翻边
• 翻边件的直径尺寸一般都要求不严,只有用作轴 套使用时,才对内径尺寸要求较严。这时,可参 考拉深模尺寸计算方法,先确定翻边凸模的直径 尺寸及公差。再由翻边间隙值确定翻边凹模的直 径尺寸,也可取约为0.75,为板料厚度。单面翻 边间隙也可按表5-7选取。
5.2 翻边
• 5.2.2外缘翻边 外缘翻边是在板料边缘进行的翻边,翻边线都是非封 闭的轮廓。 外缘翻边按变形特点可分为两类:即伸长类和压缩类; 当翻边线为内凹弧时,变形特点与翻孔是相同的,主 要变形是切向受拉伸,因此称为伸长类翻边。 而当翻边线为外凸弧时,变形特点与翻孔完全不同, 与拉深是相同的,主要变形是切向受压缩,因此称为压缩 类翻边。 外缘翻边前的工序件可以是平面件,也可以是曲面件。 按结构形式可分为四种:即伸长类平面翻边和曲面翻 边、压缩类平面翻边和曲面翻边。本书只介绍平面外缘翻 边。
5.2 翻边
1.打板 2.凹模 3.凸模 4.压料板 图5-18 倒装式翻孔模
1.凸模 2.弹簧 3.压料板 4.工序件 5.凹模 6.顶板 7.顶杆 图5- 19 顺装式翻孔模
5.2 翻边
(二)翻边凸模和凹模的设计 • 翻边时,板料相对凹模圆角没有滑动,因此对翻 边凹模的圆角半径没有严格的限制可直接取工件 要求的圆角半径。 翻边凸模的结构形式很多,图 5-20给出几种常用圆孔翻边凸模的形状和尺寸。
5.2 翻边
确定非圆孔翻边的底孔形状和尺寸,一般仍按 弯曲展开计算。但由于切向变形的不均匀性,如果 取等宽的毛坯,翻边后直壁端头不可能平齐。如果 考虑非圆孔各段之间的相互影响,修正变形区宽度, 将使底孔形状变得不规则,给底孔的制备造成不必 要的困难,而且也很难准确修正。因此,对一般要 求的非圆孔翻边件,可以不考虑底孔形状的修正问 题。只有当翻边高度要求严格时,才考虑修正变形 区宽度。这时,可先按弯曲展开计算直线段c的翻边 宽度Bc,取凹弧段a的翻边宽度Ba为Bc的1.05~1.1倍。 凸弧段b的翻边宽度可利用拉深圆筒形件的毛坯直径 计算公式求得。最后,需考虑三者间的相互影响, 将底孔形状修正光滑。
5.2 翻边
如图5-15所示,工艺计算程序是先确定翻边所 能达到的最大高度,按图示几何关系,翻边高度为:
图5-14 平板冲底孔后翻边
图5-15 拉深件底部冲孔后翻边
h 0.5(D d 0 ) (rp 0.5t ) 0.5 (rp 0.5t )
≈
则 hmax 0.5D(1 K f min ) 0.57rp
5.2 翻边
图5-16 非圆孔翻边
5.2 翻边
(二)非圆孔翻边系数 非圆孔翻边与半径相同的圆孔翻边相比较, 允许采用较小的翻边系数 K 'f ,可按下式估算: K 'f K f 1800 (5-19) 式中 Kf ——圆孔极限翻边系数,见表5-4; α——圆弧段中心角(0)。 上式适用于α ≤1800,当α >180时。直线段对圆弧 段的缓解作用已不明显,工艺计算仍需采用圆孔 翻边系数。当直线段很短时,也按圆孔翻边处理。 低碳钢板的非圆孔极限翻边系数也可以按表 5-5查得。
5.2 翻边
(三)非圆孔翻边的工艺计算 非圆孔翻边时,工艺计算主要考虑两方面内 容:一是核算变形程度;二是确定底孔的形状和 尺寸。 当翻孔形状复杂时,应分段进行变形程度的 核算。图5-17所示的非圆孔翻边件,按变形特点 可分为三种类型:凹弧段a具有翻孔的变形特点; 凸弧段b具有拉深的变形特点;而直线段c则主要 是弯曲。因此,为了判断该件能否一次成形,对 于凹弧段a应按非圆孔翻边系数判断。而且,当翻 边高度相等时,只需核算圆弧半径较小的R4段, 因为R4 <<R2,则R4段的变形程度比R2段大得多。
(三) 影响翻边系数的因素 1.材料的塑性: 由于翻孔时的主要变形是切向的伸长变形,因此 影响翻边系数的主要因素是材料的塑性。最大切 向伸长变形在底孔边缘处,其值不应超过材料的 伸长率:
D d0 D 1 max 1 1 d0 d0 Kf
≤δ
由上式可得翻边系数Kf与材料伸长率δ或断面 收缩率ψ之间的近似关系: Kf =1/(1+ ψ),或Kf =1—ψ。这表明:材料的塑性越好,其极限翻边 系数可以更小些。
随凸模圆角半径的增大,翻边力将大幅度减小。 当采用球头凸模翻孔时,翻边力可比采用小圆角 平头凸模降低50%左右。采用球头凸模的翻边力 可按下式计算:
式中
F 1.2K 0Dt b (N)
(5-21)
式中 K0——翻边力系数,见表5-6; ——板料抗拉强度 (MPa)。
b
5.2 翻边
• 四、翻孔模设计 (一)翻孔模结构类型 翻孔模的结构与拉深模相似,也有顺 装与倒装、压边与不压边等区分。像拉深 模那样,如果没有冲裁加工,翻孔模一般 不需设置模架。 图5-18所示为倒装式翻孔模。 图5-19所示为顺装式翻孔模。
5.2 翻边
4.翻边凸模的形状: 图5-12所示为用平头凸模翻边,当凸模圆角 半径rp较小时,变形过分集中于底孔边缘,容易 引起开裂。随着值的增大,直至采用球形、抛 物面形或锥形凸模,变形将得到分散,可减小 底孔边缘开裂的可能性,因而允许采用较小的 翻边系数。 表5-4给出了低碳钢的极限翻边系数Kfmin , 从中可以看出上述因素对其值的影响程度。
5.2 翻边
2.底孔的断面质量: 由于翻孔的破坏形式是底孔边缘因拉伸变形过 大而开裂,因此用钻孔代替冲孔,或冲孔后再 用整修方法去掉毛刺和表面硬化层,或冲孔后 采取软化热处理措施,都能提高翻孔的极限变 形程度,允许采用较小的翻边系数。 3.板料的相对厚度 底孔直径d0与板料厚度t的比值d0 /t较小时,表 明板料较厚,断裂前材料的绝对伸长量可以大 些,故翻边系数可相应减小些。
翻边与弯曲不同,弯曲主要是折弯线为直线,切向没有变形, 而翻边时的折弯线为曲线,切向有变形,并且常常是主要的变 形。
5.2 翻边
5.2.1内缘翻边 一、圆孔翻边 (一) 圆孔翻边的变形特点
图5-12 圆孔翻边应力状态
图5-13 圆孔翻边应力—应变分布
5.2 翻边
如图5-12所示, 翻边变形区切向受拉应力σ θ ,径向 受拉应力σ P,而板厚方向应力可忽略不计,因此应力状 态可视为双向受拉的平面应力状态。 圆孔翻边时,应力和切向应变的分布情况如图5-13所 示。切向应力σ θ 为最大主应力,径向应力σ P是由凸模对 板料的摩擦作用引起的,其值较小。应力沿径向的分布是 不均匀的,在底孔边缘处,切向应力σ θ 达到其最大值, 而径向应力σ P为零,因此该处可视为单向拉伸应力状态。 切向应变为拉应变,沿径向的分布也是不均匀的,在底孔 边缘处其值最大,越远离中心,其值越小。 可见,翻孔时底孔边缘受到强烈的拉伸作用。变形程 度过大时,在底孔边缘很容易出现裂口。因此翻孔的破坏 形式就是底孔边缘拉裂。为了防止出现裂纹,需限制翻孔 的变形程度。
d 0 D 2H 0.43rd 0.72t
(5-11)
变换上式,可得翻边高度的计算公式: H=0.5D(1-d0/D )+0.43 rd +0.72t 或 H=0.5D(1-kf )+ 0.43 rd +0.72 t (5-12) 将上式中的翻边系数以极限翻边系数Kfmin代替, 可得最大翻边高度Hmax的计算公式:
5.2 翻边
利用模具将工序件的孔边缘或外边缘翻成竖直的直边, 称为翻边。利用翻边方法加工立体零件具有很好的刚性, 这一点常常是翻边加工的主要目的。 对工件的孔进行翻边称为内缘翻边,或简称为翻孔, 见图5 -11a。对工件的外缘进行翻边称为外缘翻边,见图 5 - 1lb。
ቤተ መጻሕፍቲ ባይዱ
a) 内缘翻边 b) 外缘翻边 图5-11 内缘和外缘翻边
图5-20 常用翻孔凸模形状
5.2 翻边
• 图a为平头凸模,圆角半径不宜过小,适于翻边高度较小、 直径较大的孔翻边。图b为球头凸模,图c为抛物面形凸模。 就对翻边变形而言,b优于a,c优于b,因而允许采用较小 的翻边系数,可比平头凸模减小10%~20%,但凸模的加 工难度则正好相反。采用以上三种翻边凸模,工件需有预 制底孔,而且翻边模上需设置定位装置,对工序件进行定 位。 • 图d和图e分别为带有球头和锥头导向段的台阶式凸模,用 于倒装式翻孔模时,可利用导引段对工序件底孔进行定位, 因此模具上不需设置定位装置。锥头凸模比球头凸模容易 加工,锥角可按板料厚度选取,当t<1.5mm时,取a=550, t>1.5mm时,取a=600 。 • 图f为尖锥形凸模,用于薄料、小孔的翻边,不需预先制 备底孔。但翻边后直壁端头有裂口,对直壁要求严格时不 能采用。
5.2 翻边
三、翻边力的计算 用普通圆柱形凸模翻孔时的翻边力,可按下式估 算: F 1.1 D d 0 t s (N) (5-20) 式中 D——翻边后孔的中径(mm) d0——翻边底孔直径(mm); T ——板料厚度(mm); s ——板料屈服应力(MPa)。
b
5.2 翻边
5.2 翻边
Hmax=0.5D(1- Kfmin )+0.43 rd +0.72t (5-13)
如果翻边直壁高度H小于一次翻边的极限高度 Hmax,则只要算出预孔直径d0,按d0冲预孔后就 可以直接达到翻边高度。 如果翻边件直壁的高度超过了一次翻边极限高 度,则该件便不能一次完成翻边。这时,可采取多 次翻边(两次之间可安排退火软化工序)、对变形区 进行加热翻边等工艺方法。当翻边件直壁高度较大 时,比较好的工艺方法是先用平板毛坯拉深成带宽 凸缘的圆筒形件,在底部冲底孔后再进行翻边,使 翻出的直径与拉深件直径相同,以达到要求的翻边 高度。具体计算如下。
5.2 翻边
(二) 圆孔翻边的变形程度 圆孔翻边的变形程度用翻边系数Kf表示:
Kf d0 D
(5-9)
D——翻边后孔的中径。 显然,Kf值越小,表示变形程度越大。各种材料 的首次翻边系数Kf0和极限翻边系数Kfmin见表5-3。 采用Kfmin值时,翻孔后的边缘可能有不大的裂口。