变速器外文翻译
变速器介绍外文文献翻译、中英文翻译、外文翻译

附录附录A 英文文献Transmission descriptionTransmission gearbox's function the engine's output rotational speed is high, the maximum work rate and the maximum torque appears in certain rotational speed area. In order to display engine's optimum performance, must have a set of variable speed gear, is coordinated the engine the rotational speed and wheel's actual moving velocity. The transmission gearbox may in the automobile travel process, has the different gear ratio between the engine and the wheel, through shifts gears may cause the engine work under its best power performance condition. Transmission gearbox's trend of development is more and more complex, the automaticity is also getting higher and higher, the automatic transmission will be future mainstream.Automotive Transmission's mission is to transfer power, and in the process of dynamic change in the transmission gear ratio in order to adjust or change the characteristics of the engine, at the same time through the transmission to adapt to different driving requirements. This shows that the transmission lines in the automotive transmission plays a crucial role. With the rapid development of science and technology, people's car is getting higher and higher performance requirements, vehicle performance, life, energy consumption, such as vibration and noise transmission depends largely on the performance, it is necessary to attach importance to the study of transmission.Transmission gearbox's pattern the automobile automatic transmission common to have three patterns: Respectively is hydraulic automatic transmission gearbox (AT), machinery stepless automatic transmission (CVT), electrically controlled machinery automatic transmission (AMT). At present what applies is most widespread is, AT becomes automatic transmission's pronoun nearly.AT is by the fluid strength torque converter, the planet gear and the hydraulic control system is composed, combines the way through the fluid strength transmission and the gear to realize the speed change bending moment. And the fluid strength torque converter is the most important part, it by components and so on pump pulley, turbine wheel and guide pulley is composed, has at the same time the transmission torque and the meeting and parting function.And AT compare, CVT has omitted complex and the unwieldy gear combination variable transmission, but is two groups of band pulleys carries on the variable transmission. Through changes the driving gear and the driven wheel transmission belt's contact radius carries on the speed change. Because has cancelled the gear drive, therefore its velocity ratio may change at will, the speed change is smoother, has not shifted gears kicks the feeling.AMT and the hydraulic automatic transmission gearbox (AT) is the having steps automatic transmission equally. It in the ordinary manual transmission gearbox's foundation, through installs the electrically operated installment which the microcomputer controls, the substitution originally coupling's separation which, the joint and the transmission gearbox completes by the manual control elects to keep off, to shift gears the movement, realizes fluid drive.Manual transmission gear mainly uses the principle of deceleration. Transmission within the group have different transmission ratio gear pair, and the car at the time of shift work, that is, through the manipulation of institutions so that the different transmission gear pair work. Manual transmission, also known as manual gear transmission, with axial sliding in the gears, the meshing gears through different speed to achieve the purpose of torque variation. Manual shift transmission can operate in full compliance with the will of the driver, and the simple structure, the failure rate is relatively low, value for money.Automatic transmission is based on speed and load (throttle pedal travel) fortwo-parameter control gear in accordance with the above two parameters to automatically take-off and landing. Automatic transmission and manual transmission in common, that is, there are two-stage transmission, automatic transmission can only speed the pace to automatically shift, manual transmission can be eliminated, "setback" of the shift feel.Automatic transmission is a torque converter, planetary gears and hydraulic manipulation of bodies, through the hydraulic transmission and gear combination to achieve the purpose of variable-speed torque variation.Also known as CVT-type continuously variable CVT. This transmission and automatic transmission gear generally the biggest difference is that it eliminates the need of complex and cumbersome combination of variable-speed gear transmission, and only two groups to carry out variable-speed drive pulley.CVT transmission than the traditional structure of simple, smaller and it is not the number of manual gear transmission, no automatic transmission planetary gear complex group, mainly rely on the driving wheel, the driven wheel and the transmission ratio brought about by the realization of non-class change.Widely used in automotive internal combustion engine as a power source, the torque and speed range is very small, and complex conditions require the use of motor vehicles and the speed of the driving force in the considerable changes in the scope. To resolve this contradiction, in the transmission system to set up the transmission to change transmission ratio, the expansion of the driving wheel torque and speed range in order to adapt to constantly changing traffic conditions, such as start, acceleration, climbing and so on, while the engine in the most favorable conditions to work under the scope; in the same direction of rotation of the engine under the premise of the automobile can be driven back; the use of neutral, interruption of power transmission, in order to be able to start the engine, idle speed, and ease of transmission or power shift . Transmission is designed to meet the above requirements, so that the conditions in a particular vehicle stability.In addition to transmission can be used to meet certain requirements, but also to ensure that it and the car can have a good match, and can improve the car's power andeconomy to ensure that the engine in a favorable condition to increase the scope of the work of the use of motor vehicles life, reduce energy consumption, reduce noise, such as the use of motor vehicles.Today the world's major car companies CVT are very active in the study. The near future, with electronic control technology to further improve, electronically controlled Continuously Variable Transmission-type is expected to be a wide range of development and application.附录B 文献翻译变速器介绍发动机的输出转速非常高,最大功率及最大扭矩在一定的转速区出现。
汽车变速器外文翻译
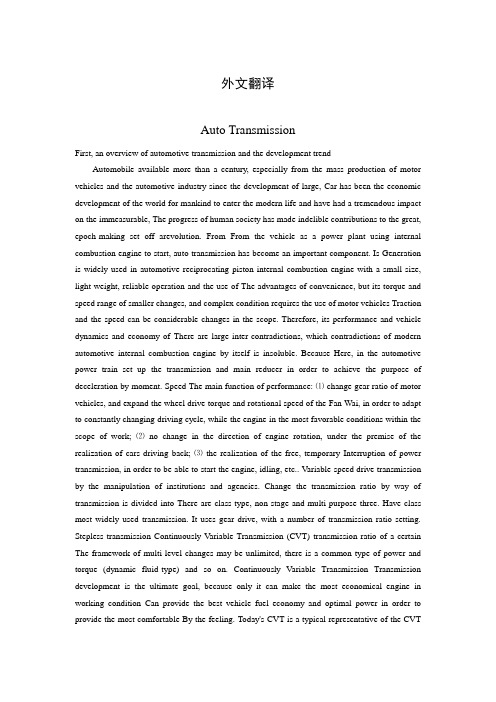
外文翻译Auto TransmissionFirst, an overview of automotive transmission and the development trendAutomobile available more than a century, especially from the mass production of motor vehicles and the automotive industry since the development of large, Car has been the economic development of the world for mankind to enter the modern life and have had a tremendous impact on the immeasurable, The progress of human society has made indelible contributions to the great, epoch-making set off arevolution. From From the vehicle as a power plant using internal combustion engine to start, auto transmission has become an important component. Is Generation is widely used in automotive reciprocating piston internal combustion engine with a small size, light weight, reliable operation and the use of The advantages of convenience, but its torque and speed range of smaller changes, and complex condition requires the use of motor vehicles Traction and the speed can be considerable changes in the scope. Therefore, its performance and vehicle dynamics and economy of There are large inter-contradictions, which contradictions of modern automotive internal combustion engine by itself is insoluble. Because Here, in the automotive power train set up the transmission and main reducer in order to achieve the purpose of deceleration by moment. Speed The main function of performance: ⑴ change gear ratio of motor vehicles, and expand the wheel drive torque and rotational speed of the Fan Wai, in order to adapt to constantly changing driving cycle, while the engine in the most favorable conditions within the scope of work; ⑵no change in the direction of engine rotation, under the premise of the realization of cars driving back; ⑶the realization of the free, temporary Interruption of power transmission, in order to be able to start the engine, idling, etc.. V ariable-speed drive transmission by the manipulation of institutions and agencies. Change the transmission ratio by way of transmission is divided into There are class-type, non-stage and multi-purpose three. Have class most widely used transmission. It uses gear drive, with a number of transmission ratio setting. Stepless transmission Continuously V ariable Transmission (CVT) transmission ratio of a certain The framework of multi-level changes may be unlimited, there is a common type of power and torque (dynamic fluid-type) and so on. Continuously V ariable Transmission Transmission development is the ultimate goal, because only it can make the most economical engine in working condition Can provide the best vehicle fuel economy and optimal power in order to provide the most comfortable By the feeling. Today's CVT is a typical representative of the CVTand IVT, however as a result of the reliability of Poor, non-durable materials and high cost issues, development is not very good. Comprehensive refers to transmission torque converter and the mechanical components have the level of transmission variable hydraulic mechanical Speed, the transmission ratio can be between the maximum and minimum range of a few discontinuous change for no class, but its Significantly lower transmission efficiency than the efficiency of gear drives. 2 By manipulation, transmission control type can be divided into mandatory, automatic and semi-automatic control to manipulate three - Species . Mandatory on the driver to manipulate the direct transmission gear shift control for the majority of motor vehicles used Also known as Manual Transmission Manual Transmission (MT). Automatic transmission control selection of the transmission ratio (transmission) is carried out automatically. Just add the driver to manipulate Speed pedal, you can control the speed, also known as Automatic Transmission Automatic Transmission (A T). It is According to the speed and load (throttle pedal travel) for two-parameter control, stall in accordance with the above two Parameters to automatically take-off and landing.A T and MT in common is that they are level transmission, but A T According to the speed of the speed shift automatically, you can eliminate the manual transmission "setback" of the shift feel. However, A T also have many drawbacks, such as body complex, mechanical efficiency is not high, high cost, reliability and control Sensitivity remains to be increasing . AMT (Automated Mechanical Transmission) is in the traditional dry clutch and manual transmission gear based on the transformation of form, mainly to change the part of the manual gearshift control. That is, the overall structure of the MT cases the same switch to electronically controlled automatic transmission to achieve. Semi-automatic control, there are two forms of transmission. A number of stalls is a common automatic control, and the remaining stalls manipulated by the driver; the other is pre-style, that is, pre-selected pilot stalls, the clutch pedal in the down or release the accelerator pedal, the for retirement or an electromagnetic device to shift the hydraulic device. In recent years, with advances in vehicle technology and road traffic density increased, the performance requirements of the transmission is also getting higher and higher. A large number of automotive engineers in improving the performance of automobile transmission study a great deal of effort devoted to the rapid transmission of technology development, such as A T, AMT, DCT, CVT and the emergence of IVT.2003 Hyundai A T, AMT, DCT, CVT forum reached a consensus on the following:in the next Development, MT will continue to be the most widely used automotive transmission, AMT will increase the proportion of the application, A T also Will occupy a large market share, CVT's use of certain limitations, can only be due to a number of small displacement Car, DCT (dual clutch transmission) will also be the budding growth. From 2003 to now, vehicle speed Thedevelopment of devices and the forum basically the consensus reached by consensus. By comparing the analysis, the traditional mechanical transmission is still the most widely used vehicle change Speed. Although it has many shortcomings, such as shifting the impact of large, bulky, cumbersome to manipulate and so on; however, it also There are many advantages, such as high transmission efficiency, reliable operation, long life, manufacturing processes mature and low cost. Therefore, if we can improve the mechanical transmission of the above-mentioned shortcomings, it still has great room for development.Second, Manual Transmission Fault DiagnosisManual transmission at the beginning of the fault diagnosis prior toFailure to confirm from other parts is not: to check the tire And wheels, to confirm the normal tire pressure, and the wheel is flat V alue of; to confirm instead of noise and vibration from the engine. Clutch , And steering and suspension, etc..(A), skip file1. PhenomenonV ehicle acceleration, deceleration, climbing or severe vehicle vibration, the gear lever neutral position automatically jump.2. Reasons① self-locking device of the ball did not enter the grooves or linked file does not meet the full-gear tooth meshing long;② self-locking device worn groove ball or serious, self-locking spring is too soft or broken fatigue;③ gear along the direction of tooth wear as a long cone-shaped;④ one or two too松旷shaft bearing, so that one or two three-axis and the crankshaft axis of the heart or different transmission and clutch shell shell bonding plane of the vertical axis the relative change in the crankshaft;⑤ Second Gear axis often axial or radial gap is too large;⑥ the axis of axial or radial gap is too large.3. Fault diagnosis and troubleshootingJump to file stalls Unascertained: After taking heat the entire vehicle, increase the use of continuous, slow approach to road test each file is determined.Will jump to the gear lever hanging file stalls the engine off, transmission cover removed carefully to observe the mating dance gear case file.① engagement does not meet the length, then the resulting fault;② to reach a total length of engagement, should continue to check;③ check mating wear parts: wear into a cone, then failure may be caused by;④ check b-axis of the gear profile and the axis of the axial and radial clearance, clearance is too large, then failure may be caused by;⑤ check self-locking devices, locking devices, if only a very small dynamic resistance, and even feel the ball is not plugged groove (the transmission cover caught in the vice, the hand-shaking shift stroke), the fault for the bad performance of self-locking ; Otherwise, the fault for the clutch and gearbox shell bonding plane and the vertical axis of the crankshaft caused by changes.(B), arbitrary files1. PhenomenonTechnical condition in the clutch normal circumstances, transmission at the same time put up or two files linked to the need to stall, the results linked to other stalls.2. Reasons① interlocking device failure: if the fork shaft, pin or interlocking interlocking ball too much wear and tear, etc.;② the bottom of the arc gear face wear and tear is too large or fork axis of the allocated blocks wear groove is too large;③ball pin gear lever broken or the ball-hole, ball松旷wear too. In short arbitrary file transmission is mainly due to institutional failure manipulation.3. Fault diagnosis and troubleshooting① linked to the need to stall, the results linked to the other stalls: rocking gear lever, to check their point of view before, if in excess of the normal range, while the lower end of failure by the gear lever ball pin and the positioning groove ball with or松旷, the ball is too large holes caused by wear and tear. Swung shift 360 °, compared with a broken pin.② If the pendulum angle to normal, still not on, or linked to more than picking file, then the lower end of failure by the gear lever away from the limitations arising from the groove in (due to break away from the bottom of the arc-shaped guide groove face wear and tear or wear).③ At the same time linked to the two files: the fault caused by the interlocking device failure.(C), the difficulties linked to files1. PhenomenonClutch technical condition, but can not be linked smoothly linked file into the stalls, often percussive sound gear.2. Reasons① synchronizer failure;② Bending fork shaft, locking the spring strong, ball injury, etc.;③ a shaft or a spline shaft bending injury;④ inadequate or excessive gear oil, gear oil does not meet the specifications.3. Fault diagnosis and troubleshooting①Synchronizer check whether the fall to pieces, cone ring is conical spiral groove wear, whether worn slider, spring is too soft, such as elastic.② If the Synchronizer normal, check whether the bending of a shaft, spline wear is severe.③ check whether the mobile axis normal fork.(D), abnormal sound transmission1. PhenomenonTransmission refers to transmission work abnormal sound when the sound is not normal.2. Reasons1) abnormal sound gearGear wear off very thin gap is too large, the impact of running in; bad tooth meshing, such as the repair did not replace the gear pairs. New and old gear with the gear mesh can not be correct; tooth metal fatigue spalling or damage to individual teeth broken; gear and the spline shaft with松旷, or the axial gear clearance is too large; axis caused by bending or bearing松旷space to change gears.2) Bearing ringSerious bearing wear; Bearing (outer) ring with the journal blocks (holes) with the loose; Ball Bearing Ma break-up or a point of ablation.3) ring made for other reasonsSuch as the transmission within缺油, lubricants have been thin, too thick or quality deterioration; transmission into the foreign body inside; some loose bolts fastening; odometer or the odometer shaft ring gear, such as fat.3. Troubleshooting①transmission issued metal dry friction sound, which is缺油and the poor quality of oil. Refueling and inspection should be the quality of oil, if necessary, replacement.② for moving into a file if the sound obvious, namely, the profile of gear tooth wear; If the occurrence of cyclical noise, while damage to individual teeth.③when the ring gap, and riding the clutch pedal under the noise disappeared after the general axis is a before and after the bearing or regular engagement ring gear; if any files are changed into the ring, after more than two-axis bearing ring.④transmission occurs when a sudden impact the work of sound, most of the tooth was broken and should be removed timely transmission inspection cover to prevent mechanicaldamage.⑤moving, only for transmission of a file into the ring gear made in the above-mentioned good premise, it should check with improper gear mesh, if necessary, should be re-assembling a pair of new gear. In addition, it may be synchronizer gear wear or damage should be repaired or replaced depending on the circumstances.⑥ when shifting gear ring made of impact, it may be the clutch or the clutch pedal can not be separated from stroke is incorrect, damaged synchronizer, excessive idling, gear improperly adjusted or tight-oriented, such as Bush. In such cases, to check whether the separation of the clutch, and then adjust the idle speed or the gear lever, respectively, the location, inspection-oriented with the bearing bushing and separation tightness.If excluded from the above examinations, the transmission is still made ring, should check the shaft bearings and shaft hole with the situation, bearing the state of their own technology, etc.; as well, and then view the odometer shaft and ring gear is made and, if necessary, be repaired or replacement.(E), transmission oil1. PhenomenonAround the transmission gear lubricants, transmission gear box to reduce the fuel can be judged as lubricant leakage.2. Reasons and troubleshooting① improper oil selection, resulting in excessive foam, or the volume too much oil, when in need of replacement or adjust the lubricant oil;② side cover is too loose, damaged gaskets, oil seal damage, damage to seals and oil seals should be replaced with new items;③ release and transmission oil tank and side cover fixed bolts loosening, tightening torque should be required;④ broken gear-housing shell or extended wear and tear caused by oil spills, must be replaced;⑤ odometer broken loose gear limit device must be locked or replaced; gear oil seal oil seal oil should be replaced.Third, the maintenance manual gearboxSantana is now as an example:Santana used to manually synchronize the entire, multi-stage gear transmission, there are four forward one block and reverse gear. Block are forward-lock synchronizer ring inertial, body-wide shift synchronizer nested engagement with a reasonable structure, the layout of a compact, reliable, long life and so on. However, if the use and maintenance is not the right way to do so, failure mayoccur at any time.The proper use of Synchronizer:1, the use of addition and subtraction block off both feet. Block addition and subtraction, if the clutch with one foot, then the speed at the time of addition and subtraction block must be correct, the timing should be appropriate and, if necessary, to addition and subtraction can be blocked off both feet, so that addition and subtraction method can reduce the block with Gear speed difference between the circumference, thereby reducing wear and tear Synchronizer to extend the life of Synchronizer.2, prohibited the use of tap-shift gear lever when the method (that is, a push of the operation of a song). Hand should always hold down the shift, this can greatly reduce the synchronizer sliding lock Moreton Central time and reduce wear and tear.3, no state in the gap off the use of force挂挡synchronizer start the engine. Moment of inertia as a great engine, the friction torque Synchronizer also small, so the time synchronization process is very long, so that lock ring temperature increased sharply, it is easy to burn synchronizer.4, is strictly prohibited by synchronizer clutch instead of the initial (that is, the use of non-use of the clutch friction synchronizer start挂挡role), control speed and braking.The correct use of lubricants:Santana at the factory, the transmission has been added to the quality of lubricating oil, under normal circumstances, the level of the transmission lubrication need to be checked. However, when normal travel 100,000 kilometers 10,000 kilometers -20 after the first lubricating oil must be replaced. Santana grade lubricants used in transmission as follows: Gear Oil API-GLA (MIL-L2105), SAE80 or SAE80W-90 grade汽车变速器一、汽车变速器概述及发展趋势汽车问世百余年来,特别是从汽车的大批量生产及汽车工业的大发展以来,汽车己为世界经济的发展、为人类进入现代生活,产生了无法估量的巨大影响,为人类社会的进步作出了不可磨灭的巨大贡献,掀起了一场划时代的革命。
变速器外文资料翻译
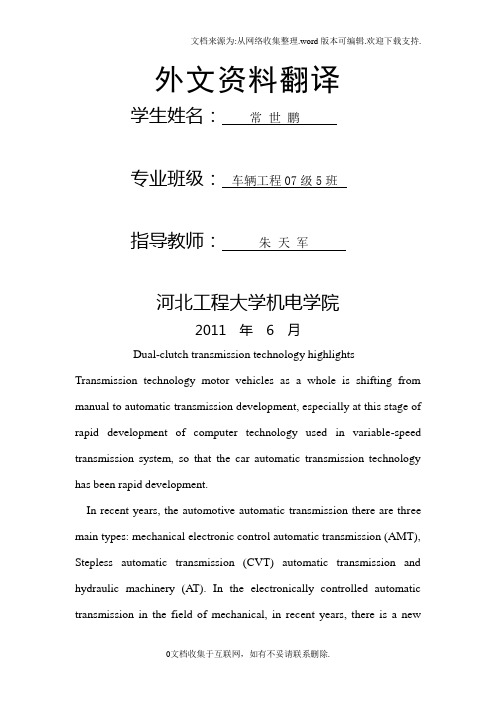
变速器英文缩写

本标准对汽车液力变速器常用结构的名称和技术术语给予定义。
1液力变速器Hydrodynamic transmission采用液力偶合器或液力变扭器的变速器。
1.1自动液力变速器Autom at ic transmission自动实现换档的液力变速器。
1.2半自动液力变速器Semiautomatic transmission部分换档功能是自动实现的液力变速器。
1.3人工换档液力变速器Manually shifted transmission人工操作实现换档的液力变速器。
1.4分流式液力变速器Split torque drive transmission从输入端到输出端具有两条或两条以上功率流的液力变速器。
1.5定轴式液力变速器Countershaft transmission采用固定轴线齿轮机构的液力变速器。
1.6行星式液力变速器Planetary transmission采用行星齿轮机构的液力变速器。
2液力传动Hydrodynamic drive在两个或两个以上叶轮组成的封闭循环流道中,通过液体动量矩的变化来传递扭矩的传动。
2.1液力传动装置Hydrodynamic unit指液力偶合器、液力变扭器。
2.1.1液力偶合器Fluid coupling不改变所传递扭矩的液力传功装置。
(在各种变速比下,变扭比均相同)。
见图1。
2.1.2液力变扭器Torque converter能改变所传递扭矩的液力传动装置。
(变扭比是速比的函数2.1.2.1锁止式液力变扭器Lock—Up torque converter装有锁止离合器的液力变扭器。
2.1.2.2变容式液力变扭器Variable capacity converter可改变自身能容的液力变扭器。
2.2液力减速器Hydraulic retarder降低车速的液力辅助装置。
2.3单向离合器One—way clutch一个方向传递扭矩,其反向允许自由转动的机械装置,见图2。
汽车变速器英语词汇

(副变速器)变速杆range selector按钮控制finger-tip control半自动换档机械式变速器semi-automatic mechanical transmission 半自动液力变速器semiautomatic transmission包角scroll泵轮impeller边斜角(进出口)bias(entrance and exit)变矩比torque ratio变矩范围torque conversion range变矩系数torque ratio变容式液力变矩器variable capacity converter变速叉shifting fork (gear shift fork)变速齿轮transmission gear变速齿轮比(变速比)transmission gear ratio变速齿轮组change gear set变速杆stick shift(gear shift lever)变速轨(拨叉道轨)shift rail变速器transmission (gearbox)变速器输出轴transmission output shaft变速器输入轴transmission input shaft变速器中间轴transmission countershaft变速器轴的刚度rigidity of shaft变速器主动齿轮轴transmission drive gear shaft变速器主轴transmission main shaft变速踏板gear shift pedal操纵杆control lever槽导变速gate change长行星齿轮long planet gear常啮齿轮constant mesh gear常啮合齿轮传动constant mesh transmission常压式同步器constant pressure synchronizer超速档变速器over drive transmission超限换档overrun shift传动比gear ratio带主减速器的变速器final driving transmission单向离合器one-way clutch单向离合器换档freewheel shift导轮可反转的变矩器torque converter with reversal reactor 倒档reverse gear倒档中间齿轮reverse idler gear低速档bottom gear(low speed gear)第二档second gear第一档first gear电磁阀调压阀solenoid regulator valve电液式自动换档系统electronic -hydraulic automatic电子同步变速装置electronically synchronized transmission assembly 调压阀pressure -regulator valve调制压力modulated pressure定输入扭矩特性constant input torque performance定轴式液力变速器countershaft transmission定子stator动力换档power shift动力换档过程timing动力相似dynamic similarity动力助力换档变速器power assisted shift transmission短行星齿轮short planet gear多级变速器multi-speed transmission多中间轴变速器multi-countershaft transmission反拖特性coast performance方向盘式变速column shift (handle change)分动齿轮(分动机构)transfer gear分动箱(分动器)transfer case分动箱控制杆transfer gear shift fork分段式多档变速器sectional type multi-speed transmission分流式液力变速器split torque drive transmission辅助变速器auxiliary gear box副变速器splitter副轴counter shaft副轴齿轮counter shaft gear高速档top gear(high gear)固定轴式变速器fixed shaft transmission 惯性式同步器inertial type of synchronizer 过载系数overloading ratio后油泵gear pump (output pump )滑差slip滑动齿轮sliding gear滑动齿轮变速器sliding gear transmission 滑动齿轮传动sliding -gear transmission 缓冲压力compensator or trimmer pressure 换档shift换档点shift point换档定时property of automatic shift换档阀shift valve换档规律process of power shift换档机构gearshift换档循环shift schedule换档元件engaging element换档指令发生器shift pattern generator回油泵scavenge oil pump机械式变速器mechanical transmission 级stage几何相似geometry similarity继动阀relay valve。
变速器外文翻译

Continuously Variable Transmissions An Overview of CVT Research Past, Present, and FutureKevin R. Lang21W. 732May 3, 2000Table of Contents Introduction (1)CVT Theory & Design (2)Push Belt (2)Toroidal Traction Drive (2)Variable Diameter Elastomer Belt (3)Other CVT Varieties (3)Background & History (3)Inherent Advantages & Benefits (4)Challenges & Limitations (5)Research & Development (6)New CVT Research (7)Future Prospects for CVTs (9)CVTs & Hybrid Electric Vehicles (9)Conclusion (10)Works Cited (11)Figures and TablesFigure 1 – Metal Push Belt CVT (2)Figure 2 – Toroidal CVT (2)Figure 3 – Variable Diameter Belt CVT (3)Figure 4 – GM’s New CVT Design (6)Figure 5 – Audi CVT with link chain (6)Figure 6 – Cutaway of Audi CVT (7)Table 1 – Efficiency vs. Gear Ratio for Automatic Transmission (4)Table 2 – Efficiency of Various CVT Designs (4)AbstractAs the U.S. government enacts new regulations for automotive fuel economy and emissions, the continuously variable transmission, or CVT, continues to emerge as a key technology for improving the fuel efficiency of automobiles with internal combustion (IC) engines. CVTs use infinitely adjustable drive ratios instead of discrete gears to attain optimal engine performance. Since the engine always runs at the most efficient number of revolutions per minute for a given vehicle speed, CVT-equipped vehicles attain better gas mileage and acceleration than cars with traditional transmissions.CVTs are not new to the automotive world, but their torque capabilities and reliability have been limited in the past. New developments in gear reduction and manufacturing have led to ever-more-robust CVTs, which in turn allows them to be used in more diverse automotive applications. CVTs are also being developed in conjunction with hybrid electric vehicles. As CVT development continues, costs will be reduced further and performance will continue to increase, which in turn makes further development and application of CVT technology desirable.This paper evaluates the current state of CVTs and upcoming research and development, set in the context of past development and problems traditionally associated with CVTs. The underlying theories and mechanisms are also discussed.IntroductionAfter more than a century of research and development, the internal combustion (IC) engine is nearing both perfection and obsolescence: engineers continue to explore the outer limits of IC efficiency and performance, but advancements in fuel economy and emissions have effectively stalled. While many IC vehicles meet Low Emissions Vehicle standards, these will give way to new, stricter government regulations in the very near future. With limited room for improvement, automobile manufacturers have begun full-scale development of alternative power vehicles. Still, manufacturers are loath to scrap a century of development and billions or possibly even trillions of dollars in IC infrastructure, especially for technologies with no history of commercial success. Thus, the ideal interim solution is to further optimize the overall efficiency of IC vehicles.One potential solution to this fuel economy dilemma is the continuously variable transmission (CVT), an old idea that has only recently become a bastion of hope to automakers. CVTs could potentially allow IC vehicles to meet the first wave of new fuel regulations while development of hybrid electric and fuel cell vehicles continues. Rather than selecting one of four or five gears, a CVT constantly changes its gear ratio to optimize engine efficiency with a perfectly smooth torque-speed curve. This improves both gas mileage and acceleration compared to traditional transmissions.The fundamental theory behind CVTs has undeniable potential, but lax fuel regulations and booming sales in recent years have given manufacturers a sense of complacency: if consumers are buying millions of cars with conventional transmissions, why spend billions to develop and manufacture CVTs? Although CVTs have been used in automobiles for decades, limited torque capabilities and questionable reliability have inhibited their growth. Today, however, ongoing CVT research has led to ever-more-robust transmissions, and thus ever-more-diverse automotive applications. As CVT development continues, manufacturing costs will be further reduced and performance will continue to increase, which will in turn increase the demand for further development. This cycle of improvement will ultimately give CVTs a solid foundation in the world’s automotive infrastructure.Figure (1) – Metal Push Belt CVTFrom [3]Figure (2) – Toroidal CVTFrom [3]CVT Theory & DesignToday’s automobiles almost exclusively use either a conventional manual or automatictransmission with “multiple planetary gear sets that use integral clutches and bands to achieve discrete gear ratios” [3]. A typical automatic uses four or five such gears, while a manual normally employs five or six. The continuously variable transmission replaces discrete gear ratios with infinitely adjustable gearing through one of several basic CVT designs.Push BeltThis most common type of CVT usessegmented steel blocks stacked on a steel ribbon, asshown in Figure (1). This belt transmits powerbetween two conical pulleys, or sheaves, one fixedand one movable [3]. With a belt drive:In essence, a sensor reads the engine output and then electronically increases or decreases thedistance between pulleys, and thus the tension of the drive belt. The continuously changing distance between the pulleys—their ratio to one another—is analogous to shifting gears. [6]Push-belt CVTs were first developed decades ago, but new advances in belt design have recently drawn the attention of automakers worldwide.Toroidal Traction-DriveThese transmissions use the high shear strength of viscousfluids to transmit torque between an input torus and an outputtorus. As the movable torus slides linearly, the angle of a rollerchanges relative to shaft position, as seen in Figure (2). Thisresults in a change in gear ratio [3].Variable Diameter Elastomer BeltThis type of CVT, as represented in Figure (2), usesa flat, flexible belt mounted on movable supports. Thesesupports can change radius and thus gear ratio. However,the supports separate at high gear ratios to form adiscontinuous gear path, as seen in Figure (3). This can lead to the problems with creep and slip that have plagued CVTs for years [3]. This inherent flaw has directed research and development toward push belt CVTs.Other CVT VarietiesSeveral other types of CVTs have been developed over the course of automotive history, butthese have become less prominent than push belt and toroidal CVTs. A nutating traction drive uses a pivoting, conical shaft to change “gears” in a CVT. As the cones change angle, the inlet radius decreases while the outlet radius increases, or vice versa, resulting in an infinitely variable gear ratio [3]. A variable geometry CVT uses adjustable planetary gearsets to change gear ratios, but this is more akin to a flexible traditional transmission than a conventional CVT.Background & HistoryTo say that the continuously variable transmission (CVT) is nothing new would be a grossunderstatement: Leonardo da Vinci sketched his idea for a CVT in 1490 [1]. In automotive applications,CVTs have been around nearly as long as cars themselves, and certainly as long as conventionalautomatics. General Motors actually developed a fully toroidal CVT in the early 1930s and conducted extensive testing before eventually deciding to implement a conventional, stepped-gear automatic due to cost concerns. General Motors Research worked on CVTs again in the 1960s, but none ever sawproduction [2]. British manufacturer Austin used a CVT for several years in one of its smaller cars, but “it was dropped due to its high cost, poor reliability, and inadequate torque transmission” [2]. Many early CVTs used a simple rubber band and cone system, like the one developed by Dutch firm Daf in 1958 [1].Figure (3) – Variable Diameter Belt CVTFrom [3]However, the Daf CVT could only handle a 0.6 L engine, and problems with noise and rough starts hurt its reputation [1]. Uninspired by these early failures, automakers have largely avoided CVTs until very recently, especially in the United States.Inherent Advantages & BenefitsCertainly, the clunk of a shifting transmission is familiar to all drivers. By contrast, a continuously variable transmission is perfectly smooth—it naturally changes “gears” discreetly and minutely such that the driver or passenger feels only steady acceleration. In theory, a CVT would cause less engine fatigue and would be a more reliable transmission, as the harshness of shifts and discrete gears force the engine to run at a less-than-optimal speed.Moreover, CVTs offer improved efficiency and performance. Table (1) below shows the power transmission efficiency of a typical five-speed automatic, i.e. the percentage of engine power translated through the transmission. This yields an average efficiency of 86%, compared to a typical manual transmission with 97% efficiency [3]. By comparison, Table (2) below gives efficiency ranges for several CVT designs.Table (1) Efficiency vs. Gear Ratio for Automatic Transmission [3] Gear Efficiency Range160-85%260-90%385-95%490-95%585-94%Table (2) Efficiency of Various CVT Designs [3] CVT Mechanism Efficiency Range Rubber Belts90-95%Steel Belts90-97%Toroidal Traction70-94%Nutating Traction75-96%Variable Geometry85-93%These CVTs each offer improved efficiency over conventional automatic transmissions, and their efficiency depends less on driving habit than manual transmissions [3]. Moreover:Because the CVT allows an engine to run at this most efficient point virtuallyindependent of vehicle speed, a CVT equipped vehicle yields fuel economy benefitswhen compared to a conventional transmission (3)Testing by ZF Getriebe GmbH several years ago found that “the CVT uses at least 10% less fuel than a 4-speed automatic transmission” for U.S. Environmental Protection Agency city and highway cycles. Moreover, the CVT was more than one second faster in 0-60 mph acceleration tests [5]. The potential for fuel efficiency gains can also be seen in the CVT currently used in Honda’s Civic. A Civic with atraditional automatic averages 28/35 miles per gallon (mpg) city/highway, while the same car with a CVT gets 34/38 mpg city/highway [4]. Honda has used continuously variable transmissions in the Civic for several years, but these are 1.6 liter cars with limited torque capabilities. Ongoing research and development will inevitably expand the applicability of CVTs to a much broader range of engines and automobiles.Challenges & LimitationsCVT development has progressed slowly for a variety of reasons, but much of the delay in development can be attributed to a lack of demand: conventional manual and automatic transmissions have long offered sufficient performance and fuel economy. Thus, problems encountered in CVT development usually stopped said progress. “Designers have … unsuccessfully tried to develop [a CVT] that can match the torque capacity, efficiency, size, weight, and manufacturing cost of step-ratio transmissions” [6].One of the major complaints with previous CVTs has been slippage in the drive belt or rollers. This is caused by the lack of discrete gear teeth, which form a rigid mechanical connection between to gears; friction drives are inherently prone to slip, especially at high torque. With early CVTs of the 1950s and 1960s, engines equipped with CVTs would run at excessively high RPM trying to “catch up” to the slipping belt. This would occur any time the vehicle was accelerated from a stop at peak torque:“For compressive belts, in the process of transmitting torque, micro slip occurs betweenthe elements and the pulleys. This micro slip tends to increase sharply once thetransmitted torque exceeds a certain value …” [8]For many years, the simple solution to this problem has been to use CVTs only in cars with relativelylow-torque engines. Another solution is to employ a torque converter (such as those used in conventional automatics), but this reduces the CVT’s efficiency [2].Perhaps more than anything else, CVT development has been hindered by cost. Low volume and a lack of infrastructure have driven up manufacturing costs, which inevitably yield higher transmission prices. With increased development, most of these problems can be addressed simply by improvements in manufacturing techniques and materials processing. For example, Nissan’s Extroid “is derived from aFigure (4) – GM’s New CVT designFrom [6]Figure (5) – Audi CVT with link chainFrom [1]century-old concept, perfected by modern technology, metallurgy, chemistry, electronics, engineering,and precision manufacturing” [2].In addition, CVT control must be addressed. Even if a CVT can operate at the optimal gear ratio at any speed, how does it “know” what ratio to select? Manual transmissions have manual controls,where the driver shifts when he or she so desires; automatic transmissions have relatively simple shifting algorithms to accommodate between three and five gears. However, CVTs require far more complex algorithms to accommodate an infinite division of speeds and gear ratios.Research & DevelopmentWhile IC development has slowed in recent years asautomobile manufacturers devote more resources to hybrid electricvehicles (HEVs) and fuel cell vehicles (FEVs), CVT research anddevelopment is expanding quickly. Even U.S. automakers, who havelagged in CVT research until recently, are unveiling new designs:General Motors plans to implement metal-belt CVTs in some vehiclesby 2002 [6].The Japanese and Germans continue to lead the way in CVT development. Nissan has taken a dramatic step with its “Extroid” CVT, offered in the home-market Cedric and Gloria luxury sedans. This toroidal CVT costs more than a conventional belt-driven CVT, but Nissan expects the extra cost to be absorbed by the luxury cars’ prices [2]. The Extroid uses a high viscosity fluid to transmit power between the disks and rollers, rather than metal-to-metal contact. Coupled with a torque converter, this yields“exceptionally fast ratio changes”. Most importantly, though, theExtroid is available with a turbocharged version of Nissan’s 3.0 literV6 producing 285 lb-ft of torque; this is a new record for CVTtorque capacity [2].Audi’s new CVT offers both better fuel mileage than a conventional automatic and better acceleration than even aFigure (6) – Cutaway of Audi CVT From [1]manual transmission. Moreover, Audi claims it can offer the CVT at only a slight price increase [1]. This so-called “multitronic” CVT uses an all-steel link plate chain instead of a V-belt in order to handle up to 280 lb-ft of torque [1]. In addition, “Audi claims that the multitronic A6accelerates from 0-100 km/h (0-62 mph) 1.3 s quicker than a gearedautomatic transmission and is 0.1 s quicker over the same speed than anequivalent model with “optimum” use of a five speed manual gearbox”[1]. If costs were sufficiently reduced, a transmission such as this couldbe used in almost any automobile in the world.Many small cars have used CVTs in recent years, and many more will use them in the near future. Nissan, Honda, and Subaru currently use belt-drive CVTsdeveloped with Dutch company Van Doorne Transmissie (VDT) in some of their smaller cars [7]. Suzuki and Daihatsu are jointly developing CVTs with Japanese company Aichi Machine, using analuminum/plastic composite belt reinforced with Aramid fibers. Their CVT uses an auxiliary transmission for starts to avoid low-speed slip. After about 6 mph, the CVT engages and operates as it normally would[7]. “The auxiliary geartrain’s direct coupling ensures sufficiently brisk takeoff and initial acceleration”[7]. However, Aichi’s CVT can only handle 52 lb-ft of torque. This alone effectively negates itspotential for the U.S. market. Still, there are far more CVTs in production for 2000 than for 1999, and each major automobile show brings more announcements for new CVTs.New CVT ResearchAs recently as 1997, CVT research focused on the basic issues of drive belt design and power transmission. Now, as belts by VDT and other companies become sufficiently efficient, research focuses primarily on control and implementation of CVTs.Nissan Motor Co. has been a leader in CVT research since the 1970s. A recent study analyzing the slip characteristics of a metal belt CVT resulted in a simulation method for slip limits and torque capabilities of CVTs [8]. This has led to a dramatic improvement in drive belt technology, since CVTs can now be modeled and analyzed with computer simulations, resulting in faster development and moreefficient design. Nissan’s research on the torque limits of belt-drive CVTs has also led to the use of torque converters, which several companies have since implemented. The torque converter is designed to allow “creep,” the slow speed at which automatic transmission cars drive without driver-induced acceleration. The torque converter adds “improved creep capability during idling for improved driveability at very low speeds and easy launch on uphill grades” [9]. Nissan’s Extroid uses such a torque converter for “smooth starting, vibration suppression, and creep characteristics” [2].CVT control has recently come to the forefront of research; even a mechanically perfect CVT is worthless without an intelligent active control algorithm. Optimal CVT performance demands integrated control, such as the system developed by Nissan to “obtain the demanded drive torque with optimum fuel economy” [13]. The control system determines the necessary CVT ratio based on a target torque, vehicle speed, and desired fuel economy. Honda has also developed an integrated control algorithm for its CVTs, considering not only the engine’s thermal efficiency but also work loss from drivetrain accessories and the transmission itself [12]. Testing of Honda’s algorithm with a prototype vehicle resulted in a one percent fuel economy increase compared to a conventional algorithm. While not a dramatic increase, Honda claims that its algorithm is fundamentally sound, and thus will it become “one of the basic technologies for the next generation’s powerplant control” [12].Although CVTs are currently in production, many control issues still amount to a “tremendous number of trials and errors” [10]. One study focusing on numerical representation of power transmission showed that “both block tilting and pulley deformation meaningfully effected the pulley thrust ratio between the driving and the driven pulleys” [10]. Thus, the resultant model of CVT performance can be used in future applications for transmission optimization. As more studies are conducted, fundamental research such as this will become the legacy of CVT design, and research can become more specialized as CVTs become more refined.As CVTs move from research and development to assembly line, manufacturing research becomes more important. CVTs require several crucial, high-tolerance components in order to function efficiently; Honda studied one of these, the pulley piston, in 1998. Honda found that prototype pistons“experienced a drastic thickness reduction (32% at maximum) due to the conventional stretch forming method” [11]. A four-step forming process was developed to ensure “a greater and more uniform thickness increase” and thus greater efficiency and performance. Moreover, work-hardening during the forming process further increased the pulley piston’s strength [11].Size and weight of CVTs has long been a concern, since conventional automatics weigh far more than manual transmissions and CVTs outweigh automatics. Most cars equipped with automatic transmissions have a curb weight between 50 and 150 pounds heavier than the same cars with manual transmissions. To solve this problem, Audi is currently developing magnesium gearbox housings, a first for cars in its class. This results in nearly a 16 pound weight reduction over conventional automatics. [1]. Future Prospects for CVTsMuch of the existing literature is quick to admit that the automotive industry lacks a broad knowledge base regarding CVTs. Whereas conventional transmissions have been continuously refined and improved since the very start of the 20th century, CVT development is only just beginning. As infrastructure is built up along with said knowledge base, CVTs will become ever-more prominent in the automotive landscape. Even today’s CVTs, which represent first-generation designs at best, outperform conventional transmissions. Automakers who fail to develop CVTs now, while the field is still in its infancy, risk being left behind as CVT development and implementation continues its exponential growth. Moreover, CVTs are do not fall exclusively in the realm of IC engines.CVTs & Hybrid Electric VehiclesWhile CVTs will help to prolong the viability of internal combustion engines, CVTs themselves will certainly not fade if and when IC does. Several companies are currently studying implementation of CVTs with HEVs. Nissan recently developed an HEV with “fuel efficiency … more than double that of existing vehicles in the same class of driving performance” [14]. The electric motor avoids the low-speed/high torque problems often associated with CVTs, through an innovative double-motor system. At low speeds:A low-power traction motor is used as a substitute mechanism to accomplish thefunctions of launch and forward/reverse shift. This has made it possible to discontinueuse of a torque converter as the launch element and a planetary gearset and wet multiplateclutches as the shift mechanism. [14]Thus use of a CVT in a HEV is optimal: the electric portion of the power system avoids the low-speed problems of CVTs, while still retaining the fuel efficiency and power transmission benefits at high speeds.. Moreover, “the use of a CVT capable of handling high engine torque allows the system to be applied to more powerful vehicles” [14]. Obviously, automakers cannot develop individual transmissions for each car they sell; rather, a few robust, versatile CVTs must be able to handle a wide range of vehicles.Korean automaker Kia has proposed a rather novel approach to CVTs and their application to hybrids. Kia recently tested a system where “the CVT allows the engine to run at constant speed and the motor allows the engine to run at constant torque independent of driving conditions” [15]. Thus, both gasoline engine and electric motor always run at their optimal speeds, and the CVT adjusts as needed to accelerate the vehicle. Kia also presented a control system for this unified HEV/CVT combination that optimizes fuel efficiency for the new configuration.ConclusionToday, only a handful of cars worldwide make use of CVTs, but the applications and benefits of continuously variable transmissions can only increase based on today’s research and development. As automakers continue to develop CVTs, more and more vehicle lines will begin to use them. As development continues, fuel efficiency and performance benefits will inevitably increase; this will lead to increased sales of CVT-equipped vehicles. Increased sales will prompt further development and implementation, and the cycle will repeat ad infinitum. Moreover, increasing development will foster competition among manufacturers—automakers from Japan, Europe, and the U.S. are already either using or developing CVTs—which will in turn lower manufacturing costs. Any technology with inherent benefits will eventually reach fruition; the CVT has only just begun to blossom.Works Cited[1]S. Birch: “Audi takes CVT from 15th century to 21st century”. Automotive Engineering International,January 2000.[2]J. Yamaguchi: “Nissan’s Extroid CVT”. Automotive Engineering International, February 2000.[3]M.A. Kluger and D.R. Fussner: “An Overview of Current CVT Mechanisms, Forces andEfficiencies” SAE Paper No. 970688, in SAE SP-1241, Transmission and Driveline SystemsSymposium, pp. 81-88 SAE, 1997.[4]U.S. Environmental Protection Agency, /feg/findacar.htm.Accessed 4/15/00.[5]M. Boos and H. Mozer: “ECOTRONIC – The Continuously Variable ZF Transmission (CVT)” SAEPaper No. 970685, in SAE SP-1241, Transmission and Driveline Systems Symposium, pp. 61-67 SAE, 1997.[6]J.L. Broge: “GM Powertrain’s evolving transmissions”. Automotive Engineering International,November 1999.[7]J. Yamaguchi: “Two new CVTs for mini cars”. Automotive Engineering International, March 1999.[8]D. Kobayashi, Y. Mabuchi and Y. Katoh: “A Study on the Torque Capacity of a Metal Pushing V-Belt for CVTs” SAE Paper No. 980822, in SAE SP –1324, Transmission and Driveline Systems Symposium, pp. 31-39 SAE, 1998.[9]K. Abo, M. Kobayashi and M. Kurosawa: “Development of a Metal Belt Drive CVT Incorporating aTorque Converter for Use with 2-liter Class Engines” SAE Paper No. 980823, in SAE SP-1324, Transmission and Driveline Systems Symposium, pp. 41-48 SAE, 1998.[10]T. Miyazawa, T. Fujii, K. Nonaka and M. Takahashi: “Power Transmitting Mechanism of a DryHybrid V-Belt for a CVT – Advanced Numerical Model Considering Block Tilting and PulleyDeformation” SAE Paper No. 1999-01-0751, in SAE SP-1440, Transmission and Driveline Systems Symposium, pp. 143-153 SAE, 1999.[11]K. Ohya and H. Suzuki: “Development of CVT Pulley Piston Featuring Variable Thickness andWork-Hardening Technologies” SAE Paper No. 980826, in SAE SP-1324, Transmission andDriveline Systems Symposium, pp. 71-79 SAE, 1998.[12]S. Sakaguchi, E. Kimura and K. Yamamoto: “Development of an Engine-CVT Integrated ControlSystem” SAE Paper No. 1999-01-0754, in SAE SP-1440, Transmission and Driveline SystemsSymposium, pp. 171-179 SAE, 1999.[13]M. Yasuoka, M. Uchida, S. Katakura and T. Yoshino: “An Integrated Control Algorithm for anSI Engine and a CVT” SAE Paper No. 1999-01-0752, in SAE SP-1440, Transmission and Driveline Systems Symposium, pp. 155-160 SAE, 1999.[14]N. Hattori, S. Aoyama, S. Kitada and I. Matsuo: “Functional Design of a Motor Integrated CVTfor a Parallel HEV” SAE Paper No. 1999-01-0753, in SAE SP-1440, Transmission and Driveline Systems Symposium, pp. 161-167 SAE, 1999.[15] C. Kim, E. NamGoong, S. Lee, T. Kim and H. Kim: “Fuel Economy Optimization for ParallelHybrid Vehicles with CVT” SAE Paper No. 1999-01-1148, in SAE SP-1440, Transmission and Driveline Systems Symposium, pp. 337-343 SAE, 1999.。
汽车变速器英语词汇

〔副变速器〕变速杆range selector按钮控制finger-tip control半自动换档机械式变速器semi-automatic mechanical transmission 半自动液力变速器semiautomatic transmission包角scroll泵轮impeller边斜角〔进出口〕bias(entrance and exit)变矩比torque ratio变矩范围torque conversion range变矩系数torque ratio变容式液力变矩器variable capacity converter变速叉shifting fork (gear shift fork)变速齿轮transmission gear变速齿轮比〔变速比〕transmission gear ratio变速齿轮组change gear set变速杆stick shift(gear shift lever)变速轨〔拨叉道轨〕shift rail变速器transmission (gearbox)变速器输出轴transmission output shaft变速器输入轴transmission input shaft变速器中间轴transmission countershaft变速器轴的刚度rigidity of shaft变速器主动齿轮轴transmission drive gear shaft变速器主轴transmission main shaft变速踏板gear shift pedal操纵杆control lever槽导变速gate change长行星齿轮long planet gear常啮齿轮constant mesh gear常啮合齿轮传动constant mesh transmission常压式同步器constant pressure synchronizer超速档变速器over drive transmission超限换档overrun shift传动比gear ratio带主减速器的变速器final driving transmission单向离合器one-way clutch单向离合器换档freewheel shift导轮可反转的变矩器torque converter with reversal reactor 倒档reverse gear倒档中间齿轮reverse idler gear低速档bottom gear(low speed gear)第二档second gear第一档first gear电磁阀调压阀solenoid regulator valve电液式自动换档系统electronic -hydraulic automatic电子同步变速装置electronically synchronized transmission assembly 调压阀pressure -regulator valve调制压力modulated pressure定输入扭矩特性constant input torque performance定轴式液力变速器countershaft transmission定子stator动力换档power shift动力换档过程timing动力相似dynamic similarity动力助力换档变速器power assisted shift transmission短行星齿轮short planet gear多级变速器multi-speed transmission多中间轴变速器multi-countershaft transmission反拖特性coast performance方向盘式变速column shift (handle change)分动齿轮〔分动机构〕transfer gear分动箱〔分动器〕transfer case分动箱控制杆transfer gear shift fork分段式多档变速器sectional type multi-speed transmission分流式液力变速器split torque drive transmission辅助变速器auxiliary gear box副变速器splitter副轴counter shaft副轴齿轮counter shaft gear高速档top gear(high gear)固定轴式变速器fixed shaft transmission 惯性式同步器inertial type of synchronizer 过载系数overloading ratio后油泵gear pump (output pump )滑差slip滑动齿轮sliding gear滑动齿轮变速器sliding gear transmission 滑动齿轮传动sliding -gear transmission 缓冲压力compensator or trimmer pressure 换档shift换档点shift point换档定时property of automatic shift换档阀shift valve换档规律process of power shift换档机构gearshift换档循环shift schedule换档元件engaging element换档指令发生器shift pattern generator回油泵scavenge oil pump机械式变速器mechanical transmission 级stage几何相似geometry similarity继动阀relay valve。
汽车变速器英语词汇
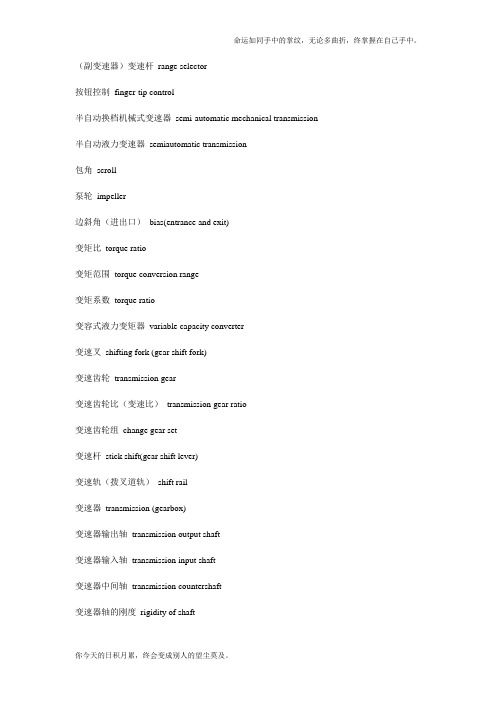
(副变速器)变速杆range selector按钮控制finger-tip control半自动换档机械式变速器semi-automatic mechanical transmission 半自动液力变速器semiautomatic transmission包角scroll泵轮impeller边斜角(进出口)bias(entrance and exit)变矩比torque ratio变矩范围torque conversion range变矩系数torque ratio变容式液力变矩器variable capacity converter变速叉shifting fork (gear shift fork)变速齿轮transmission gear变速齿轮比(变速比)transmission gear ratio变速齿轮组change gear set变速杆stick shift(gear shift lever)变速轨(拨叉道轨)shift rail变速器transmission (gearbox)变速器输出轴transmission output shaft变速器输入轴transmission input shaft变速器中间轴transmission countershaft变速器轴的刚度rigidity of shaft变速器主动齿轮轴transmission drive gear shaft变速器主轴transmission main shaft变速踏板gear shift pedal操纵杆control lever槽导变速gate change长行星齿轮long planet gear常啮齿轮constant mesh gear常啮合齿轮传动constant mesh transmission常压式同步器constant pressure synchronizer超速档变速器over drive transmission超限换档overrun shift传动比gear ratio带主减速器的变速器final driving transmission单向离合器one-way clutch单向离合器换档freewheel shift导轮可反转的变矩器torque converter with reversal reactor 倒档reverse gear倒档中间齿轮reverse idler gear低速档bottom gear(low speed gear)第二档second gear第一档first gear电磁阀调压阀solenoid regulator valve电液式自动换档系统electronic -hydraulic automatic电子同步变速装置electronically synchronized transmission assembly 调压阀pressure -regulator valve调制压力modulated pressure定输入扭矩特性constant input torque performance定轴式液力变速器countershaft transmission定子stator动力换档power shift动力换档过程timing动力相似dynamic similarity动力助力换档变速器power assisted shift transmission短行星齿轮short planet gear多级变速器multi-speed transmission多中间轴变速器multi-countershaft transmission反拖特性coast performance方向盘式变速column shift (handle change)分动齿轮(分动机构)transfer gear分动箱(分动器)transfer case分动箱控制杆transfer gear shift fork分段式多档变速器sectional type multi-speed transmission分流式液力变速器split torque drive transmission辅助变速器auxiliary gear box副变速器splitter副轴counter shaft副轴齿轮counter shaft gear高速档top gear(high gear)固定轴式变速器fixed shaft transmission 惯性式同步器inertial type of synchronizer 过载系数overloading ratio后油泵gear pump (output pump )滑差slip滑动齿轮sliding gear滑动齿轮变速器sliding gear transmission 滑动齿轮传动sliding -gear transmission 缓冲压力compensator or trimmer pressure 换档shift换档点shift point换档定时property of automatic shift换档阀shift valve换档规律process of power shift换档机构gearshift换档循环shift schedule换档元件engaging element换档指令发生器shift pattern generator回油泵scavenge oil pump机械式变速器mechanical transmission 级stage几何相似geometry similarity继动阀relay valve。
- 1、下载文档前请自行甄别文档内容的完整性,平台不提供额外的编辑、内容补充、找答案等附加服务。
- 2、"仅部分预览"的文档,不可在线预览部分如存在完整性等问题,可反馈申请退款(可完整预览的文档不适用该条件!)。
- 3、如文档侵犯您的权益,请联系客服反馈,我们会尽快为您处理(人工客服工作时间:9:00-18:30)。
翻译题目 I型动力传动无限变速机械无级变速器
学院: 汽车与交通工程学院
专业: 车辆工程
学号: 200603179022
学生姓名: 王平
指导教师: 汪建春
日期: 2010年3月
I型动力传动无限变速式机械无级变速器
Giacomo Mantriota
Dipartimento di Ingegneria Meccanica e Gestionale, Politecnico di Bari, Viale Japigia, 182-70126 Bari, Italy
概要
无限变速式机械无级变速器(IVT)具有连续传动比,传动比有可能为零,同时允许反向工作。
与IVT性能有关的实验结果是通过与V带无极变速器(CVT)的连接获得,一个行星齿轮齿轮和一个变速器对应一个传动比。
试验模型是I型功率分流串联IVT,使用一种特殊的试验台,在IVT内的功率循环以及输入输出功率都可以测得。
实验结果将与理论值相比较。
无级变速器组件的扭矩与功率与IVT的相比较,以评估它们的潜力。
IVT的效率曲线与扭矩和传动比的变化有关,最终结果将与等效CVT相比较。
2002年相关学院版权所有
关键:CVT;功率分流;IVT;功率输出;效率;试验台;可变变速箱
1.介绍
如果对于燃油消耗和动力性很关注,无级变速器对于汽车来说是一个不错的选择。
无级变速器持续改进,频繁提出新的解决方案以提高它的性能。
缩写
CVT 无级变速器FR固定传动比装置P 功率
PG行星齿轮η效率rr 比率范围
Ť扭矩τ传动比ω角速度
τIVT →0-,τIVT →0+ 分别从左右两个方向趋近零
τCVT Min,τCVT Max 无级变速器传动比的最小值与最大值
τIVT Min,τIVT Max IVT传动比的最小值与最大值
在城市驾驶配备手动变速箱的汽车对于驾驶员可能比较困难,如果他想减少燃料消耗,需要频繁地换挡。
自动CVT可以自动换挡,并永远保证最佳传动比。
Mantriota提出了一种带有两个独立操作机构的功率分流无级变速系统,能保证无功率循环。
考虑到相同的传动比范围,这种传动使我们获得相对于传统的CVT更好的效率。
IVT是功率分流无级变速系统中的一种,该系统传动比连续变化,甚至可以为零,输出轴速度为零,而输入轴非零。
一款带有离合器功能的紧凑变速器就得到了。
因此汽
车可以在无离合器的情况下低速行驶,而没有从离合器的啮合和脱离啮合控制所带来的问题。
IVT通常由三部分组成:CVT,行星轮系(PG),和固定传动比装置(FR)。
例如Beachley et al, Hanachi,Vahabzadeh等提出了一些IVT的配置和应用。
我们的研究小组最近研究了IVT的功率分流和效率。
在IVT各支路的功率分流以两个可能的方向研究。
其结果是,I型功率分流的IVT能更方便的提高效率,然而II型
功率分流的平行IVT能确保更高的效率。
结果表明,效率主要是由IVT的功率分流类型而定。
特别是,II型分流在低传动比时能提供更高的效率,而I型分流在大传动比时能保证更高的效率与输入功率。
装备了4种不同类型变速器的中级车的燃料消耗量相比,(手动,全自动机械,CVT 和IVT)进行比较。
燃油消耗是在静止的条件下计算,采用ECE和EUDC循环。
考虑到降低燃料消耗与IVT的更高的舒适性,我们的结论是,IVT可取代传动比非连续变速器和CVT,特别是在城市城市中行驶的中档车。
结合以前理论著作中的有趣结果,在巴西利卡塔大学的应用力学实验室的IVT模型成功制成,实验目的在于评价其性能。
在这项工作中,功率分流与I型功率分流串联IVT的效率等有关的数据就得到了。
试验测试平台使用一种特殊的试验台测量在不同的操作条件下的功率分流。
这项工作的主要目的是比较I型IVT与传统的CVT的性能差异。
特别是IVT在零传动比和运动反向两种状态下的性能,
试验中得到的扭矩,功率分流,和效率等结果再与理论模型所得结果相比。
2.无限变速式机械无级变速器
IVT提供无限的变速范围,这意味着它的传动比可达到零。
IVT是由三部分组成:CVT,行星轮系,固定传动比装置。
在Fig 1 FR与CVT串联。
单个组件传动比(图Fig 1)(第i条支路的角速度为 )
总的传动比
对于功率分流CVT系统可能的功率分流方向如Fig1.2.3所示,III型功率分流是唯一
一种保证流过CVT的功率比功率分流CVT所输出的功率小得多的方案。
而且效率高。
Mantriota提出只有当功率分流CVT的传动比范围远小于CVT时,三型动力流动才能得到。
IVT的两种可能的功率分流I型和II分别发生时,分别有逆向.正向相符的传动比与之对应。
要想优化传输效率,串联将用于I型功率传动。
如果IVT传动比的最小和最大值被要求是特定值,而且知道CVT的传从比变化范围(最小传动比,最大传动比),就可以计算行星齿轮的传动比和固定传动比装置的传动比。
对于I性串联功率分流IVT系统有:
对于rr CVT 总传动比即:
IVT的性能在很大程度上取决于CVT组件。
其实,CVT组件的效率最低,因此为了评价IVT的整体损失,有必要计算CVT的输出功率。
让我们假定IVT的效率有一个单位值。
拿I型动来说,很容易证明IVT的功率与CVT内循环的功率可以表述如下
CVT的传动比范围的作用是使功率比值令2τ
IVT 达到最大值。
当τ
IVT Min
=0时
从方程(6)可知当τIVT
流经CVT的功率大于IVT,当τIVT >
只有一部分的输入功率流经CVT。
关于I型功率分流,在稳态时,行星轮系的效率是基于功率方程(Fig 2):
即
作用在行星轮系轴上的力平衡方程如下:
即
因此
此外(Fig 2)
FR和CVT的效率
通过这些方程式,就可以确定那些表征IVT性能的参数。
3.试验台
与功率分流和I型串联IVT的效率有关的试验结果将通过此项工作获得。
为了这一目的,巴西利卡塔大学的力学实验室特别建了一个试验台(Fig.3.4)串联IVT使用了一台CVT和一根V带,因为是静止的工作条件,传动比的变化通过使用一个节来调整驱动半轮的位置,作用在从动半轮上的轴向推力由螺旋弹簧提供。
行星轮系的传动比经过计算使系统构成I型串联功率分流IVT,但可能使运动反向。
试验台所带的行星齿轮传动比是2,通过行星架传递正时带的运动。
固定传动比的传递通过正时带轮(
=1)。
FR
Fig. 3. Test rig.
Fig. 4. Diagram of the test rig。