电容屏制作工艺
电容屏工艺流程介绍
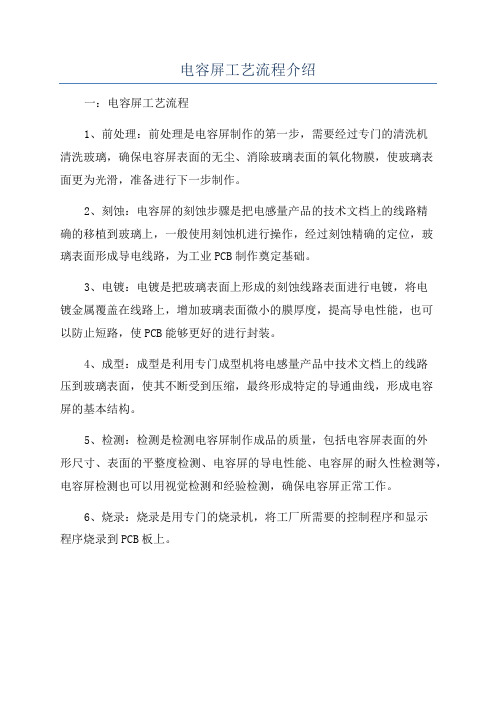
电容屏工艺流程介绍
一:电容屏工艺流程
1、前处理:前处理是电容屏制作的第一步,需要经过专门的清洗机
清洗玻璃,确保电容屏表面的无尘、消除玻璃表面的氧化物膜,使玻璃表
面更为光滑,准备进行下一步制作。
2、刻蚀:电容屏的刻蚀步骤是把电感量产品的技术文档上的线路精
确的移植到玻璃上,一般使用刻蚀机进行操作,经过刻蚀精确的定位,玻
璃表面形成导电线路,为工业PCB制作奠定基础。
3、电镀:电镀是把玻璃表面上形成的刻蚀线路表面进行电镀,将电
镀金属覆盖在线路上,增加玻璃表面微小的膜厚度,提高导电性能,也可
以防止短路,使PCB能够更好的进行封装。
4、成型:成型是利用专门成型机将电感量产品中技术文档上的线路
压到玻璃表面,使其不断受到压缩,最终形成特定的导通曲线,形成电容
屏的基本结构。
5、检测:检测是检测电容屏制作成品的质量,包括电容屏表面的外
形尺寸、表面的平整度检测、电容屏的导电性能、电容屏的耐久性检测等,电容屏检测也可以用视觉检测和经验检测,确保电容屏正常工作。
6、烧录:烧录是用专门的烧录机,将工厂所需要的控制程序和显示
程序烧录到PCB板上。
电容屏(Film_To_Film结构)制作流程

B
按客户要求,更改出PIN定义与FPC位置
C
按键往视窗方向移动0.35MM,FPC往左移动了5.35mm
DATE 10.11.06 10.11.16 10.11.16
NAME CHRICS CHRICS CHRICS
FRONT VIEW
259.00±0.10(Lens) 245.73(SENSOR OUTLINE) A
三道风切的压力上 10±3 KPa、第三道风切的压力下 8±3 KPa、第四道风切的压力上 10±3 KPa、第四道风切的压力下 8±3 KPa、
第五道风切的压力 4±1 KPa、脱膜喷林的压力 25±3KPa、第六道风切的压力上 10±2 KPa、第六道风切的压力下 8±2 KPa、第七
道风切的压力上 10±2 KPa、第七道风切的压力下 8±2 KPa、超声波清洗(循环水清洗喷淋的压力上 0.25±0.05 MPa)、超声波清
3)固化参数:
绝缘油
稀释剂
CR-18T-KT1
—
回墨刀速度 (档) 3±0.5
刮刀速度(档) 2.2±0.5
刮刀深度 (mm)
5~10
回墨刀深度 (mm) -1~1
刮刀压力 (kgf/cm2)
5±1
刮刀硬度(度) 80~85
硬化剂 —
配比 —
使用粘度 200~350dpa.s
光积量(mj/cm2) 950 ~1150
5.95
Tempered glass
T=1.1mm C
Pantone 425C
16.64±0.30
14.36±0.30
Back adhesive to outline
16.64±0.30
14.36±0.30
电容式触摸屏生产工艺

电容式触摸屏生产工艺
电容式触摸屏是一种常见的现代触摸屏技术,其生产工艺通常包括以下步骤:
1. 基材准备:选择适当的基材,通常是玻璃或塑料。
在玻璃上涂覆透明导电物质,如氧化铟锡(ITO),形成触摸层。
2. 涂布导电层:将ITO溶液通过印刷或涂覆技术均匀涂覆在
基材上,形成导电层。
然后通过加热或紫外线固化,使导电层附着在基材上。
3. 电容感应器:使用光刻和化学腐蚀技术,将导电层覆盖掉的区域进行处理,形成电容感应器的结构。
通常是将导电层分割成等大小的电容单元。
4. 绝缘层涂覆:在电容感应器上涂覆一层绝缘层,通常是氟化物或无机材料。
绝缘层的主要作用是防止触摸屏受到外界干扰和划伤。
5. 顶层涂覆:在绝缘层上涂覆一层光学透明的保护层,通常使用有机硅材料。
这一层的作用是保护触摸屏免受污染和划伤,并提供良好的触感。
6. 检验和测试:对生产的触摸屏进行检验和测试,确保其质量符合要求。
常见的测试包括触摸灵敏度、精度和稳定性等方面。
7. 组装和调试:将触摸屏与显示器或其他设备进行组装,并进
行相应的调试和校准,以确保触摸效果良好。
8. 包装和出货:将生产完成的触摸屏进行包装,并进行出货准备。
总而言之,电容式触摸屏的生产工艺涉及多个步骤,包括基材准备、涂布导电层、电容感应器制作、绝缘层涂覆、顶层涂覆、检验和测试、组装和调试以及包装和出货。
这些步骤需要精密的设备和技术,并且必须保证每个步骤的准确性和质量,才能生产出高品质的电容式触摸屏产品。
电容屏的工艺过程

电容屏的工艺过程电阻屏:目前用户数最多的,并能够持续到明年,因为电阻屏更便宜,而且更精准。
虽然电容屏也开始配备了特殊的手写笔,比如戴尔Mini 3i,但是在需要精准的触控时,却比较麻烦。
电容屏:高端智能市场的代表。
目前市面上的电容屏分为两种:基于Film的电容屏和基于玻璃的电容屏。
玻璃基础的电容屏在现在使用的比较少了,它们只在特别高端和昂贵的手机上存在,比如苹果iPhone。
基于Film的电容屏相对便宜,现在广泛用于中端定位的设备中。
电容触摸屏的介绍电容式触摸屏的构造主要是在玻璃屏幕上镀一层透明的薄膜体层,再在导体层外加上一块保护玻璃,双玻璃设计能彻底保护导体层及感应器。
电容式触摸屏在触摸屏四边均镀上狭长的电极,在导电体内形成一个低电压交流电场。
在触摸屏幕时,由于人体电场,手指与导体层间会形成一个耦合电容,四边电极发出的电流会流向触点,而电流强弱与手指到电极的距离成正比,位于触摸屏幕后的控制器便会计算电流的比例及强弱,准确算出触摸点的位置。
电容触摸屏的双玻璃不但能保护导体及感应器,更有效地防止外在环境因素对触摸屏造成影响,就算屏幕沾有污秽、尘埃或油渍,电容式触摸屏依然能准确算出触摸位置。
电容式触摸屏是在玻璃表面贴上一层透明的特殊金属导电物质。
当手指触摸在金属层上时,触点的电容就会发生变化,使得与之相连的振荡器频率发生变化,通过测量频率变化可以确定触摸位置获得信息。
由于电容随温度、湿度或接地情况的不同而变化,故其稳定性较差,往往会产生漂移现象。
该种触摸屏适用于系统开发的调试阶段。
编辑本段电容触摸屏的缺陷电容触摸屏的透光率和清晰度优于四线电阻屏,当然还不能和表面声波屏和五线电阻屏相比。
电容屏反光严重,而且,电容技术的四层复合触摸屏对各波长光的透光率不均匀,存在色彩失真的问题,由于光线在各层间的反射,还造成图像字符的模糊。
电容屏在原理上把人体当作一个电容器元件的一个电极使用,当有导体靠近与夹层ITO工作面之间耦合出足够量容值的电容时,流走的电流就足够引起电容屏的误动作。
电容屏ITO蚀刻膏制程工艺

参数规格:
碱度:0.2-0.5MOL,温度:35±5度,压力:1-2KG,速度:1.5-3.5M/MIN。
经纯水清洗,干燥。
第七步:保护胶丝印
参数规格:
膜厚:15-30μM,250-420目聚酯网,乳剂膜厚:10-20μM
保护胶:日本朝日,丰阳等,热固型。
第八步:银浆线丝印
参数规格:
大片半成品切割,激光处理成小片半成品。
第十一步:压合
参数规格:
小片半成品与FPC及IC绑定形成功能片
第十二步:测试
参数规格:
功能片的功能测试。如:线性测试,寿命测试,精度测试等。
第十三步:终检
参数规格:
最终的一个外观检查。
第十三步:包装
参数规格:
包装处理出货。
第二步:ITO GLASS
参数规格:
长宽:14*16厚度:0.55,0.7,1.1
规格:普通,钢化等,
特性:AR(抗反射),AG(防眩光),AS(防水防污),AF(防指纹)等
电容玻璃:安可,冠华,正达,正太等。
第三步:缩水
参数规格:
让ITO FILM定型,非导电层面需丝印整版保护胶。
第四步:清洗
参数规格:
ito蚀刻液ito激光蚀刻机蚀刻片zippo蚀刻蚀刻招聘狂梦蚀刻蚀刻机法力蚀刻皇冠蚀刻片用什么胶水蚀刻液
电容屏ITO蚀刻膏制程工艺
流程
第一步:ITO FILM
参数规格:
宽:406,410厚度:188,175,125
规格:单膜,双膜。
特性:单,双加硬防刮。雾面防刮,雾面防牛等。
电容膜:日东,帝人,铃寅,LG等。
将GLASS表面的脏污,油污,杂质等去除并干燥。
电容触摸屏工艺流程简介

印刷正面 镭射银浆
印刷反面 镭射银浆
ITO厂工序
印刷 反面ISO
印刷正面 ISO(可选)
反面银浆镭射
正面银浆镭射
成品
贴合
绑定
切割成小片
单层镀ITO
基板
ITO镀膜
双层镀ITO
基板
ITO镀膜
单层镀ITO+METAL
基板
ITO镀膜
金属镀膜
双层镀ITO+METAL
基板
ITO镀膜
金属镀膜
ITO蚀刻-单面结构
L
其中要求如下: 1.不允许有S形翘曲
ITO
ITO架桥:导电性差(40Ω/■左右),解决
了金属点可见的问题,同时增加一道光照,成本
增加。
绝缘材料 金属或ITO
黄光SITO 结构工艺流程图(金属架桥)
单层镀ITO
ITO蚀刻单面结构
黄光厂工序
金属蚀刻单面结构
镀SIO2/OC
印刷可剥胶 (可选)
成品
贴合
绑定
切割
2.黄光DITO结构触摸屏制程
1.黄光SITO结构触摸屏制程
介绍:SITO是Single ITO的简称。即菱型
线路做法。XY轴(发射极和感应极)都在玻璃的
同一面。
X PATTERN和Y PATTERN通过搭桥的方式,
实现触摸屏发射极和感应极的作用。
架桥的选择:
金属架桥:导电性好(0.4Ω/■左右),但
是金属点会可见,影响外观。(推荐)
大片ITO蚀刻干蚀刻
印刷 银浆线路
大片ITO蚀刻干蚀刻
印刷 银浆线路
贴大片 OCA1
贴大片 OCA2
切割成小片
成品
触摸屏工艺简介

⑤、On-cell
IC FPC贴合
功能测试
3、OCA真空贴合
4、液态胶 水胶 贴合
END 谢谢
电容触摸屏工艺流程介绍
QF 2017年5月1日
内容
电容触摸屏介绍 镀膜 黄光蚀刻介绍 网印可剥胶及切割 后段贴合简介
电容触摸屏介绍
1、电容触摸屏工作原理
普通电容式触摸屏的感应屏是一块四层复合玻璃屏,玻璃屏的内表面和夹层各涂有 一层导电层,最外层是一薄层玻璃保护层,当我们用手指触摸在感应屏上的时候,人体 的电场让手指和和触摸屏表面形成一个耦合电容,对于高频电流来说,电容是直接导体, 于是手指从接触点吸走一个很小的电流,这个电流分从触摸屏的四角上的电极中流出, 并且流经这四个电极的电流与手指到四角的距离成正比,控制器通过对这四个电流比例 的精确计算,得出触摸点的位置,
中、大
低
镀膜
1、镀膜介绍
镀膜技术也叫薄膜技术,是在真空条件下采用物理或化学方法,使物 体表 面获得所需的膜体,镀膜技术是最初起源于20世纪30年代,直 到70年代后期才得到较大发展的一种技术,目前已被广泛应用于耐 酸、耐蚀、耐热、表面硬化、装饰、润滑、光电通讯、电子集成、 能源等领域,
2、镀膜的种类
On-Cell是指将触摸屏嵌入到显示屏的彩色滤光片基板和偏 光片之间的方法,即在液晶面板上配触摸传感器,相比In-Cell技 术难度降低不少,三星、日立、LG等厂商在On-Cell结构触摸屏上 进展较快,目前,On-Cell多应用于三星Amoled面板产品上,技术上 尚未能克服薄型化、触控时产生的颜色不均等问题,
电容屏(Film_To_Film结构)制作流程

/min、脱膜液比重 1.02~1.06 g/cm3、第一道风切的压力 12±2 KPa、蚀刻喷淋压力 15±2 KPa、第二道风切的压力上 6.5±2 KPa、第
二道风切的压力下 5.5±2 KPa、循环水喷淋的压力上 25±3 KPa、循环水喷淋的压力下 17±3 KPa、DI 水喷淋的压力 10±5 KPa、第
4
IR 固化
4.2 工艺环境及参数
4.2.1 大片裁切/预烘岗位
1)作业环境:温度:22±3℃、湿度:60±10%RH、Partical:CLASS1000
2)工艺参数:
菲林材料 Prov188
3)预烘参数:
菲林型号 Prov188
裁切长度 500
预烘温度(℃) 150
裁切宽度 370
裁切速度 8000~10000
223.72(Window/AA)
4.00 17.64
1.55±0.10(含胶) 1.45±0.1
Back VIEW
? 2.50
5.05 A
Clear window ?1.00 A
256.90 [10.114"]
5.80
Back adhesive(T=0.125) TOP BOTTOM
TP ITO FILM
2
2)丝印参数:
网间距 (mm)
胶刮角 度
(度)
3.5±0.3 55±5
回墨刀速 度(档)
3±0.5
回墨刀深度 (mm) -1~1
刮刀速 刮刀深度 度(档) (mm)
2.0±0.5
5~13
离板高度(mm) 1±0.5
刮刀硬度 (度)
刮刀压力 (kgf/cm2)
80~85
4~6
- 1、下载文档前请自行甄别文档内容的完整性,平台不提供额外的编辑、内容补充、找答案等附加服务。
- 2、"仅部分预览"的文档,不可在线预览部分如存在完整性等问题,可反馈申请退款(可完整预览的文档不适用该条件!)。
- 3、如文档侵犯您的权益,请联系客服反馈,我们会尽快为您处理(人工客服工作时间:9:00-18:30)。
电容屏制作工艺比较:
DITO 与SITO对比
DITO 制造工艺复杂,但透光度、稳定性好,适用于高端
应用,据了解,iPhone 采用的是DITO 工艺;SITO 工艺较DITO 简单,但稳定性稍差,目前尚在持续改进中;FILM 透光性较差,而且一般边框较厚,美观度不理想,但成本优势
明显。
DITO 工艺的难度主要在于:第一、工序繁琐而复杂;第二、上下两层ITO 光刻对位精度极高;第三、生产过程中,玻璃的两面都要保证高度清洁。
DITO 对检测IC 也有很高的要求,由于两层ITO 间距较大(相隔一层玻璃,而
不是如同SITO 仅相隔绝缘层),层间电容较小,检测灵敏度高,但对IC 的精度要求也高。
SITO 工序的复杂度和精密度,都较DITO 为低,因此成本较低,但有两个弱点:第一、两层ITO 先后光刻在玻璃的同一面,附着强度比DITO 低,性能的稳定性也比DITO 低;第二、如上段分析,SITO 层间电容大,检测精度不如DITO。