薄膜电容器生产工艺流程图
薄膜电容器及其制造方法
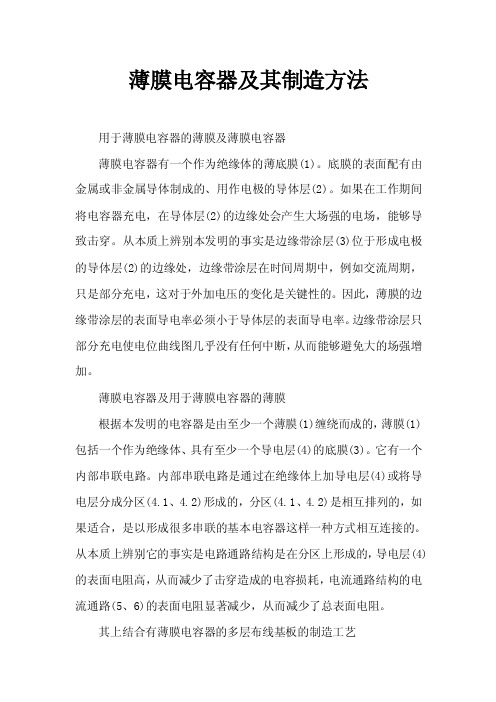
薄膜电容器及其制造方法用于薄膜电容器的薄膜及薄膜电容器薄膜电容器有一个作为绝缘体的薄底膜(1)。
底膜的表面配有由金属或非金属导体制成的、用作电极的导体层(2)。
如果在工作期间将电容器充电,在导体层(2)的边缘处会产生大场强的电场,能够导致击穿。
从本质上辨别本发明的事实是边缘带涂层(3)位于形成电极的导体层(2)的边缘处,边缘带涂层在时间周期中,例如交流周期,只是部分充电,这对于外加电压的变化是关键性的。
因此,薄膜的边缘带涂层的表面导电率必须小于导体层的表面导电率。
边缘带涂层只部分充电使电位曲线图几乎没有任何中断,从而能够避免大的场强增加。
薄膜电容器及用于薄膜电容器的薄膜根据本发明的电容器是由至少一个薄膜(1)缠绕而成的,薄膜(1)包括一个作为绝缘体、具有至少一个导电层(4)的底膜(3)。
它有一个内部串联电路。
内部串联电路是通过在绝缘体上加导电层(4)或将导电层分成分区(4.1、4.2)形成的,分区(4.1、4.2)是相互排列的,如果适合,是以形成很多串联的基本电容器这样一种方式相互连接的。
从本质上辨别它的事实是电路通路结构是在分区上形成的,导电层(4)的表面电阻高,从而减少了击穿造成的电容损耗,电流通路结构的电流通路(5、6)的表面电阻显著减少,从而减少了总表面电阻。
其上结合有薄膜电容器的多层布线基板的制造工艺一种其内结合有薄膜电容器的多层布线板的制造工艺,该工艺包括以下步骤:除了薄膜电容器的下电极形成区之外,用第一抗蚀剂膜覆盖形成在绝缘层上的第一导体图形;在用第一抗蚀剂膜覆盖的第一导体图形的整个表面上形成金属膜层,金属膜依次由阻挡金属层和钽金属层组成;除了下电极形成区之外,从第一导体图形的表面上除去第一抗蚀剂膜以除去金属膜层;除了第一导体图形的下电极形成区之外,用第二抗蚀剂膜覆盖第一导体图形的表面;在第二抗蚀剂膜露出的金属膜层上形成阳极氧化膜;在阳极氧化膜和导体图形上除去第二抗蚀剂膜,并依次附加粘附层和金属籽晶层;以及在阳极氧化膜上形成将成为上电极的第二导体图形。
2.薄膜电容器ppt课件
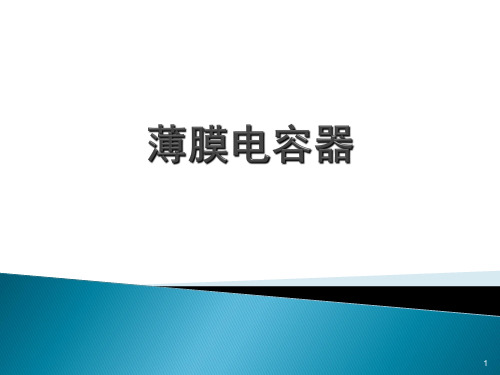
薄膜电容器的基本结构
• 请在此输入您的文本。
12
13
薄膜电容器的主要材料—薄膜介质
材料性能
聚酯PET
聚丙烯PP或 OPP
聚苯硫醚PPS
聚2,6奈乙酯 PEN
聚碳酸酯PC
聚苯乙烯PS
厚度μm
>=0.5
>=3
>=1
>=1
>=1.5
>=4
介电常数
3.0-3.3
2.1-2.2
2.8
3.0-3.3
2.6-3.2
20
6. 阻燃性 除PPS(聚苯硫醚)材料外,目前使用的有机薄膜 电介质不是阻燃材料。 尽管在薄膜电容器外封装中使用了耐火性阻燃 材料--阻燃环氧树脂或阻燃塑壳,但外部的持 续高温或火焰仍可使电容器芯子变形而产生外 封装破裂,导致电>PEN>PET>PP, 箔式>金属化 潮湿 耐湿程度:全密封>半密封>无密封 机械冲击 安装重心(贴片,轴向,径向),引脚形状
1
为了增加电容器的电容量,通常将电极轧 成金属箔,与绝缘介质薄膜一同卷绕成芯 子,以尽量减小体积,这样就形成了薄膜 电容器。 1876年英国D.斐茨杰拉德发明纸介电容器。 这就是薄膜电容器的始祖。
2
3
薄膜电容器由介质、电极、电极过渡、引出线、封装、印章标志等部分组成。 按介质分类:聚酯膜、聚丙烯膜… 按结构分类:卷绕式、叠片式、内串式。 按电极分类:金属箔、金属化(铝金属化、铝锌金属化)、膜箔复合结构。 按电极引出方式分类:径向、轴向。 按封装方式分类:盒式、浸渍型。 按用途分类:通用(直流)、脉冲、抑制电源电磁干扰、精密。
(片状,线状—粗细)
22
电容器生产工艺流程

电容器生产工艺流程电容器是一种能够储存电能的设备,广泛应用于电子产品和电力系统中。
它由两个电极之间的电介质隔离层组成,其中电介质可以是陶瓷、塑料或液体。
电容器的生产工艺流程一般包括材料准备、电介质制备、电极制备、装配和测试等步骤。
首先是材料准备。
根据电容器的设计规格,准备所需的材料,包括电极材料、电介质材料以及其他辅助材料。
电极材料通常是金属片或导电聚合物,电介质材料可以是陶瓷粉末或聚合物薄膜。
接下来是电介质制备。
对于陶瓷电容器,制备陶瓷粉末的工艺包括粉末合成、干燥、粉碎和筛分等步骤。
而对于聚合物电容器,制备电介质薄膜的工艺包括溶液制备、涂布、成膜和干燥等步骤。
这些步骤都需要严格控制各种参数,以确保电介质的性能达到要求。
然后是电极制备。
对于金属电极,可以通过压制、切割和地线等步骤将导电材料加工成所需形状和尺寸的电极片。
对于导电聚合物电极,可以通过溶液制备、涂布和成膜等步骤将导电聚合物材料制备成电极片。
为了提高电极与电介质之间的界面质量,通常会在电极表面进行活化处理。
接着是装配。
将制备好的电介质层和电极层按照规定的顺序堆叠在一起,并通过加热、加压或其他方法使其牢固地粘合在一起。
此外,还要按照设计要求添加电极引线,并用导线将引线与外部连接器焊接在一起。
最后是测试。
对生产好的电容器进行各种电性能测试,包括容量、损耗因子、电压漏率和绝缘电阻等参数的测量。
测试结果要与设计要求进行比对,确保电容器的质量符合标准。
电容器生产工艺流程中的每个步骤都需要严格的控制和监督,以确保电容器的质量和性能。
同时,还需要根据市场需求和技术发展的趋势不断改进和优化生产工艺,提高生产效率和产品质量,适应电容器应用领域的不断变革和进步。
电容器生产工艺流程

电容器生产工艺流程
电容器生产工艺流程:
1. 材料准备:准备所需的电容器材料,包括金属电极、介质材料和封装材料等。
对材料进行检验,确保符合质量标准。
2. 电极制备:将金属材料切割成适当的形状和尺寸,经过腐蚀、清洗和活化等工艺处理,使金属表面光洁度高、导电性能良好。
3. 介质制备:将介质材料经过混合、压制和烧结等工艺处理,使其达到所需的物理和化学性能,形成具有稳定电容性能的介质片。
4. 组装电容器:将电极和介质按照一定的顺序叠放在一起,形成电容层,通过热压或胶粘等方式将电容层固定在一起。
5. 包封封装:将已经组装好的电容器进行清洗和除尘处理,然后将其放置在封装模具中,注入封装材料,固化封装材料,形成电容器的外壳。
6. 电容器测试:对已封装的电容器进行电性能和尺寸等方面的测试,如容量、电阻、电容损耗和击穿电压等,确保电容器的质量符合要求。
7. 品质检验:对电容器的外观、尺寸、包装等进行检验,确保产品符合质量标准,并进行质量认证。
8. 包装和存储:将合格的电容器进行包装,并标明相关信息,如型号、容量、生产日期等,然后存放在干燥、防尘的仓库中,待出货。
9. 产品出货:按照订单要求,将成品电容器出货给客户,并建立良好的售后服务体系,跟踪产品的使用情况和反馈信息。
以上是电容器生产的一般流程,在实际生产中,根据不同类型
的电容器,还会涉及到一系列特殊的工艺流程,如电解液注入、电容器翻焊、电容器激光焊接等,以满足不同用户的需求。
金属化薄膜电容器的喷金工艺

金属化薄膜电容器的喷金工艺【摘要】金属化薄膜电容器制作的四大关键工序中,喷金工序显得尤为重要。
喷金工序的工艺状态直接影响到产品的电性能指标,特别是损耗特性。
【关键词】薄膜电容器;工艺1.喷金机理采用电弧或火焰等热源,将需喷涂的各类焊料丝材熔化并在高压空气的作用下雾化。
粉碎后的金属粒子以高速喷涂在对热能具有极高灵敏度的电容芯组端面薄膜层隙中,使芯组端面自内绕层至外绕层形成一个等电位的金属电极面,为电极引出提供一个桥接平台。
喷金工艺质量优劣的评价标准主要体现在:(1)金属涂层与金属化膜层的结合强度。
(2)喷金涂层的颗粒度和表面粗糙度大小。
(3)芯组料盘喷涂层的径向厚薄均匀度。
此外,材料的工艺利用率、残料的可收集率、环境污染、劳动强度、生产效率等也是应重点考虑的因素(在材料价格飞涨、产品制作成本居高不下的情况下这些因素尤为重要。
)2.常用的喷金工艺方式2.1热源焊料丝材熔化用的常用热源主要有电弧和火焰两种。
火焰热源一般是采用氧气和乙炔(俗称电石气)在喷枪口混合燃烧产生。
热源温度高,燃烧充分,喷金焊料(特别是高温焊料)可充分溶化和雾化,是一种比电弧更理想的热源。
目前国内常规金属化电容器主要采用电弧热源。
只在金属化叠片电容器中使用火焰热源。
2.2电容器芯组的行走方式电容器芯组在喷金机上的行走方式主要有履带式和转盘式两种。
早期(上世纪90年代以前)的喷金机主要以履带式为主。
由于:①喷涂区密封性差,粉尘对环境的污染严重;②传送履带、护板等机件由于粉尘的堆积清扫困难;③材料的工艺利用率低(约25%左右);④喷金层的厚薄均匀度难以保证;⑤占地面积较大等原因,已逐步被淘汰。
目前金属化电容器喷金工序主要采用凸轮式转盘喷金机。
通过凸轮控制、改变喷枪的平移速度,从而保证喷枪与料盘径向各点的相对线速度相等,确保涂层厚薄一致。
2.3喷金焊料目前国内喷涂焊料主要有:2.3.1五元合金(低温焊料)主要成分为:Sn(37-39%),Zn(3-6%),Sb(0.5-1.5%),Bi(0.01-0.5%),Pb(余量)。
手机自电容流程图 Microsoft Excel 工作表

备注
手机自电容生产流程
前段制作流程
裁切下料
丝印背面KBJ
烘烤KBJ
老化缩水
ITO面附保护
AG烘烤
丝印AG
酸刻脱膜
切割等份
OCA贴合
小片切割
脱泡
出货
后段制作流程
ACF粘附
预压 本压 功能测试
成品功能测
成品外观检
手贴泡棉胶、
脱泡
包装出货
前段各工序管控点、检验项目
工序流程 检验项目 各工序
裁切下料 丝印KBJ 老化缩水 丝印耐酸 UV 固化 蚀刻脱膜 丝印银浆 切割等份 时
1.切割机切出的产品均偏小0.1
1.各小片必须放置在盘子里面且
后段各工序管控点、检验项目
工序流程
ACF粘附 预压 本压 CG贴合
检验项目
温度、压力、平整度、ACF粘附位置 温度、压力、平整度、FPC压合位置 温度、压力、平整度、拉力、晶球排布pin头晶球压破个数 偏位、气泡、外观
必须先将ITO保护膜撕掉。
时不可触摸到可视区及靶标油墨图案;2.ITO面朝上 一位置排摆放。
用第2号(靠切割处)uv机固化。
口必须站一人负责预防卡料;2.碱段及清洁段将往 力调小3.放置膜片时平行风刀斜度放置。 印机前必须用丝印膜或相等同厚度的膜做丝印片; 须解冻60分钟且搅拌15分钟后方可丝印;3.试印膜 后方可丝印产品。
1.不允许将ITO膜直接放置于地 尺寸、方阻、外观(刮伤、折伤、脏污、异物) 单手拿ITO膜避免折伤;3.裁切 长边右上角剪角。 丝印孔洞、丝印覆盖面、丝印均匀性(看颜色偏 差) 1.丝印首张前先用万用表测试丝
翘边、缩水率、方阻、外观(刮伤、折伤、脏污、 异物) 1.缩水前必须先将ITO保护膜撕
电容屏生产流程图

电容屏生产工艺流程图
开料 印刷 组合
终检
贴合
压合
备注:各主要工序之具体工序见下页
PAGE 2
电容屏生产工艺流程图 ---印刷
上线 印刷背保 烘烤 撕保护膜 老化 印刷耐酸
烘烤 贴保护膜
印刷银胶
UV清洗
蚀刻
UV固化
下线
印刷背保
烘烤
撕保护膜
老化 蚀刻
印刷耐酸
烘烤
印刷银胶
UV清洗
UV固化
贴保护膜
PAGE 3
电容屏生产工艺流程图 ---组合
上线检查 上线覆OCA 下线检查 上线背面覆OCA
上线镭射
上线贴合
半成品镭射
PAGE 4
电容屏生产工艺流程图 ---压合
SENSOR擦胶 SENSOR测试 FPC检查 FPC贴ACF
FPC贴ACF
FPC与半成品假贴
FPC压合 半成品测试
PAGE 5
电容屏生产工艺流程图 ---贴合
玻璃检查 产品贴合 产品脱泡
半成品擦拭
成品测试工艺流程图 ---终检
擦拭
检验
覆保护膜
包装
OQC
薄膜生产工艺流程图

薄膜生产工艺流程图薄膜生产工艺流程图薄膜是一种宽度小于0.1毫米,具有较高的透明度和柔韧性的材料。
薄膜广泛应用于包装、电子产品、太阳能能源等领域。
下面是薄膜生产的工艺流程图。
1. 原材料准备薄膜生产的第一步是准备原材料。
通常薄膜的原材料包括塑料颗粒、添加剂和色母粒。
这些原材料需要经过称量、筛选和预处理等工序,确保原材料的质量和纯度。
2. 材料熔融准备好的原材料将被放入熔融机中进行熔融。
熔融机通过加热和搅拌原材料,将其转化为熔融状态的塑料液体。
熔融过程中还可以添加其他添加剂和色母粒,以调整薄膜的性能和颜色。
3. 挤出成型熔融的塑料液体将被挤出成型。
挤出机将熔融液体注入一个金属模具中,通过模具的挤压作用,将熔融液体挤压出来,并形成连续的薄膜带状物。
挤出过程中,可以通过控制温度和挤压力来调节薄膜的厚度和宽度。
4. 冷却和拉伸挤出成型的薄膜带状物需要经过冷却和拉伸工序。
冷却过程中,薄膜带状物被冷却器冷却,使其从液态变为固态。
拉伸过程中,薄膜带状物经过拉伸机拉伸,使其变薄并增强其柔韧性。
5. 切割和卷绕冷却和拉伸后的薄膜带状物需要经过切割和卷绕工序,以得到所需尺寸的薄膜产品。
切割机将薄膜带状物切割成所需的长度,并同时进行整边处理。
卷绕机将切割好的薄膜卷绕成卷筒状,方便包装和运输。
6. 终检和包装最后一步是对薄膜产品进行终检和包装。
在终检过程中,对薄膜产品的质量进行全面检查,确保其符合相关标准和要求。
通过包装机将薄膜产品进行包装,以保护其在运输和储存过程中的完整性和质量。
以上是薄膜生产的主要工艺流程。
当然,实际生产中还会有一些细节和补充工序,以满足不同产品的要求。
薄膜生产工艺的不断改进和创新,使得薄膜在各个领域得到了广泛应用,为我们的生活带来了方便和便利。