大型锻件组织与性能的影响因素及其控制技术_黄倩
锻件质量控制

锻件质量控制引言概述:锻件作为一种重要的金属加工工艺,广泛应用于航空、汽车、机械等行业。
然而,由于锻件创造过程中存在一系列的复杂因素,如材料性能、工艺参数等,导致锻件质量控制成为一个关键的问题。
本文将从五个方面详细阐述锻件质量控制的重要性和方法。
一、材料选择1.1 材料性能要求:锻件的质量控制首先要从材料选择入手。
根据锻件的使用环境和要求,选择合适的材料。
考虑材料的强度、韧性、耐磨性等特性,确保锻件在使用过程中能够满足要求。
1.2 材料检测方法:采用适当的材料检测方法,如化学成份分析、金相分析、硬度测试等,对原材料进行严格检验,以确保材料的质量符合要求。
1.3 材料热处理:根据锻件的材料和使用要求,进行适当的热处理,如退火、正火、淬火等,以提高材料的力学性能和组织结构,从而提高锻件的质量。
二、工艺参数控制2.1 温度控制:锻件的温度是影响锻件质量的重要因素之一。
在锻造过程中,要控制好锻件的加热温度和保温时间,避免温度过高或者过低导致材料的结构破坏或者质量问题。
2.2 压力控制:锻造过程中的锻压力度对于锻件的成形和质量控制至关重要。
要根据锻件的形状和材料的特性,合理控制锻压力度,避免过大或者过小导致锻件的变形或者裂纹等问题。
2.3 冷却控制:锻件的冷却过程也是影响锻件质量的重要因素。
要根据锻件的材料和形状,合理选择冷却介质和冷却速度,避免锻件的变形和内部应力过大,保证锻件的质量。
三、工艺检测3.1 尺寸检测:通过测量锻件的尺寸,判断锻件的成形是否符合要求。
可以采用三坐标测量仪、投影仪等设备进行尺寸检测,确保锻件的几何形状和尺寸精度符合设计要求。
3.2 缺陷检测:通过无损检测方法,如超声波检测、磁粉检测等,对锻件进行缺陷检测,如裂纹、气孔等。
及时发现并修复锻件的缺陷,以提高锻件的质量。
3.3 组织检测:通过金相显微镜等设备,对锻件的金相组织进行观察和分析,判断锻件的组织结构是否均匀、致密,以及是否存在晶粒长大等问题,确保锻件的组织质量符合要求。
大型锻造的质量控制和研究方略
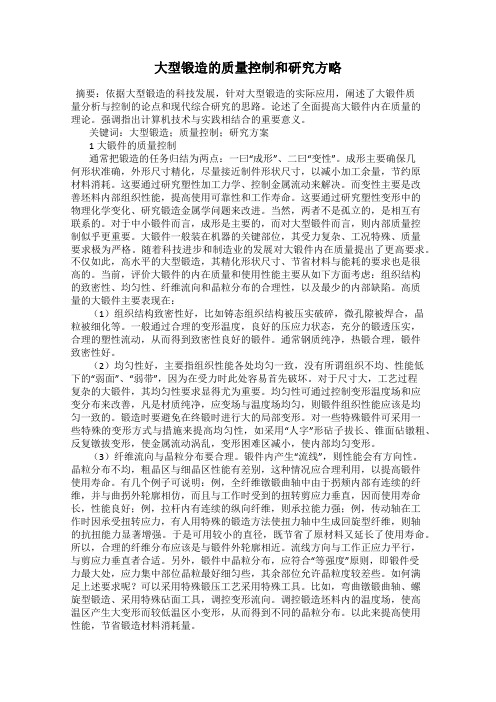
大型锻造的质量控制和研究方略摘要:依据大型锻造的科技发展,针对大型锻造的实际应用,阐述了大锻件质量分析与控制的论点和现代综合研究的思路。
论述了全面提高大锻件内在质量的理论。
强调指出计算机技术与实践相结合的重要意义。
关键词:大型锻造;质量控制;研究方案1大锻件的质量控制通常把锻造的任务归结为两点:一曰“成形”、二曰“变性”。
成形主要确保几何形状准确,外形尺寸精化,尽量接近制件形状尺寸,以减小加工余量,节约原材料消耗。
这要通过研究塑性加工力学、控制金属流动来解决。
而变性主要是改善坯料内部组织性能,提高使用可靠性和工作寿命。
这要通过研究塑性变形中的物理化学变化、研究锻造金属学问题来改进。
当然,两者不是孤立的,是相互有联系的。
对于中小锻件而言,成形是主要的,而对大型锻件而言,则内部质量控制似乎更重要。
大锻件一般装在机器的关键部位,其受力复杂、工况特殊、质量要求极为严格。
随着科技进步和制造业的发展对大锻件内在质量提出了更高要求。
不仅如此,高水平的大型锻造,其精化形状尺寸、节省材料与能耗的要求也是很高的。
当前,评价大锻件的内在质量和使用性能主要从如下方面考虑:组织结构的致密性、均匀性、纤维流向和晶粒分布的合理性,以及最少的内部缺陷。
高质量的大锻件主要表现在:(1)组织结构致密性好,比如铸态组织结构被压实破碎,微孔隙被焊合,晶粒被细化等。
一般通过合理的变形温度,良好的压应力状态,充分的锻透压实,合理的塑性流动,从而得到致密性良好的锻件。
通常钢质纯净,热锻合理,锻件致密性好。
(2)均匀性好,主要指组织性能各处均匀一致,没有所谓组织不均、性能低下的“弱面”、“弱带”,因为在受力时此处容易首先破坏。
对于尺寸大,工艺过程复杂的大锻件,其均匀性要求显得尤为重要。
均匀性可通过控制变形温度场和应变分布来改善,凡是材质纯净,应变场与温度场均匀,则锻件组织性能应该是均匀一致的。
锻造时要避免在终锻时进行大的局部变形。
对一些特殊锻件可采用一些特殊的变形方式与措施来提高均匀性,如采用“人字”形砧子拔长、锥面砧镦粗、反复镦拔变形,使金属流动涡乱,变形困难区减小,使内部均匀变形。
锻件的组织性能控制
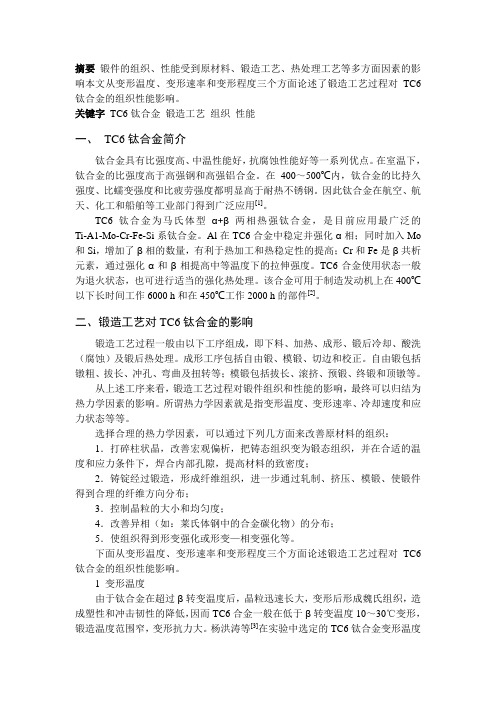
摘要锻件的组织、性能受到原材料、锻造工艺、热处理工艺等多方面因素的影响本文从变形温度、变形速率和变形程度三个方面论述了锻造工艺过程对TC6钛合金的组织性能影响。
关键字TC6钛合金锻造工艺组织性能一、TC6钛合金简介钛合金具有比强度高、中温性能好,抗腐蚀性能好等一系列优点。
在室温下,钛合金的比强度高于高强钢和高强铝合金。
在400~500℃内,钛合金的比持久强度、比蠕变强度和比疲劳强度都明显高于耐热不锈钢。
因此钛合金在航空、航天、化工和船舶等工业部门得到广泛应用[1]。
TC6钛合金为马氏体型α+β两相热强钛合金,是目前应用最广泛的Ti-A1-Mo-Cr-Fe-Si系钛合金。
Al在TC6合金中稳定并强化α相;同时加入Mo 和Si,增加了β相的数量,有利于热加工和热稳定性的提高;Cr和Fe是β共析元素,通过强化α和β相提高中等温度下的拉伸强度。
TC6合金使用状态一般为退火状态,也可进行适当的强化热处理。
该合金可用于制造发动机上在400℃以下长时间工作6000 h和在450℃工作2000 h的部件[2]。
二、锻造工艺对TC6钛合金的影响锻造工艺过程一般由以下工序组成,即下料、加热、成形、锻后冷却、酸洗(腐蚀)及锻后热处理。
成形工序包括自由锻、模锻、切边和校正。
自由锻包括镦粗、拔长、冲孔、弯曲及扭转等;模锻包括拔长、滚挤、预锻、终锻和顶镦等。
从上述工序来看,锻造工艺过程对锻件组织和性能的影响,最终可以归结为热力学因素的影响。
所谓热力学因素就是指变形温度、变形速率、冷却速度和应力状态等等。
选择合理的热力学因素,可以通过下列几方面来改善原材料的组织:1.打碎柱状晶,改善宏观偏析,把铸态组织变为锻态组织,并在合适的温度和应力条件下,焊合内部孔隙,提高材料的致密度;2.铸锭经过锻造,形成纤维组织,进一步通过轧制、挤压、模锻、使锻件得到合理的纤维方向分布;3.控制晶粒的大小和均匀度;4.改善异相(如:莱氏体钢中的合金碳化物)的分布;5.使组织得到形变强化或形变—相变强化等。
大型锻件锻造工艺及缺陷控制技术的研究现状及发展趋势分析
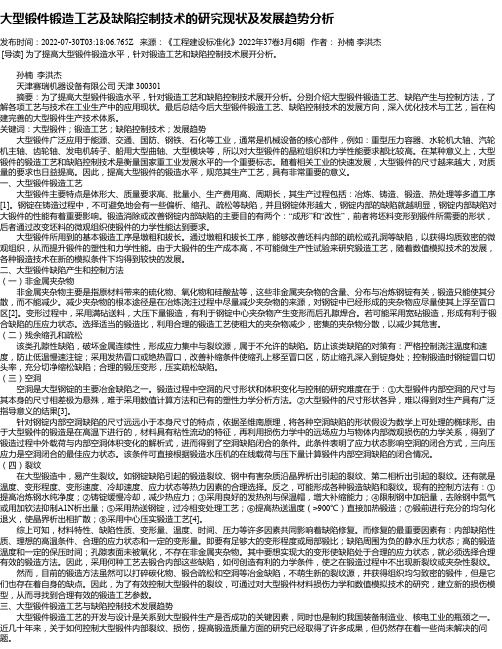
大型锻件锻造工艺及缺陷控制技术的研究现状及发展趋势分析发布时间:2022-07-30T03:18:06.765Z 来源:《工程建设标准化》2022年37卷3月6期作者:孙楠李洪杰[导读] 为了提高大型锻件锻造水平,针对锻造工艺和缺陷控制技术展开分析。
孙楠李洪杰天津赛瑞机器设备有限公司天津 300301摘要:为了提高大型锻件锻造水平,针对锻造工艺和缺陷控制技术展开分析。
分别介绍大型锻件锻造工艺、缺陷产生与控制方法,了解各项工艺与技术在工业生产中的应用现状。
最后总结今后大型锻件锻造工艺、缺陷控制技术的发展方向,深入优化技术与工艺,旨在构建完善的大型锻件生产技术体系。
关键词:大型锻件;锻造工艺;缺陷控制技术;发展趋势大型锻件广泛应用于能源、交通、国防、钢铁、石化等工业,通常是机械设备的核心部件,例如:重型压力容器、水轮机大轴、汽轮机主轴、齿轮轴、发电机转子、船用大型曲轴、大型模块等,所以对大型锻件的晶粒组织和力学性能要求都比较高。
在某种意义上,大型锻件的锻造工艺和缺陷控制技术是衡量国家重工业发展水平的一个重要标志。
随着相关工业的快速发展,大型锻件的尺寸越来越大,对质量的要求也日益提高。
因此,提高大型锻件的锻造水平,规范其生产工艺,具有非常重要的意义。
一、大型锻件锻造工艺大型锻件主要特点是体形大、质量要求高、批量小、生产费用高、周期长,其生产过程包括:冶炼、铸造、锻造、热处理等多道工序[1]。
钢锭在铸造过程中,不可避免地会有一些偏析、缩孔、疏松等缺陷,并且钢锭体形越大,钢锭内部的缺陷就越明显,钢锭内部缺陷对大锻件的性能有着重要影响。
锻造消除或改善钢锭内部缺陷的主要目的有两个:“成形”和“改性”,前者将坯料变形到锻件所需要的形状,后者通过改变坯料的微观组织使锻件的力学性能达到要求。
大型锻件所用到的基本锻造工序是墩粗和拔长。
通过墩粗和拔长工序,能够改善坯料内部的疏松或孔洞等缺陷,以获得均质致密的微观组织,从而提升锻件的塑性和力学性能。
大型锻件粗晶缺陷的成因及控制措施

本文源自:中国无损检测论坛
金属材料的晶粒大小不是一成不变的,一般情况下,随着晶粒细化,钢的屈服强度、疲劳强度提高,同时具有很高的塑性和冲击韧性。
但发生粗晶时,锻材的塑性性能便会明显下降,影响了材料使用寿命。
粗晶影响因素:
1.变形温度
加热条件下,原子的活动能力增加,随着加热温度升高,原子的扩散能力增加,晶粒长大趋势加剧,细晶粒极易变为粗晶粒。
加热温度越高,粗晶越严重。
2、保温时间
高温保温时间越长,粗晶现象越严重,但较加热温度影响小。
3、变形程度
粗晶可以通过热变形消除,原始加热温度越高,所需变形程度越大。
预防粗晶应采取的措施:
1、锻造前加热温度应严格控制在平衡图固相线(AE)以下150-250℃。
保温时间不宜过长,要根据锭型确定合理的保温时间。
2、锻造变形可以打碎粗大的奥氏体晶粒,细化组织,消除粗晶。
3、锻造过程中应尽量避免出现锻件上只加热而不变形部分。
4、在决定最后一次的加热温度时,要根据剩余变形量决定,以免由于终锻温度过高,引起晶粒粗大,变形程度过小,锻造变形力传递不到锻件中心。
在锻造变形时,应避免小压下量变形工艺。
本文摘自: 中国无损检测论坛() 详细出处请参考:/forum.php?mod=viewthread&tid=669&extra=page%3D4。
大型锻件中常见的缺陷与对策

大型锻件中常见的缺陷与对策大型锻件中常见的缺陷与对策大型锻件中的缺陷,从性质上分为化学成分、组织性能不合格,第二相析出,类孔隙性缺陷和裂纹五大类。
从缺陷的产生方面可分为,在冶炼、出钢、注锭、脱模冷却或热送过程中产生的原材料缺陷及在加热、锻压、锻后冷却和热处理过程中产生的锻件缺陷两大类。
大型锻造中,由于锻件截面尺寸大,加热、冷却时,温度的变化和分布不均匀性大,锻压变形时,金属塑性流动差别大,加上钢锭大冶金缺陷多,因而容易形成一些不同于中小型锻造的缺陷。
如严重偏析和疏松,密集性夹杂物,发达的柱状晶及粗大不均匀结晶,敏感开裂与白点倾向,晶粒遗传性与回火脆性,组织性能的严重不均匀性,形状尺寸超差等等。
大型锻件中常见的主要缺陷有:1.偏析钢中化学成分与杂质分布的不均匀现象,称为偏析。
一般将高于平均成分者,称为正偏析,低于平均成分者,称为负偏析。
尚有宏观偏析,如区域偏析与微观偏析,如枝晶偏析,晶间偏析之分。
大锻件中的偏析与钢锭偏析密切相关,而钢锭偏析程度又与钢种、锭型、冶炼质量及浇注条件等有关。
合金元素、杂质含量、钢中气体均加剧偏析的发展。
钢锭愈大,浇注温度愈高,浇注速度愈快,偏析程度愈严重。
(1)区域偏析它属于宏观偏析,是由钢液在凝固过程中选择结晶,溶解度变化和比重差异引起的。
如钢中气体在上浮过程中带动富集杂质的钢液上升的条状轨迹,形成须状∧形偏析。
顶部先结晶的晶体和高熔点的杂质下沉,仿佛结晶雨下落形成的轴心∨形偏析。
沉淀于锭底形成负偏析沉积锥。
最后凝固上部区域,碳、硫、磷等偏析元素富集,成为缺陷较多的正偏析区。
图1为我国解剖的55t34CrMolA钢锭纵剖面硫印低倍图片及区域偏析示意图。
图1 钢锭区域偏析硫印示意图①“∧”型偏析带②“∨”型偏析带③负偏析区防止区域偏析的对策是:1)降低钢中硫、磷等偏析元素和气体的含量,如采用炉外精炼,真空碳脱氧(VCD)处理及锭底吹氩工艺。
2)采用多炉合浇、冒口补浇、振动浇注及发热绝热冒口,增强冒口补缩能力等措施。
大锻件镦粗变形力数值模拟误差的研究

大锻件镦粗变形力数值模拟误差的研究齐作玉;黄健;蔡宁【摘要】分析了由塑性加工原理理论推导出的镦粗变形力公式,还研究了用商业模拟软件求解镦粗变形力,将其公式结果以及模拟结果与以前实测结果进行比较,暴露出大锻件数值模拟商业软件存在着较大定量误差的问题。
分析了该问题产生的原因,提出了改进意见,为未来能在大锻件生产领域定量准确地应用数值模拟软件奠定了一定的理论和经验基础。
%The formula of upsetting deformation force which was deduced according to the plastic processingprinciple theory has been analyzed.Meanwhile, solving the upsetting formation force by adopting the commercial simu -lation software has been studied.By comparing the calculated results and the simulated results , as well as the previousactual measured results, the problem of major quantitative error which was founded in the process of numerical simula -tion of commercial software has been exposed .Therefore, the cause of this problem has been analyzed with improve -ment proposals, as so to lay a certain theoretical and experiential foundation for the future applying of numerical simula -tion software in the field of production for heavy forgings .【期刊名称】《大型铸锻件》【年(卷),期】2015(000)006【总页数】3页(P16-18)【关键词】大锻件;数值模拟;镦粗;变形力;误差【作者】齐作玉;黄健;蔡宁【作者单位】上海重型机器厂有限公司,上海200245;上海重型机器厂有限公司,上海200245;上海重型机器厂有限公司,上海200245【正文语种】中文【中图分类】O242目前大锻件数值模拟的应用还很不成熟。
锻造对金属组织、性能的影响与锻件缺陷

锻造对金属组织、性能的影响与锻件缺陷锻造对金属组织、性能的影响与锻件缺陷锻件的缺陷包括表面缺陷和内部缺陷。
有的锻件缺陷会影响后续工序的加工质量,有的则严重影响锻件的性能,降低所制成品件的使用寿命,甚至危及安全。
因此,为提高锻件质量,避免锻件缺陷的产生,应采取相应的工艺对策,同时还应加强生产全过程的质量控制。
概要介绍三方面的问题:锻造对金属组织、性能的影响与锻件缺陷;锻件质量检验的内容和方法;锻件质量分析的一般过程。
(一)锻造对金属组织和性能的影响锻造生产中,除了必须保证锻件所要求的形状和尺寸外,还必须满足零件在使用过程中所提出的性能要求,其中主要包括:强度指针、塑性指针、冲击韧度、疲劳强度、断裂韧度和抗应力腐蚀性能等,对高温工作的零件,还有高温瞬时拉伸性能、持久性能、抗蠕变性能和热疲劳性能等。
锻造用的原材料是铸锭、轧材、挤材和锻坯。
而轧材、挤材和锻坯分别是铸锭经轧制、挤压及锻造加工后形成的半成品。
锻造生产中,采用合理的工艺和工艺参数,可以通过下列几方面来改善原材料的组织和性能:1)打碎柱状晶,改善宏观偏析,把铸态组织变为锻态组织,并在合适的温度和应力条件下,焊合内部孔隙,提高材料的致密度;2)铸锭经过锻造形成纤维组织,进一步通过轧制、挤压、模锻,使锻件得到合理的纤维方向分布; 3)控制晶粒的大小和均匀度;4)改善第二相(例如:莱氏体钢中的合金碳化物)的分布; 5)使组织得到形变强化或形变——相变强化等。
由于上述组织的改善,使锻件的塑性、冲击韧度、疲劳强度及持久性能等也随之得到了提高,然后通过零件的最后热处理就能得到零件所要求的硬度、强度和塑性等良好的综合性能。
但是,如果原材料的质量不良或所采用的锻造工艺不合理,则可能产生锻件缺陷,包括表面缺陷、内部缺陷或性能不合格等。
(二)原材料对锻件质量的影响原材料的良好质量是保证锻件质量的先决条件,如原材料存在缺陷,将影响锻件的成形过程及锻件的最终质量。
如原材料的化学元素超出规定的范围或杂质元素含量过高,对锻件的成形和质量都会带来较大的影响,例如:S、B、Cu、Sn等元素易形成低熔点相,使锻件易出现热脆。
- 1、下载文档前请自行甄别文档内容的完整性,平台不提供额外的编辑、内容补充、找答案等附加服务。
- 2、"仅部分预览"的文档,不可在线预览部分如存在完整性等问题,可反馈申请退款(可完整预览的文档不适用该条件!)。
- 3、如文档侵犯您的权益,请联系客服反馈,我们会尽快为您处理(人工客服工作时间:9:00-18:30)。
Hot Working Technology 2015,Vol.44,No.13大型锻件组织与性能的影响因素及其控制技术黄倩1,温彤1,刘清1,张鹏2(1.重庆大学材料科学与工程学院,重庆400044;2.中国第二重型机械集团公司,四川德阳618000)摘要:内部组织性能是决定大锻件产品质量的重要因素。
介绍了冶炼、铸造、热塑性成形和热处理工艺对大型锻件组织均匀性的影响,概述了大型锻件组织均匀性研究的重点内容,探讨了大型锻件内部组织性能分析与控制的关键技术。
关键词:锻件;组织;均匀性;控制DOI:10.14158/ki.1001-3814.2015.13.002中图分类号:TG316文献标识码:A文章编号:1001-3814(2015)13-0006-03Affecting Factors and Control Technology of Microstructure andProperties of Large ForgingsHUANG Qian 1,WEN Tong 1,LIU Qing 1,ZHANG Peng 2(1.School of Materials Science and Engineering,Chongqing University,Chongqing 400044,China;2.China National Erzhong Group Co.,Deyang 618000,China)Abstract :Internal microstructure and performance are important factors to determine the quality of large forgings.The influences of smelting,casting,thermal plastic forming and heat treatment process on microstructure uniformity were introduced.The key contents of studying microstructure uniformity of large forgings were summarized.The key control technology and analysis of internal microstructure and performance of large forgings were discussed.Key words :forgings;microstructure;uniformity;control收稿日期:2014-07-20基金项目:国家重大科技专项项目(2012ZX04010-081)作者简介:黄倩(1990-),女,重庆人,硕士,主要研究方向:金属塑性成形;电话:1521511786;E-mail:742566018@大型锻件作为船舶、水电、核电、火电、冶金等领域大型装备的关键部件,在经济建设、国防和现代高科技重大装备制造中发挥重要作用。
近年来,我国大锻件制造发展迅速,许多领域已稳居世界第一。
据不完全统计,迄今我国拥有约140台自由锻液压机,其中120MN 有3台[1],二重集团公司已建成世界最大的800MN 液压机1台。
目前,国内可浇铸的最大钢锭重量超过600t ,可生产重260~320t 大型锻件[1]。
由于大锻件通常用于大型设备的核心部位,工况特殊、受力复杂,对选材和成形工艺质量要求很高。
其中,大型锻件的组织均匀性是决定零件质量的重要因素。
从广义来讲,锻件的组织均匀性涉及锻件内部化学成分、相组成与力学性能等方面。
而大锻件的冶炼、铸锭、制坯、预锻、终锻、热处理等各个生产环节,都会对组织均匀性产生重大影响。
但目前相关的研究主要集中在塑性成形阶段。
为此,本文在对大锻件组织均匀性的内涵进行梳理的基础上,从冶金、塑性成形到热处理的各个工艺环节探讨影响大型锻件组织均匀性的主要因素,分析了大型锻件组织均匀性与关键控制技术。
1冶炼与铸锭过程对大锻件组织均匀性的影响保证钢液化学成分符合冶炼要求是大型锻件用钢锭冶炼的主要内容,需尽量减少磷、硫、非金属夹杂物及气体的含量。
锻件的铸锭一般为镇静钢锭,钢锭内部缺陷主要有夹杂物、气孔、偏析、缩孔和疏松等,且各种缺陷的分布位置不同。
这些缺陷的形成与金属的冶炼、浇注和结晶密切相关,且不可避免。
随着铸锭尺寸的增大,铸锭内部化学成分、组织和夹杂物分布不均匀情况愈为严重,成为大型锻件报废的主要原因。
因此在铸锭冶炼过程应根据不同冶炼过程采取相应的控制技术,以减少产品报废。
以二重公司生产的600MW 核电稳压器为例[2],对所使用的16MND5(A508-3)核电钢的纯净度、性能指标、探伤检验等要求极其苛刻。
目前国内外超纯净钢的生产,多采用各种先进的炉外真空精炼、真空浇注技术。
为了得到高质量的粗炼钢水,采用电炉或碱性平炉进行冶炼,将钢水倒入钢包精炼炉中进行高真●综述●6《热加工工艺》2015年7月第44卷第13期空精炼,再使用真空吹氩浇注[2]。
此方法提高了成品钢水的冶炼质量和浇注质量,有效地指导大量核电用钢的实际生产。
为了保证钢锭成分均匀性、锻造棒坯的组织均匀性及性能的要求,应在冶炼时尽量地除去钢液中的气体与杂质。
吴贵林[3]等采用6t真空感应炉和7t 真空白耗炉,冶炼得到直径为660mm、重量达6000kg 真空自耗锭,用来生产直径为1200mm、重量达1300kg的GH4698合金涡轮盘,满足了大锻件用铸锭的质量、性能要求。
数值模拟在铸造充型流动、凝固及温度场和残余应力的研究中取得了很大进展,且成功地应用到大型铸件凝固的模拟中,用以分析工艺优化及质量控制。
数值模拟可分析铸造充型过程的熔体流动、填充、排气和温度变化,且可有效地预测隐藏于铸件内部的缩孔缩松的位置。
因此,可根据预测缺陷位置制定相应解决工艺方案,有效消除铸件缺陷。
2热成形对大锻件组织均匀性的影响形状与尺寸是锻造工艺设计需要考虑的首要问题。
锻件微观组织均匀、细致,综合力学性能就会更佳。
因此,从本质上讲,塑性成形过程包括了“改形”与“改性”两个方面,而后者对于大型锻件尤为重要。
大锻件热锻的“改性”为后续热处理奠定良好的微观组织基础,可使后续热处理发挥作用。
对某些特殊材料的锻件,后续热处理不能有效地改变其微观组织,因此锻造工艺就是决定锻件最终组织和性能的关键因素。
为了将大锻件铸坯的铸态组织转变为变形组织,满足力学性能的要求,通常都要有一定程度的塑性变形量(锻比)。
在锻合锻件内部孔穴、疏松,提高锻件切向性能,减小锻件性能的各向异性,采用型砧拔长比镦粗更为有效。
生产实践中,为了通过热塑性成形实现大锻件组织性能的改善,必须有效控制塑性变形过程中各个区域的应力、应变。
针对不同阶段的要求,开发了WHF(宽砧大压下量锻造法)、JTS(中心压实法)、FM法(不对称平砧锻造法)、FMV(不对称V型砧锻造法)、FML(低锻压力锻造法)、CKD(用于锻造管板的工艺)、平砧锻造八面坯法、极限锻造法等各种自由锻工艺。
为了研究热塑性成形过程对锻件内部裂纹及组织的影响,刘丽娟[4]等对30Cr2Ni4MoV低压转子钢内部的裂缝进行了高温塑性变形焊合试验。
当变形量、保温时间及温度满足一定条件时,锻件裂缝可以通过扩散及再结晶等机制进行焊合。
大锻件材料在锻造的热塑性成形过程中,受高温和变形的同时作用,坯料形状发生改变、内部微观组织也经历着应变硬化、动态回复和再结晶等演化。
因此,大锻件热塑性成形过程中的组织性能变化是一个重要问题,但目前实践中还较少主动考虑微观组织(例如晶粒度)的控制问题。
实际生产中,锻件可能会出现组织不均匀、粗晶、混晶等缺陷,使组织性能不合格。
特别是涡轮盘、起落架等典型航空锻件多火次锻造或坯料设计不合理时,就容易出现这类问题。
目前已有很多相关研究[5-7]。
细小均匀的晶粒会直接影响锻件力学性能。
为了获得变形力小和晶粒细小的锻件,可以采取相应的措施优化预成形形状。
数值模拟技术已经在分析体积成形过程的塑性变形方面(即“锻件改形”)取得了很大的成功。
近年来,在塑性成形过程模拟中,考虑材料微观组织的演变成为塑性成形模拟技术的重要发展内容。
为了得到理想的模拟结果,建立合理的热成形过程微观组织演变的数学模型是一个关键。
概括起来,现有数学模型主要包括4个方面[8]:静态再结晶模型;动态再结晶模型;亚动态再结晶模型;晶粒长大模型。
模型公式一般都是以Avirami方程为基础,且同一参量所涉及的变形工艺参数大致上相同,回归系数之间有一定差异[8]。
例如动态再结晶常用的Sellar、Yada、Kopp等模型,采用Avirami形式的动力学方程来描述动态再结晶程度,给出再结晶尺寸和体积百分数。
元胞自动机(cellularautomata,简称CA)法可模拟晶粒长大过程,计算机模拟结果表明元胞自动机法反映的拓扑特征、晶界迁移规律符合晶粒长大的机制,是一种简单、有效的晶粒长大模拟方法[9]。
3热处理对大锻件组织均匀性的影响大型锻件的热处理主要目的包括消除应力、调整硬度、预防白点,以及提高化学成分均匀性,调整与细化锻件组织。
通常对钢锭采取均匀化退火(或称扩散退火)以消除经冶金处理后钢锭内部组织不均匀和偏析等缺陷。
根据相关试验,对R521冶金组织不理想的钢锭在始锻温度下增加锻造加热温度、延长锻件保温时间进行均匀化退火[10],这种方法不仅可以获得均匀化退火的效果,且可弥补增加中间热处理工序使生产成本增加的不足。
有些锻件在最终热处理后还需进行机加工,这时最终热处理就成为了保证机加工锻件性能的关键环节。
王珉、刘慧琳[11]介绍了16MND5稳压器锻件制造过程中热处理和机械加工两个关键工艺。
采用预备热处理及性能热7Hot Working Technology2015,Vol.44,No.13处理两种热处理工艺,对锻件不同部位采取不同热处理工艺,使锻件的力学性能满足其技术要求。
4大型锻件组织均匀性研究的重点内容4.1大型锻件组织均匀性的表征与分析大型锻件组织的均匀性涉及锻件内部的化学成分、相组成与力学性能等多个方面,需要采用适当方式对各种性质的组织均匀性问题进行定量的表征,才能满足理论与试验分析的要求。
如利用现代电子显微观测分析等手段对大锻件组织进行系统研究,建立化学成分分布、晶粒度与相组织、力学性能(各向异性)等的理论表征模型。
建立大锻件组织均匀性的表征与分析手段。
4.2大型锻件组织均匀性的影响因素大型锻件内部组织的均匀性取决于冶炼、制坯、锻造成形以及后续热处理等各个工艺环节,影响因素众多,也极其复杂。
因此,需要从大型锻件的铸锭、制坯、锻造到热处理的生产全过程进行系统分析,弄清楚影响大锻件内部组织均匀性的各种因素及其程度、方式与机理。