功能性试验
给水管道功能性试验

给水管道功能性试验一.强度严密性试验1.管道宜分层试压,上水时最高点要有排气装置,高低点各装一块压力表,上满水后检查管网有无渗漏,在升压时如出现渗漏时应做好标记,卸压后处理,必要时泄水处理。
2、试压用的压力表不少于两只;精度不低于1.5级,量程应为试验压力的L5~2倍。
3、对不能参与试压的设备、仪表、阀门及附件应加以隔离或拆除。
4、强度试验的测试点应设在系统管网的最低点。
对管网注水时,应将管网内的空气排净,并应缓慢升压。
给水及采暖管道试验压力为0.6Mpa o5、达到试验压力后管道稳压10分钟压力降不大于0.02MPa,然后降到工作压力进行检查,应不渗不漏。
二.冲洗■消毒1.管道系统在验收前应进行通水冲洗,冲洗水水质经有关水质部门检验合格为止。
冲洗水总流量可按系统进水口处的管内流速1.5m∕s计,从下向上逐层打开配水点龙头或进水阀进行放水冲洗,放水时间不小于Imin,同时放水的龙头或进水阀的计算当量不应大于该管段的计算当量的1/4,冲洗时间以出水口水质与进水口水质相同时为止。
放水冲洗后切断进水,打开系统最低点的排水口将管道内的水放空。
2、管道冲洗后,用含20~30mg∕L的游离氯的水灌满管道,对管道进行消毒。
消毒水滞留24h后排空。
3、管道消毒后打开进水阀向管道供水,打开配水点龙头适当放水,在管网最远配水点取水样,经卫生监督部门检验合格后方可交付使用。
=■通水试验1.管道试压完成后应进行通水试验。
2、通水时打开所有给水系统的配水点,排水系统按给水系统的1/3配水点同时开放,检查各出水口及排水点水流畅通,接口无渗漏。
四.灌水试验1.雨水及重力流排水管道必须做灌水试验,雨水管注水高度到每根立管上层的雨水斗,排水管灌水高度应不低于底层卫生器具的上边缘或底层地面高度。
2、检验方法:满水15分钟水面下降后,再灌满观察5分钟,液面不降,管道及接口无渗漏为合格。
五.通球试验排水主立管及水平干管管道均应做通球试验,通球球径不小于排水管道管径的2/3,通球率达到100%。
管道功能性实验考点

【考点】管道功能性试验给水排水管道功能性试验包括压力管道的水压试验、无压管道的严密性试验和给水管道的冲洗与消毒。
一、压力管道的水压试验(一)基本规定(1)分为预试验和主试验阶段;试验合格的判定依据分为允许压力降值和允许渗水量值,按设计要求确定。
设计无要求时,应根据工程实际情况,选用其中一项值或同时采用两项值作为试验合格的最终判定依据;水压试验合格的管道方可通水投入运行。
(2)水压试验进行实际渗水量测定时,宜采用注水法进行。
(3)管道采用两种(或两种以上)管材时,宜按不同管材分别进行试验;不具备分别试验的条件必须组合试验,且设计无具体要求时,应采用不同管材的管段中试验控制最严的标准进行试验。
(4)大口径球墨铸铁管、玻璃钢管、预应力钢筒混凝土管或预应力混凝土管等管道单口水压试验合格,且设计无要求时,可免去预试验阶段,而直接进行主试验阶段。
(5)管道的试验长度1)除设计有要求外,水压试验的管段长度不宜大于1.0km。
(二)管道试验方案与准备工作1.试验方案主要内容包括:后背及堵板的设计;进水管路、排气孔及排水孔的设计;加压设备、压力计的选择及安装的设计;排水疏导措施;升压分级的划分及观测制度的规定;试验管段的稳定措施和安全措施。
2.准备工作(1)试验管段所有敞口应封闭,不得有渗漏水现象。
(2)试验管段不得用闸阀做堵板,不得含有消火栓、水锤消除器、安全阀等附件。
3.管道内注水与浸泡(1)应从下游缓慢注入,注入时在试验管段上游的管顶及管段中的高点应设置排气阀,将管道内的气体排除。
(2)试验管段注满水后,宜在不大于工作压力条件下充分浸泡后再进行水压试验,浸泡时间规定:1)球墨铸铁管(有水泥砂浆衬里)、钢管(有水泥砂浆衬里)、化学建材管不少于24h;2)内径大于1000mm的现浇钢筋混凝土管渠、预(自)应力混凝土管、预应力钢筒混凝土管不少于72h;3)内径小于1000mm的现浇钢筋混凝土管渠、预(自)应力混凝土管、预应力钢筒混凝土管不少于48h。
管道的功能性试验
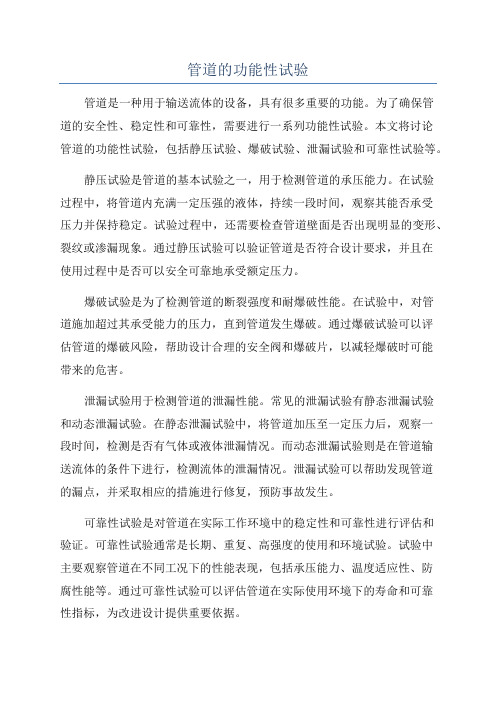
管道的功能性试验管道是一种用于输送流体的设备,具有很多重要的功能。
为了确保管道的安全性、稳定性和可靠性,需要进行一系列功能性试验。
本文将讨论管道的功能性试验,包括静压试验、爆破试验、泄漏试验和可靠性试验等。
静压试验是管道的基本试验之一,用于检测管道的承压能力。
在试验过程中,将管道内充满一定压强的液体,持续一段时间,观察其能否承受压力并保持稳定。
试验过程中,还需要检查管道壁面是否出现明显的变形、裂纹或渗漏现象。
通过静压试验可以验证管道是否符合设计要求,并且在使用过程中是否可以安全可靠地承受额定压力。
爆破试验是为了检测管道的断裂强度和耐爆破性能。
在试验中,对管道施加超过其承受能力的压力,直到管道发生爆破。
通过爆破试验可以评估管道的爆破风险,帮助设计合理的安全阀和爆破片,以减轻爆破时可能带来的危害。
泄漏试验用于检测管道的泄漏性能。
常见的泄漏试验有静态泄漏试验和动态泄漏试验。
在静态泄漏试验中,将管道加压至一定压力后,观察一段时间,检测是否有气体或液体泄漏情况。
而动态泄漏试验则是在管道输送流体的条件下进行,检测流体的泄漏情况。
泄漏试验可以帮助发现管道的漏点,并采取相应的措施进行修复,预防事故发生。
可靠性试验是对管道在实际工作环境中的稳定性和可靠性进行评估和验证。
可靠性试验通常是长期、重复、高强度的使用和环境试验。
试验中主要观察管道在不同工况下的性能表现,包括承压能力、温度适应性、防腐性能等。
通过可靠性试验可以评估管道在实际使用环境下的寿命和可靠性指标,为改进设计提供重要依据。
除了上述几种功能性试验,根据实际需要还可以进行其他试验,比如冲击试验、腐蚀试验、振动试验等。
这些试验可以更全面地评估管道的性能和可靠性,为确保管道安全工作提供科学依据。
总之,管道的功能性试验是确保管道安全可靠运行的重要手段。
通过静压试验、爆破试验、泄漏试验和可靠性试验等一系列试验,可以评估管道的性能和可靠性,及时发现问题并采取相应措施,以确保管道在工作过程中不会发生泄漏、破裂等事故,保护人员生命财产安全。
功能性能试验 流程

功能性能试验流程英文回答:Functional Performance Testing (FPT)。
Functional Performance Testing (FPT) is a type of performance testing that aims to evaluate the functional behavior of a system under varying performance conditions.It assesses how a system performs under realistic workloads to ensure that it meets specific functional requirements.Key Objectives of FPT:Evaluate the system's ability to handle peak or sustained workloads.Identify performance bottlenecks and capacity limitations.Ensure the system meets specified performance criteria.Verify the system's response times and throughput under different conditions.Validate the system's scalability and elasticity.Types of FPT Tests:Load Testing: Simulates real-world user traffic and gradually increases the load to determine the system's performance under varying load conditions.Stress Testing: Pushes the system beyond its normal operating limits to assess its stability and performance under extreme scenarios.Endurance Testing: Runs the system over an extended period of time to evaluate its resilience and performance degradation over time.Spike Testing: Injects sudden, unexpected spikes in traffic to simulate real-world scenarios where trafficpatterns fluctuate rapidly.Isolation Testing: Isolates specific components or services to pinpoint their impact on overall system performance.Methodology of FPT:Define performance requirements and acceptance criteria.Design and develop test scenarios based on real-world usage patterns.Configure the test environment with realistic workloads and traffic distributions.Execute the test scenarios and monitor key performance indicators (KPIs)。
管道功能性试验范文

管道功能性试验范文一、水压试验水压试验是最基本也是最常见的管道功能性试验。
其目的是验证管道系统是否能承受设计压力下的水压。
具体方法是将管道密封好后,使用水泵将水注入管道系统,逐步增加压力至设计压力。
在保持一段时间后,观察管道是否有渗漏或变形现象。
若在测试过程中未发现问题,则可认为管道系统通过了水压试验。
二、泄漏测试泄漏测试是为了检测管道系统是否存在泄漏现象。
方法是使用气体或流体充填管道系统,并施加一定的压力,然后通过监测压力变化或检测泄漏点来确认是否存在泄漏。
常用的泄漏测试方法有气压测试和液压测试。
在进行泄漏测试时,需要注意选择合适的试验介质和压力,以及正确操作测试设备。
三、流量测试流量测试用于验证管道系统的流量是否满足设计要求。
测试方法是通过给定的流量计,测量单位时间内通过管道的流体量。
流量测试包括静态流量测试和动态流量测试两种方法。
静态流量测试是通过关闭管道两端的阀门,并引入稳定的流量,测量管道内的静态流体量。
动态流量测试是通过在管道内流动的流体中加入速度测量装置,测量管道内流体的实时流速。
四、冲洗测试冲洗测试用于检测管道系统是否具备良好的冲洗功能。
冲洗是指通过给管道系统内提供高速的定向流动流体,以清洗污垢、异物和沉积物的过程。
测试方法是在管道系统内注入一定浓度的污染物,然后利用冲洗设备提供高速水流,观察管道系统是否能有效清洗出污物。
冲洗测试的目的是验证管道系统内部的水流动力学是否能满足冲洗要求,以确保管道系统的正常运行和维护。
在进行管道功能性试验时,有一些注意事项需要遵守。
首先,要保证试验过程的安全性,合理选择试验介质和压力,确保没有危险因素存在。
其次,试验前要确保管道系统已彻底清洗干净,不含任何杂物和污染物。
另外,在试验过程中要注意操作规范,确保测试设备的准确性和可靠性。
最后,在试验结束后,要对试验结果进行记录和分析,及时处理发现的问题,并对系统进行必要的调整和维修。
总之,管道功能性试验对于确保管道系统正常运行至关重要。
管道功能性试验
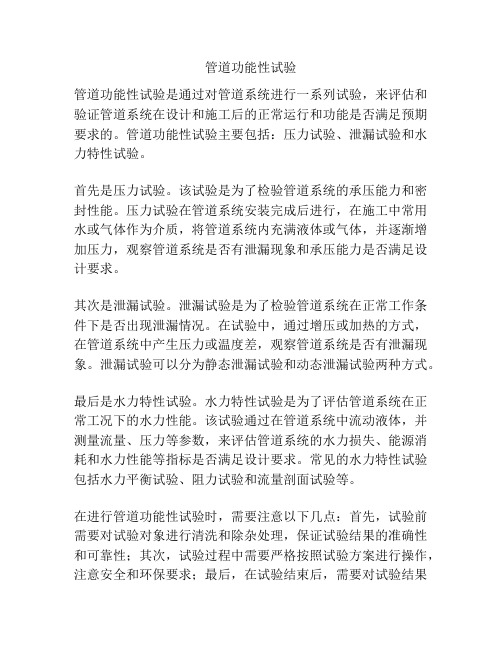
管道功能性试验管道功能性试验是通过对管道系统进行一系列试验,来评估和验证管道系统在设计和施工后的正常运行和功能是否满足预期要求的。
管道功能性试验主要包括:压力试验、泄漏试验和水力特性试验。
首先是压力试验。
该试验是为了检验管道系统的承压能力和密封性能。
压力试验在管道系统安装完成后进行,在施工中常用水或气体作为介质,将管道系统内充满液体或气体,并逐渐增加压力,观察管道系统是否有泄漏现象和承压能力是否满足设计要求。
其次是泄漏试验。
泄漏试验是为了检验管道系统在正常工作条件下是否出现泄漏情况。
在试验中,通过增压或加热的方式,在管道系统中产生压力或温度差,观察管道系统是否有泄漏现象。
泄漏试验可以分为静态泄漏试验和动态泄漏试验两种方式。
最后是水力特性试验。
水力特性试验是为了评估管道系统在正常工况下的水力性能。
该试验通过在管道系统中流动液体,并测量流量、压力等参数,来评估管道系统的水力损失、能源消耗和水力性能等指标是否满足设计要求。
常见的水力特性试验包括水力平衡试验、阻力试验和流量剖面试验等。
在进行管道功能性试验时,需要注意以下几点:首先,试验前需要对试验对象进行清洗和除杂处理,保证试验结果的准确性和可靠性;其次,试验过程中需要严格按照试验方案进行操作,注意安全和环保要求;最后,在试验结束后,需要对试验结果进行分析和评估,并制定相应的措施和方案,确保管道系统的正常运行和功能满足设计要求。
总之,管道功能性试验是保证管道系统正常运行和功能是否符合预期要求的重要手段。
通过压力试验、泄漏试验和水力特性试验等试验措施,可以对管道系统的承压能力、密封性能和水力特性等进行评估和验证,为工程项目的顺利进行提供保障。
各类管道功能性试验汇总

各类管道功能性试验汇总管道功能性试验是一种用来评估管道在设计和操作过程中是否能够满足预期功能要求的实验方法。
这种试验通常涉及对管道的流量、压力、温度等重要参数进行测量和分析,以验证管道系统的可靠性、效率和安全性。
以下是各类管道功能性试验的汇总。
1.流量测试:流量测试是管道功能性试验中最常见和基础的实验之一、它的目的是测量管道中的液体或气体的流量,并验证其是否符合设计要求。
流量测试通常会使用流量计或其他流量测量设备进行,包括涡街流量计、超声波流量计等。
这些设备能够精确测量流体通过管道的速度和体积,并将其转化为流量数据。
2.压力测试:压力测试是管道安全性的重要组成部分。
它的目的是测量管道系统中的压力,并确保其在设计条件下能够承受预期的压力。
压力测试通常分为静态压力测试和动态压力测试两种类型。
静态压力测试是在管道系统闭合的情况下进行,以测量管道中的静态压力。
动态压力测试通常会模拟实际工作条件下的压力变化,以评估管道的稳定性和耐压能力。
3.温度测试:温度测试是检验管道系统热交换性能和温度控制能力的试验。
它的目的是测量管道中的温度,并检验其是否在设计范围内保持稳定。
温度测试通常会使用温度计或其他温度传感器进行,包括接触式温度计、红外线热像仪等。
这些设备能够准确测量管道中的温度变化,并将其转化为数字或图形数据。
4.泄漏测试:泄漏测试是衡量管道系统安全性和密封性的关键试验。
它的目的是检测管道系统中是否存在泄漏点,并评估其泄漏程度。
泄漏测试通常包括压力泄漏测试和真空泄漏测试两种类型。
压力泄漏测试是在管道系统正常工作压力下进行,以发现管道系统中的压力泄漏点。
真空泄漏测试则是在管道系统抽真空的条件下进行,以发现管道系统中的真空泄漏点。
5.排放测试:排放测试是对管道系统排放性能的评估试验。
它的目的是测量管道系统中的排放物的浓度和排放速率,并确保其在规定的范围内。
排放测试通常会使用气体分析仪、颗粒物采样器等设备进行,以定量分析管道系统中的VOCs、SOx、NOx等排放物。
工器具试验技术方案
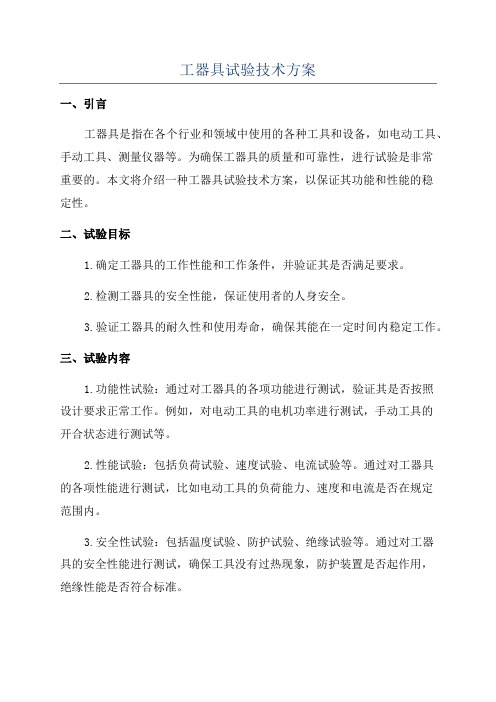
工器具试验技术方案一、引言工器具是指在各个行业和领域中使用的各种工具和设备,如电动工具、手动工具、测量仪器等。
为确保工器具的质量和可靠性,进行试验是非常重要的。
本文将介绍一种工器具试验技术方案,以保证其功能和性能的稳定性。
二、试验目标1.确定工器具的工作性能和工作条件,并验证其是否满足要求。
2.检测工器具的安全性能,保证使用者的人身安全。
3.验证工器具的耐久性和使用寿命,确保其能在一定时间内稳定工作。
三、试验内容1.功能性试验:通过对工器具的各项功能进行测试,验证其是否按照设计要求正常工作。
例如,对电动工具的电机功率进行测试,手动工具的开合状态进行测试等。
2.性能试验:包括负荷试验、速度试验、电流试验等。
通过对工器具的各项性能进行测试,比如电动工具的负荷能力、速度和电流是否在规定范围内。
3.安全性试验:包括温度试验、防护试验、绝缘试验等。
通过对工器具的安全性能进行测试,确保工具没有过热现象,防护装置是否起作用,绝缘性能是否符合标准。
4.耐用性试验:包括振动试验、冲击试验、耐腐蚀试验等。
通过对工器具进行长时间的振动、冲击、腐蚀等试验,验证其使用寿命和耐久性。
5.环境试验:包括温湿度试验、防尘试验等。
通过对工器具在各种环境条件下进行测试,验证其适应各种环境的能力。
四、试验方案1.选择适当的试验方法和仪器设备,如电压表、电流表、负荷试验台等。
根据工器具的特点和要求制定试验方案。
2.设定试验参数,如负荷大小、频率、温度、湿度等。
根据相关标准和要求进行设置。
3.进行试验前的准备工作,如校准仪器、查看试验样品和试验装置的完整性、清理试验场地等。
4.进行试验,并记录所有的试验数据和结果。
对于出现的异常情况,要及时记录和处理。
5.根据试验结果进行数据分析和评估。
判断工器具是否符合要求,是否需要进行改进和优化。
6.根据试验结果制定相关的技术标准和规范,以便后续生产和使用中的参考。
五、试验结果的评价与应用通过对工器具的试验,可以获得其性能和功能的评估结果。
- 1、下载文档前请自行甄别文档内容的完整性,平台不提供额外的编辑、内容补充、找答案等附加服务。
- 2、"仅部分预览"的文档,不可在线预览部分如存在完整性等问题,可反馈申请退款(可完整预览的文档不适用该条件!)。
- 3、如文档侵犯您的权益,请联系客服反馈,我们会尽快为您处理(人工客服工作时间:9:00-18:30)。
管道吹扫→部分回填→强度试验→严密性试验→全部回填
管道清(吹) 洗
二者试验方案的主要内容 1、后背及堵板的设计 2、进水管路、排气孔及排水孔的设计 3、加压设备、压力计的选择及安装设计 4、升压分级的划分和观测制度的规定 5、试验管段的稳定措施和安全措施 6、排水疏导措施
吹扫:1、管道安装工程除补口、涂漆外已按图纸组装完成 2、试压前按设计要求顺序进行了气体吹扫或清管球清扫,每 次吹扫管道长度不宜超过500m,超过则分段清扫。 3、吹扫气体流速不小于20m/s。 4、清管球在压缩空气推动下,管道内残存水、尘土、铁锈、 焊渣等杂物无球清至管道末端收球筒内,杂物从清扫口排出 。 注意事项:1、宜采用空气、严禁采用氧气和可燃性气体 2、吹扫管内的调压器、阀门、孔板、过滤网、燃气表等设备 不参加吹扫,吹扫合格后安装复位。 3、吹扫口与地面夹角宜为30~45°。 4、不同管径的管道应断开分别进行吹扫。
功能性试验
准备工作(必 备条件) 1、实验前编制 试验方案,并 经监理(建 设)、设计单 位审查同意 2、实验前对有 关操作人员进 行安全技术交 底 试验介质 试验顺序
水池满水试验
给排水压力管道水压试验
无压管道严密性试验
供热管道 强度试验 严密性试验 强度试验
燃气管道 严密性试验
园林理水 水压试验 泄水试验
试验压力:1、PN<5kPa, 取20kPa 2:PN≥5kPa,取max (1.15PN,0.1MPa) 所有未参加严密性试验的设 备、仪表、管件在试验后复 位,按设计压力对系统升 压,用发泡剂检查附件及连 接处,不漏者合格
喷灌系统施工流 程:定线→挖基坑 和沟槽→确定水源 泄水试验对于 和给水方式→安装 冬季有冻害地 管道→冲洗→水压 区是必须的 试验与泄水试验→ 回填→试喷
试压压力为工作压 力的1.5倍,且不小 水压:缓升至50%试验压力→初 于0.6MPa,试验压 管道内充气至30%~60%→稳 试验压力下稳压10min→ 稳压1h内(一级管网、换热 检,要求无渗漏无异常→升至 力下10min(化学管 压30min,检查系统有无异 无渗漏无压力降后降至设 站)或30min内,压力降≤ 试验压力→稳压1h→观测压力 材1h)内压力降不 常→升至试验压力→稳压≥ 计压力→设计压力稳压 0.05MPa,管道、焊缝、管路 计≥30min,无压力降为合格 应大于0.05MPa,然 24h(每小时记录不小于一 30min,无渗漏、无异常 附件及设备无渗漏,固定支架 气压:压力达到试验压力→稳 后降至工作压力进 次),修正压力降不超 声响、无压力降 无明显变形为合格 压1h→肥皂水检查接口,无漏 行检查,压力保持 133Pa合格 气为合格 不变,不渗不漏。 发现漏水及时修 补,直至不漏 1、试验所用压力表的精度不低于1.5级,量程为试验压 力1.5~2倍,数量不少于2块,表盘直径不小于100mm,在 检定有效期内。 2、试验长度为一个完整设计工段。 3、管道存在较大高差时,试验压力以最高点设计压力为 准,最低点压力不超过管道及设备承受压力。 试验压力:1.25倍设计压力且 ≥0.6MPa 试验目的:管道全部安装完成 后的全面检验 钢外护管焊缝在严密性试验合 格后进行,介质为空气,压力 缓慢上升至试验压力0.2MPa, 稳压10min,焊缝刷涂发泡剂 检查,无渗漏为合格
试验压力:1.5倍设计压 力且≥0.6MPa 试验目的:管道本身强度 +安装焊口强度 温度:5℃以上 试验时发现渗漏,严禁带 压处理,消除缺陷后重新 试验
试验压力及介质:1、PN(设计 压力)>0.8MPa的钢管,水压, 试验压力=1.5PN 2、PN≤0.8MPa的钢管、所有球 墨铸铁管、钢骨架聚乙烯复合 管(SDR11),气压,试验压力 =1.5PN且≥0.4MPa 3、聚乙烯管(SDR17.6),气 压,试验压力=1.5PN且≥ 0.2MPa 试验管道最大长度:PN≤0.4 (MPa),1000m;0.4<PN≤ 1.6,5000m;0.6<PN≤ 4,10000.
水
水
水或空气
洁净水
洁净水
空气或清洁水
空气
水
水
部分回填(埋地管道管顶以上0.5m) 严密性试验(闭水、闭气)→ →水压试验→给水管道冲洗与消毒→ 回 全部回填 填
强度试验→严密性试验→回填 水冲洗:连续进行、加大流量,平均流速≥1m/s;冲洗 前满水浸泡,水流方向同设计介质流向,严禁逆向冲 洗;清洗合格后,对排污管、除污器人工清洗,保证管 内清洁(注意事项:1、供热的供水回水管道及凝结水管 道须用清水清洗。2、清洗前将系统内流量孔板、滤网、 温度计、调节阀、止回阀阀芯拆除。3、冲洗顺序:主干 线、次干线、支线,二级管网单独冲洗。3、清洗出口管 径断面不小于原断面1/3) 蒸汽吹洗:吹洗前暖管,阀门开启缓慢进行,避免气 锤,检查管道连接、设备工作情况,恒温1h后吹洗;吹 洗后及时在管座、管端掏除污物,将流量孔板、滤网、 调节阀原样装回(注意事项:1、蒸汽管道必须蒸汽吹洗 。2、排气管引出室外,管口不得朝下临时固定,以免吹 洗反作用力。3、吹洗出口管以斜上方45°为宜,距出口 100m范围内不得有人工作或怕烫建筑物,吹洗时专人检 查保护。4、吹洗压力不大于工作压力的75%。5、排气管 截面不小于被吹洗管50%)
注水1/3设计水深→停≥24h(观测 24h水位下降值)→注水到2/3设计 水深停≥24h(观测24h水位下降 值)→注水到设计水深→停24h→ 实验流程及合 观测水位初读数→间隔24h→观测 末读数 格标准 合格标准:1、钢筋砼结构渗水量 不超过2L/(㎡·d),砌体结构不超 过3L/(㎡·d) 2、且水池外侧无明显水渍
预实验:水压缓慢升至试验压力→稳 压30min(可注水补压)。检查管道接 口、配件有无漏水、损坏 主试验:1、允许压力降值判断:停止 注水补压→稳压15min,压力下降不超 过允许压力下降值→降至工作压力, 恒压30min,无漏水现象 2、允许渗水量值判断:注水法试验 (多用)、放水法试验。
闭水:补水保持试验水头恒 定,观测时间≥30min,渗水量 不超过允许值 闭气:地下水位低于管底 150mm,温度-15~50℃,管堵密 封管道两端,充气至一定压 力,测定压力值,气压2000Pa 时开始计时,规定时间后结束 计时,测罐内压力P应≥ 1500Pa;管径≥1.6m,计算管内 气压降修正值△P应<500Pa
1、砼或砌体的砂浆强度达到设计 要求 2、现浇砼池体防水、防腐层前; 配式预应力砼池体施加预应力且锚 固段封锚以后;砖砌池体防水后; 石砌勾缝后 3、孔洞、管口临时封堵 4、池体抗浮稳定 5、充水、充气、排水系统就绪 6、安全措施到位
1、管道及检查井外观质量验收 合格 2、未回填、槽内无积水 1、所有敞口封闭、不得渗漏水 3、管道两端封堵,不得渗水 2、不得用闸阀做堵板,不得含有消火 4、管道两端堵板承载力经核算 防腐保温施工及设备安装 (系统设备安装齐全且防腐保 栓、水锤消音器、安全阀等附件 稍大于水压力的合力 之前 温完成) 3、清除管道内杂物 ,除预留进出水管外,应封堵 4、水源引接、排水疏导方案 坚固,不得渗水 5、顶管施工,其注浆孔封堵 6、水源引接、排水疏导方案
1、试验用的压力机及温度记录 仪应在校验有效期内 2、实验方案已获批准,有可靠 的通信系统和安全保障措施, 已进行技术交底 3、管道焊接检验、清扫合格 4、埋地管道回填土至管上方 0.5m以上,并流出焊接口 5、试验用仪表安装完毕,符合 规范要求
1、试验用的压力机及温度 记录仪应在校验有效期内 2、强度试验合格、管道安 开口部分全部封 装完成后,埋地的回填土至 水压试验合格 闭,竖管用堵头封 管顶0.5m以上 后进行 闭,逐段进行试压 3、实验方案已获批准,有 可靠的通信系统和安全保障 措施,已进行技术交底
打开所有手动 泄水阀,截断 立管堵头,以 免管道中出现 负压,影响泄 水效果。只要 管道无满管积 水现象,即合 格。
注意事项
1、闭水试验带井试验、一次不 超过5个连续井段 2、管道内径>700mm,井段数 量抽样选取1/3试验,不合格 时,抽样井段数量在原基础上 1、从下游缓慢注入,高点设置排气阀 加倍进行试验 渗水量按池壁和池底浸湿面积计 2、浸泡时间:非砼管≥24h,内径≤ 3、试验水头:试验水头不超管 算,测定时间必须连续,符合标准 1m砼管≥48h,内径>1m砼管≥72h 顶内壁,内壁+2m,超管顶内 时,需连续测定两次以上 3、水压试验管段长度不宜大于1km 壁,设计水头+2m,试验水头小 于10m且已超过上游检查井扣, 取上游检查井扣高度 4、污水、雨污合流、湿陷土膨 胀土及流沙区的雨水管必须做 另:注水浸泡时间≥24h