真空电镀中射频功率对镀层性能的影响研究
电镀参数对电镀镍层性能的影响
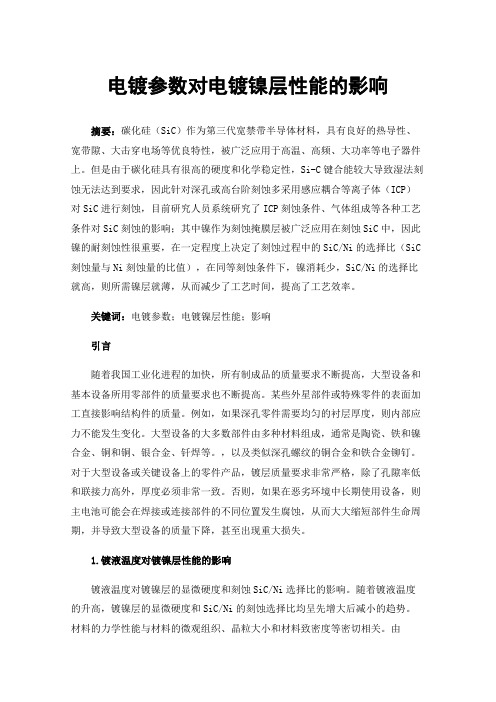
电镀参数对电镀镍层性能的影响摘要:碳化硅(SiC)作为第三代宽禁带半导体材料,具有良好的热导性、宽带隙、大击穿电场等优良特性,被广泛应用于高温、高频、大功率等电子器件上。
但是由于碳化硅具有很高的硬度和化学稳定性,Si-C键合能较大导致湿法刻蚀无法达到要求,因此针对深孔或高台阶刻蚀多采用感应耦合等离子体(ICP)对SiC进行刻蚀,目前研究人员系统研究了ICP刻蚀条件、气体组成等各种工艺条件对SiC刻蚀的影响;其中镍作为刻蚀掩膜层被广泛应用在刻蚀SiC中,因此镍的耐刻蚀性很重要,在一定程度上决定了刻蚀过程中的SiC/Ni的选择比(SiC 刻蚀量与Ni刻蚀量的比值),在同等刻蚀条件下,镍消耗少,SiC/Ni的选择比就高,则所需镍层就薄,从而减少了工艺时间,提高了工艺效率。
关键词:电镀参数;电镀镍层性能;影响引言随着我国工业化进程的加快,所有制成品的质量要求不断提高,大型设备和基本设备所用零部件的质量要求也不断提高。
某些外星部件或特殊零件的表面加工直接影响结构件的质量。
例如,如果深孔零件需要均匀的衬层厚度,则内部应力不能发生变化。
大型设备的大多数部件由多种材料组成,通常是陶瓷、铁和镍合金、铜和铜、银合金、钎焊等。
,以及类似深孔螺纹的铜合金和铁合金铆钉。
对于大型设备或关键设备上的零件产品,镀层质量要求非常严格,除了孔隙率低和联接力高外,厚度必须非常一致。
否则,如果在恶劣环境中长期使用设备,则主电池可能会在焊接或连接部件的不同位置发生腐蚀,从而大大缩短部件生命周期,并导致大型设备的质量下降,甚至出现重大损失。
1.镀液温度对镀镍层性能的影响镀液温度对镀镍层的显微硬度和刻蚀SiC/Ni选择比的影响。
随着镀液温度的升高,镀镍层的显微硬度和SiC/Ni的刻蚀选择比均呈先增大后减小的趋势。
材料的力学性能与材料的微观组织、晶粒大小和材料致密度等密切相关。
由Hall-Petch关系可知,镀层的硬度与平均晶粒尺寸呈反比,平均晶粒尺寸越小,镀层的硬度越高,晶粒尺寸随着镀液温度升高而减小,因此相应的硬度也随之变大;当镀液温度升到60℃时,镀层易生成粗晶,同时氨基磺酸根离子的氧化分解产生的副产物夹杂到镀层中,从而使得镀镍层显微硬度降低。
真空电镀中对精度的要求及提高研究
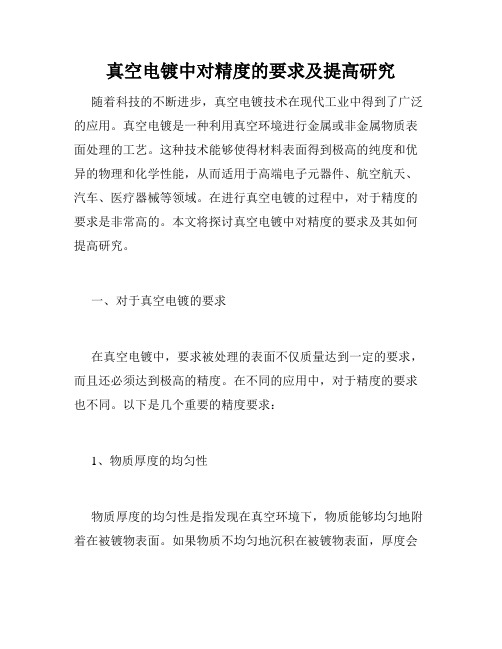
真空电镀中对精度的要求及提高研究随着科技的不断进步,真空电镀技术在现代工业中得到了广泛的应用。
真空电镀是一种利用真空环境进行金属或非金属物质表面处理的工艺。
这种技术能够使得材料表面得到极高的纯度和优异的物理和化学性能,从而适用于高端电子元器件、航空航天、汽车、医疗器械等领域。
在进行真空电镀的过程中,对于精度的要求是非常高的。
本文将探讨真空电镀中对精度的要求及其如何提高研究。
一、对于真空电镀的要求在真空电镀中,要求被处理的表面不仅质量达到一定的要求,而且还必须达到极高的精度。
在不同的应用中,对于精度的要求也不同。
以下是几个重要的精度要求:1、物质厚度的均匀性物质厚度的均匀性是指发现在真空环境下,物质能够均匀地附着在被镀物表面。
如果物质不均匀地沉积在被镀物表面,厚度会出现偏差的情况。
这种情况会导致物质变形、空气泡和裂缝,影响最终的表面质量。
2、沉积速度的确定真空电镀的工艺要求在确定沉积时间之后,必须达到一定的沉积厚度。
这种沉积速度的确定可以通过调整真空度、保证气体质量比等综合参数实现。
在实际操作中,需要严格控制沉积速度和时间关系的实验条件,并确定一个稳定的工艺流程。
3、即时测量真空度在真空环境中,镀层的质量很大程度上依赖于镀层的形成速度。
而在形成速度的过程中,真空度是一个基础指标。
为了保证镀层质量和稳定性,需要对真空度进行即时跟踪,并通过实验和计算模型进行多次控制和校准。
二、提高真空电镀精度的研究提高真空电镀精度是一项复杂而挑战性的技术,这需要开展长期的研究和实践。
一些关键技术为:1、表面改性技术随着表面改性技术的不断发展,镀层的品质得到了极大的提升。
表面改性技术汇集了多种物理化学原理,它能够改变表面的化学结构和状态,从而影响电镀效果的均匀性和稳定性。
例如,改变表面的晶体结构可以使其效果更均匀,而表面硬化可以直接影响镀层厚度和硬度。
2、混合磁力技术混合磁力技术是一种利用多种磁场控制技术,使得真空环境下的重金属离子在被镀物表面沉积的技术。
真空电镀制程介绍及异常分析
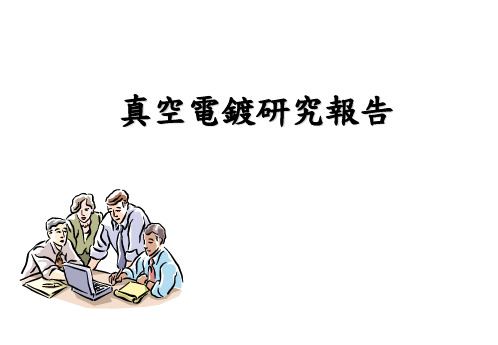
注意事項:
1.手應避免碰到油質或水
2.每爐都需更換金屬絲
在鎢絲上纏繞所需金屬絲
真空電鍍製程介紹
3.更換膠紙 更新電鍍後的透明膠 紙,以便操作人員觀察 蒸鍍的鍍膜狀況
注意事項:
1.每爐都需更換透明膠紙
2.作業時比對膠紙鍍膜的 色澤
膠紙黏貼處
Байду номын сангаас
真空電鍍製程介紹
素材前處理(線外加工) 4.素材前處理 4.1素材表面清潔 備料相應素材,清潔素材, 外觀全檢.
真空電鍍的基本認識
真空電鍍的基本原理與分類 真空電鍍是以抽真空及電極的方式,對產品表面進行金 屬鍍膜的過程. 真空電鍍可分為:真空蒸鍍和真空濺鍍. 真空蒸鍍的基本原理為: 1.用机械泵与擴散泵將真空爐里的气体抽掉,形成我們 需求的真空.(真空度1*10-4Pa) 2.通過調節電流/電壓的大小,讓真空爐里的鎢絲受電 流/電壓的改變而升溫,當達到一定溫度時,鎢絲上的金屬 絲被气化,使它以原子形態沉積在塑膠產品表面,形成一 道金屬鍍膜.
真空電鍍的基本認識
真空電鍍前處理的作用 2.1 底漆的功能和性能 a 与塑膠底材具有优良的附著強度,与所鍍的金屬( 鋁,鉻)結合牢固. b 修飾和遮蓋塑膠表面的所有缺陷,賦予其非常光 滑丰滿度很高的涂層便于鍍膜.
真空電鍍的基本認識
常用的真空電鍍材料
一般常見的真空電鍍電鍍層的金屬有:鋁和鉻 還有不常用的有:鎳/銅/銀/金等
用百格刀以3545角度在被测产品表面划101010mm的小格深度以见底材为准用3m600胶纸紧贴方格表面用手压平排出空气并用橡皮来回滚压牢表面约过9030s后拿起胶纸未粘住的一端以180方向迅速扯起不可猛拉判定標準
真空電鍍研究報告
目錄
手表用真空镀玫瑰金色镀层性能研究
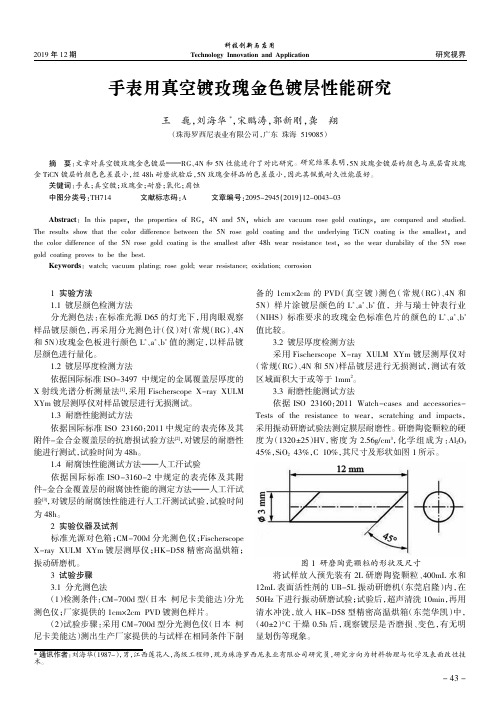
2019年12期研究视界科技创新与应用Technology Innovation and Application手表用真空镀玫瑰金色镀层性能研究王巍,刘海华*,宋鹏涛,郭新刚,龚翔(珠海罗西尼表业有限公司,广东珠海519085)1实验方法1.1镀层颜色检测方法分光测色法:在标准光源D65的灯光下,用肉眼观察样品镀层颜色,再采用分光测色计(仪)对(常规(RG )、4N 和5N )玫瑰金色板进行颜色L *、a *、b *值的测定,以样品镀层颜色进行量化。
1.2镀层厚度检测方法依据国际标准ISO-3497中规定的金属覆盖层厚度的X 射线光谱分析测量法[1],采用Fischerscope X-ray XULM XYm 镀层测厚仪对样品镀层进行无损测试。
1.3耐磨性能测试方法依据国际标准ISO 23160:2011中规定的表壳体及其附件-金合金覆盖层的抗磨损试验方法[2],对镀层的耐磨性能进行测试,试验时间为48h 。
1.4耐腐蚀性能测试方法———人工汗试验依据国际标准ISO-3160-2中规定的表壳体及其附件-金合金覆盖层的耐腐蚀性能的测定方法———人工汗试验[3],对镀层的耐腐蚀性能进行人工汗测试试验,试验时间为48h 。
2实验仪器及试剂标准光源对色箱;CM-700d 分光测色仪;Fischerscope X-ray XULM XYm 镀层测厚仪;HK-D58精密高温烘箱;振动研磨机。
3试验步骤3.1分光测色法(1)检测条件:CM-700d 型(日本柯尼卡美能达)分光测色仪;厂家提供的1cm ×2cm PVD 镀测色样片。
(2)试验步骤:采用CM-700d 型分光测色仪(日本柯尼卡美能达)测出生产厂家提供的与试样在相同条件下制备的1cm ×2cm 的PVD (真空镀)测色(常规(RG )、4N 和5N )样片涂镀层颜色的L *、a *、b *值,并与瑞士钟表行业(NIHS )标准要求的玫瑰金色标准色片的颜色的L *、a *、b *值比较。
真空电镀中多层金属镀层的制备及应用研究
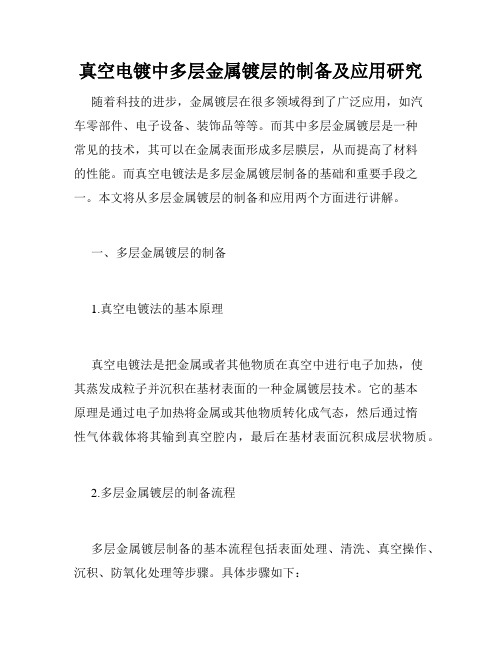
真空电镀中多层金属镀层的制备及应用研究随着科技的进步,金属镀层在很多领域得到了广泛应用,如汽车零部件、电子设备、装饰品等等。
而其中多层金属镀层是一种常见的技术,其可以在金属表面形成多层膜层,从而提高了材料的性能。
而真空电镀法是多层金属镀层制备的基础和重要手段之一。
本文将从多层金属镀层的制备和应用两个方面进行讲解。
一、多层金属镀层的制备1.真空电镀法的基本原理真空电镀法是把金属或者其他物质在真空中进行电子加热,使其蒸发成粒子并沉积在基材表面的一种金属镀层技术。
它的基本原理是通过电子加热将金属或其他物质转化成气态,然后通过惰性气体载体将其输到真空腔内,最后在基材表面沉积成层状物质。
2.多层金属镀层的制备流程多层金属镀层制备的基本流程包括表面处理、清洗、真空操作、沉积、防氧化处理等步骤。
具体步骤如下:(1)表面处理。
通过机械加工、化学处理等方式对基材进行表面处理,以保证未来沉积的金属膜层能够牢固地附着在基材表面;(2)清洗。
用稀酸清洗、溶剂清洗、超声波清洗等方式清洗表面,以清除基材表面的油污、尘埃等杂质,使得金属膜层沉积得更加均匀;(3)真空操作。
将工件放置在电极上,通过真空泵抽空使得系统内的压强降至10^-3~10^-4 Pa区间,然后采用电子束加热或者磁控溅射等方式,将需要镀层的目标材料转化成气态并沉积在工件表面;(4)沉积。
根据所需的需要沉积的金属膜层数目和材料进行选择,每沉积一层需要进行一次清洗和真空操作;(5)防氧化处理。
通过电化学、化学氧化、热处理等方式处理表面,防止氧气进入金属膜层内部导致氧化反应。
二、多层金属镀层的应用研究多层金属镀层具有高硬度、高韧性、耐腐蚀等优良性能,广泛应用于飞机、汽车、电子、医疗、化工等领域。
以下分别就汽车、电子和航空等应用领域进行阐述。
1.汽车领域汽车工业是金属镀层最广泛应用的领域之一。
多层金属镀层在制造汽车零部件和汽车整体方面具有重要的应用价值。
Titanium nitride (TiN)、钨(W) 、氮化硅(SiN) 等属于多层金属镀层的材料,在汽车工业中广泛应用于齿轮系统、刹车系统、传动和底盘系统等。
射频磁控溅射镀膜过程及机制(硕士论文草稿,有摘抄有实验有推断不保证正确)
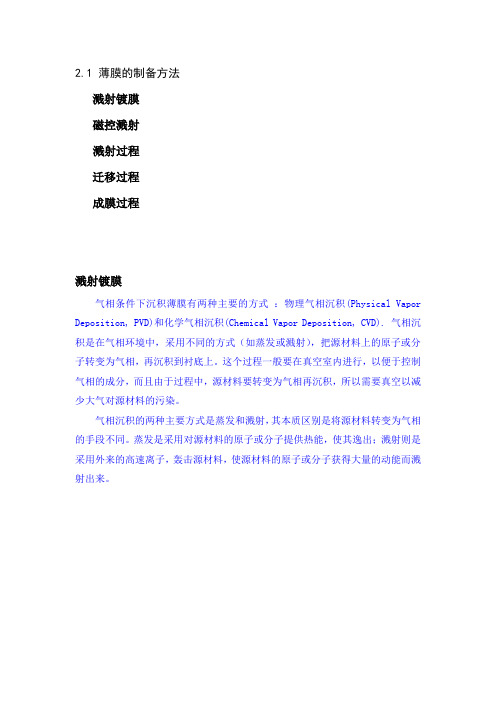
2.1 薄膜的制备方法溅射镀膜磁控溅射溅射过程迁移过程成膜过程溅射镀膜气相条件下沉积薄膜有两种主要的方式:物理气相沉积(Physical Vapor Deposition, PVD)和化学气相沉积(Chemical Vapor Deposition, CVD). 气相沉积是在气相环境中,采用不同的方式(如蒸发或溅射),把源材料上的原子或分子转变为气相,再沉积到衬底上。
这个过程一般要在真空室内进行,以便于控制气相的成分,而且由于过程中,源材料要转变为气相再沉积,所以需要真空以减少大气对源材料的污染。
气相沉积的两种主要方式是蒸发和溅射,其本质区别是将源材料转变为气相的手段不同。
蒸发是采用对源材料的原子或分子提供热能,使其逸出;溅射则是采用外来的高速离子,轰击源材料,使源材料的原子或分子获得大量的动能而溅射出来。
本论文中样品采用中科院沈阳科学仪器厂JGP350型磁控溅射镀膜机制备,真空抽气系统由机械泵(前级泵)和分子泵(主泵)组成,极限真空度可达2.0×10-4Pa。
溅射系统配有三个立式靶,其中两个接射频阴极(RF),另一个接直流阴极(DC)。
RF的溅射功率可在0~200W之间调节,直流电源电压为0~2000V。
中间样品控制架上有3个样品夹具,样品控制架可通过旋转来选择所要溅射的靶。
其中一个样品位的后面有加热电阻丝,可对该位置上的衬底加热,使得衬底温度在室温与400℃之间可调。
靶和衬底间距为5cm。
由于靶材CdTe和ZnTe陶瓷靶的电导率较低,所以采用射频溅射模式。
工作气体为氩气。
磁控溅射所用靶材是纯度为99.999%的ZnTe和CdTe化合物陶瓷靶,靶材直径为100mm、厚6mm。
沉积薄膜用的衬底均为普通玻璃,衬底厚1mm,长宽为2.5×6cm。
射频溅射时,采用高频射频电源(13.56MHz),分别将靶材和真空室的其他部分耦合在电源的两极,衬底处于靶材对应的位置,与靶材间距为5cm,射频磁控溅射时放电的过程(工作气体为Ar气):1)无光放电打开射频电源及电流显示器,即会有十毫安以下以下的电流显示。
真空电镀过程中金属镀层的膜厚控制研究

真空电镀过程中金属镀层的膜厚控制研究在当今的工业生产中,金属表面处理的方法越来越多元化,其中真空电镀是一种被广泛采用的表面处理技术。
真空电镀是利用电能将金属蒸汽在真空条件下沉积于基体表面以形成薄膜的技术。
通过真空电镀可以对金属制品进行装饰美化、增强耐腐蚀性等表面处理,广泛应用于汽车、家电、手表等工业领域。
而对于真空电镀过程中金属镀层的膜厚控制,更是至关重要的一个环节。
一、真空电镀涂层膜厚对产物性能的影响在研究真空电镀过程中金属镀层膜厚控制的问题前,先了解一下涂层膜厚对产物性能的影响。
在真空电镀过程中,镀层的膜厚是衡量涂层性能的一个重要参数,因为不同的膜厚可以对产物各方面的性能产生不同的影响。
比如,在金属薄膜的电学性能方面,膜厚过大或过小都会导致电学性能退化;在光学性能方面,膜厚过厚时会引起光学反射,而影响材料的透过率。
二、真空电镀涂层膜厚控制方法目前,常用的真空电镀镀层膜厚控制方法主要有四种,分别是质量监测法、时间控制法、功率控制法和距离控制法。
1. 质量监测法质量监测法是通过对蒸发源秤盘上的蒸发材料质量进行实时测量,从而控制镀层膜厚的方法。
常用的监测方法有平衡式秤盘法和动态式秤盘法。
在真空电镀过程中,动态式质量监测法比平衡式质量监测法的镀层膜厚控制精度更高,能够大幅提高镀层膜厚控制的准确性。
2. 时间控制法时间控制法是通过控制蒸发源加温时间实现对镀层膜厚的控制方法。
它的基本原理是通过在不同时间加温不同程度的方法来控制镀层膜厚。
该方法可通过计算控制各种金属原料的沉积速率,从而达到较高的精度。
3. 功率控制法功率控制法是通过控制蒸镀源功率调节金属蒸汽的沉积速率,从而控制涂层厚度的方法。
该方法需要充分理解不同材料的沉积特性,通过控制蒸镀源功率、电子束功率等参数来实现对涂层膜厚的精确控制。
但是这种方法控制难度较大,需要进行复杂的数学计算,使用起来也较为困难。
4. 距离控制法距离控制法是通过控制基底与蒸镀源的距离来实现对镀层膜厚的控制方法。
真空电镀中对镀层的焊接性能的研究
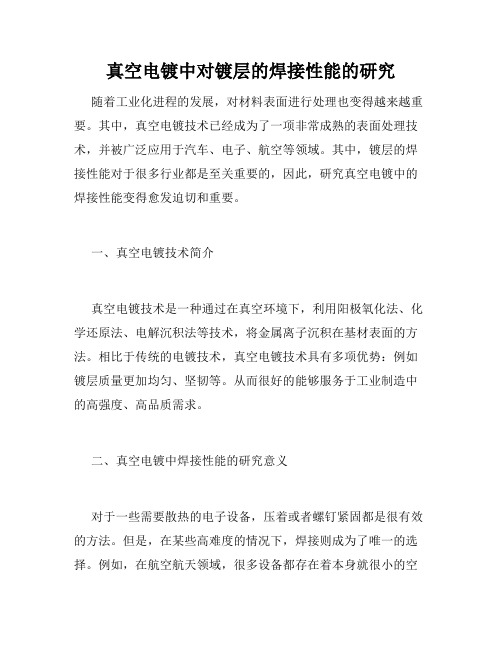
真空电镀中对镀层的焊接性能的研究随着工业化进程的发展,对材料表面进行处理也变得越来越重要。
其中,真空电镀技术已经成为了一项非常成熟的表面处理技术,并被广泛应用于汽车、电子、航空等领域。
其中,镀层的焊接性能对于很多行业都是至关重要的,因此,研究真空电镀中的焊接性能变得愈发迫切和重要。
一、真空电镀技术简介真空电镀技术是一种通过在真空环境下,利用阳极氧化法、化学还原法、电解沉积法等技术,将金属离子沉积在基材表面的方法。
相比于传统的电镀技术,真空电镀技术具有多项优势:例如镀层质量更加均匀、坚韧等。
从而很好的能够服务于工业制造中的高强度、高品质需求。
二、真空电镀中焊接性能的研究意义对于一些需要散热的电子设备,压着或者螺钉紧固都是很有效的方法。
但是,在某些高难度的情况下,焊接则成为了唯一的选择。
例如,在航空航天领域,很多设备都存在着本身就很小的空间或者垂直方向的设计特点,要是使用其它方法进行紧固和好的密封性和强度的话是十分困难的。
另外,许多的汽车、电子设备等行业都对焊接工艺的需求有着苛刻的要求,因为焊接强度的好坏直接关系到产品的使用寿命和安全性。
因此,在真空电镀技术中,对于镀层的焊接性能也需要进行研究和探究。
三、真空电镀中对镀层焊接性能的影响因素镀层的厚度、成分、表面形态等对焊接性能的影响都是非常明显的因素。
在硬度较高的电镀铬层中,如果厚度达到了一定的程度时,焊接性能可能会出现问题。
另外,镀层中不同的元素含量和氧化物等含量也会对焊接性能有所影响,因此我们需要对不同条件下的焊接实验进行对比,以了解影响因素所产生的影响。
此外,实验设备的精密程度也会对实验结果产生很大的影响。
四、真空电镀中焊接强度的测定方法在真空电镀中,焊接强度是衡量焊接质量的重要手段之一,而对于焊接强度的测定方法也有很多不同的方式:例如剪切强度法、剥离强度法等。
其中,剪切强度法通过切割试件上不同部位进行的破坏实验进行测试;而剥离强度法则是通过施加一定的张力,使其与基体分离,进而得出焊接强度。
- 1、下载文档前请自行甄别文档内容的完整性,平台不提供额外的编辑、内容补充、找答案等附加服务。
- 2、"仅部分预览"的文档,不可在线预览部分如存在完整性等问题,可反馈申请退款(可完整预览的文档不适用该条件!)。
- 3、如文档侵犯您的权益,请联系客服反馈,我们会尽快为您处理(人工客服工作时间:9:00-18:30)。
真空电镀中射频功率对镀层性能的影响研究真空电镀是一种常见的金属表面处理技术,能够为金属制品提
供出色的耐磨、防腐等性能。
在真空电镀过程中,射频功率作为
关键因素直接影响到镀层的品质和性能。
因此,在研究真空电镀
技术的过程中,研究射频功率对镀层性能的影响显得尤为重要。
一、真空电镀工艺简介
真空电镀是利用真空状态下金属表面薄膜沉积的技术。
其基本
工作原理是先将金属材料制成薄片,然后将其置于真空环境中,
利用射频等不同方式将金属原子或离子加速,使其沉积到需要的
基底表面上,形成金属膜。
真空电镀常用的金属有铬、镍、铜等,广泛应用于航空航天、电子工业等领域。
二、射频功率对真空电镀的影响
在真空电镀过程中,射频功率是影响镀层成膜速率和品质的关
键因素之一。
此外,射频功率还会影响镀层的物理性质、化学成
份等方面。
因此,研究射频功率对镀层性能的影响是非常重要的。
1. 射频功率对成膜速率的影响
射频功率的大小直接影响到成膜速率的快慢。
一般来说,射频功率与成膜速率之间成正比例关系,即射频功率越大,成膜速率越快;反之则越慢。
这是由于射频功率可以影响到有效提高电子能量,促进电子轰击形成溅射,加速金属原子或离子传输到基底表面,从而促进成膜速率。
2. 射频功率对成膜质量的影响
射频功率不仅会影响成膜速率,还会通过影响金属原子或离子传输、沉积的过程,影响成膜的物理性质、化学成份等方面。
较小的射频功率往往会导致膜的质量变差,表现为色彩变浅、光泽度降低、脆性或变薄等;较高的射频功率则有可能产生结晶过程错误、梯度较大、厚度不均等缺陷。
因此,为了达到稳定、均匀的镀层效果,需要对不同的金属材料和不同模板设计选择适当的射频功率参数。
三、射频功率控制技术
为确保在真空电镀过程中的射频功率的控制,需要使用相应的
技术手段。
目前,常用的射频功率控制技术有三种:脉冲直流放
电(PDC)、中频电源(IF)、射频电源(RF)。
1. 脉冲直流放电(PDC)
脉冲直流放电技术是将直流和脉冲电源相结合,同时使用两种
电源来控制电极间的放电,使电极产生高能离子,从而实现沉积
和腐蚀等作用。
这种技术控制严格,能够提供更好的沉积质量,
但同时也需要更高的成本,同时加工工艺比较复杂。
2. 中频电源(IF)
中频电源控制射频功率应用较广,它可以间接形成高能量电子,从而促进金属离子沉积。
中频电源通常用于金属离子镀膜过程中。
常用的中频电源有脉冲磁控镀离子放电(IPCP)、静电磁控浆镀
离子放电(ICP)、射频磁控镀离子放电(RFPC)和磁控离子束
溅射镀膜(PVD)等。
3. 射频电源(RF)
射频电源控制射频功率应用最广,大多用于金属薄膜的电化学
沉积,如金属铜、铬、铝等。
射频电源一般使用50Hz-100kHz频率,通常可以实现均匀且稳定的成膜效果。
四、总结
射频功率对真空电镀过程影响较大,不仅影响成膜速率,还会
影响成膜过程中的物理性质、化学成份等方面。
因此,为了获得
更好的真空电镀效果,需要选择合适的金属材料和模板,并通过
射频功率控制技术来进行膜层的沉积。
同时,还需要进行实验研
究来确定最佳的射频功率参数,以达到更优秀的镀层质量和性能。