(韩明,摩擦学学报,2014)湿式铜基粉末冶金摩擦材料黏着损伤研究
铜基粉末冶金摩擦材料
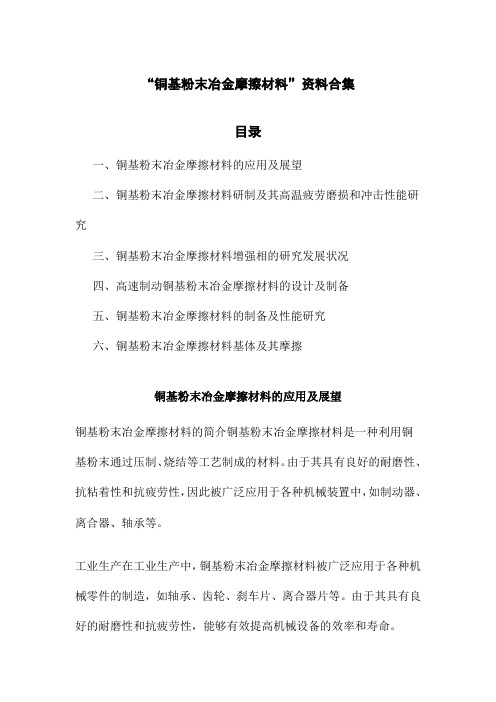
“铜基粉末冶金摩擦材料”资料合集目录一、铜基粉末冶金摩擦材料的应用及展望二、铜基粉末冶金摩擦材料研制及其高温疲劳磨损和冲击性能研究三、铜基粉末冶金摩擦材料增强相的研究发展状况四、高速制动铜基粉末冶金摩擦材料的设计及制备五、铜基粉末冶金摩擦材料的制备及性能研究六、铜基粉末冶金摩擦材料基体及其摩擦铜基粉末冶金摩擦材料的应用及展望铜基粉末冶金摩擦材料的简介铜基粉末冶金摩擦材料是一种利用铜基粉末通过压制、烧结等工艺制成的材料。
由于其具有良好的耐磨性、抗粘着性和抗疲劳性,因此被广泛应用于各种机械装置中,如制动器、离合器、轴承等。
工业生产在工业生产中,铜基粉末冶金摩擦材料被广泛应用于各种机械零件的制造,如轴承、齿轮、刹车片、离合器片等。
由于其具有良好的耐磨性和抗疲劳性,能够有效提高机械设备的效率和寿命。
医学领域在医学领域,铜基粉末冶金摩擦材料被用于制作人工关节、手术器械等医疗器械。
由于其对人体的生物相容性和耐腐蚀性优良,能够有效降低术后感染的风险,提高手术效果。
建筑与交通在建筑与交通领域,铜基粉末冶金摩擦材料被应用于各种摩擦片、刹车片、离合器片等产品的制造。
由于其具有优异的摩擦性能和耐久性,能够为建筑和交通工具提供更安全、更稳定的运行保障。
铜基粉末冶金摩擦材料的展望随着科技的不断发展,铜基粉末冶金摩擦材料的研究也在不断深入。
未来,铜基粉末冶金摩擦材料将面临以下发展方向:高性能化为了满足各种复杂工况下的高负荷、高速度、长寿命的使用要求,铜基粉末冶金摩擦材料需要具备更高的性能,如更优异的耐磨性、抗疲劳性和抗粘着性等。
绿色环保化随着环保意识的不断提高,未来的铜基粉末冶金摩擦材料将更加注重绿色环保制造,减少对环境的污染和资源的浪费。
智能化制造随着智能制造技术的不断发展,未来的铜基粉末冶金摩擦材料将更加注重智能化制造,实现生产过程的自动化、信息化、数字化,提高生产效率和产品质量。
结论铜基粉末冶金摩擦材料作为一种重要的功能材料,在工业生产、医学、建筑、交通等领域具有广泛的应用前景。
铜基摩擦材料的摩擦磨损研究

铜基摩擦材料的摩擦磨损研究摩擦磨损是各种机械设备中常见的现象,也是科学家们长期以来一直在研究的问题。
在这方面,铜基摩擦材料已经成为一种特别引人注意的材料。
铜基摩擦材料在工业生产中广泛应用,具有高温下具有较强的耐磨性能、化学惰性、优异的导电性和导热性,是一种理想的摩擦材料。
本文将对铜基摩擦材料的摩擦磨损性能进行研究和探讨。
一、铜基摩擦材料的特点铜基摩擦材料是一种由铜及其合金制成的材料,具有较高的强度和硬度,同时也具有良好的加工性、焊接性能和耐腐蚀性。
铜基摩擦材料具有优异的导电性和导热性,可以应用于电气设备和焊接行业。
此外,铜基摩擦材料的化学惰性非常强,熔点低,具有良好的塑性和韧性。
二、铜基摩擦材料的摩擦磨损机理铜基摩擦材料的摩擦磨损机理主要与其微观状态有关。
摩擦磨损的主要原因是材料表面上的微观凹坑,当机件运动时会形成一定的摩擦力,使材料表面产生塑性变形和热变形,表面上的颗粒会磨损、脱落,在同等条件下,颗粒脱落越多,则表明材料的磨损越严重。
铜基摩擦材料摩擦磨损的机理是磨粒磨损和熔角磨损。
材料表面的微小颗粒形成摩擦磨损的磨料,而在微小颗粒上的热分解产物和金属离子则成为了磨损的溶剂,促进铜基摩擦材料的摩擦磨损过程。
三、铜基摩擦材料的摩擦磨损试验铜基摩擦材料的摩擦磨损试验是对材料性能进行测试的重要方法。
试验条件是由材料的使用情况决定的,影响试验结果的条件有很多,例如试验参数、操作人员、试验设备、试验环境等。
根据铜基摩擦材料的应用领域和需要进行的试验,可以选择多种试验方法,如滑动磨损试验、旋转磨损试验、劈裂试验、磨粒磨损试验及高温试验等。
四、铜基摩擦材料的改性研究铜基摩擦材料的改性研究是为了提高其摩擦磨损性能、延长其使用寿命。
改性材料的方法有很多种,如添加一些特殊材料、改变材料的晶体结构等。
添加适量的纳米粒子或纳米管可以修饰材料表面,使其抗氧化能力增强、增加其硬度和强度,从而提高其耐磨性和防腐蚀性。
利用表面处理等方法,可以改变铜基摩擦材料的摩擦磨损性能及其相应的机理。
铜基粉末冶金刹车材料不同制动速度下的摩擦磨损性能_高红霞

第20卷 第3期郑州轻工业学院学报(自然科学版)Vol .20 No .3 2005年8月JOUR NAL OF ZHENGZHOU UNIVER SITY OF LIGHT INDUSTRY (Natural Science )Aug .2005 收稿日期:2004-09-08 基金项目:河南省重大科技攻关项目(03230239000) 作者简介:高红霞(1965—),女,河南省偃师市人,郑州轻工业学院副教授,硕士,主要研究方向:复合材料及耐磨材料. 文章编号:1004-1478(2005)03-0010-03铜基粉末冶金刹车材料不同制动速度下的摩擦磨损性能高红霞1, 刘建秀1, 王 青2(1.郑州轻工业学院机电工程学院,河南郑州450002;2.郑州轻工业学院外语系,河南郑州450002)摘要:利用MM —1000型摩擦试验机对铜基粉末冶金刹车材料在不同制动速度下的摩擦磨损性能进行测试.结果表明:该材料的摩擦系数及磨损量受制动速度影响较大.当制动速度为4000r /min 时,仍具有较高摩擦系数为0.44;制动速度大于4000r /min 时,摩擦系数迅速下降;当制动速度为3000r /min 时,材料磨损量较小.低速制动下的磨损机理主要为疲劳磨损,高速制动时主要为磨粒磨损和氧化磨损.关键词:刹车材料;摩擦磨损;制动速度;粉末冶金中图分类号:TB333 文献标识码:AFriction wear property of brake materials by copper -based powdermetallurgy with various brake speedsGAO Hong -xia 1, LIU Jian -xiu 1, W ANG Qing 2(1.College of Mech .and Electr .Eng .,Zheng zhou Univ .of Light Ind .,Zhengzhou 450002,China ;2.Dept .of Foreign Language ,Zhengzhou Univ .of Light Ind .,Z heng zhou 450002,China )A bstract :The experiment is conducted on MM -1000friction test machine ,which tests friction wear propertyof copper -based brake materials by po wder metallur gy at different brake speeds .It shows that the coefficient of friction and wear volume are greatly influenced by brake speed .When the brake speed is 4000r /min ,the mate -rial still has a c oefficient of friction with 0.44.When the brake speed is over 4000r /min ,the coefficient of friction decreased rapidly .When the brake speed is 3000r /min ,the material 's wear intensity is minor .That is to say ,no matter how higher or lower the brake speed is the wear volume is bigger relatively .With the brake speed of the lower one it mainly refers to fatigue wear ,while of higher one it mainly refers to abradant and oxi -dation wear .Key words :brake material ;friction wear ;brake speed ;powder metallurgy0 引言随着我国铁路运输业的飞速发展,列车运行速度一提再提,目前列车平均时速已超过160km .这就对列车制动技术提出了更高要求,特别是制动材料,要求其不仅具有高强度、高导热性,还必须具有优良的抗摩擦磨损性能.我国现有列车制动材料主要有高磷铸铁、有机合成材料[1,2],以及研究开发阶段的铁基和铁铜基粉末冶金材料、C /C 复合材料等[3].为了克服高磷铸铁强度低、有机合成材料导热性差等不足,笔者研究出一种铜基粉末冶金刹车材料,并系统地测试了其在不同制动速度下的摩擦磨损性能,与其他制动材料相比,铜基粉未治金刹车材料在高速制动时仍具有较高的摩擦系数和优良的耐磨性能[4],在高速列车制动零件上具有很好的应用前景.1 实验1.1 材料1.1.1 配方组成 铜基粉末冶金材料配方见表1.配方中Cu 为基体,Fe ,Sn 为合金元素,SiO 2为摩擦组元,石墨为润滑组元,BaSO 4为摩擦调整剂,其他为提高摩擦组元与基体间润湿性及促进合金元素扩散的合金添加剂.表1 铜基粉末治金材料配方组分CuFe Sn BaSO 4Si O 2石墨其他质量分数/%65~685~84~71~42~58~112~71.1.2 试件制备 将称量好的一定粒度的电解铜粉、还原铁粉、喷雾锡粉及各种组分的微粉机械混合10h ~16h ,加入适量硬质树脂和橡胶共混,在500MPa ~600MPa 压力下压制成坯块,与钢背钎焊后1050℃烧结2h 制成磨损试验用试件.试件的组织结构见图1.灰色基体为铜的固溶体,白色颗粒为SiO 2,均匀分布的黑色细条状物为石墨.试件的力学性能及物理性能见表2.图1 试件的组织结构表2 试件的力学及物理性能强度/M Pa 基体硬度/HV 弹性模量/GP a 热导率/(W ·(m ·K )-1)比热/(kJ ·(kg ·K )-1)密度/(g ·c m -3)热胀系数×10-6/K -1575503.012.64.94.916.21.2 方法1.2.1 磨损试验 在MM —1000实验机上按JB3063—82进行摩擦磨损试验.试件尺寸为内径53mm ,外径75mm ,对偶材料为30CrSiMoVA 钢.测试铜基粉末冶金材料试件在不同制动速度下的摩擦系数、稳定系数及磨损量.试验条件为制动压力p =0.98MPa ,转动惯量I =0.196kg ·m 2.摩擦系数计算公式为:μ=I ω/2pR G t ,其中,ω为开始制动时实验机主轴角速度;R G 为试件摩擦力合力作用点的半径,可通过摩擦力矩计算得到;t 为制动时间.磨损量用试件的磨损高度表示,为相同制动条件下3次制动的磨损高度的平均值.1.2.2 摩擦试件表面温度测量 在对偶材料上钻孔,孔深距摩擦表面1mm ,用热电偶测量温度.由于测温点不在试件表面,且距摩擦表面有一定距离,所测温度比试件表面实际温度低,但可用来比较不同制动速度下试件表面温度的相对高低.1.2.3 试件磨损表面的电镜观察 用JSM —5900扫描电子显微镜观察磨损后的试件表面,以分析磨损特征及磨损机理.2 结果与讨论2.1 制动速度对摩擦系数的影响不同制动速度下试件摩擦系数见表3.摩擦系数的稳定系数α= μ/μmax ,其中 μ,μmax 分别为各制动速度下测出的平均摩擦系数和最大摩擦系数.表3 不同制动速度下的摩擦系数及其稳定系数项目制动速度/(r ·min -1)10002000300040005000 μ0.430.430.460.440.34μmax 0.440.440.470.470.37α/%97.797.797.993.691.9 由表3可知,该材料在不同制动速度下摩擦系数的稳定系数均较高.当制动速度小于4000r /min 时,制动速度对材料摩擦系数影响不大,均具有较高摩擦系数;当制动速度大于4000r /min 时,摩擦系数迅速下降.这是由于制动时摩擦表面上因为摩擦造成温度升高,在不同制动速度下摩擦表面温度不同(见图2).制动速度小于4000r /min 时,摩擦表面温度小于300℃,铜基粉末冶金摩擦材料的基体组织基本不发生变化,基体本身的硬度随温度升高下降不多,再加上表面微凸的SiO 2等硬质颗粒,使克服摩擦表面啮合作用所需的力矩增大,故摩擦系数较高.当制动速度为4000r /min ,5000r /min 时,摩擦表图2 制动速度对摩擦表面温度的影响·11·第3期高红霞等:铜基粉末冶金刹车材料不同制动速度下的摩擦磨损性能面温度较高,分别为350℃,380℃,铜基粉末冶金摩擦材料组织中游离态的Pb (熔点325℃)熔化析出,在摩擦表面形成一层润滑薄膜,使摩擦系数降低;此外由于制动速度较高时,铜基摩擦材料表面产生的塑性变形及磨损增加,材料表面空隙减少,使摩擦接触面积增大,也造成了摩擦系数的降低[5].2.2 制动速度对磨损量的影响不同制动速度下试件摩损量见表4.当制动速度小于2000r /min 时,随制动速度的增加,材料的磨损量增加,这是由于制动速度增加造成摩擦表面的温度升高,基体硬度下降,导致材料耐磨性下降.当制动速度达到3000r /min 时,摩擦表面所测温度达302℃,实际温度可超过Pb 的熔点,表层熔化的Pb 在铜基粉末冶金摩擦材料表面空隙的毛细作用下渗至摩擦面,起润滑作用,使材料磨损量减少.但当制动速度为4000r /min ,5000r /min 时,摩擦表面温度更高,Pb 的润滑减轻磨损的作用远小于高温氧化增加磨损的作用,从而使材料磨损量较快地增高.表4 不同制动速度下的摩损量制动速度/(r ·min -1)10002000300040005000磨损高度/μm1.63.42.33.45.02.3 摩擦磨损机理低速(制动速度小于4000r /min )制动时,虽然材料摩擦系数较大,但磨损量较小,是由于低速时摩擦面温度低,基体硬度高,表面SiO 2等硬质颗粒可牢固地镶嵌在基体上,发挥其高硬度、耐磨的作用,使材料磨损量较小,此时磨损机理主要是疲劳磨损.材料表面受循环摩擦力作用,在铜基粉末冶金摩擦材料基体与第二相质点的界面产生疲劳裂纹,裂纹扩展使表面上局部剥离形成凹坑[6](见图3).图3 试件摩擦面SE M 照片(制动速度2000r /min ) 高速(制动速度为4000r /min )制动时,摩擦面温度高,铜基粉末冶金摩擦材料基体软化,表面层上的硬质颗粒易脱落,摩擦面上的磨料对铜基摩擦材料的基体产生磨粒磨损,形成犁沟(见图4).此外,高速制动时摩擦面温度升高使摩擦表面氧化严重,造成氧化磨损,试件高速制动后的磨损表面有大量氧化物(见图5),在摩擦力作用下,氧化物颗粒脱落,又加速磨粒磨损,因此高速制动磨损量大大高于低速制动.图4 试件摩擦面SE M 照片(制动速度4000r /min )图5 试件摩擦面SE M 照片(制动速度5000r /min )3 结论1)铜基粉末冶金摩擦材料在4000r /min 较高制动速度下仍具有较高摩擦系数(0.44),且摩擦系数的稳定性较好,可实现高速、平稳制动.2)制动速度小于4000r /min 时,铜基粉末冶金摩擦材料及对偶材料磨损量均较小.3)铜基粉末冶金摩擦材料在低速下磨损机理主要为疲劳磨损,高速下以磨粒磨损和氧化磨损为主.参考文献:[1] 周继承,黄伯云.列车制动摩擦材料研究进展[J ].材料科学与工程,1999,17(2):91—93.[2] 戴雅康.高速列车摩擦制动材料的现状与发展[J ].机车车辆工艺,1994,(2):1—8.[3] 姚萍屏,熊翔,刘强.高速电力机车制动闸瓦用粉末冶金刹车材料研究[J ].非金属矿,2002,25(2):53—55.[4] 刘建秀,李蔚,韩长生.高速列车刹车材料的性能综述[J ].江苏冶金,2003,31(2):16—18.[5] 黄培云.粉末冶金原理[M ].北京:冶金工业出版社,1985.455.[6] 董允,张廷森,林晓娉.现代表面工程技术[M ].北京:机械工业出版社,2000.58—59.·12·郑州轻工业学院学报(自然科学版)2005年。
水分对铜基摩擦材料摩擦磨损性能的影响

制 变化 , 由干摩 擦 时 的磨 粒 磨 损 和粘 着磨 损 转 即 变 为疲劳 磨损 . 阳 针 对 铝 青铜 材 料 的试 验 结 刘 果 表 明 , 摩 擦 降低 了磨 损 量 , 提 高 了摩 擦 系 湿 但 数, 这被认 为湿 摩擦 时 表 面大 量 犁 沟 引起 较 大剪 切 力. . i[ 等关 于环境 湿度 对类金 刚石 材料性 E Lu7
表 明湿摩擦 条件 下摩 擦 系数 和磨损率 明显 低于 干
摩擦 , 这被认为是水的润滑和冷却作用 降低 了摩 擦 表 面 温 度 , 而 减 少 粘 着 和 塑 性 变 形 等. 泽 从 周
华 从 摩擦 磨损机 理 角 度 , 为 水膜 引起 磨 损 机 认
1 试 验 材 料 和 方 法
第 3 卷 第 2期 1 21 0 0年 4月
大
连
l N . 13 o 2
Ap . r 201 0
J URNA OF DA I JAOT NG UNI ER I Y O L L AN I O V ST
文 章 编 号 :6 3 9 9 (0 0 0 — 0 8 0 17 — 5 0 2 1 )2 0 3 - 3
擦 性能是 有 意义 的.
认 识摩擦 材料 在 干 、 摩擦 条 件 下 的材料 性 能 也 湿
显 现 出迫切性 .
材 料摩擦 磨损 性能 的变 化规律 随其 所处摩 擦 条 件 的不 同 而有 所不 同 , 擦 环 境 的改变 联 系 到 摩 摩 擦温度 和表 面状 态等 , 因此 , 掌握 摩擦 材料在 不
能影响研究表明, 环境湿度提高 , 摩擦 系数降低 , 原因在于水膜起 到润滑和增加实际接触面积作
用. 可见 , 水分 对摩 擦材料 性 能的影 响在不 同 的摩 擦 条件下 表现 出 不 同 的结 果 , 面 对这 些 不 同 的 而 试 验结 果 , 究 者 给 出的解 释 是 不一 致 的. 研 因此 , 认 识材料 在 不 同摩 擦条 件下 的磨损 机制仍 需大 量 的工作 . 对 铜 基粉 末 冶金 摩 擦材 料 , 于 干 、 针 处 湿 条 件下 , 摩擦 性 能 的变 化 规 律 如何 ?这方 面 的研 究 工作仍 很难 见到 报导 . 显然 , 探讨这 种材 料 的摩
铜基粉末冶金摩擦材料的湿式摩擦性能

试验。
摩擦试验试样采用内、外直径分别为 65 mm 和 85 mm 的圆环,厚度为 13~15 mm,在表面上加工成 等间隔的 12 个径向油槽,沿圆周向加工两道油槽并磨 平,槽宽 2.0 mm,槽深 0.75 mm。偶件为 65Mn 钢, 其硬度 HRC 为 40~45,几何尺寸与材料试样圆环相同。
(a) 垂直压力方向;(b) 平行压力方向 图 1 铜基材料的微观结构
摩擦试验所用润滑油为重型车辆专用 4634 传动油,油
Fig.1 Microstructures of copper-based material
第3期
王秀飞,等:铜基粉末冶金摩擦材料的湿式摩擦性能
519
平整并牢固镶嵌于基体中。这样的排布方式可以保证 到 2.5 MPa 时,摩擦因数从 0.094 8 减小至 0.082 3,下
1实验
了解摩擦副的表面温度、材料的耐热性等。图 1 所示 为样品烧结后的微观组织形貌。
图 1(a)所示为材料在垂直压制压力方向上的金相 显微组织照片。可见,添加的鳞片状石墨粉和短切炭
1.1 原材料 电解铜粉:w(Cu)≥99.7%,粒径<74 μm;还原铁
粉:w(Fe)≥98.0%,粒径<74 μm;电解钛粉:w(Ti)≥ 99.8%,粒径<50 μm;天然石英砂:不规则形状, w(SiO2)≥97%,粒径为 150~246 μm;天然鳞片状石墨: w(C)≥97%,粒径为 246~500 μm;MoS2:胶体粉剂, 分析纯;短切炭纤维:T700 炭纤维。
擦试验机研究制动条件对动摩擦因数影响的变化规律。研究结果表明:添加短切炭纤维增强的材料能有效提高材
料的能量许用负荷和摩擦因数;摩擦副的制动速度为 1 500 r/min 和 2 500 r/min 时,摩擦因数随制动压力的增加而
高速制动工况下Cu基粉末冶金闸片材料摩擦磨损性能
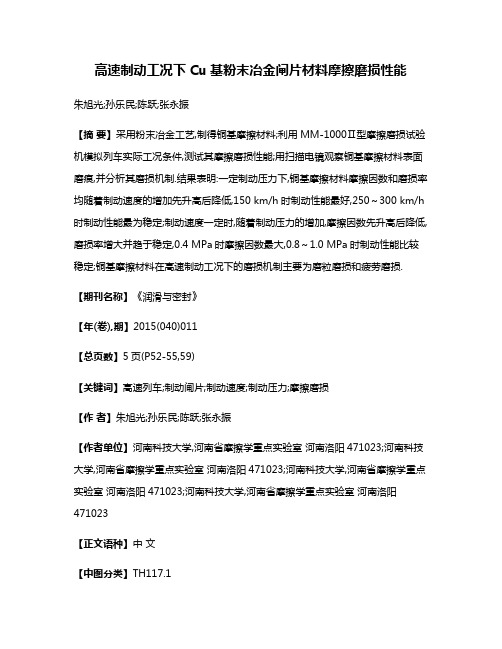
高速制动工况下Cu基粉末冶金闸片材料摩擦磨损性能朱旭光;孙乐民;陈跃;张永振【摘要】采用粉末冶金工艺,制得铜基摩擦材料;利用MM-1000Ⅱ型摩擦磨损试验机模拟列车实际工况条件,测试其摩擦磨损性能;用扫描电镜观察铜基摩擦材料表面磨痕,并分析其磨损机制.结果表明:一定制动压力下,铜基摩擦材料摩擦因数和磨损率均随着制动速度的增加先升高后降低,150 km/h时制动性能最好,250~300 km/h 时制动性能最为稳定;制动速度一定时,随着制动压力的增加,摩擦因数先升高后降低,磨损率增大并趋于稳定,0.4 MPa时摩擦因数最大,0.8~1.0 MPa时制动性能比较稳定;铜基摩擦材料在高速制动工况下的磨损机制主要为磨粒磨损和疲劳磨损.【期刊名称】《润滑与密封》【年(卷),期】2015(040)011【总页数】5页(P52-55,59)【关键词】高速列车;制动闸片;制动速度;制动压力;摩擦磨损【作者】朱旭光;孙乐民;陈跃;张永振【作者单位】河南科技大学,河南省摩擦学重点实验室河南洛阳471023;河南科技大学,河南省摩擦学重点实验室河南洛阳471023;河南科技大学,河南省摩擦学重点实验室河南洛阳471023;河南科技大学,河南省摩擦学重点实验室河南洛阳471023【正文语种】中文【中图分类】TH117.1高速列车的不断提速,对列车闸片的制动性能提出了更高的要求。
当速度为300 km/h的高速列车在实施紧急制动时,制动盘与闸片的摩擦速度达到45 m/s,摩擦因数大于0.35,每个制动盘所消耗的最高制动能达到23 MJ,制动盘体的温度可达600 ℃,盘面最高温度超过800 ℃[1-2]。
铜基粉末冶金摩擦材料由于不仅保持了基体良好的导热性和耐蚀性,还具有较高的耐磨性、高温力学性能和较低的热膨胀系数[3],因而被广泛应用于制造高速列车闸片。
为开发性能更加优越的制动闸片材料,对铜基粉末冶金摩擦材料摩擦磨损规律的研究,如材料成分对摩擦磨损性能的影响[4-5],摩擦速度和压力对摩擦磨损性能的影响等[6-7],越来越受到重视。
Cu-Fe基摩擦片摩擦磨损性能的实验研究
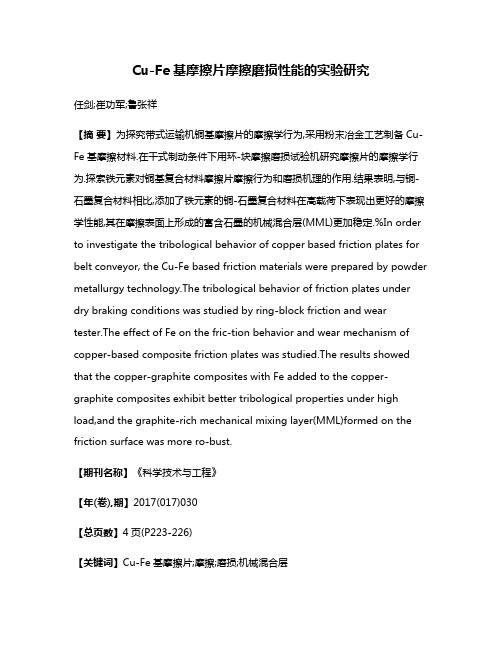
Cu-Fe基摩擦片摩擦磨损性能的实验研究任剑;崔功军;鲁张祥【摘要】为探究带式运输机铜基摩擦片的摩擦学行为,采用粉末冶金工艺制备Cu-Fe基摩擦材料.在干式制动条件下用环-块摩擦磨损试验机研究摩擦片的摩擦学行为.探索铁元素对铜基复合材料摩擦片摩擦行为和磨损机理的作用.结果表明,与铜-石墨复合材料相比,添加了铁元素的铜-石墨复合材料在高载荷下表现出更好的摩擦学性能,其在摩擦表面上形成的富含石墨的机械混合层(MML)更加稳定.%In order to investigate the tribological behavior of copper based friction plates for belt conveyor, the Cu-Fe based friction materials were prepared by powder metallurgy technology.The tribological behavior of friction plates under dry braking conditions was studied by ring-block friction and wear tester.The effect of Fe on the fric-tion behavior and wear mechanism of copper-based composite friction plates was studied.The results showed that the copper-graphite composites with Fe added to the copper-graphite composites exhibit better tribological properties under high load,and the graphite-rich mechanical mixing layer(MML)formed on the friction surface was more ro-bust.【期刊名称】《科学技术与工程》【年(卷),期】2017(017)030【总页数】4页(P223-226)【关键词】Cu-Fe基摩擦片;摩擦;磨损;机械混合层【作者】任剑;崔功军;鲁张祥【作者单位】太原理工大学机械学院,山西省矿山流体控制工程实验室,矿山流体控制国家地方联合工程实验室,太原030024;太原理工大学机械学院,山西省矿山流体控制工程实验室,矿山流体控制国家地方联合工程实验室,太原030024;太原理工大学机械学院,山西省矿山流体控制工程实验室,矿山流体控制国家地方联合工程实验室,太原030024【正文语种】中文【中图分类】TH117铜基复合材料具有较高的强度及良好的导电导热性、减磨耐磨性、耐蚀性等一系列优点,在机械零件材料等领域发挥着重要的作用[1]。
铜基石墨合金材料摩擦磨损行为的研究

第18卷 第2期2011年4月金属功能材料M etallic Fu nctional M aterialsVol.18, No.2April, 2011铜基石墨合金材料摩擦磨损行为的研究赵小根,何国球,付 沛(同济大学 材料科学与工程学院金属基材料研究所,上海 201804)摘 要:为研究铜基石墨合金材料的摩擦性能,并预测材料的磨损量变化和寿命,研究了磨损实验数据,总结出用临界热应力状态来判定磨损量线性或非线性的增长关系的结论,并通过微观机理研究、解释并证明了结论的正确性。
通过石墨润滑层损坏机理推导出磨损量计算公式并验证了公式的可行性。
关键词:石墨层;临界热应力状态;磨损公式中图分类号:T B33 文献标识码:A 文章编号:1005-8192(2011)02-0042-05Research on Attrition Loss of Copper graphiteAlloy MaterialZH AO Xiao gen,H E Guo qiu,FU Pei(Scho ol of M ater ial Science and Eng ineering ,T o ng ji U niver sity,Shang hai 201804,China)Abstract:In or der t o research the frict ion propert ies o f the copper g raphite alloy materials and for ecast v ariation o f attrition loss and material lifetime,test data are analy zed It is indicate that ther e is a cr itical t her mal stress status to determ ine the linea r o r nonlinear g ro wth relationship o f at trition lo ss and the co rr ectness o f t he conclusion is ex pla ined and pro ved by the micr oscopic mechanism.A ttr itio n lo ss fo rmula is deriv ed fro m g raphite lubr ication layer damag e mechanism and the feasibilit y is also ver ified.Key words:g r aphite layer ;critical ther mal stress status;attr itio n loss for mula作者简介:赵小根(1987-),男,硕士,研究方向是铜基粉末冶金。
- 1、下载文档前请自行甄别文档内容的完整性,平台不提供额外的编辑、内容补充、找答案等附加服务。
- 2、"仅部分预览"的文档,不可在线预览部分如存在完整性等问题,可反馈申请退款(可完整预览的文档不适用该条件!)。
- 3、如文档侵犯您的权益,请联系客服反馈,我们会尽快为您处理(人工客服工作时间:9:00-18:30)。
要: 通过离合器试验台研究了铜基粉末冶金摩擦材料的摩擦学性能和黏着损伤特性 ; 采用扫描电子显微镜
( SEM) 和能谱仪( EDS) 分析了表面损伤特征和成分变化 . 研究了湿式铜基粉末冶金摩擦材料黏着损伤形成发展历 程和损伤机理. 结果表明: 在高于临界功率密度的试验条件下 , 出现黏着损伤. 黏着损伤初期摩擦材料表面出现大 量长度 200 μm ~ 1mm 的剥落坑; 黏着损伤进展期摩擦片表面形成点状 、 连续分布撕裂坑; 黏着失效期对偶片表面出 现显著的过铜现象, 扭矩曲线波动异常. 摩擦材料发生黏着失效前 , 在低于临界功率密度的条件下 , 摩擦性能无明显 改变, 具有可回复性, 仍可继续使用. 关键词: 铜基摩擦材料; 粉末冶金; 黏着; 损伤; 摩擦性能 中图分类号: TH117. 1 文献标志码: A 文章编号: 1004 - 0595 ( 2014 ) 06 - 0623 - 08
表1 Table 1
Cu 60 ~ 70 Sn 2 ~7
铜基粉末冶金摩擦材料的组分如表 1 所示. 采 用混料、 压制、 烧结、 粗磨、 精磨的工艺路线制备铜基 粉末冶金摩擦片, 摩擦表面粗糙度 R a 为 1. 6 μm. 摩 擦片外直径 260 mm, 内直径 212 mm, 表面油槽 形式为单 头 螺 旋 槽 加 周 向 均 布 平 行 槽. 对 偶 片 为 65Mn, 淬火温度 810 ~ 850 ℃ , 油冷, 回火温度 480 ~ 520 ℃ , 金相组织为回火马氏体, 经磨削后表面粗糙 R ~ 37. 1. 6 m , HRC30 度 a为 μ 硬度为
2
625
2
2. 1
结果与讨论
功率密度对黏着损伤的影响 在实际使用中, 摩擦材料的黏着损伤表现出与
个摩擦副的摩擦面积( cm ) ,Z 为摩擦副数,T 为制 动扭矩( N·m) , ω 为摩擦片与对偶片的相对转速差 ( rad / s) , t0 为制动起始时刻 ( s ) , t1 为制动终止时 刻( s) . 保持冷却条件和制动间隔时间不变, 通过变功 率密度试验研究了功率密度对黏着损伤的影响 , 将 摩擦材料不出现黏着损伤的最大平均功率密度 , 作 为该材料在此使用条件下的黏着损伤临界功率密度 2 ε cv ( 单位 W / cm ) , 用于黏着损伤判断. 图 2 ( a ~ d ) 是 试 验 功 率 密 度 分 别 为 0. 7 ε cv 、 0. 8 ε cv 、 1. 0 ε cv 和 1. 1 ε cv 时的摩擦扭矩曲线. 由图 2 ( d) 可知, 摩擦材料在高于临界功率密度的试验条 件下, 出现黏着损伤.
铜基粉末冶金摩擦材料的组分 w
Pb 1 ~4 Else 1 ~2
Chemical composition of Cu - based PM friction materials
Zn 3 ~8 SiO2 2 ~7 graphite 17 ~ 25
表2 Table 2
C 0. 62 ~ 0. 70 Mn 0. 90 ~ 1. 20 P ≤0. 035
过程摩擦扭矩特性曲线. 为控制试验功率密度, 同时 对 4 个摩擦副进行试验, 摩擦片 ( 代号 m ) 和对偶片 ( 代号 p) 的排列次序为 p、 m、 p、 m、 p; 摩擦方式为 环 - 环 接 触; 冷 却 方 式 为 离 心 甩 油, 冷却油为
第6 期
韩明, 等: 湿式铜基粉末冶金摩擦材料黏着损伤研究
15W - 40 , 油温 50 ℃ , 流量 2. 8 L / min; 制动间隔时 间 2 min. 试验分三阶段进行: ① 黏着损伤初现及临界功 率密度试验. 逐步提高试验功率密度, 直至摩擦材 料发生黏着损伤, 扭矩曲线出现异常. ②黏着损伤进 展试验. 按阶段 1 出现黏着损伤的试验条件, 进行 10 ~ 20 次制动试验, 观察损伤进展情况. ③ 黏着失 效强化试验. 在试验台极限转速 ( 3 200 r / min ) 下, 通过提高面压增大试验功率密度, 连续进行高功率 密度强化试验, 直至摩擦元件发生黏着失效. 为研究黏着损伤后的摩擦性能回复性, 通过降 , 1 、 2 、 3 低转速和降低面压两种方式 在 阶段试验中 穿插进行黏着损伤后低功率密度摩擦性能试验 . Quanta - 200 型扫描电子显 采用 S250MK3 型、
Adhesion Damage of Wet Cu - Based Powder Metallurgy Friction Materials
HAN Ming1* , DU Jian - hua2 , NING Ke - yan1 , XU Cheng - fa3
( 1. China North Vehicle Research Institute Science and Technology on Vehicle Transmission Laboratory, Beijing 100072 , China 2. Department of Science Research, Academy of Armored Force Engineering, Beijing 100072 , China 3. Hangzhou Advance Gearbox Group Corporation Limited Company, Hangzhou 311203 , China) Abstract: The friction performace and the characteristics of adhesion damage of the wet Cu - based friction materials were studied through test bench for clutch sketch. The surface morphology and the element of the damaged surface were analyzed by scanning electron microscope and energy dispersive spectrdmeter,respectively. The results show that friction material suffered adhesion damage when power density was higher than the critical value. There are a lot of the spalling pits with lengths of 200 μm to 1 mm on the surface in the early stage of adhesion damage. There were a lot of continuously distributed punctate tearing pits in the middle stage of adhesion damage. The copper transferred from Cu - based friction materials to steel disc in case of severe adhesion damage, which led to the abnormal to torque curve. When power density was lower than the critical value,the variation of friction performance of the friction materials was insignificant before adhesion failure. Key words: Cu - based friction materials, powder metallurgy, adhesion, damage, friction performance
624
摩
擦
学
学
报
第 34 卷
擦元件的能量负荷要求日益提高, 导致摩擦表面温 升随之大幅增加, 摩擦片易发生黏着损伤甚至黏着 失效
[1 - 3 ]
黏着损伤判定和控制的设计方法奠定了理论基础 .
. 黏着损伤累积后导致摩擦表面状态和传
1
1. 1
实验部分
样品制备
递扭矩异常, 是摩擦材料主要的损伤形式之一, 但目 前对湿式铜基粉末冶金摩擦材料黏着损伤的研究报 [4 - 8 ] 道 中, 多偏重于机理分析, 对瞬态高能摩擦过程 中黏着损伤的进展情况和摩擦性能的变化情况研究 较少. 本文作者以车辆传动系统常用的螺旋槽铜基 粉末冶金摩擦元件为研究对象, 通过离合器试验台 研究了湿式铜基粉末冶金摩擦材料出现黏着损伤后 摩擦性能的变化特点、 黏着损伤的发展历程及损伤 形成机理, 为瞬态高能湿式铜基粉末冶金摩擦材料
E 为一次制动过程中的总摩滑功 ( J ) , S 为一 式中,
( a) 0. 7 ε cv ( 2 800 r / min + 1. 2 MPa)
第 34 卷 第 6 期 2014 年 11 月
摩 擦 学 学 报
Tribology
Vol 34 No 6 v, 2014
湿式铜基粉末冶金摩擦材料黏着损伤研究
韩
1* 2 1 3 明 , 杜建华 , 宁克焱 , 许成法
( 1. 中国北方车辆研究所 车辆传动重点实验室 , 北京 100072 ; 2. 装甲兵工程学院 科研部 , 北京 100072 ; 摘 3. 杭州前进齿轮箱集团股份有限公司 , 杭州 311203 )
Fig. 1 图1
Test bench for clutch sketch 离合器试验台组成示意图
微镜( SEM) 和能谱仪 EDS 分析各阶段的摩擦损伤 表面形貌和成分, 研究黏着损伤发展历程、 损伤形式 和形成机理. 为保证表面形貌分析试样的摩滑边界 条件一致性, 均以距离加压端最远处的摩擦片或对 偶片为取样对象, 通过目测, 选取摩擦片上取表面状 态变化较明显的区域以及对偶片表面过铜区域进行 制样.