Fe在铜基粉末冶金摩擦材料中的作用
铁含量对铜―铁基摩擦材料性能的影响

写一篇铁含量对铜―铁基摩擦材料性能的影响的报告,600字
铜―铁基摩擦材料的性能受到铁的含量的影响。
本报告介绍了这一影响,并且详细分析了不同铁含量对铜―铁基摩擦材料性能的影响。
铜―铁基摩擦材料由铜和铁共同制成,具有优异的耐磨性、耐腐蚀性和高强度等特点。
增加铁的含量将提高材料的介电性能,抗氧化和耐热性能也会有所增强。
但是,随着铁含量的增加,摩擦系数和耐磨性也会降低,过多的铁将会显著降低材料的表面硬度和抗磨性,使得材料效果变差。
实验表明,当铁含量为85%时,铜―铁基摩擦材料在摩擦中
的磨损行为更为复杂,摩擦系数最高,但随着摩擦时间的增加,性能也会显著降低。
而当铁含量提高到95%时,铜―铁基摩
擦材料的摩擦系数虽然明显下降,但其耐磨性明显比85%的
材料好得多,即使在长时间的摩擦中,也能保持一定的磨损程度。
此外,铁含量过高会增加材料的热膨胀系数,使材料在摩擦过程中的表面温度显著升高,影响了材料的韧性。
并且,较高的铁含量会增加材料的非晶硬化,进一步影响其耐磨性。
综上所述,铁含量对铜―铁基摩擦材料性能有着重要的影响,当铁含量大于90%时,摩擦材料的性能将会急剧降低。
因此,在进行摩擦材料的设计制造时,需要在合理范围内控制铁的含量,以保证它的性能。
铜基粉末冶金摩擦材料
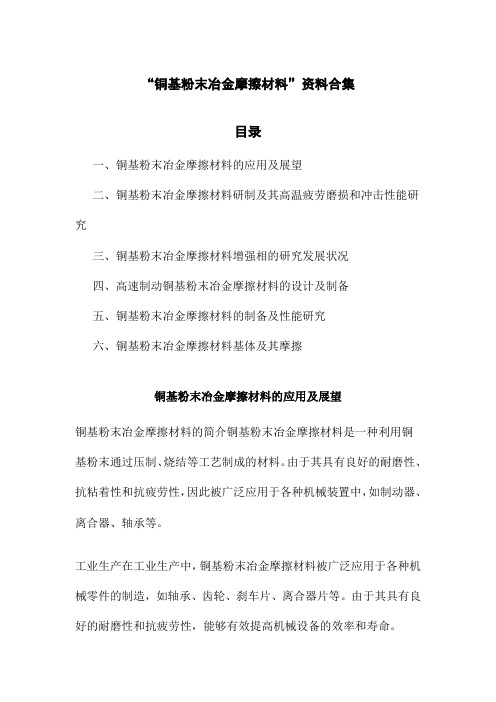
“铜基粉末冶金摩擦材料”资料合集目录一、铜基粉末冶金摩擦材料的应用及展望二、铜基粉末冶金摩擦材料研制及其高温疲劳磨损和冲击性能研究三、铜基粉末冶金摩擦材料增强相的研究发展状况四、高速制动铜基粉末冶金摩擦材料的设计及制备五、铜基粉末冶金摩擦材料的制备及性能研究六、铜基粉末冶金摩擦材料基体及其摩擦铜基粉末冶金摩擦材料的应用及展望铜基粉末冶金摩擦材料的简介铜基粉末冶金摩擦材料是一种利用铜基粉末通过压制、烧结等工艺制成的材料。
由于其具有良好的耐磨性、抗粘着性和抗疲劳性,因此被广泛应用于各种机械装置中,如制动器、离合器、轴承等。
工业生产在工业生产中,铜基粉末冶金摩擦材料被广泛应用于各种机械零件的制造,如轴承、齿轮、刹车片、离合器片等。
由于其具有良好的耐磨性和抗疲劳性,能够有效提高机械设备的效率和寿命。
医学领域在医学领域,铜基粉末冶金摩擦材料被用于制作人工关节、手术器械等医疗器械。
由于其对人体的生物相容性和耐腐蚀性优良,能够有效降低术后感染的风险,提高手术效果。
建筑与交通在建筑与交通领域,铜基粉末冶金摩擦材料被应用于各种摩擦片、刹车片、离合器片等产品的制造。
由于其具有优异的摩擦性能和耐久性,能够为建筑和交通工具提供更安全、更稳定的运行保障。
铜基粉末冶金摩擦材料的展望随着科技的不断发展,铜基粉末冶金摩擦材料的研究也在不断深入。
未来,铜基粉末冶金摩擦材料将面临以下发展方向:高性能化为了满足各种复杂工况下的高负荷、高速度、长寿命的使用要求,铜基粉末冶金摩擦材料需要具备更高的性能,如更优异的耐磨性、抗疲劳性和抗粘着性等。
绿色环保化随着环保意识的不断提高,未来的铜基粉末冶金摩擦材料将更加注重绿色环保制造,减少对环境的污染和资源的浪费。
智能化制造随着智能制造技术的不断发展,未来的铜基粉末冶金摩擦材料将更加注重智能化制造,实现生产过程的自动化、信息化、数字化,提高生产效率和产品质量。
结论铜基粉末冶金摩擦材料作为一种重要的功能材料,在工业生产、医学、建筑、交通等领域具有广泛的应用前景。
粉末冶金摩擦材料

粉末冶金摩擦材料粉末冶金摩擦材料是一种新型的摩擦材料,它由金属粉末和其他添加剂通过一系列的加工工艺制备而成。
这种材料具有优异的摩擦性能和耐磨性能,被广泛应用于汽车、机械设备、航空航天等领域。
下面将从材料特性、制备工艺和应用领域三个方面来介绍粉末冶金摩擦材料。
首先,粉末冶金摩擦材料具有优异的摩擦性能和耐磨性能。
由于其特殊的结构和成分,使得其在摩擦过程中具有较低的摩擦系数和较高的耐磨性能,能够有效减少机械设备的能量损耗和零部件的磨损。
此外,粉末冶金摩擦材料还具有良好的耐高温性能和抗腐蚀性能,能够在恶劣的工作环境下保持稳定的摩擦性能,大大延长了机械设备的使用寿命。
其次,粉末冶金摩擦材料的制备工艺相对复杂,但是具有很高的可控性和灵活性。
制备过程主要包括原料的混合、成型、烧结和表面处理等环节。
在原料的选择和配比上,可以根据具体的应用要求来确定金属粉末和添加剂的种类和比例,从而调控材料的摩擦性能和耐磨性能。
在成型和烧结过程中,可以通过压制工艺和热处理工艺来控制材料的微观结构和力学性能,从而满足不同工作条件下的需求。
此外,表面处理工艺可以进一步改善材料的摩擦性能和耐磨性能,提高其在实际应用中的性能表现。
最后,粉末冶金摩擦材料在汽车、机械设备、航空航天等领域有着广泛的应用前景。
在汽车领域,粉末冶金摩擦材料可以用于制造摩擦片、离合器、制动器等摩擦副零部件,能够提高汽车的能效和安全性能。
在机械设备领域,粉末冶金摩擦材料可以用于制造轴承、齿轮、润滑材料等零部件,能够降低设备的能耗和维护成本。
在航空航天领域,粉末冶金摩擦材料可以用于制造发动机零部件、飞机结构件等高温高载零部件,能够提高航空器的性能和可靠性。
综上所述,粉末冶金摩擦材料具有优异的摩擦性能和耐磨性能,其制备工艺具有很高的可控性和灵活性,有着广泛的应用前景。
随着科技的不断进步和工业的不断发展,相信粉末冶金摩擦材料将会在未来发挥越来越重要的作用,为各行各业带来更多的技术创新和经济效益。
Fe含量及摩擦组元对铜基粉末冶金摩擦材料性能的影响

2 0 1 4年 2月
粉 末 冶金技 术
Po wd e r M e t al l ur g y Tec hnol o gy
Vo 1 .3 2,No .1
Fe b . 2 01 4
F e 含 量 及 摩 擦 组 元 对 铜 基 粉 末 冶 金 摩 擦 材 料 性 能 的影 响
于 潇 郭 志猛 一 杨 剑 ’ 裴 广 林
赵 翔
彭 坤
1 ) ( 北 京 科 技 大 学 新 材料 技 术 研 究 院 , 北京 1 0 0 0 8 3 ) 2 ) ( 西 安 航 空 制 动 科 技 有 限公 司 , 西安 7 1 3 1 0 6 )
摘 要 : 以电解 C u 粉、 还原 F e粉 、 石墨等为 主要原料 , 采 用粉末 冶金加 压烧 结工艺 制备 了 C u基 粉 末 冶 金 摩擦材料 , 研究了 F e 含量及 S i O 、 A 1 0 , 、 S i C等 摩 擦 组 元 对 烧 结 合 金 的 显 微 组 织 、 力 学 性 能 和摩 擦 磨 损 性 能 的 影响。结果表 明 : F e 主 要 影 响摩 擦 材 料 的 力 学 性 能 , 随 F e含 量 的 增 加 , 摩 擦材 料的硬度 、 抗 压 强 度 和 抗 弯 强 度显著提高 , F e含 量 为 1 5 %( 质 量分数 , 下 同) 时具有高 摩擦 系数 、 较低磨 损量 和稳定 的摩擦过 程 ; 添 加 摩 擦 组元 S i C后 的 材 料 强 度 最 高 、 摩擦系数最大 、 磨损量最小 , 但增加了对偶材料 的磨损 , 加S i O , 后 材 料 摩 擦 系 数 最小 、 磨损量最大 , A 1 0 , 所 起作用介于二者之 间。
Fe在铜基粉末冶金摩擦材料中的作用
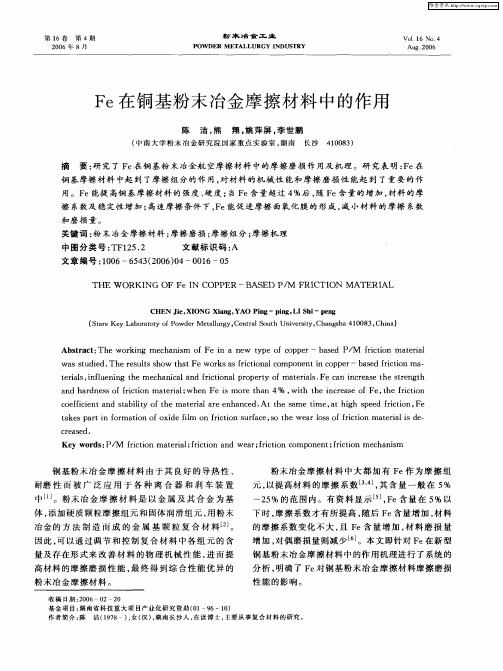
蝼
图 2 四 种 材 料 在 不 同摩 擦 速 度 下 的摩 擦 系 数
由图 2可 知 ,随摩擦 速 度 的提高 ,材 料 的摩 擦 系数呈 现逐渐 降低 的趋 势 。究 其 原 因 ,摩 擦 是 两 摩 擦 表 面 间相互 粘 着 和 啮 合 程 度 及 其 性 质 的 函数 _8 J。 根 据 分子 一机械 啮合 理 论 ,当 两摩 擦 面 间微 凸 体 相 互接 触时 ,接触 点材 料 由于 分子 间作 用力 而粘 和在 一起 。 摩 擦过 程 中 ,这 些接 触点 间 产生 相对运 动 ,从 而发 生 剪切现 象 。这种 剪 切力 必然 成 为摩擦 阻 力 。在 低转
速下摩 擦 时 ,摩 擦 表 面温升 不 大 ,摩擦 表 面未 发生 相 变等复 杂 变化 ,摩擦 阻 力 主 要来 源 于材 料 表 面 微 凸 体 与对 偶 表 面微 凸体 间 的相 互作 用 。而 铜基摩 擦 材 料较对 偶 材料 软得 多 ,因此 ,此 时摩擦 副 间 的相互作 用 主 要是 对偶 表面 硬质 微 凸体对 较软 的铜基 材料 表 面 的犁沟 作用 。故 低转 速摩 擦 时摩擦 系 数较大 。随 着摩 擦转 速 的提 高 ,由 于大 量 摩 擦 热 的存 在导 致 材 料摩擦 表 面温 度迅 速 提 高 ,而基 体 铜 较 软 ,因此 ,材 料摩擦 面 在摩擦 过 程 中发 生 软 化 和 产生 大 量 变 形 。 材料 表面存 在 的这 种严 重畸 变导 致材 料表 面能 急剧 升高 ,表面 原子 活 性 增 大 。 因此 高 温 下 表 面层 中均 匀分 布 的 Fe极 易 与大 气 中的氧 发生 反应 ,形成 一层 致 密 的氧化 膜 。高 摩 擦 速 度下 ,一 方 面 材料 表 面 的 软 化 ,增 强 了材 料 的塑性 ,降 低 了微 凸体 间的机 械 啮 合 作 用 ,因此 ,降 低 了 材料 的摩擦 系数 。另一 方 面 , 表面 氧化 膜 的形 成 也 阻隔 了对偶 与材 料金 属 问的直 接 接触 ,从 而进 一步 降低 了高速摩擦 下 的摩 擦 系数 。
各化学元素在粉末冶金中的作用
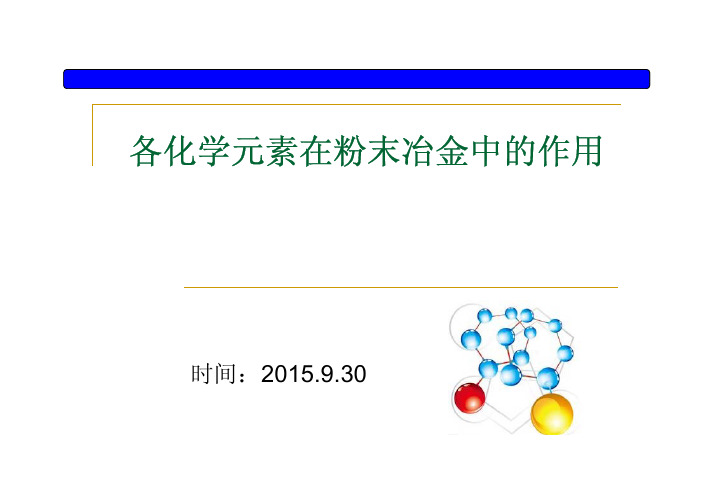
十一、各元素性能总结
1、多数合金元素使马氏体点MS降低,其中Cr、Mn、Ni元素的作用最强。 只有Al 、Co元素是提高马氏体点MS的,Si元素则影响不大; 2、Cr、W、Mo、V、Ti、Al、Si等元素的加入会使奥氏体相区缩小,特 别是Cr、 Si含量高时将限制奥氏体体区,甚至完全消失; 3、固溶强化作用递增次序:Cr<W<V<Mo<Ni<Mn<Si<P; 4、Co、Ni等部分非碳化物形成元素能增大C的扩散速度,使奥氏体形成 速度加快; 5、Ni、Mn、Co、C、N、Cu等元素的加入会使奥氏体相区扩大,特别 是Ni、Mn的影响更大; 6、V、Ti、Nb、Zr强烈阻碍奥氏体晶粒长大; W、Cr、Mo中等阻碍奥氏体晶粒长大; Mn、B促进奥氏体晶粒长大; 7、Mo、Mn、W、Cr、Ni、Si、Al对淬透性作用依次由强到弱;
九、铜(Copper)
1、物理特性: 密度:8.96g/cm³; 熔点:1083℃; 2、溶解度: α-铁:0.2%; γ-铁: 8.5% ; 3、在粉末冶金中的作用: 3.1、铜通常应用在自润滑含油轴承、青铜合金等摩擦材料上; 3.2、铜具有良好的导热、导电率,以及良好的抗腐蚀和机械性能,用作 制作渗铜类零件,导热及机械性能较好; 3.3、铜在铁基粉末冶金中有固溶强化作用,在含量低时,可以代替镍; 3.4、铜熔点较低,铁基粉末冶金烧结过程中,铜在1083℃左右便开始溶 化,产生瞬时液相,润滑基体、促进烧结。 3.5、铜与磷或硼配合使用,在铁基粉末冶金中, 提高产品摩擦性能,还能提高钢的强度和 屈服比; 3.6、铜在铁基粉末冶金中具有永久封闭孔隙的 作用。
33硼化物fec自身具有优良的耐磨性在粉末冶金中形成硼共晶硼共晶以孤立的颗粒形态存在在基体中形成良好的耐磨相但可能会由于硼化物或硼渗碳体的析出而降低力学性能通常加入一定量的铜做粘合剂改善组织结构性能
铜基粉末冶金摩擦材料的湿式摩擦性能

试验。
摩擦试验试样采用内、外直径分别为 65 mm 和 85 mm 的圆环,厚度为 13~15 mm,在表面上加工成 等间隔的 12 个径向油槽,沿圆周向加工两道油槽并磨 平,槽宽 2.0 mm,槽深 0.75 mm。偶件为 65Mn 钢, 其硬度 HRC 为 40~45,几何尺寸与材料试样圆环相同。
(a) 垂直压力方向;(b) 平行压力方向 图 1 铜基材料的微观结构
摩擦试验所用润滑油为重型车辆专用 4634 传动油,油
Fig.1 Microstructures of copper-based material
第3期
王秀飞,等:铜基粉末冶金摩擦材料的湿式摩擦性能
519
平整并牢固镶嵌于基体中。这样的排布方式可以保证 到 2.5 MPa 时,摩擦因数从 0.094 8 减小至 0.082 3,下
1实验
了解摩擦副的表面温度、材料的耐热性等。图 1 所示 为样品烧结后的微观组织形貌。
图 1(a)所示为材料在垂直压制压力方向上的金相 显微组织照片。可见,添加的鳞片状石墨粉和短切炭
1.1 原材料 电解铜粉:w(Cu)≥99.7%,粒径<74 μm;还原铁
粉:w(Fe)≥98.0%,粒径<74 μm;电解钛粉:w(Ti)≥ 99.8%,粒径<50 μm;天然石英砂:不规则形状, w(SiO2)≥97%,粒径为 150~246 μm;天然鳞片状石墨: w(C)≥97%,粒径为 246~500 μm;MoS2:胶体粉剂, 分析纯;短切炭纤维:T700 炭纤维。
擦试验机研究制动条件对动摩擦因数影响的变化规律。研究结果表明:添加短切炭纤维增强的材料能有效提高材
料的能量许用负荷和摩擦因数;摩擦副的制动速度为 1 500 r/min 和 2 500 r/min 时,摩擦因数随制动压力的增加而
铜基摩擦材料成分、组织与耐磨性研究

铜基摩擦材料成分、组织与耐磨性研究摘要铜基粉末冶金摩擦材料是由铜基体、强化组元、润滑组元和摩擦组元经粉末冶金工艺制备而成,由于制造工艺简单,同时既具有金属的良好导热性、耐高温性又具有陶瓷的耐磨性,已经成为制动摩擦材料领域研究的主要方向。
而目前国内生产的铜基粉末冶金制动摩擦材料在使用性能上仍与国外存在一定差距,因此,为了探究现有国产铜基粉末冶金制动摩擦材料在成分、组织和性能上与国外存在的差别,本文主要针对两种国外生产的铜基粉末冶金制动摩擦片,及一种国内铜基粉末冶金制动摩擦片进行成分、显微组织、显微硬度以及不同载荷和滑动速度下耐磨性的对比分析,综合各自特点和优势,进行成分优化设计和材料制备,并分析了高温耐磨性,主要研究结果如下:(1)三种国内、外铜基摩擦片的主要成分均为基体铜-锡合金、铁、石墨和陶瓷(ZrSiO4),但在含量上存在明显区别,国外铜基摩擦片2和国产铜基摩擦片主要以铜基体为主,国外铜基摩擦片1的基体含量最少,铁、石墨和陶瓷含量最多。
国外铜基摩擦片2的孔隙率以及铜基体显微硬度最高,国外铜基摩擦片1次之,国产铜基摩擦片组织较为致密,但铜基体显微硬度最低。
在20~80 N载荷范围内,40~80 N中高载荷时,国外铜基摩擦片1更适合;在30~210 mm/min的滑动速度内,国产铜基摩擦片更适于I210 mm/min高滑动速度。
(2)优化的铜基摩擦材料成分体系:67%铜基体、13%铁、3%锌、5%石墨和12%陶瓷相。
采用粉末冶金方法制备铜基摩擦材料,烧结工艺规范为:820℃烧结,20 MPa烧结压力,保温1 h,烧结试样孔隙率低,在不同载荷下的耐磨性较好。
对不同铜-锡配比的烧结铜基摩擦材料进行耐磨性分析,发现Sn/(Cu+Sn)为9%的铜基摩擦材料在不同载荷下具有良好的耐磨性。
(3)在25℃、250℃、350℃和450℃试验条件下,对自制铜基摩擦材料试样进行摩擦磨损试验,并与国外铜基摩擦片1进行对比分析。
- 1、下载文档前请自行甄别文档内容的完整性,平台不提供额外的编辑、内容补充、找答案等附加服务。
- 2、"仅部分预览"的文档,不可在线预览部分如存在完整性等问题,可反馈申请退款(可完整预览的文档不适用该条件!)。
- 3、如文档侵犯您的权益,请联系客服反馈,我们会尽快为您处理(人工客服工作时间:9:00-18:30)。
收稿日期:2006-02-20基金项目:湖南省科技重大项目产业化研究资助(01-96-10)作者简介:陈 洁(1978-),女(汉),湖南长沙人,在读博士,主要从事复合材料的研究。
Fe 在铜基粉末冶金摩擦材料中的作用陈 洁,熊 翔,姚萍屏,李世鹏(中南大学粉末冶金研究院国家重点实验室,湖南 长沙 410083)摘 要:研究了Fe 在铜基粉末冶金航空摩擦材料中的摩擦磨损作用及机理。
研究表明:Fe 在铜基摩擦材料中起到了摩擦组分的作用,对材料的机械性能和摩擦磨损性能起到了重要的作用。
Fe 能提高铜基摩擦材料的强度、硬度;当Fe 含量超过4%后,随Fe 含量的增加,材料的摩擦系数及稳定性增加;高速摩擦条件下,Fe 能促进摩擦面氧化膜的形成,减小材料的摩擦系数和磨损量。
关键词:粉末冶金摩擦材料;摩擦磨损;摩擦组分;摩擦机理中图分类号:TF12512 文献标识码:A 文章编号:1006-6543(2006)04-0016-05THE WOR KIN G OF Fe IN COPPER -BASED P/M FRICTION MA TERIALCHEN Jie ,XIONG Xiang ,YAO Ping -ping ,L I Shi -peng(Stare K ey Laboratoty of Powder Metallurgy ,Central S outh University ,Changsha 410083,China )Abstract :The working mechanism of Fe in a new type of copper -based P/M friction material was studied 1The results show that Fe works as frictional component in copper -based friction ma 2terials ,influening the mechanical and frictional property of materials 1Fe can increase the strength and hardness of friction material ;when Fe is more than 4%,with the increase of Fe ,the friction coefficient and stability of the material are enhanced 1At the same time ,at high speed friction ,Fe takes part in formation of oxide film on friction surface ,so the wear loss of friction material is de 2creased 1K ey w ords :P/M friction material ;friction and wear ;friction component ;friction mechanism 铜基粉末冶金摩擦材料由于其良好的导热性、耐磨性而被广泛应用于各种离合器和刹车装置中[1]。
粉末冶金摩擦材料是以金属及其合金为基体,添加硬质颗粒摩擦组元和固体润滑组元,用粉末冶金的方法制造而成的金属基颗粒复合材料[2]。
因此,可以通过调节和控制复合材料中各组元的含量及存在形式来改善材料的物理机械性能,进而提高材料的摩擦磨损性能,最终得到综合性能优异的粉末冶金摩擦材料。
粉末冶金摩擦材料中大都加有Fe 作为摩擦组元,以提高材料的摩擦系数[3,4],其含量一般在5%~25%的范围内。
有资料显示[5],Fe 含量在5%以下时,摩擦系数才有所提高,随后Fe 含量增加,材料的摩擦系数变化不大,且Fe 含量增加,材料磨损量增加,对偶磨损量则减少[6]。
本文即针对Fe 在新型铜基粉末冶金摩擦材料中的作用机理进行了系统的分析,明确了Fe 对铜基粉末冶金摩擦材料摩擦磨损性能的影响。
第16卷 第4期2006年8月 粉末冶金工业POWDER METALL URG Y IN DUSTR Y Vol.16No.4Aug.20061 实验材料与方法111 材料制备按比例称取各种粉末,经手工混合后置于V 型混料器中混合6~8h ,混合料在400~600MPa 压力下冷压成形。
在加压烧结炉中于氢气保护下进行烧结,烧结温度为920~950℃,烧结压力为210~315MPa ,保温3~4h ,然后水冷待温度低于100℃后出炉。
出炉后将烧结材料加工成<75mm ×53mm 的环块。
材料主要化学组成见表1。
表1 材料主要化学成分材料编号成分配比/%(质量分数)Cu Sn C Fe191452874543834584794512112 检测项目和方法在HBRF -18715型洛氏硬度计上测试材料的表观硬度(HRF ),每个试样测定五个点,取其平均值;在MeF3A 型金相显微镜上观测材料微观组织;根据G B/T10421-1989测出材料密度;在MM -1000型摩擦实验机上进行定速摩擦实验,试环及对偶尺寸<均为75mm ×53mm ,对偶材料为30CrMoSiVA 合金结构钢,硬度40HRC 。
摩擦压力为015MPa ,转动惯量为215kg ・cm ・s 2,速度分别为1000、3000、5000、7000r/min ,摩擦时间为20s ;在KYKY -2800型扫描电镜下观察材料摩擦面形貌。
2 实验结果与讨论211 Fe对材料结构及物理性能的影响图1 材料显微组织图(a )1号材料;(b )2号材料;(c )2号材料 图1为未加Fe 的1号材料和加Fe 的2号材料的显微组织图。
图1(a )中,黑色长条状组织为石墨,基体中的灰白区域为铜锡合金形成的α-固溶体,其上分布有少量孔隙。
图1(b )中,均匀分布于・71・第4期 陈 洁,等:Fe 在铜基粉末冶金摩擦材料中的作用基体中的浅灰色小斑点为加入的Fe 。
由于Fe 在铜中的溶解度极小,一般不超过014%~015%,因此Fe 颗粒多以游离状态分布于铜锡基体中,在与基体结合处少量Fe 原子能固溶于基体中。
Fe 与基体铜间这种良好的润湿性,以及该材料较高的烧结温度(920~950℃),使得烧结过程中Fe 原子活性增大,在基体中的扩散加快,因此能在基体中均匀分布,且与基体结合良好。
图1(c )为图1(b )的局部放大图,其中黑色长条状物为片状石墨,灰黑色大斑块即为Fe 颗粒。
表2列出了四种材料的密度和硬度。
由表2可表2 各材料密度及洛氏硬度(HRF )性能材料编号1234密度/g 1cm-37151715071497145硬度(HRF )42515456知,随铜基材料中Fe 含量的增加,材料密度变化并不大,而材料硬度明显提高。
铜基摩擦材料中加入Fe 后硬度提高的主要原因是,Fe 微溶于基体,与基体相不发生反应,但在与基体结合处,少量Fe 原子能固溶于基体中,起到了一定的固溶强化作用;另外,Fe 颗粒硬度明显高于基体Cu ,因此均匀分布的Fe 颗粒又起到了一定的颗粒强化的作用,从而提高了材料的硬度[7]。
212 Fe 对材料摩擦磨损性能的影响21211 Fe 对材料摩擦系数的影响图2为四种材料在不同摩擦速度下摩擦系数。
图2 四种材料在不同摩擦速度下的摩擦系数由图2可知,随摩擦速度的提高,材料的摩擦系数呈现逐渐降低的趋势。
究其原因,摩擦是两摩擦表面间相互粘着和啮合程度及其性质的函数[8]。
根据分子-机械啮合理论,当两摩擦面间微凸体相互接触时,接触点材料由于分子间作用力而粘和在一起。
摩擦过程中,这些接触点间产生相对运动,从而发生剪切现象。
这种剪切力必然成为摩擦阻力。
在低转速下摩擦时,摩擦表面温升不大,摩擦表面未发生相变等复杂变化,摩擦阻力主要来源于材料表面微凸体与对偶表面微凸体间的相互作用。
而铜基摩擦材料较对偶材料软得多,因此,此时摩擦副间的相互作用主要是对偶表面硬质微凸体对较软的铜基材料表面的犁沟作用。
故低转速摩擦时摩擦系数较大。
随着摩擦转速的提高,由于大量摩擦热的存在导致材料摩擦表面温度迅速提高,而基体铜较软,因此,材料摩擦面在摩擦过程中发生软化和产生大量变形。
材料表面存在的这种严重畸变导致材料表面能急剧升高,表面原子活性增大。
因此高温下表面层中均匀分布的Fe 极易与大气中的氧发生反应,形成一层致密的氧化膜。
高摩擦速度下,一方面材料表面的软化,增强了材料的塑性,降低了微凸体间的机械啮合作用,因此,降低了材料的摩擦系数。
另一方面,表面氧化膜的形成也阻隔了对偶与材料金属间的直接接触,从而进一步降低了高速摩擦下的摩擦系数。
Fe 在铜基粉末冶金摩擦材料中一般是作为摩擦组分加入的。
由图2可明显看出,材料的摩擦系数基本随材料中Fe 含量的增加而增加,但Fe 含量为4%的2号材料则稍有不同,与未加Fe 的1号材料相比,其各转速下的摩擦系数并未明显提高;而Fe 含量为12%的4号材料,在各转速条件下都能保持较高的摩擦系数,尤其在高速摩擦条件下,摩擦系数较其他材料有明显提高。
这说明,作为摩擦组元加入铜基材料的Fe ,只有当其含量大于4%后,材料的摩擦系数才随Fe 含量的增加而提高。
Fe 含量越高,材料摩擦系数的提高程度也越大,并且在不同的转速条件下都能保持较高的摩擦系数,特别是在高转速摩擦条件下也能表现出较高的摩擦系数。
Fe 对材料的增磨作用一方面在于,如前所述,Fe 颗粒均匀弥散地分布在材料基体中,起到了颗粒强化作用,明显提高了材料的强度、硬度;另一方面,存在于摩擦面的Fe 颗粒本身强度、硬度就比基体铜大,在摩擦过程中当较软的基体磨损后,Fe 颗粒便突出于摩擦表面,直接与对偶表面相接触,承受摩擦阻力。
并且材料中Fe 颗粒与基体铜结合紧密,基体铜对镶嵌其中的Fe 颗粒的把持作用较强,摩擦过程中受摩擦冲击力作用时,Fe 不易被拔出基体,从而提高了材料表面微凸体与对偶表面微凸体间的相互作用力,即提高了摩擦过程中摩擦副间的运动阻力,因此对材料起到了增磨作用,提高了材料的摩擦系数。
Fe 含量越高,在摩擦过程中增摩颗粒就越多,材料・81・ 粉末冶金工业 第16卷的摩擦系数也越高。
在连续的高速摩擦过程中,材料表面及相嵌其中的Fe 颗粒不断被磨损、脱落,而基体内部的Fe 颗粒随着材料表面层的降低相继露出摩擦表面,重复其对材料的增摩作用。
因此,高Fe 含量的铜基材料能在各转速条件下都保持较高的摩擦系数。
21212 Fe 对材料磨损量的影响图3为四种材料在各转速条件下,相同摩擦时间内(20s )的磨损量。