粉末冶金摩擦材料原料作用分析
制作汽车刹车片的高分子材料解析
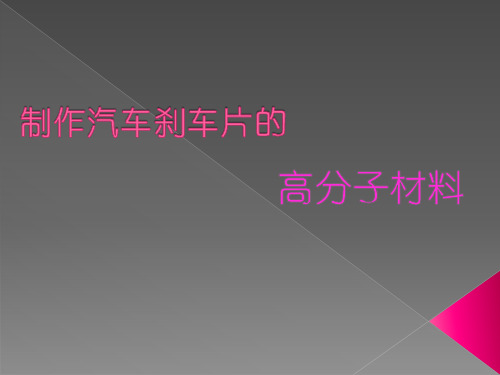
摩擦材料主要用于车辆和动力机械制动与传动,正从单一材 料向复合材料发展,其质量的好坏直接影响机器的可靠性和操 作人员的生命安全。随着科学技术的发展,人们对交通运输工 具和动力机械的速度、负荷和安全性要求越来越高。高速列车、 重载货车、轿车、赛车、摩托车等重载、高速行驶、制动频繁 的民用运载工具, 以及使用环境恶劣的装甲车、坦克、直升机等, 都对响应快、摩擦因数足够高而稳定、抗热衰减性能良好、质 量轻、寿命长和环境适应性强的高性能摩擦材料提出了迫切的 需求。20世纪90年代中期,C/C2SiC复合材料开始应用于摩擦 领域, 成为最新一代高性能制动材料而引起研究者的广泛关注和 重视,德、日等工业发达国家正逐步展开理论和应用研究。 C/C2SiC陶瓷制动材料具有密度低、耐磨性好、摩擦因数高、 制动平稳、抗腐蚀、抗氧化、耐高温、环境适应性强和寿命长 等优点,C/C2SiC陶瓷材料必将在高速高能载交通工具和工程 机械的摩擦机构上得到广泛应用,并且成本合理,所以该材料 在机械制动等领域有良好的应用前景。
C/C复合材料,即炭纤维增强炭基体复合材料。 自从1958年问世以来,由于其具有比重小(约为铁的 1/5)、强度高(抗拉强度>2GP)、热膨胀系数小、 耐高温等优点,在军工、航空、航天等方面取得了长 足的发展。其在民用领域方面的应用也日益扩大,很 多民用飞机(如波音系列:Boeing747、Boeing757 等,空客系列:A330、A340等)和高档赛车(Ferrari F2005、Renault R25、Toyota TF105等)已开始装备 C/C刹车副。目前国内中南大学、西北工业大学、中 科院金属所、航天集团第四院43所、621所等几家单位 的研究在国内居于领先水平。中南大学以博云新材料 股份有限公司为依托,C/C刹车副已全面实现产业化、 国产化[13-15]。由于C/C复合材料采用化学气相沉积 (CVD),液相浸渍炭化的生产工艺,生产周期较长, 因此成本较高,价格昂贵(一副C/C刹车盘价格高达 上万元),这也制约了其在更广阔领域特别是汽车领 域的应用。
粉末冶金摩擦材料

粉末冶金摩擦材料
• 用粉末冶金的方法制成的、具有高摩擦系 数和高耐磨性的金属与非金属组成的材料, 也称烧结摩擦材料。 • 粉末冶金摩擦材料的成分是由三部分组成 1.机体组元 其中基体组元保证材料的承受能力、热稳 定性和耐磨性,它占摩擦材料质量的50%-90%。 辅助组元则是用来改善基本组元的性能;
2.润滑组元 一般用石墨和铅,也可用铋代替铅,它一 般占摩擦材料质量的5%-25%,有利于材料的 抗卡性能和抗粘结性能,提高材料的耐磨性; 3.摩擦组元 多用二氧化硅、石绵、碳化硅、三氧化二 铝、氮化硅等,其作用是可以提高摩擦材料 的摩擦系数和耐磨性,防止焊接。
铜基摩擦材料工艺性能好,摩擦系数稳定, 抗粘结抗卡、滞性能好。 铁基的摩擦材料在高温高负荷下能显示出更 良好的摩擦性能,机械强度高,可在4001100度范围内使用。 为了增加粉末冶金摩擦材料的强度,通常将 其粘结在钢背上而成为双金属结构。 其工艺流程如图: 铜基:钢芯板→镀铜→镀锡 原料粉末→混合→压制
粉末冶金摩擦材料-培训教材

粉末冶金摩擦材料(培训教材)中国粉末冶金实验基地目录1.概述2.粉末冶金摩擦材料的特点3.我国生产的粉末冶金摩擦材料4.粉末冶金摩擦材料的装配5.粉末冶金摩擦材料的组成6.粉末冶金摩擦材料的生产7.对摩材料1.概述摩擦材料是制动器(刹车制动)、离合器(传递扭矩)使用的一种功能性材料,它对制动器、离合器的工作起着重要的作用。
例如,飞机的刹车片、汽车的刹车带、火车的制动闸瓦(闸片)等,是用做制动器中的摩擦材料。
离合器片则是用在离合器中的摩擦材料。
与摩擦材料一起摩擦进行工作的材料在飞机上称为对偶,或者叫作对摩材料;而在火车和汽车上则称为制动盘材料。
摩擦材料和对摩材料构成一组摩擦副。
尽管摩擦副的工作是由摩擦材料和对摩材料的共同性质所决定的,但是在其中起主要作用的、决定性作用的仍然是摩擦材料。
制动就是强制运转的机器或机械减速和停止的过程。
在制动器中,摩擦副吸收机器或机械的动能,并把它转化为热能。
一部分热量发散到周围的环境中去,而另一部分为摩擦副所吸收,使摩擦副本身的温度升高。
传递扭矩摩擦副的工作和制动摩擦副的工作没有什么本质的区别,同样都是摩擦副中摩擦材料和对摩材料的相对速度发生变化。
工作开始时相对速度最大,而后逐渐减小到零的过程。
区别是工作时间的长短(制动时间一般是从几秒到十几秒,传递扭矩的时间一般是十分之几秒到几秒)不同,吸收能量的大小不同,摩擦因数不同,因而摩擦副的工作温度也不同。
摩擦副在工作过程中总是要吸收能量,使本身的温度升高。
因此,摩擦材料不是在室温,而是在较高的温度下工作的。
摩擦材料工作时的温度和升温速度,在结构一定的情况下,主要和摩擦副工作时必须吸收的能量大小、吸收这些能量的时间间隔有关。
吸收的能量越大、时间间隔越短,那么摩擦材料的温度越高,升温速度也越大。
在某些情况下,发生热冲击,也就是在很短的时间间隔之内,摩擦表面产生极高的温度。
例如,飞机在着陆制动时,在3~5秒种之内,摩擦材料工作表面温度可达到1000℃以上,体积温度高达400℃~600℃。
铜基粉末冶金摩擦材料
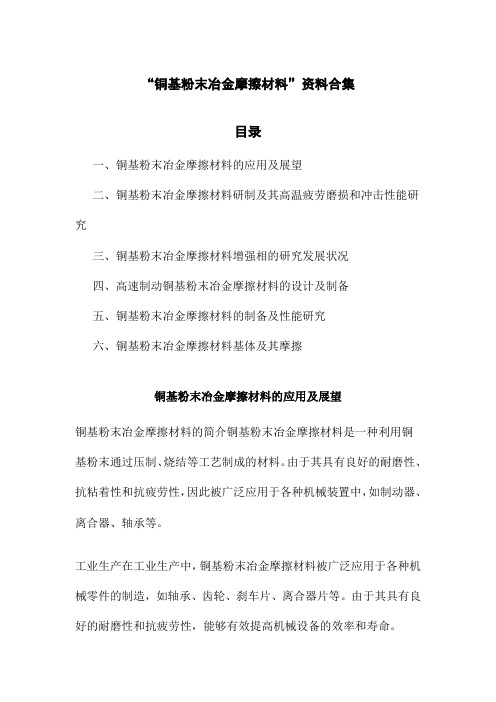
“铜基粉末冶金摩擦材料”资料合集目录一、铜基粉末冶金摩擦材料的应用及展望二、铜基粉末冶金摩擦材料研制及其高温疲劳磨损和冲击性能研究三、铜基粉末冶金摩擦材料增强相的研究发展状况四、高速制动铜基粉末冶金摩擦材料的设计及制备五、铜基粉末冶金摩擦材料的制备及性能研究六、铜基粉末冶金摩擦材料基体及其摩擦铜基粉末冶金摩擦材料的应用及展望铜基粉末冶金摩擦材料的简介铜基粉末冶金摩擦材料是一种利用铜基粉末通过压制、烧结等工艺制成的材料。
由于其具有良好的耐磨性、抗粘着性和抗疲劳性,因此被广泛应用于各种机械装置中,如制动器、离合器、轴承等。
工业生产在工业生产中,铜基粉末冶金摩擦材料被广泛应用于各种机械零件的制造,如轴承、齿轮、刹车片、离合器片等。
由于其具有良好的耐磨性和抗疲劳性,能够有效提高机械设备的效率和寿命。
医学领域在医学领域,铜基粉末冶金摩擦材料被用于制作人工关节、手术器械等医疗器械。
由于其对人体的生物相容性和耐腐蚀性优良,能够有效降低术后感染的风险,提高手术效果。
建筑与交通在建筑与交通领域,铜基粉末冶金摩擦材料被应用于各种摩擦片、刹车片、离合器片等产品的制造。
由于其具有优异的摩擦性能和耐久性,能够为建筑和交通工具提供更安全、更稳定的运行保障。
铜基粉末冶金摩擦材料的展望随着科技的不断发展,铜基粉末冶金摩擦材料的研究也在不断深入。
未来,铜基粉末冶金摩擦材料将面临以下发展方向:高性能化为了满足各种复杂工况下的高负荷、高速度、长寿命的使用要求,铜基粉末冶金摩擦材料需要具备更高的性能,如更优异的耐磨性、抗疲劳性和抗粘着性等。
绿色环保化随着环保意识的不断提高,未来的铜基粉末冶金摩擦材料将更加注重绿色环保制造,减少对环境的污染和资源的浪费。
智能化制造随着智能制造技术的不断发展,未来的铜基粉末冶金摩擦材料将更加注重智能化制造,实现生产过程的自动化、信息化、数字化,提高生产效率和产品质量。
结论铜基粉末冶金摩擦材料作为一种重要的功能材料,在工业生产、医学、建筑、交通等领域具有广泛的应用前景。
粉末冶金摩擦材料的应用现状及对原材料的要求

粉末冶金摩擦材料的应用现状及对原材料的要求
粉末冶金摩擦材料是指利用金属粉末或其他复合材料,采用冶金工艺加工而成
的多种摩擦材料的总称。
粉末冶金摩擦材料的应用现状及所需要的原材料各有不同,因此在这里不一一做详细介绍。
首先,粉末冶金摩擦材料的铁基摩擦材料是经典的粉末冶金摩擦材料,首先采
用质量等级为12L14最佳的中碳钢材料做成铁基摩擦材料,其优点是抗强度高,使用寿命长,耐腐蚀,磨损性能好,经济实惠,大多用于分离,电炉辊材料等方面。
其次,有些金属粉末摩擦材料,如铝粉末摩擦材料,以及铜粉末摩擦材料,等。
它们的特点是耐腐蚀性、抗氧化性好,抗冲击性能良好,抗磨损性能优越,热电绝缘性能较好,是汽车零部件,锅炉及新能源充电系统等领域的首选材料。
最后,也有一些以碳化硅为摩擦材料的,它具有耐磨性良好,强度高,耐腐蚀
性佳等优点,是航空及航天,汽车制造业领域,尤其是发动机和变速箱等特殊部件,都应用有它。
综上所述,粉末冶金摩擦材料应用十分广泛,要求的原材料根据其不同的应用
场合来定,一般而言,要求采用质量较优的中碳钢材料,碳化硅等满足不同应用要求的摩擦材料,以保证摩擦材料的使用寿命和性能达到最佳状态。
粉末冶金摩擦材料

粉末冶金摩擦材料粉末冶金摩擦材料是一种新型的摩擦材料,它由金属粉末和其他添加剂通过一系列的加工工艺制备而成。
这种材料具有优异的摩擦性能和耐磨性能,被广泛应用于汽车、机械设备、航空航天等领域。
下面将从材料特性、制备工艺和应用领域三个方面来介绍粉末冶金摩擦材料。
首先,粉末冶金摩擦材料具有优异的摩擦性能和耐磨性能。
由于其特殊的结构和成分,使得其在摩擦过程中具有较低的摩擦系数和较高的耐磨性能,能够有效减少机械设备的能量损耗和零部件的磨损。
此外,粉末冶金摩擦材料还具有良好的耐高温性能和抗腐蚀性能,能够在恶劣的工作环境下保持稳定的摩擦性能,大大延长了机械设备的使用寿命。
其次,粉末冶金摩擦材料的制备工艺相对复杂,但是具有很高的可控性和灵活性。
制备过程主要包括原料的混合、成型、烧结和表面处理等环节。
在原料的选择和配比上,可以根据具体的应用要求来确定金属粉末和添加剂的种类和比例,从而调控材料的摩擦性能和耐磨性能。
在成型和烧结过程中,可以通过压制工艺和热处理工艺来控制材料的微观结构和力学性能,从而满足不同工作条件下的需求。
此外,表面处理工艺可以进一步改善材料的摩擦性能和耐磨性能,提高其在实际应用中的性能表现。
最后,粉末冶金摩擦材料在汽车、机械设备、航空航天等领域有着广泛的应用前景。
在汽车领域,粉末冶金摩擦材料可以用于制造摩擦片、离合器、制动器等摩擦副零部件,能够提高汽车的能效和安全性能。
在机械设备领域,粉末冶金摩擦材料可以用于制造轴承、齿轮、润滑材料等零部件,能够降低设备的能耗和维护成本。
在航空航天领域,粉末冶金摩擦材料可以用于制造发动机零部件、飞机结构件等高温高载零部件,能够提高航空器的性能和可靠性。
综上所述,粉末冶金摩擦材料具有优异的摩擦性能和耐磨性能,其制备工艺具有很高的可控性和灵活性,有着广泛的应用前景。
随着科技的不断进步和工业的不断发展,相信粉末冶金摩擦材料将会在未来发挥越来越重要的作用,为各行各业带来更多的技术创新和经济效益。
Fe在铜基粉末冶金摩擦材料中的作用
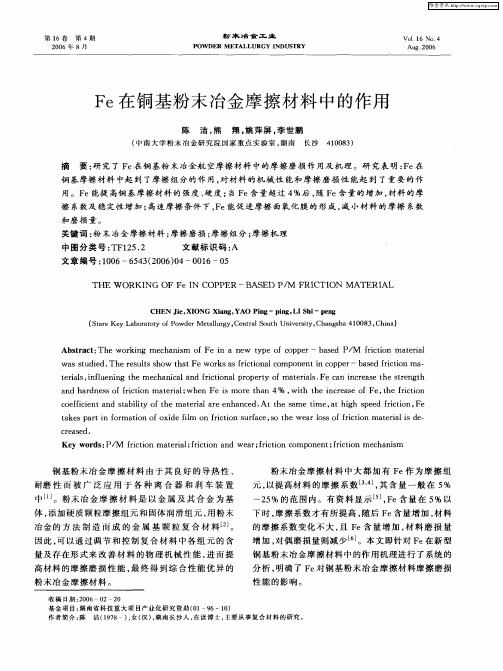
蝼
图 2 四 种 材 料 在 不 同摩 擦 速 度 下 的摩 擦 系 数
由图 2可 知 ,随摩擦 速 度 的提高 ,材 料 的摩 擦 系数呈 现逐渐 降低 的趋 势 。究 其 原 因 ,摩 擦 是 两 摩 擦 表 面 间相互 粘 着 和 啮 合 程 度 及 其 性 质 的 函数 _8 J。 根 据 分子 一机械 啮合 理 论 ,当 两摩 擦 面 间微 凸 体 相 互接 触时 ,接触 点材 料 由于 分子 间作 用力 而粘 和在 一起 。 摩 擦过 程 中 ,这 些接 触点 间 产生 相对运 动 ,从 而发 生 剪切现 象 。这种 剪 切力 必然 成 为摩擦 阻 力 。在 低转
速下摩 擦 时 ,摩 擦 表 面温升 不 大 ,摩擦 表 面未 发生 相 变等复 杂 变化 ,摩擦 阻 力 主 要来 源 于材 料 表 面 微 凸 体 与对 偶 表 面微 凸体 间 的相 互作 用 。而 铜基摩 擦 材 料较对 偶 材料 软得 多 ,因此 ,此 时摩擦 副 间 的相互作 用 主 要是 对偶 表面 硬质 微 凸体对 较软 的铜基 材料 表 面 的犁沟 作用 。故 低转 速摩 擦 时摩擦 系 数较大 。随 着摩 擦转 速 的提 高 ,由 于大 量 摩 擦 热 的存 在导 致 材 料摩擦 表 面温 度迅 速 提 高 ,而基 体 铜 较 软 ,因此 ,材 料摩擦 面 在摩擦 过 程 中发 生 软 化 和 产生 大 量 变 形 。 材料 表面存 在 的这 种严 重畸 变导 致材 料表 面能 急剧 升高 ,表面 原子 活 性 增 大 。 因此 高 温 下 表 面层 中均 匀分 布 的 Fe极 易 与大 气 中的氧 发生 反应 ,形成 一层 致 密 的氧化 膜 。高 摩 擦 速 度下 ,一 方 面 材料 表 面 的 软 化 ,增 强 了材 料 的塑性 ,降 低 了微 凸体 间的机 械 啮 合 作 用 ,因此 ,降 低 了 材料 的摩擦 系数 。另一 方 面 , 表面 氧化 膜 的形 成 也 阻隔 了对偶 与材 料金 属 问的直 接 接触 ,从 而进 一步 降低 了高速摩擦 下 的摩 擦 系数 。
粉末冶金摩擦材料
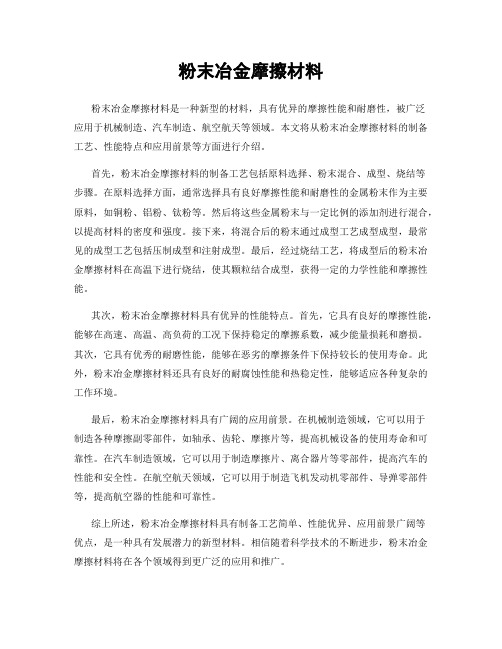
粉末冶金摩擦材料粉末冶金摩擦材料是一种新型的材料,具有优异的摩擦性能和耐磨性,被广泛应用于机械制造、汽车制造、航空航天等领域。
本文将从粉末冶金摩擦材料的制备工艺、性能特点和应用前景等方面进行介绍。
首先,粉末冶金摩擦材料的制备工艺包括原料选择、粉末混合、成型、烧结等步骤。
在原料选择方面,通常选择具有良好摩擦性能和耐磨性的金属粉末作为主要原料,如铜粉、铝粉、钛粉等。
然后将这些金属粉末与一定比例的添加剂进行混合,以提高材料的密度和强度。
接下来,将混合后的粉末通过成型工艺成型成型,最常见的成型工艺包括压制成型和注射成型。
最后,经过烧结工艺,将成型后的粉末冶金摩擦材料在高温下进行烧结,使其颗粒结合成型,获得一定的力学性能和摩擦性能。
其次,粉末冶金摩擦材料具有优异的性能特点。
首先,它具有良好的摩擦性能,能够在高速、高温、高负荷的工况下保持稳定的摩擦系数,减少能量损耗和磨损。
其次,它具有优秀的耐磨性能,能够在恶劣的摩擦条件下保持较长的使用寿命。
此外,粉末冶金摩擦材料还具有良好的耐腐蚀性能和热稳定性,能够适应各种复杂的工作环境。
最后,粉末冶金摩擦材料具有广阔的应用前景。
在机械制造领域,它可以用于制造各种摩擦副零部件,如轴承、齿轮、摩擦片等,提高机械设备的使用寿命和可靠性。
在汽车制造领域,它可以用于制造摩擦片、离合器片等零部件,提高汽车的性能和安全性。
在航空航天领域,它可以用于制造飞机发动机零部件、导弹零部件等,提高航空器的性能和可靠性。
综上所述,粉末冶金摩擦材料具有制备工艺简单、性能优异、应用前景广阔等优点,是一种具有发展潜力的新型材料。
相信随着科学技术的不断进步,粉末冶金摩擦材料将在各个领域得到更广泛的应用和推广。
- 1、下载文档前请自行甄别文档内容的完整性,平台不提供额外的编辑、内容补充、找答案等附加服务。
- 2、"仅部分预览"的文档,不可在线预览部分如存在完整性等问题,可反馈申请退款(可完整预览的文档不适用该条件!)。
- 3、如文档侵犯您的权益,请联系客服反馈,我们会尽快为您处理(人工客服工作时间:9:00-18:30)。
高铁粉末冶金刹车片用原材料作用分析粉末冶金摩擦材料的问世距今已有近百年的历史,尤其在近几年发展尤为迅猛。
粉末冶金工艺可以将金属和非金属组分的不同性能很好地配合于一种材料中,已有逐渐代替有机物粘结高分子材料的趋势。
粉末冶金摩擦材料一般由三部分组成:构成基体金属骨架的组元、润滑组元和摩擦组元。
是一种含有金属和非金属多种组分的假合金。
1构成基体金属骨架的组元简称基体组元。
常用铜、铁、二硫化钼、镍、钛、铬、钼、钨、磷、锡、铝、锌等.基体组元由基本组元和辅助组元两部分组成,基本组元在成分中占的比重最大。
在铁基中,基本组元是铁。
在铜基中,基本组元是铜。
辅助组元与基本组元形成合金,从而改善基本组元的性能,或者是赋予基本组元以某种所需要的性能。
辅助组元在铁基材料中有二硫化钼、镍、铬、钼、铜及磷等。
在铜基中主要是锡、铝、锌及磷等。
粉末冶金摩擦材料的性能、工艺特点在很大程度上取决于基体组元的化学成分、结构和物理机械性能。
基体组元保证了材料的承载能力、热稳定性、耐磨性,以及在高温工作时保持住摩擦剂和润滑剂颗粒的能力。
一般在粉末冶金摩擦材料中,基体组元占铁基材料的50%~70%,占铜基材料的60%~90%。
1.1铁近年来铁基粉末冶金摩擦材料的发展很快,主要是由于它节省有色金属,在高温高负荷下显示出更加优良的摩擦性能,机械强度高,能够承受比较大的压力,因而它应用在很多领域。
但是,由于铁与对偶具有很强的亲和性,有利于粘结过程的发展,因此需加入大量的其他元素使铁合金化以降低铁的塑性,提高其强度、屈服极限和硬度,以克服次缺点,但同时也提高了成本和加工工艺复杂度。
铁基材料的基体组元中,加入镍、铬、钼,主要目的在于提高材料机械-物理性能和耐热耐腐性能。
加入磷,能提高材料的强度,提高耐磨性.加入二硫化钼,能提高材料的机械性能和摩擦性能。
加入铜,能提高材料的导热性能,有利于材料的强度。
1.2铜铜基粉末冶金摩擦材料具有工艺性能好,摩擦系数稳定,抗粘结、卡滞性能好,导热快等特点,在中高速制动方面使用比较多,比如高铁刹车片基本都是铜基材料。
此外,在湿式条件下工作,也具有很高的耐磨性,因而在油中工作的粉末冶金摩擦材料,基本上都是铜基材料.铜基粉末冶金摩擦材料中,加入锡、锌、铝,它们能与铜基体形成固溶体,从而提高了材料的机械物理性能和摩擦性能,对抗腐蚀性能也有很大的好处。
此外,铜不仅可以作为基本组元,也可以作为铁基材料的辅助组元.铁基粉末冶金摩擦材料中加入铜,在烧结过程中,只有一小部分溶入铁中,形成固溶体,其余呈游离状态存在。
加入铜,增加了材料的导热性能,在高速、高负荷下工作是有利的。
加入铜,也有利于材料的机械物理性能。
提高了材料的密度.但当含铜超过10%的时候,使材料的耐磨性降低,增加了磨损,且成本会提高.1.3锡在铜做基本组元时,加入4~12%的锡可以使基体具有很高的耐热性、强度和硬度,烧结过程很容易合金化,且压坯强度很高,提高了工艺性。
锡也可以防止铜与钢对偶摩擦时,摩擦表面的粘结。
但在高温工作时,加入锡会使摩擦系数不稳定,一般加入石墨,二氧化硅等组分能明显提高摩擦性能。
锡在高温工作时,会向粘结摩擦层的钢背扩散,引起钢背因晶间腐蚀的破裂.1。
4铝铜铝合金具有很高的机械物理性能和减摩性能,比铜锡合金在强度、耐热性、耐蚀性、抗粘结方面好很多。
1.5钨、钼、锌、钛这些金属的加入可以强化基体,且这些金属的热容量高,易于氧化,可吸收摩擦过程产生的大量的热。
但成本高、加工不方便。
此外,钼还可以组织基本组元的氧化,减少了制动中的噪音和振动。
1.6二硫化钼二硫化钼是作为铁基材料的基体组元的辅助组元加入的,主要作用是通过在烧结过程中,与基体组元铁发生相互作用,从而改善材料基体的性能,进一步的提高了材料的机械物理性能和摩擦性能。
因此,二硫化钼作铁基材料的基体组元加入是很普遍的。
我国生产的铁基粉末冶金摩擦材料,几乎全都加入二硫化钼。
在铜基材料中,由于烧结温度低,二硫化钼在烧结中的行为很复杂,但作用不明显,并不作为基体组元.二硫化钼在铁基材料的烧结中(一般烧结温度为1000~1100℃),发生分解,析出硫和钼。
分解的过程,伴随着硫化铁型的硫化物产生.由二硫化钼还原出来的钼,使铁合金化,材料的机械物理性能发生变化。
硫化铁有润滑减摩作用,而且还原出来的钼,还能与碳发生反应,形成碳化钼。
所以加入二硫化钼,提高了铁基材料的硬度、抗压强度,提高了摩擦系数,降低了磨损.2润滑组元常用石墨,钼、铜、锌、钨、钡、铁等的硫化物,铜、镍、铁、钴等的磷化物,氮化硼、滑石及低熔点纯金属(铅、锡、铋、锑等)。
粉末冶金摩擦材料中加入的润滑组元,应满足以下的要求:具有较高的润滑能力,相对于金属基体来讲是不活泼的,在烧结温度和实际采用的烧结介质中不分解,或分解产物具有良好的润滑性能。
润滑组元的加入,有利于材料的抗卡性能、抗粘结性能。
提高了材料的耐磨性。
特别是有利于对摩材料的耐磨性.使摩擦副的工作更加平稳,但降低了材料的强度和摩擦系数.无论是铁基材料还是铜基材料,一般用石墨和铅作润滑组元,也有用铋来代替铅来作润滑组元的.润滑组元一般占摩擦材料重量的5~25%.铁基材料与对摩材料(铸铁和钢)的焊结倾向大,工作中容易造成不平稳。
因此,一般来讲,铁基材料中的润滑组元,比铜基材料占的比例要大一些。
2.1石墨石墨是粉末冶金摩擦材料中的最主要的润滑组元,对材料的机械物理性能、摩擦性能和压制性能都有重大的影响。
石墨对粉末冶金摩擦材料的影响,与加入的含量、存在的状态有关。
摩擦材料中加入的石墨量总是比较大的,一般都在5%以上.在烧结过程中,一部分石墨被烧损,绝大部分呈游离存在.对铁基材料来讲,尚有一部分溶解在铁中,形成铁-碳合金,增加了材料的强度。
石墨的烧损量与石墨的含量、烧结温度、保温时间和烧结时的保护气氛有关。
还和加入的其他金属材料的氧化程度有关.加入石墨能提高材料的耐磨性,特别是能提高对摩材料的耐磨性,提高摩擦副的抗焊结、抗卡能力,有利于平稳的工作。
少量的石墨尚能提高铁基材料的强度和摩擦系数。
加入石墨量过多,将会使摩擦材料的机械强度、摩擦系数下降.石墨还可以在摩擦过程中吸收电晕放电和火花放电,减少了摩擦表面的破碎,因而降低了磨损.2。
2铅铅能提高材料的磨合性、抗粘结性及耐磨性,但对摩擦系数没有好处.只是对稳定摩擦系数有些帮助.铅的熔点很低,摩擦材料工作时产生的热,可以使铅熔化。
熔化了的铅,在工作表面形成一种特殊的金属润滑剂,降低了表面的摩擦系数和温度,对稳定摩擦系数,提高耐磨性有很大的作用。
当温度降低,熔融金属又重新凝固,使得摩擦系数提高到原有水平.表面液体润滑膜的形成促使滑动平稳,这点在高温时特别重要,因为正是在高温下金属基体具有很大的粘结和卡滞的倾向.铅的比重很大,一般填加少量的铅,对材料强度影响不大。
因为铅在烧结时,形成液相,减少了材料的孔隙,也起到烧结活化剂的作用。
由于铅无论和铁还是和铜,都没有明显的溶解作用,因此在材料中起隔离作用。
因此,增加铅的含量,会使材料的机械物理性能下降。
铅有毒,一般用锑、铋来代替铅。
2。
3二硫化钼二硫化钼具有层状结晶构造,这就造成了分子间结合力和各个层之间的结合力存在着差别,层与层之间的力相当于范德华力.由于层与层之间相对位移所必需的切向应力不大,因而摩擦系数是低的.工作中产生的微粒对金属存在粘附作用,从而降低磨损。
然而,二硫化钼在烧结过程中易被氢气还原,分解为钼和硫溶解到金属基体中,硫生成铜或铁的硫化物,其润滑作用较二硫化钼要差很多。
3摩擦组元摩擦组元主要是起调节机械相互作用大小的作用,常用硅、铝、铁、镁、锰、锆、铍、钙、铬、钛、钼、硅铁、硅、铝、铬的氧化物,碳化硅和碳化硼,氮化硅、矿物性的复杂化合物(石棉、莫来石、蓝晶石、硅灰石、高铝红柱石、长石、锂辉石、硅酸铝、硅酸锆、皂土、软锰矿、硅线石、尖晶石)等。
石棉由于其在摩擦工作时产生大量粉尘,具有致癌作用,现已禁用。
这类组元具有非金属性质,能促进形成多相组织,减少表面粘滞和卡滞.加入摩擦组元,能提高摩擦系数,提高耐磨性和防止焊接。
摩擦组元与润滑组元一起,成为摩擦表面薄膜的一部分,使摩擦副具有很高的耐磨性,稳定性和抗焊接性能。
摩擦组元有消除配对零件表面上从烧结粉末片转移过来的金属,并使对偶表面擦伤和磨损很小的作用。
摩擦剂的基本任务并不是对配对零件材料起一种磨料磨损的作用,而是保证与对偶工作表面适当的啮合,并使对偶表面保持良好的性能。
所以在选择摩擦组分时,必须首先注意它与基体相比较的硬度以及它的颗粒形状和大小。
对于提高摩擦系数的组分有以下要求:高的熔点和离解热;从室温到烧结或使用温度区间不产生多晶型转变;不与其它组分及烧结中的保护气氛起反应;具有足够高的机械强度和硬度,以保证摩擦过程中大量能量消耗于摩擦剂的磨损上,但也不能过高,否则固体颗粒的强度和硬度太高,破坏的将不是摩擦剂颗粒本身,而在很大程度上磨损了配对零件的材料;摩擦剂具有与基体合金的湿润性或能与它牢固的粘附,在这种情况下,要从基体分离出固体颗粒,将消耗很大的摩擦功,因而促进耐磨性的提高。
3.1铁铁可以作为青铜基材料的摩擦剂,主要是铁比铜熔点高且在铜中溶解度很小。
很牢固的保持在金属基体中,因此它除增加摩擦系数外,还在一定程度上提高了材料的耐磨性。
固定在较软基体中的硬质点也促进磨削作用,有利于防止摩擦表面与对偶的粘结。
铁的含量对摩擦时的噪音和振动影响很大,因此一般加入量不要太高。
3.2二氧化硅二氧化硅是最常用的摩擦组元,通常叫做石英砂,来源方便,成本很低。
摩擦材料采用的是含94%以上二氧化硅的天然棱状结晶石英砂。
在摩擦作用中,摩擦系数对二氧化硅的含量很敏感,含量过高会造成对偶的磨损严重。
适量的二氧化硅能促使高温下摩擦系数稳定。
但加入二氧化硅等非金属添加剂又会很大程度上降低了金属基体的强度.同时,在铁基材料中,高温时二氧化硅中的硅溶解于铁中引起碳化铁含量减少而降低了摩擦性能。
3.3莫来石莫来石的加入不会降低金属基体的强度,反而会提高,因此在铁基材料中使用较多。
且其具有很高的热稳定性,摩擦系数高,可以代替二氧化硅作摩擦剂。
粉末冶金摩擦材料中的三个组成部分,要有一个合适的搭配。
根据不同的使用要求,有不同的比例关系。
就一般而言,干式应用中的润滑组元比例要大一些;湿式应用中的摩擦组元要多一些;高负荷工作的摩擦材料,基体要强一些,导热要好一些,摩擦组元要多一些,而且摩擦组元要选择那些熔点更高、硬度更高的材料,以保持在更高的温度有较高的摩擦系数.比如高铁刹车片,便要采用铜或铜锡铝合金、铜锌合金为基本组元,铁为辅助组元,鳞片石墨做润滑组元,二氧化硅或碳化硅做摩擦组元。
技术质量部苏星宇。