粉末冶金摩擦副材料及其成形技术
粉末压制和常用复合材料成形过程材料成型技术基础讲课稿

3—高压容器; 4—高压泵
Page 25
3)三向压制
这种方法得到的
压坯密度和强度超过
用其他成形方法得到 的压坯。但它适用于 成形形状规则的零件, 如圆柱形、正方形、 长方形、套筒等。
综合了单 向钢模压 制与等静 压制的特 点
1—侧向压力;2—轴向冲头;3—放气孔
Page 26
在现今汽车工业中广泛采用粉末压制制造零件。烧 结结构件总产量的60%~70%用于汽车工业,如发动 机、变速箱、转向器、启动马达、刮雨器、减震 器、车门锁中都使用有烧结零件。
Page 40
汽车变速箱中粉末压制件
零件名称 材料及处理 零件名称 材料及处理
离合器导向轴 Fe-C-Pb, Fe-
承
Cu-C
B 烧结分类
① 固相烧结 :烧结过程中各组元均不形成液相。
② 液相烧结:烧结时部分组元形成液相。在液相表面张力的作用 下,粉粒相互靠紧,故烧结速度快,制品强度高。
Page 32
4.1.4 压坯烧结
粉末压坯一般因孔隙度大,表面积大,在烧结 中高温长时间加热下,粉粒表面容易发生氧化,造 成废品。因此,烧结必须在真空或保护气氛中进行, 若采用还原性气体作保护气氛则更为有利。
(2)颗粒形状和大小
颗粒形状是影响粉末技术特征(如松装密度、流动 性等)的因素之一。通常,粉粒以球状或粒状为好。
颗粒大小常用粒度表示。粉末粒度通常在0.1~50 0μm,150μm以上的定为粗粉,40~150μm定为中等 粉,10~40μm的定为细粉,0.5~10μm为极细粉,0.5 μm以下的为超细粉。粉末颗粒大小通常用筛号表示 其范围,各种筛号表示每平方英寸(1 in2=6.45×104 m2)筛网上的网孔数。
粉末冶金成形新技术综述

收稿日期:2005-11-16作者简介:张建国(1965-)男,河南郑州人,郑州铁路职业技术学院讲师;冯 湘(1963-),男,湖南湘潭人,郑州铁路职业技术学院副教授。
粉末冶金成形新技术综述张建国,冯 湘(郑州铁路职业技术学院,河南郑州450052)摘 要:粉末冶金成形新技术包括温压技术、流动温压技术、模壁润滑技术、高速压制技术等新技术。
认为粉末冶金新技术、新工艺的不断出现,必将促进高技术产业的快速发展。
关键词:粉末冶金;成形;新技术中图分类号:TF12 文献标识码:A 文章编号:1672-0342(2006)01-0027-03 粉末冶金是一项集材料制备与零件成形于一体,节能、节材、高效、最终成形、少污染的先进制造技术,在材料和零件制造业中具有不可替代的地位和作用,已经进入当代材料科学的发展前沿。
目前粉末冶金技术正向着高致密化、高性能化、低成本方向发展,本文着重介绍几种近十年来粉末冶金零件的成形新技术。
一、温压技术温压技术是粉末冶金领域近几年发展起来的一项新技术,可生产出高密度、高强度,具有非常广泛的应用前景。
所谓温压技术就是采用特制的粉末加温、粉末输送和模具加热系统,将加有特殊润滑剂的预合金粉末和模具等加热至130~150C ,并将温度波动控制在12.5C 以内,然后和传统粉末冶金工艺一样进行压制、烧结而制得粉末冶金零件的技术。
其技术关键:一是温压粉末制备,二是温压系统。
与传统工艺相比,温压成形的压坯密度约有0.15~0.30g /cm 3的增幅,其密度可达7.45g /cm 3。
在相同的压制压力下,温压材料的屈服强度比传统工艺平均高11%,极限拉伸强度平均高13.5%,冲击韧性可提高33%。
[1]另外,温压零件的生坯强度高,可达20~30Mpa ,比传统方法提高50~100%,不仅降低生坯搬运过程中的破损率而且能对生坯进行机加工,表面光洁度好。
此外,温压工艺的压制压力低和脱模力小,同时零件性能均一,产品精度高,材料利用率高。
材料成型:粉末成型

2、硬质合金
6
五、粉末冶金制品的结构工艺性(详见表4.2) 1、壁厚不能过薄 2、沿压制方向的横截面变化时,不能逐渐增大
不合理
合理
7
3、阶梯圆柱体每级直径之差不宜大于3mm,每级的长度与直径之比应小于3,上下底面之差也不能 悬殊太大,否则不易压实
不合理
合理
8
4、应避免与压制方向垂直的或斜交的沟槽、孔腔以及网纹花
零件成形方法:
1、材料成形法——进入工艺过程物料初始重量近似等于加 工后最终重量。如铸造、压力加工、粉末冶金、注塑成 形等,这些方法多用于毛坯制造,但也可直接成形零件。
2、材料去除法——零件的最终几何形状局限在毛坯的初始 几何形状范围内,零件形状的改变是通过去除一部分材 料,减少一部分重量来实现的。如切削与磨削,电火花 加工、电解加工等特种加工等。
b.连续式: 网带传送式烧结炉
4
4、后处理: (1)浸渗:利用烧结件的多孔性的毛细现象,浸入各种液体 (2)表面冷挤压 (3)切削加工 (4)热处理 (5)表面保护处理
5
五、粉末冶金成型的应用 1、机械制造中常用的粉末冶金材料 (1)粉末冶金减摩材料 (2)粉末冶金铁基结构材料 (3)粉末冶金摩擦材料
26
构造三维模型 模型近似处理
切片处理
激光
喷射源
固化树脂 切割箔材 烧结粉末
喷粘结剂 喷热熔材料
三维产品(样品/模具)
表面处理
27
图6-1 快速成型过程
设计
设计
铸造 锻压 焊接
模具
去
模具
毛坯 (大于工件)
除
半成品
加 工
a)
半成品 工件
样品
图6-2 传统加工与快速成型比较
粉末冶金成型技术

粉末冶金成型技术粉末冶金成型技术(PM)是一种新兴的金属加工技术,它使用粉末材料,经过热处理、压实、成形和加工等工艺,最终形成最终产品。
这种技术可以有效地生产复杂结构和高精度零件,被广泛应用于航天航空、汽车制造、电子信息、新材料研发等领域。
粉末冶金技术主要包括热解法(thermal decomposition)、汽化烧结法(vapour deposition sintering)和气相混合法(gas phase mixing)等。
热解法是目前最常用的一种技术,它利用热力学原理将粉末金属转化为熔融的金属液,然后将其冷却固化,最终形成最终产品。
汽化烧结法通过加热粉末材料来达到烧结的效果,最终形成的零件均匀性及结合强度较高,可应用于高强度零件的制造。
气相混合法利用点火系统在真空中燃烧粉末金属材料,使其形成金属熔融物,随后冷却固化即可形成最终零件。
粉末冶金技术具有诸多优势,如质量高、制造成本低、能够生产复杂结构复杂精度零件、有利于环境保护等。
然而由于其复杂性和技术门槛高,其产品形成损耗大,生产效率低,制造过程中不易控制精度等,使得粉末冶金技术的应用受到了一定的限制。
另外,粉末冶金技术的发展还需要更加完善的研究与管理体系。
粉末冶金技术的成功应用,需要良好的研究成果和合理的经济效益,这一技术必须结合全面的工艺改进技术、生产管理和后处理方法进行系统研究,以满足不断增长的市场需求。
综上所述,粉末冶金技术是一种潜在的应用范畴十分广泛的技术,它可广泛应用于复杂结构和精度零件的制造,极大地改变了传统的金属加工技术。
未来,粉末冶金技术将继续发展,在先进制造业及家用电器等领域获得更多的应用,成为一个重要的制造技术。
粉末冶金成型技术是一种新兴技术,它能够有效地生产复杂结构和高精度零件,它的应用范围也会随着新材料和新技术的不断发展而更新更换,并促进经济和生活进步。
未来,粉末冶金技术将迎来更大的发展,在航天航空、汽车制造、新材料研发及家用电器等领域都有广泛的应用前景。
05-2粉末冶金及其成型

结
构
工
艺
性
制
1.避免模具出现脆弱的尖角
品 的
因为压制模具工作时要承受较高的压力,它的各个零件都具有很高的硬度,若 压坯形状不合理,则极易折断。所以,应避免在压模结构上出现脆弱的尖角, 延长模具的使用寿命。
结
构
工
艺
性
制
2.避免模具和压坯出现局部薄壁
品
压制时,粉末基本不发生横向流动。为了保证压坯厚度、密度 均匀,粉末均匀填充型腔的各个部位,应避免模具和压坯局部出现
5 粉末冶金及其成型(2)
硬 • 硬质合金是一种优良的工具材料,主要用于切削工具、金属 成型工具、表面耐磨材料以及高刚性结构部件。
质 合 金 粉 末 冶 金
硬
• 硬质合金由硬质基体和黏接金属两部分组成。
质 合
• 硬质基体采用难熔金属化合物,主要是碳化钨和碳化钛 ,还有碳化钽、碳化铌和碳化钒等,保证合金具有较高 的硬度和耐磨性。
金
• 黏接金属用铁族金属及其合金,以钴为主,使合金具有
粉
一定的强度和韧度。
末
冶
金
粉 • 把粉料与热塑性树脂等有机物混练后得到的混合料,在注射机上 于一定温度和压力下高速注入模具,迅速冷凝后脱模取出坯体。
末 注 射 成 型 技 术
粉
优势
末
注
• 可以直接制造出有最终形状的零部件,节省原材料,减 少机械加工量。
结
构
工
艺
性
制
4.需要有脱模锥角或圆角
品
为方便脱模,应使与压制方向一致的内孔、外凸台等 有一定斜度或圆角。
的
结
构
工
艺
性
制
5.适应压制方向的需要
粉末冶金技术 第四讲 粉末成形概述

收缩率
S LD
L0 LD L0
100%
S LS
LD LS LD
100%
S LT
L0 LS L0
100%
成形工艺对后续工艺的影响
成形对机械加工的影响 ➢ 对加工余量的影响 ➢ 孔隙率对加工性能的影响
金属粉末与陶瓷粉末特性比较
➢ 粉末可塑性 ➢ 粉末粒度 ➢ 氧化性和冷变形强化性
金属与陶瓷成形工艺特点比较
成形工艺对后续工艺的影响
成形工艺对干燥工艺的影响 ➢ 坯体干燥过程与干燥缺陷 ➢ 挤制成形 ➢ 注浆成形 ➢ 轧膜成形 ➢ 压制成形等
成形工艺对后续工艺的影响
成形工艺对烧结的影响 ➢ 成形方法的影响 ➢ 成形压力的影响 ➢ 坯体密度均匀性的影响
成形工艺对后续工艺的影响
成形工艺对后续工艺的影响
形、热压注成形、注射成形、原位凝固成形 ➢ 无模具成形:轧制成形、挤压成形、楔形压形、
轧膜成形、流延法成形
注:至少有一个方向的尺寸是自由的。
成形坯体的结构与性质
➢ 结构:包含固、气、液相的多相体系 ➢ 性能:包括坯体的致密度或孔隙率、坯
体致密度或孔隙率分布的均匀性、坯体 强度、坯体外形完整性和表观质量及几 何尺寸
粉末冶金技术 第四讲
粉末成形概述
➢粉末成形方法分类 ➢前道基本工序对后道工序的影响 ➢金属成形与陶瓷成形工艺特点比较
术语
➢ 粉体 ➢ 坯料 ➢ 坯体 ➢ 烧结体
成形方法分类
➢ 按材料类别分类
了解各种材料、坯料所适用的成形方法
➢ 按坯料特性分类➢ 按成形续性分类了解连续、间歇、有模、无模成形方法
➢ 成形坯体具有一定强度的原因有哪些?
坯料对成形工艺的影响
粉末冶金材料及制备技术
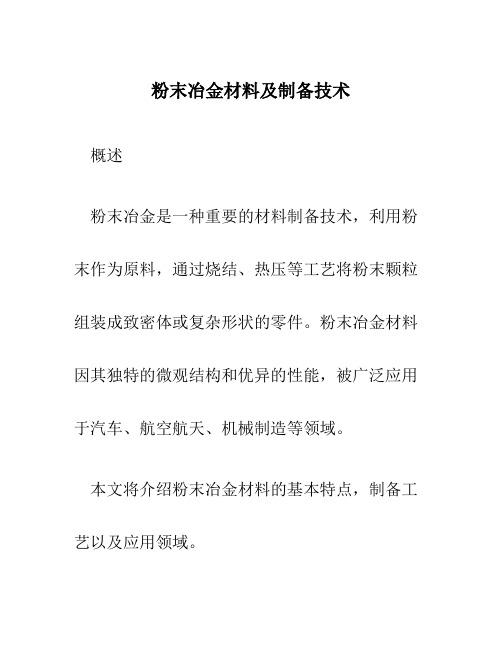
粉末冶金材料及制备技术概述粉末冶金是一种重要的材料制备技术,利用粉末作为原料,通过烧结、热压等工艺将粉末颗粒组装成致密体或复杂形状的零件。
粉末冶金材料因其独特的微观结构和优异的性能,被广泛应用于汽车、航空航天、机械制造等领域。
本文将介绍粉末冶金材料的基本特点,制备工艺以及应用领域。
粉末冶金材料的特点粉末冶金材料具有以下几个特点:1.化学均匀性:粉末冶金材料由单一原料粉末组成,保持了原料的化学均匀性,避免了其他制备工艺中容易出现的成分偏析问题。
2.孔隙率可控:通过调整粉末的颗粒大小和形状,以及制备工艺中的烧结、热压参数,可以控制材料的孔隙率。
这对于某些应用中需要具有特定孔隙结构的材料十分重要。
3.致密且均匀:粉末冶金材料的制备过程中,粉末颗粒会经历烧结或热压等工艺,使得颗粒之间发生固化,形成致密的材料结构。
同时,由于粉末冶金材料的制备过程是固相制备,因此几乎没有晶粒长大的问题,材料的晶界均匀性较好。
4.组织可控:粉末冶金材料的组织可以通过调整原料粉末的物理性质、添加外加剂以及制备工艺来进行调控。
这使得粉末冶金材料可以具备多种特殊的组织结构,如纳米晶材料、金属陶瓷复合材料等。
粉末冶金材料的制备技术粉末冶金材料的制备技术主要包括粉末制备和粉末冶金工艺。
粉末制备粉末冶金材料的制备首先需要粉末的制备。
常见的粉末制备方法包括:1.机械法:通过机械碾磨或球磨等机械力的作用,将原料材料研磨成粉末。
2.化学法:通过化学反应使得原料形成沉淀或气体生成,再进行沉淀或气体的分离和干燥,得到粉末。
3.物理法:包括气相凝聚法、电解法、热气法等,通过物理方法将原料转化为粉末。
粉末冶金工艺粉末冶金工艺是将粉末颗粒进行组装和固化的过程,常见的工艺包括:1.烧结:将粉末颗粒加热至接近熔点的温度,使得颗粒之间发生结合,形成致密体。
2.热压:在高温和高压条件下对粉末进行压制,使颗粒之间发生固化,形成致密体。
3.注射成形:将粉末和有机粘结剂混合后,通过注射成形的方式进行制备,形成绿体后再进行烧结。
粉末冶金成形及非金属成形

化工容器、管道、法兰接头、汽车零件、仪表罩壳
酚醛(PF) 强度和刚性好,耐磨性良好,易于成形
仪表外壳、灯头、插座
尼龙(PA) 韧性好,耐磨、耐油、吸水性大,影响尺寸稳定性
轴承、密封圈、轴瓦、石墨填充轴承
聚甲醛(POM)
耐磨、耐疲劳,抗冲击,摩擦系数低,吸水率小,但成形收缩率较大 大型轴承、齿轮、蜗轮、轴套。阀杆、螺母等。
浮动模压制:浮动模压制
压坯密度较均匀,适于压制 高度或厚度较大的制品。
2.粉末轧制 将粉末引入一对旋转轧辊之间使其压实成连续带坯
的方法。 适用于生产多孔材料、摩擦材料、复合材料和硬质合
金等的板材及带材。
3.挤压成形 将置于挤压筒内的粉末、压
坯或烧结体通过模孔压出的成 形方法
设备简单、生产率高,可以 获得沿长度方向密度均匀的制 品。 用于生产截面较简单的条、棒 和螺旋形条、棒(如麻花钻)
特点
第5章 粉末冶金成形
粉末冶金是制取金属粉末并通过成形和烧结等 工艺将金属粉末(或与非金属粉末)的混合物制 成制品的加工方法
既可以制取用普通熔炼方法难以制取的特殊 材料,又可以制造各种精密的机械零件 省工省料
模具和金属粉末成本较高
批量小时或制品尺寸过大时不宜采用
普通粉末冶金制品的密度较低且很不均匀,强 度比相应的铸件或锻件约低20%~30%;一般只适 用于中、小型制品的成批、大量生产。
具有特殊性能的制品如硬质合金、金属陶瓷等
3.影响粉末制品烧结质量的因素 粉末制品的烧结质量取决于烧结温度、烧结时间
和烧结气氛等因素。 (1) 烧结温度和时间: 烧结温度过高或或过低, 时间过长或过短,都会使产品性能下降
- 1、下载文档前请自行甄别文档内容的完整性,平台不提供额外的编辑、内容补充、找答案等附加服务。
- 2、"仅部分预览"的文档,不可在线预览部分如存在完整性等问题,可反馈申请退款(可完整预览的文档不适用该条件!)。
- 3、如文档侵犯您的权益,请联系客服反馈,我们会尽快为您处理(人工客服工作时间:9:00-18:30)。
机器设备在运转过程中,部分零件之间相互接触产生摩擦形成摩擦副。
摩擦副零件是机器设备的重要组成部分,其性能对机器设备使用寿命有着重要影响。
组成摩擦副的零件一般在相对速度高、接触比压大的摩擦工况下服役,因此此类零件磨损也较为严重。
现代工业发展促使了高能效和微型化机械设备的应用,这使得摩擦副零件工况条件更为苛刻,所以开发高性能摩擦副材料具有重要意义。
粉末冶金工艺生产机械零件具有突出的经济优势、良好的尺寸精度,并可生产形状复杂的零件。
因此,国内外对粉末冶金摩擦副材料及制品开发高度关注,并开展了大量工作。
粉末冶金摩擦副材料主要包括两类,一类是粉末冶金减摩耐磨材料,另一类是粉末冶金摩擦材料。
其中粉末冶金减摩耐磨材料主要是在基体中浸入润滑油或加入固体润滑剂,使材料具有减摩耐磨性能,这类材料主要用来制造轴承、轴瓦以及滑块等零件。
粉末冶金摩擦材料主要由基体组元、润滑组元和摩擦组元组成,要求材料具有较高的摩擦系数和耐磨性,主要用于离合器和制动器等关键零部件。
粉末成形作为粉末冶金重要的一项生产工序,直接影响生坯的密度和强度,进而对制品性能产生影响。
目前,应用于摩擦副零件制备的成形工艺主要有传统模压成形、粉末注射成形、温压以及粉末锻造技术等,这些成形工艺各有其独特的优点。
本文简述了粉末冶金摩擦副产品的性能特点,介绍了其成形工艺技术发展现状,并对摩擦副零件市场进行了展望。
1 粉末冶金摩擦副材料发展现状1.1 粉末冶金摩擦材料机械设备运行速度以及负载增加,使得传动装置对摩擦材料性能要求变得越来越高。
粉末冶金技术可以在大范围内改变材料组分,所以粉末冶金摩擦材料工作可靠性、摩擦系数稳定性和耐摩性较好。
常见粉末冶金摩擦材料主要有铁基和铜基两类。
铜基摩擦材料主要应用于高铁、风电及航空航天等领域,其摩擦学性能与材料组分有关,如在基体中添加适量合金元素Sn可提高材料强度和硬度;还可通过润滑组元和摩擦组元的合理搭配,来提高材料耐磨性。
与铜基摩擦材料相比,铁基摩擦材料更耐高温,成本也相对较低,但此类材料容易与对偶件发生咬合,且抗氧化性和导热性相对较差;为了改善这种状况,可以在基体中添加合金元素Cu等。
近年来,C/C复合材料也被广泛用于飞机和高速列车等摩擦副部件制造中。
这种材料虽然密度较低,但其高温强度较为优异,但此类材料摩擦系数相对较低,高温抗氧化性较差;为了改善材料性能,可在基体中加入S i C等来提高材料的抗氧化性和耐磨性。
1.2 粉末冶金减摩耐磨材料粉末冶金减摩耐磨材料在基体选择上与粉末冶金摩擦材料基本相同,但主要考虑减摩性能。
传统粉末冶金减摩耐磨材料是通过浸油处理使基体含有一定润滑油,它是以牺牲材料本身力学性能来获得减摩效果。
由于润滑油在某些工况条件(如超低温、高真空和高速高负载)下容易失效,使材料减摩耐磨性能下降甚至完全丧失,导致零件严重磨损。
因此,粉末冶金减摩耐磨固体自润滑材料应运而生。
目前,粉末冶金减磨耐磨固体自润滑材料研究主要集中在开发固体润滑剂方面,包括多元固体润滑剂和纳米固体润滑剂。
固体润滑剂开发和应用对于解决关键零部件摩擦问题具有重要意义。
在某些特殊工况条件下,仅依靠单一润滑学性能要求。
例如,在烧结过程中,分发生固相反应,生成Mo和Mo(1.合肥工业大学材料学院,合肥 230009;2.安徽省粉末冶金工程技术研究中心,合肥 230009;3.合肥波林新材料股份有限公司,合肥 231121)摘 要:机器设备失效主要原因之一是摩擦副零件的磨损。
作为高性能摩擦副材料的重要组成部分,粉末冶金摩擦副材料研究与开发受到了国内外的广泛关注。
传统粉末冶金摩擦副制品由于受孔隙和强度等因素限制,在高速、重载等工况条件下容易发生失效,所以发展高性能的粉末冶金摩擦副材料及其制备技术具有重要意义。
主要简述了国内外粉末冶金减摩耐磨材料和摩擦材料最新研究进展,重点介绍了一些典型粉末冶金摩擦副零件成形工艺与特点,同时对粉末冶金摩擦副零件市场应用和发展趋势进行讨论。
关键词:粉末冶金 摩擦副 磨损 成形技术通讯作者:程继贵。
材料的机械性能;若同时添加石墨和hBN,不仅可以获得优良的摩擦磨损性能,还能有效改善材料的力学性能。
材料的力学性能和摩擦学性能在一定程度上受固体润滑剂颗粒粒径影响。
添加微米石墨和纳米石墨的铜基材料的摩擦磨损性能变化情况如图1所示,可以发现石墨含量较小时,添加纳米石墨铜基复合材料的摩擦学性能明显要优于添加微米石墨的铜基复合材料。
(a)摩擦系数(b)磨损率材料,导致其在特殊工况条件下容易发生失效。
国内某些企业为了提高制品力学性能,采用复压复烧工艺来制备摩擦副零件。
复压在提高制品密度时,内部会发生明显的晶粒碎化和晶格歪扭,从而引起粉末颗粒加工硬化;经复烧可消除加工硬化,并细化晶粒,实现组织均匀化。
但复压复烧工艺生产摩擦副零件加工工序较多,导致生产成本成倍增加。
2.2 粉末注射成形与传统工艺相比,粉末注射成形具有精度高、组织均匀以及生产成本低等特点。
因此,粉末注射成形技术在制备高性能、复杂形状的摩擦副零部件方面具有巨大优势。
粉末注射成形工艺流程如图2所示,其被誉为“当今最热门的零部件成形技术”之一。
图2 粉末注射成形工艺流程图相关研究者采用粉末注射成形法制备了铜基摩擦材料,研究了石墨含量对材料摩擦学性能的影响,结果表明:当石墨含量小于10%时,磨损率和摩擦系数随石墨含量增加而减小;当石墨含量为10%~15%时,摩擦系数可以在较低水平保持稳定,此时材料密度与硬度也相对较高;当石墨含量大于15%时,材料摩擦系数和磨损率均有所增大。
2.3 温压成形温压是将预热混合粉末(如铁粉、石墨粉、合金元素粉及高温润滑剂)在预热封闭钢模中进行加压成形,其工艺流程如图3所示。
采用温压工艺制备的材料密度较高,且成本低于复压复烧、渗铜与热锻。
图3 温压工艺流程图相关研究者采用温压成形与微波烧结相结合方法制备HRC58,摩擦系数仅为0.085,该材料被应用于燃烧发动机阀导杯中,并进行了500h的测试,测试结束后工作表面上未出现任何明显磨损。
3 粉末冶金摩擦副零件的市场应用和发展趋势由于粉末冶金材料性能优异且成本较低,所以在汽车、家电和飞机等领用中得到了广泛应用。
在汽车上有许多摩擦副部件,其中汽车底盘中有减振器零件,如导向器、活塞和底阀座;制动系统中有ABS传感器、刹车片等;泵类零件主要有燃油泵、机油泵和变速器泵中关键零部件,如齿轮、内外转子等;发动机中有导管、座圈、连杆、轴承座、可变气门正时系统(VVT)关键零部件和排气管支座等;变速器中有同步毂和行星齿轮架等零件。
在这些零件中,近90%可采用粉末冶金方法制造。
然而,我国粉末冶金摩擦副制品在汽车上的应用水平仍然低于发达国家。
由此可见,粉末冶金摩擦副零件在汽车上仍有很大的发展空间。
近年来,我国家电行业蓬勃发展,仅2017年,空调市场零售量就达到5572万台,同比增长29.4%。
以家用空调压缩机中多孔滑动轴承为例,该零件是典型的摩擦副制品,一般要由粉末冶金方法来制造,由此说明,家用电器是粉末冶金摩擦副零件应用的主要市场之一。
在飞机装置中,刹车片是用量最大的摩擦副部件,在飞机着陆过程中,刹车片承受非常高的载荷,表面瞬时温度非常高,造成其非常容易发生粘结,导致刹车失效而引起轮胎爆裂。
到目前为止,绝大多数军用飞机和民用机都采用粉末冶金刹车片。
虽然粉末冶金摩擦副零件在整个粉末冶金零件中难以单独统计,但无论是按重量还是按零件数量,粉末冶金摩擦副零件在汽车、摩托车中所占的比例都远远大于其他粉末冶金零件。
由此可见,粉末冶金摩擦副零件在整个粉末冶金零件中处于快速发展地位。
随着人类环保意识加强,改善发动机性能、减轻重量、替代或补充动力系统以及提高燃油效率是未来汽车主要发展方向,这对汽车摩擦副零件提出了更高要求。
未来粉末冶金摩擦副零件的发展方向是降低磨损和提高摩擦部件寿命,同时承担高负荷和高滑动速度。
4 结语目前,粉末冶金摩擦副产品正处于快速发展阶段,其材料成分优化、工艺技术创新、摩擦磨损机理研究以及新技术新工艺如何与实际生产相结合仍然是需要解决的难题。
粉末成形工艺作为主要生产工序,通过对其工艺参数改进和技术引进,已经可以较好地制备高密度生坯,从而为生产高性能粉末冶金摩擦副材料提供保障。
粉末冶金摩擦副参考文献[1]周海滨.粉末冶金摩擦材料特征摩擦组元与铜基体的界面及其对摩擦磨损机理影响研究[D].长沙:中南大学,2014.[2]周海滨,姚萍屏,肖叶龙,等.铜基粉末冶金摩擦材料特征摩擦组元与基体的界面形成及磨损机理[J].中国有色金属学报,2016,(2):328-336.[3]周海滨,姚萍屏,肖叶龙,等.SiC颗粒强化铜基粉末冶金摩擦材料的表面形貌特征及磨损机理[J].中国有色金属学报,2014,(9):2272-2279.[4]冀盛亚,任兆麟,龚安华.载流条件下铜基粉末冶金滑板材料的电弧侵蚀防护[J].热加工工艺,2011,(10):74-77.Developments and Applications of Powder Metallurgy Friction Pairs and Their Forming TechnologyXU Jiabing1,2,3, CHENG Jigui1,2,3, CHEN Pengqi1,2,3, CHEN Wenchao1,2, XU Wei2,3(1.School of Materials Science and Engineering, Hefei University of Technology, Hefei 230009;2.Engineering Research Center of Powder Metallurgy of Anhui Province, Hefei 230009;3.Hefei Bolin Advanced Materials Co., Ltd, Hefei 231121)Abstract: One of the main causes of machine equipment failure is the wear of the friction pair parts. As an important part of high-performance friction accessory materials, research and development of powder metallurgy friction accessory materials have received extensive attention at home and abroad. Traditional powder metallurgy friction by-products are subject to limitations such as porosity and strength, and are prone to failure under high-speed and heavy-duty conditions. Therefore, it is of great significance to develop high-performance powder metallurgy friction pair materials and their preparation techniques. The latest research progress of powder metallurgy anti-friction and wear-metallurgy friction parts are discussed.Key wordstechnology。