烧结气氛论文:烧结工艺对铜基粉末冶金摩擦材料性能的影响
铜基粉末冶金摩擦材料
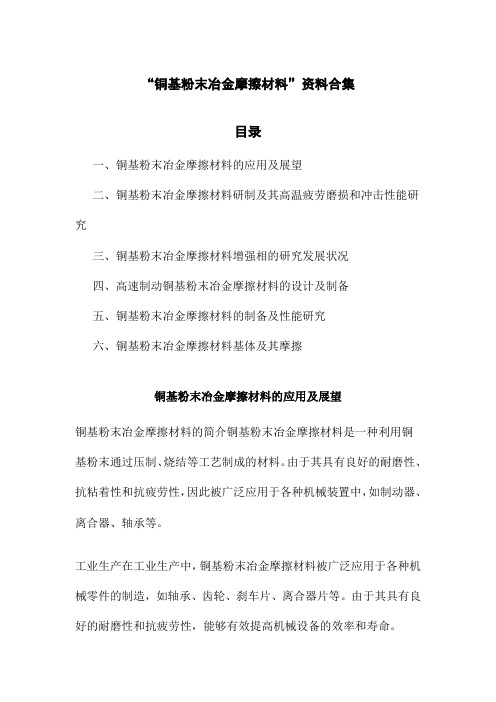
“铜基粉末冶金摩擦材料”资料合集目录一、铜基粉末冶金摩擦材料的应用及展望二、铜基粉末冶金摩擦材料研制及其高温疲劳磨损和冲击性能研究三、铜基粉末冶金摩擦材料增强相的研究发展状况四、高速制动铜基粉末冶金摩擦材料的设计及制备五、铜基粉末冶金摩擦材料的制备及性能研究六、铜基粉末冶金摩擦材料基体及其摩擦铜基粉末冶金摩擦材料的应用及展望铜基粉末冶金摩擦材料的简介铜基粉末冶金摩擦材料是一种利用铜基粉末通过压制、烧结等工艺制成的材料。
由于其具有良好的耐磨性、抗粘着性和抗疲劳性,因此被广泛应用于各种机械装置中,如制动器、离合器、轴承等。
工业生产在工业生产中,铜基粉末冶金摩擦材料被广泛应用于各种机械零件的制造,如轴承、齿轮、刹车片、离合器片等。
由于其具有良好的耐磨性和抗疲劳性,能够有效提高机械设备的效率和寿命。
医学领域在医学领域,铜基粉末冶金摩擦材料被用于制作人工关节、手术器械等医疗器械。
由于其对人体的生物相容性和耐腐蚀性优良,能够有效降低术后感染的风险,提高手术效果。
建筑与交通在建筑与交通领域,铜基粉末冶金摩擦材料被应用于各种摩擦片、刹车片、离合器片等产品的制造。
由于其具有优异的摩擦性能和耐久性,能够为建筑和交通工具提供更安全、更稳定的运行保障。
铜基粉末冶金摩擦材料的展望随着科技的不断发展,铜基粉末冶金摩擦材料的研究也在不断深入。
未来,铜基粉末冶金摩擦材料将面临以下发展方向:高性能化为了满足各种复杂工况下的高负荷、高速度、长寿命的使用要求,铜基粉末冶金摩擦材料需要具备更高的性能,如更优异的耐磨性、抗疲劳性和抗粘着性等。
绿色环保化随着环保意识的不断提高,未来的铜基粉末冶金摩擦材料将更加注重绿色环保制造,减少对环境的污染和资源的浪费。
智能化制造随着智能制造技术的不断发展,未来的铜基粉末冶金摩擦材料将更加注重智能化制造,实现生产过程的自动化、信息化、数字化,提高生产效率和产品质量。
结论铜基粉末冶金摩擦材料作为一种重要的功能材料,在工业生产、医学、建筑、交通等领域具有广泛的应用前景。
烧结钢烧结过程中的气氛控制
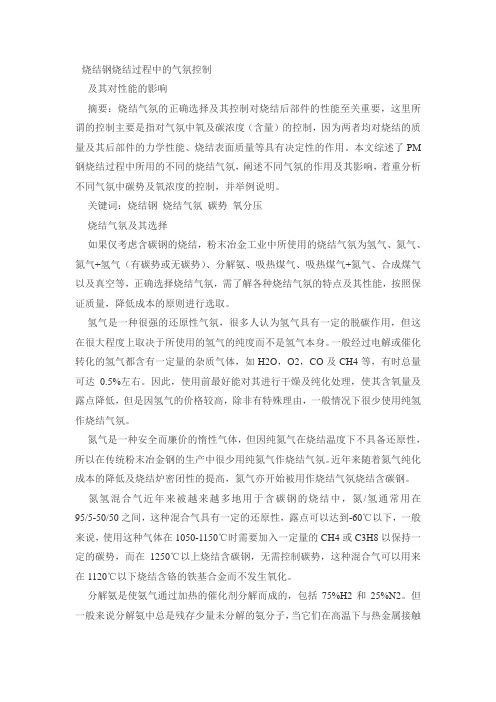
烧结钢烧结过程中的气氛控制及其对性能的影响摘要:烧结气氛的正确选择及其控制对烧结后部件的性能至关重要,这里所谓的控制主要是指对气氛中氧及碳浓度(含量)的控制,因为两者均对烧结的质量及其后部件的力学性能、烧结表面质量等具有决定性的作用。
本文综述了PM 钢烧结过程中所用的不同的烧结气氛,阐述不同气氛的作用及其影响,着重分析不同气氛中碳势及氧浓度的控制,并举例说明。
关键词:烧结钢烧结气氛碳势氧分压烧结气氛及其选择如果仅考虑含碳钢的烧结,粉末冶金工业中所使用的烧结气氛为氢气、氮气、氮气+氢气(有碳势或无碳势)、分解氨、吸热煤气、吸热煤气+氮气、合成煤气以及真空等,正确选择烧结气氛,需了解各种烧结气氛的特点及其性能,按照保证质量,降低成本的原则进行选取。
氢气是一种很强的还原性气氛,很多人认为氢气具有一定的脱碳作用,但这在很大程度上取决于所使用的氢气的纯度而不是氢气本身。
一般经过电解或催化转化的氢气都含有一定量的杂质气体,如H2O,O2,CO及CH4等,有时总量可达0.5%左右。
因此,使用前最好能对其进行干燥及纯化处理,使其含氧量及露点降低,但是因氢气的价格较高,除非有特殊理由,一般情况下很少使用纯氢作烧结气氛。
氮气是一种安全而廉价的惰性气体,但因纯氮气在烧结温度下不具备还原性,所以在传统粉末冶金钢的生产中很少用纯氮气作烧结气氛。
近年来随着氮气纯化成本的降低及烧结炉密闭性的提高,氮气亦开始被用作烧结气氛烧结含碳钢。
氮氢混合气近年来被越来越多地用于含碳钢的烧结中,氮/氢通常用在95/5-50/50之间,这种混合气具有一定的还原性,露点可以达到-60℃以下,一般来说,使用这种气体在1050-1150℃时需要加入一定量的CH4或C3H8以保持一定的碳势,而在1250℃以上烧结含碳钢,无需控制碳势,这种混合气可以用来在1120℃以下烧结含铬的铁基合金而不发生氧化。
分解氨是使氨气通过加热的催化剂分解而成的,包括75%H2和25%N2。
粉末冶金工艺对制备工艺材料性能的影响
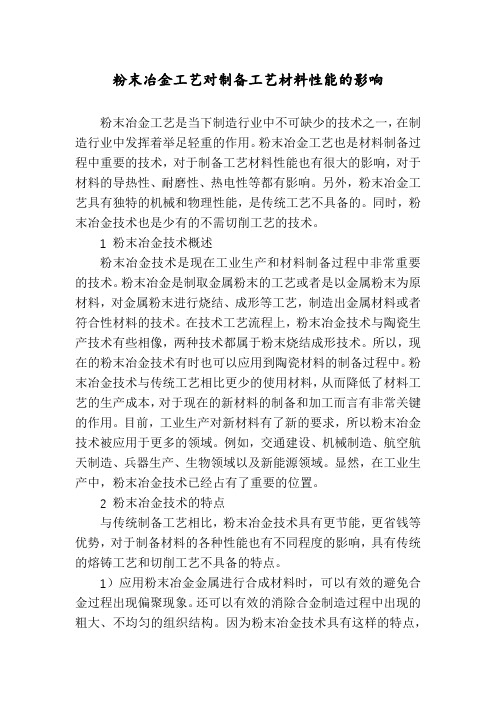
粉末冶金工艺对制备工艺材料性能的影响粉末冶金工艺是当下制造行业中不可缺少的技术之一,在制造行业中发挥着举足轻重的作用。
粉末冶金工艺也是材料制备过程中重要的技术,对于制备工艺材料性能也有很大的影响,对于材料的导热性、耐磨性、热电性等都有影响。
另外,粉末冶金工艺具有独特的机械和物理性能,是传统工艺不具备的。
同时,粉末冶金技术也是少有的不需切削工艺的技术。
1 粉末冶金技术概述粉末冶金技术是现在工业生产和材料制备过程中非常重要的技术。
粉末冶金是制取金属粉末的工艺或者是以金属粉末为原材料,对金属粉末进行烧结、成形等工艺,制造出金属材料或者符合性材料的技术。
在技术工艺流程上,粉末冶金技术与陶瓷生产技术有些相像,两种技术都属于粉末烧结成形技术。
所以,现在的粉末冶金技术有时也可以应用到陶瓷材料的制备过程中。
粉末冶金技术与传统工艺相比更少的使用材料,从而降低了材料工艺的生产成本,对于现在的新材料的制备和加工而言有非常关键的作用。
目前,工业生产对新材料有了新的要求,所以粉末冶金技术被应用于更多的领域。
例如,交通建设、机械制造、航空航天制造、兵器生产、生物领域以及新能源领域。
显然,在工业生产中,粉末冶金技术已经占有了重要的位置。
2 粉末冶金技术的特点与传统制备工艺相比,粉末冶金技术具有更节能,更省钱等优势,对于制备材料的各种性能也有不同程度的影响,具有传统的熔铸工艺和切削工艺不具备的特点。
1)应用粉末冶金金属进行合成材料时,可以有效的避免合金过程出现偏聚现象。
还可以有效的消除合金制造过程中出现的粗大、不均匀的组织结构。
因为粉末冶金技术具有这样的特点,所以在制备高性能稀土材料、稀土发过材料和新型技术材料的过程中都要应用粉末冶金技术,从而提升生产材料的整体性能。
2)粉末冶金技术能够使制备材料具有更好的导电性能以及物理性能,所以被更多的应用于制备非品、纳米晶体和微品等高性能非平衡材料的过程。
3)粉末冶金技术的应用,在材料制备过程中可以让多种材料有效的复合,并且材料复合后还能够保持多种原材料的独有特性,使复合材料的性能更具多元性,讓制备出的复合材料能够被更加广泛的影响,提升了复合材料的实用性。
粉末冶金综述论文
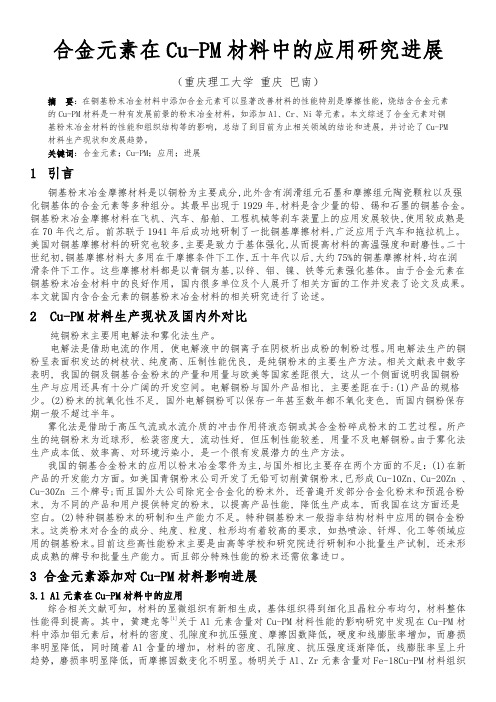
合金元素在Cu-PM材料中的应用研究进展(重庆理工大学重庆巴南)摘要:在铜基粉末冶金材料中添加合金元素可以显著改善材料的性能特别是摩擦性能,烧结含合金元素的Cu-PM材料是一种有发展前景的粉末冶金材料,如添加Al、Cr、Ni等元素。
本文综述了合金元素对铜基粉末冶金材料的性能和组织结构等的影响,总结了到目前为止相关领域的结论和进展,并讨论了Cu-PM 材料生产现状和发展趋势。
关键词:合金元素;Cu-PM;应用;进展1 引言铜基粉末冶金摩擦材料是以铜粉为主要成分,此外含有润滑组元石墨和摩擦组元陶瓷颗粒以及强化铜基体的合金元素等多种组分。
其最早出现于1929年,材料是含少量的铅、锡和石墨的铜基合金。
铜基粉末冶金摩擦材料在飞机、汽车、船舶、工程机械等刹车装置上的应用发展较快,使用较成熟是在70年代之后。
前苏联于1941年后成功地研制了一批铜基摩擦材料,广泛应用于汽车和拖拉机上。
美国对铜基摩擦材料的研究也较多,主要是致力于基体强化,从而提高材料的高温强度和耐磨性。
二十世纪初,铜基摩擦材料大多用在干摩擦条件下工作,五十年代以后,大约75%的铜基摩擦材料,均在润滑条件下工作。
这些摩擦材料都是以青铜为基,以锌、铝、镍、铁等元素强化基体。
由于合金元素在铜基粉末冶金材料中的良好作用,国内很多单位及个人展开了相关方面的工作并发表了论文及成果。
本文就国内含合金元素的铜基粉末冶金材料的相关研究进行了论述。
2 Cu-PM材料生产现状及国内外对比纯铜粉末主要用电解法和雾化法生产。
电解法是借助电流的作用, 使电解液中的铜离子在阴极析出成粉的制粉过程。
用电解法生产的铜粉呈表面积发达的树枝状、纯度高、压制性能优良, 是纯铜粉末的主要生产方法。
相关文献表中数字表明, 我国的铜及铜基合金粉末的产量和用量与欧美等国家差距很大, 这从一个侧面说明我国铜粉生产与应用还具有十分广阔的开发空间。
电解铜粉与国外产品相比, 主要差距在于:(1)产品的规格少。
烧结工艺对铁基粉末冶金组织性能影响研究

烧结工艺对铁基粉末冶金组织性能影响研究摘要:借助传统金相、XRD及扫描电镜测试技术,研究了不同烧结工艺对铁基粉末冶金组织性能的影响,优化了烧结工艺。
将一定比例的铁粉进行充分混合后压制成型,在不同温度下进行烧结,随炉冷却到室温或淬火。
利用电子显微镜进行金相分析,扫描电镜观察微观组织及断口形貌,测量测密度与耐磨性等综合性能。
研究结果表明,烧结温度越高,粉末颗粒被烧结的程度越好,组织均匀性明显提高,材料的硬度、耐磨性也得到提高。
关键词:铁基粉末冶金;烧结工艺;粒度;性能铁基粉末冶金材料是发展迅速的工程材料。
近年来,由于具有优异的技术经济性,铁基粉末冶金材料逐渐取代部分传统的锻铸材料在机械、航天、农机,特别是汽车工业得到广泛的应用,制造像汽车齿轮、齿类零件和凸轮轴等几何形状复杂,加工困难或加工成本高的部件。
目前,粉末冶金技术正向着高致密化高性能化集成化和低成本等方向发展[1]。
1.实验内容实验样品采用在200目铁粉中添加3 %的400目、3%的800目和0.3%的3000目的羰基铁粉,0.2%碳粉。
在研钵中均匀混合30min-50min后,将粉末置于钢模中用平板硫化机采用单向压制出直径为20mm,高为5mm的圆柱形试样,压力定位600MPa。
按照表1中的各种配方成型件烧结热处理工艺,将试样置于箱式电阻炉进行烧结,用耐火土覆盖[2]。
成品试样测试内容包括断口扫描、XRD、密度测试、金相组织观察等[3]。
2.实验结果与分析由试样在不同烧结温度下烧结金相照片图1可以看出,当烧结温度为1000℃时,粉末基本得到烧结,但也存在组织不均匀,铁颗粒之间烧结不够充分,还没有扩散连接的部位,;当烧结温度为1050℃时,烧结效果也要优于1000℃;当烧结温度为1100℃,可以看到组织较均匀,也看不到明显的碳颗粒,铁粉之间得到了很好的烧结,缺陷也有所减少,组织均匀程度好[4]。
从表2可以看出,在相同的成分下,随着温度的提高,试样密度也在提高。
Ti(C,N)基金属陶瓷抗弯强度的Weibull分析

Ti(C,N)基金属陶瓷抗弯强度的Weibull分析王晓灵;刘咏【摘要】作为金属切削工具材料,Ti(C,N)基金属陶瓷强韧性的可靠性是制约其推广应用的主要因素.由于Ti(C,N)基金属陶瓷比WC基硬质合金脆性更大,其强韧性对内外缺陷更敏感,抗弯强度分散性更大,使用时,极易出现突然断裂,失效可预测性低.本文采用Weibull统计强度理论以及双样本t检验的方法对工业化批量生产的Ti(C,N)基金属陶瓷的抗弯强度(TRS)的可靠性及其主要影响因素进行分析.结果显示,物料批次、烧结炉次(烧结气氛)对抗弯强度的分散性有显著影响.同物料批次、同炉次烧结的Ti(C,N)基金属陶瓷样本的抗弯强度具有较大的Weibull模数,最高可达m=41.64,而多物料批次、多炉次烧结样本的抗弯强度的分散性较大,Weibull模数约为10~15,特征强度约为(2350±150)MPa.抗弯强度的Weibull分布还受到样品尺寸的影响,小尺寸样品的特征强度更大,但Weibull模数更小.【期刊名称】《粉末冶金材料科学与工程》【年(卷),期】2017(022)004【总页数】10页(P546-555)【关键词】Ti(C,N);金属陶瓷;抗弯强度;可靠性;Weibull分析;假设检验【作者】王晓灵;刘咏【作者单位】中南大学粉末冶金研究院,长沙 410083;自贡硬质合金有限责任公司成都分公司,成都 610100;中南大学粉末冶金研究院,长沙 410083【正文语种】中文【中图分类】TF125.31上世纪70年代初,奥地利KIEFFER等[1]发现,在TiC-Ni-Mo(Mo2C)金属陶瓷中添加TiN,可以显著提高除抗热变形能力外的其它各项性能,由此发明了Ti(C,N)基金属陶瓷[2]。
作为金属切削工具材料,与WC-Co硬质合金相比,Ti(C,N)基金属陶瓷具有相对更高的硬度,更好的高温性能和化学稳定性,在某些应用场合,如钢件的高速精加工等,具有极大的优势[3−7]。
铜_石墨烧结材料中第三体对摩擦磨损性能的影响

第26卷 第4期Vol 126 No 14材 料 科 学 与 工 程 学 报Journal of Materials Science &Engineering 总第114期Aug.2008文章编号:167322812(2008)0420554205铜2石墨烧结材料中第三体对摩擦磨损性能的影响符 蓉,高 飞,宋宝韫,于庆军(大连交通大学材料科学与工程学院,辽宁大连 116028) 【摘 要】 采用粉末冶金技术制备了铜和铜-石墨粉末冶金材料。
通过定速摩擦试验机测试了材料的摩擦磨损性能,观察比较了两种材料摩擦学特征和表面摩擦第三体的变化过程。
结果表明:摩擦表面第三体状态与材料成分密切相关,并影响材料的摩擦系数和磨损量。
纯铜摩擦时,形成的第三体颗粒尺寸大、粘着性强,金属间的粘着撕裂造成摩擦系数剧烈波动和磨损量加大;添加石墨,细化了第三体颗粒尺寸,流动性好的第三体容易覆盖表面的损伤区,这有利于增加真实接触面积,减少应力集中,起到稳定摩擦系数、降低磨损量的作用。
【关键词】 第三体;摩擦磨损;铜石墨烧结材料中图分类号:TF125;TB333 文献标识码:ACharacteristics of Third Bodies and the FrictionProperties of the Sintered Cu 2graphiteFU Rong ,G AO Fe ,SONG B ao 2yun ,Y U Q ing 2jun(College of Materials Science and E ngineering ,Dalian Jiaotong U niversity ,Dalian 116028,China)【Abstract 】 Powder metallurgy techniques were employed to fabricate Cu and Cu 2graphite materials ,whose friction andwear properties were measured by a constant 2speed tester.The tribological characteristics and the evolution of the third bodies at the surface were investigated.The results show that the states of third bodies are relevant to the composition and they have effects on the f riction coefficients as well as the wear.In case of pure Cu ,third bodies have large sizes and the adhesive abrasion occurs between the metals ,resulting in oscillation of f riction coefficients and a large loss of mass.Adding some graphite ,which brings third bodies with good mobility ,can refine the size of third bodies.These third bodies cover the interfaces ,increase the real contacting areas ,reduce the stress concentration ,and as a result ,stabilize the f riction coefficients and reduce the wear.【K ey w ords 】 third bodies ;f riction and wear ;sintered Cu 2graphite收稿日期:2007208205;修订日期:2007210215基金项目:国家863计划资助项目(2006AA03Z515)和国家自然科学基金资助项目(50375025)作者简介:符 蓉(1965-),女,副教授,主要从事摩擦磨损及第三体摩擦机理的研究。
压力烧结工艺对铜-石墨复合材料的性能影响03
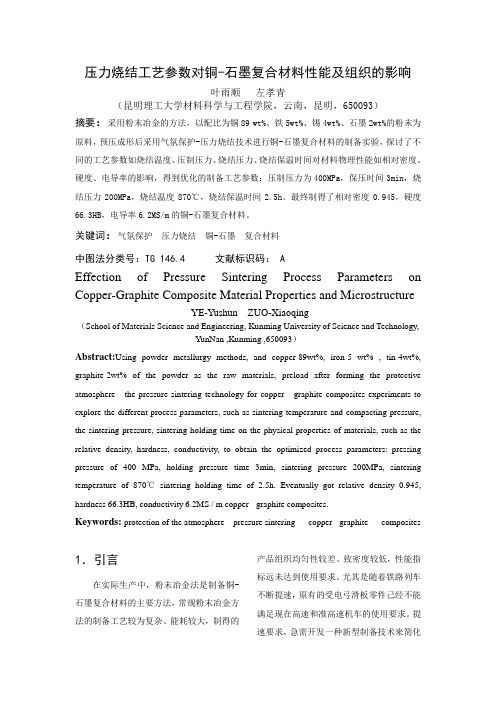
压力烧结工艺参数对铜-石墨复合材料性能及组织的影响叶雨顺左孝青(昆明理工大学材料科学与工程学院,云南,昆明,650093)摘要:采用粉末冶金的方法,以配比为铜89 wt%、铁5wt%、锡4wt%、石墨2wt%的粉末为原料,预压成形后采用气氛保护-压力烧结技术进行铜-石墨复合材料的制备实验,探讨了不同的工艺参数如烧结温度、压制压力、烧结压力、烧结保温时间对材料物理性能如相对密度、硬度、电导率的影响,得到优化的制备工艺参数:压制压力为400MPa,保压时间3min,烧结压力200MPa,烧结温度870℃,烧结保温时间2.5h。
最终制得了相对密度0.945,硬度66.3HB,电导率6.2MS/m的铜-石墨复合材料。
关键词:气氛保护压力烧结铜-石墨复合材料中图法分类号:TG 146.4 文献标识码: AEffection of Pressure Sintering Process Parameters on Copper-Graphite Composite Material Properties and MicrostructureYE-Yushun ZUO-Xiaoqing(School of Materials Science and Engineering, Kunming University of Science and Technology,YunNan ,Kunming ,650093)Abstract:Using powder metallurgy methods, and copper-89wt%, iron-5 wt% , tin-4wt%, graphite-2wt% of the powder as the raw materials, preload after forming the protective atmosphere - the pressure sintering technology for copper - graphite composites experiments to explore the different process parameters, such as sintering temperature and compacting pressure, the sintering pressure, sintering holding time on the physical properties of materials, such as the relative density, hardness, conductivity, to obtain the optimized process parameters: pressing pressure of 400 MPa, holding pressure time 3min, sintering pressure 200MPa, sintering temperature of 870℃sintering holding time of 2.5h. Eventually got relative density 0.945, hardness 66.3HB, conductivity 6.2MS / m copper - graphite composites.Keywords: protection of the atmosphere pressure sintering copper - graphite composites1.引言在实际生产中,粉末冶金法是制备铜-石墨复合材料的主要方法,常规粉末冶金方法的制备工艺较为复杂、能耗较大,制得的产品组织均匀性较差、致密度较低,性能指标远未达到使用要求。
- 1、下载文档前请自行甄别文档内容的完整性,平台不提供额外的编辑、内容补充、找答案等附加服务。
- 2、"仅部分预览"的文档,不可在线预览部分如存在完整性等问题,可反馈申请退款(可完整预览的文档不适用该条件!)。
- 3、如文档侵犯您的权益,请联系客服反馈,我们会尽快为您处理(人工客服工作时间:9:00-18:30)。
烧结气氛论文:烧结工艺对铜基粉末冶金摩擦材料性能的影响【中文摘要】随着我国铁路运输业的飞速发展,列车运行速度一提再提,这就对制动摩擦材料提出了更为苛刻的要求。
铜基粉末冶金摩擦材料因其具有高的机械强度、高导热性和优良的摩擦磨损性能而成为高速列车制动闸片的首选材料,如何通过制备工艺和原料体系的改进提高材料的耐温性能和摩擦稳定性一直是人们研究的重点。
本文通过采用不同的烧结工艺制备了铜基粉末冶金摩擦材料,研究不同烧结温度和烧结气氛对材料显微组织、物理机械性能和摩擦磨损性能的影响,并探讨了材料在不同制动条件下的摩擦磨损行为及机理,结果表明:(1)铜基粉末冶金摩擦材料中各组元分布均匀,组元间接触紧密,鳞片状石墨垂直于压制方向呈层状分布,SiO2以黑色大颗粒状镶嵌于铜基体内。
随的烧结温度提高,材料中各组元间的孔隙减少,当达到一定程度后,孔隙不再减少;烧结气氛对材料的形貌无明显影响。
(2)烧结工艺对材料的物理-机械性能影响较大。
随烧结温度的提高,采用N2和N2+H2混合气制备材料的密度先升后降,抗压强度较大,且随之呈上升趋势;H2气氛制备材料的密度呈下降趋势,抗压强度与其他两种气氛下制备的相比显著降低,且呈下降趋势。
(3)相同制动压力下,材料的摩擦系数随的转速的提高先升高后降低,磨损量随着转速的提高逐渐增加;在较低转速时,磨损以粘着磨损为主,随着转速提高,磨损逐渐表现为氧化磨损和疲劳磨损。
N2+H2混合气氛烧结材料在较低转速下具有较好的摩擦性能,磨损量很低,且随烧结温度提高呈下降趋势;N2气氛烧结材料在较高转速下摩擦性能较好,摩擦稳定性好,而且磨损量也较低。
(4)在一定转速下,随着制动压力的提高,材料的摩擦系数呈下降趋势,摩擦稳定性系数先升高后下降,磨损量显著增加;较低压力时,磨损主要由粘着机理控制,较高压力时,磨损主要表现为疲劳磨损和剥层脱落。
N2+H2混合气氛烧结材料在高制动压力下具有较好的摩擦性能,摩擦稳定性最高,磨损量最小,且随烧结温度升高先减少后增加,在1000℃时最低。
【英文摘要】With the development of train transport, the requirements are stiffer and stiffer in the properties of the braking materials by the speed improvement. Because of the high mechanical strength, high conductibility and excellent friction and wear properties, Cu-based P/M friction materials have been the leading material for friction brake of high-speed train.Cu-based P/M friction material has been made by different sintering process. The effect of sintering temperature and atmosphere on the micro-structure, physical and mechanical properties and friction and wear properties of material have been investigated, and the friction and wear behavior and mechanism in the different braking conditions have been discussed. The results show:(1) Scaly graphite and SiO2 are well-distributed in Cu-based P/M materials. With theincreasing of sintering temperature, the pore volume between different components decreases gradually till reached a certain degree. Sintering atmospheres have no effect on the micro-structure of materials.(2) Sintering process have important effects on the physical and mechanical properties of materials. With the increasing of sintering temperature, the densities of materials sintered in N2 andN2+H2 atmosphere increases firstly and decreases then, but the densities in H2 trends to decrease; the compressive strength of materials sintered in N2 and N2+H2 are higher than that in H2.(3) On the same braking pressure, with speed increased, the frictional coefficient increases firstly and decreases then, but the wear volume increases gradually. The slipping speed changes, the wear mechanism changes also. At low speeds, adhesion wear is the main mechanism, but oxidation and fatigue wear takes on priority at high speeds. The materials sintered in the N2+H2 atmosphere have the best frictional property at low speeds, besides, the wear volumes are the lowest and decreases with the increasing sintering temperature. The materials sintered in the N2 atmosphere have the best frictional property at high speeds, and with high frictional stability and lower wear volume at the same time.(4) At the certain speed, with brakingpressure increased, the frictional coefficient trends to decrease, frictional stability increases firstly and decreases then, but the wear volume increases greatly. On low pressures, the main wear mechanism is adhesion wear, but fatigue and flake wear are the main mechanism on high pressures. The materials sintered in the N2+H2 atmosphere have the best frictional property on high pressure, the highest frictional stability and the lowest wear volumes, besides, with sintering temperature increased, the wear volume decreases firstly and increases then, and has the lowest value in the sintering temperature of 1000℃.【关键词】烧结气氛烧结温度粉末冶金铜基摩擦材料摩擦磨损【英文关键词】sintering atmosphere sintering temperature powder metallurgy Cu-based friction material friction and wear【目录】烧结工艺对铜基粉末冶金摩擦材料性能的影响摘要6-7ABSTRACT7-8目录9-12第一章绪论12-25 1.1 高速列车发展概述12-13 1.2 摩擦材料概述13-16 1.2.1 摩擦材料的种类13-15 1.2.1.1 有机摩擦材料13-14 1.2.1.2 铸铁14 1.2.1.3 粉末冶金摩擦材料14-15 1.2.1.4 碳/碳复合材料15 1.2.2 摩擦材料技术要求15-16 1.3 粉末冶金摩擦材料16-23 1.3.1 粉末冶金摩擦材料组成16-19 1.3.1.1 基体组元17 1.3.1.2 摩擦组元17-18 1.3.1.3 润滑组元18-19 1.3.2 粉末冶金摩擦材料种类19-22 1.3.2.1 铜基粉末冶金摩擦材料19-20 1.3.2.2 铁基粉末冶金摩擦材料20-21 1.3.2.3 铁-铜基粉末冶金摩擦材料21 1.3.2.4 其它金属基粉末冶金摩擦材料21-22 1.3.3 粉末冶金摩擦材料在铁道车辆上的应用22-23 1.4 选题意义和主要工作23-25第2章试验设计和研究方法25-30 2.1 材料组成和制备工艺25 2.1.1 材料组成25 2.1.2 制备工艺25 2.2 试验方案25-26 2.3 性能检测手段26-30 2.3.1 密度和孔隙率27-28 2.3.2 硬度28 2.3.3 抗压强度28 2.3.4 组织结构和表面形貌分析28-29 2.3.5 摩擦表面成分及相结构分析29 2.3.6 摩擦磨损性能测试29-30第3章材料的物理机械性能及组织结构研究30-38 3.1 烧结温度和气氛对材料密度和孔隙率的影响30-32 3.2 烧结温度和气氛对材料抗压强度的影响32-33 3.3 烧结温度和气氛对材料硬度的影响33-34 3.4 烧结温度和气氛对材料组织结构的影响34-36 3.5 本章小结36-38第4章材料的摩擦磨损性能研究38-61 4.1 不同温度烧结材料的摩擦磨损性能研究38-53 4.1.1 转速对材料摩擦磨损性能的影响38-47 4.1.1.1 转速对材料摩擦系数的影响39-40 4.1.1.2 不同转速下摩擦系数的稳定性研究40-41 4.1.1.3 转速对材料磨损量的影响41-43 4.1.1.4 摩擦磨损机理分析43-47 4.1.2 制动压力对材料摩擦磨损性能的影响47-53 4.1.2.1 压力对材料摩擦系数的影响48-49 4.1.2.2 不同制动压力下摩擦系数的稳定性研究49-50 4.1.2.3 压力对材料磨损量的影响50-52 4.1.2.4 摩擦磨损机理分析52-53 4.2 不同气氛烧结材料的摩擦磨损性能研究53-60 4.2.1 转速对材料摩擦磨损性能的影响53-57 4.2.1.1 转速对材料摩擦系数的影响53-55 4.2.1.2 不同转速下摩擦系数的稳定性研究55 4.2.1.3 转速对材料磨损量的影响55-57 4.2.2 制动压力对材料摩擦磨损性能的影响57-60 4.2.2.1 压力对材料摩擦系数的影响57-58 4.2.2.2 不同制动压力下摩擦系数的稳定性研究58-59 4.2.2.3 压力对材料磨损量的影响59-60 4.3 本章小结60-61结论61-62致谢62-63参考文献63-68攻读硕士学位期间发表的学术论文68。