粉末冶金烧结工艺
粉末冶金常用烧结方法
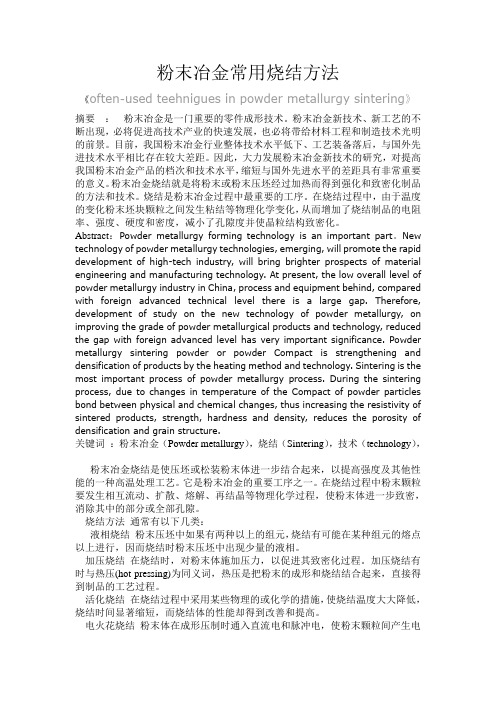
粉末冶金常用烧结方法《often-used teehnigues in powder metallurgy sintering》摘要:粉末冶金是一门重要的零件成形技术。
粉末冶金新技术、新工艺的不断出现,必将促进高技术产业的快速发展,也必将带给材料工程和制造技术光明的前景。
目前,我国粉末冶金行业整体技术水平低下、工艺装备落后,与国外先进技术水平相比存在较大差距。
因此,大力发展粉末冶金新技术的研究,对提高我国粉末冶金产品的档次和技术水平,缩短与国外先进水平的差距具有非常重要的意义。
粉末冶金烧结就是将粉末或粉末压坯经过加热而得到强化和致密化制品的方法和技术。
烧结是粉末冶金过程中最重要的工序。
在烧结过程中,由于温度的变化粉末坯块颗粒之间发生粘结等物理化学变化,从而增加了烧结制品的电阻率、强度、硬度和密度,减小了孔隙度并使晶粒结构致密化。
Abstract:Powder metallurgy forming technology is an important part。
New technology of powder metallurgy technologies, emerging, will promote the rapid development of high-tech industry, will bring brighter prospects of material engineering and manufacturing technology. At present, the low overall level of powder metallurgy industry in China, process and equipment behind, compared with foreign advanced technical level there is a large gap. Therefore, development of study on the new technology of powder metallurgy, on improving the grade of powder metallurgical products and technology, reduced the gap with foreign advanced level has very important significance. Powder metallurgy sintering powder or powder Compact is strengthening and densification of products by the heating method and technology. Sintering is the most important process of powder metallurgy process. During the sintering process, due to changes in temperature of the Compact of powder particles bond between physical and chemical changes, thus increasing the resistivity of sintered products, strength, hardness and density, reduces the porosity of densification and grain structure.关键词:粉末冶金(Powder metallurgy),烧结(Sintering),技术(technology),粉末冶金烧结是使压坯或松装粉末体进一步结合起来,以提高强度及其他性能的一种高温处理工艺。
粉末冶金原理-烧结

有限固溶系:Fe-C、Fe-Ni、Fe-Cu、W-Ni等
互不固溶系:Ag-W、Cu-W、Cu-C等
液相烧结
在烧结过程中出现液相的烧结。
包括:稳定液相(长存液相)烧结
不稳定液相(瞬时液相)烧结
二、烧结理论研究的目的、范畴和方法
研究目的:研究粉末压坯在烧结过程中微观结构的演化
物质蒸发的角度
3.蒸气压差
曲面与平面的饱和蒸气压之差
P P0 / KTr
1 1 1 r x
吉布斯-凯尔文方程
x
1 1 r
P 0 / KT 颈 P
对于球表面,1/r=2/a (a为球半径)
P 0 2 / KTa 球 P
颗粒表面(凸面)与烧结颈表面(凹面)之间存在大的蒸气压 差,导致物质向烧结颈迁移
烧 结 的 重 要 性
4)纳米块体材料的获得依 赖烧结过程的控制
(三) 烧结的分类
粉末体烧结类型 不施加外压力
施加外压力
固相烧结 单相粉末
多相粉末
液相烧结
长存液相 瞬时液相
热压 热锻
热等静压
反应烧结
活化烧结
超固相线烧结 液相热压 反应热压 反应热等静压
强化烧结
按烧结过程有无外加压力
●无压烧结 (Pressureless sintering) 包括:固相烧结、液相烧结等 ●加压烧结(有压烧结)
烧结颈长大
3.封闭孔隙球化和缩小阶段 当烧结体密度达到90%以后,• 多数孔隙被完全分隔,闭 孔数量大的增加,孔隙形状趋近球形并不断缩小。在这个 阶段,整个烧结体仍可缓慢收缩,但主要是靠小孔的消失 和孔隙数量的减少来实现。这一阶段可以延续很长时间, 但是仍残留少量的隔离小孔隙不能消除。也就是一般不能 达到完全致密。
烧结球团工艺流程
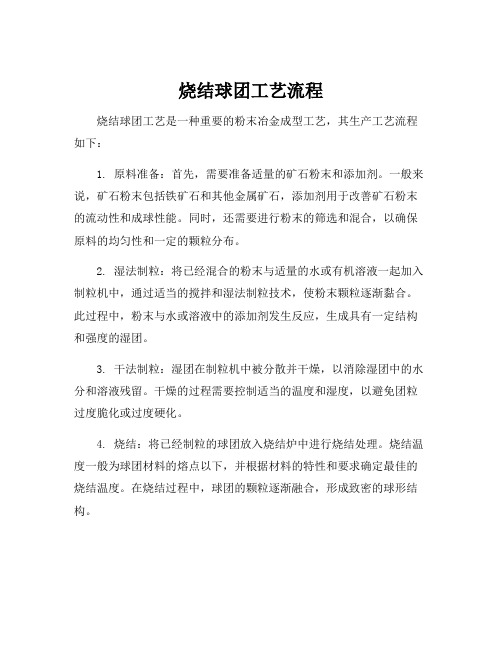
烧结球团工艺流程烧结球团工艺是一种重要的粉末冶金成型工艺,其生产工艺流程如下:1. 原料准备:首先,需要准备适量的矿石粉末和添加剂。
一般来说,矿石粉末包括铁矿石和其他金属矿石,添加剂用于改善矿石粉末的流动性和成球性能。
同时,还需要进行粉末的筛选和混合,以确保原料的均匀性和一定的颗粒分布。
2. 湿法制粒:将已经混合的粉末与适量的水或有机溶液一起加入制粒机中,通过适当的搅拌和湿法制粒技术,使粉末颗粒逐渐黏合。
此过程中,粉末与水或溶液中的添加剂发生反应,生成具有一定结构和强度的湿团。
3. 干法制粒:湿团在制粒机中被分散并干燥,以消除湿团中的水分和溶液残留。
干燥的过程需要控制适当的温度和湿度,以避免团粒过度脆化或过度硬化。
4. 烧结:将已经制粒的球团放入烧结炉中进行烧结处理。
烧结温度一般为球团材料的熔点以下,并根据材料的特性和要求确定最佳的烧结温度。
在烧结过程中,球团的颗粒逐渐融合,形成致密的球形结构。
5. 冷却:烧结完成后,将球团从烧结炉中取出并迅速冷却。
此过程可以通过自然冷却或使用冷却设备来实现。
冷却过程中,球团的温度逐渐降低,使其结构更加稳定和坚固。
6. 筛分和包装:经过冷却的球团经过筛分,将不符合规格的球团重新破碎与再制粒,符合规格的球团进行必要的包装和标识。
同时,还需对产品进行质量检查,确保产品达到指标要求。
烧结球团工艺流程的实施需要注意以下几点:1. 原料的选择和准备是保证产品质量的关键。
需要选择高质量的矿石粉末和合适的添加剂,并进行充分的筛选和混合,以确保原料的均匀性和颗粒分布。
2. 制粒过程需要控制适当的湿度和搅拌强度,以确保粉末颗粒的黏结和团粒的形成。
同时,制粒后的干燥也需要控制适当的温度和湿度,避免团粒过度脆化或过度硬化。
3. 烧结条件的选择要考虑材料的熔点和烧结性能,以确保球团的致密性和强度。
同时,烧结过程中的温度和时间也需要精确控制,以避免烧结不完全或过度烧结。
4. 冷却过程需要迅速进行,以避免球团受热应力影响产生开裂和变形。
热压烧结的操作步骤及应用
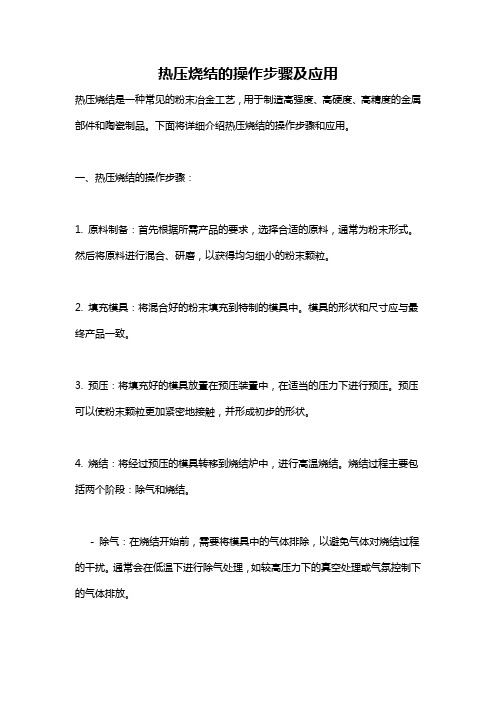
热压烧结的操作步骤及应用热压烧结是一种常见的粉末冶金工艺,用于制造高强度、高硬度、高精度的金属部件和陶瓷制品。
下面将详细介绍热压烧结的操作步骤和应用。
一、热压烧结的操作步骤:1. 原料制备:首先根据所需产品的要求,选择合适的原料,通常为粉末形式。
然后将原料进行混合、研磨,以获得均匀细小的粉末颗粒。
2. 填充模具:将混合好的粉末填充到特制的模具中。
模具的形状和尺寸应与最终产品一致。
3. 预压:将填充好的模具放置在预压装置中,在适当的压力下进行预压。
预压可以使粉末颗粒更加紧密地接触,并形成初步的形状。
4. 烧结:将经过预压的模具转移到烧结炉中,进行高温烧结。
烧结过程主要包括两个阶段:除气和烧结。
- 除气:在烧结开始前,需要将模具中的气体排除,以避免气体对烧结过程的干扰。
通常会在低温下进行除气处理,如较高压力下的真空处理或气氛控制下的气体排放。
- 烧结:将除气后的模具加热到适当的温度,使粉末颗粒发生相互结合和扩散,形成致密的固体。
烧结温度、时间和气氛的选择取决于所用材料和所需产品的特性。
5. 冷却:在烧结结束后,将模具从炉中取出,进行自然冷却或采用其他冷却方式。
冷却过程中,要注意避免产品出现热应力导致的开裂。
6. 除模:将烧结后的成品从模具中取出。
通常需要经过机械加工或其他后续处理步骤,以满足最终产品的要求。
二、热压烧结的应用:1. 金属制品:热压烧结可以用于制造各种金属制品,如钢制品、铝合金制品等。
由于热压烧结可以使金属颗粒充分结合,因此制造的金属制品具有高强度、高硬度和良好的耐磨性。
常见的应用包括汽车零部件、工具和模具、航空航天部件等。
2. 陶瓷制品:热压烧结是制造陶瓷制品的常用工艺之一。
热压烧结可以使陶瓷颗粒结合更紧密,从而获得高强度、高硬度和高密度的陶瓷制品。
常见的应用包括陶瓷刀具、陶瓷瓷砖、陶瓷合成材料等。
3. 硬质合金:热压烧结是制造硬质合金的主要工艺之一。
硬质合金通常由金属粉末和碳化物等非金属粉末混合而成。
粉末冶金新技术-烧结

用SPS制取块状纳米晶Fe90Zr7B3软磁的过程是: 先将由非 晶薄带经球磨制成的50~150μm非晶粉末装入WC/Co合金 模具内,并在SPS烧结机上烧结(真空度1×10-2Pa以下、升温 速度0.09~1.7K/s、温度673~873K、压力590MPa), 再把所 得的烧结体在1×10-2Pa真空下、以3 7K/s速度加热到923K、 保温后而制成。材料显示较好的磁性能:最大磁导率29800、 100Hz下的动态磁导率3430, 矫顽力12A/m。
3
双频微波烧结炉 生产用大型微波烧结炉 已烧结成多种材料:如陶瓷和铁氧体等材料。另 外,在日本又开发出相似的毫米波烧结技术,并成功 地在2023K下保温1h烧结成全致密的AlN材料。
4
2.爆炸压制技术 爆炸压制又称冲击波压制是一种有前途的工艺
方法,它在粉末冶金中发挥了很重要的作用, 爆炸压 制时,只是在颗粒的表面产生瞬时的高温,作用时间 短,升温和降温速度极快。适当控制爆炸参数,使得 压制的材料密度可以达到理论密度的90%以上,甚至 达到99%。
3)快速脉冲电流的加入, 无论是粉末内的放电部位还是焦耳 发热部位, 都会快速移动, 使粉末的烧结能够均匀化。
11
与传统的粉末冶金工艺相比,SPS工艺的特点是:
• 粉末原料广泛:各种金属、非金届、合金粉末,特别是 活性大的各种粒度粉末都可以用作SPS 烧结原科。
• 成形压力低:SPS烛结时经充分微放电处理,烧结粉末表 面处于向度活性化状态.为此,其成形压力只需要冷压烧 结的l/10~1/20。
17
SPS制备软磁材料 通常用急冷或喷射方法可得到FeMe(Nb、Zr、Hf)B的非 晶合金,在稍高于晶化温度处理后, 可得到晶粒数10nm,具有 体心立方结构,高Bs 、磁损小的纳米晶材料。但非晶合金目 前只能是带材或粉末, 制作成品还需要将带材重叠和用树脂固 结, 这使得成品的密度和Bs均变低。近年, 日本采用SPS工艺研 究FeMeB块材的成形条件及磁性能。
粉末冶金原理-烧结

按烧结过程有无液相出现分类
■ 固相烧结: 单元系固相烧结:单相(纯金属、 化合物、固溶体)粉末的烧结: 烧结过程无化学反应、无新相形 成、无物质聚集状态的改变。 多元系固相烧结:两种或两种以 上组元粉末的烧结过程,包括反 应烧结等。 元限因溶系:Cu-Ni、Cu-Au、 Ag-Au等。 有限固溶系:Fe-C、Fe-Ni、FeCu、W-Ni等。 互不固溶系:Ag-W、Cu-W、 Cu-C等。
低包括下述几个方面: (1)由于颗粒结合面(烧结颈〉的增大和颗粒表面平直化,粉末体 的总比表面积和总表面自由能减小; (2)烧结体内孔隙的总体积和总表面积减小; (3)粉末颗粒内晶格畸变部分消除。
二、烧结的热力学问题
■ 粉末过剩自由能包括表面能和晶格畸变能,在烧结过程中特 别是早期阶段,作用较大的主要是表面能。
核,结晶长大等原子过程形成烧结颈。在这一阶段中,颗粒内的 晶粒不发生变化,颗粒外形也基本未变,整个烧结不发生收缩, 密度增加也极微,但是烧结体的强度和导电性由于颗粒结合面增 大而有明显增加。
粉末等温烧结过程的三个阶段
等温烧结过程按时间大致可分为三个界限不十分明显的阶段: 1、烧结颈长大阶段 ■ 原子向颗粒结合面的大量迁移使烧结颈扩大,颗粒间距离缩小,
(二)烧结机构的分类
2、宏观迁移:V-V ■ 体积扩散(volumeorlatticediffusion):借助于空位运动,原子
等向颈部迁移。 ■ 粘性流动(viscousflow):非晶材料,在剪切应力作用下,产生
粘性流动,物质向颈部迁移。 ■ 塑性流动(plasticflow):烧结温度接近物质熔点,当颈部的拉
对烧结定义的理解1
■ 粉末也可以烧结(不一定要成形) 松装烧结,制造过滤材料(不锈钢,青铜,黄铜,铁等)和催化材料 (铁,镍,铂等)等。
粉末冶金烧结的原理是什么
粉末冶金烧结的原理是什么首先,在粉末冶金烧结过程中,需要将金属或非金属粉末按照一定比例混合均匀,并进行固定的颗粒度筛选。
然后,将混合好的粉末通过压制工艺,将其压制成一定形状的坯料。
压制过程中,需要选用适当的模具和压力来保证坯料的整体性能和形状精度。
在烧结过程中,首先需要将压制好的坯料放入烧结炉中进行加热。
粉末烧结过程中,温度是一个非常重要的因素。
一般来说,烧结温度应该高于材料的熔点,但低于其蒸发温度。
在加热过程中,粉末颗粒的表面会发生扩散,使得颗粒之间逐渐结合。
当温度升高到足够高时,颗粒之间的结合力会增强,进而产生一定的熔融,促使颗粒之间的结合更为紧密,形成致密的块材。
在粉末冶金烧结过程中,还需要选用合适的还原气氛来促进烧结过程的进行。
还原气氛是指在烧结过程中,为了避免粉末在高温下与氧气反应而氧化,需要在烧结过程中加入一定的还原剂,使气氛富含还原性气体。
常用的还原气氛有氢气(H2)、氮气(N2)等。
还原气氛的选用对于烧结过程的成功与否具有重要影响。
一方面,氢气在高温下具有很强的还原性,能高效地还原粉末中的氧化物,促进颗粒之间的结合。
另一方面,氮气可以有效地减少粉末的氧化反应,并且氮气在高温下不会与大多数金属发生化合反应,可作为一种较好的保护气氛。
需要注意的是,还原气氛的选择也要考虑到烧结材料的特点和要求。
例如,一些材料在高温下容易吸氧或与氢气反应,就不适合在氢气气氛中进行烧结。
此外,还原气氛的流速和温度也需要控制得当,以确保烧结过程的均匀性和质量稳定性。
综上所述,粉末冶金烧结的原理主要包括粉末的压制和烧结过程。
在烧结过程中,还原气氛的选用是至关重要的,可以通过选择合适的还原剂和控制流速、温度等条件来提高烧结过程的效果。
粉末冶金材料的烧结
粉末冶金材料的烧结在粉末冶金生产过程中,为了将成型工艺制得的压坯或者松装粉末体制成有一定强度、一定密度的产品,需要在适当的条件下进行热处理,最常用的工艺是烧结。
烧结是把粉末或粉末压坯后,在适当的温度和气氛条件下加热的过程,从而使粉末颗粒相互黏结起来,改善其性能。
烧结的结果是颗粒间发生黏结,烧结体强度增加,而且多数情况下,其密度也提高。
在烧结过程中,发生一系列的物理和化学变化,粉末颗粒的聚集体变为晶粒的聚集体,从而获得具有所需物理、力学性能的制品或材料。
在粉末冶金生产过程中,烧结是最基本的工序之一。
从根本上说,粉末冶金生产过程一般是由粉末成型和粉末毛坯热处理这两道基本工序组成的。
虽然在某些特殊情况下(如粉末松装烧结)缺少成型工序,但是烧结工序或相当于烧结的高温工序(如热压或热锻)是不可缺少的。
另外,烧结工艺参数对产品性能起着决定性的作用,由烧结工艺产生的废品是无法通过其他的工序来挽救的。
影响烧结的两个重要因素是烧结时间和烧结气氛。
这两个因素都不同程度地影响着烧结工序的经济性,从而对整个产品成本产生影响。
因此,优化烧结工艺,改进烧结设备,减少工序的物质和能量消耗,如降低烧结温度、缩短烧结时间,对产品生产的经济性具有重大意义。
一、烧结过程的基本类型用粉末烧结的方法可以制得各种纯金属、合金、化合物以及复合材料。
烧结体按粉末原料的组成可分为由纯金属、化合物或固溶体组成的单相系,由金属,金属、金属-非金属、金属化合物组成的多相系。
为了反映烧结的主要过程和烧结机构的特点,通常按烧结过程有无明显液相出现和烧结系统的组成对烧结进行分类,如固相烧结和液相烧结,单元系烧结和多元系烧结等。
二、固相烧结粉末固相烧结是指整个烧结过程中,粉末压坯的各个组元都不发生熔化,即无液相出现和形成的烧结过程。
按其组元的多少,可分为单元系固相烧结和多元系固相烧结两类。
1.单元系固相烧结单元系固相烧结,即单一粉末成分的烧结。
例如各种纯金属的烧结、预合金化粉末的烧结、固定成分的化合物粉末的烧结等,均为单元系固相烧结。
热压烧结原理
热压烧结原理
热压烧结是一种常用的粉末冶金工艺,通过高温和高压下将粉末颗粒结合成致
密的块状材料。
本文将介绍热压烧结的原理及其在工业生产中的应用。
热压烧结的原理是利用高温下材料的扩散和形变特性,使粉末颗粒之间发生结合,从而形成致密的块状材料。
在热压烧结过程中,首先需要将粉末颗粒置于模具中,然后施加高温和高压,使粉末颗粒发生塑性变形和扩散,最终形成致密的块状材料。
热压烧结的原理可以通过以下几个步骤来详细解释:
首先,粉末颗粒在高温下会发生表面扩散,当颗粒之间的表面接触面积增大时,会促进颗粒之间的结合。
其次,高温下的材料会发生形变,当粉末颗粒受到高压作用时,会发生塑性变形,使得颗粒之间产生更多的接触点,从而增强颗粒之间的结合力。
最后,通过高温和高压的作用,粉末颗粒之间的结合变得更加牢固,最终形成致密的块状材料。
热压烧结在工业生产中有着广泛的应用,特别是在粉末冶金、陶瓷制品、复合
材料等领域。
在粉末冶金中,热压烧结可以将金属粉末制成高强度、高硬度的零部件,提高材料的密度和机械性能。
在陶瓷制品的生产中,热压烧结可以制备出高密度、高强度的陶瓷制品,提高产品的质量和耐磨性。
在复合材料的制备中,热压烧结可以将不同材料的粉末颗粒结合成复合材料,拓展材料的应用范围和性能。
总之,热压烧结是一种重要的粉末冶金工艺,通过高温和高压下将粉末颗粒结
合成致密的块状材料。
其原理是利用材料在高温下的扩散和形变特性,使粉末颗粒之间发生结合。
热压烧结在工业生产中有着广泛的应用,可以制备出高性能的材料,提高产品的质量和性能。
希望本文对热压烧结的原理和应用有所帮助,谢谢阅读!。
2024年粉末冶金的烧结技术(三篇)
2024年粉末冶金的烧结技术⑴按原料组成不同分类。
可以将烧结分为单元系烧结、多元系固相烧结及多元系液相烧结。
单元系烧结是纯金属(如难熔金属和纯铁软磁材料)或化合物(Al2O3、B4C、BeO、MoSi2等)熔点以下的温度进行固相烧结。
多元系固相烧结是由两种或两种以上的组元构成的烧结体系,在其中低熔成分的熔点温度以下进行的固相烧结。
粉末烧结合金多属于这一类。
如Cu-Ni、Fe-Ni、Cu-Au、W-Mo、Ag-Au、Fe-Cu、W-Ni、Fe-C、Cu-C、Cu-W、Ag-W等。
多元系液相烧结以超过系统中低熔成分熔点的温度进行的烧结。
如W-Cu-Ni、W-Cu、WC-Co、TiC-Ni、Fe-Cu(Cu10%、Fe-Ni-Al、Cu-Pb、Cu-Sn、Fe-Cu(Cu10%)等⑵按进料方式不同分类。
分为为连续烧结和间歇烧结。
连续烧结烧结炉具有脱蜡、预烧、烧结、制冷各功能区段,烧结时烧结材料连续地或平稳、分段地完成各阶段的烧结。
连续烧结生产效率高,适用于大批量生产。
常用的进料方式有推杆式、辊道式和网带传送式等。
间歇烧结零件置于炉内静止不动,通过控温设备,对烧结炉进行需要的预热、加热及冷却循环操作,完成烧结材料的烧结过程。
间歇烧结可依据炉内烧结材料的性能确定合适的烧结制度,但生产效率低,适用于单件、小批量生产,常用的烧结炉有钟罩式炉、箱式炉等。
除上述分类方法外。
按烧结温度下是否有液相分为固相烧结和液相烧结;按烧结温度分为中温烧结和高温烧结(1100~1700℃),按烧结气氛的不同分为空气烧结,氢气保护烧结(如钼丝炉、不锈钢管和氢气炉等)和真空烧结。
另外还有超高压烧结、活化热压烧结等新的烧结技术。
2.影响粉末制品烧结质量的因素影响烧结体性能的因素很多,主要是粉末体的性状、成形条件和烧结的条件。
烧结条件的因素包括加热速度、烧结温度和时间、冷却速度、烧结气氛及烧结加压状况等。
⑴烧结温度和时间烧结温度的高低和时间的长短影响到烧结体的孔隙率、致密度、强度和硬度等。
- 1、下载文档前请自行甄别文档内容的完整性,平台不提供额外的编辑、内容补充、找答案等附加服务。
- 2、"仅部分预览"的文档,不可在线预览部分如存在完整性等问题,可反馈申请退款(可完整预览的文档不适用该条件!)。
- 3、如文档侵犯您的权益,请联系客服反馈,我们会尽快为您处理(人工客服工作时间:9:00-18:30)。
粉末冶金中的烧结
烧结是粉末冶金过程中最重要的工序。
在烧结过程中,由于温度的变化粉末坯块颗粒之间发生粘结等物理化学变化,从而增加了烧结制品的电阻率、强度、硬度和密度,减小了孔隙度并使晶粒结构致密化。
一.定义
将粉末或粉末压坯经过加热而得到强化和致密化制品的方法和技术。
二.烧结分类
根据致密化机理或烧结工艺条件的不同,烧结可分为液相烧结、固相烧结、活化烧结、反应烧结、瞬时液相烧结、超固相烧结、松装烧结、电阻烧结、电火花烧结、微波烧结和熔浸等。
1.固相烧结:按其组元的多少可分为单元系固相烧结和多元系固相烧结两类。
单元系固相烧结纯金属、固定成分的化合物或均匀固溶体的松装粉末或压坯在熔点以下温度(一般为绝对熔点温度的2/3一4/5)进行的粉末烧结。
单元系固相烧结过程大致分3个阶段:
(1)低温阶段(T烧毛0.25T熔)。
主要发生金属的回复、吸附气体和水分的挥发、压坯内成形剂的分解和排除。
由于回复时消除了压制时的弹性应力,粉末颗粒间接触面积反而相对减少,加上挥发物的排除,烧结体收缩不明显,甚至略有膨胀。
此阶段内烧结体密度基本保持不变。
(2)中温阶段(T烧(0.4~。
.55T动。
开始发生再结晶、粉末颗粒表面氧化物被完全还原,颗粒接触界面形成烧结颈,烧结体强度明显提高,而密度增加较慢。
(3)高温阶段(T烧二0.5一。
.85T熔)。
这是单元系固相烧结的主要阶段。
扩散和流动充分进行并接近完成,烧结体内的大量闭孔逐渐缩小,孔隙数量减少,烧结体密度明显增加。
保温一定时间后,所有性能均达到稳定不变。
(2)多元固相烧结:组成多元系固相烧结两种组元以上的粉末体系在其中低熔组元的熔点以下温度进行的粉末烧结。
多元系固相烧结除发生单元系固相烧结所发生的现象外,还由于组元之间的相互影响和作用,发生一些其他现象。
对于组元不相互固溶的多元系,其烧结行为主要由混合粉末中含量较多的粉末所决定。
如铜一石墨混合粉末的烧结主要是铜粉之间的烧结,石墨粉阻碍铜粉间的接触而影响收缩,对烧结体的强度、韧性等都有一定影响。
对于能形成固溶体或化合物的多元系固相烧结,除发生同组元之间的烧结外,还发生异组元之间的互溶或化学反应。
烧结体因组元体系不同有的发生收缩,有的出现膨胀。
异扩散对合金的形成和合金均匀化具有决定作用,一切有利于异扩散进行的因素,都能促进多元系固相烧结过程。
如采用较细的粉末,提高粉末混合均匀性、采用部分预合金化粉末、提高烧结温度、消除粉末颗粒表面的吸附气体和氧化膜等。
2.活化烧结:是指采用物理或化学的手段使烧结温度降低、烧结时间缩短、烧结体活化烧结性能提高的一种粉末冶金方法.活化烧结工艺分为物理活化烧结工艺和化学活化烧结工艺两大类。
物理活化烧结:物理活化烧结工艺有依靠周期性改变烧结温度、施加机械振动、超声波和外应力等促进烧结过程。
化学活化烧结工艺:(1)预氧化烧结。
(2)改变烧结气氛的成分和含量。
(3)粉末内添加微量元素。
(4)使用超细粉末、高能球磨粉末进行活化烧结。
活化烧结主要用于钨、钼、铼、铁、钽、钒、铝、钛和硬质化合物材料等的烧结。
活化烧结过程烧结过程是一个物理化学反应过程,其烧结反应速度常数K可用下式表示
[1]:K=AexP(-Q/RT)式中A为包含反应原子碰撞的“频率因素”在内的常数;Q为烧结过程活化能;T为烧结温度。
由上式可以看出,提高烧结温度T、降低烧结活化能Q和增大A值均可提高烧结速度。
活化烧结是指降低烧结活化能Q的烧结方法。
实现方式活化烧结主要是从3个方面来实现的:(1)改变粉末表面状态,提高粉末表面原子活性和原子的扩散能力。
(2)改变粉末颗粒接触界面的特性,以改善原子扩散途径。
(3)改善烧结时物质的迁移方式。
[2]
活化剂的选择准则(1).活化剂在烧结过程中形成低熔点液相(2).活化剂在基体中的溶解度应低,而基体组元在活化剂中的溶解度要大。
(3).活化剂应在烧结过程中偏聚在基体颗粒之间,为基体组元间的物质迁移提供通道。
三.烧结气氛
为了控制周围环境对烧结制品的影响并调整烧结制品成分,在烧结中使用以下几类不同功能的烧结气氛:
1.氧化性气氛,包括纯氧、空气、水蒸气等,用于贵金属的烧结,氧化物弥散强化材料和某些含氧化物质点电接触材料的内氧化烧结以及预氧化活化烧结;
2.还原性气氛,包括氢、分解氨、煤气、转换天然气等,用于烧结时还原被氧化的金属及保护金属不被氧化,广泛用于铜、铁、钨、钼等合金制品的烧结中;
3.惰性或中性气氛,包括氮、氩、氦及真空等;
4.渗碳气氛,即CO,CH4及其他碳氢化合物的气体,对于铁及低碳钢具有渗碳作用;5.渗氮气氛,即NH。
以及对于某些合金系而言的N2。
对于不同合金,上述分类可以有变化。
在烧结过程中,在不同阶段可能采用不同的气氛。
四.烧结防氧化
如果是气氛烧结,主要控制气氛的露点,露点太高表示气氛水分含量高,会产生氧化。
如果是真空烧结,主要控制真空度,确保炉子的密封性能
五.烧结制度
烧结制度包括升温、高温烧结、冷却等几个部分。
在烧结时,根据需要,可以采用快速升温,也可以采用慢速升温;可以直接升温到最高烧结温度,也可以分阶段逐步升温,如在需预烧或脱除成形剂和润滑剂时的情况,烧结温度和保温时间由金属特性和制品尺寸决定。
冷却也有慢冷、快冷和淬火等几种情况。
六.粉体的变化
在烧结过程中,粉末体发生以下一系列变化:表面吸附的水分或气体挥发或分解;应力松弛;发生回复和再结晶;原子在颗粒表面、晶界或晶内扩散,使颗粒间的结合由机械结合逐步转变为冶金结合,化学组分均匀化;在有液相存在时,发生颗粒重排,固相物质的溶解和析出,液相网络提供一物质输运的快速通道。
在这些过程的综合作用下,能获得满足一定物理、化学和几何特性要求的材料或零件。
七.烧结影响因素
烧结过程受许多因素影响,它们可分为3类
第1类与材料的温度特性有关,包括自由表面能、界面能和体积自由能,以及点阵、晶界、表面扩散系数等。
第2类为粉体特性,包括有效接触面积、表面活性、体积活性、接触面取向等。
第3类为外部因素,包括烧结气氛、烧结温度、烧结保温时间、升温及降温速度、颗粒表面层附层状态等。
八.烧结设备
常用的烧结设备有箱式炉、管式炉、马弗炉、碳管炉、感应炉、推舟炉、带式炉、辊式炉、反射炉等,分间断式、半连续、连续式等几类。
采用的加热方式有电阻加热,以镍铬合金、铁铬铝合金、钨、钼、碳化硅、硅化钼等作为发热元件。
还可以用碳管来通电发热,有时也利用坯块本身的电阻。
感应加热的应用也很普遍。
除电能外,天然气、燃油、煤亦可作为加热能源。
根据对温度、升降温速度、气氛、生产的连续与否等要求,选择烧结炉及加热方式。
九.烧结时间的确定
应该根据不同不同的材质来确定烧结的时间和温度,温度大概在它们熔点的80%左右。
十.举例
粉末冶金高速钢,简称粉冶高速钢,或PM 高速钢。
采用粉末冶金方法(雾化粉末在热态下进行等静压处理)制得致密的钢坯,再经锻、轧等热变形而得到的高速钢型材,简称粉末高速钢。
粉末高速钢组织均匀,晶粒细小,消除了熔铸高速钢难以避免的偏析,因而比相同成分的熔铸高速钢具有更高的韧性和耐磨性,同时还具有热处理变形小、锻轧性能和磨削性能良好等优点。
粉末高速钢中的碳化物含量大大超过熔铸高速钢的允许范围,使硬度提高到HRC67以上,从而使耐磨性能得到进一步提高。
如果采用烧结致密或粉末锻造等方法直接制成外形尺寸接近成品的刀具、模具或零件的坯件,更可取得省工、省料和降低生产成本的效果。
粉末高速钢的价格虽然高于相同成分的熔铸高速钢,但由于性能优越、使用寿命长,用来制造昂贵的多刃刀具如拉刀、齿轮滚刀、铣刀等,仍具有显著的经济效益。
优点
粉末冶金高速工具钢由于其制造工艺的独特性, 与铸锻高速钢比较, 具有一系列优异性能:1) 无偏析, 晶粒细小, 碳化物细小;2) 热加工性好;3) 可磨削性好;4) 热处理变形小;5) 力学性能(韧性, 硬度, 高温硬度)佳;6) 扩大了高速钢合金含量, 创造了新的超硬高速钢7) 扩大了使用领域
十一.粉末冶金材料和制品的今后发展方向:
1、有代表性的铁基合金,将向大体积的精密制品,高质量的结构零部件发展。
2、制造具有均匀显微组织结构的、加工困难而完全致密的高性能合金。
3、用增强致密化过程来制造一般含有混合相组成的特殊合金。
4、制造非均匀材料、非晶态、微晶或者亚稳合金。
5、加工独特的和非一般形态或成分的复合零部件。
参考资料
[1]中南矿冶学院:粉末冶金原理(第三分册),19772.
[2] 黄培云主编《粉末冶金原理》
[3] 韩凤麟《粉末冶金手册》冶金工业出版社
[4] 陈文革、王发展编著《粉末冶金工艺及材料》冶金工业出版社
[5](苏)C.A.楚克尔曼著《粉末冶金基本知识》
粉抹冶金。