压铸熔炼工艺及其影响因素.
铝合金压铸过程危险有害因素分析及对策措施

铝合金压铸过程危险有害因素分析及对策措施铝合金压铸工艺中,铝合金锭通常采用电阻式熔化保温炉熔化,熔化温度约650~800℃,熔化保温炉是一种最简单的熔炼设备,主要用于熔化熔点不太高的有色金属,如铜、铝及其合金等。
合金在坩埚内熔化,热量经坩埚传给炉料。
熔炼时将铝锭放置在坩埚中,坩埚置于炉内,电加热。
坩埚采用石墨材料制成。
炉料铝锭在投炉前放置在炉口预热。
采用的压铸机设有手动、半自动(仅运行一个循环)、自动三种,通过操作面板设置工作模式。
铝锭熔化后,通过五连杆给汤机利用机械连杆原理从熔化保温炉内取铝液按设定的轨迹送至压铸机压射室内进行压铸。
为便于铝压铸件和模具分离,在每次压铸完成后通过伺服连杆喷雾机利用机械连杆原理把喷雾装置伸进模腔内喷雾(脱模剂溶液),该溶液由硅油基脱模剂原液和水以1:100比例稀释得到,大部分因高温气化形成水汽。
压铸成形后的铸件经伺服取件机从模具夹取产品后按设定的轨迹将产品送至安全区域,冷却后经冲床进行加工,即得到的产品。
1 危险有害因素的辨识危险、有害因素辨识是对评价项目的自然条件、生产作业过程、设备和设施、物料和物体的贮运等可能存在的危险、有害因素,以及能量失控产生的危险、有害因素进行辨识分析。
危险因素分析的目的是对系统的潜在危险进行分析、辨识,确定其危险等级,并根据其危险等级提出防止这些危险发展成事故的对策措施。
通过危险、有害因素的辨识和对其性质、种类、条件、级别及可能产生的后果的分析、评价,提出相应的对策措施,以控制事故和职业危害的发生,或将危险和有害因素降低到可接受程度,从而保障作业人员的安全和健康。
1.1 物料的危险有害因素分析铝合金压铸使用的原辅料有铝锭、脱模剂,同时熔化、压铸过程中还涉及熔融铝液。
1.1.1物质分类针对铝合金压铸过程中各类物质的分类辨识如下:1)根据《危险化学品目录》(2015版)辨识,不涉及危险化学品,不涉及剧毒化学品。
2)根据《建筑设计防火规范》(GB50016-2014)(2018年版)辨识,铝锭、脱模剂及产品铝铸件属于戊类火灾危险介质。
影响热压铸成型工艺质量的因素探讨
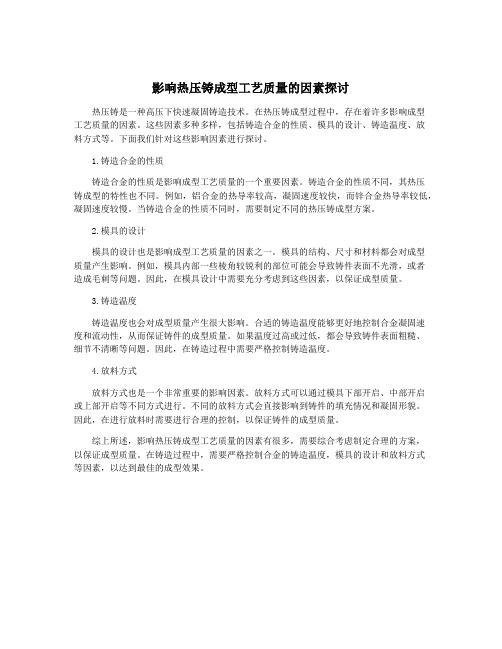
影响热压铸成型工艺质量的因素探讨热压铸是一种高压下快速凝固铸造技术。
在热压铸成型过程中,存在着许多影响成型工艺质量的因素。
这些因素多种多样,包括铸造合金的性质、模具的设计、铸造温度、放料方式等。
下面我们针对这些影响因素进行探讨。
1.铸造合金的性质铸造合金的性质是影响成型工艺质量的一个重要因素。
铸造合金的性质不同,其热压铸成型的特性也不同。
例如,铝合金的热导率较高,凝固速度较快,而锌合金热导率较低,凝固速度较慢。
当铸造合金的性质不同时,需要制定不同的热压铸成型方案。
2.模具的设计模具的设计也是影响成型工艺质量的因素之一。
模具的结构、尺寸和材料都会对成型质量产生影响。
例如,模具内部一些棱角较锐利的部位可能会导致铸件表面不光滑,或者造成毛刺等问题。
因此,在模具设计中需要充分考虑到这些因素,以保证成型质量。
3.铸造温度铸造温度也会对成型质量产生很大影响。
合适的铸造温度能够更好地控制合金凝固速度和流动性,从而保证铸件的成型质量。
如果温度过高或过低,都会导致铸件表面粗糙、细节不清晰等问题。
因此,在铸造过程中需要严格控制铸造温度。
4.放料方式放料方式也是一个非常重要的影响因素。
放料方式可以通过模具下部开启、中部开启或上部开启等不同方式进行。
不同的放料方式会直接影响到铸件的填充情况和凝固形貌。
因此,在进行放料时需要进行合理的控制,以保证铸件的成型质量。
综上所述,影响热压铸成型工艺质量的因素有很多,需要综合考虑制定合理的方案,以保证成型质量。
在铸造过程中,需要严格控制合金的铸造温度,模具的设计和放料方式等因素,以达到最佳的成型效果。
压铸工艺流程及常见问题分析

压铸工艺流程及常见问题分析引言:压铸工艺是一种通过将熔化的金属注入模具中,通过压力和冷却后获得所需形状的铸造方法。
它广泛应用于汽车制造、电子设备、航空航天等领域。
本文将介绍压铸工艺的基本流程,并分析常见问题及解决方法,以期对该领域的专业人员提供帮助和指导。
一、压铸工艺流程1. 模具制造模具是压铸工艺的关键步骤之一,它决定了最终产品的形状和质量。
在模具制造过程中,需要进行模具设计、材料选择、数控加工、热处理等环节。
同时,合理的模具结构设计和维护对于生产效率和产品质量也至关重要。
2. 材料准备压铸工艺常用的材料包括铝合金、锌合金等。
在材料准备阶段,需要根据产品要求选择合适的材料,并进行熔炼和调整成合适的液态金属。
材料质量的优劣直接关系到最终产品的强度和外观。
3. 注射将准备好的液态金属通过注射机注入模具中,通常是利用高压将金属压入模具中,以确保金属充分填充模具的空腔。
注射阶段需控制注射时间、速度和压力,以避免产品缺陷和模具磨损。
4. 冷却在注射完成后,需要将模具中的金属冷却固化,以使其达到设计要求的硬度和强度。
冷却时间和方式的控制对于产品质量至关重要。
5. 取出待冷却固化后,通过卸模机将铸件从模具中取出。
取出过程需要注意避免对铸件造成损伤或变形。
6. 修磨与加工取出的铸件通常需要进一步修磨、抛光和加工,以达到最终产品的要求。
这一阶段涉及到表面光洁度、尺寸精度和配合度等问题,要注意机械加工过程中的控制。
7. 检测与质量控制在每个工序结束后,都需要进行检测以确保产品质量符合标准要求。
常见的检测方法包括外观检查、尺寸测量、力学性能测试等。
质量控制是保证产品质量的关键环节,确保成品合格,减少次品率。
二、常见问题分析及解决方法1. 气孔缺陷气孔是压铸过程中常见的缺陷之一,主要是由于金属内部气体没有充分排出造成的。
解决方法包括提高注射压力、增加冷却时间、提高金属的纯度和液态性等。
2. 热裂纹热裂纹是由于金属在快速冷却过程中产生的应力超过材料抗拉强度引起的。
压铸铝锭熔炼技术中压铸铝锭工艺流程应注意

压铸铝锭熔炼技术中压铸铝锭工艺流程应注意压铸铝锭熔炼技术中压铸铝锭工艺流程应注意的重要事项000在生产过程中,对于不同的产品所要求的原铝化学成分不同,当进铝和配料过程完成后,对熔体进行充分的搅拌,使熔体内部化学成分均匀,再进行取样分析,如果中间取样分析结果表明熔体的化学成分不符合要求(如:Fe 含量较大,影响产品质量;Fe含量偏小,造成质量浪费),需按实际情况样进行相应的化学调整。
1.对重熔用铝锭配料,当保持炉内铝液中间分析不符合要求时,需进行配料调整。
如炉内铝液过多,Fe含量较大,经计算往炉内加入Fe含量小的铝液后容量超出保持炉容量时,须先放出第定数量的铝液,再往炉内加入Fe含量小的铝液进行调整,然后进行搅拌均匀,再进行中间取样分析,直至合格。
如果炉内Fe含量较小,为了不造成质量浪费,经计算可想炉内假如一定量的高铁大块铝。
2.对于连铸连轧生产所须的原铝,如Fe含量不符合要求时,其成分调整和重熔用铝锭成分调整一样。
当中间分析中Ti、V含量超出标准后,就需往炉内添加相应的BAI合金或其他添加剂,降低Ti、V含量,然后将铝液搅拌均匀。
3.对于合金生产所需原铝,经配料、搅拌均匀处理后,取中间分析,如分析表明哪种元素不符合要求,相应地对哪种元素进行调整,直至符合标准要求。
三、相关知识(一)熔体成分控制要求1,工业纯铝铸造在铸造工业纯铝锭时,工业纯铝锭没有形成冷裂纹的倾向,但当铁硅比例控制不当时,会产生各种形式的程度不同的热裂纹。
(1)重熔用铝锭铸造时,主要控制的是Fe、Si含量。
根据牌号规定,如果Fe、Si含量较高,可能会超标;Fe、Si含量较低,由会产生质量损失,造成浪费。
(2)在水平和垂直铸造生产中,当工业纯铝的品位较高,Si大于Fe 时,合金的热脆性比较大,产生热裂纹的倾向性也增大,故应当控制Fe大于Si,以降低铸锭的热裂纹倾向。
随着工业纯铝品位降低,要求Fe大于Si的亮变小。
当生产含Si量大于0。
影响热压铸成型工艺质量的因素探讨

影响热压铸成型工艺质量的因素探讨热压铸成型是一种常见的金属成型工艺,通过在高温和高压条件下将金属材料注入模具进行成型,可以获得高精度、高强度的零件和产品。
影响热压铸成型工艺质量的因素很多,包括材料选择、工艺参数、设备性能等,这些因素直接关系到成型产品的质量和性能。
本文将从这些方面进行探讨,分析影响热压铸成型工艺质量的主要因素。
一、材料选择1. 金属材料热压铸成型适用于铝合金、镁合金、铜合金等金属材料的成型。
不同的金属材料具有不同的熔点、流动性和收缩率等特性,因此在选择材料时需要根据产品要求和工艺条件进行合理选择。
2. 原料质量影响热压铸成型工艺质量的另一个重要因素是原料质量。
原料的含气量、杂质含量、粒度大小等都会直接影响到成型产品的性能和表面质量。
在生产过程中需要对原料进行严格的质量控制,确保原料符合工艺要求。
二、工艺参数1. 温度控制成型温度是影响热压铸成型工艺质量的重要参数之一。
温度过高会导致金属材料的流动性增加,但容易造成产品表面气孔和热裂纹;温度过低则会影响金属材料的充填性和流动性,导致成型产品的收缩不均匀。
对成型温度进行精确的控制非常重要。
2. 压力控制成型压力直接影响到成型产品的密度和性能。
过高或过低的成型压力都会对产品的质量造成影响,因此需要根据产品要求和材料特性合理确定成型压力。
3. 注射速度注射速度影响到金属材料的充填速度和流动性,过快或过慢的注射速度都会影响到产品的成型质量。
4. 保压时间保压时间是影响成型产品密度和组织性能的重要参数,保压时间过短会导致产品收缩不足和表面质量不好,保压时间过长则会增加成本。
三、设备性能1. 模具设计模具设计是影响热压铸成型工艺质量的关键因素之一。
模具的结构、表面处理、温度控制等都会直接影响到成型产品的精度和表面质量。
2. 设备精度除了模具设计外,设备的精度和稳定性也会直接影响到成型产品的质量。
设备性能不稳定会导致产品尺寸偏差、表面缺陷等问题。
压铸不良原因与措施

压铸不良原因与措施压铸是一种常见的金属加工方法,用于制造各种各样的金属零件。
然而,在压铸过程中常常会出现一些不良情况,导致产品质量下降或无法使用。
以下是一些常见的压铸不良原因及相应的措施。
1.缩孔(针眼)原因:高温熔融金属凝固时,金属液缩小所形成的孔洞。
措施:-控制材料的熔点和凝固温度,避免温度过高。
-提高注入压力和速度,确保金属充实完全。
-控制铸造工艺参数,如浇注温度、压力和速度,减少气体夹杂物。
2.气孔原因:熔融金属中混入空气或水分,冷凝成孔洞。
措施:-净化材料,确保金属液没有杂质。
-增加浇注温度,减少金属和气体冷凝。
-提高注入速度,使气体远离金属液。
3.热裂纹原因:金属在凝固过程中,由于残余应力、金属浓缩和组织缺陷等原因引起的开裂。
措施:-优化铸造工艺,减少或消除金属残余应力。
-控制金属的凝固速度,避免快速凝固造成应力集中。
-添加合适的合金元素,改善金属组织结构。
4.狭长缺陷原因:熔融金属填充模腔的过程中,金属液流动不均匀,形成局部过渡缩小的缺陷。
措施:-设计合理的铸造模具,确保金属液能够均匀填充模腔。
-调整铸造工艺参数,如入口和出口位置、浇注温度和速度,改善金属液流动状态。
-使用合适的流道和浇口设计,使金属流动更加均匀。
5.长气孔原因:金属液注入模腔的过程中,气体无法顺利排出,形成长而突出的孔。
措施:-增大出口尺寸,提高气体排出的通道。
-调整浇注顺序,避免气泡在金属液中积聚。
-使用适当的排气装置,确保顺畅排出气体。
6.表面不良原因:压铸件表面出现裂纹、气孔、疤痕等缺陷。
措施:-增加模具的冷却系统,提高金属液凝固速度。
-优化模具表面处理,减少摩擦和热传导。
-控制铸造工艺参数,如浇注温度和速度,减少金属液与模具的接触时间。
总之,压铸不良的原因和措施是多种多样的,需要根据不同情况采取相应的措施。
通过优化材料、设计模具、调整工艺参数等方法,可以有效地减少压铸不良,提高产品质量。
铝合金熔炼与铸造

铝合金熔炼与铸造铝合金是一种常见且广泛使用的金属材料,具有较低的密度、良好的导热性和耐腐蚀性,因此在许多行业中得到了广泛的应用。
铝合金的熔炼和铸造是制造铝合金制品的关键步骤。
本文将介绍铝合金熔炼和铸造的基本原理、工艺和注意事项。
一、铝合金熔炼1.1 熔炼原理铝合金熔炼的主要原理是将铝及其他合金元素加热至其熔点,使其融化成液态,以便进行后续的铸造工艺。
铝的熔点较低,约为660°C,因此相对较容易熔化。
而其他合金元素的加入可以改变铝合金的性质,例如提高其强度、耐腐蚀性或者改善加工性能。
1.2 熔炼工艺铝合金熔炼工艺一般分为两种:批量熔炼和连续熔炼。
批量熔炼是将一定量的铝和其他合金元素加入炉内,通过加热熔化成液态,并进行充分混合。
这种方法适用于小规模生产,常用的炉型有电阻炉和燃气炉。
而连续熔炼是将铝合金材料加入熔炉的顶部,通过炉内的加热和熔化过程,使得底部的液态铝合金不断流出。
这种方法适用于大规模生产,常用的炉型有回转炉和隧道炉。
1.3 熔炼注意事项在铝合金的熔炼过程中,需要注意以下几个方面。
首先,炉内的温度需要控制在适当的范围内,以避免过度燃烧或者过度冷却。
其次,需要保持良好的熔炼环境,防止氧气、水分或杂质等对炉内材料的影响。
最后,在加入其他合金元素时,需要根据配比和工艺要求进行准确的添加,以保证最终铝合金的性能。
二、铝合金铸造2.1 铸型设计铝合金铸造的第一步是进行铸型设计。
铸型设计的目的是根据最终产品的形状和要求,确定合适的铸造方法和材料,以及适当的铸型结构。
常见的铸型结构有砂型、金属型和陶瓷型等。
其中砂型是最常用的铸造方法,可以应用于各种形状和尺寸的产品。
2.2 铸造工艺铝合金的铸造工艺可以分为传统铸造和压铸两种。
传统铸造是将熔融的铝合金液体倒入铸型中,并通过自然冷却形成最终产品。
这种方法适用于小批量生产,但精度和表面光滑度相对较低。
压铸是将高压液压机将铝合金液体注入铸型中,通过压力传递和快速冷却,实现快速成型。
影响热压铸成型工艺质量的因素探讨
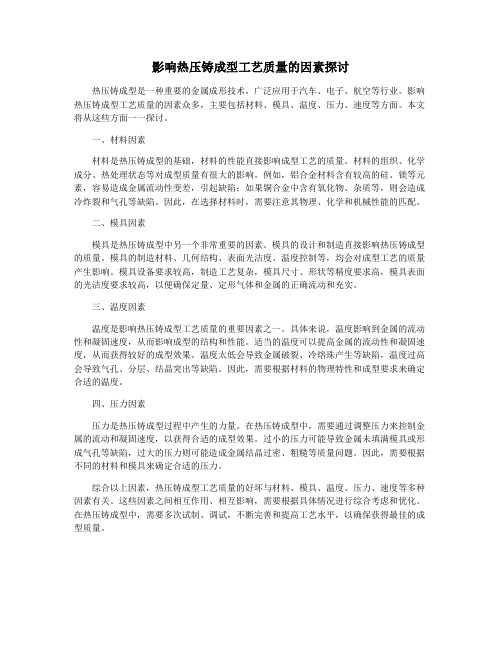
影响热压铸成型工艺质量的因素探讨热压铸成型是一种重要的金属成形技术,广泛应用于汽车、电子、航空等行业。
影响热压铸成型工艺质量的因素众多,主要包括材料、模具、温度、压力、速度等方面。
本文将从这些方面一一探讨。
一、材料因素材料是热压铸成型的基础,材料的性能直接影响成型工艺的质量。
材料的组织、化学成分、热处理状态等对成型质量有很大的影响。
例如,铝合金材料含有较高的硅、镁等元素,容易造成金属流动性变差,引起缺陷;如果铜合金中含有氧化物、杂质等,则会造成冷炸裂和气孔等缺陷。
因此,在选择材料时,需要注意其物理、化学和机械性能的匹配。
二、模具因素模具是热压铸成型中另一个非常重要的因素。
模具的设计和制造直接影响热压铸成型的质量。
模具的制造材料、几何结构、表面光洁度、温度控制等,均会对成型工艺的质量产生影响。
模具设备要求较高,制造工艺复杂,模具尺寸、形状等精度要求高,模具表面的光洁度要求较高,以便确保定量、定形气体和金属的正确流动和充实。
三、温度因素温度是影响热压铸成型工艺质量的重要因素之一。
具体来说,温度影响到金属的流动性和凝固速度,从而影响成型的结构和性能。
适当的温度可以提高金属的流动性和凝固速度,从而获得较好的成型效果。
温度太低会导致金属破裂、冷熔珠产生等缺陷,温度过高会导致气孔、分层、结晶突出等缺陷。
因此,需要根据材料的物理特性和成型要求来确定合适的温度。
四、压力因素压力是热压铸成型过程中产生的力量。
在热压铸成型中,需要通过调整压力来控制金属的流动和凝固速度,以获得合适的成型效果。
过小的压力可能导致金属未填满模具或形成气孔等缺陷,过大的压力则可能造成金属结晶过密、粗糙等质量问题。
因此,需要根据不同的材料和模具来确定合适的压力。
综合以上因素,热压铸成型工艺质量的好坏与材料、模具、温度、压力、速度等多种因素有关。
这些因素之间相互作用、相互影响,需要根据具体情况进行综合考虑和优化。
在热压铸成型中,需要多次试制、调试,不断完善和提高工艺水平,以确保获得最佳的成型质量。
- 1、下载文档前请自行甄别文档内容的完整性,平台不提供额外的编辑、内容补充、找答案等附加服务。
- 2、"仅部分预览"的文档,不可在线预览部分如存在完整性等问题,可反馈申请退款(可完整预览的文档不适用该条件!)。
- 3、如文档侵犯您的权益,请联系客服反馈,我们会尽快为您处理(人工客服工作时间:9:00-18:30)。
职业教育材料成型与控制技术专业教学资源库
铝合金熔剂喷粉精炼机
铝合金铸件铸造技术课程
职业教育材料成型与控制技术专业教学资源库
压铸熔炼工艺
(4)熔炼过程保持液面平衡。合理控制出料温度、时间、减少保温
时间。
(5)为得到更加纯的合金液,可对从熔炼炉出来的铝合金液,经过
陶瓷过滤网,把夹杂物滤掉,再送到压铸机的保温炉。 (6)铝液质量的现场检测可采用测氢仪和直读光谱仪。
铝合金铸件铸造技术课程 铝合金铸件铸造技术
职业教育材料成型与控制技术专业教学资源库
覆盖剂 造渣剂 净化剂 变质剂
熔炼熔剂种类
铝合金铸件铸造技术课程 铝合金铸件铸造技术
职业教育材料成型与控制技术专业教学资源库
覆盖剂
可在熔炼过 程构成一层液 态保护层使金
造渣剂
吸收氧化物
净化剂
利用上浮过 程把金属液中 的非金属杂质
职业教育材料成型与控制技术专业教学资源库
THANKS
(3)除了利用熔剂进行精炼、除气和除渣外,还可以采用铝合金熔
剂喷吹综合处理装置, 使精炼、变质、晶粒细化一步完成。也可采
用旋转转子法吹氮 ( 氩)、喷射熔剂法等高效精炼方法精炼铝液。
铝合金铸件铸造技术课程 铝合金铸件铸造技术
职业教育材料成型与控制技术专业教学资源库
铝合金熔剂喷吹精炼机
铝合金铸件铸造技术课程
压铸熔炼工艺
(1)合金锭成分符合标准、干燥, 防止合金料或熔化工具表面吸附
的湿气溶入铝液中转化为氢。新料与回炉料搭配时,回炉料不超过50
%。回炉料投入熔炼炉之前,必须清理干净和进行烘干处理。合理控
制投料量、投料时间、料块大小。 (2)熔炼温度:控制在670—760℃范围内。过高温度会发生氧化或 吸气, 过低温度不易分离炉渣。
职业教育材料成型与控制技术专业教学资源库
压铸熔炼工艺影响因素
铝合金铸件铸造技术课程
职业教育材料成型与控制技术专业教学资源库
小结:
这节课学习了压铸熔炼 工艺及其影响因素!
思考题:
1、压铸熔炼工艺过程有什么特点?需要注意哪些方面?
2、影响压铸熔炼工艺的因素有哪些?
铝合金铸件铸造技术课程 铝合金铸件铸造技术
变质剂
加入钠,改 善微观组织。
和非金属物质
聚集在金属液 面清除。
属不氧化、不
吸氢。
除掉。
铝合金铸件铸造技术课程 铝合金铸件铸造技术
职业教育材料成型与控制技术专业教学资源库
精炼作用 熔剂 作用 除气作用 除渣作用
铝合金铸件铸造技术课程 铝合金铸件铸造技术
职业教育材料成型与控制技术专业教学资源库
压铸熔炼工艺
铝合金铸件铸造技术课程 铝合金铸件铸造技术
职业教育材料成型与控制技术专业教学资源库
铝液测氢仪
铝合金铸件铸造技术课程
职业教育材料成型与控制技术专业教学资源库
直读光谱仪
铝合金铸件铸造技术课程
职业教育材料成型与控制技术专业教学资源库
压铸熔炼工艺
(7)合理选择坩埚及炉衬材料,防止坩埚中的Fe渗入铝液,以及铝
职业教育材料成型与控制技术专业教学资源库
压铸熔炼工艺及其影响因素
制作人:张保林 陕西工业职业技术学院
铝合金铸件铸造技术课程
职业教育材料成型与控制技术专业教学资源库
压铸熔炼工艺过程有 什么特点?需要注意哪些
方面?
铝业教育材料成型与控制技术专业教学资源库
压铸熔炼过程特点
合金的化学成分、杂质含量、含气量等都会影响合金的力学性
能、铸件的缩松及铝液的表面张力。杂质元素极大降低铝的表面
张力,而表面张力影响充型过程气体扩散,从而影响产生气孔的
分布。同时,还会产生氧化、吸氢、杂质、结渣和增铁等现象。
铝合金铸件铸造技术课程 铝合金铸件铸造技术
职业教育材料成型与控制技术专业教学资源库
液与耐火炉衬之间发生反应而结渣。按时清理炉壁、炉底的残渣。保
温炉采用高导热性的超高强不粘铝耐火材料作炉衬材料,在内衬与炉
外壁之间则用超级保温隔热材料一体成型,从而使炉内上下部分的金 属液温差小。
铝合金铸件铸造技术课程 铝合金铸件铸造技术
职业教育材料成型与控制技术专业教学资源库
压铸熔炼工艺影响因素
铝合金铸件铸造技术课程