六个标准差6σ概念与DMAIC手法运用介绍
(六西格玛管理)六西格玛管理简介

六西格玛(6σ)管理简介一、 什么是六西格玛(6σ)管理?6加上希腊字母σ(西格玛)。
σ本来是一个反映数据特征的希腊字母,表示数据的标准差。
我们常用下面的计算公式计算σ的大小:1)(12--=∑=n x x n i i σ ,式中x i 为样本观测值,x 为样本平均值, n 为样本容量。
现在,σ不仅仅是单纯的标准差的含义,而被赋予了更新的内容——即成为一种过程质量的衡量标准。
对于任何企业来说,过程变异都是他们最大的敌人,因为过多的过程变异会导致产品和服务无法满足客户的要求,为企业带来损失。
6σ管理可以为企业提供战略方法和相应的工具通过严谨的、系统化以及以数据为依据的解决方案和方法,消除包括从生产到销售、从产品到服务所有过程中的缺陷,从而改善企业的利润。
那么究竟什么是6σ呢?我们可以从以下几个方面来说明6σ的含义。
第一,它是一种衡量的标准。
从统计意义上讲,一个过程具有六西格玛(西格玛)能力意味着过程平均值与其规定的规格上下限之间的距离为6倍标准差,此时过程波动减小,每100万次操作仅有3.4次落在规格上下限以外。
即六西格玛水平意味着差错率仅为百万分之三点四(即3.4ppm )。
因此,它首先是一种度量的标准,可以通过样本的散布情况来衡量系统的稳定性。
6σ的数量越多,产品合格率越高,产品间的一致性越好,或产品的适应环境的能力越强,产品(服务)的质量就越好。
第二,6σ是一个标杆。
管理学上有一种设定目标的方法就是“标杆法”,将你的目标设定在你所要超越的对象上,将领先者的水平作为超越的“标杆”。
6σ也是一个标杆,它的目标就是“零缺陷”(差错率百万分子3.4)。
进行6σ管理就是要以这个目标作为追赶和超越的对象。
第三,6σ是一种方法:“一种基于事实和数据的分析改进方法,其目的是提高企业的收益。
”这个方法的最大特点就是一切基于事实,一切用数据说话。
不论是说明差错的程度,还是分析原因,以及检验改进措施的成效,都要用事实和数据说话,而不是基于主观上的想像。
六西格玛six-sigma

简介六西格玛(Six Sigma),又称:六式码、六标准差、6σ、6Sigma,不能使用大写的Σ,西格玛(Σ,σ)是希腊文的字母,在统计学中称为标准差,用来表示数据的分散程度。
其含义引申后是指:一般企业的瑕疵率大约是3到4个西格玛,以4西格玛而言,相当于每一百万个机会里,有6210次误差。
如果企业不断追求品质改进,达到6西格玛的程度,绩效就几近于完美地达成顾客要求,在一百万个机会里,只找得出3.4个瑕疵。
六西格玛(6σ)概念作为品质管理概念,最早是由摩托罗拉公司的麦克.哈里于1987年提出,其目的是设计一个目标:在生产过程中降低产品及流程的缺陷次数,防止产品变异,提升品质。
真正流行并发展起来,是在通用电气公司的实践,在杰克韦尔奇于20世纪90年代发展起来的6σ(西格玛)管理是在总结了全面质量管理的成功经验,提炼了其中流程管理技巧的精华和最行之有效的方法,成为一种提高企业业绩与竞争力的管理模式。
该管理法在摩托罗拉、通用电气、戴尔、惠普、西门子、索尼、东芝、华硕等众多跨国企业的实践证明是卓有成效的。
为此,国内一些部门和机构在国内企业大力推6σ管理工作,引导企业开展6σ管理。
随着实践的经验积累,它已经从单纯的一个流程优化概念,衍生成为一种管理哲学思想。
它不仅仅是一个衡量业务流程能力的标准,不仅仅是一套业务流程不断优化的方法,进而成为一种应对动态的竞争环境,提升企业竞争力,取得长期成功的企业战略。
辨别优先次序,实施流程改进对需要改进的流程进行区分,找到高潜力的改进机会,优先对其实施改进。
如果不确定优先次序,企业多方面出手,就可能分散精力,影响6σ管理的实施效果。
业务流程改进遵循五步循环改进法,即DMAIC模式:1.定义(Define)。
定义阶段主要是明确问题、目标和流程,需要回答以下问题:应该重点关注哪些问题或机会?应该达到什么结果?何时达到这一结果?正在调查的是什么流程?它主要服务和影响哪些顾客?2.评估(Measure)。
六西格玛管理dmaic方法操作实务

六西格玛管理dmaic方法操作实务六西格玛是一种管理方法论,旨在通过减少缺陷和变异性,提高组织的质量和绩效。
DMAIC是六西格玛的一种常用方法,用于解决问题和改进流程。
DMAIC是一个缩写,分别代表了Define(问题定义)、Measure(测量)、Analyze(分析)、Improve(改进)和Control (控制)这五个阶段。
首先是问题定义(Define)。
在这个阶段,团队需要明确问题的范围和目标,确立改进的方向。
这个阶段的关键是确定关注的流程或问题,并设立改进的目标,以此来引导后续的工作。
问题定义应尽量精确,避免过于笼统或过于狭窄。
接下来是测量(Measure)。
在这个阶段,团队需要确定如何测量流程或问题的关键指标,并收集相关数据。
通过数据的收集和分析,可以更好地了解问题的本质和原因。
同时,测量的结果也能为后续的分析和改进提供依据。
然后是分析(Analyze)。
在这个阶段,团队需要分析测量数据,找出问题的根本原因。
通过使用六西格玛工具和技术,如因果图、统计分析等,可以帮助团队进行深入的分析。
分析的目的是找出主要的问题根源,从而为下一步的改进提供指导。
接着是改进(Improve)。
在这个阶段,团队需要制定并实施改进计划,解决问题根本原因,并优化流程。
关键是确定改进的措施和方法,并进行试验和验证。
改进过程需要考虑到各种因素的影响,以确保改进的效果能够持续。
最后是控制(Control)。
在这个阶段,团队需要建立控制机制,以确保改进效果的持续性和可靠性。
控制包括制定标准化的工作流程、培训相关人员、设立绩效指标等。
控制的目的是确保改进的效果不会被逐渐丢失,同时也为后续的持续改进提供基础。
通过上述的DMAIC方法,可以帮助组织解决问题,改进流程,并提高组织的绩效和质量。
每个阶段都有明确的任务和目标,方便团队按部就班地进行工作。
同时,DMAIC方法也强调数据驱动决策和持续改进的理念,确保改进过程的科学性和可行性。
六西格玛分析流程(DMAIC)
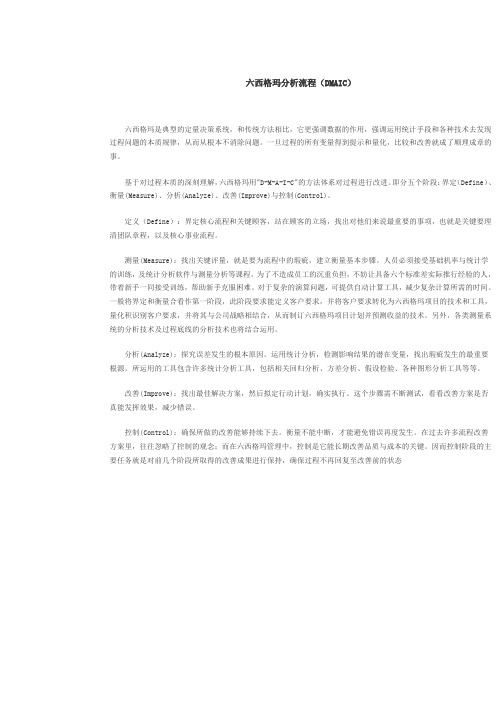
六西格玛分析流程(DMAIC)六西格玛是典型的定量决策系统,和传统方法相比,它更强调数据的作用,强调运用统计手段和各种技术去发现过程问题的本质规律,从而从根本不消除问题。
一旦过程的所有变量得到提示和量化,比较和改善就成了顺理成章的事。
基于对过程本质的深刻理解,六西格玛用"D-M-A-I-C"的方法体系对过程进行改进。
即分五个阶段:界定(Define)、衡量(Measure)、分析(Analyze)、改善(Improve)与控制(Control)。
定义(Define):界定核心流程和关键顾客,站在顾客的立场,找出对他们来说最重要的事项,也就是关键要理清团队章程,以及核心事业流程。
测量(Measure):找出关键评量,就是要为流程中的瑕疵,建立衡量基本步骤。
人员必须接受基础机率与统计学的训练,及统计分析软件与测量分析等课程。
为了不造成员工的沉重负担,不妨让具备六个标准差实际推行经验的人,带着新手一同接受训练,帮助新手克服困难。
对于复杂的演算问题,可提供自动计算工具,减少复杂计算所需的时间。
一般将界定和衡量合看作第一阶段,此阶段要求能定义客户要求,并将客户要求转化为六西格玛项目的技术和工具,量化积识别客户要求,并将其与公司战略相结合,从而制订六西格玛项目计划并预测收益的技术。
另外,各类测量系统的分析技术及过程底线的分析技术也将结合运用。
分析(Analyze):探究误差发生的根本原因。
运用统计分析,检测影响结果的潜在变量,找出瑕疵发生的最重要根源。
所运用的工具包含许多统计分析工具,包括相关回归分析、方差分析、假设检验、各种图形分析工具等等。
改善(Improve):找出最佳解决方案,然后拟定行动计划,确实执行。
这个步骤需不断测试,看看改善方案是否真能发挥效果,减少错误。
控制(Control):确保所做的改善能够持续下去。
衡量不能中断,才能避免错误再度发生。
在过去许多流程改善方案里,往往忽略了控制的观念;而在六西格玛管理中,控制是它能长期改善品质与成本的关键。
六西格玛讲解

在通用电气公司应用六西格玛取得了巨大成功后,很多 企业开始大力推行六西格玛管理,如IBM-UK公司、福特、杜 邦、东芝、惠而浦、三星、LG、西门子、爱立信,除了以上 这些制造型企业,六西格玛在服务型行业也取得了良好的推 广效果,如英特尔、微软、泛美保险公司、亚马迅网站、 Bankers Life Insurance公司、Capital One Services公司、 花旗银行、美国运通等等。现在, 20%以上的财富500强已 经实施或正在实施六西格玛管理法。以下为部分受益于六西 格玛的企业:
2、六西格玛的推广
六西格玛方法的创造者是摩托罗拉公司,但真正将这一方法变成管 理哲学和实践的是杰克〃韦尔奇领导下的通用电气公司。 在杰克〃韦尔奇的带领下,通用电气公司于1995年开始了它的六西格 玛计划,在1996年初开始把六西格玛作为一种管理战略列在其三大公 司战略举措之首(另外两个是全球化和服务业),全面推行六西格玛变 革方法。通用电气首创了倡导者(champion)、黑带大师(master black belt)、黑带(black belt)、绿带(green belt)的组织形式, 使六西格玛逐渐演变为一个管理系统。总裁杰克〃韦尔奇把六西格玛描 述为“公司实施最富挑战性且回报最高的战略”。他在公司1999年2月 致股东的信中说道:“通用电器的六西格玛质量2000将成为对我个人 而言最大的汇报以及有史以来收益最大的项目……从3年前我们开始对 六西格玛项目进行大量投资到目前为止,已经投入了超过10亿美元的 资金,而得到的回报是财务状况成指数增长。”
4、六西格玛的相关术语
因素(Factors):在实验设计中在不同水平变化的变量。 失效(Failure):当一个设备不能完成所希望的功能时即位失效。 失效模式与影响分析(FMEA,Failure Mode and Effects Analysis):用来分析产品或服务及其过程由于失效导致风险的方法。 方差分析(ANOVA,Analysis of variance):将因素对质量特性 的影响与误差对质量特性的影响加以区分并做出估计,然后进行比 较,分析、推断哪些因素或哪些因素间的交互作用对质量特性有显 著影响。 回归分析(Regression Analysis):利用实验所得到的数据,通过 数学模型的方法来量化响应变量和影响变量之间的关系。 实验设计(DOE,Design of Experiments):析因实验和相应的改 进方法。 回归分析(Regression Analysis):变量间关系的分析方法。
6-sigma的概念与导入
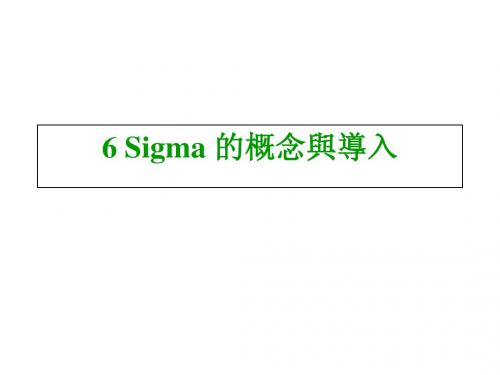
分析
分析/澄清 潜在原因
改善目标 确认潜在原 因 统计验证
改善
确认根因 及最佳化
确认关键性 少数 最佳化 设立作业窗 口
控制
管制 计划
确认管制能 力 管制计划 以管制系统 锁定
VOC VOB QFD COPO
流程地图 柏拉图 GR&R(Y) 能力
假设检定 回归 ANOVA DOE
脑力激荡 DOE 顺序矩阵 FMEA
-- 回应值(response)—结果(performance measure) -- 可控因子(Factors,controllable)—输入(input) -- 不可控因子(Factors,uncontrollable)—流程(process) -- 等级(level)—特别设立之可控因子 -- 推移(run)--特别设立之可控因子的实验次数 -- 主要作用 (Main effect ) -- 一个因子会受到另一个因子影响 (Interaction ) -- 重复( Repeat)
现状绩效等级 清楚 量化 简单
提升后绩效等级
常态分配的运用
Q:某公司员工A的身高为X=170 σ =10,则超过 : 180cm的员工占百分之几?
180 170 z= =1 10
查常态分配表可得 当Z=1时,计算或然率为0.84 因此超过180cm的机率为0.16 即16%
-2σ -1σ σ σ
一个自变数对应一个因变数
复回归 (multiple linear regression)
两个以上之自变数对应两个以上之因变数
非线性回归 (non-linear regression)
两者之间为非线性对应
预测未来(如销售,不良率等) 0 ≤R2 ≤100%, R2值愈大,表示关系愈强
6西格玛(6σ)管理方法

6西格玛(6σ)管理西格玛(σ)在统计学上是指标准差,用来表示数据的分散程度。
6西格玛(6σ)即6倍标准差。
在质量上表示每百万个产品的不良品率(ppm)少于3.4,但是6西格玛(6σ)管理不仅仅是指产品质量,而是一整套系统的企业管理理论和实践方法。
6西格玛(6σ)管理核心理念实际上不仅是一个质量上的标准,它更代表着一种全新的管理理念。
尽管过去确实做得很好,但事实离6西格玛(6σ)管理的目标还差的很远。
美国摩托罗拉公司6σ控制方式简介(详见《中国质量》2000.5P13~P16)1.工业控制方式的进展20世纪70年代,美国工业的控制方式相当于2σ控制方式,Cp=0.67。
20世纪80年代,美国工业的控制方式前进了,相当于3σ控制方式,Cp=1.0。
而日本在20世纪80年代早期则以达到4σ控制方式,Cp=1.33。
到20世纪80年代中期,日本进一步发展到5σ控制方式,Cp=1.67。
这对美国无疑是一种极大的挑战,故在20世纪80年代末90年代初美国摩托罗拉公司提出著名的6σ控制方式。
美国摩托罗拉公司的设计标准摩托罗拉公司提出的设计标准是对所有的零部件及过程,要求是:Cp≥2 ,Cpk≥1.5 。
而过程能力指数计算公式是:Cp=T/6σ=(Tu-Tl)/6σ ;Cpk=(1-K)Cp ;ε=6σ(1-Cpk/ Cp)。
其中K=2ε/T ;Tu、Tl 分别为上下规格界限;σ为标准差;T为技术规格的公差幅度;ε为实际分布中心(μ)与公差中心(M)的偏移即ε=│M-μ│,K即为偏移度。
将Cp=2.0和Cpk=1.5代入ε=6σ(1-Cpk/ Cp)计算得ε=1.5σ,即在Cp=2.0 ,T/2=6σ的情况下分布中心往一侧偏移了1.5σ,于是该侧的不合格品率为P(4.5σ),另一侧的不合格品率为P(7.5σ)。
查日本《统计数值表》,JSA-1972中的正态分布表知P(4.5σ)= 0.0000033977 ≈ 0.0000034 = 3.4PPM 、P(7.5σ)= 0.01331909 。
6西格玛(6σ)管理方法

4.5. DMAIC流程:DMAIC流程是6西格玛(6σ)管理中用于过程革新的方法。每一个字母代表了一个工作阶段,它们分别是:
a.D定义(Define)质量的标准源于用户,所以首先应确定用户认,为的质量关键点,并将用户的要求转化为可测量的指标。要更多的关注用户潜在的需求和期望。
4.1. 6西格玛(6σ)管理:西格玛(σ)在统计学上是指标准差,用来表示数据的分散程度。6西格玛(6σ)即6倍标准差。在质量上表示每百万个产品的不良品率(ppm)少于3.4,但是6西格玛(6σ)管理不仅仅是指产品质量,而是一整套系统的企业管理理论和实践方法。
4.2. 6西格玛(6σ)管理核心理念实际上不仅是一个质量上的标准,它更代表着一种全新的管理理念。尽管过去确实做得很好,但事实离6西格玛(6σ)管理的目标还差的很远。
4.4.6西格玛(6σ)管理的实施方法:摩托罗拉公司提出并取得成功的七步骤法(Seven—roblem and describe it clearly)。把要改善的问题找出来,当目标锁定后便召集有关人员,成为改善的主力,并选出首领,作为改善的责任人,跟着便制定时间表跟进。
一、目的:
制定教育训练相关资料,并整理成册作为部门技术资料,作为品保部在职员工及新进员工教育训练之依据,及其它相关单位职员工教育训练时作参考。
二、范围:
适用于公司品保部及各相关部门。
三、权责:
3.1品保部:负责相关资料的收集、整理及修正、资料的维护。
3.2各相关单位:资料的使用及维护。
四、内容:6西格玛(6σ)管理方法
c.黑带(Black Beit):为全职6西格玛人员,具体执行和推广6西格玛,同时负责培训绿带。一般情况下,一名黑带一年要培训100名绿带。
- 1、下载文档前请自行甄别文档内容的完整性,平台不提供额外的编辑、内容补充、找答案等附加服务。
- 2、"仅部分预览"的文档,不可在线预览部分如存在完整性等问题,可反馈申请退款(可完整预览的文档不适用该条件!)。
- 3、如文档侵犯您的权益,请联系客服反馈,我们会尽快为您处理(人工客服工作时间:9:00-18:30)。
平均數(Mean)
某顧問公司的員工薪資如下: 30,30,30,84,30,30,40,30,40,45,70,38,95 求員工的平均薪資為多少? Ans:45.538
6 σ可以是多樣的
已統計上來說 達到6 σ反映 出一個作業流程每一百萬次 中只有3.4次的機率會出錯 從允許不良到近乎完美
6 σ的焦點
因變數 Y 相依 產出 結果 徵兆 監視
自變數 X1….Xn 獨立 輸入過程 原因 問題 控制
6 σ焦點釋意
目標是以數學的方式敘述流程 6 σ的方法是教我們將焦點放在獨立與 相依的兩個變數上 與過去將焦點放在 Y (產出)的觀念不同 應加強在 X 的了解上
計量值
計量值(Variable): 必須用量而得到的數據 零件尺寸 電器產品的電流,電壓,電阻 又稱為連續型隨機變數
製程能力指數(CP)
製程能力指數(Process Capability Index) 製程精密度 表示製程特性的一致性程度 值越大,表示越集中 值越小,表示越分散
DMAIC 突破性策略
定義 量測
特性化
突破性 策略 最佳化
追求真原因
分析
改善
追求效果
控制
定義-由一個創意觀念開始
目標顧客是誰? 顧客心目中的品質關鍵環節是什麼? 誰是顧客的代言人? 專業經營策略是什麼? 誰握有專業經營的利害關係? 誰可以幫忙定義議題? 所包含的關鍵流程有哪些?
全距(Range)
資料群中最大的數減去最小的數所得的差
分析:比較集中的情況比較好.
變異數(Variance)
測量差異,離散情況重要量數 測量資料群中每一個數值與平均數間的差 例如:一組樣本資料為48,47,42,50,61,52 平均數=(48+47+42+50+61+52)=50 樣本變異數=[(48-50)2+ (47-50)2+ (42-50)2+ (50-50)2+ (61-50)2+ (52-50)2]/(6-1)=40.4 樣本標準差=變異數開根號
D-M-A-I-C
Define-Measure-Analyze-Improve-Control
對於每一個產品或流程的品質關鍵環節 -- 定義.測量.分析.改善.控制 定義:顧客期望的流程是什麼? 測量:缺點發生的頻率如何? 分析:缺點Why,When,Where? 改善:如何去改善流程? 控制:如何讓改善的流程能持續?
Ca值等級
A級 l Ca l 12.5% B級 12.5%< l Ca l 25% C級 25% < l Ca l 50% D級 50% < l Ca l
統計的基本概念
綜合製程能力指數-Cpk 同時考慮偏移及一致性程度 Cpk = (1-k) x Cp Cpk = min(CPU,CPL)
C.定義流程地圖
定義流程 結合顧客與流程 繪出事業流程的地圖 驗證流程地圖 得到主要經營關係人的背書
團隊任命的五個要素
以事業經營為案例 解釋為何要進行這個專案 問題綜整與目標計畫 以清楚簡明扼要可量化的方式來描述問題 專案範圍 流程的維度/大小可利用的資源 里程碑/時程 達到目標的主要步驟及日期 角色 人員 期望 責任
Cp值等級
A級 2.00Cp B級 1.33Cp<2.00 C級 1.00Cp<1.33 D級 Cp<1.00
製程能力指數(Ca)
製程能力指數(Process Capability Index) 製程準確度(Accuracy) 表示製程中心位置的偏移程度 值越大,表示偏移越大 值越小,表示偏移越小 值等於零,表示不偏移
規格界線
顧客採購某產品或其相關流程時,所能容 忍的公差或績效範圍. 1 σ: 68.27 2 σ: 95.45 3 σ: 99.73 (目前一般業界要求) 4 σ: 99.994
計數值
計數值(Attribute): 可用數而得到的數據 不連續的特質 每公尺棉布有幾個瑕疵點 無塵室中每立方公尺含微粒之個數 又稱為離散型隨機變數
6 σ與以往不同之處
傳統的品質計劃 內部導向 專注在結果 改善缺點 著眼在工廠 改善品質 向後看 全神灌注產在產品上 重視理論及員工 6 σ 顧客導向 專注在流程上 防止缺點發生 著眼在整個企業 改善整個營運效益 向前看 重視方法及數據
6 σ的思維模式
如果不能量測改善對顧客或自己企業的 成長,成本或利潤所帶來的效益. 任何所進行的活動都是流程. 所有改善作業流程所需要的資訊都存在 於數據之中. 6 σ提供了統計工具分析資料來引導整 個作業流程的改善,從而帶來營運的效益.
六個標準差(6σ)概念與 DMAIC手法運用介紹
課程大綱
6個標準差的概念介紹 基本統計概念 6σ的涵義 6σ的運用範圍 6σ的效益 6個標準差的DMAIC手法運用與實例
課程預期效益
透過本課程的介紹,期望能將正確的6個 標準差的觀念與運用手法介紹給企業界, 達到以後用6σ手法來提昇顧客滿意度, 減少製程週期時間,增加生產力,改善產 能與產出,降低不良率,提昇產品可靠度 及改善流程等效益的目的.
定義階段
A.確認專案 B.發展團隊成員 C.定義流程地圖
A.確認專案
確認目標顧客 編輯並分析現有顧客資料 分析顧客的聲音 將顧客的需求轉換為要求 整合要求到專業經營策略中 確認專案的要求
B.發展團隊成員
以事業經營為案例 發展先期問題的計劃 評估專業的範圍 發展目標計劃 選擇團隊成員並明定職責 授權委任
6 σ目標
6 σ要求的是 Cp=2.0 Ca=0.25 3.4 PPM(Parts Par Million)百萬分之多少 一個以顧客為中心 數據為導向的 領導策略
為什麼要推行6 σ
顧客的需求不斷增加 競爭者提供越來越多的服務 員工不願停滯不前 全球市場的要求越來越高 速度與高品質