6西格玛标准公差计算公式
6西格玛计算公式详细讲解
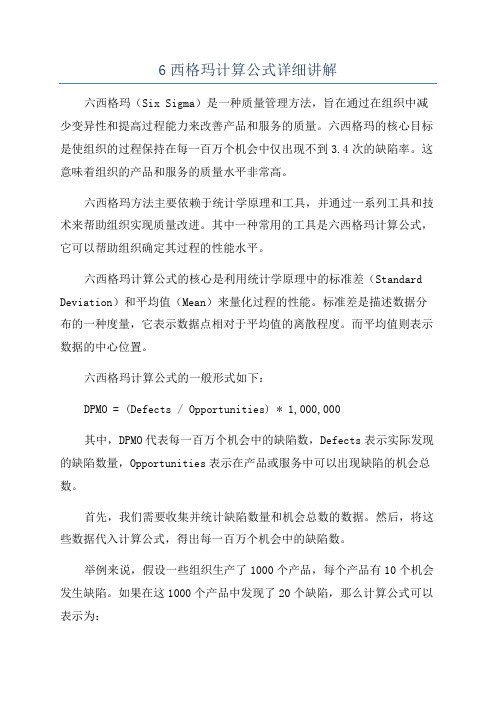
6西格玛计算公式详细讲解六西格玛(Six Sigma)是一种质量管理方法,旨在通过在组织中减少变异性和提高过程能力来改善产品和服务的质量。
六西格玛的核心目标是使组织的过程保持在每一百万个机会中仅出现不到3.4次的缺陷率。
这意味着组织的产品和服务的质量水平非常高。
六西格玛方法主要依赖于统计学原理和工具,并通过一系列工具和技术来帮助组织实现质量改进。
其中一种常用的工具是六西格玛计算公式,它可以帮助组织确定其过程的性能水平。
六西格玛计算公式的核心是利用统计学原理中的标准差(Standard Deviation)和平均值(Mean)来量化过程的性能。
标准差是描述数据分布的一种度量,它表示数据点相对于平均值的离散程度。
而平均值则表示数据的中心位置。
六西格玛计算公式的一般形式如下:DPMO = (Defects / Opportunities) * 1,000,000其中,DPMO代表每一百万个机会中的缺陷数,Defects表示实际发现的缺陷数量,Opportunities表示在产品或服务中可以出现缺陷的机会总数。
首先,我们需要收集并统计缺陷数量和机会总数的数据。
然后,将这些数据代入计算公式,得出每一百万个机会中的缺陷数。
举例来说,假设一些组织生产了1000个产品,每个产品有10个机会发生缺陷。
如果在这1000个产品中发现了20个缺陷,那么计算公式可以表示为:DPMO=(20/(1000*10))*1,000,000=2000这意味着每一百万个机会中会发生2000个缺陷。
根据六西格玛的目标,这个组织的质量水平是不合格的,因为它的缺陷率超过了3.4通过六西格玛计算公式,组织可以定量地了解到底有多少缺陷出现在产品和服务中,从而进一步分析和改进其质量管理过程。
如果发现缺陷率较高,组织可以采取一系列措施来降低缺陷率,例如改进生产过程、提高员工培训水平等。
在实际应用中,六西格玛计算公式可以结合其他统计工具一起使用,例如直方图、散点图等,以更全面地了解和评估组织的质量水平。
6 西格玛标准公差计算公式.

六西格玛管理系列讲座之一什么是6西格玛管理?当人们谈论世界著名公司-通用电器(GE)的成功以及世界第一CEO-杰克.韦尔奇先生为其成功制定的三大发展战略时,都会不约而同地提出这样的问题。
如果概括地回答的话,可以说6西格玛管理是在提高顾客满意程度的同时降低经营成本和周期的过程革新方法,它是通过提高组织核心过程的运行质量,进而提升企业赢利能力的管理方式,也是在新经济环境下企业获得竞争力和持续发展能力的经营策略。
因此,管理专家Ronald Snee先生将6西格玛管理定义为:“寻求同时增加顾客满意和企业经济增长的经营战略途径。
”如果展开来回答的话,6西格玛代表了新的管理度量和质量标准,提供了竞争力的水平对比平台,是一种组织业绩突破性改进的方法,是组织成长与人才培养的策略,更是新的管理理念和追求卓越的价值观。
让我们先从6西格玛所代表的业绩度量谈起:符号σ(西格玛)是希腊字母,在统计学中称为标准差,用它来表示数据的分散程度。
我们常用下面的计算公式表示σ的大小:如果有两组数据,它们分别是1、2、3、4、5;和3、3、3、3、3;虽然它们的平均值都是3,但是它们的分散程度是不一样的(如图1-1所示)。
如果我们用σ来描述这两组数据的分散程度的话,第一组数据的σ为1.58,而第二组数据的σ为0。
假如,我们把数据上的这些差异与企业的经营业绩联系起来的话,这个差异就有了特殊的意义。
假如顾客要求的产品性能指标是3±2(mm),如果第一组数据是供应商A所提供的产品性能的测量值,第二组数据是供应商B所提供的产品性能的测量值。
显然,在同样的价格和交付期下,顾客愿意购买B的产品。
因为,B的产品每一件都与顾客要求的目标值或理想状态最接近。
它们与顾客要求的目标值之间的偏差最小。
假如顾客要求的产品交付时间是3天。
如果第一组数据和第二组数据分别是供应商A和B每批产品交付时间的统计值,显然,顾客愿意购买B的产品。
因为,B每批产品的交付时间与顾客要求最接近。
6西格玛标准公差计算公式

六西格玛管理系列讲座之一什么是6西格玛管理?当人们谈论世界著名公司-通用电器(GE)的成功以及世界第一CE O-杰克.韦尔奇先生为其成功制定的三大发展战略时,都会不约而同地提出这样的问题。
如果概括地回答的话,可以说6西格玛管理是在提高顾客满意程度的同时降低经营成本和周期的过程革新方法,它是通过提高组织核心过程的运行质量,进而提升企业赢利能力的管理方式,也是在新经济环境下企业获得竞争力和持续发展能力的经营策略。
因此,管理专家Ro naldSnee先生将6西格玛管理定义为:“寻求同时增加顾客满意和企业经济增长的经营战略途径。
”如果展开来回答的话,6西格玛代表了新的管理度量和质量标准,提供了竞争力的水平对比平台,是一种组织业绩突破性改进的方法,是组织成长与人才培养的策略,更是新的管理理念和追求卓越的价值观。
让我们先从6西格玛所代表的业绩度量谈起:符号σ(西格玛)是希腊字母,在统计学中称为标准差,用它来表示数据的分散程度。
我们常用下面的计算公式表示s的大小:如果有两组数据,它们分别是1、2、3、4、5;和3、3、3、3、3;虽然它们的平均值都是3,但是它们的分散程度是不一样的(如图1-1所示)。
如果我们用σ来描述这⎬两组数据的分散程度的话,第一组数据的σ为1.58,而第二组数据的s为0。
假如,我们把数据上的这些差异与企业的经营业绩联系起来的话,这个差异就有了特殊的意义。
假如顾客要求的产品性能指标是3±2(mm),如果第一组数据是供应商A所提供的产品性能的测量值,第二组数据是供应商B所提供的产品性能的测量值。
显然,在同样的价格和交付期下,顾客愿意购买B的产品。
因为,B的产品每一件都与顾客要求的目标值或理想状态最接近。
6σ 计算公式
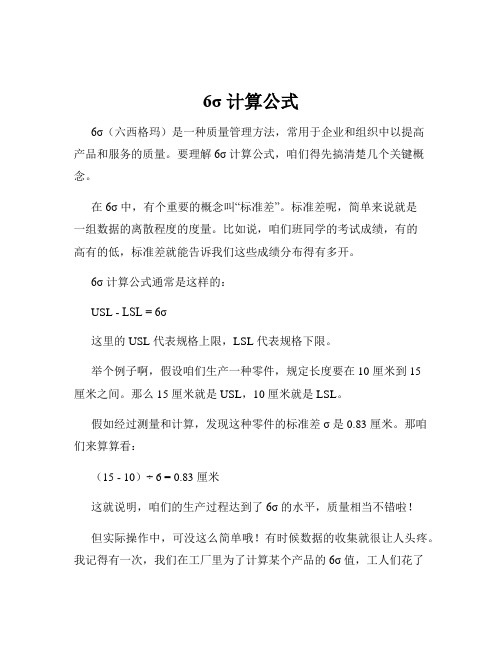
6σ 计算公式6σ(六西格玛)是一种质量管理方法,常用于企业和组织中以提高产品和服务的质量。
要理解6σ 计算公式,咱们得先搞清楚几个关键概念。
在6σ 中,有个重要的概念叫“标准差”。
标准差呢,简单来说就是一组数据的离散程度的度量。
比如说,咱们班同学的考试成绩,有的高有的低,标准差就能告诉我们这些成绩分布得有多开。
6σ 计算公式通常是这样的:USL - LSL = 6σ这里的 USL 代表规格上限,LSL 代表规格下限。
举个例子啊,假设咱们生产一种零件,规定长度要在 10 厘米到 15厘米之间。
那么 15 厘米就是 USL,10 厘米就是 LSL。
假如经过测量和计算,发现这种零件的标准差σ 是 0.83 厘米。
那咱们来算算看:(15 - 10)÷ 6 = 0.83 厘米这就说明,咱们的生产过程达到了6σ 的水平,质量相当不错啦!但实际操作中,可没这么简单哦!有时候数据的收集就很让人头疼。
我记得有一次,我们在工厂里为了计算某个产品的6σ 值,工人们花了好几天时间来测量和记录各种数据。
那真是累得够呛!有的数据还不准确,又得重新测量,可把大家折腾坏了。
而且,6σ 可不仅仅是个计算公式那么简单。
它代表着一种追求卓越质量的理念和文化。
要真正实现6σ 水平的质量管理,需要整个团队的努力,从设计、生产到检验,每个环节都不能马虎。
比如说,在设计阶段,就得充分考虑各种可能的因素,把产品的规格定得合理又精确。
生产过程中,要严格控制每一道工序,保证产品的质量稳定。
检验的时候,更是要一丝不苟,不放过任何一个次品。
总之,6σ 计算公式虽然看起来不复杂,但要把6σ 真正运用好,可不是一件容易的事儿。
这需要我们有耐心、细心,还得有团队合作的精神。
只有这样,才能不断提高产品和服务的质量,让客户满意,让企业发展得越来越好!。
6西格玛计算公式
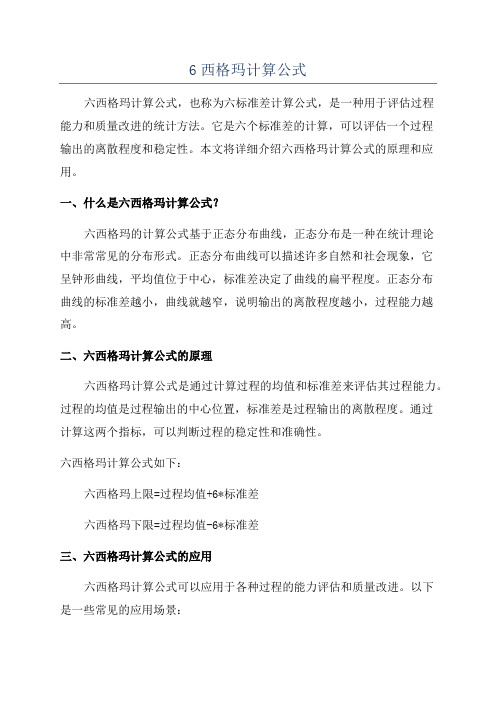
6西格玛计算公式六西格玛计算公式,也称为六标准差计算公式,是一种用于评估过程能力和质量改进的统计方法。
它是六个标准差的计算,可以评估一个过程输出的离散程度和稳定性。
本文将详细介绍六西格玛计算公式的原理和应用。
一、什么是六西格玛计算公式?六西格玛的计算公式基于正态分布曲线,正态分布是一种在统计理论中非常常见的分布形式。
正态分布曲线可以描述许多自然和社会现象,它呈钟形曲线,平均值位于中心,标准差决定了曲线的扁平程度。
正态分布曲线的标准差越小,曲线就越窄,说明输出的离散程度越小,过程能力越高。
二、六西格玛计算公式的原理六西格玛计算公式是通过计算过程的均值和标准差来评估其过程能力。
过程的均值是过程输出的中心位置,标准差是过程输出的离散程度。
通过计算这两个指标,可以判断过程的稳定性和准确性。
六西格玛计算公式如下:六西格玛上限=过程均值+6*标准差六西格玛下限=过程均值-6*标准差三、六西格玛计算公式的应用六西格玛计算公式可以应用于各种过程的能力评估和质量改进。
以下是一些常见的应用场景:1.生产过程能力评估:通过计算生产过程的均值和标准差,可以评估生产过程的稳定性和准确性。
如果生产过程的输出在规范范围之外,就可以采取措施来改进生产过程,以提高产品质量。
2.服务过程能力评估:六西格玛计算公式可以用于评估各种服务过程的能力,例如客户服务、物流配送等。
通过评估过程的稳定性和准确性,可以发现并改进服务过程中的问题,提高服务质量。
3.工程过程改进:六西格玛计算公式可以用于工程过程的能力评估和改进。
通过评估工程过程的能力,可以发现并改进工程过程中的问题,提高工程质量和效率。
4.采购过程能力评估:通过评估采购过程的能力,可以判断供应商的质量稳定性,从而选择合适的供应商。
采购过程能力评估还可以帮助采购部门改进采购过程,提高采购效率和准确性。
五、结论六西格玛计算公式是一种用于评估过程能力和质量改进的统计方法。
它通过计算过程的均值和标准差来评估过程的稳定性和准确性。
六西格玛

第一章概述一、6σ:新世纪的质量理念6个西格玛作为一个由Motorola公司最先开发和发展而来的伟大品质创举,是一种通过驱使所有人员热情地追求不断改善的最高质量要求的模式改变,其理念成熟于1985 到 1986年间。
摩托罗拉公司于80年代将其作为组织开展全面质量管理过程实现最佳绩效的一种质量理念和方法,它带来了公司文化的改变。
摩托罗拉公司也因此成为美国波多里奇国家质量奖的首位获得者。
几年过去了,直到今天,6个西格玛仍象当初一样在各行各业为我们所应用。
今天,随着竞争的加剧,我们6个西格玛目标的追求比以往更加强烈了。
在各行各业,6个西格玛仍然是一个主要的目标。
二、6σ与传统的过程改进6σ与传统的质量改进方法一个最明显的区别在于认知方面。
全面质量管理中所采用的过程改进方法在取得初期成功之后,便逐渐走向衰退,因为它们缺少 6σ所要求的来自高层管理者的承诺。
另外,在一个高技术的世界环境中,企业要取得竞争胜利,它们的首要目标是质量改进。
但质量只是组织进行自我度量的一个参数。
而 6σ则是一种全面经营过程改进的方法。
尽管它测评的是单位产品缺陷及每百万次运行所存在的缺陷,但它的目标是消除无附加值活动,缩短循环周期,增加利润。
当组织成功地实施了 6σ,它们就将对管理人员的培训及评估方法与 6σ过程结合在一起,确保了管理者对获取成功作出关键的承诺。
我们还记得60年代提出的“零缺陷”,这与6σ有什么不同呢?6σ强调在过程这每一步都对用户满意度进行测评,对每次测评结果,通过团队活动,不断缩短循环周期,减少DPMO。
通过实施6σ,所反映出的DPMO已非常小,既所谓“真正的完美”。
在这里强调确定过程中每一步的缺陷,用DPMO来表示缺陷,并制定改进目标,这一切都与传统的持续改进方法是不同的。
但是6σ是采取什么方法来实现改进的?当我们检验一下6σ方法及技术时,我们发现6σ所使用的方法与传统的过程改进工具有许多惊人的相似之处。
例如:6σ方法涉及到基本的问题解决技术,所包括的质量工具有:因果分析、排列图、矩形图、抽样检验、控制图等。
[整理]6西格玛标准公差计算公式
六西格玛管理系列讲座之一什么是6西格玛管理?当人们谈论世界著名公司-通用电器(GE)的成功以及世界第一CEO-杰克.韦尔奇先生为其成功制定的三大发展战略时,都会不约而同地提出这样的问题。
如果概括地回答的话,可以说6西格玛管理是在提高顾客满意程度的同时降低经营成本和周期的过程革新方法,它是通过提高组织核心过程的运行质量,进而提升企业赢利能力的管理方式,也是在新经济环境下企业获得竞争力和持续发展能力的经营策略。
因此,管理专家Ronald Snee先生将6西格玛管理定义为:“寻求同时增加顾客满意和企业经济增长的经营战略途径。
”如果展开来回答的话,6西格玛代表了新的管理度量和质量标准,提供了竞争力的水平对比平台,是一种组织业绩突破性改进的方法,是组织成长与人才培养的策略,更是新的管理理念和追求卓越的价值观。
让我们先从6西格玛所代表的业绩度量谈起:符号σ(西格玛)是希腊字母,在统计学中称为标准差,用它来表示数据的分散程度。
我们常用下面的计算公式表示σ的大小:如果有两组数据,它们分别是1、2、3、4、5;和3、3、3、3、3;虽然它们的平均值都是3,但是它们的分散程度是不一样的(如图1-1所示)。
如果我们用σ来描述这两组数据的分散程度的话,第一组数据的σ为1.58,而第二组数据的σ为0。
假如,我们把数据上的这些差异与企业的经营业绩联系起来的话,这个差异就有了特殊的意义。
假如顾客要求的产品性能指标是3±2(mm),如果第一组数据是供应商A所提供的产品性能的测量值,第二组数据是供应商B所提供的产品性能的测量值。
显然,在同样的价格和交付期下,顾客愿意购买B的产品。
因为,B的产品每一件都与顾客要求的目标值或理想状态最接近。
它们与顾客要求的目标值之间的偏差最小。
假如顾客要求的产品交付时间是3天。
如果第一组数据和第二组数据分别是供应商A和B每批产品交付时间的统计值,显然,顾客愿意购买B的产品。
因为,B每批产品的交付时间与顾客要求最接近。
6西格玛-六个标准差(6_Sigma)
3 的不足(一)
過去個世紀以來,一般企業多建立在三 個希格瑪的品質水平,此一水平今後已 經無法接受。試想,99.73%的良品率看 來已經相當完善,但就服務業而言,它 的績效水平卻是如下所述
8
3 的不足(二)
每年20,000次的醫生藥方發生錯誤 銀行每小時有22,000張支票扣款弄錯 每年8.6小時的水電供應失常 在芝加哥國際機場,每天兩架飛機失事 每週有500次失敗的外科手術 每小時弄丟2,000份郵件
一個需要 250 個零件組成的產品由兩個廠 家來生產,他們的質量水平分別是3 與 6 ,那麼,每生產 10,000 個產品,他們 交給客戶的無缺陷產品將是 5,087 個及 9,999 個,由於市場是由顧客決定的,無 庸質疑, 6σ質量具有強勁的市場競爭力 。
27
Motorola 與 6 (一)
六個標準差(6 ) 中方國際集團達方軟件有限公司
-6σ
-5σ -4σ
-3σ
-2σ
-1σ
+1σ +2σ
+3σ
4σ
5σ
6σ
1
課程內容
1.什麼是 6
2. 6 的優勢
3. 6 的影響 4. Motorola 與 GE
2
什麼是 6
唸 “ 西格瑪 ” 或 “ Sigma ” 是希臘字母,在統計學上用來表示數據的 分散程度 對計量值而言,用 來度量與目標值的偏移 程度,6 表示分散程度只占規格公差的一半 對計數值而言,用 來度量缺陷率、不良率, 6 表示缺陷率為 3.4 PPM 6 = 3.4 PPM = Cp >= 2.0 = Cpk >= 1.5
六西格玛的计算公式
六西格玛的计算公式六西格玛是一种质量管理工具,旨在通过降低缺陷和错误率来提高过程的质量和性能。
它是一种系统化的方法,用于识别并消除造成问题的根本原因,以确保所生产的产品或提供的服务达到或超过客户的期望。
六西格玛的核心是一套统计工具和方法,用于分析数据并评估过程的可变性。
计算六西格玛的公式包括:1.DPMO(每百万机会缺陷数):DPMO表示在每一百万次机会中出现的缺陷数。
它是评估六西格玛过程能力的指标。
DPMO=(缺陷数/机会数)×1,000,0002. Sigma Level(西格玛水平):六西格玛可以根据DPMO值将过程分为不同的水平。
西格玛水平越高,表示过程的质量越高。
Sigma Level = 1 - (DPMO / 1,000,000)或 Z值其中,Z值是以标准正态分布为基础的统计度量。
3.CP(过程能力指数):CP是评估过程能力的指标,用于衡量过程的性能是否能够满足规定的要求。
CP指数大于1表示过程能够满足要求。
CP=(上限规格限制-下限规格限制)/(6×标准偏差)其中,标准偏差是过程的可变性的度量。
4.PPM(每百万机会缺陷率):PPM用于描述每一百万次机会中出现的缺陷数量。
它是评估过程质量的指标。
PPM=(缺陷数/机会数)×1,000,000以上是六西格玛计算公式的一些常见例子。
在实际应用中,根据具体情况和需求,可能会有其他计算公式和指标。
利用这些公式和指标,可以对过程进行度量和评估,找出问题的根本原因,并采取相应的改进措施,以提高过程的质量和性能。
六西格玛的计算公式
六西格玛的计算公式六西格玛(Six Sigma)是一种以数据驱动的管理方法,旨在提高组织的质量和效率。
它的主要思想是通过减少变异性和改进过程,达到持续改善的目标。
六西格玛的核心是一系列的计算公式和工具,用于描述和分析问题,提供解决方案。
本文将详细介绍六西格玛的常用计算公式。
1. 过程的故障指数(Defects Per Unit, DPU)过程的故障指数是指单位产品中存在的缺陷数量。
它可以通过以下公式计算:DPU=缺陷数/产品数量2. 故障率(Failure Rate)故障率是指单位时间内出现的故障数量。
它可以通过以下公式计算:故障率=故障数/总工作时间3. 流程的能力指数(Process Capability Index, Cp)流程的能力指数是用于评估一个流程是否能够在规定的上下限范围内稳定运行。
它可以通过以下公式计算:Cp=(上限规格-下限规格)/(6*标准差)4. 流程的能力指数 (至少100) = Total Variation/Specification Variation5. 流程的能力指数 (至少101) = Total Variation/Specification Variation6. 流程的能力指数 (至少105) = Total Variation/Specification Variation7. 流程的能力指数 (至少110) = Total Variation/Specification Variation8. 流程的能力指数 (至少120) = Total Variation/Specification Variation9. 流程的能力指数 (至少130) = Total Variation/Specification Variation10. 流程的能力指数(Process Performance Index, Ppk)流程的性能指数是用于评估一个流程是否能够在规定的上下限范围内稳定运行,并考虑了流程的中心位置。
- 1、下载文档前请自行甄别文档内容的完整性,平台不提供额外的编辑、内容补充、找答案等附加服务。
- 2、"仅部分预览"的文档,不可在线预览部分如存在完整性等问题,可反馈申请退款(可完整预览的文档不适用该条件!)。
- 3、如文档侵犯您的权益,请联系客服反馈,我们会尽快为您处理(人工客服工作时间:9:00-18:30)。
六西格玛管理系列讲座之一什么是6西格玛管理?当人们谈论世界著名公司-通用电器(GE)的成功以及世界第一C EO-杰克.韦尔奇先生为其成功制定的三大发展战略时,都会不约而同地提出这样的问题。
如果概括地回答的话,可以说6西格玛管理是在提高顾客满意程度的同时降低经营成本和周期的过程革新方法,它是通过提高组织核心过程的运行质量,进而提升企业赢利能力的管理方式,也是在新经济环境下企业获得竞争力和持续发展能力的经营策略。
因此,管理专家R onald Snee先生将6西格玛管理定义为:“寻求同时增加顾客满意和企业经济增长的经营战略途径。
”如果展开来回答的话,6西格玛代表了新的管理度量和质量标准,提供了竞争力的水平对比平台,是一种组织业绩突破性改进的方法,是组织成长与人才培养的策略,更是新的管理理念和追求卓越的价值观。
让我们先从6西格玛所代表的业绩度量谈起:符号σ(西格玛)是希腊字母,在统计学中称为标准差,用它来表示数据的分散程度。
我们常用下面的计算公式表示s的大小:如果有两组数据,它们分别是1、2、3、4、5;和3、3、3、3、3;虽然它们的平均值都是3,但是它们的分散程度是不一样的(如图1-1所示)。
如果我们用σ来描述这⎬两组数据的分散程度的话,第一组数据的σ为1.58,而第二组数据的s为0。
假如,我们把数据上的这些差异与企业的经营业绩联系起来的话,这个差异就有了特殊的意义。
假如顾客要求的产品性能指标是3±2(mm),如果第一组数据是供应商A所提供的产品性能的测量值,第二组数据是供应商B所提供的产品性能的测量值。
显然,在同样的价格和交付期下,顾客愿意购买B的产品。
因为,B的产品每一件都与顾客要求的目标值或理想状态最接近。
它们与顾客要求的目标值之间的偏差最小。
假如顾客要求的产品交付时间是3天。
如果第一组数据和第二组数据分别是供应商A和B每批产品交付时间的统计值,显然,顾客愿意购买B的产品。
因为,B每批产品的交付时间与顾客要求最接近。
尽管两个供应商平均交付时间是一样的,但顾客的评判,不是按平均值,而是按实际状态进行的。
假如顾客要求每批产品交付数量是3件。
如果第一组数据和第二组数据分别是供应商A和B每批产品交付数量的统计值,显然,供应商B向顾客供货的能力要大于A。
因为,供应商B每批都准确地达到了顾客交付数量的要求,而供应商A在交付期内不是由于各种原因达不到交付数量的要求,使顾客不满意;就是多生产了产品,增加了库存,积压了资金。
假如这些数据代表了服务响应时间、顾客满意程度、产品开发周期...等等,这些数据与顾客要求的离散程度以及与竞争对手的差异,就有了管理上的特殊意义。
We d on’t know what we don’t know.我们不了解我们不知道的东西,We can’t do what we don’t know.我们对不了解的东西不能有所作为,We don’t know until we measure.直到我们度量了我们才能了解,We don’t measure what we don’t value.我们不度量我们认为没有价值的东西,We don’t value what we don’t measu re.我们不重视我们不度量的东西。
在6西格玛管理中常常提到以上的谚语:我们不重视我们不度量的东西,我们对不度量的东西不能有所作为。
因此,6西格玛管理特别强调度量的作用,强调用顾客满意的方式,用提高竞争力和追求卓越的方法度量我们的业绩。
这点与我们传统的管理模式与方法是根本不同的。
让我们来看一看,在“度量什么”和“怎样度量”上,6西格玛管理与我们传统的做法有什么不同。
首先,在“度量什么”上,6西格玛管理提供了广泛的业绩度量“视角”。
我们许多企业在组织业绩的度量方面是不完善的。
在我们的日常管理活动中,针对产品特性或实现过程的度量往往比较明确,但对其他业绩的度量则比较含糊。
我们不善于使用客观的量化度量方法来度量企业当前的表现以及竞争对手的水平。
比如,一个追求“以快制胜”的企业,从未认真地度量过自己关键业务流程的周期,例如产品开发周期、试验与测试周期、主要产品的制造周期、市场导入周期等等,也不清楚自己的流程在“时间”上的“瓶颈”。
如果企业对“快”的追求是盲目的,就无法真正对“快”有所作为。
又比如,一个“以提供顾客服务”为营销特点的企业,并不清楚顾客对服务的需求与期望,也从没有认真地对服务过程的表现度量过。
比如说顾客对服务响应时间的要求以及目前企业的服务响应时间达到了什么水平等。
因此企业对“服务”无法真正有所作为。
6西格玛管理是基于对组织业绩度量的管理,它强调按照顾客的需求和企业发展重点度量组织业绩的各个方面。
比如:交付期、交付状态、产品质量、服务特性、成本、库存、顾客满意、员工满意、管理活动等等。
通过对组织业绩的广泛度量,寻求组织业绩突破和改进的空间。
再则,在“怎样度量”上,6西格玛管理提供了“追求卓越”的度量方法。
传统上,我们的度量仅限于“符合性”上。
举例来说,我们对照规范检查产品质量,我们把符合规范的记为合格品。
对合格品来说,一般我们不再关心其符合顾客要求的程度。
例如,某工序生产了A、B、C三个零件,A的测量值接近顾客要求的目标值,而B接近于规范下限,C则超过了规范下限(如图1-2所示)。
我们把控制与改进的注意力集中在C上。
尽管A产品的质量接近理想状态,而B产品几乎超差,但在传统的度量方法下,它们的质量表现是一样的,都视为合格品。
但正是这种度量方法忽略掉的差异,在竞争力方面带来了不可忽略的差异。
6西格玛管理重视符合顾客要求程度方面的差异,并通过采用揭示这些差异的度量方法,展示业绩改进的空间。
在6西格玛管理中,通常使用西格玛水平Z作为满足顾客要求程度的业绩度量。
在这种度量中,我们把每个测量值相对于顾客要求的偏离程度考虑进来。
Z有几种表达形式:最简单的一种是用测量数据的标准差s与顾客要求的上限(USL)和下限(LSL)的关系来表达,其公式为:达到6西格玛水平是指Z等于6。
如果用我们熟悉的正态分布来解释的话,也就是说过程的波动非常小,集中在目标值附近。
它们满足顾客要求的能力很强。
而3西格玛水平则波动较大,其满足顾客要求的能力远不如6西格玛水平。
(如图1-3所示)Z还有另一种表达形式:用百万分之缺陷率(ppm)来表示。
一个服从正态分布的过程,其超出规范限的缺陷百分比与西格玛水平是一一对应的(如图1-4所示)。
根据这个规律,我们可以通过测量缺陷的比率,估算过程的西格玛水平Z,并以此考察过程满足顾客要求的能力。
通常,6西格玛水平所代表的过程缺陷率为3.4ppm,而3西格玛水平的缺陷率为66807ppm。
我们不重视我们不度量的东西,我们对不度量的东西不能有所作为。
用顾客满意的方式,用提高竞争力和追求卓越的方法度量我们业绩的方方面面,是6西格玛管理的基础。
只有解决了“度量什么”和“怎样度量”的问题,才能发现我们在竞争力上的差距和改进空间。
这是实施6西格玛管理首先要解决的问题。
六西格玛管理系列讲座之二在上一讲中,我们介绍了6西格玛管理是基于组织业绩度量的管理。
6西格玛管理在“度量什么”和“怎样度量”上不同于传统的方法,它为提升组织的竞争力揭示出广泛的业绩改进空间。
由于测量对象、测量方法和数据类型不同,在6西格玛管理中有若干种用于业绩度量的指标。
下面我们就一些常用的指标作一介绍。
在6西格玛管理的度量中,常常用到下面的度量指标,它们是:FTY (First Time Yield) -首次产出率。
是指过程输出一次达到顾客规范要求的比率。
也就是我们常说的一次提交合格率。
RTY(Rolled Throughput Yield)-滚动产出率。
是构成过程的每个子过程的FTY之乘积。
表明由这些子过程构成的大过程的一次提交合格率。
RTY=FTY1⨯FTY2⋯⨯⋯⨯FTYn式中:FTYi是各子过程的首次产出率,n是子过程的个数。
用FTY或RTY度量过程可以揭示由于不能一次达到顾客要求而造成的报废和返工返修以及由此而产生的质量、成本和生产周期的损失。
这与我们通所采用的产出率的度量方法是不尽相同的。
在很多企业中,只要产品没有报废,在产出率上就不计损失。
因此掩盖了由于过程输出没有一次达到要求而造成的返修成本的增加和生产周期的延误。
举例来说,某过程由4个生产环节构成(如图2-1所示)。
该过程在步骤2和步骤4之后设有质控点。
根据生产计划部门的安排,投料10件。
经过步骤1和步骤2的加工后,在检验发现2个不合格品。
1件须报废,另1件经返修处理后可继续加工,这样有9件进入了后续的加工过程。
这9件产品经过步骤3和步骤4后又有1件报废,1件返修。
整个加工结束后,有8件产品交付顾客。
因此,生产计划部门的统计数据是:产出率=80%。
这个统计数据不能表明在这80%中,有一些是经过返修后交付的,这些返修活动增加了生产成本和生产周期。
如果我们用RTY来度量的话,可以看出,步骤1和步骤2的FT Y1为8/10=80%,步骤3和步骤4的FT Y2为7/9=78%。
如果投料100件的话,经过步骤1和步骤2,第一次就达到要求的是100⨯80%=80件,这些一次就达是要求的合格品经过步骤3和步骤4后,一次就能达到要求的将是80件⨯78%=62件。
也就是100⨯80%⨯78%=100⨯62.4%=62.4件,而80%⨯78%=62.4%正是我们说的FTY1⨯FTY2=RTY。
就这个例子来说,只有62%左右的产品(6件)是一次就达到加工要求的,而38%左右的产品需经返修或报废处理。
FTY=99%是不是足够好?在很多人看来,这已经足够好了。
FTY达到3.4ppm不过是种“理想”状态,实际上并不需要如此低的缺陷比率。
但是,如果我们用RTY来度量的话,可以发现越是步骤多、越是技术含量高的过程,对FTY的要求就越高。
从下表中可以看出,如果每个子过程的FTY都为99%,那么由50个子过程构成的大过程的RTY只有60.5%,也就是说将有40%的过程输出需经返工或报废处理。
也许,经过返修处理后,过程的输出可以100%地交付顾客,用我们传统的产出率的统计方法,这个过程的产出率是100%。
但事实上,这个过程中存在着质量、成本和周期的巨大损失。
而这些损失是竞争力的损失。
我们还可以用下面一些度量指标衡量过程满足顾客要求的能力:DPU (Defect Per Unit) -单位缺陷数。
是过程的“缺陷”数量与过程输出的“单位”数量比。
平均每个单位上有多少缺陷。
计算式为:DPU=缺陷总数/单位总数DPO (Defect Per Opportunity) -单位机会缺陷数。
是过程输出的“缺陷”的数量与过程输出的“缺陷机会数”之比。
计算式为:DPO=缺陷总数/缺陷机会总数DPMO (Defect Per Million Opportunity) -百万缺陷机会缺陷数。