锡珠的形成及对策29页PPT
波峰焊锡珠产生的原因及解决方案

波峰焊锡珠产生的原因及解决方案大家好,今天咱们聊聊波峰焊锡珠的事儿。
要说波峰焊,真的是电子制造中一个非常关键的环节。
它像是给咱们的电路板披上了一层“金色铠甲”,保护它不受外界的侵害。
但是,有时候,这个看似完美的过程会出现一些小麻烦,比如焊锡珠。
那么,这些焊锡珠到底是怎么来的呢?又该如何解决呢?接下来,就让咱们一探究竟吧。
1. 焊锡珠的成因1.1 焊接温度过高首先,我们得知道,焊锡珠通常是在焊接过程中出现的。
第一个大头原因就是焊接温度太高。
想象一下,你在厨房里做菜,火开得太猛,油锅里就会冒油花儿,烫得你跳脚。
波峰焊的情况也是类似,如果焊接温度过高,焊锡在碰到电路板的时候就容易挥发,导致焊锡珠的产生。
过高的温度不仅让焊锡液体挥发,还可能影响到板子的质量,简直就是一场灾难!1.2 焊锡液体过多再有一个原因就是焊锡液体的量过多。
就像你做饭时加了过多的盐,结果整锅饭都咸了。
在波峰焊中,如果焊锡液体的量过多,也会导致焊锡珠的产生。
这是因为焊锡液体在焊接过程中不能完全被板子吸收,最终就会形成多余的小珠子,挂在电路板上,这看起来真是让人哭笑不得。
2. 焊锡珠的解决方案2.1 调整焊接温度知道了问题的根源,咱们也有解决的办法。
首先要做的就是调整焊接温度。
试着把焊接温度降低一点点,看看效果如何。
焊接温度一般在240°C到260°C之间比较合适,大家可以根据自己的实际情况微调一下。
温度过高可不是好事,得适中才行。
你要记住,温度调得太高,锡珠飞溅,调得太低,又可能导致焊接不良,找准那个平衡点,才能让焊锡珠远离你的电路板。
2.2 控制焊锡液体量其次,焊锡液体的量也要控制好。
如果焊锡液体过多,就像是汤锅里的水太多,容易溢出来。
你可以通过调整焊锡槽的液面高度来控制焊锡的量。
合适的液体量不仅可以有效减少焊锡珠的产生,还能保证焊接的质量。
所以,控制好液体量也是非常关键的一个环节。
3. 板子的处理3.1 保持电路板干净除了以上两点,还得保证电路板的干净整洁。
锡珠的产生原因与解决措施

波峰焊接中溅锡珠的形成原因⑴ “小爆炸”理论波峰焊接中在 PCB 的焊接面及元件面上均可能产生锡珠飞溅现象。
普遍认为在 PCB 进入波峰之前有水汽滞留在PCB上的话,一旦与波峰钎料接触,在剧烈升温的过程中,就会在极短的时间内迅速汽化变成蒸汽,发生爆发性的排气过程。
正是这种剧烈的排气可能引发正处在熔融状态中的焊接点内部的小爆炸,从而促使钎料颗粒在脱离波峰时飞溅在PCB上形成锡珠。
在波峰焊接前PCB水汽的来源,杭州东方通信公司对此进行过专题研究和试验,归纳的结论如下:① 制造环境和PCB存放时间制造环境对电子装联的焊接质量有着很大的影响。
制造环境的湿度较重,或PCB包装开封较长时间后再进行贴片和波峰焊生产,或者PCB贴片、插装后放置一段时间后再进行波峰焊,这些因素都很有可能使PCB在波峰焊接过程中产生锡珠。
如果制造环境的湿度太大,在产品制造过程中空气浮动着水汽很容易会在PCB表面凝结,使PCB通孔中凝结有水珠,在过波峰焊时,通孔中的水珠经过预热温区后可能还没有完全挥发完,这些没有挥发完的水珠接触到波峰的焊锡时,经受了高温,就会在短时间内汽化变成蒸汽,而此时正是形成焊点的时候,水汽就会在焊料内产生空隙,或挤出焊料产生锡球。
严重的话就会形成一个爆点,并在它的周围分布有被吹开的细小的锡珠。
假如PCB在包装开封较长时间后再进行贴片和波峰焊,通孔中也会凝结有水珠;PCB完成贴片后或插装完成后放置了一段时间,也会凝结水珠。
同样的原因,这些水珠都有可能在波峰焊过程中导致锡珠产生。
因而,作为从事电子装联的企业,对制造环境的要求和对产品制造过程中的时间安排显得特别地重要。
贴片完成后的PCB应在24小时内完成插装并进行波峰焊,假如天气晴朗干燥,可以在48小时内完成。
② PCB阻焊材料和制作质量在PCB制造过程中所使用的阻焊膜也是波峰焊产生锡球的原因之一。
因为阻焊膜与助焊剂有一定的亲合性,阻焊膜加工不良常常会引起锡珠粘附,产生焊锡球。
浅析SMT组装中锡珠的产生原理及预防措施

浅析SMT组装中锡珠的产生原理及预防措施焊锡珠(SOLDER BALL)现象是表面贴装(SMT)过程中的重要缺陷,主要发生在片式阻容组件(CHIP)的周围,由诸多因素引起。
焊锡珠的存在,不仅影响了电子产品的外观,也对产品的质量埋下了隐患。
本文为大家简单解析一下锡珠的形成原理及应对方法。
一、焊球的分类根据锡珠的发生个数和大小,可以分为4种情况。
单个焊粉的情况下,直径为10~40µm,如果大小有50µm以上,则认为是多个焊粉融合。
二、助焊剂内锡珠形成原理・加热时锡膏坍塌在加热时锡膏出现坍塌,但并不是完全连接两焊盘(见0.1m m位置),而是在绿油桥中形成薄薄的锡珠(见0.2m m位置)。
・助焊剂流出随着溶融时助焊剂流出,较迟溶解的焊粉流出。
三、常见锡珠形成原因①回流焊温度曲线设置不当;②助焊剂未能发挥作用;③模板的开孔过大或变形严重;④贴片时放置压力过大;⑤焊膏中含有水分;⑥印制板清洗不干净,使焊膏残留于印制板表面及通孔中;⑦采用非接触式印刷或印刷压力过大;⑧焊剂失效。
四、常见防止锡珠产生方法PC B线路板上的阻焊层是影响锡珠形成最重要的一个因素。
在大多数情况下,选择适当的阻焊层能避免锡珠的产生。
使用一些特殊设计的助焊剂能帮助避免锡珠的形成。
另外,要保证使用足够多的助焊剂,这样在PC B线路板离开波峰的时候,会有一些助焊剂残留在PC B线路板上,形成一层非常薄的膜,以防止锡珠附着在PC B线路板上。
同时,助焊剂必须和阻焊层相兼容,助焊剂的喷涂必须采用助焊剂喷雾系统严格控制。
1、尽可能地降低焊锡温度;2、使用更多的助焊剂可以减少锡珠,但将导致更多的助焊剂残留;3、尽可能提高预热温度,但要遵循助焊剂预热参数,否则助焊剂的活化期太短;4、更快的传送带速度也能减少锡珠。
锡珠产生的原因分析
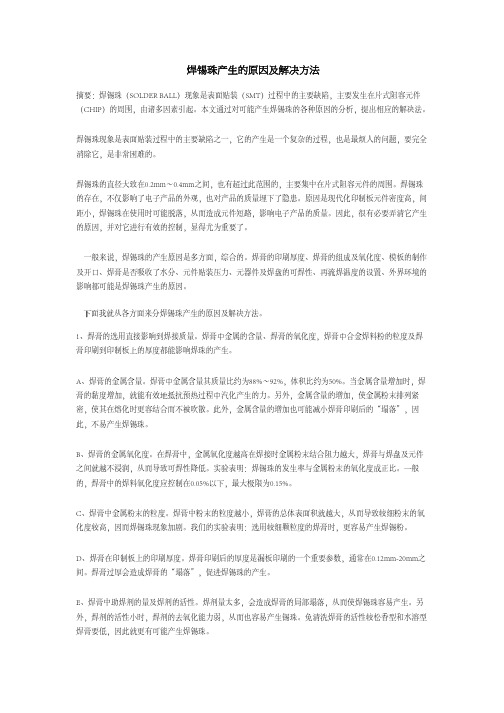
焊锡珠产生的原因及解决方法摘要:焊锡珠(SOLDER BALL)现象是表面贴装(SMT)过程中的主要缺陷,主要发生在片式阻容元件(CHIP)的周围,由诸多因素引起。
本文通过对可能产生焊锡珠的各种原因的分析,提出相应的解决法。
焊锡珠现象是表面贴装过程中的主要缺陷之一,它的产生是一个复杂的过程,也是最烦人的问题,要完全消除它,是非常困难的。
焊锡珠的直径大致在0.2mm~0.4mm之间,也有超过此范围的,主要集中在片式阻容元件的周围。
焊锡珠的存在,不仅影响了电子产品的外观,也对产品的质量埋下了隐患。
原因是现代化印制板元件密度高,间距小,焊锡珠在使用时可能脱落,从而造成元件短路,影响电子产品的质量。
因此,很有必要弄清它产生的原因,并对它进行有效的控制,显得尤为重要了。
一般来说,焊锡珠的产生原因是多方面,综合的。
焊膏的印刷厚度、焊膏的组成及氧化度、模板的制作及开口、焊膏是否吸收了水分、元件贴装压力、元器件及焊盘的可焊性、再流焊温度的设置、外界环境的影响都可能是焊锡珠产生的原因。
㆘面我就从各方面来分焊锡珠产生的原因及解决方法。
1、焊膏的选用直接影响到焊接质量。
焊膏中金属的含量、焊膏的氧化度,焊膏中合金焊料粉的粒度及焊膏印刷到印制板上的厚度都能影响焊珠的产生。
A、焊膏的金属含量。
焊膏中金属含量其质量比约为88%~92%,体积比约为50%。
当金属含量增加时,焊膏的黏度增加,就能有效地抵抗预热过程中汽化产生的力。
另外,金属含量的增加,使金属粉末排列紧密,使其在熔化时更容结合而不被吹散。
此外,金属含量的增加也可能减小焊膏印刷后的“塌落”,因此,不易产生焊锡珠。
B、焊膏的金属氧化度。
在焊膏中,金属氧化度越高在焊接时金属粉末结合阻力越大,焊膏与焊盘及元件之间就越不浸润,从而导致可焊性降低。
实验表明:焊锡珠的发生率与金属粉末的氧化度成正比。
一般的,焊膏中的焊料氧化度应控制在0.05%以下,最大极限为0.15%。
C、焊膏中金属粉末的粒度。
波峰焊过程中出现锡珠波峰焊过程中出现锡珠的原因及预防控制办法
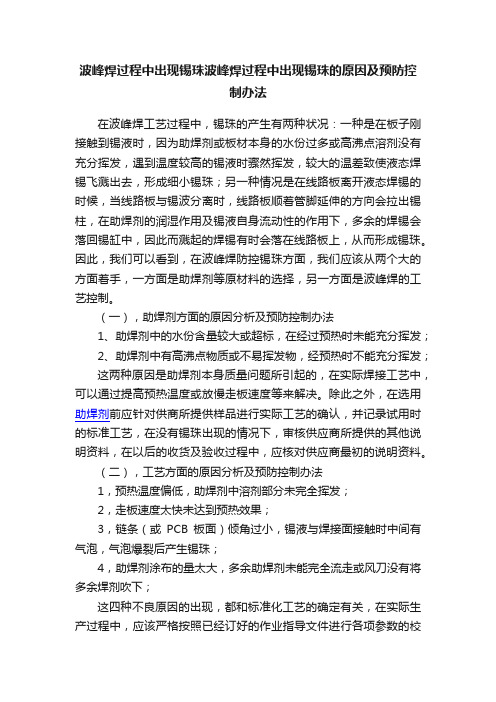
波峰焊过程中出现锡珠波峰焊过程中出现锡珠的原因及预防控制办法在波峰焊工艺过程中,锡珠的产生有两种状况:一种是在板子刚接触到锡液时,因为助焊剂或板材本身的水份过多或高沸点溶剂没有充分挥发,遇到温度较高的锡液时骤然挥发,较大的温差致使液态焊锡飞溅出去,形成细小锡珠;另一种情况是在线路板离开液态焊锡的时候,当线路板与锡波分离时,线路板顺着管脚延伸的方向会拉出锡柱,在助焊剂的润湿作用及锡液自身流动性的作用下,多余的焊锡会落回锡缸中,因此而溅起的焊锡有时会落在线路板上,从而形成锡珠。
因此,我们可以看到,在波峰焊防控锡珠方面,我们应该从两个大的方面着手,一方面是助焊剂等原材料的选择,另一方面是波峰焊的工艺控制。
(一),助焊剂方面的原因分析及预防控制办法1、助焊剂中的水份含量较大或超标,在经过预热时未能充分挥发;2、助焊剂中有高沸点物质或不易挥发物,经预热时不能充分挥发;这两种原因是助焊剂本身质量问题所引起的,在实际焊接工艺中,可以通过提高预热温度或放慢走板速度等来解决。
除此之外,在选用助焊剂前应针对供商所提供样品进行实际工艺的确认,并记录试用时的标准工艺,在没有锡珠出现的情况下,审核供应商所提供的其他说明资料,在以后的收货及验收过程中,应核对供应商最初的说明资料。
(二),工艺方面的原因分析及预防控制办法1,预热温度偏低,助焊剂中溶剂部分未完全挥发;2,走板速度太快未达到预热效果;3,链条(或PCB板面)倾角过小,锡液与焊接面接触时中间有气泡,气泡爆裂后产生锡珠;4,助焊剂涂布的量太大,多余助焊剂未能完全流走或风刀没有将多余焊剂吹下;这四种不良原因的出现,都和标准化工艺的确定有关,在实际生产过程中,应该严格按照已经订好的作业指导文件进行各项参数的校正,对已经设定好的参数,不能随意改动,相关参数及所涉及技术层面主要有以下几点:(1),关于预热:一般设定在90℃-110℃,这里所讲温度是指预热后PCB板焊接面的实际受热温度,而不是表显温度;如果预热温度达不到要求,则焊后易产生锡珠。
锡珠的产生原因及解决方法

锡珠的产生原因及解决方法锡珠的产生原因及解决方法锡珠现象是smt过程中的主要缺陷,主要发生在片式阻容元件的周围,由诸多因素引起。
它的产生是一个复杂的过程,也是最烦人的问题,要完全消除它,是非常困难的。
锡珠的直径大致在0.2mm——0.4mm之间,也有超过此范围的。
锡珠的存在,不仅影响了电子产品的美观,对产品的质量也有极大的隐患。
我们都知道现在smt工艺中的元件间距小,密度高,若是锡珠在使用时脱落,就可能造成元件短路,影响电子产品的质量。
因此,弄清锡珠产生的原因,并对它进行有效的控制,显得尤为重要了。
锡珠的产生原因是多方面造成的。
锡膏的印刷厚度、其组成及氧化度、模板的制作及开口都有可能造成锡珠现象,同时锡膏是否吸收了水分、元件贴装压力、元器件及焊盘的可焊性、再流焊温度的设置、外界环境的影响都可能是锡珠产生的原因。
下面吉田店铺就从各方面来分锡珠产生的原因及解决方法。
1、锡膏的金属氧化度。
在锡膏中,金属氧化度越高在焊接时金属粉末结合阻力越大,锡膏与焊盘及元件之间就越不浸润,从而导致可焊性降低。
锡珠的发生率与金属粉末的氧化度成正比。
一般的,锡膏中的焊料氧化度应控制在0.05%以下,最大极限为0.15%。
2、锡膏在印制板上的印刷厚度。
锡膏印刷后的厚度是漏板印刷的一个重要参数,通常在0.12mm——0.20mm之间。
锡膏过厚会造成锡膏“塌边”,促进锡珠的产生。
3、锡膏中助焊剂的量及焊剂的活性。
焊剂量太多,会造成锡膏的局部塌落,从而使锡珠容易产生。
另外,焊剂的活性小时,焊剂的去氧化能力弱,从而也容易产生锡珠。
免清洗锡膏的活性较松香型和水溶型锡膏要低,因此就更有可能产生锡珠。
4、此外,锡膏在使用前,一般冷藏在冰箱中,取出来以后应该使其恢复到室温后打开使用,否则,锡膏容易吸收水分,在再流焊锡飞溅而产生锡珠。
58回流焊中锡珠形成的原因及解决方法介绍|南昌回流焊原理2017-03-22 12:44 | #2楼波峰焊第一品牌【精极科技】深圳市精极科技有限公司成立于2002年8月,是一家以设计、生产、销售等工业仓储设备及柔性生产线设备为主的专业生产厂家,同时分销配套的防静电周边产品。
锡珠的形成及对策分析

7
而非锡珠(solder beads)
返回
锡珠形成的原因概述
锡珠
是怎样产生的
A 材料的原因
B 工艺的原因
I. 锡膏触变系数大
①
II. 锡膏冷坍塌或轻微热坍塌 ②
III. 焊剂过多或活性温度低
③
IV. 锡粉氧化率高或颗粒不均匀 ④
V. PCB的焊盘间距小
⑤
VI. 刮刀材质硬度小或变形
刮刀
锡膏
焊盘
钢版
9 PCB
返回
PCB 与钢版的间隔
在紧密印刷中不建议有间隔
!!
不建议
印刷钢板
PAD
PAD
线路板
10
不建议
脱模
返回
锡珠形成的原因(贴零件环节)锡膏印刷来自贴零件装 IC
回流焊接
检验
零件贴装部分
a) 贴片压力太大 b) 贴片精度太差 c) 其它因素
11
返回
贴片精度
线路板的精确度 ( PAD,校准点等)
共需要45分钟
介绍
锡珠 的形成和解决 SMT各工艺环节锡珠的预防措施和解决方法 根据鱼骨图逐项排除
3
大纲
相关词汇 (名词解释或定义)
SMT焊接中形成锡珠的现象
(正确的认识,错误的识别)
形成锡珠的原因(各工艺环节)
(印刷,贴件,回流焊接)
不停线调整减少锡珠的暂时对策
(暂时对策)
改良网版设计消除产生锡珠的隐患
14
Solder Beads
返回
其它的预防和改良措施
SMT各层工作人员的素质 SMT管理人员品质标准的培训 SMT 操作人员的相关操作的培训 明确各个工作岗位的权责(该做与不该做) 思想觉悟以及品质意识的提高
锡珠

焊锡珠是一颗或一些大的焊锡球,通常落在片状电容和电阻周围。
虽然这常常是丝印时锡膏过量堆积的结果,但有时可以调节温度曲线解决。
和焊锡球一样,在RTS曲线上产生的焊锡珠通常是升温速率太慢的结果。
这种情况下,慢的升温速率引起毛细管作用,将未回流的锡膏从焊锡堆积处吸到元件下面。
回流期间,这些锡膏形成锡珠,由于焊锡表面张力将元件拉向机板,而被挤出到元件边。
和焊锡球一样,焊锡珠的解决办法也是提高升温速率,直到问题解决。
看了你的炉温曲线设定有异常,升温速率过快,锡膏中的溶剂容易产生突沸,气体将锡珠带出。
升温速率降下来还有锡珠考虑钢网开孔方案一般0805 开U形槽还是有问题就开内缩外导角
问题仍未解决,就考虑PCB板材潮湿问题
另外锡膏使用方法是否得当回温时间不够易产生锡珠(当然这是在锡膏没有问题的情况下)
我也比较赞成炉温的升温和恒温时间,升温建议你时间拉长点,平缓一点,恒温时间加长;不太熟悉你这个测试软件,有点搞不清楚你的升温和恒温的具体时间。
你应该是做的有铅产品吧!另外看看锡膏使
用有没按要求吧!。