轴承加工工艺流程
轴承生产工艺流程

轴承生产工艺流程
轴承生产工艺流程:
原材料——内、外圈加工、钢球或滚子加工、保持架(冲压或实体)加工——轴承装配——轴承成品。
轴承内外圈工艺流程:
棒材——下料——锻造——球化退火——车加工——热处理——磨加工——超精加工——零件终检——防锈入库。
钢球的加工过程:
棒料或线材冷冲(有的棒料冷冲后还需冲环带和退火)——挫削、粗磨、软磨或光球——热处理——硬磨——精磨——精研或研磨——终检分组——防锈、包装——入库〈待合套装配〉。
滚子的加工过程:
棒料车加工或线材冷镦后串环带及软磨——热处理——串软点——粗磨外径——粗磨端面——终磨端面——细磨外径——终磨外径——终检分组——防锈、包装——入库(待合套装配〉。
保持架的加工过程:
铸铜件——车内径、外径、端面、倒角——钻孔(或拉孔、镗孔)——去毛刺——酸洗——终检——防锈、包装——入库〈待合套装配〉。
轴承加工工艺流程

轴承加工工艺流程引言轴承是机械设备中常见的零件之一,用于支撑和定位旋转机械的轴。
轴承的加工工艺流程对于轴承的质量和性能有着重要的影响。
本文将介绍轴承加工的一般工艺流程,包括原料准备、车、磨、热处理和装配等环节。
一、原料准备轴承的原材料一般是钢材,根据需要可以选择不同种类和牌号的钢材。
在轴承加工之前,首先需要对原材料进行准备。
原料准备的主要步骤包括材料验收、材料切割和材料成型。
首先,对原材料进行验收,检查原材料的质量和规格是否符合要求。
然后,将原材料切割成适当的长度,以便后续加工操作。
最后,通过冷锻、热锻等成型工艺,将切割好的原材料进一步成型为轴承的预制件。
二、车削加工车削是轴承加工中常用的一种加工方法,主要用于加工轴承的外圆、内圆和面。
车削加工的流程包括设备调整、工件夹持、刀具选择、车削操作和尺寸检测等环节。
在车削加工之前,需要调整车床等设备,保证其正常运转和加工精度。
然后,将轴承安装在车削设备上,并进行夹持。
接下来,选择合适的刀具,根据轴承的要求进行车削操作。
最后,通过尺寸检测,确保车削加工的尺寸精度和表面质量符合要求。
三、磨削加工磨削是轴承加工中另一种常用的加工方法,主要用于提高轴承的精度和表面质量。
磨削加工的流程包括设备调整、砂轮选择、工件夹持、磨削操作和尺寸检测等环节。
在磨削加工之前,同样需要调整磨削设备,保证其正常运转和加工精度。
然后,选择适当的砂轮,根据轴承的要求进行磨削操作。
在磨削过程中,需要注意控制砂轮的磨损和磨削温度,以避免影响磨削效果。
最后,通过尺寸检测,确保磨削加工的尺寸精度和表面质量达到要求。
四、热处理热处理是轴承加工中一个重要的环节,可以改变轴承的组织结构和性能。
常见的热处理方法包括淬火、回火和渗碳等。
热处理的流程包括预热、热处理和冷却等阶段。
在热处理之前,需要对轴承进行预热,以去除表面的污垢和湿气,提高热处理效果。
然后,将轴承放入热处理炉中,进行淬火、回火或渗碳等热处理操作。
减速箱轴承的加工工艺流程
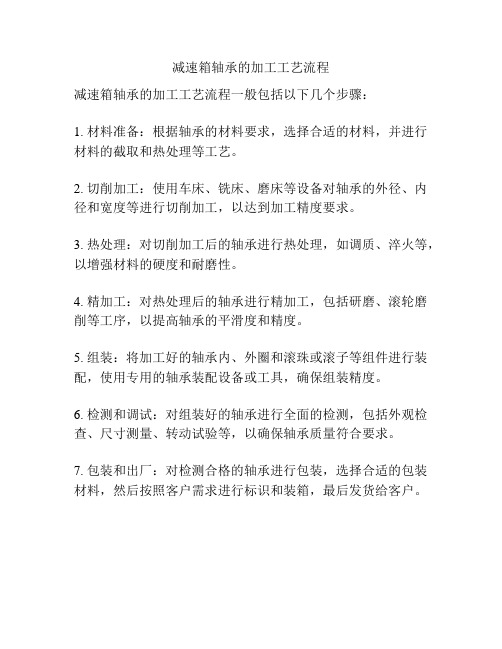
减速箱轴承的加工工艺流程
减速箱轴承的加工工艺流程一般包括以下几个步骤:
1. 材料准备:根据轴承的材料要求,选择合适的材料,并进行材料的截取和热处理等工艺。
2. 切削加工:使用车床、铣床、磨床等设备对轴承的外径、内径和宽度等进行切削加工,以达到加工精度要求。
3. 热处理:对切削加工后的轴承进行热处理,如调质、淬火等,以增强材料的硬度和耐磨性。
4. 精加工:对热处理后的轴承进行精加工,包括研磨、滚轮磨削等工序,以提高轴承的平滑度和精度。
5. 组装:将加工好的轴承内、外圈和滚珠或滚子等组件进行装配,使用专用的轴承装配设备或工具,确保组装精度。
6. 检测和调试:对组装好的轴承进行全面的检测,包括外观检查、尺寸测量、转动试验等,以确保轴承质量符合要求。
7. 包装和出厂:对检测合格的轴承进行包装,选择合适的包装材料,然后按照客户需求进行标识和装箱,最后发货给客户。
滚动轴承的机械加工工艺过程卡
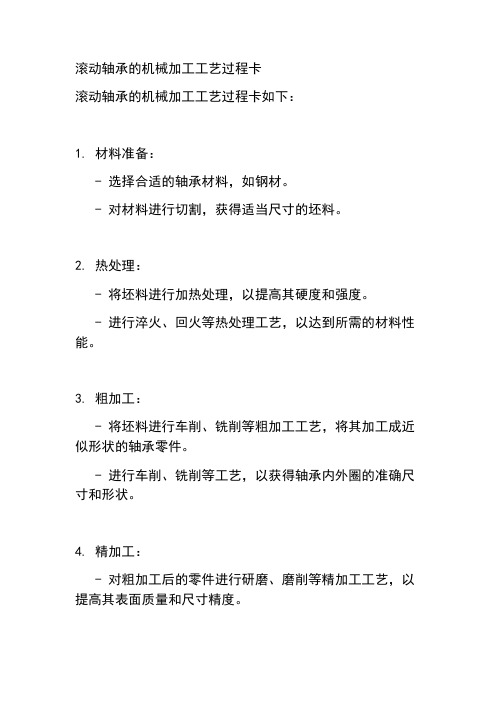
滚动轴承的机械加工工艺过程卡
滚动轴承的机械加工工艺过程卡如下:
1. 材料准备:
- 选择合适的轴承材料,如钢材。
- 对材料进行切割,获得适当尺寸的坯料。
2. 热处理:
- 将坯料进行加热处理,以提高其硬度和强度。
- 进行淬火、回火等热处理工艺,以达到所需的材料性能。
3. 粗加工:
- 将坯料进行车削、铣削等粗加工工艺,将其加工成近似形状的轴承零件。
- 进行车削、铣削等工艺,以获得轴承内外圈的准确尺寸和形状。
4. 精加工:
- 对粗加工后的零件进行研磨、磨削等精加工工艺,以提高其表面质量和尺寸精度。
- 进行研磨、磨削等工艺,以获得轴承内外圈的光滑表
面和准确尺寸。
5. 组装:
- 将精加工后的轴承内外圈与滚动体、保持架等零件进
行组装。
- 使用适当的装配工艺和工具,将各个零件组装在一起,形成完整的轴承。
6. 检测:
- 对组装好的轴承进行检测,以确保其质量和性能符合
要求。
- 进行外观检查、尺寸检测、轴向游隙检测等工艺,以
验证轴承的质量和性能。
7. 表面处理:
- 对检测合格的轴承进行表面处理,如防锈处理、涂层
处理等。
- 进行防锈、涂层等工艺,以提高轴承的耐腐蚀性和使
用寿命。
8. 包装:
- 将经过表面处理的轴承进行包装,以保护其不受损坏。
- 使用适当的包装材料和方法,将轴承包装好,以便运输和存储。
以上是滚动轴承的机械加工工艺过程卡的详细描述,每个步骤都是为了确保轴承的质量和性能,以满足使用要求。
轴承加工工艺流程
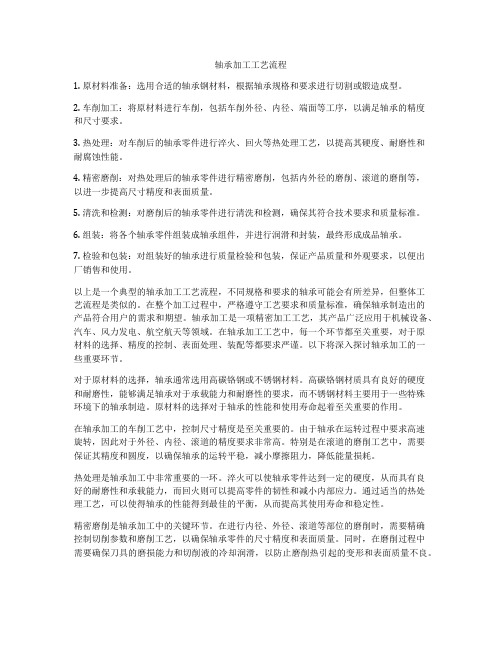
轴承加工工艺流程1. 原材料准备:选用合适的轴承钢材料,根据轴承规格和要求进行切割或锻造成型。
2. 车削加工:将原材料进行车削,包括车削外径、内径、端面等工序,以满足轴承的精度和尺寸要求。
3. 热处理:对车削后的轴承零件进行淬火、回火等热处理工艺,以提高其硬度、耐磨性和耐腐蚀性能。
4. 精密磨削:对热处理后的轴承零件进行精密磨削,包括内外径的磨削、滚道的磨削等,以进一步提高尺寸精度和表面质量。
5. 清洗和检测:对磨削后的轴承零件进行清洗和检测,确保其符合技术要求和质量标准。
6. 组装:将各个轴承零件组装成轴承组件,并进行润滑和封装,最终形成成品轴承。
7. 检验和包装:对组装好的轴承进行质量检验和包装,保证产品质量和外观要求,以便出厂销售和使用。
以上是一个典型的轴承加工工艺流程,不同规格和要求的轴承可能会有所差异,但整体工艺流程是类似的。
在整个加工过程中,严格遵守工艺要求和质量标准,确保轴承制造出的产品符合用户的需求和期望。
轴承加工是一项精密加工工艺,其产品广泛应用于机械设备、汽车、风力发电、航空航天等领域。
在轴承加工工艺中,每一个环节都至关重要,对于原材料的选择、精度的控制、表面处理、装配等都要求严谨。
以下将深入探讨轴承加工的一些重要环节。
对于原材料的选择,轴承通常选用高碳铬钢或不锈钢材料。
高碳铬钢材质具有良好的硬度和耐磨性,能够满足轴承对于承载能力和耐磨性的要求,而不锈钢材料主要用于一些特殊环境下的轴承制造。
原材料的选择对于轴承的性能和使用寿命起着至关重要的作用。
在轴承加工的车削工艺中,控制尺寸精度是至关重要的。
由于轴承在运转过程中要求高速旋转,因此对于外径、内径、滚道的精度要求非常高。
特别是在滚道的磨削工艺中,需要保证其精度和圆度,以确保轴承的运转平稳,减小摩擦阻力,降低能量损耗。
热处理是轴承加工中非常重要的一环。
淬火可以使轴承零件达到一定的硬度,从而具有良好的耐磨性和承载能力,而回火则可以提高零件的韧性和减小内部应力。
轴承制造工艺流程

轴承制造工艺流程轴承是一种旋转运动的零件,广泛应用于各种机械设备中。
轴承的制造工艺流程包括以下几个主要步骤:1.材料准备:轴承的材料一般选用高品质的轴承钢,如GCr15、首先需要从供应商处购买合格的轴承钢材料,并进行材料的检验和鉴定。
2.热处理:轴承钢经过锻造后,需要进行热处理,以提高其硬度和强度。
热处理过程包括均热、淬火和回火等步骤,以使轴承钢具有所需的机械性能。
3.毛坯制备:将经过热处理的轴承钢锻坯进行车削、锯切等操作,将其加工成符合轴承尺寸和几何要求的毛坯。
毛坯可通过铣床、车床和切割等机械设备进行加工。
4.理化分析:对轴承毛坯进行理化分析,以检测其化学成分、机械性能等指标是否符合要求。
常用的检测手段包括金相显微镜、硬度计、冲击试验仪等。
5.精车:对轴承毛坯进行精车,以提高表面质量和尺寸精度。
精车过程可以采用磨床、车床等设备进行,使得轴承表面光滑平整,并控制尺寸在规定的公差范围内。
6.组装:将精车好的轴承外环、内环和滚动体进行组装。
组装过程需要使用适当的工具和设备,以确保各零件的配合间隙、间隔和位置。
7.试验和检测:组装后的轴承进行试验和检测,以验证其性能和质量。
常见的检测项目包括径向游隙、轴向游隙、旋转精度、噪音和振动等。
8.表面处理:对轴承外环和内环表面进行处理,以提高其耐磨、耐腐蚀和润滑性能。
表面处理方式包括电镀、浸油、热处理等。
9.包装和出厂:对合格的轴承进行包装,以便于运输和流通。
包装方式通常包括盒装、木箱装等。
经过包装后,轴承即可出厂销售。
轴承制造工艺流程的每个步骤都需要特定的设备和工艺技术支持,其中精车、组装和检测是关键步骤,直接影响轴承的质量和性能。
进一步提高轴承制造工艺水平,优化流程,提高产品质量,是轴承制造行业面临的挑战和任务。
轴承工艺基本知识

轴承工艺基本知识一.轴承加工过程:锻件→锻造→退火→车加工车内径、外基面→车内外径、基面→软磨平面→软管料磨内外径→细车内径→倒角→车沟→提交车外内径、非基面→车外径、基面→软磨平→软磨外径→倒角→车沟→车牙口→车止动槽→提交→磨加工磨平面→粗、细磨外径→磨外沟→精研外沟→磨坡→修磨外径→清洗磨内平面→磨内外径→磨内沟→磨内径→精研内沟→清洗→装配:装前清洗、退磁、印字→合套(擦套)→压力铆合→成品清洗→压盖→包装二.轴承磨加工:磨加工第一道工序是平面工序,它是基础工序,直接影响下工序的加工质量,精度要求有:平面的平行度、平凸面度及平面的平面度。
这三项是平面加工的主要精度要求,还有磨削的光度及外观质量。
对不同精度等级的产品,精度要求不同,主要有P0;P6;P5及出国产品,出国产品主要是外观要求比较严格。
1.外套工序:1). 磨外径工序:是基础工序,主要精度要求有:尺寸、园度(椭圆、三角、波纹度)、垂直差、锥度、光洁度、表面质量。
对不同等级的产品要求不一样,一般精度要求每级要差1~3μm。
该工序是外沟的加工基准,园度及尺寸是直接影响外沟园度及尺寸的主要因素,垂直差和锥度影响轴承使用过程中的装配和性能。
2). 磨外沟工序:是加工轴承主要工作表面的工序,主要精度要求有:尺寸、园度(椭圆、三角、波纹度)、烧伤、沟曲率R、沟位置、沟侧摆、光洁度、表面质量等。
对不同等级的产品要求不一样,该工序的尺寸要求较松。
由于外沟从1990年以后均采用浮动圆弧支点,故可以改变部分外径园度对外沟园度的影响。
因此外径园度要求一般控制在外沟园度要求的基础上,约小1~2。
实际工作中外沟园度基本保证在外径园度要求上下约1μm左右。
平面的平行度等三项精度影响外沟的沟侧摆。
3). 外沟精研工序:其精度要求与磨外沟工序相同,波纹度和光洁度的要求较高, Ra为0.32,在加工P5(Z1、Z2)产品时,要采用较好的精研油石,粒度要细一些。
一般粗研油石为W14的,精研油石为W3.5混合磨料的。
轴承的工艺流程

轴承的工艺流程轴承是一种常用的机械元件,用于支撑旋转轴的运动。
轴承制造工艺流程包括原材料准备、零件加工、装配和淬火等步骤。
下面简要介绍一下轴承的工艺流程。
首先是原材料的准备。
轴承的主要原材料是钢材,通常使用高碳铬钢或不锈钢制造。
原材料需要经过检验,确保质量符合要求。
然后将原材料切割成适当的尺寸,以备后续加工。
第二步是零件的加工。
首先是球体的加工,将切割好的原材料在机床上进行数控加工,使其成为规定尺寸和形状的球体。
然后对轴承套圈和外圈进行车削、铣削等加工工序,使其能与球体配合运动。
接下来对其他零件如内圈、挡圈等进行相应的加工工艺,以产生与球体和套圈外圈的正确配合关系。
第三步是装配。
在装配过程中,先将内圈和外圈与球体组合一起,然后通过润滑剂和密封圈等配件进行加工,形成完整的轴承。
在装配过程中需要严格控制套圈和球体之间的间隙,以确保轴承的正常运转。
最后是淬火。
淬火是为了提高轴承的硬度和耐磨性能。
在淬火过程中,将轴承加热到适当温度,然后迅速冷却,使其在金相组织上形成马氏体结构,提高硬度。
接下来进行回火处理,以减轻淬火产生的内应力,提高韧性和抗脆性,使轴承具有较好的综合性能。
整个工艺流程中,需要密切关注零件加工精度和装配过程中的质量控制。
只有在确保零件尺寸和形状精度的前提下,才能保证轴承正常运转和使用寿命。
此外,还需要保证装配过程中的清洁环境,避免灰尘、污染等对轴承的影响。
综上所述,轴承工艺流程包括原材料准备、零件加工、装配和淬火等步骤。
通过严格控制每个环节的工艺要求和质量控制,可以生产出高质量的轴承产品。
轴承的质量对机械设备的运行和寿命有着重要的影响,因此轴承制造工艺流程的合理设计和实施非常关键。
- 1、下载文档前请自行甄别文档内容的完整性,平台不提供额外的编辑、内容补充、找答案等附加服务。
- 2、"仅部分预览"的文档,不可在线预览部分如存在完整性等问题,可反馈申请退款(可完整预览的文档不适用该条件!)。
- 3、如文档侵犯您的权益,请联系客服反馈,我们会尽快为您处理(人工客服工作时间:9:00-18:30)。
轴承是当代机械设备中一种重要零部件。
它的主要功能是支撑机械旋转体,降低其运动过程中的摩擦系数,并保证其回转精度。
按运动元件摩擦性质的不同,轴承可分为滚动轴承和滑动轴承两大类。
轴承可同时承受径向负荷和轴向负荷。
能在较高的转速下工作。
接触角越大,轴向承载能力越高。
那么轴承是怎么加工出来的呢?
轴承制造加工基本过程(以套圈制造基本流程为重点,材料选用高碳铬轴承钢Gcr15SiMn)?
<1>滚动体(钢球)制造基本流程:
原材料——冷镦——光磨——热处理——硬磨——初研——外观?——精研?
<2>保持架(钢板)制造基本流程:
原材料——剪料——裁环——光整——成形——整形——冲铆钉孔?
<3>套圈(内圈、外圈)制造基本流程:?
原材料——锻造——退火——车削——淬火——回火——磨削——装配
汇普轴承加工流程图
(1)锻造加工:锻造加工是轴承套圈加工中的初加工,也称毛坯加工。
?
套圈锻造加工的主要目的是:?
(a)获得与产品形状相似的毛坯,从而提高金属材料利用?率,节约原材料,减少机械加工量,降低成本。
(b)消除金属内在缺陷,改善金属组织,使金属流线分布合理,金属紧密度好,从而提高轴承的使用寿命。
锻造方式:一般是在感应加热炉、压力机、扩孔机和整形机组成连线的设备体进行流水作业?
(2)退火:套圈退火的主要目的是:高碳铬轴承钢的球化退火是为了获得铁素体基体上均匀分布着细、小、匀、圆的碳化物颗粒的组织,为以后的冷加工及最终的淬回火作组织准备。
?
Gcr15SiMn退火基本工序:?
在790—810℃保温2-6h,?以10—30℃/h,冷至600℃以下,出炉空冷?
(3)车削加工:车削加工是轴承套圈的半成品加工,也可以说是成型加工。
车削加工的主要目的是:?
(a)使加工后的套圈与最终产品形状完全相同。
?
(b)为后面的磨削加工创造有利条件。
?
车削加工的方法:?
集中工序法:在一台设备上完成所有车削工序的小批量生产。
?
分散工序法:在一台设备上完成某一种车削工序的大批量生产。
(4)热处理:热处理是提高轴承内在质量的关键加工工序。
?
热处理的主要目的是:?
(a)通过热处理使材料组织转变,提高材料机械性能。
(b)提高轴承内在质量(耐磨性、强韧性),从而提高轴承寿命。
对于高碳铬轴承钢Gcr15SiMn,热处理包括淬火和低温回火淬火:?
加热温度:820—840(℃)?保温时间:?1-2h??冷却介质:油?低温回火:?
加热温度:150—180(℃)?保温时间:2-5h??冷却方式:空冷?
(5)磨削加工:磨削加工是轴承套圈和滚子加工中的最终加工,称为成品加工。
??
磨削加工的主要目的是:?
(a)使套圈的尺寸精度和形状精度达到设计要求。
(b)为轴承装配提供合格的套圈和。
?
磨削加工方法:一般采用分散工序法加工,也可把多台设备通过上、下料装置连接组成生产流水线加工,提高生产效率。
(6)轴承装配:轴承装配是轴承生产过程中的最后工序,对轴承性能具有重要的影响。
?
轴承装配的主要目的是:
(a)把经过多种工序加工的零件(外圈、内圈、滚子和保持
架)装配成轴承产品。
?
(b)按不同的技术要求,装配成各种精度、各种游隙和其他特殊要求的轴承产品。